Abstract
Heating rate plays a major role in the ceramic sintering process, especially in many new advanced sintering techniques. In this study, the effects of ultra-high heating rate up to 1200°C/s have been investigated on various ceramic nanoparticles by in situ transmission electron microscopy (TEM) heating experiments to monitor the morphological changes immediately after the heating process and during the holding time. It was revealed that an ultra-high heating rate is highly effective in densifying 3 mol.% yttria-stabilized zirconia nanoparticles but was less effective for 8 mol.% yttria-stabilized zirconia or zinc oxide due to the competing diffusion mechanisms.
GRAPHICAL ABSTRACT
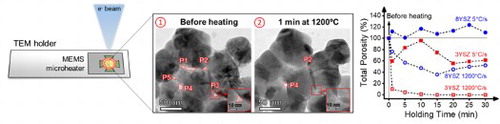
IMPACT STATEMENT
This work demonstrates the use of in situ TEM heating for real-time and direct observation of ceramic nanoparticles to study the impact of ultra-high heating rates up to 1200°C/s.
1. Introduction
One of the most highly desired characteristics in bulk ceramics is reaching full density while maintaining nanosized grain sizes [Citation1,Citation2], which makes sintering is one of the most critical processing step in achieving these characteristics. Sintering involves high temperature below the melting temperature and long holding time to provide sufficient thermal energy for the diffusional process to transport mass from the bulk or grain boundaries to the pores and thus densify the material. This is a challenging process as surface diffusion occurs simultaneously which leads to grain coarsening and the reduction of the driving force for densification. As a result, high levels of densification are often accompanied by significant grain growth during the long and high-temperature sintering process. Therefore, the ceramic sintering process has to be meticulously studied in order to find the optimized conditions (i.e. sintering time, temperature, heating rate) to reach full density while maintaining a nanosized grain structure [Citation3–5].
Increasing the heating rate has been a simple yet effective way to improve the densification of ceramics, especially during the initial and intermediate stages of sintering. Slow heating rates are typically dominated by surface diffusion because it has a lower activation energy than densification mechanisms and dominates at low temperatures [Citation6]. By using a high heating rate, coarsening can be suppressed at low temperatures and the driving force can be maximized for densifying the particles. Early studies showing the advantages of high heating rates were fast firing studies, where samples were rapidly inserted into a preheated furnace and led to significant improvement in the final density and less grain growth compared to that if the conventionally sintered samples [Citation4,Citation7–9].
Recently, the development of new sintering techniques with external fields has quickly evolved because the use of external fields has shown to significantly reduce the highly intensive heating process [Citation10]. Interestingly, the effectiveness of these new sintering techniques is mainly attributed to the elevated heating rates. Figure shows the heating rates involved in various ceramic sintering techniques, including the new techniques such as flash sintering and ultra-fast high-temperature sintering [Citation11–17]. The rapid heating rates achieved in these new techniques are in the estimated range of 103 to 104°C/min [Citation11,Citation12,Citation15,Citation17]. However, most of the fundamental sintering studies have only investigated the effects of heating rates in the typical heating rate range between 10 to 103°C/min [Citation4,Citation18,Citation19]. Hence, there is a strong need for fundamental sintering studies in the ultra-high heating rate range to explore the benefits of using a higher heating rate but without the impact of an external field.
In situ transmission electron microscopy (TEM) is a highly effective characterization technique for studying direct and real-time changes to a material. This advanced technique has helped to study various phenomena that are challenging to understand through ex situ techniques, such as interfacial reactions and phase change during battery cycling [Citation20,Citation21], defect dynamics in resistive switching [Citation22,Citation23] and sintering of metal nanoparticle for catalytic process [Citation24,Citation25]. Currently, there are only a handful of studies which have utilized this in situ technique for studying ceramic sintering [Citation26–30]. In order to investigate the effects of ultra-high heating rates on sintering of ceramic nanoparticles, in situ TEM is employed in this work to directly observe and analyze the evolution of the nanoparticles after ultra-high heating rates. With the use of a micro-electro-mechanical system (MEMS) microheater, the desired temperature (up to 1200°C) can be immediately reached and thus achieving ultra-high heating rates (∼1200°C/s). In this study, 3YSZ (3 mol.% yttria-stabilized zirconia), 8YSZ (8 mol.% yttria-stabilized zirconia), and ZnO systems were investigated using in situ TEM, since they are the most well-studied ceramic systems using the ultra-high heating rates. The implementation of this in situ technique revealed a contrasting response of each oxide to the effects of ultra-high heating rates on the ceramic sintering process.
2. Experimental procedures
Three different nanopowders were used in this study, including 3YSZ (TZ-3Y, Tosoh corporation, 80 nm) 8YSZ (TZ-8Y, Tosoh corporation, 80 nm) and ZnO (US Research Nanomaterials, Inc, 20 nm). The nanopowders were dispersed in ethanol and sonicated for 15 min. The dispersed powders in solution were then dropped on MEMS-based microheater chips (Thermo Fisher Scientific) with an amorphous carbon film. The chips were left to dry for 30 min to allow full evaporation of ethanol and then mounted on a NanoExTM-i/v TEM holder (Thermo Fisher Scientific).
The in situ TEM heating experiments were conducted in a Thermo Fisher Scientific Talos F200X TEM operated at 200 kV. A small current is applied to the MEMS microheater chip with the nanoparticles to begin the heating process. An area of the particle agglomerate with minimal overlap and at least five enclosed porosities was selected for quantitative analysis before, during and after the heating process. To minimize electron beam effects, the beam illumination area was enlarged to avoid heating issues and the electron beam was periodically moved to a different region in between the image and video acquisitions to minimize any electron beam-induced effects. The selected highlights of the videos are compiled and included in the supplementary files.
3. Results
For the heating of 3YSZ nanoparticles, the target temperature was set to 1200°C, which is commonly used by conventional sintering studies [Citation31]. Figure (a) shows the heating profile used for 3YSZ for the ultra-high heating rate and the corresponding TEM micrographs. Before the heating process, five enclosed porosity sites among the agglomerate of nanoparticles were marked by the outlines and labeled P1 to P5. The target temperature of 1200°C was reached immediately within a second by the MEMS microheater, resulting in an ultra-high heating rate of 1200°C/s. Due to the abrupt change of temperature, the snapshot was captured one minute after the heating process in order to readjust the image focus. Within one minute of heating at 1200°C, majority of the porosity sites (P1, P3 and P5) were completely eliminated and the remaining porosity sites (P2 and P4) have significantly reduced in size. For comparison, another in situ experiment with a slow heating rate of 5°C/s was employed with the same target temperature for 3YSZ nanoparticles as shown in Figure (b). Similarly, five porosities were tracked and labeled P6 to P10. The removal of porosity was clearly less effective after slow heating, as all of the porosity still remained after one minute at 1200°C. The measured total pore area before and after the heating process is shown in Figure S1 for both ultra-high heating rate (sum of P1 to P5) and slow heating rate (sum of P6 to P10). The total pore area is very similar for both samples before heating but showed a much larger reduction with the ultra-high heating rate.
Figure 2. Heating profile for (a) ultra-high heating rate (1200°C/s) and (b) slow heating rate (5°C/s) with corresponding snapshots of the 3YSZ nanoparticles before heating and one minute after reaching 1200°C during in situ TEM.
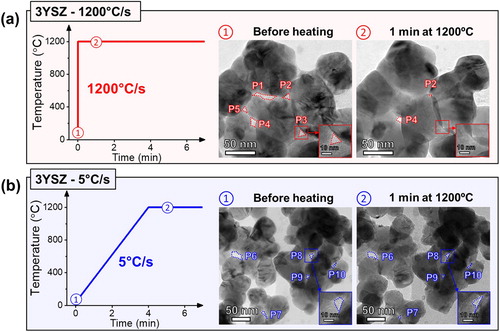
As the 3YSZ case showed such significant improvement in porosity removal using a higher heating rate, we further analyzed the difference in selected area electron diffraction (SAED) patterns before heating and one minute after reaching 1200°C for both heating rates. The SAEDs shown in Figure S2 were acquired in separate in situ TEM heating experiments for the purpose of keeping continuous microstructure observation in the first experiment. The SAED for the ultra-high heating rate showed mostly discrete spots in a diffraction ring before heating. After one minute of heating at 1200°C, the SAED remained in a similar pattern. On the other hand, the nanoparticles which experienced a slow heating rate had several additional distinguished diffraction spots which appeared due to particle rotations.
To analyze the impact of the heating rate over the sintering time, the target temperature was further held for 30 minutes. Figure shows the snapshots of the evolution of nanoparticles during the holding time after ultra-high heating rate and slow heating rate, along with the measured pore areas during the holding time. As most of the porosity was quickly removed during the first minute of heating after an ultra-high heating rate, the remaining porosity was minimal and was successfully removed within 15 min of heating to 1200°C. During the rest of the holding time, some particles begin to coalescence which are signs of coarsening and typical final stage sintering. On the contrary, the porosity removal for the slow heating rate occurs at a much more gradual rate during the holding time and still contained residual porosity even after heating for 30 minutes. In addition, the pore on the top left corner transformed into a more circular shape and significant particle coalescence occurred, which are indications of surface diffusion occurring during the holding time.
Figure 3. Snapshots of the 3YSZ nanoparticles during the holding time at 1200°C after (a) ultra-high heating rate (1200°C/s) and (b) slow heating rate (5°C/s). The measured pore areas during the holding time are shown in (c) and (d) for ultra-high heating rate and slow heating rate, respectively.
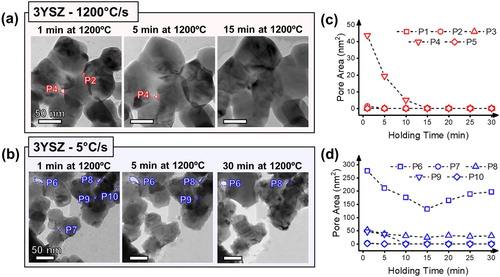
To further investigate the effect of ultra-high heating rates on other oxide nanoparticles, in situ TEM heating studies on 8YSZ and ZnO were also conducted and compared. The same heating profile was utilized for 8YSZ to directly compare the difference to that of 3YSZ. Figure shows the snapshots for 8YSZ nanoparticles before heating, after heating and during the holding time with an ultra-high heating rate (1200°C/s) and slow heating rate (5°C/s). While no pores were completely removed after heating for both cases, the change in total pore area before and after heating (Figure S3) showed a reduction in pore area for the ultra-high heating rate, while the slow heating rate showed an increase in total pore area. The decrease in pore area after ultra-fast heating of 8YSZ is not as significant as 3YSZ, but is still an improvement compared to the nanoparticles which experienced a slow heating rate. During the holding time, there were significant fluctuations in the ultra-high heating rate sample, where some pores experienced shrinkage and some pores experienced coalescence. The slow heating rate sample did not exhibit much changes during the holding time with very minimal shrinkage overall.
Figure 4. Snapshots of the 8YSZ nanoparticles before heating and during the holding time at 1200°C after (a) ultra-high heating rate (1200°C/s) and (b) slow heating rate (5°C/s). The measured pore areas during the holding time are shown in (c) and (d) for ultra-high heating rate and slow heating rate, respectively.
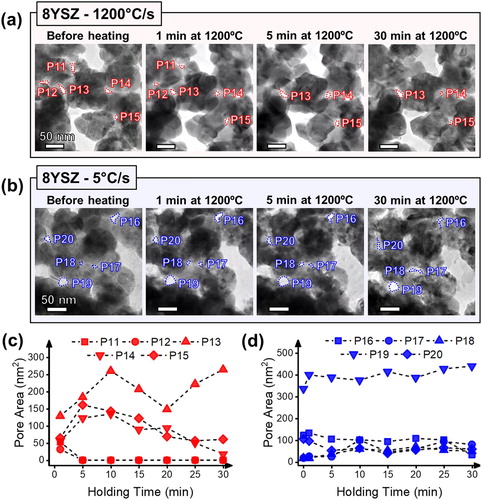
To compare the densification rates between the 3YSZ and 8YSZ samples, the porosity percentage of ultra-high heating rate and slow heating rate for 3YSZ and 8YSZ were collectively compared in Figure S4. The initial porosity area before heating was assumed to be 100% for all cases at 0 min. The 3YSZ with ultra-high heating rate showed the largest decrease in porosity area within one minute of holding time, followed by 3YSZ with a slow heating rate, 8YSZ with ultra-high heating rate and finally 8YSZ with slow heating rate. During the holding time, both 3YSZ and 8YSZ with ultra-high heating rate showed further removal of porosity, while the slow heating of 3YSZ and 8YSZ both showed fluctuations due to pore coalescence.
A similar comparison of heating rates was performed on ZnO nanoparticles. The temperature was heated to 1000°C, which is around the conventional sintering temperature for ZnO [Citation32,Citation33]. Figure (a) shows the heating profiles and series of snapshots for ZnO nanoparticles before heating, 30 seconds after the ultra-high heating rate at 1000°C/s and 200 s of holding at 1000°C. After the temperature was instantly raised to 1000°C, there was no major change to the particle morphology. Only after 200 seconds at the holding temperature, substantial transformation in the particle morphology was observed. Although densification is likely to have occurred due to the reduction in particle agglomerate size, there was still porosity left within the agglomerate which could point towards the sintering mechanism of vapor transport. For comparison, the heating profile for the slow heating rate (5°C/s) is shown in Figure (b) with the corresponding snapshots. During the slow heating to 1000°C, there were already significant changes in the particle arrangement between the temperature of 780–1000°C. In addition, all of the porosity within the cluster was completely removed leading to a much more compact nanoparticle agglomerate.
4. Discussion
Through these real-time observations of particle morphology changes, the effects of ultra-high heating rate on ceramic nanoparticles can be directly monitored. The 3YSZ nanoparticles exhibited the expected pronounced effects of heating rate. Within the first minute of heating to 1200°C using the ultra-high heating rate, most pores were completely eliminated and the remaining pores were reduced in size. Consequently, the remaining porosity was rapidly removed within the next 15 min of heating. The size of the pores has a significant impact on the kinetics of sintering, as large pores tend to reduce the driving force for densification [Citation34]. Using a slower heating rate is less efficient in removing the porosity especially due to the reduction of driving forces from surface diffusion. In addition, the SAED results show that the slow rate heating provided sufficient time to drive the particles to rotate. This could likely contribute to enhanced coarsening as particles can easily coalesce and lead to large grain structures [Citation35]. Further investigation on the impact of heating rate on particle rotation during sintering is needed and can be studied by utilizing dark field imaging during in situ TEM heating experiments.
The results from the in situ TEM heating of 3YSZ nanoparticles in this work strongly agree with the fundamental understanding of heating rate on sintering and also recent heating rate studies performed on 3YSZ in bulk samples. Studies reported by Ji et al. compared sintering of 3YSZ through various techniques, including fast firing, self-propagating high-temperature synthesis and flash sintering [Citation11,Citation12]. Their work showed that the rapid densification in the flash sintering technique is mainly contributed by the rapid heating rate with and without an electric field. Prajzler et al. performed similar heating rate experiments for 3YSZ with larger geometry samples and reached the same conclusion [Citation36]. In this study, the direct real-time observation of nanoparticles reveals how the suppression of surface diffusion during ultra-high heating rates really aid to eliminate porosity for 3YSZ.
Interestingly, the effectiveness of ultra-high heating rates is not equal for other systems. 8YSZ is usually more difficult to sinter into fine grain sizes and dense microstructures compared to 3YSZ. This can be attributed to the activation energy for grain growth is 105 kcal/mol for tetragonal but only 69 kcal/mol for cubic [Citation37]. Consequently, the growth rate for cubic zirconia has been predicted to be up to 250 times faster than that of tetragonal zirconia [Citation37]. Even with the ultra-high heating rates, the reduced activation energy for grain growth mechanisms are dominant and avert the densifying mechanisms. Overall, the improvement in densification under an ultra-high heating rate was significantly less pronounced for 8YSZ in comparison to 3YSZ. This agrees well with the previous studies comparing the sintering of 3YSZ and 8YSZ [Citation38,Citation39]. Thus, the sintering of 8YSZ may require additional driving force for densification, such as an applied pressure, will be needed to result in fully dense and nanograin samples [Citation40].
In comparison to 3YSZ and 8YSZ, ZnO showed a very contrasting morphology evolution. Both ultra-high and low heating rates underwent very notable changes to the structure of the particle agglomeration after a short heating period. Studies have shown that ZnO experiences significant vapor transport, especially at high temperatures above 1000°C [Citation32,Citation33]. As the heating experiment was performed in an ultra-high vacuum atmosphere, the vapor transport mechanism could be even more pronounced. One of the most interesting observations for ZnO was the significant morphological changes which occurred during the slow heating between 780°C and 900°C. This specific temperature range seems to be the optimal sintering temperature for ZnO where most of the densification process occurs. This same temperature range was also noted by Mazaheri et al. where they showed that the rate of sintering ZnO was most significant [Citation32]. With the in situ TEM heating capability, the specific range of temperature for rapid densification could be easily identified through direct observation in TEM.
Based on the in situ TEM heating results, we can observe the advantages of ultra-high heating rates for densifying ceramic samples, which could also apply to many of the new sintering techniques. However, there are limitations and challenges which remain in the implementation of this in situ TEM technique. Due to the limited projected view of TEM imaging, there could be overlapping of particles and removal of porosity in the direction of the electron beam which could not be observed. This makes the quantification of morphological changes challenging and will require either 3D tomography technique to be implemented [Citation41], or analysis through annular dark field image and EELS mass-thickness maps [Citation27]. In addition, the free surface effects during particle sintering in the TEM could differ from the particle sintering in bulk form, considering the particle arrangement and potential e-beam interactions during TEM observation. Although such free surface effects are likely to impact the sintering kinetics, the in situ TEM heating results are consistent with prior bulk sintering studies, which suggests that it has minimal impact on the overall sintering study.
5. Conclusions
This in situ TEM heating study sheds light on the effects of ultra-high heating rate on ceramic nanoparticle sintering. Using an ultra-high heating rate clearly has a very strong impact on densifying 3YSZ nanoparticles specifically. However, the effects of the ultra-high heating rate do not seem to carry over to the other two oxides tested in this work. For the case of 8YSZ, the differences between the ultra-high and slow heating rates were minimal, where the nanoparticles experienced limited densification even at an ultra-high heating rate. On the other hand, the sintering of ZnO nanoparticles using both ultra-high and low heating rates resulted in significant vapor transport at high temperatures. These direct observations through in situ TEM heating have revealed contrasting effects of ultra-high heating rates in various ceramic systems and will help to understand the densification behavior in the new sintering techniques, such as flash sintering, microwave sintering and ultra-fast high-temperature sintering.
Supplemental Material
Download MS Word (684.5 KB)Acknowledgements
This work was supported by the U.S. Office of Naval Research [Contract Nos.: N00014-16-1-2688 (DURIP in situ TEM holders), N00014-20-1-2043 (TEM) and N00014-17-1-2087 (flash sintering)].
Disclosure statement
No potential conflict of interest was reported by the author(s).
Additional information
Funding
References
- Lu K. Sintering of nanoceramics. Int Mater Rev. 2008;53:21–38.
- Chaim R, Levin M, Shlayer A, et al. Sintering and densification of nanocrystalline ceramic oxide powders: a review. Adv Appl Ceram. 2008;107:159–169.
- Chen I-W, Wang X-H. Sintering dense nanocrystalline ceramics without final-stage grain growth. Nature. 2000;404:168–171.
- Chu M, Rahaman MN, Jonghe LC, et al. Effect of heating rate on sintering and coarsening. J Am Ceram Soc. 1991;74:1217–1225.
- Su H, Johnson DL. Master sintering curve: a practical approach to sintering. J Am Ceram Soc. 1996;79:3211–3217.
- Rahaman MN. Ceramic processing and sintering [internet]. 2nd ed. Boca Raton: CRC Press; 2007.
- Brook RJ. Fabrication principles for the production of ceramics with superior mechanical properties. Proc Br Ceram Soc. 1982;32:7–24.
- Lin FJT, Jonghe LC, Rahaman MN. Initial coarsening and microstructural evolution of fast-fired and MgO-doped Al2O3. J Am Ceram Soc. 1997;80:2891–2896.
- García DE, Seidel J, Janssen R, et al. Fast firing of alumina. J Eur Ceram Soc. 1995;15:935–938.
- Jha SK, Phuah XL, Luo J, et al. The effects of external fields in ceramic sintering. J Am Ceram Soc. 2018;102:5–31.
- Ji W, Parker B, Falco S, et al. Ultra-fast firing: effect of heating rate on sintering of 3YSZ, with and without an electric field. J Eur Ceram Soc. 2017;37:2547–2551.
- Ji W, Zhang J, Wang W, et al. The microstructural origin of rapid densification in 3YSZ during ultra-fast firing with or without an electric field. J Eur Ceram Soc. 2020;40:5829–5836.
- Xu G, Lloyd IK, Carmel Y, et al. Microwave sintering of ZnO at ultra high heating rates. J Mater Res. 2001;16:2850–2858.
- Munir ZA, Quach D V, Ohyanagi M. Electric Current activation of sintering: a review of the pulsed electric current sintering process. J Am Ceram Soc. 2011;94:1–19.
- Grasso S, Sakka Y, Rendtorff N, et al. Modeling of the temperature distribution of flash sintered zirconia. J Ceram Soc Japan. 2011;119:144–146.
- Eqbal A, Arya KS, Chakrabarti T. In-depth study of the evolving thermal runaway and thermal gradient in the dog bone sample during flash sintering using finite element analysis. Ceram Int. 2020;46:10370–10378.
- Wang C, Ping W, Bai Q, et al. A general method to synthesize and sinter bulk ceramics in seconds. Science. 2020;368:521–526.
- Chen D-J, Mayo MJ. Rapid rate sintering of nanocrystalline ZrO2-3 mol% Y2O3. J Am Ceram Soc. 1996;79:906–912.
- Ewsuk KG, Ellerby DT, DiAntonio CB. Analysis of nanocrystalline and microcrystalline ZnO sintering using master sintering curves. J Am Ceram Soc. 2006;89:2003–2009.
- Wang CM, Li X, Wang Z, et al. In situ TEM investigation of congruent phase transition and structural evolution of nanostructured silicon/carbon anode for lithium ion batteries. Nano Lett. 2012;12:1624–1632.
- Zeng Z, Liang WI, Liao HG, et al. Visualization of electrode-electrolyte interfaces in LiPF 6/EC/DEC electrolyte for lithium ion batteries via in situ TEM. Nano Lett. 2014;14:1745–1750.
- Kwon J, Sharma AA, Bain JA, et al. Oxygen vacancy creation, drift, and aggregation in TiO2-based resistive switches at low temperature and voltage. Adv Funct Mater. 2015;25:2876–2883.
- Li C, Gao B, Yao Y, et al. Direct observations of nanofilament evolution in switching processes in HfO2-based resistive random access memory by in situ TEM studies. Adv Mater. 2017;29:1–8.
- Simonsen SB, Chorkendorff I, Dahl S, et al. Direct Observations of oxygen-induced platinum nanoparticle Ripening studied by In situ TEM. J Am Chem Soc. 2010;132:7968–7975.
- Challa SR, Delariva AT, Hansen TW, et al. Relating rates of catalyst sintering to the disappearance of individual nanoparticles during Ostwald ripening. J Am Chem Soc. 2011;133:20672–20675.
- Rankin J, Sheldon BW. In situ TEM sintering of nano-sized ZrO2 particles. Mater Sci Eng A. 1995;204:48–53.
- Majidi H, Holland TB, van Benthem K. Quantitative analysis for in situ sintering of 3% yttria-stabilized zirconia in the transmission electron microscope. Ultramicroscopy. 2015;152:35–43.
- Kocjan A, Logar M, Shen Z. The agglomeration, coalescence and sliding of nanoparticles, leading to the rapid sintering of zirconia nanoceramics. Sci Rep. 2017;7:2541.
- Majidi H, van Benthem K. Effects of non-contact electric fields on consolidation behavior of agglomerated yttria-stablized zirconia. Microsc Microanal. 2015;21:1511–1512.
- Shi J-L, Deguchi Y, Sakabe Y. Relation between grain growth, densification and surface diffusion in solid state sintering – a direct observation. J Mater Sci. 2005;40:5711–5719.
- Hotza D, García DE, Castro RHR. Obtaining highly dense YSZ nanoceramics by pressureless, unassisted sintering. Int Mater Rev. 2015;60:353–375.
- Mazaheri M, Zahedi AM, Sadrnezhaad SK. Two-step sintering of nanocrystalline ZnO compacts: effect of temperature on densification and grain growth. J Am Ceram Soc. 2007;91:56–63.
- Hynes AP, Doremus RH, Siegel RW. Sintering and characterization of nanophase zinc oxide. J Am Ceram Soc. 2002;85:1979–1987.
- Kim D-H, Kim CH. Effect of heating rate on pore shrinkage in yttria-doped zirconia. J Am Ceram Soc. 1993;76:1877–1878.
- Zhang J, Huang F, Lin Z. Progress of nanocrystalline growth kinetics based on oriented attachment. Nanoscale. 2010;2:18–34.
- Prajzler V, Salamon D, Maca K. Pressure-less rapid rate sintering of pre-sintered alumina and zirconia ceramics. Ceram Int. 2018;44:10840–10846.
- Lee IG, Chen I-W. Sintering and grain growth in tetragonal and cubic zirconia. Sinter. 1988;87:340–345.
- Gómez SY, da Silva AL, Gouvêa D, et al. Nanocrystalline yttria-doped zirconia sintered by fast firing. Mater Lett. 2016;166:196–200.
- Matsui K, Yoshida H, Ikuhara Y. Grain-boundary structure and microstructure development mechanism in 2–8mol% yttria-stabilized zirconia polycrystals. Acta Mater. 2008;56:1315–1325.
- Anselmi-Tamburini U, Woolman JN, Munir ZA. Transparent nanometric cubic and tetragonal zirconia obtained by high-pressure pulsed electric current sintering. Adv Funct Mater. 2007;17:3267–3273.
- Vanrompay H, Buurlage J, Pelt DM, et al. Real-time reconstruction of arbitrary slices for quantitative and in situ 3D characterization of nanoparticles. Part Part Syst Charact. 2020;37:2000073.