Abstract
The microstructure and composition evolution of FeCoNiCrMn high entropy alloy during extreme deformation with a strain rate of 108–109 s−1 induced by cold spray technology was investigated. In the region experiencing extremely large strain and high strain rate deformation, ultrafine nanograins with an average size of smaller than 100 nm were formed due to the occurrence of dynamic recrystallization. Additionally, the rapid redistribution of segregated Mn and Ni elements in extremely deformed FeCoNiCrMn was found for the first time. The reason for this phenomenon is the increased grain boundary area and dislocation density caused by extreme plastic deformation.
GRAPHICAL ABSTRACT
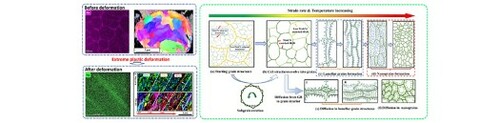
IMPACT STATEMENT
The redistribution of Mn and Ni elements was found in extremely deformed FeCoNiCrMn. This finding enriches our knowledge on the microstructure evolution mechanism of high entropy alloys under extreme deformation.
Introduction
When conventional metals or alloys are subjected to strong thermo-mechanically coupled effects in severe plastic deformation (SPD), the large strain and high strain rate normally result in the occurrence of unique microstructural evolution. For example, high strain rate is able to result in the refinement of coarse grains into nanosized grains, or the formation of amorphous phases [Citation1–5]. Also, the extreme thermo-mechanical history during SPD can lead to atomic diffusion and hence the formation of intermetallic [Citation6–9]. In recent years, high entropy alloys (HEAs) consisting of multi-principal elements with equiatomic or near-equiatomic concentration have been attracting great attentions due to their excellent mechanical and unique functional properties [Citation10]. Among all HEAs, FeCoNiCrMn with single FCC phase is one of the most investigated alloys due to its outstanding strength, ductility, and fracture toughness [Citation11]. The SPD of FeCoNiCrMn HEA has been studied in recent years, and it has been revealed that SPD significantly influences the microstructure evolution of FeCoNiCrMn such as the occurrence of grain refinement [Citation12–14], the phase transformation from FCC to HCP, and amorphization in solid state [Citation15]. However, the maximum strain rate that has been applied so far to induce the SPD of HEAs was approximately 106 s−1 [Citation15]. What happens to the microstructure and elemental composition at higher strain rates is still not understood. Such a research gap limits our understanding of the deformation mechanisms of novel HEAs. Therefore, the main objective of the current paper is to reveal the microstructure and local composition changes of FeCoNiCrMn under the extreme deformation at ultra-high strain rates of 108–109 s−1. For achieving the extremely high strain rate deformation, a so-called cold spray technology was applied to inject micro-sized FeCoNiCrMn particles onto a substrate at super-high speeds. The impact-induced adiabatic plastic deformation has an extremely high strain rate of approximately 108–109 s−1 [Citation16].
Materials and methods
An in-house cold spray system available in Trinity College Dublin was used to consolidate FeCoNiCrMn particles into a bulk sample. A detailed description of this process is provided in the Supplementary Document. The FeCoNiCrMn powder used in this work was supplied by Vilory Advanced Materials Technology Ltd, China. The powder had a spherical shape and a size range from 15 and 53 μm. Figure (a) shows the morphology of the FeCoNiCrMn powder taken by scanning electron microscope (SEM, Carl Zeiss Ultra Plus, Germany) where dendrite structures were clearly seen on the surface, and the grain structure at the cross-section of a powder particle characterized by electron backscatter diffraction (EBSD) inverse pole figure (IPF). The IPF also indicated that the powder had an average grain size of approximately 1.37μm. The slight change of the color in the grains and the high fraction of low angle misorientation as shown Fig. S2 indicated the existence of subgrains in grains. Figure (b) shows the high-angle annular dark-field (HADDF) image and the corresponding energy dispersive spectroscopy (EDS) mapping of a starting FeCoNiCrMn particle [Citation17]. As can be seen, the five principal elements were homogeneously distributed in most regions, while Mn and Ni were segregated in the boundaries of cell structures.
Figure 1. Characterization of the FeCoNiCrMn powder used in this work. (a) Surface morphology and EBSD IPF map showing the cross-sectional grain structure of a particle, and (b) HADDF and EDS mapping of a starting powder cross-section showing segregated elements in the boundaries of cell structures [Citation17].
![Figure 1. Characterization of the FeCoNiCrMn powder used in this work. (a) Surface morphology and EBSD IPF map showing the cross-sectional grain structure of a particle, and (b) HADDF and EDS mapping of a starting powder cross-section showing segregated elements in the boundaries of cell structures [Citation17].](/cms/asset/cf099908-ad4e-487b-baba-39340984d6fc/tmrl_a_2023678_f0001_oc.jpg)
In order to characterize the grain structure and element distribution of the highly deformed FeCoNiCrMn after cold spraying, a transmission electronic microscopy (TEM) foil was prepared by focused ion beam (FIB). The foil was taken from the interfacial region between the adjacent HEA particles where the particles experienced the highest strain rate during the impact-induced deformation [Citation18]. The FIB-prepared foil specimen was then characterized by FEI Tecnai G2 F20 transmission electron microscopy (TEM) and transmission Kikuchi diffraction (TKD) through SEM equipped with EBSD detector (Oxford Instruments). The element distribution was studied by using energy dispersive spectroscopy (EDS) mapping in scanning transmission electron microscope (STEM) equipped with the EDS detector (Oxford Instruments).
Results and discussion
Figure shows the BF-TEM images and TKD testing results including IPF and Kernel average misorientation (KAM) images. It can be seen that significant grain refinement occurred at the interparticle interfaces, which is the consequence of dynamic recrystallization. Because the particle impact velocity was extremely high, the time period of deformation was too short to induce long distance grain boundary migration. In this case, discontinuous dynamic recrystallization (DDRX) that relies on grain boundary migration could not be the refinement mechanism. Continuous dynamic recrystallization (CDRX) which is represented by the continuous increase of boundary misorientation via rotation of subgrains or dislocation cell structures is thus sensible to be considered as the dominant mechanism for the grain refinement [Citation1,Citation19–22].
Figure 2. Characterization of the highly deformed region of the FeCoNiCrMn after extreme deformation. (a) BF-TEM image showing the overall microstructure, the characteristic regions, and magnified microstructures (Figure ai and Figure aii) (b) TKD map showing the three characteristic regions. The TKD image was taken from the selected zone marked as white square in the BF-TEM image (Figure a). The interparticle interface was marked by red and yellow dash lines in the IPF map and KAM maps respectively.
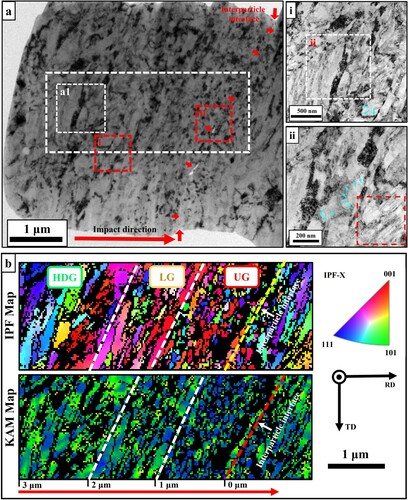
From the TKD results shown in Figure (b), three characteristic regions can be identified, namely, highly deformed grain (HDG) region, laminar grain (LG) region, and ultrafine grain (UG) region. The strain, strain rate and temperature in these three regions were estimated through finite element analysis (FEA) and the results are demonstrated in Table . The detailed description of the FEA model is provided in the Supplementary Document. It can be seen that the strain, strain rate and temperature increased as the distance getting closer to the interparticle interface because the plastic deformation became larger and larger along the direction from the particle interior to the interface. This is a typical microstructural feature of highly deformed cold sprayed particles [Citation23].
Table 1. Average grain size and calculated strain, strain rate and temperature in the starting powder and the three characteristic regions.
In order to further study the various microstructures in the three regions, a more detailed analysis is provided herein. In the HDG region, the DRX grains had an average size of 619 nm. The size of these grains was much smaller than that in the starting powder particles (i.e. 1.37 μm), which indicates the occurrence of CDRX in the HDG region. However, due to the lowest deformation condition among the three regions, the newly formed DRX grains could not be refined too much. In the LG region, strain and strain rate increased as compared to in the HDG region. Therefore, the finer DRX grains could be further deformed and refined into laminar shape with an average diagonal size of 156 nm. At the same time, it is also noticed that smaller substructures including dislocation cells (marked by teal arrows in Figure (ai, aii)) and nanotwins (marked by the red square in Figure (aii)) were formed in laminar grains. In the near-interface UG region where plastic deformation was the largest in the three regions, strain, strain rate and temperature were the highest as listed in Table . Under this condition, more dislocations could be generated during deformation, which then evolved into substructures including dislocation cell and twins [Citation24–26]. These substructures rotated or bulged out of the grain, forming ultra-fine nanoscale CDRX grains. As measured from the TEM images provided in the Supplementary Document, the smallest grain size in the UG region was ∼15 nm.
Moreover, in the UG region, the dislocation density was low due to the dissipation of dislocations through DRX. This could be confirmed by the low local misorientation as shown in the KAM image (Figure (b)). In the LG and HDG regions, the plastic deformation and DRX were less prominent, and hence local misorientation was higher than that in the UG region, which indicates higher dislocation density. In addition, from Figure (b), it is also found that the grains having higher dislocation density were mostly small and thin grains as marked by red arrows in the LG and HDG regions. This is attributed to the high density of geometrically necessary dislocations (GNDs) which resulted from large strain gradient [Citation27]. Note that the estimated strain gradient by FEA in the three regions was 0.16∼0.44 μm−1, which was large enough to induce high density of GNDs [Citation28–30]. Especially, for smaller grains, the density of GNDs was normally higher than that in larger grains and this is why higher dislocation density was only found in thinner and smaller [Citation27,Citation31,Citation32].
Figure (a,b) demonstrates the BF-TEM images and the corresponding EDS maps taken from the region I (in the boundary between the HDG and the LG region) and region II (in the UG region) marked by red dash-lines in Figure (a). By comparing the undeformed starting powder with the highly deformed region, one can notice that the Mn–Ni segregation evolved from network style (Figure (b)) into ribbon-like concentrated style (Figure (a,b)). These Mn–Ni-enriched ribbons mainly concentrated in the laminar grains as indicated by the red dash lines in the BF-TEM images, and they were separated by thicker grains. In addition, the Mn–Ni-enriched ribbons was thinner than the Mn–Ni segregation cell walls in the starting particle. However, it is interesting to note that the Mn–Ni-enriched ribbons could not be found in the equiaxed nanograins of the UG region as marked by two green lines in Figure (b). This phenomenon indicated the outstanding redistribution of segregated elements and the occurrence of long-distance atomic diffusion. But it should be noted that the deformation process here was finished within 30–60 ns that was too short for atoms to achieve a long-distance diffusion only by bulk diffusion. Moreover, one can also find that nanoscale Mn-rich precipitation with other element depleted appeared in the triple joint of laminar grains as marked by the white circles in Figure (a). Precipitation and decomposition phenomenon after long-time annealing of deformed FeCoNiCrMn has been widely reported and investigated [Citation12,Citation14,Citation33]. Therefore, the mechanism of segregated Mn–Ni redistribution and the formation of Mn-rich precipitation observed in this study must be different from previous reports, and these will be discussed in the following text.
Figure 3. EDS maps showing the element distribution of the regions selected from Figure (a). (a) EDS map for region Ⅰ, and (b) EDS map for region II. Dark-filed (DF) TEM showing the Mn precipitate at the triple joint of laminar grains was provided in the top-right corner of the BF-TEM image in Figure (a). The grain structures having segregated Ni and Mn were marked by red lines in the BF-TEM images. Mn precipitates were marked by white circle.
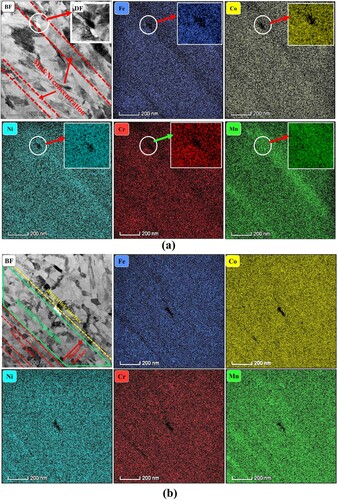
During the rapid solidification in the gas-atomisation process, dendrites as shown in Figure (a) were formed, and Mn and Ni concentrated in the interdendrite due to their low melting temperature [Citation34–38]. Moreover, the segregation of low melting elements induced large shrinkage stress and caused the twisting or rotation of dendrite, which consequently resulted in the formation of low angle grain boundaries (LAGB) in the interdendrite of the starting powder where Mn and Ni were also concentrated [Citation39,Citation40]. Therefore, the Mn–Ni segregated cell structures in the starting powder as shown in Figure (b) was actually the cross-sections of dendrite in Figure (a). These cell structures were separated by low angle grain boundary, and hence they could be considered as subgrains. These Mn–Ni segregated subgrains then participated in CDRX and influenced the compositional redistribution. Additionally, it has been found that Mn had the highest diffusion rate among the five principal elements in FeCoNiCrMn and the sluggish diffusion of Ni vanished when Ni atoms diffused along the grain boundary [Citation17,Citation28,Citation41]. Therefore, long distance atomic migration was prone to occur for Mn and Ni in FeCoNiCrMn.
Figure shows the schematic to explain the element redistribution process during the extreme deformation. Originally, Mn and Ni were segregated in the interdendrite, and subgrain boundaries were formed in the starting powders (Figure (a)). During the deformation, the subgrains with LAGB evolved into high angle grain boundaries (HAGB) via continuous rotation, and the average grain size decreased. Due to the grain refinement, the grain boundary area considerably increased. The large area of grain boundaries provided a large number of shortcuts for the diffusion of Ni and Mn. Thus, the segregated Ni and Mn diffused along newly formed grain boundaries (Figure (b–f)). Since this process was accompanied by grain structure evolution in the deformation, segregated elements can wildly disperse in the newly formed grain boundary network within tens of nanoseconds.
Figure 4. Schematic showing the redistribution process of the Mn and Ni elements during extreme deformation. (a) Mn and Ni are initially segregated in interdendrite and subgrains are formed; (b) with deformation going on, low angle grain boundary subgrains become high angle grain boundaries; (c) newly formed grains are deformed into laminar shape; (d) When the deformation becomes severest, large amounts of substructures are formed and transferred into equiaxed nanograins. At the same time segregated Ni and Mn diffusion along the grain boundary and create concentration gradient between the grain boundary and interior; (e) in the laminar grains, atoms diffuse into thinner grain; (f) in equiaxed DRX grain, segregated elements uniformly diffuse into nanograins.
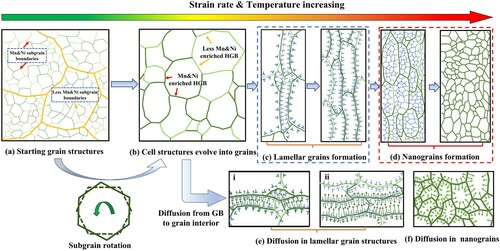
At the same time, the segregated Mn and Ni in the grain boundaries also created an elemental concentration gradient decreasing from the grain boundary to the inner part of the grain, which provided a driving force for the segregated elements to diffuse from grain boundaries into the grain interior (Figure (e–f)). Meanwhile, the deformation-induced high temperature intensified the atomic vibration and production of vacancies, which reduced the energy barrier for atomic diffusion. These factors worked together to promote the Ni and Mn diffusing from the grain boundaries into the grains.
For the equiaxed nanograins in the UG region, grains were heavily refined to less than 100 nm and grain boundary area was much higher than in the other regions. The temperature was the highest among the three regions as well. Thus, the segregated Ni and Mn could instantly diffuse along the grain boundaries and quickly diffused into the grain interior as shown in Figure (e), which finally resulted in a homogenous compositional distribution. In the other regions, the grain size was larger, and consequently the concentration gradient of the segregated elements was lower, which led to a lower diffusion driving force. Meanwhile, the temperature in these regions was lower as addressed in Table , which weakened the atomic migration. Therefore, the inward diffusion from the grain boundary to the grain interior was suppressed.
However, as compared with the equiaxed nanograin region in the UG region, the other regions had higher dislocation density. It is interesting to note that the lamellar grain as marked by the white circle on the right side of the BF images in Figure (a) had higher dislocation density than that in the neighbor grain structure on the left side and the thick Mn ribbon was located in the grains with higher dislocation density as shown in Fig.S5, which indicated the dependency of redistribution to dislocation density. It is known that dislocations can act as tunnels for atomic diffusion since they could reduce the energy barrier for diffusion by dissipating their stored strain energy [Citation42]. In this case, the role of dislocation density in the diffusion became apparent in the LG, HDG and the rest of the UG regions. Furthermore, it is known that, for a single grain in polycrystalline materials, dislocation density near the grain boundary is higher than that in the grain interior [Citation43]. Herein, high strain rate induced a high dislocation multiplication rate and the ultra-high strain gradient resulted in the formation of GNDs, which consequently promoted the dislocation accumulation. The highly accumulated dislocations in the grain boundary provided extra pathways for segregated Mn and Ni atoms to diffuse into the grain interior, which partially compensated for the negative effect of lower temperature and the reduction of diffusion driving force due to increased grain size. For a thinner grain, it had higher dislocation density than larger grain due to their small volume and higher GNDs density. Moreover, compared with coarser grains, the concentration gradient of Mn and Ni in thinner grains was also higher, which led to higher diffusion driving force. Consequently, as described in Figure (e), segregated elements were prone to diffuse into thinner grains. Finally, two thinner ribbon-like Mn and Ni enriched grains which were separated by a thicker grain without outstanding element enrichment was formed (Figure ).
As for the Mn-rich precipitation observed in the triple joint of grains (Figure (a)), it can be seen in Figure (b) that the concentration of segregated elements in the cell boundaries was inhomogeneous. Atomic diffusion rate in grain boundaries could be influenced by grain boundaries area and misorientations [Citation44]. Therefore, during the grain structure evolution, the concentration of segregated elements could not redistribute homogeneously in the grain boundary network. In certain positions, the concentration of segregated elements may be sufficiently high to trigger precipitation nucleation. Because this process occurred in grain boundaries, the formation of precipitation was promoted due to heterogeneous nucleation. In the triple joint of grains, heterogeneous nucleation was more prone to occur [Citation33,Citation45]. Consequently, Mn-rich precipitation was mainly detected in the triple joint of grains as shown in Figure (a).
Conclusions
In summary, a systematic investigation was conducted to study the microstructure evolution and composition redistribution of FeCoNiCrMn HEA under extreme deformation at ultra-high strain rate of 108–109 s−1 in this paper. The results found in this work showed some interesting phenomena with regard to high entropy alloys. It is found that the coarse micro-sized grains were significantly refined into nano-sized grains after extreme deformation due to the occurrence of DRX. Different extents of plastic deformation led to refined grains with different sizes. At the region experiencing extremely large strain and high strain deformation, ultrafine nanograins with average size of smaller than 100 nm were achieved. In addition, for the first time, the deformation-induced rapid redistribution of Mn and Ni elements were revealed in FeCoNiCrMn HEA. The reason for this phenomenon is the consequence of microstructural change, i.e. the increase of grain boundary area and dislocation density, due to extreme plastic deformation.
Supplemental Material
Download MS Word (1.6 MB)Disclosure statement
No potential conflict of interest was reported by the author(s).
Additional information
Funding
References
- Liu ZY, Wang HZ, Hache M, et al. Formation of refined grains below 10 nm in size and nanoscale interlocking in the particle-particle interfacial regions of cold sprayed pure aluminum. Scr Mater. 2020;177:96–100.
- Villegas JC, Shaw LL. Nanocrystallization process and mechanism in a nickel alloy subjected to surface severe plastic deformation. Acta Mater. 2009;57:5782–5795.
- Valiev RZ, Islamgaliev RK, Alexandrov IV. Bulk nanostructured materials from severe plastic deformation. Prog Mater Sci. 2000;45:103–189.
- Chen M, McCauley JW, Hemker KJ. Shock-induced localized amorphization in boron carbide. Science. 2003;299:1563–1566.
- Li SZ, Pastewka L, Gumbsch P. Glass formation by severe plastic deformation of crystalline Cu vertical bar Zr nano-layers. Acta Mater. 2019;165:577–586.
- Wang M, Averback RS, Bellon P, et al. Chemical mixing and self-organization of Nb precipitates in Cu during severe plastic deformation. Acta Mater. 2014;62:276–285.
- Bachmaier A, Pippan R. Generation of metallic nanocomposites by severe plastic deformation. Int Mater Rev. 2013;58:41–62.
- Romankov S, Park YC, Shchetinin IV, et al. Atomic-scale intermixing, amorphization and microstructural development in a multicomponent system subjected to surface severe plastic deformation. Acta Mater. 2013;61:1254–1265.
- Sauvage X, Wetscher F, Pareige P. Mechanical alloying of Cu and Fe induced by severe plastic deformation of a Cu-Fe composite. ACTA Mater. 2005;53:2127–2135.
- George EP, Raabe D, Ritchie RO. High-entropy alloys. Nat Rev Mater. 2019;4:515–534.
- George EP, Curtin WA, Tasan CC. High entropy alloys: a focused review of mechanical properties and deformation mechanisms. Acta Mater. 2020;188:435–474.
- Park JM, Moon J, Bae JW, et al. Strain rate effects of dynamic compressive deformation on mechanical properties and microstructure of CoCrFeMnNi high-entropy alloy. Mater Sci Eng A. 2018;719:155–163.
- Li Z, Zhao S, Alotaibi SM, et al. Adiabatic shear localization in the CrMnFeCoNi high-entropy alloy. Acta Mater. 2018;151:424–431.
- Schuh B, Mendez-Martin F, Völker B, et al. Mechanical properties, microstructure and thermal stability of a nanocrystalline CoCrFeMnNi high-entropy alloy after severe plastic deformation. Acta Mater. 2015;96:258–268.
- Zhao S, Li Z, Zhu C, et al. Amorphization in extreme deformation of the CrMnFeCoNi high-entropy alloy. Sci Adv. 2021;7:eabb3108.
- Yin S, Cavaliere P, Aldwell B, et al. Cold spray additive manufacturing and repair: fundamentals and applications. Addit Manuf. 2018;21:628–650.
- Zhang Y, Bian T, Shen X, et al. Sintering mechanism and microstructure evolution of a CoCrFeNiMn high entropy alloy fabricated by metal injection molding. J Alloys Compd. 2021;868:158711.
- Assadi H, Kreye H, Gärtner F, et al. Cold spraying – a materials perspective. Acta Mater. 2016;116:382–407.
- Huang K, Logé RE. A review of dynamic recrystallization phenomena in metallic materials. Mater Des. 2016;111:548–574.
- Sakai T, Belyakov A, Kaibyshev R, et al. Dynamic and post-dynamic recrystallization under hot, cold and severe plastic deformation conditions. Prog Mater Sci. 2014;60:130–207.
- Pan X, Wang X, Tian Z, et al. Effect of dynamic recrystallization on texture orientation and grain refinement of Ti6Al4 V titanium alloy subjected to laser shock peening. J Alloys Compd. 2021;850:156672.
- Lu JZ, Wu LJ, Sun GF, et al. Microstructural response and grain refinement mechanism of commercially pure titanium subjected to multiple laser shock peening impacts. Acta Mater. 2017;127:252–266.
- King PC, Zahiri SH, Jahedi M. Microstructural refinement within a cold-sprayed copper particle. Metall Mater Trans A. 2009;40:2115–2123.
- Humphreys FJ, Hatherly M. Recrystallization and related annealing phenomena. Oxford: Elsevier; 2012.
- Derby B. The dependence of grain size on stress during dynamic recrystallisation. Acta Metall Mater. 1991;39:955–962.
- Mecking UFK. Physics and phenomenology of strain hardening: the FCC case. Prog Mater Sci. 2003;48:171–273.
- Fleck NA, Muller GM, Ashby MF, et al. Strain gradient plasticity: theory and experiment. Acta Metall Mater. 1994;42:475–487.
- Liu XC, Zhang HW, Lu K. Strain-induced ultrahard and ultrastable nanolaminated structure in nickel. Science. 2013;342:337–340.
- Zhu C, Harrington T, Gray GT, et al. Dislocation-type evolution in quasi-statically compressed polycrystalline nickel. Acta Mater. 2018;155:104–116.
- Pan X, He W, Huang X, et al. Plastic deformation behavior of titanium alloy by warm laser shock peening: microstructure evolution and mechanical properties. Surf Coatings Technol. 2021;405:126670.
- Zhang J, Wang B, Wang H. Geometrically necessary dislocations distribution in face-centred cubic alloy with varied grain size. Mater Charact. 2020;162:110205.
- Littlewood PD, Britton TB, Wilkinson AJ. Geometrically necessary dislocation density distributions in Ti–6Al–4V deformed in tension. Acta Mater. 2011;59:6489–6500.
- Otto F, Dlouhý A, Pradeep KG, et al. Decomposition of the single-phase high-entropy alloy CrMnFeCoNi after prolonged anneals at intermediate temperatures. Acta Mater. 2016;112:40–52.
- Laurent-Brocq M, Akhatova A, Perrière L, et al. Insights into the phase diagram of the CrMnFeCoNi high entropy alloy. Acta Mater. 2015;88:355–365.
- Cantor B, Chang ITH, Knight P, et al. Microstructural development in equiatomic multicomponent alloys. Mater Sci Eng A. 2004;375–377:213–218.
- Prashanth KG, Eckert J. Formation of metastable cellular microstructures in selective laser melted alloys. J Alloys Compd. 2017;707:27–34.
- Wang YM, Voisin T, McKeown JT, et al. Additively manufactured hierarchical stainless steels with high strength and ductility. Nat Mater. 2018;17:63–71.
- Zhu ZG, Nguyen QB, Ng FL, et al. Hierarchical microstructure and strengthening mechanisms of a CoCrFeNiMn high entropy alloy additively manufactured by selective laser melting. Scr Mater. 2018;154:20–24.
- Napolitano RE, Schaefer RJ. The convergence-fault mechanism for low-angle boundary formation in single-crystal castings. J Mater Sci. 2000;35:1641–1659.
- Wagner A, Shollock BA, McLean M. Grain structure development in directional solidification of nickel-base superalloys. Mater Sci Eng A. 2004;374:270–279.
- Beke DL, Erdélyi G. On the diffusion in high-entropy alloys. Mater Lett. 2016;164:111–113.
- Hart EW. On the role of dislocations in bulk diffusion. Acta Metall. 1957;5:597.
- Humphreys FJ, Hatherly M. Chapter 4 – the structure and energy of grain boundaries. In: Humphreys FJ, Hatherly M, editors. Recrystallization and related annealing phenomena. 2nd ed. Oxford: Elsevier; 2004. p. 91–119.
- Paul A, Laurila T, Vuorinen V, et al. Thermodynamics, diffusion and the Kirkendall effect in solids. Cham: Springer; 2014.
- Glienke M, Vaidya M, Gururaj K, et al. Grain boundary diffusion in CoCrFeMnNi high entropy alloy: kinetic hints towards a phase decomposition. Acta Mater. 2020;195:304–316.