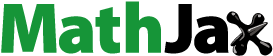
ABSTRACT
The present work reports a simple one-step powder metallurgy approach for producing bulk fine-grained Al2024 alloy with a unique harmonic structure and superior mechanical properties. The grain size of the bulk specimen could be easily manipulated by changing the initial powder size. Tensile test suggested that the yield strength of the fine-grained specimen with an average grain size of 3.78 µm (powder size ∼20 µm) was about 265 MPa, which was three times higher than that of the conventional coarse-grained counterpart, maintaining a good ductility (total elongation ∼15%). The reasons for the unique microstructure and the enhanced mechanical properties were discussed.
GRAPHICAL ABSTRACT
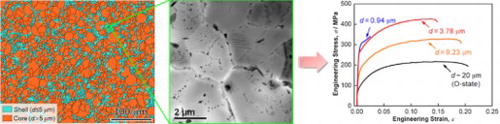
IMPACT STATEMENT
Bulk Al alloy with a unique ‘harmonic structure' and enhanced mechanical properties was successfully fabricated by a simple one-step powder metallurgy approach using gas atomized powders.
1. Introduction
Aluminum (Al) alloys are widely used in aerospace and transportation fields as structural component, achieving significant environmental and economic benefits. However, Al alloys have been challenged by titanium alloys and magnesium alloys recently, because both materials are either stronger or lighter than those of Al alloys. Therefore, there has been a strong demand for further improve the mechanical properties of Al alloys, especially enhancing their strength without significant sacrificing of their ductility [Citation1–3].
According to the well-known Hall–Petch relationship [Citation4,Citation5], grain refinement is considered as a promising way to strengthen metallic materials without changing their chemical composition. The techniques for realizing ultra-grain refinement can be broadly divided into two categories: a so-called up-to-bottom approach, such as severe plastic deformation (SPD), or a so-called bottom-to-up approach, such as consolidation of mechanical milled powders.
SPD can produce bulk defect-free ultrafine-grained (UFG) or nanocrystalline (NC) metals [Citation6–8]. However, the UFG/NC structures produced by SPD are thermodynamically unstable, owing to the high amount of free energy stored in the grain boundaries [Citation9]. Moreover, the bulk UFG/NC metals usually have deformed microstructures, so they always exhibit quite limited ductility due to the difficulty for dislocation accumulation [Citation10].
Powder metallurgy (P/M) is an alternative way to produce bulk metals with refined microstructure, which can greatly reduce the amount of used metals compared to other metal removal processes, thereby resulting in lower costs [Citation11–13]. P/M approach usually includes two steps: mechanical milling (MM) and hot consolidation. MM is an important procedure to realize ultra-grain refinement. However, undesired contaminations are introduced during the MM process, which may reduce the interfacial bonding strength between powder particles, resulting in very poor ductility of the bulk materials under tension test. In contrast, Le et al. [Citation14] have shown that it was possible to fabricate bulk UFG (grain size smaller than 1 µm) or fine grained (FG, grain size 1–5 µm) pure Al specimens by a simple one-step P/M route, namely, skipping the MM step. Due to the pinning effect of the thin oxide film on the Al powder surface, the grain sizes of the sintered samples were very close to the initial powder particle sizes. That means, the grain size of bulk specimen could be easily adjusted just by tailoring the initial powder size. But the situation might be different in Al alloys, probably due to the addition of various alloying elements. However, up to now, the feasibility of this one-step P/M approach in widely used commercial Al alloys has not been verified yet.
Consequently, the present work seeks to address this gap and investigate the effect of initial powder size on the microstructure and mechanical properties of bulk specimen. Commercial Al–Cu–Mg alloy (Al2024) powders with different average particle sizes were selected as the starting materials.
2. Experimental
Commercial gas-atomized Al2024 alloy powders with average particle size of ∼1 µm (fine powder), ∼20 µm (medium powder) and ∼50 µm (coarse powder) in diameter were used as the starting materials (see Figure S1). The detailed chemical composition of the powders is listed in Table S1. The powders were directly provided for consolidation using SPS without MM. A multi-step sintering program proposed by Le et al. [Citation14] was adopted. Microstructures of the powders and bulk alloys were characterized using scanning electron microscopy (SEM), X-ray diffraction (XRD), electron backscattering diffraction (EBSD) and transmission electron microscopy (TEM), etc. The mechanical properties of the bulk samples were characterized by room temperature tensile test. Due to space limitation, experimental details are described in Supplemental Information (also see Figure S2).
3. Results and discussion
Figure shows microstructure of the bulk samples consolidated from powders with different particle sizes. Figure (a) is a typical SEM image of the bulk sample consolidated from the fine powder. Although the sintering temperature (600°C) has been very close to the melting point of Al, some sub-micro-sized pores could be still clearly observed, as indicated by the white arrows [Citation15]. In contrast, dense alloy could be obtained by sintering the medium powder at a much lower temperature (500°C). As shown in Figure (c), powder particles bonded well with each other and detectable pores could not be found. Additionally, some very fine intermetallic phases (white particles) were presented along the particle boundaries and inside the powder particles. They are probably Al–Cu or Al–Cu–Mg phase formed during cooling process after SPS [Citation16]. Phase composition of bulk samples was analyzed by XRD. As shown in Figure (b,d), besides the strong diffraction peaks of Al, some weak peaks correspond to Al2Cu (θ-phase) and Al2O3 phases could also be observed. The Al2Cu phase is one of the most commonly observed second phases in Al–Cu–Mg alloys and it was probably precipitated out during the cooling process after sintering. The Al2O3 phase may result from the thin oxide film naturally covered on the surface of the gas-atomized Al powders. The microstructure of the bulk sample consolidated from the coarse powder is similar to that of the bulk sample sintered from medium powder (not shown here).
Figure 1. (a and c) SEM micrographs and (b and d) XRD patterns of bulk samples consolidated from (a and b) fine and (c and d) medium powders.
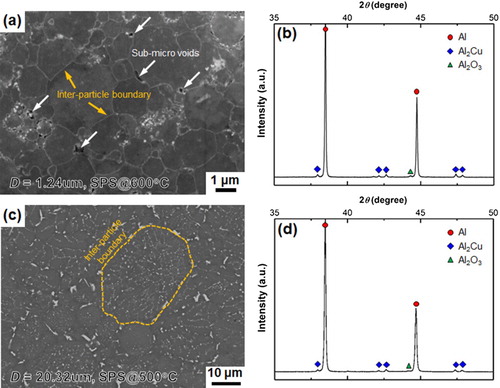
Figure shows the EBSD results of the sintered bulk samples. For each sample, inverse pole figure (IPF) map, grain boundary (GB) map, grain size distribution histogram and (001) pole figure (PF) are presented. Generally, all the samples exhibited recrystallized microstructures. As shown in the upper row (Figure (a–d)), bulk sample consolidated from the fine powder was filled by equiaxed grains. Most of the grains were surrounded by high angle grain boundaries (HAGBs), with the fraction of HAGBs greater than 90% and an average misorientation angle (θave.) of 34.9° (see Figure S3(a)). The average grain size is approximately 0.94 µm (UFG specimen, hereafter), which is very close to the initial powder size. The similarity between grain size and powder size indicates that grain boundary migration during SPS was inhibited by the thin oxide film naturally covered on the surface of the powder particles. For the bulk sample consolidated from the medium powder (Figure (e–h)), fully recrystallized grains with a mean grain size of 3.78 µm (FG specimen, hereafter) is observed, which is much finer than the initial powder size. In fact, the boundary of the powder particles could still be distinguished. For example, a spherical powder particle (red broken line) in the middle of the IPF map contains more than 20 grains, and the grains close to the powder surface are smaller than the inner ones, which is believed to be due to the faster cooling rate of the outer region during gas-atomization process. The bulk sample consolidated from the coarse powder exhibited a mean grain size of 9.23 µm (CG specimen hereafter), which is also much smaller than the initial powder size. In addition, the average misorientation angles of the FG specimen (θave. = 29.0o) and the CG specimen (θave. = 24.9o) are lower than that of the UFG specimen (Figure S3), which is due to the presence of some low angle grain boundaries (LAGBs) inside of the powder particles. Note that all the samples show nearly random crystallographic texture, as indicated from the colorful IPF maps (Figure (a, e, i)) and (001) pole figures (Figure (d, h, l)).
Figure 2. (a, e, and i) Inverse pole figure (IPF) maps, (b, f, and j) grain boundary (GB) maps, (c, g, and k) grain size distribution histograms and (d, h, and i) (001) pole figures (PF) of bulk samples prepared from (a–d) fine, (e–h) medium and (i–l) coarse powders, respectively.
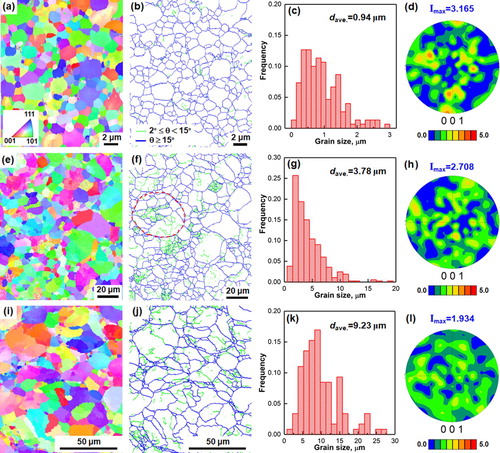
In order to provide insight into the excellent thermal stability of the microstructure obtained in the bulk specimens, scanning transmission electron microscopy (STEM) EDS analysis was conducted on the UFG and the FG specimens. For each specimen, bright field STEM image, high angle annular dark field (HAADF) image and corresponding EDS elemental mapping results are presented. As shown in Figure (a,b), sub-micro sized particles distributed densely along the powder boundaries. During pressure-assisted sintering process, the spherical powders underwent a certain degree of plastic deformation (known from the polygonal grains), and thus the continuous oxide film covered on the surface of the powder particles was disintegrated into very fine particles [Citation17]. However, due to the insufficient plastic strain, the disintegrated oxide particles remained on the particle boundaries and accordingly continued to act as effective diffusion barrier to the inter-particle diffusion of aluminum atoms, resulting in UFG microstructure as well as relative weak interparticle bounding strength. The corresponding EDS elemental mapping results (Figure (c)) reflect that powder boundaries are rich in Mg and O. In addition, a micron-sized Cu rich particle (probably Al2Cu phase) is presented in the trip-junction of several Al powders.
Figure 3. (a and d) STEM micrographs, (b and e) HAADF micrographs and (c and f) corresponding EDS elemental mapping results of bulk samples prepared from (a–c) fine and (d–f) medium powders, respectively.
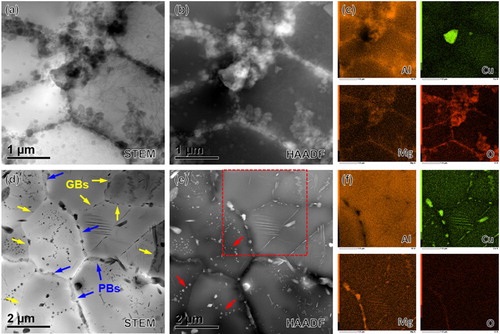
Figure (d–f) display STEM-EDS results of the FG specimen. As shown in Figure (d), the thin and sharp boundaries are grain boundaries (GBs), whereas the thick and fuzzy boundaries correspond to original powder boundaries (PBs), as indicated by yellow and blue arrows, respectively. Moreover, a large number of granular (mean diameter ∼100 nm) and acicular precipitates (mean length ∼400 nm) are observed. These precipitates are located not only along various type of boundaries but also distributed in the form of chains in the grain interior (see the red arrows in Figure (e)). EDS elemental mapping results (Figure (f)) of the boxed region in Figure (e)) demonstrated that these precipitates are rich in Cu and Mg, which are in good agreement with the XRD result shown in Figure (d). These nano-sized particles could effectively pin the original grain boundaries in the as-atomized polycrystalline powders and inhibit grain boundary migration during SPS, resulting in FG microstructure in the bulk sample. It is also worth mentioning that the oxygen content of the FG specimen should be much lower than that of the UFG specimen, and only slight enrichment of oxygen could be confirmed along original powder boundaries, as indicated by the very low contrast of the oxygen EDS map. Consequently, extensive sintering could be achieved even at relative low temperature (500°C).
The bulk samples were subjected to room temperature tensile test (Figure ). For comparison purpose, stress–strain curves of conventional hot rolled and annealed (O-state) Al2024 plate with an average grain size of approximately 20 µm were also provided [Citation18]. For the UFG specimen (d = 0.94 µm), the yield strength (YS) and ultimate tensile strength (UTS) were 294 and 340 MPa, respectively. The YS was almost 3.5 times higher than that of the conventional O-state specimen (YS ∼84 MPa). However, it fractured just after yielding, resulting in a total tensile elongation (EL) of only 2.6%. We believe the limited tensile ductility of the UFG specimen was caused by the residual pores and the oxide enriched particles distributed along powder boundaries. The YS, UTS and EL of the FG specimen (d = 3.78 µm) were 265, 425 MPa and 15.0%, respectively. The YS was more than three times higher than that of the O-state specimen and without significant sacrificing of tensile ductility. The EL of the CG specimen (19.2%) was even better than that of the FG specimen, however, the YS was only 160 MPa, which is much lower than that of the FG specimen. Thus, it is clear that the FG specimen exhibited the best combination of strength and ductility among all the specimens.
Figure 4. (a) Typical engineering stress–strain curves and (b) work-hardening rate curves of UFG, FG, CG and conventional O-state Al2024 alloy specimens. Tensile fracture surfaces of (c) UFG and (d) FG specimens. The insets in (c) and (d) were enlarged view of the boxed regions.
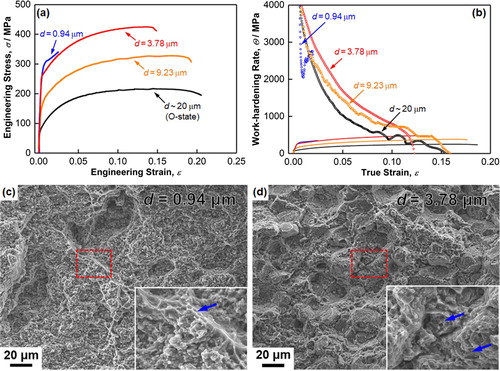
The uniform elongation is an important parameter for engineering materials, and it is determined by Considére criterion [Citation19] shown below:
(1)
(1) where σ is the true stress and ε is the true strain. Based on the Considére criterion, the work-hardening rate,
of the present specimens was plotted as a function of the true strain in Figure (b). The intersection point between the work-hardening rate curve and the true stress curve should be the point of plastic instability, i.e. the uniform elongation. For the O-state specimen, the work-hardening rate decreased monotonically with the increase of the strain, resulting in a uniform tensile elongation of 13.5% (in true strain). In case of the UFG specimen, the work-hardening rate firstly decreased quickly down to a value of ∼2000 MPa, and then recovered to ∼2800 MPa. The unique change of work-hardening rate corresponds to the yield drop phenomena in stress–strain curve, which is due to the lack of initial mobile dislocations in fully recrystallized UFG microstructure [Citation20,Citation21]. However, the specimen fractured abruptly at a true strain of 2.1% before the plastic instability point. As shown in Figure (c), only limited dimple patterns (indicated by blue arrow) are observed in the fracture surface of the UFG specimen, which is consistent with the poor ductility obtained in the tensile test. For the FG specimen, the work-hardening rate decreased monotonically with the increase of true strain, and it was always higher than that of the O-state specimen at any given strain. However, due to the very high true stress level of the FG specimen, the plastic instability point was achieved at a true strain of 11.7%, which was quite comparable with that of the O-state specimen. Moreover, the fracture surface (see Figure (d)) of the FG specimen was covered by a high number density of dimples with a mean dimple size of about 1–3 µm, which is strong evidence of ductile failure. The work-hardening rate of the CG specimen was located between those of the O-state plate and the FG specimen. However, due to the relatively low strength of the CG specimen, the intersection point for plastic instability (uniform elongation) was achieved at a true strain of 14.4%.
To reveal the underlying mechanisms for the enhanced work-hardening rate in the FG specimen, a large area EBSD scan (300 µm * 500 µm) was further performed on this specimen. The light blue and orange grains in Figure (a) correspond to ‘shell grains’ with grain sizes smaller than 5 µm (mean grain size ∼2.38 µm) and ‘core grains’ with grain sizes larger than 5 µm (mean grain size ∼9.96 µm), respectively. Note that the FG specimen consists of a peculiar microstructure wherein the ‘shell grains' areas form a nearly interconnected 3D network surrounding ‘core grains' regions, which are distributed periodically. This typical microstructure is referred as ‘harmonic structure', which was firstly proposed and realized by Ameyama et al. [Citation22,Citation23]. Due to the difference in strength between the ‘shell grains' and the ‘core grains', deformation incompatibility is generated at the interface regions during plastic deformation. Thus, geometrically necessary dislocations (GNDs) are required to accommodate the strain gradient, which will generate long-range back stress near the interfaces, and thereby producing additional back stress work-hardening [Citation24–26]. Moreover, the present ‘harmonic structure' could promote uniformity of deformation when compared with conventional random bimodal structure, leading to suppressed strain localization and relatively larger uniform elongation [Citation22]. In addition, we believe that the finely dispersed nano-precipitates (Figure (d–f)) could pin mobile dislocations during plastic deformation, thereby contributing to the enhanced work-hardening rate. Since Al2024 alloy is a typical age-hardenable alloy, the mechanical properties of the FG specimen can be further optimized through subsequent T6 (solid solution + artificial aging) treatment.
4. Conclusion
In summary, UFG, FG and CG Al2024 alloys were successfully fabricated by direct consolidation of gas-atomized powders. The FG Al2024 alloy consolidated from the medium powder exhibited the best combination of strength and ductility among all the specimens. The excellent thermal stability of the FG structure was due to the pinning effect of the finely dispersed precipitates. The superior mechanical properties were associated with back stress hardening and dislocation pinning effect, originating from the unique ‘harmonic structure’ as well as the high number density of fine precipitates, respectively. This simple one-step approach can be easily scaled up or applied to other metallic materials, and therefore has great potential for the future practical applications.
Disclosure statement
No potential conflict of interest was reported by the authors.
ORCID
Additional information
Funding
References
- Liddicoat PV, Liao XZ, Zhao Y, et al. Nanostructural hierarchy increases the strength of aluminium alloys. Nature Commun. 2010;1:63. doi: 10.1038/ncomms1062
- Zhao YH, Liao XZ, Cheng S, et al. Simultaneously increasing the ductility and strength of nanostructured alloys. Adv Mater. 2006;18(17):2280–2283. doi: 10.1002/adma.200600310
- Ma K, Wen H, Hu T, et al. Mechanical behavior and strengthening mechanisms in ultrafine grain precipitation-strengthened aluminum alloy. Acta Mater. 2014;62:141–155. doi: 10.1016/j.actamat.2013.09.042
- Hall EO. The deformation and ageing of mild steel: III discussion of results. Proc Phys Soc London B. 1951;64:747–753. doi: 10.1088/0370-1301/64/9/303
- Petch NJ. The cleavage strength of polycrystals. J Iron Steel Inst. 1953;174:25–28.
- Zhilyaev AP, Langdon TG. Using high-pressure torsion for metal processing: fundamentals and applications. Prog Mater Sci. 2008;53:893–979. doi: 10.1016/j.pmatsci.2008.03.002
- Valiev RZ, Langdon TG. Principles of equal-channel angular pressing as a processing tool for grain refinement. Prog Mater Sci. 2006;51:881–981. doi: 10.1016/j.pmatsci.2006.02.003
- Tsuji N, Saito Y, Lee SH, et al. ARB (Accumulative Roll-bonding) and other new techniques to produce bulk ultrafine grained materials. Adv Eng Mater. 2003;5:338–344. doi: 10.1002/adem.200310077
- Kumpmann A, Günther B, Kunze HD. Thermal stability of ultrafine-grained metals and alloys. Mater Sci Eng A. 1993;168:165–169. doi: 10.1016/0921-5093(93)90722-Q
- Meyers MA, Mishra A, Benson DJ. Mechanical properties of nanocrystalline materials. Prog Mater Sci. 2006;51:427–556. doi: 10.1016/j.pmatsci.2005.08.003
- Gutmanas EY. Materials with fine microstructures by advanced powder-metallurgy. Prog Mater Sci. 1990;34:261–366. doi: 10.1016/0079-6425(90)90003-R
- Suryanarayana C. Mechanical alloying and milling. Prog Mater Sci. 2001;46:1–184. doi: 10.1016/S0079-6425(99)00010-9
- Zheng R, Sun Y, Xiao W, et al. Nanostructured Al87Ni8.5Ce3Fe1Cu0.5 alloy prepared by mechanical milling spark plasma sintering and hot extrusion. Mater Sci Eng A. 2014;606:426–433. doi: 10.1016/j.msea.2014.03.119
- Le GM, Godfrey A, Hansen N. Structure and strength of aluminium with sub-micrometer/micrometer grain size prepared by spark plasma sintering. Mater Des. 2013;49:360–367. doi: 10.1016/j.matdes.2013.01.018
- Dirras G, Gubicza J, Tingaud D, et al. Microstructure of Al-Al2O3 nanocomposite formed by in situ phase transformation during Al nanopowder consolidation. Mater Chem Phys. 2011;29:846–852. doi: 10.1016/j.matchemphys.2011.05.022
- Zheng R, Sun Y, Ameyama K, et al. Optimizing the strength and ductility of spark plasma sintered Al 2024 alloy by conventional thermo-mechanical treatment. Mater Sci Eng A. 2014;590:147–152. doi: 10.1016/j.msea.2013.10.017
- Kwon H, Park DH, Park Y, et al. Spark plasma sintering behavior of pure aluminum depending on various sintering temperatures. Met Mater Int. 2010;16(1):71–75. doi: 10.1007/s12540-010-0071-2
- Zheng R, Bhattacharjee T, Shibata A, et al. Effect of accumulative roll bonding (ARB) and subsequent aging on microstructure and mechanical properties of 2024 Al Alloy. Mater Trans. 2016;57(9):1462–1470. doi: 10.2320/matertrans.MH201512
- Dieter GE. Mechanical metallurgy. New York: McGraw-Hill; 1986. p. 289.
- Gao S, Bai Y, Zheng R, et al. Mechanism of huge lüders-type deformation in ultrafine grained austenitic stainless steel. Scr Mater. 2019;159:28–32. doi: 10.1016/j.scriptamat.2018.09.007
- Zheng R, Bhattacharjee T, Shibata A, et al. Simultaneously enhanced strength and ductility of Mg-Zn-Zr-Ca alloy with fully recrystallized ultrafine grained structures. Scr Mater. 2017;131:1–5. doi: 10.1016/j.scriptamat.2016.12.024
- Vajpai SK, Ota M, Zhang Z, et al. Three-dimensionally gradient harmonic structure design: an integrated approach for high performance structural materials. Mater Res Lett. 2016;4(4):191–197. doi: 10.1080/21663831.2016.1218965
- Park HK, Ameyama K, Yoo J, et al. Additional hardening in harmonic structured materials by strain partitioning and back stress. Mater Res Lett. 2018;6(5):261–267. doi: 10.1080/21663831.2018.1439115
- Yang M, Pan Y, Yuan F, et al. Back stress strengthening and strain hardening in gradient structure. Mater Res Lett. 2016;4(3):145–151. doi: 10.1080/21663831.2016.1153004
- Wu XL, Jiang P, Chen L, et al. Synergetic strengthening by gradient structure. Mater Res Lett. 2014;2(4):185–191. doi: 10.1080/21663831.2014.935821
- Wu X, Jiang P, Chen L, et al. Extraordinary strain hardening by gradient structure. Proc Natl Acad Sci. 2014;111(20):7197–7201. doi: 10.1073/pnas.1324069111