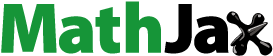
Abstract
Stable L12 structured Cr3Cu precipitates were determined in a Cu-4.06Cr-1.25Nb alloy rather than b.c.c. structured Cr precipitates by transmission electron microscope (TEM) and three-dimension atom probe tomography (3DAP) at 450 oC. The precipitation sequence of the studied alloy aged at 400 oC was supersaturated solid solution → f.c.c. Cr phase → Cr3Cu phase (L12). Nb atoms would segregate in the interface between the Cu and Cr phase, reduce the Cu/Cr interfacial energy, affect the precipitation, growth, phase transformation, and coarsening of the precipitate. These Cr3Cu precipitates significantly improved the high-temperature strength of the Cu-Cr-Nb alloy (223 ± 5 MPa at 500 oC).
GRAPHICAL ABSTRACT
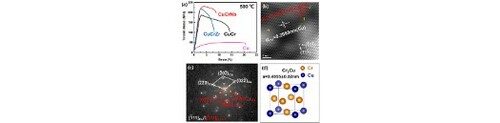
IMPACT STATEMENT
TEM images and calculations revealed that Nb can stabilize metastable Cr3Cu precipitates (L12) by reducing the Cu/Cr interfacial energy, and provide a higher high-temperature strengthening effect than b.c.c. Cr.
1. Introduction
Cu-Cr alloys were reported from the 1970s and serviced as lead-frame materials since the 1990s. Nano-scale Cr precipitates formed in the ageing process made the Cu-Cr-based alloy a high strength and conductivity material [Citation1,Citation2]. However, Cr precipitates’ coarsening at high temperatures led to a sudden decline in the high-temperature mechanical properties of the alloy [Citation3,Citation4]. Cu-Cr alloys required high heat stability as a key heat sink material in service [Citation5,Citation6]. Therefore, studying the precipitate evolution of Cu-Cr alloy was of great significance to increase the high-temperature mechanical properties of the alloy. The typical precipitation sequence of Cu-Cr alloys during ageing was supersaturated solid solution → GP zones → f.c.c. Cr precipitate→ ordered f.c.c. Cr-rich precipitate → b.c.c. Cr precipitate [Citation7]. F.c.c. Cr precipitate was a meta-stable phase that was coherent with the matrix [Citation8]. B.c.c. Cr precipitate was an equilibrium phase with an N-W relationship and K-S relationship [Citation9]. The possible mechanism of transformation from f.c.c. Cr phase to b.c.c. Cr phase was: the dissolution of f.c.c. phase led to an increase in the supersaturation and subsequent homogeneous nucleation of the b.c.c. phase [Citation10]. The reported Cu-Cr alloy showed a significantly coarsening behavior as service at high temperatures. Therefore, high thermal stability phases were required in Cu-Cr system alloys, just as the stability of the austenite phase has an important effect on the strength in steel [Citation11–13]. Researchers had proved that additions of Mg [Citation8], Ti [Citation14], and Zr [Citation15] could affect the precipitation and suppress Cr precipitates’ growth. Glenn Research Center had reported a Cu-8Cr-4Nb alloy with excellent high-temperature creep resistance [Citation16–18], which was mainly strengthened by Cr2Nb particles, but the mechanical properties of the alloy were poor. In recent years, Dierk and Li developed Cu-3.4Cr-0.6Nb and Cu-0.47Cr-0.16Nb alloys with high room mechanical properties and emphasized the main strengthening effect was from nano-scale Cr precipitates [Citation19,Citation20]. However, the effect of Nb on the thermal stability of the Cr precipitate and nano-scale Cr precipitates on the high mechanical properties of Cu-Cr-Nb alloys were still unclear.
In this work, L12 structured Cr3Cu precipitates were obtained in a Cu-4.06Cr-1.25Nb alloy. The effects of Nb on the precipitation, growth, phase transformation and coarsening of the precipitate were analysed and the effects of the precipitate crystal structure on the high-temperature strength of the alloy were discussed. The purpose of this work is to propose a new stable phase to improve the high-temperature mechanical of Cu-Cr system alloys.
2. Materials and methods
The Cu-Cr-Nb alloy was fabricated by an atmospheric melting. The actual composition of the alloy, Cu-4.06Cr-1.25Nb (mass%), was measured by an inductively coupled plasma optical emission spectrometer (ICP-OES). Cu, Cu-Cr (C18200, USA) and Cu-Cr-Zr (C18150, USA) alloys compared in the present study were commercial alloys received in the cast state. Then, these as-cast ingots were homogenized at 950 oC for 4 h, hot rolled by 80% at 900 oC, solid solution treated at 940 oC for 4 h, cold-rolled by 50%, and ageing treated at 400, 450 and 500 oC for a specific time. Constant strain rate (0.001 s−1) tensile tests were carried out on a UTM5105 electronic universal testing machine with a holding furnace. Before testing at high-temperature, samples were heated to the specified temperature and maintained for 10 min in a furnace. The room temperature tensile samples were processed according to GB/T 228 1-2010, and the high-temperature tensile samples were processed according to GB/T 4338-2006. Repeat 3 times for each condition of testing. Microstructures were characterized by a Talos F200X TEM with an operating voltage of 200 kV. TEM specimens were grounded to 50 μm in thickness and then milled by a PI 691 ion-beam milling. 3DAP was conducted on a CAMECA LEAP-4000X HR APT system. The 3DAP samples with a needle-like shape of 0.5×0.5×20 mm3 were prepared by the standard two-step electro-polishing procedure. The first-principles calculations were performed using the Vienna Ab-initio Simulation Package (VASP) [Citation21]. The generalized gradient approximation (GGA) and the projector augmented wave (PAW) method were used for the exchange–correlation functional [Citation22]. The plane wave truncation energy was 520 eV. According to the orientation relationship (OR) between f.c.c. Cr phase and Cu matrix during the ageing process in the studied Cu-Cr-Nb alloy, interface models with 15 Å vacuum layer were constructed by the Material Studio software, and the Brillouin zone was divided by 4×4×1 k-point grids.
3. Results and discussion
3.1. Mechanical properties
Figure shows the tensile strength of Cu, Cu-Cr, Cu-Cr-Zr, and Cu-Cr-Nb alloys tested at 20 oC, 400 oC, 450 oC, and 500 oC. The ultimate tensile strength (UTS) of the studied Cu-Cr-Nb alloy at room temperature was 438 ± 3 MPa, which was lower than that of the Cu-Cr-Zr alloy (484 ± 4 MPa) but was close to that of Cu-Cr alloy (435 ± 5 MPa). As the tensile test temperature exceeded 450 oC, the UTS of Cu-Cr-Nb alloy at 450 oC and 500 oC were 262 ± 3 MPa and 223 ± 5 MPa, respectively, which were higher than Cu-Cr alloys and Cu-Cr-Zr alloys. Tensile test results were mentioned in Figure e with the standard deviation.
3.2. Precipitation
Figure shows the TEM images of the studied Cu-Cr-Nb alloy after ageing treated at 400 oC for 2 h and 20 h. Fine Cr precipitates were detected in the matrix as aged at 400 oC for 2 h (Figure a). The high-resolution TEM (HRTEM) image (Figure b) and its fast Fourier transform (FFT) image (Figure c) showed that Cr precipitates had an f.c.c. structure and a cube-on-cube coherent OR with the Cu matrix. After ageing for 20 h, many Cr precipitates still maintained a fine size of smaller than 10 nm (Figure d). After carefully examining more than 10 HRTEM images (aged at 400 oC for 20 h), only f.c.c. Cr precipitates (Figure e and Figure f) and ordered f.c.c. Cr-rich precipitates were detected which surprised us (Figure g and Figure h). The OR between the f.c.c. Cr/ ordered f.c.c. Cr-rich precipitates and the matrix were still cube-on-cube OR. To verify the stability of ordered f.c.c. Cr-rich precipitates, we increased the ageing temperatures.
Figure 2. The TEM image of the Cu-Cr-Nb alloy aged treated at 400 oC for different time. 2 h: (a) Bright-field image (BF image), (b) HRTEM image, (c) FFT image; 20 h: (d) Bright-field image, (e) HRTEM image, (f) FFT image, (g) HRTEM image, (h) FFT image. ○ marked spots were superlattice spots from the orderd f.c.c. structure.
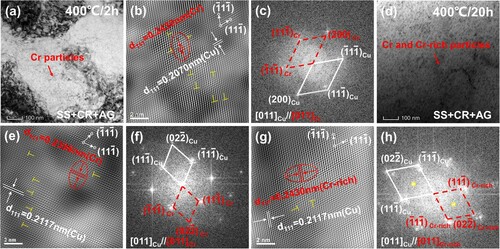
Figure a–h show TEM images of the Cu-Cr-Nb alloy after ageing at 450 oC for 2 h, 20 h, and 100 h. After ageing for 2 h, diffraction spots of f.c.c. structured Cr precipitates were detected, additional diffraction spots (with weak diffraction intensity) were also found at the midpoints between the (000) and Cr’ diffraction spots (Figure c), which indicated that Cr particles had been ordered. With the increase of ageing time to 20 h and 100 h, these additional diffraction spots were still visible (Figure f and h). The ordered f.c.c. Cr-rich phase was stable at 450 oC and maintained a cube-on-cube coherent OR with the matrix (Figure h). Cr precipitates in Cu-Cr, Cu-Cr-Mg, Cu-Cr-Zr, Cu-Cr-Zr-Ti alloys usually exist in the form of stable b.c.c. structure after a long-time ageing treatment [Citation7,Citation8,Citation10,Citation14]. However, in the studied alloy, even ageing at 500 oC, 550 oC, 600 oC for 1 h, Cr-rich precipitates still maintained an ordered f.c.c. structure in the Cu-Cr-Nb alloy (which will be reported in future articles).
Figure 3. The TEM image of Cu-Cr-Nb alloy aged at 450 oC for different time. 2 h: (a) BF image, (b) HRTEM image, (c) FFT image; 20 h: (d) BF image, (e) HRTEM image, (f) FFT image; 100 h: (g) BF image, (h) SAED image; (i) Crystal structure of L12 ordered Cr3Cu. The ordered f.c.c. Cr-rich particles in Figure a–h and Figure g, h were finally determined to be L12 ordered Cr3Cu particles.
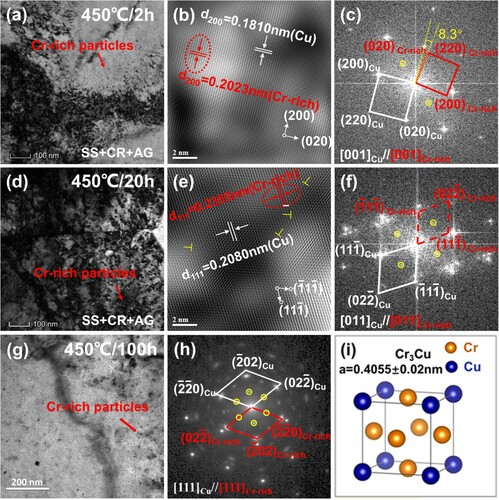
Figure shows 3DAP results of the Cu-Cr-Nb alloy aged at 400 oC for 2 h and 20 h. In the early ageing stage at 400 oC for 2 h, coffee-bean-like precipitates were pure Cr phase with an f.c.c. structure. After ageing for 20 h, precipitates coarsened, and Cu atoms were enriched in some precipitates. The average diameters of precipitates were 3.4 ± 0.2 nm and 7.7 ± 0.1 nm as aged at 400 oC for 2 h and 20 h. The element percentage of Nb on the Cu/Cr interface was 2.7% after ageing for 2 h, while that was 3.0% as aged for 20 h. Combined with the symmetry of crystal structure and the enrichment of Cu atoms in precipitates (Figure b), it could be inferred that the ordered f.c.c. Cr-rich phase was L12 structured Cr3Cu (Figure i). The precipitation sequence of the studied Cu-Cr-Nb alloy during ageing at 400 oC was supersaturated solid solution → f.c.c. Cr phase → L12 structured Cr3Cu phase.
Figure 4. 3DAP data of Cr density maps and corresponding tested concentration of Cr and Nb in Cu-Cr-Nb alloy aged at 400 oC. (a) and (b) show the element concentration in the sample for 2 and 20 h, respectively. (c) and (d) show the distribution of Cr and Nb in the sample aged for 2 and 20 h, respectively.
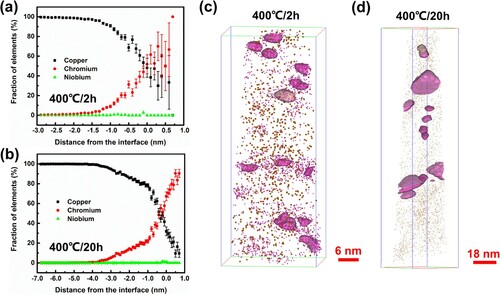
3.3. Effect of Nb on the precipitate structure and mechanical properties
Figure shows the first-principles calculation results, indicating that the Nb atom was easier to replace the Cu side atom rather than the Cr side on the Cu/Cr interface. The interfacial energy of the Cu/Cr interface was 107.1 mJ/m2, however, that of Cu/Cr interface with Nb atoms segregation was 78.2 mJ/m2. The segregation of 2-3% of Nb atoms was difficult to cause the Cu/Cr interfacial energy to drop by about 27%. To verify the rationality of the first-principles calculation results, we used a formula to recalculate the influence of Nb on the interfacial energy [Citation10].
(1)
(1) where a is the lattice parameter (without Nb: a = (0.368 + 0.3615)/2 nm [Citation10,Citation23]. With Nb: a = (0.4108 +0.3615)/2 nm) and ϵ is the ordering effective energy (1.14×10−20 J [Citation10]). χp and χm are solute atom concentrations in the precipitate (100%) and the matrix (0%). For Cr nuclei, γ = 86 mJ/m2 (without Nb) and γ = 77 mJ/m2 (with Nb). The calculation results of the two methods both indicated that Nb segregation on the interface can reduce the interfacial energy, but the latter is more reasonable (drop by 10.5%).
Figure 5. Cu(111)/Cr(111) interface structure model. (a) Cu/Cr interface; (b) Cu/Cr interface with Nb atom segregation.
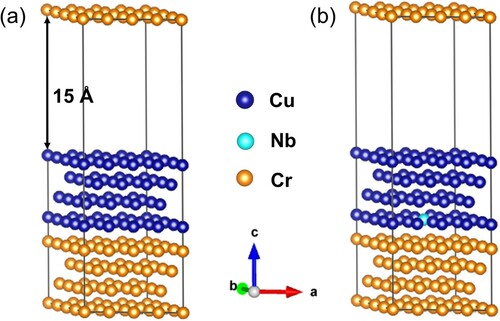
The nucleation of Cr precipitates from the perspective of thermodynamics and kinetics was discussed to analyse the effect of Nb segregation on precipitates. The nucleation barrier () for f.c.c. Cr precipitates could be computed as follows [Citation10,Citation24]:
(2)
(2) where γ is the interfacial energy between precipitate and matrix.
is the driving force.
is the elastic energy. The driving force could be computed by [Citation14]:
(3)
(3) where GA, Gm and Gp are the Gibbs free energies of the alloy, matrix and precipitates, respectively. The thermodynamic database was derived from references [Citation25]. Vmol is the molar volume of the precipitates (7.2×10−6 m3/mol for Cr). The elastic energy could be computed by [Citation26]:
(4)
(4) where E, υ and δ are the elastic modulus (130 GPa), the Poisson ratio (0.34) for Cu matrix, and the misfit between matrix and precipitate, respectively. For Cr nuclei, without Nb atoms segregated on the interface, the misfit between matrix and precipitate is 1.9% [Citation10]. For that with Nb atoms segregated on the interface, it could be computed by:
(5)
(5) where am (0.3615 nm) and ap (0.4108 ± 0.0053 nm) are the lattice parameter of matrix and precipitate. When Nb atoms segregated on the interface, the misfit between matrix and precipitate is 11.5 ± 0.6%, which is higher than that without Nb. This is caused by the difference between the lattice constant of the Cr particle and Cu matrix in the Cu-Cr-Nb alloy, but the lattice constant of the two are similar in the Cu-Cr alloy.
For Cr nuclei with Nb atoms segregated on the interface, the nucleation barrier is 2.9×10−22 J, which are lower than that for Cr nuclei without Nb atoms segregated on the interface (1.6×10−21 J). The precipitation kinetic calculation based on the change of alloy electrical conductivity during ageing. The calculated activation energy is 80.93 kJ/mol, which is lower than 85.36 kJ/mol reported in the Cu-Cr-Zr alloy [Citation27], and 93.10 kJ/mol reported in the Cu-Cr binary alloy [Citation28]. Therefore, Nb could increase the nuclei probability and accelerate f.c.c. Cr’s precipitation in the early ageing process. Finally, these led to a rapid decrease of solute atom concentration in the matrix and the formation of Cr-poor zones around the f.c.c. Cr phase, thereby suppressing the growth and phase transformation of Cr precipitates.
From the TEM images of Figure and Figure , we could certify that nano-scale Cr and stable Cr3Cu precipitates kept nano-scale size even exposed at high temperatures for a long time. According to the particle coarsening model proposed by Lifshitz Slyozof [Citation29] and Wagner (LSW) [Citation30], the relation between the particle’s average radius () and time (t) in the coarsening process could be expressed as:
(6)
(6) where
is the particle’s average radius at t0. D is the diffusion coefficient of solute atoms in the matrix (
[Citation31]). M is the molecular weight of Cr phase (52 g/mol). γ is the interface energy between matrix and precipitate.
is the equilibrium solubility of the precipitate phase (
[Citation32]). R is the ideal gas constant (8.314 J/(mol·K)). T is the Kelvin temperature (673 K). ρ is the Cr precipitate’s density (7.19 g/cm3).
The calculation result shows that f.c.c. Cr particles in Cu-Cr-Nb alloy grew to 11.2 nm after ageing at 400 oC for 20 h. We also considered that f.c.c. Cr particles had been ordered before ageing at 400 oC for 20 h (Figure g, h and Figure b). The interface energy between matrix and L12 ordered Cr3Cu was 0.752 = 9/16 times lower than that of matrix and f.c.c. Cr [Citation10]. L12 ordered Cr3Cu particles would grow to 9.4 nm after aged at 400 oC for 20 h. Suppose Cr particles were b.c.c. structure, the interfacial energy of Crbcc/Cufcc was 625 mJ/m2 (non-coherent interface) [Citation33], particles would grow to 22.3 nm after aged at 400 oC for 20 h. The L12 ordered Cr3Cu had stronger resistance to coarsening than the b.c.c. Cr. Therefore, the main reason for the Cu-Cr-Nb alloy had higher mechanical properties than Cu-Cr alloy at high temperature was that L12 ordered Cr3Cu particles had higher resistance to coarsening than the b.c.c. Cr.
4. Conclusions
In summary, a Cu-4.06Cr-1.25Nb alloy was fabricated by an atmospheric melting, showing a high tensile strength at high temperature (223 ± 5 MPa at 500 oC). Stable L12 structured Cr3Cu precipitates were detected in the studied alloy with high thermal stability. The precipitation sequence during ageing at 400 oC was supersaturated solid solution → f.c.c. pure Cr phase → L12 structured Cr3Cu phase. Nb atoms segregated on the interface between the Cu matrix and Cr precipitates (Cr3Cu precipitates). The addition of Nb reduced the interfacial energy, promoted the f.c.c. structured Cr’s precipitation, and inhibited precipitates’ growth, phase transformation and coarsening. Compared with the b.c.c. structured Cr precipitate, the f.c.c. Cr precipitate and the L12 structured Cr3Cu precipitate coarsened much slower at high temperatures. These led to the studied Cu-Cr-Nb alloy having a higher high-temperature mechanical property than Cu-Cr alloy.
Acknowledgements
This work was supported by the National Natural Science Foundation of China (51901250), and the Key Technologies R&D Program of Yunnan Province (202102AB080019-1).
Disclosure statement
No potential conflict of interest was reported by the author(s).
Additional information
Funding
References
- Lai RL, Li XQ, He DQ, et al. Microstructures evolution and localized properties variation of a thick friction stir welded CuCrZr alloy plate. J Nucl Mater. 2018;510:70–79.
- Wang WY, Zhu JL, Qin NN, et al. Effects of minor rare earths on the microstructure and properties of Cu-Cr-Zr alloy. J Alloys Compd. 2020;847:155762. doi:https://doi.org/10.1016/j.jallcom.2020.155762.
- Yuan Y, Li Z, Xiao Z, et al. Microstructure evolution and properties of Cu-Cr alloy during continuous extrusion process. J Alloys Compd. 2017;703:454–460. doi:https://doi.org/10.1016/j.jallcom.2017.01.355.
- Sun XL, Jie JC, Wang PF, et al. Effects of Co and Si additions and cryogenic rolling on structure and properties of Cu–Cr alloys. Mater Sci Eng: A. 2019;740-741:165–173. doi:https://doi.org/10.1016/j.msea.2018.10.093.
- Team IJC. The impact of materials selection on the design of the International Thermonuclear Experimental Reactor (ITER). J Nucl Mater. 1994;s 212–215(part-P1):3–10. doi:https://doi.org/10.1016/0022-3115(94)90027-2.
- Wang L, Martin D, Chen WY, et al. Effect of sink strength on coherency loss of precipitates in dilute Cu-base alloys during in situ ion irradiation. Acta Mater. 2021;210:116812. doi:https://doi.org/10.1016/j.actamat.2021.116812.
- Peng LJ, Xie HF, Huang GJ, et al. The phase transformation and strengthening of a Cu-0.71 wt% Cr alloy. J Alloys Compd. 2017;708:1096–1102. doi:https://doi.org/10.1016/j.jallcom.2017.03.069.
- Sun YQ, Peng LJ, Huang GJ, et al. Effects of Mg addition on the microstructure and softening resistance of Cu–Cr alloys. Mater Sci Eng: A. 2020;776:139009. doi:https://doi.org/10.1016/j.msea.2020.139009.
- Fujii T, Nakazawa H, Kato M, et al. Crystallography and morphology of nanosized Cr particles in a Cu–0.2% Cr alloy. Acta Mater. 2000;48(5):1033–1045. doi:https://doi.org/10.1016/S1359-6454(99)00411-5.
- Chbihi A, Sauvage X, Blavette D. Atomic scale investigation of Cr precipitation in copper. Acta Mater. 2012;60(11):4575–4585. doi:https://doi.org/10.1016/j.actamat.2012.01.038.
- Anijdan SM, Sediako D, Yue S. Optimization of flow stress in cool deformed Nb-microalloyed steel by combining strain induced transformation of retained austenite, cooling rate and heat treatment. Acta Mater. 2012;60:1221–1229. doi:https://doi.org/10.1016/j.actamat.2011.11.019.
- Sabzi M, Farzam M. Hadfield manganese austenitic steel: a review of manufacturing processes and properties. Mater Res Express. 2019;6(10):1065c2. doi:https://doi.org/10.1088/2053-1591/ab3ee3.
- Far AH, Anijdan SM, Abbasi S. The effect of increasing Cu and Ni on a significant enhancement of mechanical properties of high strength low alloy, low carbon steels of HSLA-100 type. Mater Sci Eng: A. 2019;746:384–393. doi:https://doi.org/10.1016/j.msea.2019.01.025.
- Wang H, Gong LK, Liao JF, et al. Retaining meta-stable fcc-Cr phase by restraining nucleation of equilibrium bcc-Cr phase in CuCrZrTi alloys during ageing. J Alloys Compd. 2018;749:140–145. doi:https://doi.org/10.1016/j.jallcom.2018.03.238.
- Tian W, Bi L, Ma F, et al. Effect of Zr on as-cast microstructure and properties of Cu-Cr alloy. Vacuum. 2018;149:238–247.
- Anderson KR, Groza JR, Dreshfield RL, et al. High-Performance dispersion-strengthened Cu-8 Cr-4 Nb alloy. Metall Mater Trans A. 1995;26(9):2197–2206. doi:https://doi.org/10.1007/BF02671235.
- Ellis DL, Michal GM, Orth NW. Production and processing of Cu-Cr-Nb alloys. Scripta Metall Mater. 1990;24(5):885–890. doi:https://doi.org/10.1016/0956-716X(90)90130-9.
- Anderson KR, Groza JR. Microstructural size effects in high-strength high-conductivity Cu-Cr-Nb alloys. Metall Mater Trans A. 2001;32(5):1211–1224. doi:https://doi.org/10.1007/s11661-001-0130-x.
- Kini AR, Maischner D, Weisheit A, et al. In-situ synthesis via laser metal deposition of a lean Cu-3.4Cr-0.6Nb (at%) conductive alloy hardened by Cr nano-scale precipitates and by Laves phase micro-particles. Acta Mater. 2020;197:330–340. doi:https://doi.org/10.1016/j.actamat.2020.07.035.
- Guo XL, Xiao Z, Qiu WT, et al. Microstructure and properties of Cu-Cr-Nb alloy with high strength, high electrical conductivity and good softening resistance performance at elevated temperature. Mater Sci Eng: A. 2019;749(11):281–290.
- Kresse G, Furthmüller J. Ab initio molecular dynamics for open-shell transition metals. Phys Rev B. 1993;48:13115–13118. doi:https://doi.org/10.1103/PhysRevB.48.13115.
- Blöchl PE. Projector augmented-wave method. Phys Rev B. 1994;50:17953–17979. doi:https://doi.org/10.1103/PhysRevB.50.17953.
- Pearson WB. A handbook of lattice spacings and structures of metals and alloys. Oxford: Pergamon Press; 1964. p. 531.
- Porter DA, Easteterling KE, Sherif MY. Phase transformations in metals and alloys, 3rd edition. Boca Raton (FL): CRC Press; 2009. p. 263.
- Liu XJ, Jiang ZP, Wang CP, et al. Experimental determination and thermodynamic calculation of the phase equilibria in the Cu–Cr–Nb and Cu–Cr–Co systems. J Alloys Compd. 2009;478:287–296. doi:https://doi.org/10.1016/j.jallcom.2008.11.162.
- Christian JW. The theory of transformations in metals and alloys: an advanced textbook in physical metallurgy. 3rd ed. New York (NY): Oxford Pergamon Press; 2002. p. 426.
- Zhou JM, Zhu DG, Tang LT, et al. Microstructure and properties of powder metallurgy Cu-1%Cr-0.65%Zr alloy prepared by hot pressing. Vacuum. 2016;131:156–163.
- Peng LJ, Xie HF, Huang GJ, et al. Dynamics of phase transformation in Cu-Cr-Zr alloy. Adv Mat Res. 2014;887:333–337.
- Lifshitz IM, Slyozov VV. The kinetics of precipitation from supersaturated solid solutions. J Phys Chem Solids. 1961;19(1):35–50. doi:https://doi.org/10.1016/0022-3697(61)90054-3.
- Wagner C. Theorie der alterung von niederschlägen durch umlösen (ostwald-reifung) [theory of the aging of precipitation by dissolution (ostwald ripening)]. Z Phys Chem (NF). 1961;65(7-8):581–591.
- Harzer TP, Duarte MJ, Dehm G. In-situ TEM study of diffusion kinetics and electron irradiation effects on the Cr phase separation of a nanocrystalline Cu–4 at.% Cr thin film alloy. J Alloys Compd. 2017;695:1583–1590. doi:https://doi.org/10.1016/j.jallcom.2016.10.302.
- Doi T. Studies on copper alloys containing chromium (1st report). On the copper side phase diagram. J JPN I Met Mater. 1957;21(5):337–340.
- Aguilar C, Martinez V, Palacios JM, et al. A thermodynamic approach to energy storage on mechanical alloying of the Cu–Cr system. Scripta Mater. 2007;57(3):213–216. doi:https://doi.org/10.1016/j.scriptamat.2007.04.006.