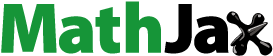
ABSTRACT
Effects of surface grain refinement and residual stress on the local and global properties of pure Cu processed using ultrasonic nanocrystalline surface modification (UNSM) was investigated. To distinguish each contribution to the local hardness and global tensile properties of the UNSM treated Cu, a stress-relief specimen of the same microstructure as the UNSM treated one was produced by low-temperature annealing after the UNSM treatment. The distinct contributions of residual stress and surface grain refinement to the tensile property of UNSM treated Cu were determined and discussed.
GRAPHICAL ABSTRACT
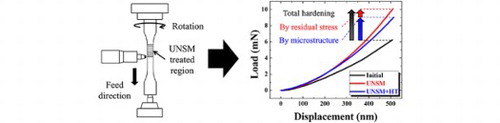
IMPACT STATEMENT
The contributions of surface grain refinement and compressive residual stress on the enhanced local and global strengths of the UNSM-processed Cu were estimated as 80% and 20%, respectively.
A persistent dream in the structural material community is to achieve both high strength and ductility. However, it is well known that homogeneous ultrafine-grained (UFG) and nanocrystalline (NC) metallic materials have high strength but low ductility. As a result, many studies on heterogeneous microstructure materials have been performed to improve their strength and still provide reasonable ductility in UFG materials [Citation1,Citation2]. In particular, creating a gradient structure is one of the solutions used to overcome the strength and ductility trade-off. Gradient structured materials have heterogeneous microstructures with varying grain size (from a few nanometers or micrometers to a few millimeters) from the surface to inner regions and many good mechanical properties have been reported by those using this approach [Citation3,Citation4].
Surface severe plastic deformation (S2PD) processes, such as surface mechanical attrition treatment (SMAT), shot peening (SP), and high-pressure torsion [Citation5–8], are efficient surface-nanostructuring processes used to manufacture gradient structure with high-strength UFG or NC surface regions. Recently, a new S2PD called the ultrasonic nanocrystalline surface modification (UNSM) technique, shown in Figure , has exhibited improved global mechanical properties as well as surface properties of the processed material [Citation9,Citation10]. The advantages of the UNSM technique include uncomplicated production facility, low apparatus and processing costs, and easily and accurately controllable static and dynamic loadings. These are characteristics important not only for obtaining accurate and reproducible gradient microstructures but also for realistic industrialization [Citation11].
The source of the evolution of microstructure and improved properties in S2PD-processed materials is the combination of surface grain refinement and residual stress. Nevertheless, most of the reports on S2PD-processed materials have dealt with microstructural aspects and ignored the residual stress effect. However, as with the other S2PD processes (e.g. SMAT and SP), UNSM induces highly compressive residual stress in the processed surface region [Citation12–14]. While there have been several studies on the effect of residual stress on improved fatigue properties of S2PD-processed materials, the separate effects of surface grain refinement and residual stress on the tensile/compressive properties have hardly been investigated [Citation15–17]. To examine the tensile properties of the S2PD-processed materials, if any examination of them was done, micro samples for the tensile tests were fabricated from the local nano crystalline region and the residual stress was ignored [Citation18,Citation19]. In addition to the local properties, the global mechanical behavior of a processed material is also important in engineering design for specific applications.
In this study, the effects of residual stress and surface grain refinement on the local and global mechanical properties of Cu processed by UNSM were investigated. To distinguish the contributions of surface grain refinement and residual stress to the local and global properties of the UNSM treated Cu, a stress-relief specimen with the same microstructure as the UNSM treated one was produced by low-temperature annealing after the UNSM treatment.
For the experimental study, pure Cu was selected. Copper sheet with commercial purity of 99.99% was annealed at 600°C for 2 h. This was followed by furnace cooling for homogenization in the initial state (homogeneous and stress-free) specimen. For UNSM processing, dog-bone shaped specimens of 1.5 mm gauge length and 6.25 mm diameter were fabricated from the annealed sample. The specimens were designed based on the ASTM E8 standard size with reduced gauge length. The UNSM process was performed at room temperature and the parameters related to the quality of the UNSM process are listed in Table .
Table 1. UNSM treatment parameters for pure Cu.
To remove the residual stress induced on the surface after the UNSM process without microstructural change, low-temperature heat treatment (HT) was performed at 50°C for 4 h. This HT condition was determined after doing various experiments with several combinations of temperature (from 50°C to 100°C) and time. The temperature and time were chosen at which the residual stress could be removed effectively to prevent recrystallization or grain growth [Citation20]. Hereafter, the UNSM treated sample and the surface-grain-refined + stress-relief specimen will be called UNSM and UNSM + HT samples, respectively.
To observe the grain size distributions of the samples, the microstructures in the cross-sections were examined using a field emission scanning electron microscope (FE-SEM: XL-30S FEG, Philips Electron Optics, Netherlands) equipped with electron backscatter diffraction (EBSD). The EBSD data were analyzed using orientation imaging microscopy (OIM) analysis software (TSL OIM Analysis 5).
The residual stress of the samples was investigated using X-ray diffraction (XRD: D/MAX-2500, RIGAKU, Japan) and checked using nano indentation analysis (Agilent G200, CA, USA) [Citation21,Citation22]. For XRD measurement, cube-shaped specimens with the volume of 1 cm3 were prepared and each measuring side was processed by the UNSM treatment. The experimental parameters of the UNSM process are listed in Table . The XRD patterns of the Cu sample were measured from 30° to 140° and the residual stress was calculated at the {111} plane. The elastic lattice strains () of Cu were calculated using a diffraction peak shift, as follows:
(1)
(1) where
and
are the diffraction angles for the deformed and initial specimens, respectively [Citation22]. Then, the residual stress (
) in a biaxial plane stress condition was calculated as follows:
(2)
(2) where
is the elastic modulus and
is the Poisson’s ratio of the hkl plane [Citation23].
Nano indentation analysis was performed to analyse the local hardness and qualitative residual stress of the surface region in the cross-sections of the specimens. Only the completely grain-refined regions (0–30 µm below the surface) were investigated in this test.
To determine the global mechanical properties, tensile tests of whole samples were performed with dog-bone shaped specimens using a universal testing machine (Instron 1361, Instron Corp., Canton, USA). This was done at room temperature with a quasi-static strain rate of 1 × 10−3 s−1. The strain distributions on the specimens were accurately measured using digital image correlation (DIC) (ARAMIS v 6.1, GOM Optical Measuring Techniques, Germany) [Citation24].
Figure shows an optical microscopy (OM) image of a cross-section of the specimen after UNSM processing. Deformation was generated in a surface region ∼100 µm thick. To investigate only the residual stress effect on the tensile property of the UNSM-processed specimen, the microstructure of the UNSM + HT specimen had to be compared with the microstructure of the UNSM specimen. Hence, EBSD analyses on the initial specimen and deformed regions (∼100 µm deep) of the UNSM and UNSM + HT specimen surfaces were performed.
Figure shows the microstructure of the initial specimen and the microstructural evolution after UNSM and UNSM + HT treatment in the deformed region (∼0–100 µm below the surface). The average initial grain size measured using EBSD is 70 µm. The deformed region presents two visually distinct regions: completely and partially refined. The thickness of the completely refined UFG region was ∼30 µm from the surface after UNSM, which is the same as in the UNSM + HT specimen (Figure (b)). To provide more detail of the surface refinement, the completely refined regions (∼30 µm) of the UNSM and UNSM + HT specimens were analyzed using EBSD (Figure (c)). The grain sizes of the UFG regions after UNSM and after UNSM + HT were ∼2 µm. The fractions of high-angle boundary and low-angle boundary after UNSM were 0.387 and 0.325, respectively, and after UNSM + HT were 0.395 and 0.310, respectively, as shown in Table . The values of kernel average misorientation (KAM) angle related to the geometrically necessary dislocations were ∼0.6 both after UNSM and after UNSM + HT. This shows that low-temperature annealing did not influence on the dislocation density [Citation21]. Although the average grain size did not change during the HT, the thermally more unstable low-angle grain boundary decreased. Both of these results show that the use of HT to relieve residual stress hardly changed the microstructure of the UNSM-processed sample. It is worth mentioning here that the average grain size refined by UNSM can be in the range from several microns to several tens of nanometers. The finest grain was found to be about ∼40 nm depending on the UNSM parameters.
Figure 3. Inverse pole figure maps of the (a) Initial specimen, (b) Depth of ∼100 µm from the surface, and (c) Depth of ∼30 µm from the surface of the (1) UNSM and (2) UNSM + HT specimens.
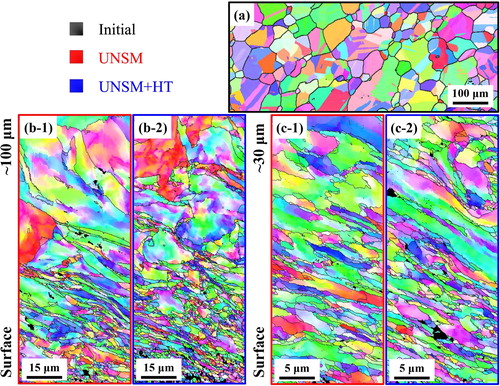
Table 2. Grain size and the fraction of high angle boundary and low angle boundary of the initial, UNSM, and UNSM + HT Cu specimens.
Figure shows the XRD and nano indentation experimental results of the initial, UNSM, and UNSM + HT specimens. The degree of grain refinement of the UNSM and UNSM + HT specimens was estimated using XRD peak broadening. The amount of compressive residual stress was calculated from the peak shift using Equations (1) and (2). The terms and
were taken from Ref. [Citation23]. The lattice strain and the compressive residual stress on the surface generated during UNSM were −0.00087 and 286 MPa, respectively, and, the generated stress was totally relieved by low-temperature stress relief annealing. The residual stress was measured on the top surface of the specimen. The UNSM treated specimens have gradient nano-grained structures on the surface. The gradient nano-grained structure has much higher yield strength in comparison to the coarse-grained counterpart [Citation4]. It has been reported that the measured grain size of the UNSM treated Cu-based alloy was in the rage of 40–100 nm at the top surface [Citation10]. By calculating the yield strength based on the Hall-Petch relationship between yield stress and grain size of pure Cu, the yield strength is estimated as ∼600 MPa [Citation25] and this value consistent with the previous result in Ref. [Citation4]. As a result, the measured residual stress values using XRD analysis can be verified. Some studies have also shown that the value of residual stress on the top surface of the UNSM treated samples is much bigger than the value of yield strength of the untreated UNSM samples [Citation11,Citation26].
Figure 4. (a) X-ray diffraction patterns obtained on the surface and (b) Nanoindentation load-displacement curves of the initial, UNSM, and UNSM + HT specimens.
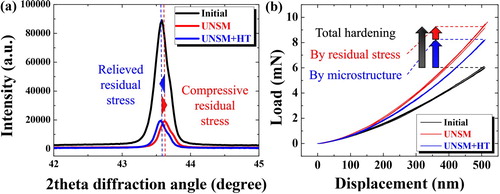
For the analysis of surface local properties, the nano indentation load-displacement curves of the initial, UNSM, and UNSM + HT specimens shown in Figure (b) were measured in the completely deformed region (∼30 µm below the surface). Because there was no microstructural difference between the UNSM and UNSM + HT specimens, the only difference between the two specimens was residual stress. The hardness of the initial specimen (1.96 GPa) increased to 2.62 GPa (increment after UNSM 2.62 − 1.96 = 0.66 GPa) after the UNSM process due to the combined effect of the microstructure (grain refinement) and compressive residual stress. The hardness of the UNSM + HT specimen decreased to 2.43 GPa. It should be noted that this amount of hardness decrement (2.62 − 2.43 = 0.19 GPa, ∼30% hardness increment) is due to the compressive stress relief effect and the remaining hardening (2.43−1.96 = 0.47 GPa, ∼70%) is from the microstructure effect. That is, the compressive residual stress contributed about 30% and the grain refinement contributed about 70%, to the increase in hardness of the UNSM-processed specimen. It should also be noted that this combined effect influences only the surface-grain-refined region, not the inner undeformed region.
Figure shows the tensile stress–strain curves (global mechanical property) of the initial, UNSM, and UNSM + HT specimens. While the nano indentation results (Figure ) represent the contributions of the residual stress and grain refinement to the strengthening of the surface local region, the tensile testing corresponds to the condition of the whole specimen (i.e. from the surface to the center). The yield strengths of the initial specimen, after UNSM, and after UNSM + HT are 84, 131, and 122 MPa, respectively. That is, the contributions of the surface grain refinement and residual stress to the increase of yield strength in UNSM were ∼80% (38 MPa) and ∼20% (9 MPa), respectively. The difference in strengths between the UNSM and UNSM + HT samples decreases with strain and approaches zero in ultimate tensile strength (UTS). The UTS of the initial, UNSM, and UNSM + HT specimens was 226, 233, and 233 MPa, respectively. The UTS increased about 3% after UNSM and was not changed by the stress relief heat treatment. This result shows that the compressive residual stress contributes initially to the enhanced global yield strength of the UNSM-processed Cu by ∼20%, and that the contribution decreases with strain within the uniform plastic deformation stage (see the yellow box region in Figure ). Because the dislocation density and strength in the severely deformed and grain-refined surface region are already saturated and no more strain hardening is occurring, the global UTSs of the UNSM and UNSM + HT samples become similar. Though the gauge length of the specimens is shorter than the ASTM E8 standard size, the gage length does not influence on the uniform elongation because we used accurate DIC for measuring strain. The sample size effect on tensile testing was clarified in Ref. [Citation27].
In addition to the effect from the fraction of the surface-grain-refined region, on the entire cross section of the specimen, the tensile strength of the UNSM specimen was higher than the simple rule-of-mixture strength due to additional strengthening by the strain gradient effect and heterogeneous structure effect [Citation1,Citation28]. Therefore, the contribution of residual stress is smaller in tensile strength than in nano hardness.
In summary, the separate effects of residual stress and surface grain refinement on the local nano hardness and global tensile properties of UNSM-processed material were investigated. Within the surface-grain-refined region of the specimen, the contribution of residual stress to hardening estimated using a nano indentation test was ∼30%. For the regions of surface ultrafine-grain and core coarse-grain, the contribution of residual stress to hardening that was estimated using tensile tests was ∼20% in yield strength. This gradually decreased to zero in the region of uniform deformation. In conclusion, it has been proven that the contribution of residual stress is not negligible when analyzing the mechanical behavior of UNSM-processed materials. The current conclusion also applies to surface-grain-refined, processed materials.
Disclosure statement
No potential conflict of interest was reported by the authors.
ORCID
Hyoung Seop Kim http://orcid.org/0000-0002-3155-583X
Additional information
Funding
References
- Park HK, Ameyama K, Yoo J, et al. Additional hardening in harmonic structured materials by strain partitioning and back stress. Mater Res Lett. 2018;6:261–267. doi: 10.1080/21663831.2018.1439115
- Kang JY, Kim JG, Kim HS. Outstanding mechanical properties of high-pressure torsion processed multiscale TWIP-cored three layer steel sheet. Scr Mater. 2016;123:122–125. doi: 10.1016/j.scriptamat.2016.06.009
- Lu K. Making strong nanomaterials ductile with gradients. Science. 2014;345:1455–1456. doi: 10.1126/science.1255940
- Fang TH, Li WL, Tao NR, et al. Revealing extraordinary intrinsic tensile plasticity in gradient nano-grained copper. Science. 2011;331:1587–1590. doi: 10.1126/science.1200177
- Arifvianto BS, Mahardika M. Effects of surface mechanical attrition treatment (SMAT) on a rough surface of AISI 316L stainless steel. Appl Surf Sci. 2012;258:4538–4543. doi: 10.1016/j.apsusc.2012.01.021
- Unal O, Varol R. Surface severe plastic deformation of AISI 304 via conventional shot peening, severe shot peening and repeening. Appl Surf Sci. 2015;351:289–295. doi: 10.1016/j.apsusc.2015.05.093
- Hohenwarter A. Incremental high pressure torsion as a novel severe plastic deformation process: processing features and application to copper. Mater Sci Eng A. 2015;626:80–85. doi: 10.1016/j.msea.2014.12.041
- Song Y, Chen M, Wang W, et al. Inhomogeneous deformation of interstitial free steel during the high pressure torsion process. Korean J Met Mater. 2017;55(10):710–715.
- Amanov A, Pyun YS, Sasaki S. Effects of ultrasonic nanocrystalline surface modification (UNSM) technique on the tribological behavior of sintered Cu-based alloy. Tribol. Int. 2014;72:187–197. doi: 10.1016/j.triboint.2013.12.003
- Amanov A, Cho IS, Kim DE. Effectiveness of high-frequency ultrasonic peening treatment on the tribological characteristics of Cu-based sintered materials on steel substrate. Mater. Design. 2013;45:118–124. doi: 10.1016/j.matdes.2012.08.073
- Amanov A, Cho I, Pyun Y. Microstructural evolution and surface properties of nanostructured Cu-based alloy by ultrasonic nanocrystalline surface modification technique. Appl Surf Sci. 2016;388:185–195. doi: 10.1016/j.apsusc.2016.01.237
- Chae J, Lee K, Amanov A. Gradient nanostructured tantalum by thermal-mechanical ultrasonic impact energy. Mater. 2018;11(3):452. doi: 10.3390/ma11030452
- Amanov A, Urmanov B, Amanov T, et al. Strengthening of Ti-6Al-4V alloy by high temperature ultrasonic nanocrystal surface modification technique. Mater Lett. 2017;196:198–201. doi: 10.1016/j.matlet.2017.03.059
- Khan MK, Fitzpatrick ME, Wang QY, et al. Effect of ultrasonic nanocrystal surface modification on residual stress and fatigue cracking in engineering alloys. Fatigue Fract Eng Mater Struct. 2018;41:844–855. doi: 10.1111/ffe.12732
- Kattoura M, Telang A, Mannava SR, et al. Effect of ultrasonic nanocrystal surface modification on residual stress, microstructure and fatigue behavior of ATI 718Pluas alloy. Mater Sci Eng A. 2018;711:364–377. doi: 10.1016/j.msea.2017.11.043
- Chen G, Gao J, Cui Y, et al. Effects of strain rate on the low cycle fatigue behavior of AZ31B magnesium alloy processed by SMAT. J Alloys Compd. 2018;735:536–546. doi: 10.1016/j.jallcom.2017.11.141
- Prabhakaran S, Kulkarni A, Vasanth G, et al. Laser shock peening without coating induced residual stress distribution, wettability characteristics and enhanced pitting corrosion resistance of austenitic stainless steel. Appl Surf Sci. 2018;428:17–30. doi: 10.1016/j.apsusc.2017.09.138
- Chen XH, Lu J, Lu L, et al. Tensile properties of a nanocrystalline 316L austenitic stainless steel. Scr Mater. 2005;52:1039–1044. doi: 10.1016/j.scriptamat.2005.01.023
- Wang YM, Wang K, Pan D, et al. Microsample tensile testing of nanocrystalline copper. Scr Mater. 2003;48:1581–1586. doi: 10.1016/S1359-6462(03)00159-3
- Herring DH. Stress relief. Wire Forming Technol Int. 2010;13:306–307.
- Kim JG, Yoon JI, Baek SM, et al. Residual stress effect on the delayed fracture of twinning-induced plasticity steels. Metall Mater Trans A. 2017;48A:2692–2696. doi: 10.1007/s11661-017-4056-3
- Oritz AL, Tian JW, Villegas JC, et al. Interrogation of the microstructure and residual stress of a nickel-base alloy subjected to surface severe plastic deformation. Acta Mater. 2008;56:413–426. doi: 10.1016/j.actamat.2007.10.003
- Tsuru T, Shibutani Y. Anisotropic effects in elastic and incipient plastic deformation under (001), (110), and (111) nanoindentation of Al and Cu. Phys Rev B. 2007;75:035415. doi: 10.1103/PhysRevB.75.035415
- Yoon JI, Kim JG, Jung JM, et al. Obtaining reliable true plastic stress-strain curves in a wide range of strains using digital image correlation in tensile testing. Korean J Met Mater. 2016;54:231–236. doi: 10.3365/KJMM.2016.54.4.231
- Hahn EN, Meyers MA. Grain-size dependent mechanical behavior of nanocrystalline metals. Mater Sci Eng A. 2015;646:101–134. doi: 10.1016/j.msea.2015.07.075
- Amanov A, Umarov R. The effects of ultrasonic nanocrystal surface modification temperature on the mechanical properties and fretting wear resistance of Inconel 690 alloy. Appl Surf Sci. 2018;441:515–529. doi: 10.1016/j.apsusc.2018.01.293
- Zhao YH, Guo YZ, Wei Q, et al. Influence of specimen dimensions on the tensile behavior of ultrafine-grained Cu. Scr Mater. 2008;59:627–630. doi: 10.1016/j.scriptamat.2008.05.031
- Wu X, Zhu Y. Heterogeneous materials: a new class of materials with unprecedented mechanical properties. Mater Res Lett. 2017;5:527–532. doi: 10.1080/21663831.2017.1343208