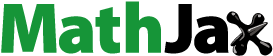
Abstract
SmCo7-based permanent magnets with a TbCu7-type structure have excellent high-temperature performance. However, most of the previously reported SmCo7 nanocrystalline magnets were isotropic, which limited their application. So the preparation of anisotropic SmCo7 magnets with preferred texture is still a challenge. In this work, we prepared anisotropic SmCo6.8Hf0.2 nanocrystalline magnets by hot pressing and hot deformation method. EBSD results indicated that the {0001} orientation texture of the hot deformed magnet was remarkably preferred, which further improved the remanence. Subsequently, the structural evolution process was systematically characterized by TEM. It provides crucial insight for developing high-performance SmCo7-based magnets.
Impact Statement: Up to now, most of the previously reported SmCo7 nanocrystalline magnets were isotropic, which limited their application. This work opens up new opportunities to create high-performance SmCo7-based nanostructured magnets.
GRAPHICAL ABSTRACT
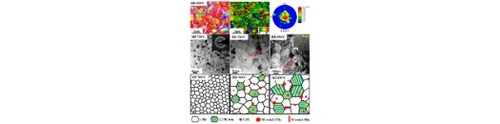
1. Introduction
Sm-Co alloys have become irreplaceable permanent magnet materials in high-temperature applications because of their low-temperature coefficient and high Curie temperature [Citation1-3]. Specifically, the SmCo7 magnet can combine the advantages of a large magnetocrystalline anisotropy field and high Curie temperature, which make it a potential high-temperature permanent magnet [Citation4-9]. But SmCo7 (1:7H) phase is a metastable phase with a TbCu7-type structure, which easily decomposes into SmCo5 (1:5H) and Sm2Co17 (2:17R) phases [Citation10-13]. Some studies show that the 1:7H phase can stably exist at room temperature by doping alloy elements or nano-crystallization of grains [Citation14-17]. For example, it is reported that doping the Hf element (x = 0.2) can decrease the formation energy of the 1:7H phase, which effectively stabilizes the SmCo7−xHfx compound with the TbCu7-type structure [Citation18-20]. Moreover, nanocrystalline materials’ thermal stability, phase stability, and phase transition behavior are significantly different from traditional coarse-grained materials [Citation21]. Due to competition between surface enthalpy and crystalline transformation energy caused by the size effect, some metastable phase compounds can stably exist at the nanoscale [Citation22-24].
More importantly, the SmCo7 magnets reported above are almost all isotropic, limiting their application. Therefore, it is crucial to prepare anisotropic magnets. At present, hot pressing (HP) and hot deformation (HD) method is an effective way to prepare anisotropic nanocrystalline magnets. The HP can support the nanostructure formation, and the HD can help obtain a strong c-axis texture [Citation25-31]. A. M. Gabay et al. systematically analyzed the texture forming ability of HD nanocrystalline SmCo (1:5, 1:7, 2:7, 2:17) magnets, the order of which is 2:17(R) < 1:7 < 1:5 < 2:7 [Citation32]. Zhang et al. prepared anisotropic SmCo7 nanocrystalline magnets by High-pressure thermal compression, but it did not involve the evolution of phase structure [Citation6]. So far, for the SmCo7-based anisotropic magnets, texture formation and phase stability are not systematically studied during the HD. In this paper, the spark plasma sintering (SPS) technology was used to prepare an anisotropic SmCo6.8Hf0.2 nanocrystalline magnet by the HP-HD method. The microstructure, texture, and magnetic properties were systematically analyzed. The structural evolution process of the magnet was especially investigated.
2. Materials and methods
SmCo6.8Hf0.2 ingot was prepared by induction melting method with 99.9% pure elements, excess Sm of 8 wt.% was added to compensate Sm loss due to evaporation. The ingot was crushed, then ball milled for 5 h in a high-energy mill under an argon atmosphere, with a ball-to-power weight ratio of 10:1. Then the ball-milled powders were put into cemented carbide mold and fast consolidated into a columnar-shaped sample at 700 °C for 8 min under 500 MPa by SPS to prepare isotropic HP magnets. At last, the HP magnets were further put into molds and deformed with a height reduction of 72% at 700, 850 °C.
The crystal structure and texture of the sample were analyzed by powder X-ray diffraction (XRD, Bruker D8 Advance) with Cu-Kα radiation. Magnetic properties of the sample were measured by a vibrating sample magnetometer (VSM, Quantum Design, VersaLab) at 27 °C. Then, the electron back-scattered diffraction (EBSD) data of the sample was collected by the EBSD detector (Hikari EDAX) incorporated in SEM (FEI Quanta 250). The chemical composition and element distributions of the sample were identified by a JEOL JXA-8100 electron probe microanalysis (EPMA). Furthermore, the microstructure of the sample was observed by transmission electron microscope (TEM, FEI, Tecnai G2 F30).
3. Results and discussion
According to the XRD results in Figure (a), the HP magnet has a single-phase 1:7H structure. However, the HD magnet consists of 1:7H, 2:17R, and 1:5H. Moreover, the degree of 1:7H phase decomposition intensifies with increasing temperature. Furthermore, the intensity of (001) and (002) diffraction peaks of the 1:5H phase significantly increases after HD, indicating that a strong c-axis texture is formed along the pressure direction. Therefore, the texture of the HD magnets is from not only the 1:7H phase but also the 1:5H phase generated by the phase transformation. However, the 2:17R phase with a low magnetocrystalline anisotropy is difficult to obtain texture by the HD, which is not conducive to texture formation [Citation32]. Therefore, it is important to research the evolution process of the 1:7H phase for the application of the SmCo7-based magnets. In addition, the magnetic properties of the HP and HD magnets are shown in Figure (b). The hysteresis loops of the HD magnets show good squareness. It can be seen that the remanence of the HD magnet greatly increases from 5.4 kG (HP) to 7.4 kG (HD 850 °C). On the contrary, the coercivity decreases from 20.4 kOe (HP) to 4.9 kOe (HD 850 °C). Under the combined influence of coercivity and remanence, (BH)max reaches a peak value of 13.3 MGOe at HD 700 °C, which is significantly improved compared with that of isotropic HP magnets (7.8 MGOe).
Figure 1. (a) and (b) are XRD patterns and hysteresis loops of the HP and HD SmCo6.8Hf0.2 magnets at different deformation temperatures. The measurement surface of the XRD is perpendicular to the pressure direction. The test direction of the magnetic properties is parallel to the pressure direction.
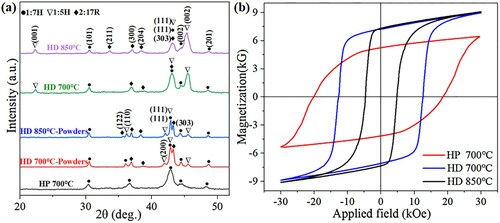
It is well understood that the increase of remanence is due to the improvement of c-axis texture. However, the coercivity is strongly dependent on microstructure. For HP magnets, the grain size is relatively small and close to the size of the single domain. The abundant nanocrystalline boundaries become the main pinning source of magnetic domains movement. So the pinning effect on the reversal of the magnetic moments is enhanced, resulting in the increase of coercivity. In addition, the Hf substitution for the Co atoms in the crystal structure induces lattice distortion and affects the movement of the domain walls. During hot deformation, under the strong thermal-mechanical coupling, The (00 l) orientation of the HD magnet is significantly improved, resulting in the enhancement of the remanence. However, the coercivity decreases gradually with increasing temperature. The pinning effect of the grain boundaries is weakened rapidly due to grain growth, and the grain size may be larger than the dimension of the single domain. Furthermore, the formation of the 2:17R phase with low magnetocrystalline anisotropy has an adverse effect on the coercivity. Therefore, we infer that it is possible to obtain anisotropic SmCo7-based nanocrystalline magnets with excellent magnetic properties by further optimizing the deformation process, increasing the height reduction, and decreasing the deformation temperature.
The microtexture of the HD 850 °C magnet was analyzed by the EBSD (Figure ). The IPF [Figure (a)] shows that a strong [0001] c-axis texture exists in the magnet. In addition, the misorientation angle of grains, {0001} PF and IPF (Figure (b-d)) can quantitatively count the c-axis texture. The misorientation angle of grains shows that the deviation of the individual c-axis from the ideal [000 l] direction is parallel to the pressing direction. The high intensity of the {0001} PF is concentrated in the central area, and the corresponding maximum intensity is about 6.25 MRD (multiple of a random distribution). The IPF also shows that the normal direction is more concentrated in the [0001] crystal direction. The above results further prove that the anisotropic SmCo6.8Hf0.2 nanocrystalline magnet exhibits a strong c-axis texture, which is important to improve the remanence of the magnet.
Figure 2. EBSD results of the HD 850 °C magnet: (a) The inverse pole figure (IPF) quick map; (b) The misorientation angle between c-axis direction and pressing direction; (c) {0001} pole figure (PF); (d) {0001} inverse pole figure (IPF). The test surface is perpendicular to the pressure direction of the HD magnet.
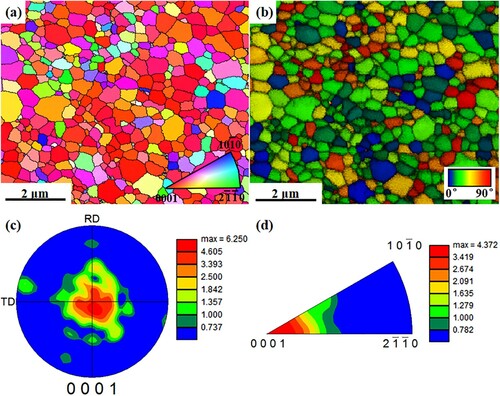
TEM results of the HP magnet are shown in Figure . It can be seen from Figure (a) that the grains of the HP magnet are fine and uniform, and the average grain size is about 25 nm. It can be determined that the HP magnet has a TbCu7-type structure by calibrating the ring diffraction pattern [Figure (b)], which is consistent with the XRD results. The IFFT results of the local nanocrystalline structure [Figure (c)] were analyzed. The measured lattice spacings are d(100) ≈ 0.43 nm, d(001) ≈ 0.41 nm. Then the calculated lattice parameters are a ≈ 0.49 nm and c ≈ 0.41 nm. In addition, both the NBED results of randomly selected two grains [Figure (d and e)] also prove that the HP magnet has the 1:7H phase. The above results show that the HP magnet has strong 1:7H single-phase stability, owing to doping Hf element and nanoscale grains.
Figure 3. TEM results of the HP magnet: (a) The bright field (BF) image of microstructure; (b) The selected area electron diffraction (SAED) image; (c) The inverse fast fourier transform (IFFT) image; (d-e) The Nanobeam electron diffraction(NBED) results of the designated area marked by the red dotted line [Figure (a)1, 2]. The test surface is perpendicular to the pressure direction of the HP magnet.
![Figure 3. TEM results of the HP magnet: (a) The bright field (BF) image of microstructure; (b) The selected area electron diffraction (SAED) image; (c) The inverse fast fourier transform (IFFT) image; (d-e) The Nanobeam electron diffraction(NBED) results of the designated area marked by the red dotted line [Figure 3(a)1, 2]. The test surface is perpendicular to the pressure direction of the HP magnet.](/cms/asset/4f650d40-5171-48da-8c05-f614cc2017ce/tmrl_a_2075712_f0003_oc.jpg)
Figure shows the TEM result of the HD 700 °C magnet. It can be seen from Figure (a) that grains grow up, with an average grain size of about 65 nm. It is worth noting that the microstructure of the HD magnet has changed. The ring diffraction pattern shows that the HD magnet no longer maintains a 1:7H single-phase state and presents the coexistence of 1:7H, 2:17R, and 1:5H phases [Figure (b)], indicating that part of the 1:7H phases decomposes into 2:17R and 1:5H phases during the HD process. In addition, EPMA results also show that the Hf element is enriched in the local area (Fig. S1). The diffraction patterns of specific area (1, 2, 3, 4) in Figure (a) are shown in Figure (c-f). It can be determined that the matrix (area 1) is 1:7H phase, the twins (area 2) are 2:17R phase [Citation33,Citation34], and the spherical precipitates of about 8 nm (area 3) are 1:5H phase. The granular precipitates of about 25 nm (area 4) might be 2:17R type Hf-rich phase. To further study the crystallographic characteristic between the new phase (2:17R and 1:5H) and the parent phase (1:7H), the characteristic two-phase area was selected to be analyzed. From the lattice images in Figure (g and h), the interface relationship is incoherent between the (2:17R and 1:5H phases) with the 1:7H phases. It may be due to existing large external stress during the HD process. When strain energy becomes the main resistance to a solid phase transition, maintaining an incoherent interface relationship is conducive to reducing strain energy [Citation35]. In addition, the 1:5H phase and the 1:7H phase have a certain orientation relationship [Figure (i)], ()1:5H //(
)1:7H, [
]1:5H//[
]1:7H.
Figure 4. TEM results of the HD 700 °C magnet: (a) The BF image of microstructure; (b) The SAED image; (c)-(f) Diffraction patterns of the corresponding area 1, 2, 3, 4 marked by the red dotted line in Figure (a); (g)-(h) IFFT results of two-phase areas; (I) Diffraction pattern corresponding to Figure (h). The test surface is perpendicular to the pressure direction of the HD magnet.
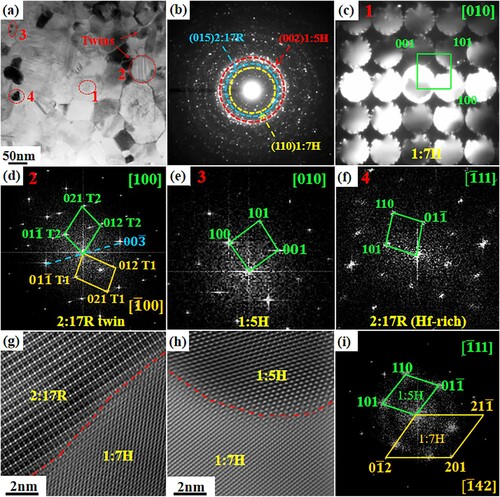
The TEM results of the HD 850 °C magnet are shown in Figure . Compared with the microstructure of the HD 700 °C magnet, the grains of the HD 850 °C magnet become larger, with an average grain size of about 500 nm. Moreover, the heterogeneity of microstructure is more prominent. The ratio of 1:7H phase (area 1) decreases, the ratio and grain size of 2:17R twins (area 2) increases. By measuring the interplanar distances in the lattice image [Figure (d)], it can be determined that the twin boundary is (001) plane. The twin on either side of the twin boundary matches the other twin variant perfectly after rotating for 60° taking the [100] as the rotation axis. In addition, the ratio and size of the 1:5H phase (area 3) and the granular 2:17R type Hf-rich phase (area 4) also show the increasing trend. It is worth noting that when the HD temperature is 850 °C, the rod-like precipitates (area 5) in the microstructure. The distribution of the Hf element content in Figure (c) shows that both granular (L1) and rod-like (L2) are Hf-rich phase. Combined the diffraction pattern [Figure (i)], the rod-like precipitates might be 1:5H type Hf-rich phase. It can be found from Figure (b) that two different types of Hf-rich phases (2:17R and 1:5H) are preferentially enriched at grain boundaries, irregular granular shape (2:17R) at the triangular grain boundary, and rod-like shape (1:5H) at the biangular grain boundary.
Figure 5. TEM results of the HD 850 °C magnet: (a) The BF image of microstructure; (b) The high-angle annular dark field (HAADF) image, the yellow dotted line marks the grain boundary (GB); (c) The distribution of Hf element content in the corresponding area (L1, L2). (d) The IFFT result of twin, the green line indicates the twin boundary (TB); (e)-(i) Diffraction pattern of the corresponding areas (1, 2, 3, 4, 5) marked by the red dotted line in Figure (a). The test surface is perpendicular to the pressure direction of the HD magnet.
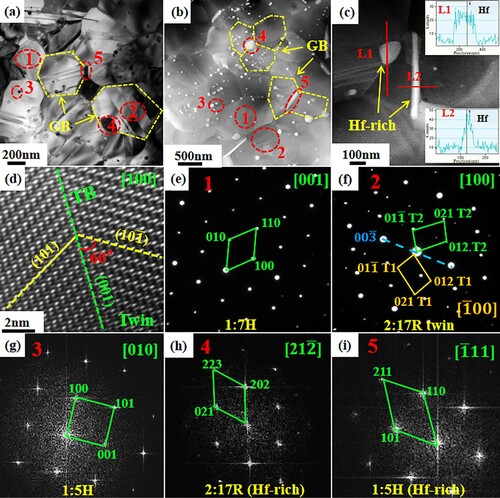
The above analysis shows that the phase stability of the SmCo6.8Hf0.2 magnets deteriorates with increasing the HD temperature, and more 1:7H phases decompose into 2:17R and 1:5H phases. It corresponds to the XRD result. There are two main reasons for the 1:7H phase decomposition during the HD process. First, the intense diffusion induces both faster grain growth (driven by the difference in energy between the grains and grain boundaries) and a greater decomposition degree of the metastable 1:7H structure (driven by the difference in energy between the 1:7H structure and the mixture structures of the 1:5H and 2:17R) [Citation36]. Second, the Hf-rich phase is precipitated from the 1:7H phase, so the Hf content in the matrix decreases, which is not conducive to the stabilization of the 1:7H phase structure.
Based on the structural evolution process analysis, it is found that HD temperature has a significant influence on the phase stability of the SmCo6.8Hf0.2 magnets [Citation37,Citation38]. Fig. S2 shows the structural evolution schematic diagram of the SmCo6.8Hf0.2 nanocrystalline magnet. For the single-phase nanocrystalline SmCo6.8Hf0.2, the 1:7H phase structure is stable. During the HD process, with the HD temperature increases, the effect of thermal activation enhances, and the pinning effect of the grain boundaries is significantly weakened [Citation39]. The intense diffusion induces that the stability of the 1:7H phase decreases, decomposing into 1:5H and 2:17R phases. The 1:5H phase randomly distributed in the form of spherical precipitates, and the 2:17R phase existed in the form of twins. The Hf-rich phases with 2:17R (granular) and 1:5H (rod-like) structures preferentially precipitated at grain boundaries. It is speculated that when the temperature is high enough, the 1:7H phase will be completely decomposed. During the phase transformation, the Co–Co dumbbell pair become ordered, which promotes the transformation of the lattice structure. The 2:17R twins with mirror symmetry are formed on both sides of the crystal plane. After ordering the Co–Co dumbbell pairs in the 1:7H phase is completed, the regions without Co–Co dumbbell pairs will form the 1:5H phase [Citation34]. In addition, as the twins develop, local stress concentration can be relieved, and the plastic deformation ability of the HD SmCo6.8Hf0.2 magnet can be improved.
The hot deformation (HD) technique is considered as one of the effective ways to obtain crystallographic texture and magnetic anisotropy for nanocrystalline permanent magnets. In previous studies, the texture formation mechanism of the HD Nd-Fe-B magnets has been discussed. For the HD Nd-Fe-B magnets with the Nd-rich phase, the texture in HD Nd-Fe-B magnets develops because of the stress-induced preferential grain growth via a dissolution-precipitation mechanism [Citation40]. For the HD Nd-Fe-B magnets without the Nd-rich phase, this can be attributed to a preferential nucleation of the Nd-Fe-B nanocrystals with a (00 l) orientation during the HD process under large uniaxial stress [Citation41,Citation42]. However, the HD SmCo6.8Hf0.2 nanocrystalline magnets do not have abundant Sm-rich boundary phases. It is speculated that the texture is formed under the condition of thermal-mechanical coupling. Under large height reduction, the hard magnetic phases nucleate preferentially along the c-axis, and then the (00 l) texture is formed by directional growth under the temperature gradient field. In addition, the sliding of grain boundaries is the main deformation mode of nanocrystalline materials at high temperature. The direct sliding and short-range diffusion of the atoms at grain boundaries coordinate to achieve grain boundary slip [Citation43]. The texture formation mechanism of the HD SmCo6.8Hf0.2 nanocrystalline magnets may also be related to the preferential diffusion slip induced by stress.
4. Conclusions
In summary, we have successfully prepared an anisotropic SmCo6.8Hf0.2 nanocrystalline magnet by the HP-HD method. The magnet exhibits a strong c-axis texture, which is attributed to the preferential nucleation of the SmCo6.8Hf0.2 nanocrystals during the hot deformation processes. As the deformation temperature increases, grains grow and the stability of the 1:7H phase decreases, which leads to the formation of the 2:17R and 1:5H phases. The 2:17R phase exists in the form of twins, and the 1:5H phase randomly distributes in a spherical form. There are also some Hf-rich phases (2:17R and 1:5H), distributing in grain boundaries in irregular granular (2:17R) and rod-like (1:5H) shapes. Under the combined influence of coercivity and remanence, the (BH)max of the HD magnet is significantly improved compared with isotropic HP magnets. Our findings provide a crucial strategy to create high-performance SmCo7-based nanostructured magnets.
Supplemental Material
Download MS Word (3.8 MB)Acknowledgements
This work was supported by the Natural Science Foundation of China (51871005, 51931007), and by the Key Program of Science and Technology Development Project of Beijing Municipal Education Commission of China under Grant (KZ202010005009).
Disclosure statement
No potential conflict of interest was reported by the author(s).
Additional information
Funding
References
- Liu JF, Ding Y, Hadjipanayis GC. Effect of iron on the high temp erature magnetic properties and microstructure of Sm(Co,Fe,Cu,Zr)z permanent magnets. J Appl Phys. 1999;85:1670–1674.
- Gutfleisch O, Willard MA, Brück E, et al. Magnetic materials and devices for the 21st century: stronger, lighter, and more energy efficient. Adv Mater. 2011;23:821–842.
- Yue M, Zhang XY, Liu JP. Fabrication of bulk nanostructured permanent magnets with high energy density: challenges and approaches. Nanoscale. 2017;9:3674–3697.
- Zhang ZX, Song XY, Qiao YK, et al. A nanocrystalline Sm-Co compound for high-temperature permanent magnets. Nanoscale. 2013;5:2279–2284.
- Luo J, Liang JK, Guo YQ, et al. Crystal structure of SmCo6.7Zr0.3 and NdCo4Cu3 compounds with TbCu7-type structure. J Alloys Compd. 2004;372(1-2):187–189.
- Song WP, Li XH, Lou L, et al. Anisotropic bulk SmCo7 nanocrystalline magnets with high energy product. APL Mater. 2017;5:116101.
- Seyring M, Song XY, Zhang ZX, et al. Concurrent ordering and phase transformation in SmCo7 nanograins. Nanoscale. 2015;7:12126–12132.
- Li XH, Lou L, Song WP, et al. Novel bimorphological anisotropic bulk nanocomposite materials with high energy products. Adv Mater. 2017;29:1606430.
- Chang HW, Huang ST, Chang CW, et al. Comparison on the magnetic properties and phase evolution of melt-spun SmCo7 ribbons with Zr and Hf substitution. Scr Mater. 2007;56:1099–1102.
- Liu T, Li W, Li XM, et al. Crystal structure and magnetic properties of SmCo7−xAGx. J Magn Magn Mater. 2007;310:e632–e634.
- Guo JG, Chen NX, Shen J. Atomistic simulation for disordered rare-earth compounds SmCo7 and Sm(Co, Ti)7. J Alloys Compd 2006;425:14–23.
- Zhou J, Al-Omari IA, Liu JP, et al. Structure and magnetic properties of SmCo7-xTix with TbCu7 structure. J Appl Phys. 2000;87:5299–5301.
- Yue M, Zhang JX, Zhang DT, et al. Structure and magnetic properties of bulk nanocrystalline SmCo6.6Nb0.4 permanent magnets. Appl Phys Lett. 2007;90:242506.
- Li YY, Shen J, Chen Y. Atomistic simulation for disordered TbCu7-type compounds SmCo7 and Sm(Co, T)7 (T = Ti, Ga, Si, Cu, Hf, Zr). Solid State Sci 2010;12:33–38.
- Guo YQ, Li W, Feng WC, et al. Structural stability and magnetic properties of SmCo7−xGax. Appl Phys Lett. 2005;86:192513.
- An SZ, Zheng L, Zhang TL, et al. Bulk anisotropic nanocrystalline SmCo6.6Ti0.4 permanent magnets. Scr Mater. 2013;68:432–435.
- Guo YQ, Feng WC, Li W, et al. Magnetism and phase stability of R(Co, M)7 pseudobinary intermetallics with TbCu7-type structure. J Appl Phys 2007;101:023919.
- Luo J, Liang JK, Guo YQ, et al. Effects of the doping element on crystal structure and magnetic properties of Sm(Co, M)7 compounds (M = Si, Cu, Ti, Zr, and Hf). Intermetallics, Intermetallics. 2005;13:710–716.
- Zhang DT, Yue M, Pan LJ, et al. Structure and magnetic properties of bulk nanocrystalline SmCo7−xHfx sintered magnets. J Appl Phys. 2008;103:07E124.
- Luo J, Liang JK, Guo YQ, et al. Crystal structure and magnetic properties of SmCo7-xHfx compounds. Appl Phys Lett. 2004;85(22):5299–5301.
- Zhang YW, Jiang WL, Wang CM, et al. Grain growth and phase stability of nanocrystalline cubic zirconia under Ion irradiation. Phys Rev B. 2010;82:184105.
- Hannon JB, Tersoff J, Tromp RM. Surface stress and thermodynamic nanoscale size selection. Science. 2002;295:299–301.
- Zhang ZX, Song XY, Xu WW, et al. Crystal structure and magnetic performance of single-phase nanocrystalline SmCo7 alloy. Scr Mater. 2010;62:594–597.
- Jiang CB, Venkatesan M, Gallagher K, et al. Magnetic and structural properties of SmCo7-xTix magnets. J Magn Magn Mater. 2001;236:49–55.
- Fuerst CD, Brewer EG, Mishra RK, et al. Die-upset Pr-Fe-B-type magnets from melt-spun ribbons. J Appl Phys. 1994;75:4208–4213.
- Li XH, Lou L, Song WP, et al. Controllably manipulating three-dimensional hybrid nanostructures for bulk nanocomposites with large energy products. Nano Lett. 2017;17(5):2985–2993.
- Xia XS, Liu M, Zhang TQ, et al. Dependence of grain size and aspect ratio on grain boundary additives in hot-deformed Nd-Fe-B magnets. Mater Charact. 2020;168:110543.
- Xu XC, Li YQ, Ma ZH, et al. Sm2Co7 nanophase inducing low- temperature hot deformation to fabricate high performance SmCo5 magnet. Scr Mater. 2020;178:34–38.
- Yang YQ, Zhang DT, Li YQ, et al. Phase and texture evolution of hot deformed Sm(Co,Fe,Cu,Zr)z magnet. IEEE Trans Magn. 2021;57(2):1–5.
- Li HL, Lou L, Hou FC, et al. Simultaneously increasing the magnetization and coercivity of bulk nanocomposite magnets via severe plastic deformation. Appl Phys Lett. 2013;103:142406.
- Yue M, Zuo JH, Liu WQ, et al. Magnetic anisotropy in bulk nanocrystalline SmCo5 permanent magnet prepared by hot deformation. J Appl Phys. 2011;109:07A711.
- Gabay AM, Marinescu M, Liu JF, et al. Deformation-induced texture in nanocrystalline 2:17, 1:5 and 2:7 Sm-Co magnets. J Magn Magn Mater 2009;321(19):3318–3323.
- Zhou XL, Song X, Jia WT, et al. Atomic scale understanding of the defects process in concurrent recrystallization and precipitation of Sm-Co-Fe-Cu-Zr alloys. Scr Mater. 2020;182:1–5.
- Zhang ZX, Song XY, Xu WW, et al. Phase evolution and its effects on the magnetic performance of nanocrystalline SmCo7 alloy. Acta Mater. 2011;59(4):1808–1817.
- Meltzman H, Mordehai D, Kaplan WD. Solid-solid interface reconstruction at equilibrated Ni-Al2O3 interfaces. Acta Mater. 2012;60:4359–4369.
- Hua G, Song XY, Liu D, et al. Effects of Hf on phase structure and magnetic performance of nanocrystalline SmCo7-type alloy. J Mater Sci. 2016;51(7):3390–3397.
- Xu WW, Song XY, Zhang ZX. Multiphase equilibrium, phase stability and phase transformation in nanocrystalline alloy systems. Nano. 2012;7:1250012.
- Xu WW, Song XY, Lu ND, et al. Thermodynamic and experimental study on phase stability in nanocrystalline alloys. Acta Mater. 2010;58:396–407.
- Xu WW, Song XY, Zhang ZX. Thermodynamic study on metastable phase: from polycrystalline to nanocrystalline system. Appl Phys Lett. 2010;97:181911.
- Chen RJ, Wang ZX, Tang X, et al. Rare earth permanent magnets prepared by hot deformation process. Chin Phys B. 2018;27:117504.
- Liu YG, Xu L, Wang QF, et al. Development of crystal texture in Nd-lean amorphous Nd9Fe85B6 under hot deformation. Appl Phys Lett. 2009;94:172502.
- Zhang XY. Heterostructures: new opportunities for functional materials. Mater Res Lett. 2020;8:49–59.
- Wang L, Zhang Y, Zeng Z, et al. Tracking the sliding of grain boundaries at the atomic scale. Science. 2022;375:1261–1265.