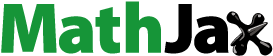
Abstract
The correlations between tensile properties and some common parameters in BCC refractory multi-principal element alloys (RMPEAs) have been systematically investigated. The findings can be used as guidelines for the alloy design. We found that there exists a positive linear correlation between average atomic shear modulus mismatch and yield strength, and more negative enthalpy of mixing is peculiarly prone to brittle fracture in RMPEAs. Meanwhile, some BCC RMPEAs with first-class tensile properties were designed successfully. The analyses of alloys’ toughen mechanism revealed that their high strength, as well as good ductility, is attributed to lattice distortion and dislocation glide respectively.
GRAPHICAL ABSTRACT
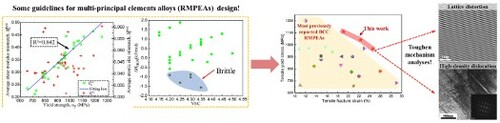
IMPACT STATEMENT
This work provided some effective guidelines for the design of BCC refractory multi-principal element alloys with superior strength-ductility combinations via utilizing several common physical parameters.
1. Introduction
Designing alloys with multiple-principal elements is a novel alloy-design strategy, which has been widely adopted in the search for alloys with superior mechanical properties [Citation1–3]. A sub-group of these multiple principal element alloy (MPEA) systems, composed of refractory elements (e.g., titanium, zirconium, hafnium, vanadium, niobium, tantalum, molybdenum, and tungsten), has recently drawn much attention for their potential application at elevated temperature [Citation4–7]. A series of RMPEAs with high strength have been reported in recent years, however, most of them exhibit brittle fractures in tensile stress or limited ductility at room temperature [Citation8–11]. Serious efforts have been devoted to boosting the ductility of RMPEAs, and the most common approach is utilizing intrinsically ductile metals (i.e., titanium, zirconium, hafnium, vanadium, niobium, tantalum) to design the alloys. However, only a few compositions possessing tensile ductility have been discovered [Citation12,Citation13], and their ductility always declines rapidly with increasing yield strength [Citation14,Citation15].
There are two obstacles to design high-performance RMPEAs. First, the strategies of designing RMPEAs frequently rely on high-entropy alloys design concepts, such as mixing entropy (ΔSmix) ≥ 1.5R and ‘equiatomic or near-equiatomic', which have hindered the discovery of high-performance composition [Citation11]. There is a vast compositional space to design the alloys with superior mechanical properties in the RMPEAs group [Citation4,Citation16]. Second, it is still hard to predict the alloy compositions that may possess attractive strength and tensile ductility via qualitative or quantitatively-predictive theories. For example, a few solid-solution strengthening models have been developed to estimate yield strength in multi-principal element alloys, but some parameters of solid-solution strengthening models are still ambiguous in different subsets of the RMPEAs system [Citation17–19]. The valence electron concentration (VEC) theory is an important criterion to predict the ductile-to-brittle transitions, suggesting that RMPEAs with VEC ≤ 4.5 tends to be ductile, and the alloys tend to be brittle when VEC > 4.5 [Citation20]. However, the VEC criterion doesn’t apply to all RMPEAs [Citation21,Citation22]. The absence of a sufficiently wide range of data is the critical obstacle for the development of criteria to anticipate RMPEAs’ mechanical properties [Citation21,Citation22].
Here, we focus on the BCC RMPEAs with VEC ≤ 4.5, to search alloys possessing a good combination of strength and ductility. The first step of our work involves establishing a tensile properties dataset for these RMPEAs. Subsequently, we tried to systematically analyze some common and easy-to-obtain parameters to explore correlations capable of predicting strength and ductility in RMPEAs, and provide some effective guidelines for the design of RMPEAs with excellent mechanical properties. Five important parameters of these RMPEAs have been considered (e.g., delta parameter (δ) (which determines the atomic-size difference in multicomponent alloys), enthalpy of mixing , mixing entropy
, electronegativity difference (Δχ) and VEC). These parameters are related to the collective behavior of the constituent elements. The calculation methods of them are based on the Eqns. (S1-7), which are given as supplementary information. Moreover, the average values of shear modulus mismatch and atomic radius mismatch relating to the solid-solution strengthening have been defined via Li’s solid solution strengthening model [Citation19] and described in Eqns. (S8-14). All the data for the calculations used in this work are shown in Tables S1-2.
2. Experimental methods
All alloys were prepared by arc melting high purity metal (> 99.95 wt. %) in an argon atmosphere. Ingots were obtained through drop-casting of the melt into a copper mold (10 mm × 10 mm × 50 mm) cooled by water. The stress–strain curves were obtained using an MTS universal electronic tensile testing machine at a strain rate of 1 × 10−3 s−1 at room temperature. The elongation of samples was measured by a mechanical extensometer. The dog-bone-shaped tensile samples with a gauge length of 15 mm and cross-section of 2 × 4.0 mm2 were sectioned from the ingots using an electrical discharge cutting machine. At least 4 samples were tested for each componential condition to ensure reproducibility and yield good statistics. X-ray diffraction (XRD) with Cu Kα radiation was conducted to identify the phase structure of the alloys. The microstructures, elemental distributions, and tensile fracture morphologies at the micro-scale were characterized using a scanning electron microscope (SEM) equipped with Oxford electron backscatter diffraction (EBSD) and energy dispersive spectrometer (EDS) systems. Micro- and nano-scale characterizations were performed in a transmission electron microscope (TEM, Talos F200X) at 200 kV.
3. Results and discussion
Figure (a) shows the relationships among average shear modulus mismatch , average atomic radius mismatch
and tensile yield strength (σy) in as-cast BCC refractory multi-principal element alloys (RMPEAs) from our dataset (Table S4). Figure (a1) shows the dependence of
on
and
, respectively. A positive linear correlation between
and
can be observed, where the strength increases with the increase of
. Although the proportional correlation between
and
cannot be found, it still shows a trend that
displayed a superimposed effect in increasing or decreasing the yield strength in some RMPEAs in our dataset. To better reflect the superimposed effect of
and
on
, these three data are superimposed and shown in a contour plot (Figure (a2)). The figure exhibits a trend that the strength of RMPEAs can be enhanced with the increase of
and
. Figure (b) shows the effects of atomic-size differences (δ), valence electron concentration (VEC), and enthalpy of mixing
on tensile fracture elongation (ϵ) (the correlations between ϵ and other two parameters are shown in Fig. S1). Here, the RMPEAs with tensile elongation of less than 5% are classified as brittle alloys. The correlation between the ϵ and δ is weak as shown in Figure (b1), despite it was stated in the literature that a reduction of δ can improve multi-principal element alloys’ ductility [Citation23,Citation24]. All the RMPEAs in this work possess VEC ≤ 4.5, but their elongations generally range from 1.4 to 26%, as shown in Figure (b2), which means the VEC ductility criterion cannot be broadly supported in our dataset of RMPEAs. Figure (b3) shows the correlation between ϵ and
. The figure shows all the RMPEAs in our dataset with
less than about - 0.88 kJ/mol (yellow region) are brittle. To better reflect the VEC and
affecting the ductility, these two parameters are superimposed, as shown in Figure (b4). We find that most RMPEAs with VEC ≤ 4.5 can possess good tensile ductility excluding some of them with relatively low
in our dataset.
is a critical parameter about the bonding state and lower (more negative)
means a greater tendency to form the brittle intermetallic compounds in multi-principal alloys [Citation25,Citation26]. Thus, it is acceptable to treat
as an important factor to anticipate the ductility in RMPEAs. In summary, there are two guidelines about high-performance RMPEAs design. First, the yield strength increases with the increase of average shear modulus mismatch monotonously, and increasing the average atomic radius mismatch can provide a synergistic effect in enhancing the strength in RMPEAs. Second, avoiding too negative mixing enthalpy (higher than -0.88 kJ/mol may be better) as well as following the VEC criteria can contribute to discover the RMPEAs with high ductility.
Figure 1 The analyses of the correlations capable of predicting tensile yield strength or ductility via a dataset comprising a series of RMPEAs with VEC ≤ 4.5. (a) Relationships among average shear modulus mismatch , atomic radius mismatch
and yield strength
; (b) effects of atomic-size differences (δ), valence electron concentration (VEC), and enthalpy of mixing
on tensile fracture elongation (ϵ).
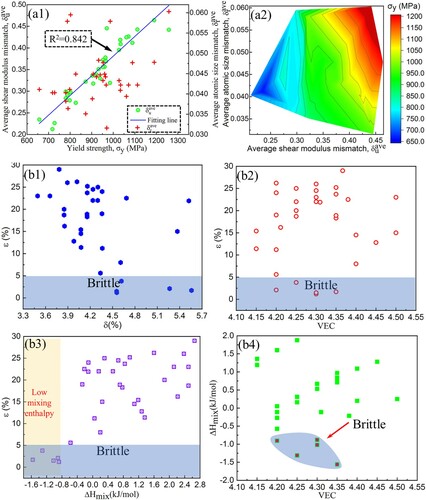
Figure 2. (a) The true stress-strain curves and corresponding data for three representative RMPEAs; (b) the tensile strength-ductility combination in comparison with previously reported BCC RMPEAs [Citation4,Citation12,Citation13,Citation27–34].
![Figure 2. (a) The true stress-strain curves and corresponding data for three representative RMPEAs; (b) the tensile strength-ductility combination in comparison with previously reported BCC RMPEAs [Citation4,Citation12,Citation13,Citation27–34].](/cms/asset/1a3777dc-7d91-4831-a975-b1d4964eedfb/tmrl_a_2024615_f0002_oc.jpg)
Figure 3. Microscopic structure studies for (a) Nb20Ta5, (b) Nb15Ta10 and Nb10Ta15, respectively. (a1-c1) The IPF maps and corresponding grain size distributions; (a2-c2) the BSE-SEM images; (a3-c3) the elemental distribution maps.
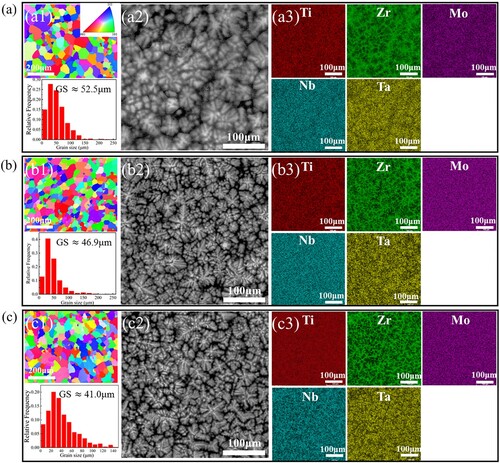
Figure 4. (a) XRD spectra and the BCC phase map and (b) the bright-field TEM images with corresponding SAED patterns of Nb20Ta5, Nb15Ta10 and Nb10Ta15 alloys, respectively; (c-d) the HRTEM micrographs and Fourier-filtered transformed (FFT) image for (-2 0 0) planes of Nb20Ta5 and Nb10Ta15 alloys, respectively.
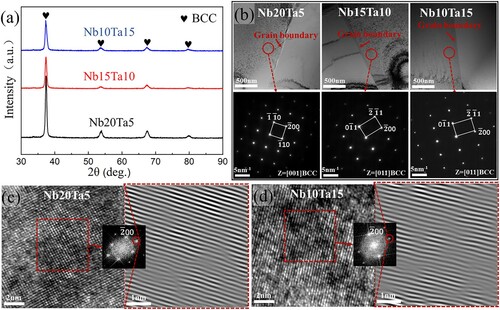
Figure 5 Analysis of fracture mechanism performed in Nb20Ta5 and Nb10Ta15. (a) Optical image of the tensile fracture specimen and the red frame position indicates the interest region for the following EBSD and TEM analyses; (b-c) SEM images of the fractured surfaces; (d-e) lateral morphology of the tensile fracture sample; (f-g) the IPF maps from the near tensile fracture region; and corresponding point-point misorientation analyses from the typical lenticular structure; (h-i) the bright-field TEM images and corresponding SAED patterns for the fractured specimens; (j-k) the dislocation patterning for the fractured specimen in Nb20Ta5 alloy.
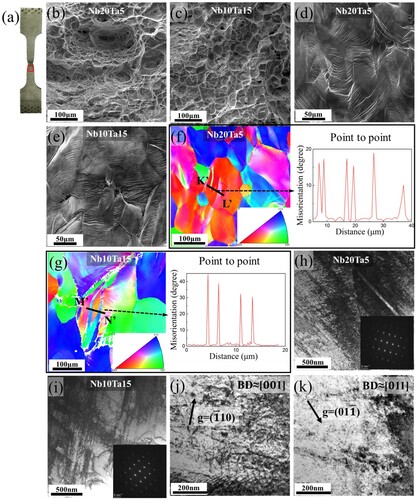
In this work, several RMPEAs possessing superior mechanical properties were designed successfully that are presented in Table S4. The tensile properties of three representative RMPEAs among them are shown in Figure (a). Three alloys have high yield strength approximately ranging from 0.97 GPa to 1.11 GPa, and excellent tensile elongation ranging from 19.1 to 24.6%. Correspondingly, the average shear modulus mismatches of three alloys ranged from about 0.37 to 0.44, and their average atomic size mismatches are similar (∼ 0.0433). All of them possess low VEC (4.35) and > 0.7 kJ/mol. The tensile strength-ductility combinations achieved in the previously reported RMPEAs are included in Figure (b). Our newly designed RMPEAs stand out, with a synergy of excellent strength and ductility. Considering the composition of these alloys, we found the introduction of Mo can effectively raise the shear modulus mismatch and enhance the strength in RMPEAs. Moreover, the Ta content in a certain range also can effectively improve the strength of RMPEAs, due to its higher shear modulus than other refractory elements in group IV and V. Increasing Ta content from 5 at. % (Nb20Ta5) to 15 at. % (Nb10Ta15), their average shear modulus mismatch raised from 0.37 to 0.44, and the corresponding yield strength increased from about 0.97 GPa to 1.1 GPa, as shown in Figure (a). However, we point out that 5 at. % for Mo or 15 at. % for Ta may not be the optimal values and additional research is needed to optimize the alloys’ composition.
Here, to reveal the underlying toughen mechanism of these high-performance RMPEAs, we have investigated the microstructure of all three as-cast RMPEAs (i.e., Nb20Ta5, Nb15Ta10, and Nb10Ta15) in detail. Figure (a1-c1) show the inverse pole figure (IPF) maps and corresponding grain size distributions of three samples. The IPF maps reveal that the grain-orientation distributions of these samples are random (see the top right insert). The specific grain sizes (GS) evaluated from the grain orientation maps are shown in the normal distribution statistics, and the average grain sizes are about 52.5, 46.9, and 41.0 μm for Nb20Ta5, Nb15Ta10, and Nb10Ta15 respectively. It can be deduced that the changes in strength for three alloys are not due to the Hall-Petch or size effects, for their average grain sizes are quite similar. Figure (a2-c2) show the representative backscattered electron (BSE) scanning electron microscope (SEM) image of three alloys. All three BSE-SEM images exhibit the dendritic structure composing light-gray and dark-gray contrast. We conducted an energy dispersive spectroscopy (EDS) analysis of these dendritic structures and the results are shown in (a3-c3). Our data reveals that Zr and Ta tend to segregate during the solidification processes, whereby Zr is enriched in the inter-dendritic region and Ta in the dendrite core. Ti also possesses a weak tendency to segregate in the inter-dendrite region. The other two high melting point elements (i.e., Nb, Mo) exhibit a similar segregation tendency with Ta, but this trend is weak. These elemental segregation results may contribute from the element’s melting point and enthalpy of mixing differences [Citation35,Citation36]. It should be pointed out that the elemental segregation existence will not significantly affect the strength of the alloys in current work, which can be confirmed in supplementary Fig. S2 and Fig. S3.
We employed X-ray diffraction (XRD) to identify the phase structure for three alloys, as shown in Figure (a). The XRD pattern reveals that all three alloys have a single body-centered cubic (BCC) phase, which indicates that the componential segregation cannot change their BCC structure. Figure (b) shows the bright-field images and corresponding selected area electron diffraction (SAED) patterns of these alloys. Owing to the presence of elemental segregation, SAED analysis was conducted on the region near the grain boundary in as-cast specimens. The result demonstrates no presence of a secondary phase in all three alloys. Subsequently, high-resolution TEM (HRTEM) was employed to further study the lattice structure of two representative alloys (i.e., Nb20Ta5 and Nb10Ta15), as shown in Figure (c-d). The lattice distortions are visible through heterogeneous fringe separation from the HRTEM images of the Nb20Ta5and Nb10Ta15 alloys. The obvious kinks and bends in the lattice structures are revealed in the inverse Fourier-filtered transformed (FFT) images from (00) planes (as shown in right figures) both in Nb20Ta5and Nb10Ta15 alloys, indicating the existence of the lattice distortions in our alloys. Lattice distortion of alloys can serve as a strengthening mechanism for introducing an energy barrier that first needs to be overcome before dislocation movement [Citation37]. And severe lattice distortion is a core effect in determining the yield strength for multi-principal element alloys [Citation38]. Combining with the above microstructure research results, we concluded that the high strength of our alloys was vastly contributed by the lattice distortion effect. Furthermore, the lattice distortion effect arises from significant atomic radius mismatch and modulus mismatch [Citation19], which is consistent with above mention findings of the dependency of strength on average shear modulus mismatch and the average atomic radius mismatch.
The detailed analyses of the fracture mechanism was performed in Nb20Ta5 and Nb10Ta15 alloys synchronously. Figure (a) shows the optical image of the tensile fracture specimen. The red frame position indicates the interest region for the following EBSD and TEM analyses. Figure (b-c) show the SEM images of the fractured surface. The figures reveal that the samples are covered with ductile dimples and without any faceted cleavages, indicating a typical ductile fracture. Figure (d-e) show the extensive slip bands and noticeably elongated grains both in Nb20Ta5 and Nb10Ta15. Although there are giant shear offsets between bands, the intergranular cracks cannot be found Nb20Ta5, indicating the alloy possesses excellent plastic deformation ability. Since Nb10Ta15 alloy was subjected to higher stresses during deformation, we can find the intragranular or intergranular micro-cracks in some severely deformed grains. However, these cracks only occur in a single crystal, ensuring excellent tensile ductility in Nb10Ta15. Moreover, a dense of wavy slip bands can be seen in both two alloys, which reveals frequent dislocation cross-slips are occurring in the deformation process. Figure (f-g) show the IPF maps from EBSD analysis for the tensile fracture specimens. Some lenticular structures can be observed in the IPF maps, and most of them originate from the grain boundaries and terminate inside the grains. The point-to-point misorientations crossing the typical lenticular structures (along the ‘KL’ line in Nb20Ta5 and ‘MN’ line in Nb10Ta15) show that the angles are lower than the characteristic 50.5° angle of {332}β<113>β twins or the 60° angle of {112}β<111>β twins in BCC titanium alloys [Citation39,Citation40]. This result indicates that the dominant deformation mechanisms are ordinary dislocation glide both in two alloys. To further reveal the fracture mechanism of the alloys, we conducted TEM analysis on the tensile fracture samples. From Figure (h-i), the high-density dislocations and planar arrays of high dislocation density walls can be observed. Through the bright-field TEM images and SAED pattern, we found that no phase transformations or mechanical twinning occurred during the deformation process both in Nb20Ta5 and Nb10Ta15 alloys. In the Nb20Ta5 alloy, the dislocations are visible with a reflection vector (g) of (Figure (j)), while being out of contrast with 01
(Figure (k)). Thus, the Burgers vector of dislocations is ±1/2 [
11], which is similar to conventional refractory high entropy alloys [Citation41,Citation42]. Furthermore, the dislocations sub-structure is marked by the presence of numerous debris as shown in Figure (j), reflecting the intrinsic ability to cross-slip for the alloy [Citation43]. Thus, we conclude that the extensive dislocation actions, especially, the actions of dislocation cross-slip have contributed to the excellent ductility in our newly designed RMPEAs.
4. Conclusions
In conclusion, we have investigated a series of refractory multi-principal element alloys (RMPEAs) to search for high-performance ones and develop some guidelines for designing these alloys. We find that the yield strength increases with the increase of average shear modulus mismatch monotonously, and increasing the average atomic radius mismatch can provide a synergistic effect in enhancing the strength in RMPEAs. Moreover, avoiding too negative mixing enthalpy (higher than -0.88 kJ/mol may be better) as well as following the VEC criteria can contribute to discover the RMPEAs with high ductility. Although the above guidelines still need more data and additional work to establish a statistical significance, they are still instructive for the design of RMPEAs with good mechanical performance. Meanwhile, some novel RMPEAs with exceptional combinations of high strengthen and good ductility were developed successfully, and some of them are superior to most of the currently existing RMPEAs. The underlying toughen mechanism studies were conducted on the representative high-performance alloys, indicating that their high strengths mainly originate from severe lattice distortion effect and the high ductility are dominated by extensive dislocation actions. Our work has not only successfully designed several high-performance RMPEAs, but also provided semi-empirical alloy-design guidelines, which cast new light on the exploration of RMPEAs with unprecedented mechanical properties.
Supplemental Material
Download MS Word (2.3 MB)Acknowledgments
This work was supported by supported by National Key R&D Program of China (2017YFB0305100, 2017YFB0305104), the Science and Technology Planning Project of Guangdong Province No. 2017B090903005 and the Education Department of Guangdong Province No. 2020ZDZX2024. XJW acknowledges the Fundamental Research Funds for the Central Universities (No. 21620110).
References
- Yeh JW, Chen SK, Lin SJ, et al. Nanostructured high-entropy alloys with multiple principal elements: novel alloy design concepts and outcomes. Adv Eng Mater. 2004;6(5):299–303.
- Gludovatz B, Hohenward A, Catoor D, et al. A fracture-resistant high-entropy alloy for cryogenic applications. Science. 2014;345(6201):1153–1158.
- Yang T, Zhao YL, Tong Y, et al. Multicomponent intermetallic nanoparticles and superb mechanical behaviors of complex alloys. Science. 2018;362:933–937.
- Wei SL, Kim SJ, Kang JY, et al. Natural-mixing guided design of refractory high-entropy alloys with as-cast tensile ductility. Nat Mater. 2020;19(11):1175–1181.
- An ZB, Mao SC, Yang T, et al. Spinodal-modulated solid solution delivers a strong and ductile refractory high-entropy alloy. Mater Horiz. 2021: 948–955.
- An ZB, Mao SC, Liu YN, et al. A novel HfNbTaTiV high-entropy alloy of superior mechanical properties designed on the principle of maximum lattice distortion. J Mater Sci Technol. 2021;79:109–117.
- Wang M, Ma ZL, Xu ZQ, et al. Designing VxNbMoTa refractory high-entropy alloys with improved properties for high-temperature applications. Scr Mater. 2021;191:131–136.
- Zou Y, Maiti S, Steurer W, et al. Size-dependent plasticity in an Nb25Mo25Ta25W25 refractory high-entropy alloy. Acta Mater. 2014;65:85–97.
- Juan CC, Tsai MH, Tsai CW, et al. Enhanced mechanical properties of HfMoTaTiZr and HfMoNbTaTiZr refractory high-entropy alloys. Intermetallics. 2015;62:76–83.
- Senkov ON, Miracle DB. Development and exploration of refractory high entropy alloys—A review. J Mater Res. 2018;33(19):3092–3128.
- Miracle DB, Senkov ON. A critical review of high entropy alloys and related concepts. Acta Mater. 2017;122:448–511.
- Yuan Y, Wu Y, Yang Z, et al. Formation structure and properties of biocompatible TiZrHfNbTa high entropy alloys. Mater Res Lett. 2019;7(6):225–231.
- Lilensten L, Couzinié JP, Perrière L, et al. Study of a bcc multi-principal element alloy: Tensile and simple shear properties and underlying deformation mechanisms. Acta Mater. 2018;142:131–141.
- Senkov ON, Pilchak AL, Semiatin SL. Effect of cold deformation and annealing on the microstructure and tensile properties of a HfNbTaTiZr refractory high entropy alloy. Metall Mater Trans A. 2018;49(7):2876–2892.
- Zýka J, Málek J, Veselý J, et al. Microstructure and room temperature mechanical properties of different 3 and 4 element medium entropy alloys from HfNbTaTiZr system. Entropy. 2019;21(2):114.
- Huang HL, Wu Y, He JY, et al. Phase-transformation ductilization of brittle high-entropy alloys via metastability engineering. Adv Mater. 2017;29:1701678.
- Coury FG, Kaufman M, Clarke AJ. Solid-solution strengthening in refractory high entropy alloys. Acta Mater. 2019;175:66–68.
- Toda-Caraballo I, Rivera-Díaz-del-Castillo PEJ. Modelling solid solution hardening in high entropy alloys. Acta Mater. 2015;85:14–23.
- Li L, Fang QH, Li J, et al. Lattice-distortion dependent yield strength in high entropy alloys. Mater Sci Eng A. 2020;784:139323.
- Sheikh S, Shafeie S, Hu Q, et al. Alloy design for intrinsically ductile refractory high-entropy alloys. J Appl Phys. 2016;120(16):164902.
- Wang ZP, Fang QH, Li J, et al. Effect of lattice distortion on solid solution strengthening of BCC high-entropy alloys. J Mater Sci Technol. 2018;34(2):349–354.
- Senkov ON, Miracle DB, Rao SI. Correlations to improve room temperature ductility of refractory complex concentrated alloys. Mater Sci Eng A. 2021;820:141512.
- Mustafi L, Nguyen V, Lu SL, et al. Microstructure, tensile properties and deformation behaviour of a promising bio-applicable new Ti35Zr15Nb25Ta25 medium entropy alloy (MEA). Mater Sci Eng A. 2021;824:141805.
- Nguyen VT, Qian M, Shi Z, et al. Compositional design of strong and ductile (tensile) Ti-Zr-Nb-Ta medium entropy alloys (MEAs) using the atomic mismatch approach. Mater Sci Eng A. 2019;742:762–772.
- Sheng G, Liu CT. Phase stability in high entropy alloys: Formation of solid-solution phase or amorphous phase. Prog Nat Sci Mater Int. 2011;21(6):433–446.
- Li M, Zhang Z, Thind AS, et al. Microstructure and properties of NbVZr refractory complex concentrated alloys. Acta Mater. 2021;213:116919.
- Lai WJ, Liu H, Yu X, et al. A design of TiZr-rich body-centered cubic structured multi-principal element alloys with outstanding tensile strength and ductility. Mater Sci Eng A. 2021;813:141135.
- Chen YW, Xu ZQ, Wang M, et al. A single-phase V0.5Nb0.5ZrTi refractory high-entropy alloy with outstanding tensile properties. Mater Sci Eng A. 2020;792:139774.
- Yan XH, Zhang Y. A body-centered cubic Zr50Ti35Nb15 medium-entropy alloy with unique properties. Scr Mater. 2020;178:329–333.
- Wang SB, Wu DL, She H, et al. Design of high-ductile medium entropy alloys for dental implants. Mater Sci Eng C. 2020;113:110959.
- Wang SP, Ma E, Xu J. New ternary equi-atomic refractory medium-entropy alloys with tensile ductility: Hafnium versus titanium into NbTa-based solution. Intermetallics. 2019;107:15–23.
- Wu YD, Cai YH, Wang T, et al. A refractory Hf25Nb25Ti25Zr25 high-entropy alloy with excellent structural stability and tensile properties. Mater Lett. 2014;130:277–280.
- Wang SP, Ma E, Xu J. Notch fracture toughness of body-centered-cubic (TiZrNbTa) Mo high-entropy alloys. Intermetallics. 2018;103:78–87.
- Chen SY, Tseng KK, Tong Y, et al. Grain growth and Hall-Petch relationship in a refractory HfNbTaZrTi high-entropy alloy. J Alloys Compd. 2019;795:19–26.
- Senkov ON, Wilks GB, Miracle DB, et al. Mechanical properties of Nb25Mo25Ta25W25 and V20Nb20Mo20Ta20W20 refractory high entropy alloys. Intermetallics. 2011;19:698–706.
- Senkov ON, Wilks GB, Miracle DB, et al. Refractory high-entropy alloys. Intermetallics. 2010;18(9):1758–1765.
- Lee C, Song G, Gao MC, et al. Lattice distortion in a strong and ductile refractory high-entropy alloy. Acta Mater. 2018;160:158–172.
- Tong Y, Zhao SJ, Bei HB, et al. Severe local lattice distortion in Zr- and/or Hf-containing refractory multi-principal element alloys. Acta Mater. 2020;183:172–181.
- Lai MJ, Tasan CC, Raabe D. On the mechanism of {332} twinning in metastable β titanium alloys. Acta Mater. 2016;111:173–186.
- Bertrand E, Castany P, Péron I, et al. Twinning system selection in a metastable β-titanium alloy by Schmid factor analysis. Scr Mater. 2011;64(12):1110–1113.
- Yasuda HY, Yamada Y, Cho K, et al. Deformation behavior of HfNbTaTiZr high entropy alloy singe crystals and polycrystals. Mater Sci Eng A. 2021;809:140983.
- Couzinié JP, Lilensten L, Champion Y, et al. On the room temperature deformation mechanisms of a TiZrHfNbTa refractory high-entropy alloy. Mater Sci Eng A. 2015;645:255–263.
- Wasserbäch W. Plastic deformation and dislocation arrangement of Nb [sbnd] 34 at.% Ta alloy single crystals. Philos Mag A. 1986;53(3):335–356.