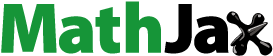
Abstract
An equiatomic VCoNi medium-entropy alloy possesses high sensitivity to grain-boundary strengthening, achieved by severe lattice distortions. Its ultrafine-grain structure enables 1.5 Gigapascal yield strength even for the fully recrystallized alloy with a single face-centered cubic structure. The high density of grain boundaries also generates high back stresses via piling up of massive dislocations, and the low cross-slip probabilities produce not only robust dislocation-mediated plasticity but also high back stress contribution to flow stress, which affords high strain-hardening capability to ultrafine-grain alloys, with 1.7 Gigapascal ultimate tensile strength with remarkable ductility. Our approach provides a new method for developing ultrastrong metallic materials.
GRAPHICAL ABSTRACT
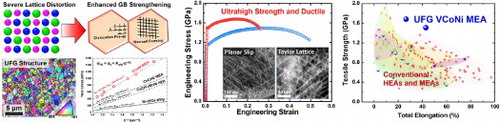
Introduction
Developing stronger and more ductile materials has been a key issue for obtaining desirable service performance in various structural applications [Citation1–6]. However, traditional strengthening methods for developing strong metallic materials usually involves the sacrifice of ductility, which is known as a strength–ductility trade-off. Most material scientists have attempted to overcome this challenge using novel metallurgical strategies with respect to metastability engineering [Citation2], multi-phase or precipitation strengthening [Citation3,Citation4], and nano- and hetero-structuring of microstructure [Citation5–7]. Furthermore, the emergence of multi-principal element alloys, known as high-entropy alloys (HEAs) and medium-entropy alloys (MEAs), with no single dominant element in contrast to traditional dilute alloys, significantly increases the possibility of the discovery of new alloys via traditionally uncommon element grouping [Citation8]. Based on this new alloying design concept, various alloys with high performance have been intensively developed over the past decade [Citation2–4,Citation6–12].
As multi-principal element alloys are composed of several principal elements, it is widely known that high solid-solution strengthening could be achieved by producing severe lattice distortions [Citation13–15]. In this respect, by utilizing the irreplaceable advantage of multi-principal element alloys, an equiatomic VCoNi MEA with a single face-centred cubic (FCC) phase was recently developed, which exhibited superior tensile properties with a near 1 GPa yield strength [Citation15]. The novel mechanical properties of the VCoNi alloy were derived from the concept of the enhanced solid-solution strengthening induced by the large difference in atomic radius in the V–Co–Ni system as compared with those in conventional alloys. Moreover, beyond the substantial merits for good mechanical properties, the VCoNi MEA exhibits multi-functional performances, such as high resistance to hydrogen embrittlement due to low hydrogen diffusivity [Citation16], good corrosion resistance due to the absence of a local potential gradient [Citation16], and high strain-rate superplasticity, achieved via active dynamic recrystallization at high temperatures [Citation17].
Of specific interest is the enhanced solid-solution strengthening has a crucial role in improving the grain-size dependency of yield strength as well in recrystallized FCC alloys [Citation13,Citation15]. In other words, as grain-boundary (GB) strengthening could be much more effective for VCoNi alloy than other FCC-structured alloys, it is perceived that further improvement of mechanical properties can be realized by nano-structuring. However, the verification of the proposed suggestions is very challenging because the single FCC phase could be obtained at high temperatures (over 850°C) in an equiatomic VCoNi system [Citation17], which impedes the grain refinement by annealing at relatively low temperature conducted in conventional processing routes [Citation18,Citation19]. In this respect, a severe plastic deformation (SPD) along with post-annealing heat treatment can produce ultrafine-grained (UFG) materials by offering a considerably high driving force of recrystallization for grain refinement [Citation18,Citation19], while delicate processing controls are required to form fully recrystallized alloys maintaining UFG structures. In this study, therefore, we conducted a high-pressure torsion (HPT) process to introduce significant strain energy and subsequently followed by short-time annealing treatment at a high rate to avoid undesirable grain growth. We found the fabricated fully recrystallized UFG VCoNi alloy exhibited superior strain-hardening capability producing high tensile strength (∼1.7 GPa) with remarkable ductility (∼27%), and thus the underlying mechanisms were revealed in terms of roles of grain boundaries and deformation structures.
Materials and methods
The equiatomic VCoNi alloy ingots were produced by vacuum induction melting in Ar atmosphere using pure metal pellets with high purity (>99.95%). Homogenization was conducted for as-cast ingots at 1200°C for 24 h in an evacuated ampule. For the homogenized ingots, cold rolling was performed for the thickness reduction from 7 mm to 1.5 mm to break the coarse casting microstructure. Moreover, to maximize the driving force of recrystallization for obtaining homogeneous fine grain structures, HPT was performed on machined samples with a disc shape of 10 mm diameter and 1.5 mm thickness. A total of five turns of HPT were carried out for each sample at 1 rpm under 6 GPa for inducing sufficient shear strains on the samples [Citation18–20].
After HPT, the short-time annealing was conducted for the samples at 900°C (for the phase diagram of V-Co-Ni system, See Supplementary Figure 1) for 30 and 150 s under vacuum atmosphere (8 × 10−3 Torr) using a rapid thermal processing system (LABSYS RTP-1200, NEXTRON, Korea). The heating rate was maintained at 100°C/s to suppress grain growth during heating, and the samples were quenched in He after isothermal holding for UFG-structuring while maintaining a single FCC phase. Notably, the samples annealed for 30 and 150 s are hereafter denoted as UFG and FG, respectively.
For microstructural investigation, all the samples were finely polished using a colloidal silica suspension. Electron backscatter diffraction (EBSD) analysis was performed using a field-emission scanning electron microscope (XL-30S FEG, FEI Co., USA), and the EBSD data were interpreted using a TSL OIM Analysis 7 software. To characterize the UFG and FG structures of the VCoNi alloys, scanning transmission electron microscopy (STEM, Talos F200X, FEI Co., USA) analysis was carried out on thin-foil samples prepared by focused ion beam (FIB, Helios Nanolab 650i, FEI Co., USA) extraction. Furthermore, to verify compositional homogeneities of the samples, atom probe tomography (APT) analysis was performed on the sample prepared using the FIB milling system with a local electrode atom probe (LEAP-4000X HR, CAMECA Inc., France) at 50 K under <10−7 Pa.
Results and discussion
Figure reveals the initial microstructure of the annealed VCoNi alloys after HPT process. The alloys clearly exhibit the UFG and fine-grained (FG) structures in the range of a few hundred nanometres to micrometres as a single FCC phase with a nearly random crystallographic orientation (Figure (a,c)). Noticeably, as shown in Figure (b,d), although the annealing heat treatment is performed for a short-time period for severely deformed samples, the annealed samples display a fully recrystallized microstructure with a sufficiently low KAM distribution (for detailed estimation of recrystallized fractions, see Supplementary Figure S2). This result demonstrates the annealing temperature of 900°C can efficiently promote the recrystallization of the severely deformed samples while maintaining a single FCC phase. In addition, a short period of annealing time could also be effective for interrupting grain growth of the alloys. The average grain sizes (d) of the UFG and FG alloys are determined to be 657 ± 321 nm and 1.32 ± 0.41 μm (insets in Figure (b,d)), respectively.
Figure 1. (a and c) IPF maps and (b and d) and KAM maps for (a and b) UFG and (c and d) FG VCoNi alloys. The insets in (b) and (d) indicate the grain-size distribution of UFG and FG alloys, respectively. (e) 3D reconstructed element distributions of FG VCoNi alloy by APT analysis. The GBs are marked in black lines in the EBSD maps and denoted as a black-dashed line in the APT reconstruction maps.

The compositional homogeneities were verified by APT across grain boundaries for the UFG alloy (Figure (a)), revealing that the constituent elements are homogeneously distributed with nearly equimolar compositions of V, Co, and Ni, without any observable segregation at the GB (for the 1D profile of the chemical composition for the APT sample, see Supplementary Figure S3).
Figure presents the mechanical properties for the UFG and FC alloys, compared with those of CrCoNi MEA produced by HPT and post heat treatment. Detailed tensile properties measured from tensile curves are listed in Table . Notably, although the alloys comprise a fully recrystallized microstructure with a single FCC phase, they exhibit extremely high yield strength (YS) and ultimate tensile strength (UTS), as well as remarkable total elongation (El.) (Figure (a)). The strength levels of UFG VCoNi surpassed those of other single FCC-structured alloys having similar grain sizes [Citation13,Citation18–22], which demonstrated that the strength enhancement via GB strengthening () was much more effective for VCoNi MEAs. Based on the Hall–Petch relationship (
), where
and
are the lattice friction and Hall–Petch slope for slip, respectively, the VCoNi MEA had a significantly high value for Hall–Petch slope (864 MPa μm1/2) in comparison with those for other FCC-structured materials (Supplementary Figure S4). This strongly supported the beneficial effect of severe lattice distortions on GB strengthening (for comparison of lattice distortion between VCoNi alloy and CrCoNi alloy, see Supplementary Figure S5 and Table S1).
Figure 2. (a) Engineering stress–strain curves and (b) Strain–hardening rate curves of the UFG and FG VCoNi MEAs compared with those of CrCoNi MEAs having similar grain size.
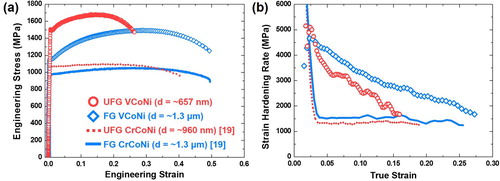
Table 1. Room-temperature tensile properties of the UFG and FG VCoNi and CrCoNi MEAs.
Moreover, surprisingly, the UFG VCoNi MEAs exhibit a much higher strain-hardening rate than UFG CrCoNi MEAs in overall plastic deformation (Figure (b)). Generally, due to low stacking fault energy (SFE), FCC-structured HEAs and MEAs often exhibit high strain-hardening capability, which are usually attributed to the deformation mechanism transition from slip to either twinning-induced plasticity (TWIP) or transformation-induced plasticity (TRIP), which provides additional hardening sources [Citation21–23]. However, it has been well reported that grain refinement suppresses the TWIP or TRIP effect on the flow behaviours of the alloys [Citation18,Citation19,Citation21–23]. For instance, with respect to the Hall–Petch equation for critical twinning stress (), the Hall–Petch slope (
) can often be estimated to be twice as large as the slope for slip (
) [Citation21]. Therefore, the flow behaviours of UFG HEAs are often governed by dislocation slip because of the high required stress for twin initiation. In addition to the restraint of TWIP or TRIP, it has been widely reported that the high densities of GBs could effectively act as sinks for glide dislocations based on greater diffusion-controlled plasticity in UFG materials [Citation24,Citation25]; thus, the strain-hardening capability could be significantly decreased when compared with those of the coarse-grained alloys [Citation13,Citation18,Citation19,Citation21]. On the contrary, the UFG VCoNi MEAs maintained high strain-hardening rate despite significant grain refinement. This high strain-hardening rate offered not only ultra-high tensile strength, but also large uniform elongation (U. El.), by delaying the onset of plastic instability of the alloy during tensile deformation.
Meanwhile, it has been known that the Hall–Petch equation is highly related to dislocation pile-ups at GBs generating long-range internal stresses known as back stresses [Citation26]. In other words, it could be supposed that the extremely high value of Hall–Petch slope for VCoNi alloy is also related to strong GB effectively interrupting dislocation movement with profuse dislocation pile-ups generating high back stress during plastic deformation. In order to reveal underlying mechanism of the unusual strain-hardening behaviour, deformed microstructure was investigated for UFG alloy, as presented in Figure . It is clearly identified that the dislocations are densely piled-up as a planar array configuration from the GB (Figure (b,c)). This result implies that the massive pile-ups of dislocations at the GBs strongly generate back stresses, which kinematically contributed to strain hardening of the alloys during plastic deformation [Citation24–27]. Generally, the strain hardening of FCC-structured alloys can be usually expressed as the contributions of two types of hardening mechanisms [Citation25–27]: isotropic hardening by the evolution of forest dislocations; and kinematic hardening by dislocation accumulation at the GB. Moreover, the kinematic hardening is governed by the combinatorial effect of back stress and forward stress between soft grains and hard grains across the GB [Citation28]. In order to obtain a synergetic hardening effect by profuse dislocation pile-ups for materials during deformation, the contributions of back stress should be larger than those of forward stress based on the distinguished distribution of each type of stress around the GB [Citation29].
Figure 3. (a) STEM micrographs for deformed microstructure of UFG VCoNi alloy. (b) High angle annular dark-field (HAADF) micrograph indicating planar slip of massive dislocation walls near GBs. (c) The magnified image for the region enclosed in the green box in (b). (d) HAADF micrograph presenting the nano-sized dislocation substructure formed by intersections of non-coplanar slip walls. (e) The magnified micrograph for the region enclosed in the blue box in (d).
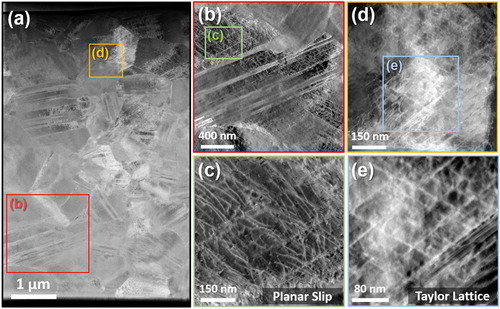
Meanwhile, it has been suggested that the contribution of back stress to strain hardening is dominated by the cross-slip probability of materials [Citation27]. The back-stress () hardening can be expressed as a function of the evolution of the dislocation density (ρ) with increasing strain (ε) using the following equations [Citation30]:
(1)
(1)
(2)
(2) where M is the Taylor factor, α is a constant in the Taylor equation [Citation21], G is the shear modulus, b is the Burgers vector, and P is the probability of cross slip (0 ≤ P ≤ 1). Here, k and β are model parameters determined from experiments [Citation30]. According to Equations (1) and (2), when P decreased, the contribution of back stress to strain hardening increased. Bouaziz et al. [Citation30] recently reported that the solute solutions in HEAs could effectively decrease P associated with larger spacing between Shockley partial dislocations induced by the solute, which strongly promotes planar slip during plastic deformation. In other words, this could be considered an advantage of multi-principal element alloys with strong back-stress hardening effects (solute back strengthening) [Citation30]. For the UFG VCoNi alloy designed by maximized solid-solution strengthening, considering the high planarity of slip as indicated in Figure (b,c), it can be proposed that the high back-stress hardening has a significant effect on the strain-hardening capability at lower d values in the initial stage of deformation according to Equations (1) and (2).
Furthermore, the planar dislocation walls were crystallographically aligned as the coplanar slip bands on the {111} planes (Figure (d,e)), indicating the non-coplanar slip bands are activated with an increase in plastic strain. Consequently, the coplanar and non-coplanar slip bands intersect each other, which significantly reduces the spacing between the slip bands as the formation of nano-scale dislocation substructures (i.e. Taylor lattices) in grain interiors [Citation31]. This non-cell-forming structure verifies the difficulty of cross slip of the present alloy. Noticeably, the spacing between adjacent slip bands is measured to be ∼30 nm in the Taylor lattice (Figure (d,e)). In addition, this dynamic slip-band refinement significantly enhances the strain-hardening capability via the storage of massive dislocations in the grain interiors as well as GB effects. It has been known that the GB effects are weakened at the later regime of the plastic deformation, while the GBs could be regarded as perfectly opaque barriers to dislocations at the early part of deformation [Citation32]. However, the efficient dislocation-mediated plasticity (non-cell forming) could still accelerate the strain hardening of UFG VCoNi MEA by dynamic-slip band refinement at the late part of plastic deformation.
Figure compares the tensile properties of the UFG VCoNi MEAs with those of other HEAs and MEAs (for the database of the alloys, see Supplementary Table S2). Notably, the UFG VCoNi MEA exhibits a much superior YS–U. EL combination compared to those for other single FCC-structured alloys. Meanwhile, the YS level of UFG VCoNi MEA could be similar to those of several multi-phase HEAs hardened by multiple-strengthening mechanisms (i.e. heterogeneous structure, precipitation hardening, etc.) [Citation3]. However, as a different point of view, although the single FCC-structured alloys with the strain-free state are usually considered as soft materials, the YS level of UFG VCoNi is nearly equivalent or higher via just effect of severe lattice distortion and its advantage for GB strengthening than those of most of the multiple-strengthened alloys, which could be considered as the new alloying/microstructure design concepts for developing ultrastrong materials. Furthermore, as the VCoNi alloy exhibits high strain-hardening capability in spite of UFG structure, the sacrificing ductility was minimized as compared with UTS enhancement, which consequently resulted in overcoming the strength–ductility trade-off of multiple-strengthened alloys.
Figure 4. Ashby plots indicating (a) YS vs. U. EL and (b) UTS vs. T. EL of the UFG VCoNi MEAs at room-temperature (present work) in comparison with those of existing HEAs and MEAs. Note that the ordered FCC, ordered body-centered cubic (BCC), hexagonal close-packed phases, and other intermetallic compounds having complex lattice structures (e.g. σ phase, μ phase, and carbides) are referred to as L12, B2, HCP, and CP, respectively.
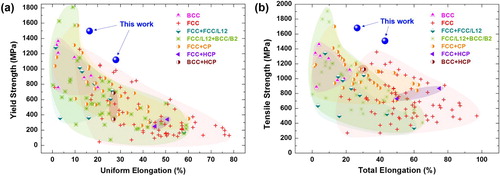
Conclusions
In this study, the UFG VCoNi MEA is successfully produced by HPT and subsequent short-time annealing. The alloys present ultra-high levels of YS (∼1.5 GPa) via effective GB strengthening with respect to the high Hall–Petch slope. The high density of GBs and the low cross-slip probability have a synergetic effect on enhanced strain-hardening capability even for UFG structure of alloy via generating high back stress contribution by massive dislocation pile ups at GBs. Furthermore, because the suppressed cross-slips produces the dynamic slip-band refinements at the late part of deformation, the alloy exhibits ultrahigh UTS (∼1.7 GPa) with remarkable ductility (>25%) compared with those of other UFG alloys. This work can pave the way for new metallurgical strategies to develop novel high-performance materials by utilising the merits of solid-solution strengthening in multi-principal element alloys.
Supplemental Material
Download MS Word (6.2 MB)Disclosure statement
No potential conflict of interest was reported by the author(s).
Additional information
Funding
References
- Raabe D, Tasan CC, Olivetti EA. Strategies for improving the sustainability of structural metals. Nature. 2019;575:64–74.
- Li Z, Pradeep KG, Deng Y, et al. Metastable high-entropy dual-phase alloys overcome the strength-ductility trade-off. Nature. 2016;534:227–230.
- Liang YJ, Wang L, Wen Y, et al. High-content ductile coherent nanoprecipitates achieve ultrastrong high-entropy alloys. Nat Commun. 2018;9:4063.
- Yang H, Li J, Guo T, et al. Fully recrystallized Al0.5CoCrFeMnNi high-entropy alloy strengthened by nanoscale precipitates. Met Mater Int. 2019;25:1145–1150.
- Cheng Z, Zhou H, Lu Q, et al. Extra strengthening and work hardening in gradient nanotwinned metals. Science. 2018;362:559.
- Sathiyamoorthi P, Kim HS. High-entropy alloys with heterogeneous microstructure: processing and mechanical properties. Prog Mater Sci. 2020: 1–30. https://doi.org/10.1016/j.pmatsci.2020.100709
- Lee HH, Hwang KJ, Jung J, et al. Grain size effect on mechanical properties under biaxial stretching in pure tantalum. Met Mater Int. 2019;25:1448–1456.
- Miracle DB. High entropy alloys as a bold step forward in alloy development. Nat Commun. 2019;10:1805.
- Jang MJ, Kwak H, Lee YW, et al. Plastic deformation behavior of 40Fe–25Ni–15Cr–10Co–10V high-entropy alloy for cryogenic applications. Met Mater Int. 2019;25:277–284.
- Moon J, Park JM, Bae JW, et al. A new strategy for designing immiscible medium-entropy alloys with excellent tensile properties. Acta Mater. 2020;193:71–82.
- Park JM, Choe J, Kim JG, et al. Superior tensile properties of 1%C-CoCrFeMnNi high-entropy alloy additively manufactured by selective laser melting. Mater Res Lett. 2020;8:1–7.
- Park JM, Choe J, Park HK, et al. Synergetic strengthening of additively manufactured (CoCrFeMnNi)99C1 high-entropy alloy by heterogeneous anisotropic microstructure. Addit Manuf. 2020;35:101333.
- Yoshida S, Bhattacharjee T, Bai Y, et al. Friction stress and Hall-Petch relationship in CoCrNi equi-atomic medium entropy alloy processed by severe plastic deformation and subsequent annealing. Scr Mater. 2017;134:33–36.
- Moon J, Jang MJ, Bae JW, et al. Mechanical behavior and solid solution strengthening model for face-centered cubic single crystalline and polycrystalline high-entropy alloys. Intermetallics. 2018;98:89–94.
- Sohn SS, Da Silva AK, Ikeda Y, et al. Ultrastrong medium-entropy single-phase alloys designed via severe lattice distortion. Adv Mater. 2019;31:1807142.
- Luo H, Sohn SS, Lu W, et al. A strong and ductile medium-entropy alloy resists hydrogen embrittlement and corrosion. Nat Commun. 2020;11:3081.
- Sohn SS, Kim DG, Jo YH, et al. High-rate superplasticity in an equiatomic medium-entropy VCoNi alloy enabled through dynamic recrystallization of a duplex microstructure of ordered phases. Acta Mater. 2020;194:106–117.
- Asghari-Rad P, Sathiyamoorthi P, Nguyen NTC, et al. Fine-tuning of mechanical properties in V10Cr15Mn5Fe35Co10Ni25 high-entropy alloy through high-pressure torsion and annealing. Mater Sci Eng A. 2020;771:138604.
- Sathiyamoorthi P, Bae JW, Asghari-Rad P, et al. Effect of annealing on microstructure and tensile behavior of CoCrNi medium entropy alloy processed by high-pressure torsion. Entropy. 2018;20:849.
- Sathiyamoorthi P, Bae JW, Asghari-Rad P, et al. Ultra-high tensile strength nanocrystalline CoCrNi equi-atomic medium entropy alloy processed by high-pressure torsion. Mater Sci Eng A. 2018;735:394–397.
- Sun SJ, Tian YZ, Lin HR, et al. Transition of twinning behavior in CoCrFeMnNi high entropy alloy with grain refinement. Mater Sci Eng A. 2018;712:603–607.
- Sun SJ, Tian YZ, Lin HR, et al. Temperature dependence of the Hall–Petch relationship in CoCrFeMnNi high-entropy alloy. J Alloys Compd. 2019;806:992–998.
- Su J, Raabe D, Li Z. Hierarchical microstructure design to tune the mechanical behavior of an interstitial TRIP-TWIP high-entropy alloy. Acta Mater. 2019;163:40–54.
- Kim HS, Estrin Y. Ductility of ultrafine grained copper. Appl Phys Lett. 2001;79:4115.
- Bouaziz O, Estrin Y, Bréchet Y, et al. Critical grain size for dislocation storage and consequences for strain hardening of nanocrystalline materials. Scr Mater. 2010;63:477–479.
- Jiang M, Devincre B, Monnet G. Effects of the grain size and shape on the flow stress: A dislocation dynamics study. Int J Plast. 2019;113:111–124.
- Bouaziz O, Barbier D, Embury JD, et al. An extension of the Kocks–Mecking model of work hardening to include kinematic hardening and its application to solutes in ferrite. Phil Mag. 2013;93:247–255.
- Zhu Y, Wu X. Perspective on hetero-deformation induced (HDI) hardening and back stress. Mater Res Lett. 2019;7:393–398.
- Zhu Y, Ameyama K, Anderson PM, et al. Heterostructured materials: superior properties from hetero-zone interaction. Mater Res Lett. 2021;9:1–31.
- Bouaziz O, Moon J, Kim HS, et al. Isotropic and kinematic hardening of a high entropy alloy. Scr Mater. 2021;191:107–110.
- Welsch E, Ponge D, Hafez Haghighat SM, et al. Strain hardening by dynamic slip band refinement in a high-Mn lightweight steel. Acta Mater. 2016;116:188–199.
- Sinclair CW, Poole WJ, Bréchet Y. A model for the grain size dependent work hardening of copper. Scr Mater. 2006;55:739–742.