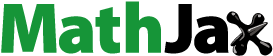
Abstract
Heterogeneous Ti-W metal–metal composites were designed in this study. The effects of W particles on microstructural evolution and strengthening mechanisms were investigated. There was slight diffusion between W particles and Ti matrix. After hot-and-cold rolling, the composites can form high-density hetero-structures. The heterogeneous composites exhibit a better strength-ductility combination, compared with the traditional titanium-matrix composites with uniformly distributed ceramic particles. The hetero-deformation-induced (HDI) strengthening was analyzed, and a new interface stress model was proposed to evaluate the HDI stress. The HDI stress values obtained from the new interface stress model agreed better with the experimental results than the traditional method.
GRAPHICAL ABSTRACT

IMPACT STATEMENT
Heterogeneous Ti-W composites have a good strength-ductility combination due to strong HDI strengthening effect. A new interface stress model is proposed to evaluate the HDI stress based on residual plastic strain energy, leading to a more reasonable estimated result.
1. Introduction
Titanium and titanium alloys are widely used in airplane, aerospace and biomedical fields due to their excellent specific strength and corrosion resistance [Citation1,Citation2]. The strength of titanium alloys can be significantly enhanced by introducing reinforcements, such as TiC and TiB, to form titanium matrix composites (TMCs) [Citation3,Citation4]. After the introduction of ceramic reinforcements, the strength of TMCs improves remarkably through dislocation pile-up, but the plasticity reduces dramatically (1∼3%) [Citation5,Citation6]. The piles-up and accumulation of dislocations usually occur at the interface between the titanium matrix and the ceramic reinforcements, leading to stress concentration and then premature fracture in TMCs.
Titanium matrix metal–metal composites (TMMCs), instead of ceramic reinforced composites, exhibit an excellent combination of strength and ductility [Citation7–9]. In TMMCs, such as Ti-Ta and Ti-Mo composites [Citation9,Citation10], the interface between titanium matrix and metallic reinforcements is compositionally continuous with coherent structures. In such interface, strain gradient always occurs during the plastic deformation, causing plastic strain partition where the ductile phase will bear more plastic strain than the hard phase, and can improve strength and ductility synergistically. Such extra strengthening in TMMCs is so-called hetero-deformation induced (HDI) strengthening [Citation11,Citation12]. In order to evaluate the effect of HDI strengthening, Zhu et al. [Citation13] have proposed a model to calculate the value of HDI stress during the deformation. But in this HDI stress model, all internal stresses opposite the movement of dislocations were roughly replaced by frictional stress. The calculated value of HDI stress can describe the degree and tendency of the HDI strengthening effect, but cannot evaluate the increment of strength like other strengthening effects in alloys [Citation14]. Therefore, it is important to reconstruct a new model to establish a relationship between HDI stress and strength.
In this work, we developed Ti-W composites with heterogeneous structure. The effect of W particles on the microstructural evolution and mechanical behavior of Ti-W composites were investigated, and a theoretical calculation of HDI stress was conducted.
2. Materials and methods
The process of heterogeneous Ti-W composites is schematically shown in Figure (a). High purity (> 99.8%) Ti powders (40∼45 μm) and W powders (2∼4 μm) were mixed by low-energy ball-milling for 8 h under argon atmosphere. Subsequently, the as-prepared Ti-W powder mixtures were hot-pressed at 1100°C for 1 h under a pressure of 25 MPa. Then, the as-sintered billets with a size of 40×80×10 mm3 were hot-rolled to a reduction of 50% at 700°C. In addition, the billets were held at 700°C for 30 min before hot-rolling, and the reduction of each pass was 1 mm. Subsequently, the hot-rolled sheets were cold-rolled to a reduction of 35% with a reduction of 0.1 mm at each pass. The effect of hot-and-cold rolling is to obtain fully dense and high-strength Ti-W composites. Ti-W composites reinforced with 5∼30 wt.% W particles were prepared, which were respectively labeled as Ti-5W, Ti-10W, Ti-20W and Ti-30W.
Figure 1. The fabrication of heterogeneous Ti-W composites: (a) The schematic diagram about the preparation process; (b) Ti powder; (c) W powder; (d) Ti-W mixed powder; As-sintered microstructure of (e) Ti-5W, (f) Ti-10W, (g) Ti-20W and (h) Ti-30W; XRD patterns of Ti-W composites (i) before rolling, (j) after rolling.
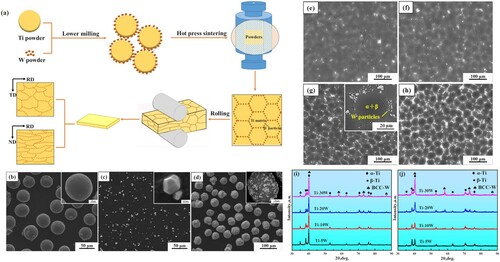
Uniaxial tensile tests and load-unloading-reloading (LUR) tensile tests were conducted on an Instron 8802 machine at a strain rate of 1×10−3 s−1 at room temperature, and the tensile strain was measured by using an extensometer. A total of four I-shaped tensile specimens were cut from the as-rolled sheets with a gauge length of 10 mm and a rectangular cross-section of 2 mm×2 mm. During the LUR test, the specimen was loaded to a strain of 2% at a strain rate of 1×10−3 s−1, followed by unloading to 50 N at the same strain rate, and then reloaded with a strain increment of 1.5%. In-situ tensile tests were performed by employing in-situ loading stage, which was fixed in the scanning electron microscopy (SEM, MIRA 3). The in-situ tension specimens were double-I-shaped with a gauge length of 1.5 mm and a rectangular cross-section of 1mm×2 mm, as shown in Figure S1. The in-situ tensile tests were conducted at a displacement rate of 1 μm/s at room temperature. Under certain load conditions, the tests would be paused to record the crack initiation and propagation. The phase constitution was identified by using X-ray diffraction analyses (XRD, Advance D8), and the microstructures were characterized by using a scanning electron microscope (SEM, Nova NanoSEM230) equipped with an Energy Dispersive Spectrometer (EDS).
3. Results
Figure (b–d) shows the morphology of Ti powders, W powders, and Ti-W powder mixtures. Obviously, the as-received spherical Ti powders disperse uniformly, with particle sizes ranging from 40 to 45 μm (Figure (b)). The fine W powders have irregular shapes, with particle sizes ranging from 2 to 4 μm (Figure (c)). After low-energy ball-milling, W particles are adhered to the surface of the Ti powders (Figure (d)), which is beneficial to form hetero-interfaces [Citation15]. The microstructures of the hot-pressed Ti-W composites are illustrated in Figure (e–h). In Ti-5W and Ti-10W, W particles are separated by titanium matrix (Figure (e–f)), due to the low content of W. But, in Ti-20W and Ti-30W, the W particles form a regular network structure with a grid size of about 45 μm (Figure (g–h)) in the titanium matrix. Besides, the magnified images of microstructure are shown in Figure S2, which indicates that the lamellar α and β phases are alternately distributed around the W particles. Therefore, the heterogeneous Ti-W composite mainly consists of α-Ti, β-Ti, and W particles, similarly verified by XRD patterns (Figure (i)). Furthermore, it was found that there was no new phase in all composites after rolling (Figure (j)), but the content of β phase reduced obviously.
Figure shows the structural characterization of the heterogeneous Ti-W composites after rolling. The network microstructure was elongated along the rolling direction (RD), and flattened along the normal direction (ND), as shown in Figure (a–b, d–e). It should be noted that W is a β-stabilizing element, which can promote the formation of the β-Ti phase around the Ti/W interface. The compositional analyses of Figure (c, f) further confirmed the diffusion between Ti and W. The W particles were dissolved with ∼10% Ti, while the width of the inter-diffusion zone is about 2 μm.
Figure 2. Microstructures of Ti-W sheets (a–b) Ti-5W, (c) the line scanning patterns near W particles, (d)–(e) Ti-30W, (f) corresponding EDS pattern of (d).
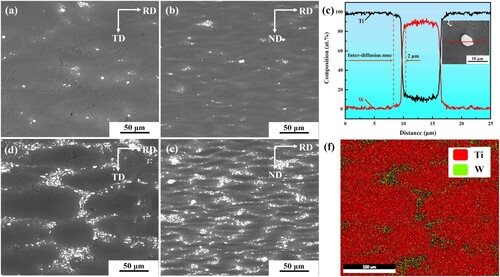
The tensile properties of the heterogeneous Ti-W composites are illustrated in Figure (a–b). The details are provided in Table 1. Both the ultimate tensile strength (UTS) and yield strength (YS) of Ti-W composites increase with W contents, while the ductility decreases gradually. Ti-30W has a high tensile strength of 1135 MPa, which is 75.4% higher than that of pure Ti. A comparison in UTS vs elongation of the presented heterogeneous composites with other conventional TMCs reinforced by ceramic particles is exhibited in Figure (b) [Citation5,Citation6,Citation16–24]. The strength of TMCs reinforced by ceramic particles can be enhanced to about 1000 MPa, but the plasticity drops sharply to less than 5%. Instead, the heterogeneous Ti-W composites show a good combination of strength and ductility. The in-situ tensile observation of Ti-20W is shown in Figure S3. Cracks initiated and propagated in the titanium matrix, but underwent hindered at the front of W particles. A lot of tearing edges around the W particles can be seen from the fracture morphology (Figure S3(j–k)). Therefore, the Ti matrix shows high plasticity.
Figure 3. Tensile properties of Ti-W composites (a–b) and the analysis of conventional strengthening mechanisms in Ti-W composites (c–d): (a) true stress-strain curve, (b) comparison of tensile properties with other TMCs materials reinforced by ceramics, (c) the contribution of various strengthening mechanisms, (d) the comparison between the calculated value of the yield strength and the experimental value.
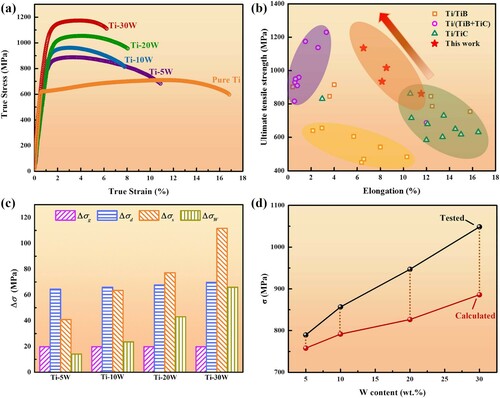
4. Discussion
Generally, strengthening mechanisms of alloys include solid solution strengthening (Δσs), grain-boundary strengthening (Δσg), and dislocation strengthening (Δσd) [Citation25]. In this study, when the composite was loaded, W particles can hinder the movement of dislocation in the Ti matrix (ΔσW). Therefore, the yield strength of Ti-W composites () can be calculated as following:
(1)
(1) where
is the yield strength of Ti matrix, which is 619 MPa obtained from pure Ti fabricated through the same powder metallurgical method. Here, the corresponding calculation equations and material parameters for the above strengthening mechanisms are detailedly shown in Table 2 [Citation26–38].
The increments in yield strength caused by various strengthening mechanisms are illustrated in Figure (c–d). The increments from grain-boundary strengthening and dislocation strengthening are very close in Ti-W composites, because the composites have gone through the same rolling process, and the change in the grain size was slightly influenced by the content of W. On the contrast, the solid solution strengthening and W particle strengthening exhibit significantly positive correlations with the content of W. Thus, the effects of the introduction of W particles on the strengthening behavior could be summarized as follows. Firstly, the dissolution of W particles in the Ti matrix causes remarkable solid solution strengthening. Secondly, the W particles can directly bear the stress transferred from the Ti matrix and act as strengthener. And thirdly, the increased density of the Ti/W interface induces more accumulation and pile-up of dislocations, which further enhance the strength.
Based on the evaluation of the above strength increments, the yield strength of Ti-W composites can be calculated by Equation (1), as shown in Figure (d). It is clear that the trend of the calculated yield strength is similar to the experimental results, but there is an obvious gap between the calculated values and the experimental values, and the gap increases with the increase of the W particles. Therefore, there could exist an extra strengthening mechanism owing to the heterogeneous structure, called as HDI strengthening [Citation14,Citation39]. The contributions of HDI strengthening can be evaluated by the LUR experiment. The hysteresis loop indicates the Bauschinger effect, and shows the relationship between the HDI stress and the flow stress. The unloading and reloading curves of four Ti-W composites are illustrated in Figure S4. Usually, the HDI stress () can be estimated by [Citation13]:
(2)
(2) where the stress
and
are the yield stress in the reloading and unloading process. Each yield point was defined as the point which has a 10% reduction in slope from the effective elastic modulus. In order to clearly define the yield point, every loop is fitted as a polynomial function [Citation40]. The values of HDI stress are plotted and fitted by a polynomial function, as shown in Figure (a). Obviously, the HDI stress of four Ti-W composites increases with the strain, which means that the contribution of HDI strengthening becomes stronger with the increase of strain. Furthermore, it is found that the HDI stress also increases with the increasing of W particles. The HDI stress of Ti-30W is about 200 MPa higher than that of Ti-5W at a total stain of 2%. This indicates a stronger HDI strengthening in Ti-W composites with high content of W particles. Because the continuity of W particles increases with the content of W particles. The high-density hetero-interfaces can strongly affect the plastic deformation of Ti matrix, which results in a large strain gradient [Citation25], and thus, strong HDI strengthening.
Figure 4. Analyses of HDI stress based on LUR tests: (a) HDI stress calculated by conventional model; (b) Interface stress calculated by new model; (c) The HDI value obtained by two methods (when ϵ = 2%); Schematic diagram of plastic strain energy calculation in (d) the first loading and unloading circuit, and (e) the ith loading and unloading circuit.
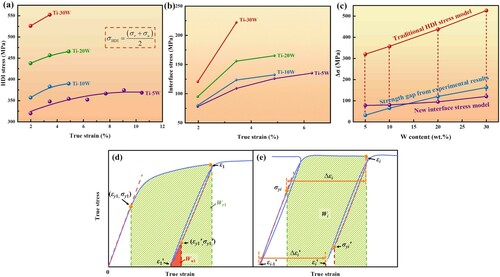
However, the values of HDI stress calculated by Equation (2) are much higher than the strength gap shown in Figure (c). Although the HDI strengthening value cannot be simply added to Equation (1), it may be much overestimated.
In order to reconstruct the relationship between HDI stress and strength, we propose a new model in terms of residual plastic strain energy. At first, we define the plastic strain energy due to the internal stress:
(3)
(3) where W is the plastic strain energy,
is the average internal stress in the plastic deformation process, and
is the plastic strain. In the process of LUR, due to the existence of back stress, partial strain energy will be restored during the unloading process. Therefore, the increment of the strain energy (W1) during the first loading and unloading process is:
(4)
(4) where
is the internal stress during the first loading process, and
is the internal stress during the first unloading process. As shown in Figure (d), the terms of Equation (4) can be decomposed into two parts, elastic and plastic ones:
(5)
(5) where
and
are the elastic internal stress and plastic internal stress during the first loading process,
and
are the elastic internal stress and plastic internal stress during the first unloading process. The separation of elastic and plastic deformation is at a strain point of
during the first loading process and at a strain point of
during the first unloading process. We assume that the elastic strain energy can be fully recovered. The strain energy during the first loading and unloading process, that is, the plastic strain energy W1 can be expressed by the following equation:
(6)
(6) where
is the increment of plastic strain energy during the first loading, and
is the change value of plastic strain energy during the first unloading. According to the flow stress equation in the plastic deformation process:
(7)
(7) where
is the strain during loading and unloading,
is the stress at the end of first loading, K is the strength coefficient, and n is the strain hardening exponent representing the uniform-deformation ability. During the first loading process, when the strain is
, the yield stress
is:
(8)
(8) Substituting Equation (8) into Equation (7), we can get:
(9)
(9) For many titanium alloys, the ability of strain hardening is very limited, and the value of n is about 0.05 [Citation41]. In this work, the Ti-W composites also exhibit limited strain hardening as shown in Figure (a), and it can be deduced that the value of n is very close to 0. In order to simplify the calculation, we could make an approximation:
. Similarly, the approximation could also be made during the first unloading process. Equation (6) can be calculated as
(10)
(10)
Subsequently, we assume the elastic strain is equivalent during the loading and unloading process: . This approximation is reasonable because the elastic strain energy produced during the loading process can be fully recovered during the subsequent unloading process. Besides, the elastic modulus of loading and unloading are similar, and the strain hardening is weak in the current Ti-W composites, which help to result in a similar elastic strain during the loading and unloading process. Meanwhile, we introduce an average internal stress
during the first loading and unloading process:
(11)
(11) Therefore, the average internal stress
in the ith loading and unloading loop can be extrapolated as:
(12)
(12) where
is the plastic strain during the ith loading process, and
is the residual plastic strain during the ith loading and unloading process, as shown in Figure (e). The average internal stress obtained from Equation (12) is generated during the loading and unloading process of the composite. In heterogeneous materials, internal stress is mainly caused by the accumulation and reaction of dislocations at the hetero-interfaces, so here the internal stress was replaced by the interface stress. In order to obtain the increment of plastic strain energy (
) caused by Ti/W interfaces at the ith loading and unloading loop, the plastic strain energy can be considered as the combined results from the contribution of the matrix and the introduction of W particles, and thereby the
can be expressed as:
(13)
(13)
(14)
(14) where Wi is the total change of plastic strain energy and Wmatrix is the change of plastic strain energy from the matrix during the ith loading and unloading process. Here, the increments caused by strain hardening were both ignored for calculating Wi and Wmatrix, since the strain hardening is very weak in the Ti-W composites. Then,
can be approximately replaced by the yield strength of the composites at the first loading in the LUR experiment. Therefore, the interface stress (
) caused by the introduction of W particles during the LUR process is as follows:
(15)
(15) However,
is calculated based on the total change of plastic strain energy (Wi) of the composite with W particles. Therefore, the calculation of
includes the strengthening effect by the Ti/W interfaces and the work hardening of titanium matrix dislocation strengthening. Both effects of strengthening are related to dislocations at the interface. The former is caused by the accumulation of GNDs at the interface of Ti and W, and the latter is caused by the accumulation of mobile dislocations at the grain boundary or at the phase interface of α-Ti and β-Ti. Therefore, Equation (15) can be reasonably used to estimate the interface stress induced by heterogeneous structure. It should be noted that for other alloys with high n-value, such as Al2024 alloy (n = 0.2) [Citation41], the expression of Equation (10) will become more complicated due to the invalid of approximation in Equation (9). Therefore, the new interface stress is reasonable just for those alloys with low n-values to evaluate the HDI strengthening effect.
According to Equations (15), the interface stress values of Ti-W composites are calculated, shown in Figure (b). The values of interface stress increase by the strain. The first hysteresis loop finished when the total strain is around 2%, and the corresponding HDI values were calculated by the two methods (Figure (c)). It is apparent that the HDI value obtained by the new interface stress model is closer to the strength gap than that calculated by using the traditional method. Therefore, the new interface stress model can evaluate the values of the HDI strengthening effect more reasonably.
5. Conclusion
In summary, heterogeneous Ti-W metal–metal composites have a better combination of strength and ductility than traditional TMCs reinforced by ceramic particles. The HDI strengthening is the dominant strengthening mechanism in Ti-W composites. It seems that the HDI strengthening value was overestimated by using the traditional method, and thus, a new interface stress model was proposed in terms of residual plastic strain energy. The calculation indicates that the results are more reasonable to describe the HDI strengthening.
Supplemental Material
Download MS Word (2.2 MB)Acknowledgements
This work was supported by the National Natural Science Funds for Distinguished Young Scholar of China [No. 51625404] and the Science and Technology Innovation Program of Hunan Province [No. 2020RC2007].
Disclosure statement
No potential conflict of interest was reported by the author(s).
Additional information
Funding
References
- Zhao ST, Ell J, Yu Q, et al. Cryoforged nanotwinned titanium with ultrahigh strength and ductility. Science. 2021;373(6561):1363–1368.
- Zhang DY, Qiu D, Gibson MA, et al. Additive manufacturing of ultrafine-grained high-strength titanium alloys. Nature. 2019;576(7785):91–95.
- Badini C, Ubertalli G, Puppo D, et al. High temperature behaviour of a Ti-6Al-4V/TiCp composite processed by BE-CIP-HIP method. J Mater Sci. 2000;35(15):3903–3912.
- Godfrey TMT, Wisbey A, Goodwin PS, et al. Microstructure and tensile properties of mechanically alloyed Ti–6A1–4 V with boron additions. Mater Sci Eng A. 2000;282(1):240–250.
- Ni DR, Geng L, Zhang J, et al. Effect of B4C particle size on microstructure of in situ titanium matrix composites prepared by reactive processing of Ti–B4C system. Scripta Mater. 2006;55(5):429–432.
- Ni DR, Geng L, Zhang J, et al. Fabrication and tensile properties of in situ TiBw and TiCp hybrid-reinforced titanium matrix composites based on Ti-B4C-C. Mater Sci Eng A. 2008;478(1-2):291–296.
- Xu SH, Qiu JH, Zhang HB, et al. Evolution of nano-scaled lamellae and its effect on strength of Ti–Ta composite. Mater Sci Eng A. 2020;805(3-4):140552.
- Xu SH, Du M, Li J, et al. Bio-mimic Ti–Ta composite with hierarchical “brick-and-mortar” microstructure. Materialia. 2019;8:100463.
- Xu SH, Liu Y, Yang C, et al. Compositionally gradient Ti-Ta metal-metal composite with ultra-high strength. Mater Sci Eng A. 2018;712:386–393.
- Cao YK, Zhang WD, Liu B, et al. Extraordinary tensile properties of titanium alloy with heterogeneous phase-distribution based on hetero-deformation induced hardening. Mater Res Lett. 2020;8(7):254–260.
- Wu XL, Zhu YT. Heterogeneous materials: a new class of materials with unprecedented mechanical properties. Mater Res Lett. 2017;5(8):527–532.
- Zhu YT, Wu XL. Perspective on hetero-deformation induced (HDI) hardening and back stress. Mater Res Lett. 2019;7(10):393–398.
- Yang MX, Pan Y, Yuan FP, et al. Back stress strengthening and strain hardening in gradient structure. Mater Res Lett. 2016;4(3):145–151.
- Wu XL, Yang MX, Yuan FP, et al. Heterogeneous lamella structure unites ultrafine-grain strength with coarse-grain ductility. Proc Natl Acad Sci. 2015;112(47):14501.
- Liu ZQ, Li RT, Wang Y, et al. High-performance titanium-based composite strengthened with in-situ network-distributed 3D reinforcements. Mater Sci Eng A. 2021;802:140572.
- Liu BX, Huang LJ, Geng L. Elastic and plastic behaviors of laminated Ti-TiBw/Ti composites. J Wuhan Univ Technol, Mater Sci Ed. 2015;30(3):596–600.
- Huang LJ, Wang S, Dong YS, et al. Tailoring a novel network reinforcement architecture exploiting superior tensile properties of in situ TiBw/Ti composites. Mater Sci Eng A. 2012;545:187–193.
- Hayat MD, Singh H, He Z, et al. Titanium metal matrix composites: An overview. Composites. Part A. 2019;121:418–438.
- Ranganath S, Vijayakumar M, Subrahmanyan J. Combustion-assisted synthesis of Ti-TiB-TiC composite via the casting route. Mater Sci Eng A. 1992;149(2):253–257.
- Lu X, Pan Y, Li WB, et al. High-performance Ti composites reinforced with in-situ TiC derived from pyrolysis of polycarbosilane. Mater Sci Eng A. 2020;795:139924.
- Zhang C, Guo ZM, Yang F, et al. In situ formation of low interstitials Ti-TiC composites by gas-solid reaction. J Alloys Compd. 2018;769:37–44.
- Ma FC, Zhou JJ, Liu P, et al. Strengthening effects of TiC particles and microstructure refinement in in situ TiC-reinforced Ti matrix composites. Mater Charact. 2017;127:27–34.
- Li SF, Kondoh K, Imai H, et al. Microstructure and mechanical properties of P/M titanium matrix composites reinforced by in-situ synthesized TiC–TiB. Mater Sci Eng A. 2015;628:75–83.
- Wu H, Lei CX, Du Y, et al. Microstructure and superior mechanical property of in situ (TiBw + TiCp)/Ti composites with laminated structure. Ceram Int. 2021;47(8):11423–11431.
- Wu XL, Zhu YT, Lu K. Ductility and strain hardening in gradient and lamellar structured materials. Scripta Mater. 2020;186:321–325.
- Hu ZY, Cheng XW, Li SL, et al. Investigation on the microstructure, room and high temperature mechanical behaviors and strengthening mechanisms of the (TiB + TiC)/TC4 composites. J Alloys Compd. 2017;726:240–253.
- Lutjering G. Influence of processing on microstructure and mechanical properties of (α+β) titanium alloys. Mater Sci Eng A. 1998;243(1-2):32–45.
- Chen SJ, Li LJ, Peng ZW, et al. On the correlation among continuous cooling transformations, interphase precipitation and strengthening mechanism in Ti-microalloyed steel. J Mate Res Technol. 2021;10:580–593.
- Yurchenko NY, Panina ES, Zherebtsov SV, et al. Microstructure evolution of a novel low-density Ti–Cr–Nb–V refractory high entropy alloy during cold rolling and subsequent annealing. Mater Charact. 2019;158:109980.
- Labusch R. A statistical theory of solid solution hardening. Phys Status Solidi. 1970;41(2):659–669.
- Donachie M. Titanium: a technical guide. Ohio: ASM International; 2000.
- Ramakrishnan N. An analytical study on strengthening of particulate reinforced metal matrix composites. Acta Mater. 1996;44(1):69–77.
- Lu WJ, Zhang D, Zhang XN, et al. Microstructure and tensile properties of in situ (TiB + TiC)/Ti6242 (TiB:TiC = 1:1) composites prepared by common casting technique. Mater Sci Eng A. 2001;311(1-2):142–150.
- Zhang Q, Chen DL. A model for predicting the particle size dependence of the low cycle fatigue life in discontinuously reinforced MMCs. Scripta Mater. 2004;51(9):863–867.
- Proville L, Rodney D, Marinica M-C. Quantum effect on thermally activated glide of dislocations. Nat Mater. 2012;11(10):845–849.
- Brown LM, Stobbs WM. The work-hardening of copper-silica v. equilibrium plastic relaxation by secondary dislocations. Philo Mag. 1976;34(3):351–372.
- Wolf SM. Properties and applications of dispersion-strengthened metals. JOM. 1967;19(6):22–28.
- Yokota K, Bahador A, Shitara K, et al. Mechanisms of tensile strengthening and oxygen solid solution in single β-phase Ti-35 at.%Ta + O alloys. Mater Sci Eng A. 2021;802:140677.
- Li DY, Fan GH, Huang XX, et al. Enhanced strength in pure Ti via design of alternating coarse- and fine-grain layers. Acta Mater. 2021;206:116627.
- Park HK, Ameyama K, Yoo J, et al. Additional hardening in harmonic structured materials by strain partitioning and back stress. Mater Res Lett. 2018;6(5):261–267.
- Zhang ZP, Qiao YJ, Sun Q, et al. Theoretical estimation to the cyclic strength coefficient and the cyclic strain-hardening exponent for metallic materials: preliminary study. J Mater Eng Perform. 2009;18(3):245–254.