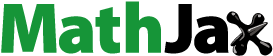
Abstract
In this study, Al matrix composites (AMCs) reinforced with few-layered MXene (FLM) were fabricated for the first time using self-assembly protocol and powder metallurgy. Individual FLM platelets, which decorated the grain boundaries without structural degradation, were singly incorporated into the Al matrix. The interfacial load transfer was considerably increased due to the generation of strong anchors at the FLM–Al interface via Al phase infiltration under densification. Consequently, the addition of 0.26 vol.% FLM considerably increased the composite strength by approximately 66%. This work demonstrated the effective application of MXene as a 2D reinforcement for AMCs towards high-specific-strength materials.
GRAPHICAL ABSTRACT
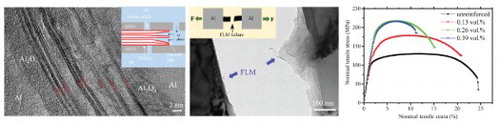
IMPACT STATEMENT
This work demonstrated for the first time, the potential application and significant strengthening effect of 2D MXene in Al matrix composites.
1. Introduction
High-performance and lightweight materials are integral components of most energy and environmental sustainability strategies, which are the hallmark of modern society [Citation1]. Al matrix composites (AMCs) are high-performance lightweight materials, which have attracted increasing attention for improving the energy efficiency in various applications such as automotive, marine, packaging, electronic, and aerospace industries, owing to their high specific strength, superior thermal and electrical conductivities, and cost-effective properties [Citation2]. Various reinforcement such as ceramic particles [Citation3–7], carbon nanotubes (CNTs) [Citation8–13], graphene [Citation14–20], and refractory metals [Citation21,Citation22], have been extensively studied and incorporated into AMCs over the past two decades. Among reinforcement, graphene is considered as the best filler due to its extremely high electrical conductivity, Young's modulus, and strength [Citation20]. For instance, the addition of 0.3 wt.% graphene platelets (GPLs) can improve the ultimate tensile strength (UTS) of AMCs by ∼60% compared to pure Al [Citation20]. Furthermore, when AMCs are doubly reinforced with GPL and Al2O3, the UTS of Al matrix increases from 160 to 308 MPa [Citation16]. However, the strengthening efficiency of GPLs is still much lower than the theoretically expected value, hindering the practical applications of GPL-reinforced AMCs [Citation14–20]. This can be explained from two aspects: (i) high-quality graphene is prone to agglomeration during traditional powder processing due to its hydrophobic surface, while the graphene derivatives with good dispersibility (e.g. graphene oxide (GO)) show inferior intrinsic properties compared to the perfect structured graphene [Citation16,Citation19,Citation20]. (ii) the natural GPL/Al interface has a weak physical bonding, which results in a poor load transfer with insufficient strengthening effect. Although the interfacial strength can be enhanced by appropriate interfacial reactions, the precise control of the reaction is extremely challenging during composite processing due to the low formation energy of Al4C3 [Citation19]. Moreover, the structure of GPLs can be damaged by immoderate reactions, in which the Al4C3 might become the preferential sites of cracks due to its brittle and hygroscopic characteristics [Citation15].
To overcome the limitations of graphene, 2D transition metal carbides, known as MXene, has been proposed as an effective reinforcement for AMCs due to its excellent mechanical properties and hydrophilic surface [Citation23,Citation24]. The termination of MXene by hydroxyl, oxygen, and fluoride groups during the synthesis of MXene by the chemical etching of A layers from MAX phases enables the dispersion of MXene in various polar solvents [Citation25,Citation26]. In addition, among water dispersible 2D materials such as GO, MXene has the best measured Young's modulus (330 GPa) and breaking strength (17.3 GPa) [Citation26]. In contrast to carbon-based fillers, MXene has a higher chemical stability, as it can withstand contact with molten metal [Citation25,Citation27]. However, the true potential of MXene in metal-based composites has not been extensively studied. Therefore, in this work, we demonstrated the potential application and strengthening behavior of 2D MXene in AMCs. Few-layered MXene (FLM)-reinforced AMCs were fabricated using self-assembly protocol and traditional powder metallurgies. The composite strength was increased by approximately 66% with the addition of 0.26 vol.% FLM.
2. Experimental
Ti3C2Tx MXene colloid (∼3 mg mL−1) was fabricated by the selective etching of Al atomic layers from the Ti3AlC2 phase, as reported elsewhere [Citation28]. MXene/Al mixed powders were prepared via a hetero-agglomeration process utilized for the fabrication of nanocarbon/Al composites [Citation11,Citation19]. A 0.13, 0.26, or 0.39 vol.% MXene/Al powder mixture was obtained using a density of 4.2 g cm−3 for Ti3C2Tx and 2.7 g cm−3 for Al. The MXene/Al powders were consolidated via spark plasma sintering (SPS) [Citation13,Citation19]. In order to utilize the superior in-plane strength of 2D materials, hot extrusion was further conducted to align MXene platelets in a single direction [Citation18,Citation19]. The detailed information for the synthesis of MXene, powder mixing and consolidation, and characterization methods can be found in Supporting Information.
3. Results and discussion
Figure a presents a comparison of the X-ray diffraction (XRD) patterns of the Ti3AlC2 phase and the as-prepared MXene. As observed in the XRD pattern of MXene, the (104) peak disappeared and the (002) peak shifted to a lower angle, indicating the elimination of the Al atomic layers from Ti3AlC2 and the formation of MXene with an increased interlayer distance. The transmission electron microscopy (TEM) image of MXene as shown in Figure b, reveals that MXene is a transparent sheet with crumbled and wrinkled surfaces, indicating its ultrathin and flexible nature. The selected-area electron diffraction (SAED) pattern (upper inset of Figure b) illustrated a hexagonal symmetry for the MXene single-crystal. The atomic force microscopy (AFM) analysis of MXene revealed that the as-prepared MXene was an FLM (i.e. <10 layers). Figure c displays the FLM with a thickness of ∼3 nm. Field-emission scanning electron microscopy (FESEM) observations confirmed that the FLM was irregularly shaped with a lateral size of ∼2.8 µm (Figure S1 of Supporting Information).
Figure 1. (a) XRD patterns of the starting Ti3AlC2, as-prepared MXene, and 0.39 vol.% MXene/Al composite; (b) TEM image of MXene on a Cu grid; (c) AFM image of the MXene; (d) Cross-sectional HRTEM image of the Al powder near the surface; (e) FESEM and (f) TEM images of the MXene/Al powder mixture. Insets in (b) show the SAED pattern and EDS analysis of MXene taken from the green and blue spots, respectively. Inset in (c) shows the height profile along the white dashed line. Inset in (d) shows the fast Fourier transform (FFT) pattern of oxide layer.
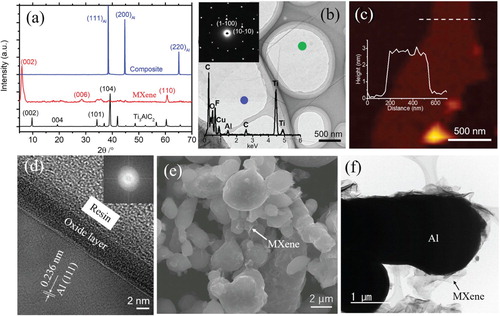
The high-resolution (HR) TEM image of the cross-section of the Al particle as shown in Figure d, reveals that the surface of the Al powder was continuously covered by an amorphous thin film of Al2O3 (inset of Figure d), with an average thickness of ∼5.2 nm, which was induced by the gas atomization process [Citation19]. The Al powders were ionized to produce Al3+, displaying a zeta potential of +18 ± 11 mV in water [Citation29]. However, due to the surface functionalities of the FLM [Citation28,Citation30], corresponding to -F, -OH, or =O (see the lower inset of Figure b), the FLM was significantly negatively charged at −43 ± 6 mV. Hence, the Al powder and FLM could be assembled spontaneously during the hetero-agglomeration process due to electrostatic attraction. The dispersion state of 0.26 vol.% FLM/Al powder mixture was observed via FESEM. As shown in Figure e, the FLM was easily deformed and covered on the Al surface, which is due to the ultrathin, flexible, and high-aspect-ratio characters. The TEM image in Figure f demonstrated the wrapping of the Al powder by the FLM. Due to the strong sheet-to-sheet van der Waals interactions, however, the random restacking of FLM was also detected (Figure f).
The FLM/Al composites consolidated via SPS and hot extrusion possessed high relative densities of >99% (Table S1), indicating that the FLM had no significant effect on the densification behavior of Al. Electron back-scattered diffraction (EBSD)-inverse pole figure (IPF) was used to characterize the microstructure of the 0.26 vol.% FLM/Al composite. The primary Al particles were spindle-shaped (Figure a) and exhibited a <111> fiber texture along the extrusion direction (Figure d) due to the metallic plastic flow [Citation13,Citation19,Citation31]. This metallic plastic flow might benefit to the stretching and flattening of the wrinkled FLM incorporated within the Al particle boundaries. The longitudinal cross-section view of the FLM/Al composite (see blue arrows in Figure b–c) revealed that the FLM platelets were individually distributed and mostly aligned along the extrusion direction [Citation18,Citation19]. Moreover, the distance between two adjacent FLM platelets was determined to be ∼0.5–2 µm (Figure b). However, the flexible FLM surrounded and fitted into the curved boundary of the Al grains in the composite transverse cross-section (Figure e–f). This indicates that the FLM platelets decorated the grain boundaries, which were aligned along a single direction.
Figure 2. Microstructures of the 0.26 vol.% FLM/Al composite in the (a-c) longitudinal and (d-f) transverse cross-sections: (a, d) EBSD-IPF maps; (b, c, e, f) TEM images. (f) is taken from the yellow square in (e).
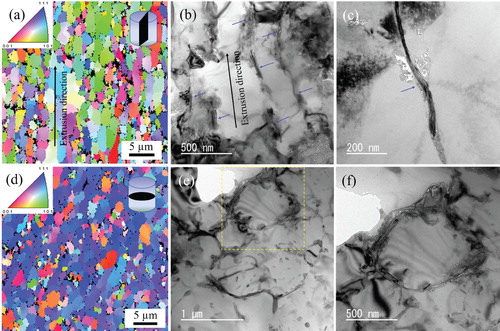
The average grain size of pure Al was determined as 2.92 µm, which decreased to be 2.45 or 1.96 µm with incorporating 0.13 vol.% or 0.26 vol.% FLM, respectively (Figure S2). This grain refinement is caused by the pinning of FLM platelets during densification process. In addition, the grain size of FLM/Al composites was similar to that of other AMCs [Citation9,Citation11,Citation19,Citation21].
Annular bright field (ABF)-scanning TEM (STEM) and the corresponding energy dispersive spectroscopy (EDS) maps were used to investigate the interfacial structure of the FLM/Al composite. As shown in Figure b, a Ti-rich film with a thickness of ∼18 nm was embedded in the Al2O3 band, thus, separating two Al grains. This suggests the formation of an Al-Al2O3-FLM-Al2O3-Al multiple interphase. As shown in the HRTEM image of the FLM platelet sandwiched between two thin Al2O3 layers (Figure c), the Al2O3 layer was slightly thicker than that on the starting Al powder (Figure d), possibly due to the surface oxidation during powder mixing in water. In addition, the sandwiched FLM consisted of 8 layers of MXene monolayers, as indicated by the red lines in Figure c. Furthermore, the (002) basal planes of the FLM were continuous and mutually parallel, showing a typical etching-induced accordion-like feature with an interlayer distance of ∼0.5–3 nm (Figure S3) [Citation25,Citation27]. This indicates that the FLM preserved a high crystallinity during composite densification.
Figure 3. (a) TEM image of a 0.26 vol.% FLM/Al composite in the longitudinal cross-section; (b) ABF-STEM image and corresponding EDS maps of elemental Al, Ti, and O taken from the yellow square in (a); (c) HRTEM image of the FLM-Al interface. Inset in (a) shows the SAED pattern of Al taken from the green spot. Insets in (c) show the EDS analysis taken from the yellow spot, and the schematic of the Al filled into the grooved edge of the FLM, respectively.
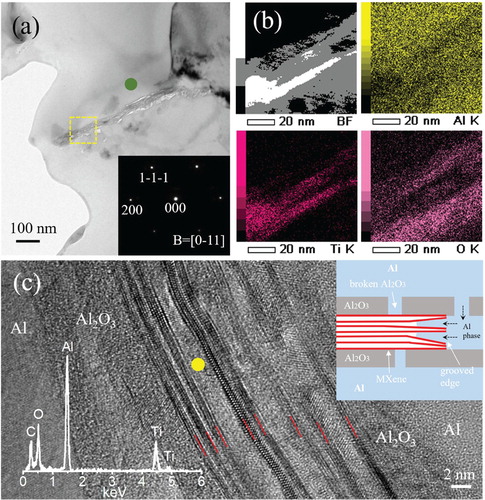
Further HRTEM-EDS inspection revealed that the Al phase was filled into the spacing of the FLM interlayers (lower inset of Figure c). There are two possible factors responsible for this phenomenon: (i) as clarified in the SPS processing of Al-based alloys or composites [Citation11,Citation19], the transient liquid Al phase formed from the fractured Al2O3 layer due to high local temperatures, is automatically filled into the FLM platelets by the capillary force. (ii) The Al phase was forced to infiltrate the grooved edges of the accordion-like FLM, owing to the strong applied stress during SPS or hot extrusion (upper inset of Figure c). To understand the reason for this phenomenon, we performed a high-temperature wetting analysis of the FLM-Al interface. The average contact angle of the Al droplet on the MXene film was determined to be ∼142.9° (inset of Figure a), suggesting a poor interfacial wettability. Thus, the presence of the Al phase within the FLM interlayers can be attributed to the severe plastic deformation of the Al during densification. Furthermore, in accordance with the TEM observation in Figure c, no interfacial reaction occurred between the FLM and molten Al (inset of Figure a), indicating the superior thermal stability of MXene [Citation20,Citation23].
Figure 4. (a) Cyclic thermal expansion behavior of the 0.26 vol.% FLM/Al composite; (b) TEM image of the crack produced by bending the FLM/Al composite; (c) Nominal tensile stress-tensile strain curves for unreinforced Al and the FLM/Al composites; (d) Comparison of the strengthening efficiency of FLM and other reinforcement for AMCs. Inset in (a) shows the optical images of the Al bulk on the MXene film at 973 K.
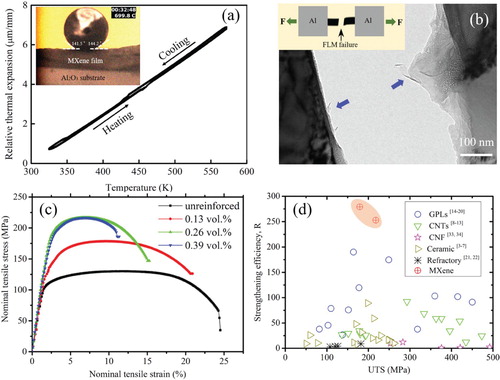
As shown in Figure c, regardless of the insufficient wettability of the FLM-Al interface, the FLM was in close contact to the Al or Al2O3-layer, which is free of nanovoids or impurities. To further clarify the interfacial state, the thermal expansion behavior of the FLM/Al composite was evaluated under cyclic thermal load in a temperature range of 323–573 K. As shown in Figure a, no hysteresis of the expansion behavior, which is generally caused by the local interfacial slippages bearing thermal loads [Citation11], was observed. However, the cyclic thermal expansion of the FLM/Al composite was linear and reversible, indicating a thermally stable, and robust FLM-Al interfaces. This result is consistent with the TEM observation of the fractured composite surface. TEM observation was carried out on an ion-milled FLM/Al specimen, which has been gradually bent by two tweezers under optical microscope so that it underwent catastrophic crack propagation but did not break completely. The TEM observation of the detached fractured surface revealed that the broken FLM platelets were always detected in pairs (see blue arrows in Figure b). This indicates that the FLM experienced bridging, and then failed in the center of the FLM under loading (inset of Figure b). This result confirms the efficient load transfer at the FLM-Al interface induced by the anchor effect of the Al phase infiltration, as well as the presence of Al2O3 phase that possibly acted as a bonding agent between the FLM and Al. Moreover, in contrast to the weak van der Waals attraction between the inter-walls of the CNTs and GPLs [Citation32], the interlayers of the FLM in AMCs were tightly conjoined by the infiltration of the Al phase, possibly contributing to the enhanced load-bearing capability of MXene. Consequently, the FLM/Al composites may exhibit the desired mechanical performance.
Figure c shows the nominal tensile stress–strain curves of unreinforced Al and the FLM/Al composites. The UTS and failure elongation of the unreinforced Al were determined to be 131.5 ± 8.6 MPa and 24.2 ± 2.7%, respectively. However, the UTS of the FLM/Al composites increased with an increase in the FLM concentration, reaching a maximum value of 217.9 ± 9.5 MPa at 0.26 vol.%; simultaneously, a large failure elongation of 15.3 ± 1.6% was realized. These results clearly indicate that FLM is an effective reinforcement for AMCs. However, with incorporating 0.39 vol.% FLM, the UTS of the composite decreased to 213.8 ± 10.4 MPa, and the ductility was severely degraded as well (11.2 ± 3.2%). This is caused by FLM agglomerations due to insufficient contact surface of Al particles for hosting high-concentration FLM sheets during powder mixing (Figure S4). Thus, the FLM clusters acted as preferential sites for crack generation under tensile loads.
The advantage of FLM for the stiffening of AMCs can be better appreciated by comparing its strengthening efficiency, , with other types of reinforcements [Citation8], that is:
(1)
(1) where
and
are the UTS of the composite and matrix, respectively, and
is the volume fraction of the fillers. As demonstrated in Figure d, the strengthening efficiency of FLM is ∼250–280, which is considerably higher than those of conventional ceramics [Citation3–7] or refractory particles [Citation21,Citation22], fiber reinforcements [Citation33,Citation34], as well as CNTs [Citation8–13] and GPLs [Citation14–20]. This superiority can be attributed to the incorporating features of the undamaged FLM platelets. The construction of FLM platelets parallel to the tensile direction formed a robust bonding with the matrix via Al infiltration, thus, leading to the adequate exertion of the intrinsic strength of MXene. The high strengthening efficiency of FLM makes it a promising reinforcement for high-specific-strength AMCs and, from a practical aspect, are beneficial for reducing the cost of materials.
4. Conclusions
In summary, we successfully incorporated individual MXene into AMCs to enhance the mechanical performance using the self-assembly protocol and powder metallurgy. FLM was prepared by selectively etching Al atomic layers from Ti3AlC2 phases, and was homogeneously mixed with Al powders under electrostatic attraction in an aqueous solution. After densification by SPS and hot extrusion, the FLM platelets, decorating the grain boundaries, were aligned in the AMCs along the extrusion direction under a metallic plastic Al flow. The contact angle of the Al droplet on FLM platelets was experimentally measured as 142.9°. In addition, the TEM observation and cyclic thermal expansion behaviors revealed that the FLM was robustly bonded to the Al matrix, thus, improving the interfacial load transfer through the anchor effect of the infiltrated Al phase during densification. Consequently, a 66% enhancement of UTS was achieved for pure Al by incorporating 0.26 vol.% FLM, indicating that the FLM has a remarkably higher strengthening efficiency than other reinforcements. This work demonstrated that MXene can be exploited as an effective reinforcement, and provides further insight on the design of high-performance AMCs for practical applications.
Supplemental Material
Download MS Word (2.4 MB)Acknowledgment
The authors would like to thank Dr. Takamichi Miyazaki and Dr. Kosei Kobayashi for the assistance of TEM analysis.
Disclosure statement
No potential conflict of interest was reported by the author(s).
References
- Pollock TM. Weight loss with magnesium alloys. Science. 2010;328:986–987.
- Surappa MK. Aluminium matrix composites: challenges and opportunities. Sadhana. 2003;28:319–334.
- Kang Y-C, Chan SL-I. Tensile properties of nanometric Al2O3 particulate-reinforced aluminum matrix composites. Mater Chem Phys. 2004;85:438–443.
- Su H, Gao W, Feng Z, et al. Processing, microstructure and tensile properties of nano-sized Al2O3 particle reinforced aluminum matrix composites. Mater Des (1980–2015). 2012;36:590–596.
- Mazahery A, Ostadshabani M. Investigation on mechanical properties of nano-Al2O3-reinforced aluminum matrix composites. J Compos Mater. 2011;45:2579–2586.
- Rahman MH, Al Rashed HM. Characterization of silicon carbide reinforced aluminum matrix composites. Procedia Eng. 2014;90:103–109.
- Hemanth J. Development and property evaluation of aluminum alloy reinforced with nano-ZrO2 metal matrix composites (NMMCs). Mater Sci Eng A. 2009;507:110–113.
- Jiang L, Li ZQ, Fan GL, et al. The use of flake powder metallurgy to produce carbon nanotube (CNT)/aluminum composites with a homogenous CNT distribution. Carbon. 2012;50:1993–1998.
- Chen B, Li S, Imai H, et al. An approach for homogeneous carbon nanotube dispersion in Al matrix composites. Mater Des. 2015;72:1–8.
- Kwon H, Estili M, Takagi K, et al. Combination of hot extrusion and spark plasma sintering for producing carbon nanotube reinforced aluminum matrix composites. Carbon. 2009;47:570–577.
- Zhou W, Yamaguchi T, Kikuchi K, et al. Effectively enhanced load transfer by interfacial reactions in multi-walled carbon nanotube reinforced Al matrix composites. Acta Mater. 2017;125:369–376.
- Yang XD, Liu EZ, Shi CS, et al. Fabrication of carbon nanotube reinforced Al composites with well-balanced strength and ductility. J Alloys Compd. 2013;563:216–220.
- Chen B, Kondoh K, Li J, et al. Extraordinary reinforcing effect of carbon nanotubes in aluminium matrix composites assisted by in-situ alumina nanoparticles. Compos B Eng. 2020;183:107691.
- Gao X, Yue HY, Guo EJ, et al. Preparation and tensile properties of homogeneously dispersed graphene reinforced aluminum matrix composites. Mater Des. 2016;94:54–60.
- Li G, Xiong BW. Effects of graphene content on microstructures and tensile property of graphene-nanosheets/aluminum composites. J Alloys Compd. 2017;697:31–36.
- Zhang Y, Li X. Bioinspired, graphene/Al2O3 doubly reinforced aluminum composites with high strength and toughness. Nano Lett. 2017;17:6907–6915.
- Bisht A, Srivastava M, Kumar RM, et al. Strengthening mechanism in graphene nanoplatelets reinforced aluminum composite fabricated through spark plasma sintering. Mater Sci Eng A. 2017;695:20–28.
- Shin SE, Choi HJ, Shin JH, et al. Strengthening behavior of few-layered graphene/aluminum composites. Carbon N Y. 2015;82:143–151.
- Zhou W, Mikulova P, Fan Y, et al. Interfacial reaction induced efficient load transfer in few-layer graphene reinforced Al matrix composites for high-performance conductor. Compos B Eng. 2019;167:93–99.
- Wang JY, Li ZQ, Fan GL, et al. Reinforcement with graphene nanosheets in aluminum matrix composites. Scripta Mater. 2012;66:594–597.
- Huang G, Shen Y, Guo R, et al. Fabrication of tungsten particles reinforced aluminum matrix composites using multi-pass friction stir processing: Evaluation of microstructural, mechanical and electrical behavior. Mater Sci Eng A. 2016;674:504–513.
- Chen LG, Lin SJ, Chang SY. Tensile properties and thermal expansion behaviors of continuous molybdenum fiber reinforced aluminum matrix composites. Compos Sci Technol. 2006;66:1793–1802.
- Naguib M, Kurtoglu M, Presser V, et al. Two-dimensional nanocrystals produced by exfoliation of Ti3AlC2. Adv Mater. 2011;23:4248–4253.
- Naguib M, Mashtalir O, Carle J, et al. Two-dimensional transition metal carbides. ACS Nano. 2012;6:1322–1331.
- Kamysbayev V, James NM, Filatov AS, et al. Colloidal gelation in liquid metals enables functional nanocomposites of 2D metal carbides (MXenes) and lightweight metals. ACS Nano. 2019;13:12415–12424.
- Lipatov A, Lu H, Alhabeb M, et al. Elastic properties of 2D Ti3C2Tx MXene monolayers and bilayers. Sci Adv. 2018;4:eaat0491.
- Zhang J, Li S, Hu S, et al. Chemical stability of Ti3C2 MXene with Al in the temperature range 500–700°C. Materials. 2018;11:1979.
- Lu X, Zhang Q, Liao J, et al. High-efficiency thermoelectric power generation enabled by homogeneous incorporation of MXene in (Bi, Sb) 2Te3 matrix. Adv Energy Mater. 2020;10:1902986.
- Li Z, Fan G, Tan Z, et al. Uniform dispersion of graphene oxide in aluminum powder by direct electrostatic adsorption for fabrication of graphene/aluminum composites. Nanotechnology. 2014;25:325601.
- Ghidiu M, Lukatskaya MR, Zhao M, et al. Conductive two-dimensional titanium carbide ‘clay’with high volumetric capacitance. Nature. 2014;516:78–81.
- Kwon H, Takamichi M, Kawasaki A, et al. Investigation of the interfacial phases formed between carbon nanotubes and aluminum in a bulk material. Mater Chem Phys. 2013;138:787–793.
- Estili M, Kawasaki A. Engineering strong intergraphene shear resistance in multi-walled carbon nanotubes and dramatic tensile improvements. Adv Mater. 2010;22:607.
- Cao X, Shi Q, Liu D, et al. Fabrication of in situ carbon fiber/aluminum composites via friction stir processing: Evaluation of microstructural, mechanical and tribological behaviors . Compos B Eng. 2018;139:97–105.
- Hajjari E, Divandari M, Mirhabibi A. The effect of applied pressure on fracture surface and tensile properties of nickel coated continuous carbon fiber reinforced aluminum composites fabricated by squeeze casting. Mater Des (1980–2015). 2010;31:2381–2386.