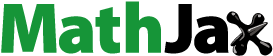
ABSTRACT
This paper reports on a heterogeneous-structured β-Ti alloy with an exceptional combination of high strength and ductility, resulting from optimized hierarchical features in a lamellar microstructure. The microstructure is achieved by controlling a fraction of coarse/fine domains, spatial grain-size distribution, and different types of grain boundaries. The large degree of microstructural heterogeneity leads to obvious mechanical incompatibility and strain partitioning during plastic deformation. In addition, experimental results demonstrate that the unique heterogeneous structure induces high hetero-deformation induced hardening and promotes dislocation accumulation, thereby achieving a high yield strength ∼970 MPa and uniform tensile elongation of ∼16%.
GRAPHICAL ABSTRACT
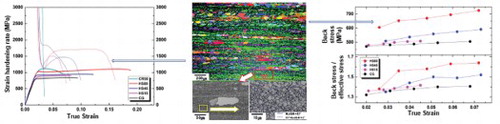
IMPACT STATEMENT
Microstructural heterogeneities can induce inhomogeneous deformation behavior, which leads to steep strain gradients, and consequently the potential to achieve enhanced strength-ductility synergy.
Despite very attractive combinations of low Young’s modulus, high ductility, and superior fatigue resistance, the translation of metastable β-Ti alloys into commercial applications has been mainly hindered by the relative low strength, compared to conventional α- and α + β Ti alloys [Citation1]. With progress in attaining a high level of strength, a prominent approach has been considered for strengthening mechanisms, particularly exploiting precipitation hardenability to utilize dispersed nano-sized secondary α′′ and/or ω phases through aging heat treatments [Citation1,Citation2]. However, as newly designed alloys, an intrinsic drawback of the thermo-mechanical processes is the conventional trade-off dilemma: the substantial improvement in strength by brittle secondary phases inevitably brings about a drastic loss of ductility and a significant increase of Young’s modulus, which is adverse for structural- and bio-applications [Citation3]. Thus, a new strategy for imparting strengthening, while still preserving large ductility and acceptable Young’s modulus in metastable β-alloys is fairly needed.
In recent years, many research efforts have been devoted to the design of distinct microstructures consisting of heterogeneous structures to overcome the strength-ductility trade-off dilemma. Examples include producing harmonic structures with micrometer-sized grains surrounded by ultrafine grains [Citation4–6], generating spatially grain-size gradient microstructures [Citation7–11], designing heterogeneous materials with large-sized lamella domains embedded into a matrix of ultrafine grains [Citation12,Citation13], and other complex hierarchical structures [Citation14,Citation15]. The resulting materials, with the heterogenous features, have exhibited remarkable strength-ductility enhancement compared to their homogeneous counterparts. According to the extensive study on underlying deformation behavior, the intentional microstructural heterogeneity can induce steep stress and strain gradients across domain interfaces, which is beneficial towards a synergy between high strength and high ductility [Citation10,Citation13–15]. Therefore, an efficient strengthening and effective strength-ductility synergy are expected by deploying heterogeneous microstructure in metastable β-Ti alloys, which has previously received little attention.
Recently, Wu et al. [Citation16] have suggested that an exceptional improvement in the strength-ductility synergy could be accomplished by introducing microstructural lamella, such as 30 vol% soft lamella grains embedded in a hard matrix. In addition, a study on a grain size dependent harmonic structure [Citation5] reveals deformation incompatibility is required for the generation of geometrically necessary dislocation (GND), contributing to abnormally high strain hardening, especially when the structural/strain gradient is large. Consequently, the mechanical behaviors in heterogeneous-structured materials are strongly related to microstructural heterogeneity, for stimulating local non-homogeneous plasticity during plastic deformation. Owing to a lack of controllable processing variables, however, the design strategy to control the spatial distribution of coarse/fine grains and optimize their volume fraction is limited [Citation7,Citation16].
The aim of this study is to develop the desired heterogeneous microstructure through microstructural design optimization, so as to achieve an optimized strength-ductility synergy in a metastable Ti alloy. The various microstructural heterogeneities are effectively introduced by cold-rolling and annealing of a pre-twinned Ti–23Nb–0.7Ta–2.0Zr–1.0O(at%) Gum Metal. The newly designed Gum Metal combining lamella and hierarchical features exhibits a superior combination of strength and ductility compared to its homogenous counterpart, based on hetero-deformation induced hardening by imparting stress and/or strain partitioning.
The Ti–23Nb–0.7Ta–2.0Zr–1.0O(at%) Gum Metal alloys were fabricated by arc-melting under an argon atmosphere from pure raw materials Ti, Nb, Ta, Zr and TiO2, followed by a homogenization treatment at 1000°C for three hours, and subsequent water cooling (Figure S1(a)). The homogenized alloy was processed by a thermomechanical-cyclic method to form a pre-twinned microstructure (Figure S1(b)). The twinned Ti–Nb-based Gum Metal was used for processing heterogeneous microstructures. Detailed processing history and mechanical properties of the starting material and pre-twinned Gum Metal have been reported previously [Citation17]. For the next step, the heterogeneous structure was effectively introduced by cold-rolling to 85%, followed by annealing at 690°C. The heavily twin-dominated microstructure reverted back to recrystallized grains during the post annealing treatment (Figure S2). More importantly, twinning-mediated plastic deformation could control the important parameters of heterogeneous geometries, such as grain size, volume fractions between coarse grains and fine grains, and a spatial distribution of lamella structures. As a result, distinct microstructures combining various fractions of coarse-grained and fine-grained regions, can be obtained through the relatively sluggish recrystallization kinetics (detailed behavior during post-deformation annealing is explained in the Supplementary material). In this study, three heterogeneous-structured Gum Metals have been prepared, and are denoted as HS80, HS45 and HS15 with the number denoting the fraction of fine-grained domains (refer to Figure S3(a) for variations of coarse-grain/fine-grain area fraction as a function of annealing time, and the corresponding phase constitution shown in Figure S3(b)).
The heterogeneous microstructures were characterized by a Thermo-Fisher Apreo FEG-SEM equipped with an Oxford Instruments EBSD-Symmetry detector. Standard dog-bone shaped specimens, with the gage dimensions of 20 mm × 2 mm × 1 mm, were subjected to uniaxial tensile tests and loading-unloading-reloading (LUR) tensile tests with an initial strain rate of 5 × 10−4 s−1 (tensile direction parallel to the rolling direction).
Similar to the near-ideal heterogeneous microstructure schematically presented in ref. [Citation16], the tailored Gum Metals clearly exhibits microstructural heterogeneity with three types of grains at multiple length scales, as depicted in Figures and S4. The macro-EBSD image of the HS80, Figure (a), illustrates a typical heterogeneous lamella geometry with a specific spatial distribution of coarse-grained and fine-grained domains. In Figure (b), a magnified view of the black box in Figure (a), the coarse grains, which comprise an area fraction of ∼23% soft regions, (see Figure S3(a)), are embedded in the fine-grained lamella matrix, wherein a pronounced bimodality is seen (Figure (d)). Due to a large grain size (average size is approximately 78 µm), these regions will be referred to as coarse grains, and other structures will be referred to as fine- and/or ultrafine-sized grains, all with size of <14 µm in width. An enlarged microstructure of the fine-grain domain, indicated as the yellow box in Figure (b), is presented in Figure (c).
Figure 1. (a) EBSD map of the HS80 Gum Metal and (b) magnified image quality (IQ) map of the black box. (c) A magnified map of the fine-grained domain (in the yellow box). (d) The grain size distributions of the HS80 sample and the fine-grained domain (shown in the inset).
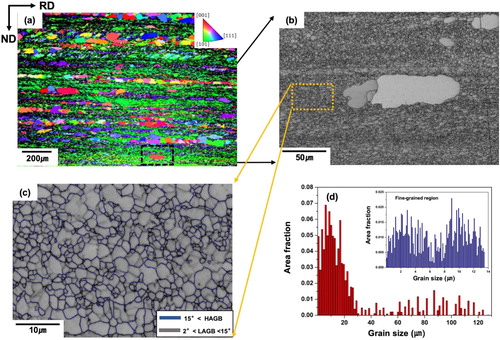
The fine-grain regions are grouped as two types of grains with various size ranging from 0.1 to 14 µm (the inset of Figure (d)): fully recrystallized grains with ultrafine-size (all with a size ∼2 µm) and partially recrystallized grains including subgrain boundaries (LAGB: 2∼15°) are with fine scales ranging from 2 to 14 µm. Therefore, it can be expected a coupling effect due to the size difference and inhomogeneous dislocation density after partially recrystallization in the small grain domains, leading to the significantly scattered strength values between the recrystallized zones and partial recrystallized zones [Citation13,Citation18]. Note that the partially recrystallized grains dramatically decrease with increasing annealing time and are hardly observable in HS45 and HS15 samples (Figure S4). Concurrently, the HS80 sample is a unique heterogeneous microstructure composed of lamella and hierarchical features, which are expected to provide a wide range of microstructural heterogeneity across multiple length scales in the Gum Metal.
Figure shows the tensile properties of three heterogeneous-structured Gum Metals with distinct microstructures, and the results are summarized in the inset Table. To highlight the enhancement in the strength-ductility synergy achieved by the heterogeneous microstructure design, the curves of 90% cold-rolling labeled (CR90) and its fully annealing state (CG, grain size in ∼73 µm) are also included. The microstructural engineering of severely deformed microstructure by cold-rolling results in the CG sample with plastic instability that develops immediately after yielding, along with higher yield strength (YS) and ultimate tensile strength (UTS). In contrast, heterogeneous-structured Gum Metals exhibit a good combination of high strength and high ductility. Note that the relatively poor ductility of the HS15 specimen, compared to that of the CG sample, can be affected by a formation of thermally induced α′′ phase during the relatively long annealing process [Citation18] (see Figure S3b).
Figure 2. (a) True strain–stress curves where the inset table represents measured values of the mechanical properties; UTS and EFT are obtained from Engineering strain–stress curves (Figure S5). (b) Strain hardening rate curves as function of true strain. (c) The loading-unloading-reloading behavior of the HS80 and homogeneous coarse-grained samples. (d) hetero-deformation induced stress and ratio of hetero-deformation induced stress and effective stress values obtained from the LUR test.
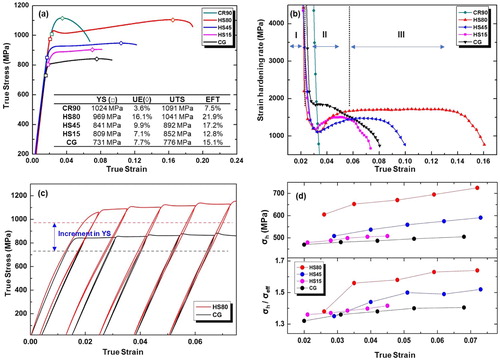
As compared to the homogenous coarse-grained sample, an extraordinary strength-ductility synergy is observed in the HS80 sample, as evidence by the abnormally high tensile strength (YS: 969 MPa and UTS: 1041 MPa) and ductility (total elongation (ETF): 21.9% and uniform elongation (UE): ∼16.1%). Interestingly, heterogeneous-structured samples show a yield drop at the onset of plastic deformation, followed by a transient deformation stage, seen in Figure (a). The strain transition results in an up-turn in the strain hardening rate (SHR, Figure (b)), wherein strain hardening rate drops rapidly first (region I), then finally reaches its maximum (region II). By comparison with the coarse-grained Gum Metal (1.0 at.% O), the double-yielding observed in heterogeneous-structured samples mainly originates from the inherited microstructural heterogeneity as widely reported in heterostructured materials [Citation15]. Moreover, the HS80 sample shows a remarkable feature of strain-hardening-rate retention over a wide strain range (region III), leading to excellent tensile ductility [Citation8]. A high strain hardening capability is thus essential to evade the typical strength-ductility trade-off. The experimental results imply that the intentional microstructural heterogeneity is key to achieving high strength and high ductility in metastable Ti alloys, resulting from enhanced stable plastic flow, thus enhancing the strength-ductility synergy.
To prove the peculiar mechanical behavior of heterogeneous-structured samples, loading-unloading-reloading (LUR) tensile tests have been performed (Figures (c) and S6(a)). The tests were conducted in the strain range of uniform elongation. The flow stress can be divided into the hetero-deformation induced stress associated with the forward motion of dislocations, and the effective stress required locally for activating dislocation sources [Citation19], seen in Figure S6(b). Hence, it is significant to estimate the effect of the hetero-deformation induced stress on strain hardening during plastic deformation. It should be noted that the hetero-deformation induced stress is composed of back-stress developed in soft domains and forward stress mainly induced by the back-stress in hard domains, which affects the mechanical behavior in heterogeneous structure [Citation20]. Figure (d) displays the values of hetero-deformation induced stress () and the ratio of hetero-deformation induced stress to effective stress (
/
), estimated by the method reported in Ref. [Citation13]. The hetero-deformation induced stress of heterogeneous-structured samples near the yield point is much higher than that of the homogeneous coarse-grained sample. It is apparent that to trigger yielding, additional external stress needs to be supplied to move dislocations, so that yield strength would be enhanced by as much as the hetero-deformation induced stress contributes, particularly producing the back-stress in soft domains.
Figure 3. EBSD analysis of deformation microstructures in the homogeneous coarse-grained (a, c) and heterogenous-structured (b, d, e) samples with a strain of 0.05: (a), (b) IPF maps and (c), (d) the corresponding KAM maps. (e) A magnified KAM map of the heterostructured sample.
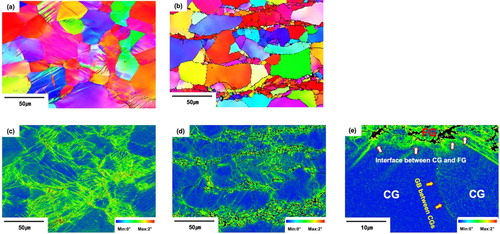
Furthermore, the high hetero-deformation induced stress leads to enhancement in the strain hardening capability, attributed to strain partitioning originated from strain gradients between hard and soft domains [Citation5,Citation11–13,Citation20]. With increasingly higher applied strain, the hetero-deformation induced stress of the HS80 sample increases linearly, showing a pronounced enhancement compared to the HS15, HS45 and homogeneous coarse-grained samples. The ratio, /
, is indicative of the contribution of hetero-deformation induced stress to flow stress, and illustrates that the influence of hetero-deformation induced stress is much higher than the effective stress over the entire plastic range. It is evident that the strain gradient would be larger with ongoing deformation, especially when microstructural inhomogeneity increases in the materials. Generally, the back stress to offset the applied stress is accompanied by pile-ups of GNDs in soft domains of hetero-structured materials [Citation12,Citation20–22]. Therefore, this indicates that the GND densities would be higher in the HS80, which is necessary for the high flow stress, and consequently enhancing the strain hardening rate with an increase in overall plastic strain in the sample.
Figure presents the deformation microstructures of the homogeneous coarse-grained and heterogeneous-structured Gum Metal samples using Kernel Average Misorientation (KAM) maps, where the average grain sizes are approximately 73 and 67 µm, respectively. Drastic changes in the microstructure features are apparent at a strain of 0.05. The EBSD micrograph of the homogeneous coarse-grained sample, Figure (a), shows that deformation-induced features are visible in a few grains, as intragranular bands with different orientations. Note that the deformation bands are characterized with misorientations of ∼50.5°, which correspond to {332} < 113 >β twins as the primary deformation mechanism of a Ti–Nb Gum Metal [Citation1]. Meanwhile, no mechanical twins are observed for heterogeneous-structured sample with uniform deformation as shown in Figure (b). Based on the knowledge of the nucleation of twins at grain boundaries, it is believed that accommodation of back stresses at interfaces such as coarse-grain/fine-grain boundaries could inhibit twinning formation in coarse-grained domains by increasing the activation energy for twin nucleation [Citation4]. Figure (c) presents the local misorientation of the deformed coarse-grain sample (KAM values are higher at higher strain), showing that strain localization is associated with extensive deformation twinning, leading to poor tensile ductility. Conversely, the mechanical response of the heterogeneous-structured Gum Metal is preceded by non-localized plastic strain, shown in Figure (d). There is little evidence for stress concentrations and well-distributed strains are observed, wherein plastic strains are enhanced mainly near interfaces separating coarse-grain/fine-grain domains. The designed structural heterogeneities therefore promote a higher degree of uniformity of deformation, which contributes to sustained strain hardening to large strains (uniform elongation values).
In Figure (e), higher KAM values are seen adjacent to the interface between different domains compared to that of the grain boundary between coarse-sized grains. The partial recrystallized fine grains show little residual stress before loading (Figure S7). Since the high KAM values are indicators of local lattice distortion and strain energy within the grain, this is clear evidence of strain partitioning caused by the strain gradient between coarse-grain and fine-grain domains, which results in the production of GNDs in the soft domains [Citation5,Citation14,Citation20,Citation22]. Such pile-ups in GNDs is a unique characteristic of heterogeneous materials, leading to strain hardening not only by generating long-range back stress, but also by creating obstacles to further slip [Citation16,Citation21,Citation23]. In this regard, the excellent strength-ductility synergy achieved in the heterogeneous-structured Gum Metal originates from the plastic incompatibilities that arise from non-homogeneous plastic deformation induced by strength heterogeneity between different domains.
Finally, we analyzed the distribution of GND density in the heterogeneous microstructure, which can experimentally verify the local back stress strengthening mechanism. With a tensile test interrupted prior to the yield point of the HS45, the quantification of GNDs was performed using the obtained EBSD orientation data (Figure (a)) [Citation24]. The calculated values of the grain average GND density versus grain area (see Figure S8) is given in Figure (b). It is found that the high-density data lies primarily within the fine-grain regions, whereas the relatively low GND density is seen in the coarse-grain region. Hence, there exist huge heterogeneities in microstructure and resulting difference in mechanical responses with different grain sizes. Specifically, the soft coarse-grain would deform plastically more than the hard, fine grain. This plastic instability requires excess GNDs to maintain material continuity in the coarse grain, which enables the soft grains to harden to the level of the fine grains, thus increasing yield strength [Citation9,Citation20,Citation21]. It was also reported that, under uniaxial loading condition, the evolution of incompatible deformation can induce multiaxial stress among neighbor grains, which promote the interaction between GNDs and mobile dislocations [Citation10]. As an important consequence, the multiaxial stress is related, not only to extra strength through forest hardening [Citation22], but to additional ductility through the activation of new slip systems (cross-slip mechanisms) [Citation10,Citation21]. Consequently, significant microstructural heterogeneity, related to spatial grain size distribution and high interface density, leads to local non-homogeneous plastic deformation, creating long-range back stresses due to GNDs serving as a significant strain hardening mechanism. This overall effect results in abnormally high strength and an extraordinary strength-ductility synergy in Ti-Nb Gum Metal with a heterogeneous microstructure.
Figure 4. (a) EBSD micrograph of the HS45 sample and (b) Grain average GND density (log m–2) plotted against grain area (log m2) with each data point colored according to the order of magnitude of grain average density.
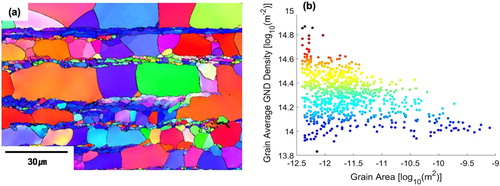
In summary, a new methodology to design a heterogeneous microstructure, with twin-structured Gum Metal, enables manipulation of microstructural heterogeneity by controlling the fraction of coarse grains/fine grains involving lamella and hierarchical features. The heterogeneous-structured Gum Metal, containing approximately 80% hard matrix, exhibits a remarkable strength-ductility enhancement, compared to its coarse-grain counterpart, as well as other heterogeneous-structured Gum Metals. Based on the previous results, it suggests that huge heterogeneities in microstructure induce large stress and strain gradients due to plastic incompatibility between soft and hard domains, leading to an outstanding combination of strength and ductility in metastable Ti alloys.
Supplemental Material
Download MS Word (1.7 MB)Disclosure statement
No potential conflict of interest was reported by the authors.
ORCID
Kenneth S. Vecchio http://orcid.org/0000-0003-0217-6803
Additional information
Funding
References
- Banerjee D, Williams JC. Perspectives on titanium science and technology. Acta Mater. 2013;61:844–879. doi: 10.1016/j.actamat.2012.10.043
- Gao J, Knowles AJ, Guan D, et al. Ω phase strengthened 1.2 GPa metastable β titanium alloy with high ductility. Scr Mater. 2019;162:77–81. doi: 10.1016/j.scriptamat.2018.10.043
- Kuroda D, Niinomi M, Morinaga M, et al. Design and mechanical properties of new β type titanium alloys for implant materials. Mater Sci Eng A. 1998;243:244–249. doi: 10.1016/S0921-5093(97)00808-3
- Dirras G, Ueda D, Hocini A, et al. Cyclic shear behavior of conventional and harmonic structure-designed Ti-25Nb-25Zr β-titanium alloy: back-stress hardening and twinning inhibition. Scr Mater. 2017;138:44–47. doi: 10.1016/j.scriptamat.2017.05.033
- Park HK, Ameyama K, Yoo J, et al. Additional hardening in harmonic structured materials by strain partitioning and back stress. Mater Res Lett. 2018;6:261–267. doi: 10.1080/21663831.2018.1439115
- Zheng R, Li G, Zhang Z, et al. Manipulating the powder size to achieve enhanced strength and ductility in harmonic structured Al alloy. Mater Res Lett. 2019;7:217–224. doi: 10.1080/21663831.2019.1580621
- Vajpai SK, Ota M, Zhang Z, et al. Three-dimensionally gradient harmonic structure design: an integrated approach for high performance structural materials. Mater Res Lett. 2016;4:191–197. doi: 10.1080/21663831.2016.1218965
- Fu Z, MacDonald BE, Zhang D, et al. Fcc nanostructured TiFeCoNi alloy with multi-scale grains and enhanced plasticity. Scr Mater. 2018;143:108–112. doi: 10.1016/j.scriptamat.2017.09.023
- Wu XL, Jiang P, Chen L, et al. Synergetic strengthening by gradient structure. Mater Res Lett. 2014;2:185–191. doi: 10.1080/21663831.2014.935821
- Wu X, Jiang P, Chen L, et al. Extraordinary strain hardening by gradient structure. Proc Natl Acad Sci. 2014;111:7197–7201. doi: 10.1073/pnas.1324069111
- Lei C, Deng X, Li X, et al. Simultaneous enhancement of strength and ductility through coordination deformation and multi-stage transformation induced plasticity (TRIP) effect in heterogeneous metastable austenitic steel. Scr Mater. 2019;162:421–425. doi: 10.1016/j.scriptamat.2018.12.007
- Zhang C, Zhu C, Harrington T, et al. Design of non-equiatomic high entropy alloys with heterogeneous lamella structure towards strength-ductility synergy. Scr Mater. 2018;154:78–82. doi: 10.1016/j.scriptamat.2018.05.020
- Wu X, Yang M, Yuan F, et al. Heterogeneous lamella structure unites ultrafine-grain strength with coarse-grain ductility. Proc Natl Acad. Sci. 2015;112:14501–14505. doi: 10.1073/pnas.1517193112
- Shukla S, Choudhuri D, Wang T, et al. Hierarchical features infused heterogeneous grain structure for extraordinary strength-ductility synergy. Mater Res Lett. 2018;6:676–682. doi: 10.1080/21663831.2018.1538023
- Wei Y, Li Y, Zhu L, et al. Evading the strength–ductility trade-off dilemma in steel through gradient hierarchical nanotwins. Nat Commun. 2014;5:3580–3588. doi: 10.1038/ncomms4580
- Wu X, Zhu Y. Heterogeneous materials: a new class of materials with unprecedented mechanical properties. Mater Res Lett. 2017;5:527–532. doi: 10.1080/21663831.2017.1343208
- Shin S, Zhu C, Vecchio KS. Observations on {332}< 113 > twinning-induced softening in Ti-Nb Gum metal < 113 > twinning-induced softening in Ti-Nb Gum metal. Mater Sci Eng A. 2018;724:189–198. doi: 10.1016/j.msea.2018.03.062
- Hao YL, Niinomi M, Kuroda D, et al. Young’s modulus and mechanical properties of Ti-29Nb-13Ta-4.6Zr in relation to α” martensite. Metall Mater Trans A. 2002;33:3137–3144. doi: 10.1007/s11661-002-0299-7
- Feaugas X. On the origin of the tensile flow stress in the stainless steel AISI 316L at 300K: back stress and effective stress. Acta Mater. 1999;14:3617–3632. doi: 10.1016/S1359-6454(99)00222-0
- Zhu Y, Wu X. Perspective on hetero-deformation induced (HDI) hardening and back stress. Mater Res Lett. 2019;7:393–398. doi: 10.1080/21663831.2019.1616331
- Ma E, Zhu T. Towards strength–ductility synergy through the design of heterogeneous nanostructures in metals. Mater Today. 2017;20:323–331. doi: 10.1016/j.mattod.2017.02.003
- Ashby MF. The deformation of plastically non-homogeneous materials. Philos Mag. 1970;21:399–424. doi: 10.1080/14786437008238426
- Gao HJ, Huang YG. Geometrically necessary dislocation and size-dependent plasticity. Scr Mater. 2003;48:113–118. doi: 10.1016/S1359-6462(02)00329-9
- Zhu C, Harrington T, Livescu V, et al. Determination of geometrically necessary dislocations in large shear strain localization in aluminum. Acta Mater. 2016;118:383–394. doi: 10.1016/j.actamat.2016.07.051