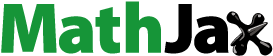
Abstract
Heterogeneous cellular structure combined with bimodal grain structure contributed to the high hetero-deformation-induced (HDI) stress in selective laser melted 316L stainless steel (SLMed 316L SS) and high grain boundary density at molten pool boundaries and thick cellular boundaries inside grains both acted as hard domains. However, the HDI hardening rate caused by cellular boundary was lower compared with the traditional grain boundary due to its weaker dislocation motion resistance. Under high deformation, massive deformation-induced twins penetrated the cellular boundary and distorted its configuration; therefore, grain boundary heterogeneity dominated the overall HDI stress in SLMed 316L SS after large deformation.
GRAPHICAL ABSTRACT
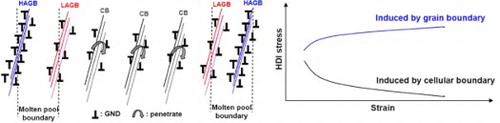
Impact statement
Heterogeneous cellular structure combined with bimodal grain structure contributed to the high hetero-deformation-induced stress in additively manufactured 316L SS, the former effect was lower compared to the latter.
1. Introduction
Hetero-structured materials are defined as materials containing domains with substantial different flow stresses and the soft parts can be plastically deformed while the hard parts are still under elastic condition [Citation1,Citation2]. During the plastic deformation process, geometrically necessary dislocation (GND) gliding in the soft parts will be accumulated at the elastic/plastic domain boundaries and the piling-up of GNDs at the boundary can produce long-range internal stress, i.e. back stress in the soft parts, which turns the soft parts become stronger the stress concentration at the head of the piling-up GNDs exerts strong forward stress in the adjacent hard parts at the same time. This additional stress would also increase the strain hardening rate to some extent. Therefore, Hetero-structured materials, such as heterogeneous lamella materials [Citation3], harmonic structure [Citation4], dual-phase alloys [Citation5], laminated materials [Citation6] and composites [Citation7], have been confirmed to have an excellent combination of strength and ductility. More recently, Zhu et al. [Citation8] re-visited this kind of back stress as a hetero-deformation-induced (HDI) stress more accurately.
The additively manufactured components were also widely characterized as a heterogeneous structure caused by the non-uniform temperature gradients during the fast-melting and solidification process [Citation9,Citation10]. During the laser melting, an evident localized laser spot creates a steep thermal gradient between the center and edge of the molten pool, combining with the attendant Marangoni convection, causing different temperature gradients at various regions inside the molten pool and thereby different grain and cellular sizes [Citation11]. Comprehensive literature revealed that the widely existed sub-micro cellular structures were enriched in dislocations and decorated by segregated elements or precipitates at the boundaries, and numerous experiments have confirmed that the cellular structures can result in substantial effects on the mechanical properties of additively manufactured parts, especially the increase in yield strength [Citation12]. This sort of heterogeneous structure in additively manufactured parts would also undergo an HDI stress effect under plastic deformation, however, remains comparatively less-explored. Chen et al. [Citation13] revealed that there existed a higher compressive yield strength compared with the tensile yield strength for the selective laser melted 316L stainless steel (SLMed 316L SS), which was attributed to the development of substantial HDI stresses. Wang et al. [Citation14] calculated that the HDI stress for SLMed 316L SS at ∼3.3% strain was about 300 MPa, nearly half of the total strength at this strain level. However, they did not give a detailed investigation of the underlying reasons for the high HDI stress, especially the intragranular HDI stress arising from the heterogeneous cellular structure inside the grains.
In our work, 316L SSs were fabricated by a selective laser melting method and the loading–unloading–reloading tensile test was conducted to investigate the HDI stress effect, the related microstructure evolution for the SLMed 316L SS was characterized via electron backscatter diffraction (EBSD) and electron channeling contrast imaging (ECCI) measurements. We hope this result can provide a factual basis for future understanding of the HDI stress issue in additively manufactured parts.
2. Experimental details
2.1. Materials and microstructure
The as-built SLMed 316L SSs with a relative density of higher than 99.95% were produced by EOS M290 and the detailed printing parameters were described in our previous works [Citation15]. To avoid or alleviate the effect of printing residual stress, all samples were heat-treated under 300°C for 1 h and cooled in the air. Samples were mechanical ground with a series of SiC papers up to 4000# and then polished using diamond suspension with particle size down to 1 µm together with 40 nm colloidal SiO2 polishing suspension. Finally, the polished samples were ultrasonically cleaned in an acetone bath for 30 min. EBSD data were recorded under 25 kV high voltage with a working distance of 17.00 mm in a TESCAN MIRA 3 scanning electron microscope (SEM); the scanning step size was 1 µm and the kernel average misorientation (KAM) calculation was based on the first nearest kernel with perimeter only. ECCI measurements were conducted with an acceleration voltage of 20 kV and a beam intensity of 16 nA with an 8.00 mm working distance under optimized diffraction conditions. The morphology of cellular structure was characterized using transmission electron microscopy (TEM, FEI Tecnai G2 F20).
2.2. Loading–unloading–reloading test
The uniaxial loading–unloading–reloading tensile experiment was carried out using the Gatan MTEST2000 micro-mechanical testing system and the strain evolution was captured using digital image correlation and analyses via a GOM software. The loading rate was set as 0.1 mm/min and the unloading force was set as 30 N, respectively. The dog bone sample was prepared by electrical discharge machining with 1 mm in thickness, with a gauge length of 6.5 mm and a gauge width of 2.5 mm, respectively. Specimens were ground sequentially with emery papers down to 2000# grit and the tensile direction was vertical to the building direction of the printed samples.
3. Results and discussion
The laser scanning strategy and the typical molten pool morphology were illustrated in Figure (a1,a2), and in our work, the distance between the nearby scanning paths was 80 µm and the powder layer thickness was 25 µm, respectively. The molten pool boundaries can be clearly observed from the metallographic morphologies (Figure (a3,a4)), and the grain can grow across the molten pool boundary from the side view. Due to the various thermal gradients inside the molten pool, a heterogeneous microstructure was formed and periodically distributed according to the scanning pattern. As we can see from the inverse pole figure (IPF) and image quality (IQ) results (Figure (b1)), small grains with an average grain size of 26 µm mainly generated along the molten pool boundaries and big grains (∼58 µm) existed at the molten pool interiors, this resulted into a typical bimodal grain structure (Figure (b4)). This bimodal grain structure was also found on the xoz plane (same on yoz plane) for the SLMed 316L SS (Figure (c1–c4)) and the grain in this plane was elongated along the building direction. The total length of LAGB (2–15°) was larger than that of the HAGB (15–63°) on both the xoy and xoz planes, making a substantial contribution to material strength. As for a comparison, the grain size for commercial wrought 316L SS was relatively uniform with an average size of 51 µm and there were few LAGBs in the material (Figure (d1–d4)).
Figure 1. (a1) The printing strategy for the selective laser melting process and (a2) typical molten pool morphology. The metallographic morphologies of (a3) xoy plane and (a4) xoz plane; EBSD results of the SLMed 316L SS on xoy plane: (b1) IPF + IQ, (b2) HAGB, (b3) LAGB and (b4) grain size, respectively; EBSD results of the SLMed 316L SS on xoz plane: (c1) IPF + IQ, (c2) HAGB, (c3) LAGB and (c4) grain size, respectively; EBSD results of the commercial 316L SS: (d1) IPF + IQ, (d2) HAGB, (d3) LAGB and (d4) grain size, respectively.
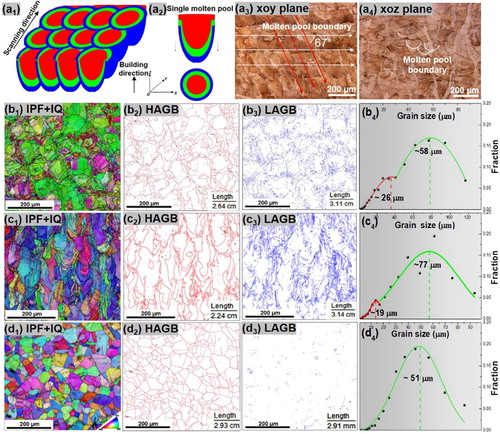
The widely distributed cellular structure can be seen in the etched SLMed 316L SS (Figure 2(a)) and there were also some typical boundaries near the molten pool boundary. From the ECCI combined with EBSD results (Figure (b1–b3)), it can be confirmed that the LAGB is a kind of cellular boundary but with high misorientation, while the HAGB is much straight and not a kind of cellular boundary. The thickness ratio between cellular boundary and the cellular interior was around 1:10 (Figure (b4)), and the cellular boundary was enriched of dislocation and also decorated with Cr and Mo enrichment as confirmed in our previous results [Citation16]. The origin of the cellular structure can be explained as follows: the high thermal gradient and crystal growth rate ratio during the fast solidification decided its cellular shape [Citation9], and the high density of dislocations at the cellular boundaries was attributed to the compression-tension cycles rendered by the localized heating/cooling heterogeneity upon laser scanning [Citation17]. After 1.5% deformation (Figure (c1–d2)), the slip band penetrated the cellular boundary, but the propagation direction did not change across the normal cellular boundary. In contrast, the direction changed around 10° when across the cellular boundary with high misorientation (namely LAGB), which indicated that the LAGB had a higher pinning effect for dislocation motion compared with the normal cellular boundary (Figure S1). Moreover, these slip bands can be entirely stopped by HAGB, indicating a strong resistance to dislocation [Citation18]. Liu et al. [Citation19] confirmed that the blocking ability of the normal cellular boundary in SLMed 316L SS is weaker than that of typical grain boundaries in terms of the strengthening effect. Recently, Fang et al. [Citation20] also confirmed that high misorientation at the boundary between the soft and hard domains was more effective in developing HDI hardening in a heterogeneous brass. Figure (e) displayed the schematic illustration of local shear stress across the normal cellular boundary, LAGB and HAGB, respectively. The higher the shear stress was, the higher the GND density would be generated to accommodate the strain incompatibility across these boundaries (Figure (f)). Meanwhile, it should be noted that the LAGB and HAGB were consistently distributed near the molted pool boundaries, which led to a heterogeneous structure at a grain size scale. Thus, this HDI stress in SLMed 316L SS should be ascribed to the heterogeneous cellular structures, and heterogeneous LAGB and HAGB distribution.
Figure 2. (a) SE image of the etched SLMed 316L SS, (b1) ECCI result of the cellular structure, (b2) GB distribution for this region, (b3) enlarged area in (b1), (b4) TEM result of the cellular structure; EBSD results of the 1.5% deformed SLMed 316L SS: (c1) IPF + IQ and (c2) GB distribution; (d1) SE image and (d2) ECCI result of the marked area in (c1); (e) schematic illustration of local shear stress across the normal cellular boundary, LAGB and HAGB, respectively, (f) compensation of shear strain mismatch at different boundaries by GNDs.
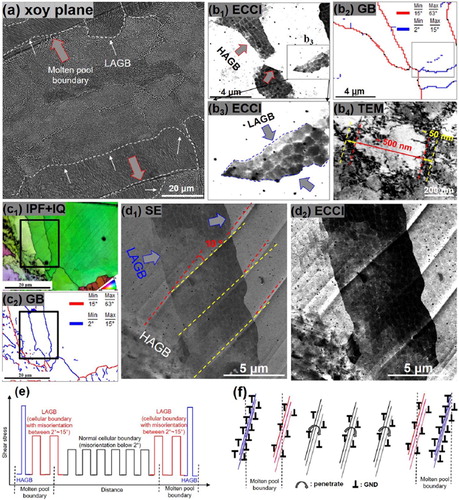
There was a large loop area in the loading–unloading–reloading test for the SLMed 316L SS (Figure (a)), indicating a higher HDI stress compared with the commercial counterpart. The method to calculate the HDI stress in this work was adopted referred to Yang et al. [Citation21]:
where
is the HDI stress,
is the reloading yield stress,
is the unloading yield stress, and detailed calculation was shown in Figure S2. The HDI stress value for the SLMed 316L SS was much higher than the commercial counterpart at any strain levels (Figure (b)), the residual heat stress should be small in our case since stress-relief heat treatment was conducted for all the samples [Citation13]. Moreover, the HDI stress and flow stress ratio was also large for the SLMed 316L SS even it deserved a high yield strength, especially near the yielding point (Figure (c)). The initial high HDI stress at around 2% deformation could be attributed to the fast GND accumulation rate at the cellular boundary at small strain since it needed a very short distance for GND to accumulate at the cellular boundary. At the same time, it required more strain for GND to accumulate at the GB, and this led to an evident gap for the HDI stress and flow stress ratio at the initial deformation stage. However, the increasing rate for HDI stress for the SLMed 316L SS was lower than the commercial counterpart, which indicated the HDI hardening rate was low for the SLMed 316L SS, and this was consistent with the result in Figure (e) that the strain hardening rate of the SLMed 316L SS was not higher at any strains compared with the commercial 316L SS with only the grain size effect. This further indicated that the HDI hardening rate caused by cellular boundary was lower than that of the traditional GB. For the weak HDI hardening rate of the cellular structure, one reason might be that there was a weak accommodation ability of GND at the cellular boundary compared with GB. As illustrated in Figure (f), the Burgers vector direction of the GNDs for each side of the cellular boundary was opposite and the dislocations would penetrate across the cellular boundary under appropriate external force, they will be consequently annihilated and as a result, lead to the decrease of GND density. Similar results were also found in SLMed AlSi10Mg alloy that the exhaustion rate of mobile dislocation was higher than that of heat-treated counterparts lacking cellular structures during deformation [Citation22]. However, this was different from the result of the nano-grain materials, in which traditional GB has a strong resistance to the motion of glissile dislocations [Citation23].
Figure 3. (a) The loading–unloading–reloading curves for the SLMed and commercial 316L SSs, (b) HDI stress and effective stress evolution with the strain and (c) HDI stress and flow stress ratio evolution with the strain for the SLMed and commercial 316L SSs, respectively. The engineering strain stress curve (d) and strain hardening rate (e) for the SLMed and commercial 316L SSs, respectively.
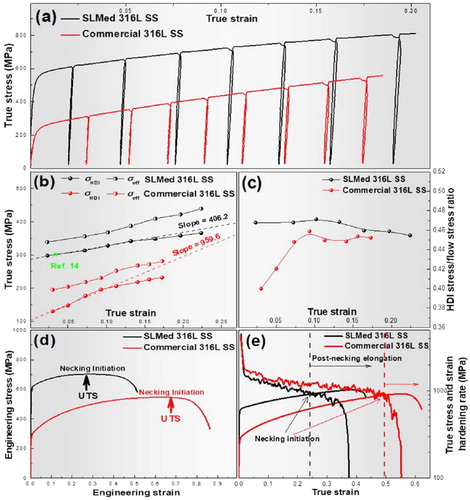
Another reason might be that nano-twins can initiate from and penetrate the cellular boundaries, which distorted their configuration [Citation19]. In this case, the massive deformation-induced twin boundaries dominated the resistance of dislocation motion, which in turn weakened the cellular boundary’s effect. The deformation twining can provide additional strain hardening rate, however, the gap of strain hardening rate after about 25% deformation became bigger (Figure (e)). This was attributed to the early crack initiation around the oxides in the SLMed 316L SS, and a large number of cracks would compromise the strength during deformation, mitigating the strain hardening rate to some extent [Citation24].
At a low strain level, individual slip band can be generated and the cellular boundary can be still visible while increasing the strain level up to 5% (Figure (a1,a2)), while a high density of nano-twin embryos was produced under 20% deformation in Figure (a3). At higher strain levels, grain boundary heterogeneity dominated the overall HDI stress; the GND density increased more significantly for the SLMed 316L SS after 20% deformation compared with the commercial counterpart and the GNDs mainly distributed near the molten pool boundaries (Figure (b1–b4)). More evident results were shown in Figure (d1,d2), where the GND enriched at the small grain region around the big grain and the deformation-induced twins inside the big grain occurred to sustain the stain incompatibility across the boundaries. For the commercial 316L SS with uniform grain size, GND density was relatively low and thus provided a low HDI stress eventually (Figure (c1–c4)). However, the HDI stress and flow stress ratio after large deformation for these two materials became close, which also suggested that the GB heterogeneity dominated the overall HDI stress effect after large deformation.
Figure 4. ECCI results of SLMed 316L SS under different deformation levels: (a1) 1.5%, (a2) 5% and (a3) 20%, respectively. EBSD results of the 20% deformed SLMed 316L SS: (b1) IPF + IQ, GND distribution (b2) before and (b3) after deformation, and (b4) related GND density, respectively. EBSD results of the 20% deformed commercial 316L SS: (c1) IPF + IQ, GND distribution (c2) before and (c3) after deformation, and (c4) related GND density, respectively. Enlarged region marked in (b1): (d1) IPF + IQ, (d2) GND + IQ, (d3) misorientation profile along the line in (d1).
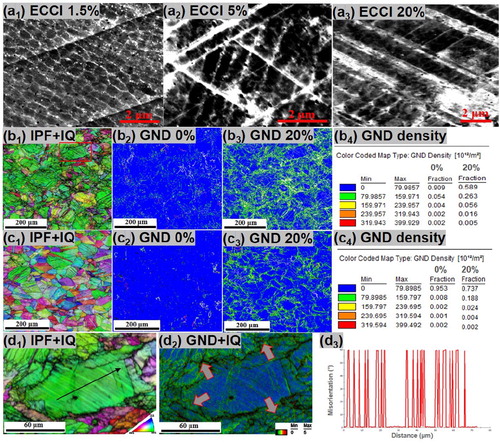
4. Conclusions
Heterogeneous structure widely existed in additively manufactured metals and alloys due to its complex thermal history, the loading–unloading–reloading test combined with the microstructural characterization methods were conducted in this work to investigate the HDI stress and the main conclusions can be drawn as follows:
High density of grain boundaries at the molten pool boundary and thick cellular boundary (∼50 nm) acted as hard domains in this heterogeneous structure, both of them contributed to the high HDI stress in SLMed 316L SS.
The HDI hardening rate caused by cellular structure was lower than that of the traditional GB due to its weak GND accommodation, and GND can penetrate the cellular boundary and annihilate with the opposite dislocations.
Under large deformation, massive deformation-induced twins penetrated the cellular boundary and distorted its configuration in SLMed 316L SS, which weakened the HDI stress caused by cellular boundary and GB heterogeneity dominated the overall HDI stress after large deformation.
Disclosure statement
No potential conflict of interest was reported by the author(s).
Additional information
Funding
References
- Ma E, Wu X. Tailoring heterogeneities in high-entropy alloys to promote strength-ductility synergy. Nat Commun. 2019;10(1):1–10.
- Wu XL, Zhu YT. Heterogeneous materials: a new class of materials with unprecedented mechanical properties. Mater Res Lett. 2017;5(8):527–532.
- Wu XL, Yang MX, Yuan FP, et al. Heterogeneous lamella structure unites ultrafine-grain strength with coarse-grain ductility. Proc Natl Acad Sci USA. 2015;112(47):14501–14505.
- Park HK, Ameyama K, Kim HS. Additional hardening in harmonic structured materials by strain partitioning and back stress. Mater Res Lett. 2018;6(5):261–267.
- Delince M, Brechet Y, Embury JD, et al. Structure-property optimization of ultrafine-grained dual-phase steels using a micro structure-based strain hardening model. Acta Mater. 2007;55(7):2337–2350.
- Ma XL, Huang CX, Moering J, et al. Mechanical properties of copper/bronze laminates: role of interfaces. Acta Mater. 2016;116:43–52.
- Wei SL, Huang L, Li X. Network-strengthened Ti-6Al-4V/(TiC+ TiB) composites: powder metallurgy processing and enhanced tensile properties at elevated temperatures. Metal Mater Trans A. 2019;50(8):3629–3645.
- Zhu YT, Wu XL. Perspective on hetero-deformation induced (HDI) hardening and back stress. Mater Res Lett. 2019;7(10):393–398.
- Kou S. Welding metallurgy. New Jersey: Wiley; 2003.
- Wei SL, Huang LJ, Chang J. Primary phase growth and microstructure evolution of rapidly solidifying ternary Ti-12Al-8V alloy. Mater Lett. 2016;175:291–295.
- Li Z, He B, Guo Q. Strengthening and hardening mechanisms of additively manufactured stainless steels: the role of cell sizes. Scripta Mater. 2020;177:17–21.
- Smith TR, Sugar JD, Schoenung JM. Strengthening mechanisms in directed energy deposited austenitic stainless steel. Acta Mater. 2019;164:728–740.
- Chen W, Voisin T, Zhang Y, et al. Microscale residual stresses in additively manufactured stainless steel. Nat Commun. 2019;10:1–10.
- Wang YM, Voisin T, McKeown JT, et al. Additively manufactured hierarchical stainless steels with high strength and ductility. Nat Mater. 2018;17(1):63–69.
- Kong D, Ni X, Dong C. Bio-functional and anti-corrosive 3D printing 316L stainless steel fabricated by selective laser melting. Mater Design. 2018;152(5):88–101.
- Kong D, Ni X, Dong C, et al. Heat treatment effect on the microstructure and corrosion behavior of 316L stainless steel fabricated by selective laser melting for proton exchange membrane fuel cells. Electrochim Acta. 2018;276:293–303.
- Wang G, Ouyang H, Fan C. The origin of high-density dislocations in additively manufactured metals. Mater Res Lett. 2020;8(8):283–290.
- Guo Y, Collins DM, Tarleton E, et al. Measurements of stress fields near a grain boundary: exploring blocked arrays of dislocations in 3D. Acta Mater. 2015;96:229–236.
- Liu LF, Ding QQ, Zhong Y, et al. Dislocation network in additive manufactured steel breaks strength-ductility trade-off. Mater Today. 2018;21(4):354–361.
- Fang XT, He GZ, Zheng C, et al. Effect of heterostructure and hetero-deformation induced hardening on the strength and ductility of brass. Acta Mater. 2010;186:644–655.
- Yang MX, Pan Y, Yuan FP, et al. Back stress strengthening and strain hardening in gradient structure. Mater Res Lett. 2016;4(3):145–151.
- Li Z, Li Z, Tan Z, et al. Stress relaxation and the cellular structure-dependence of plastic deformation in additively manufactured AlSi10Mg alloys. Int J Plasticity. 2020;127:102–111.
- Wu XL, Jiang P, Chen L, et al. Extraordinary strain hardening by gradient structure. Proc Natl Acad Sci USA. 2014;111(20):7197–7201.
- Lou X, Andresen PL, Rebak RB. Oxide inclusions in laser additive manufactured stainless steel and their effects on impact toughness and stress corrosion cracking behavior. J Nucl Mater. 2018;499:182–190.