Abstract
We report the enhancement of the thermal conductivity of neopentylglycol (NPG) by compositing it with graphene nanosheets (GPNs). Adding 50 wt% GPNs enhanced the thermal conductivity from 0.42 to 18.4 Wm−1K−1, and the barocaloric entropy change can still reach 122 Jkg−1K−1 under pressure loading of 0 → 1.0 kbar. The obtained composites demonstrated reduced thermal hysteresis, which will facilitate the large reversible entropy change. The present work thus provides a simple and feasible way to enhance the thermal conductivity of plastic crystals with a giant barocaloric effect, and promisingly accelerate the application of these materials in the solid-state refrigeration technique.
GRAPHICAL ABSTRACT
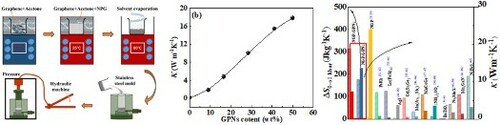
Solid-state refrigeration based on magnetocaloric, electrocaloric, and mechanocaloric effects (which refers to the adiabatic temperature change or the isothermal entropy change of the material upon the application of magnetic field, electric field, and stress respectively) is nowadays under extensive investigation worldwide [Citation1–14]. Recently, some compounds in the plastic crystals family have attracted much attention [Citation5–9] because of their giant barocaloric effect. The giant barocaloric effect of the plastic crystals stems from first-order phases transition that is accompanied by the extremely large latent heat, with the non-isochoric transitional character making their transition easily driven by pressure. Since B. Li et.al. reported the giant barocaloric effect in the plastic crystal NPG [Citation5], many plastic crystals with similar characteristics have been suggested as potential barocaloric candidates [Citation6–14].
However, to act as solid-state refrigerants, there are many other requirements except for the giant caloric effect, for example, thermal conductivity and thermal hysteresis are among the main concerns [Citation15–19]. For a refrigerant, the generated heat has to be transferred out of the solid body to surrounding heat transfer fluids to create the hot and cold end in the regenerator bed within a certain operating frequency [Citation17,Citation18]. Moreover, the dynamic study of the solid-state refrigeration prototype shows that the operating frequencies also demand high thermal conductivities [Citation15–17]. Nevertheless, the plastic crystal exhibits quite low thermal conductivity, taking the well-studied neopentylglycol (NPG) for example, its thermal conductivity is only 0.42 W m−1K−1 at room temperatures [Citation20], the ultra-low thermal conductivity inevitably inhibits its application as a solid-state refrigerant.
Carbon materials are known for their thermal-conductive properties and usually served as conductive fillers to enhance the thermal conductivity of polymer and plastic materials [Citation21–31]. Among the carbon materials,} graphene nanoplatelets (GNPs) that contain several layers of graphene are usually considered one of the best conductive fillers in carbon materials because of their good thermal conductivity, low cost, and fair dispersibility in the polymer matrix [Citation24–31]. Moreover, the unique layered nanostructure with platelet shape offers advantages over other spherical or cylindrical morphologies, because they can overlap with a large contact area permitting much closer contact between adjacent platelets and reducing the thermal contact resistance at the interfaces [Citation26,Citation31].
Hence, here in this article, the GPNs have been chosen as the conductive filler to fabricate the NPG-GPNs composites with high thermal conductivity. The NPG-GNPs composites were fabricated using a rather simple impregnation method. The results denote that the GNPs fillers were well dispersed into the NPG matrix, and high thermal conductivities were obtained. By compositing 50 wt% GPNs into NPG, the thermal conductivity can be enhanced from 0.42 to 18.4 W m−1K−1. Our further study demonstrates that the added GPNs do not influence the structural phase transitions of NPG, and the entropy change reaches 122 J kg−1K−1 for the NPG-GPNs composites under a pressure change of 0 → 1 kbar. The thermal conductivity and barocaloric entropy change were compared with the previously reported barocaloric materials [Citation32–50] and are shown in Figure . Obviously, the fabricated composites show priorities with both high thermal conductivity and large entropy change, thus promoting the possible application of the NPG plastic crystals as the solid-state refrigerator.
Figure 1 The comparison of the barocaloric entropy change under hydrostatic pressure change of 0 → 1 kbar and the thermal conductivity between the present composites and the reported barocaloric materials.
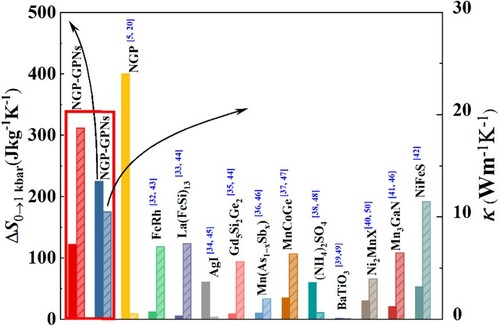
Graphene nanoplatelets (GNPs) were supplied by the Qingdao Yanhai carbon materials Co. Ltd. The GNPs have a platelet morphology with a thickness of 5-10 nm and an average width of 15 um. NPG is commercially accessible. The NPG-GNPs composites were prepared by a simple impregnation method. GPNs were firstly dispersed into 100 mL acetone and were ultrasonicated for 15 min, and NPG was added to the obtained solution. The mixture was ultrasonically treated for 30 min at room temperature to make the NPG dispersed in the solution. Subsequently, the solvent was evaporated by heating the solution to 80 °C accompanying the ultrasonic process, to let the acetone volatilize. Using this method, NPG-GNPs composites with GNPs mass ratios of 9.1, 16.6, 28.5, 41.1, and 50 wt% respectively were prepared. It needs to note here that the mass ratios of the composites are the starting ones that do not consider the possible evaporation of NPG during the fabrication process. The obtained powder composites were then pressed into a cycloidal plate with a thickness of 2 mm and a diameter of 20 mm. The fabrication process of the composites plates was briefly manifested in Figure (a). The thermal conductivity along the parallel direction of the obtained plates was measured with a hot disk thermal analyser, which was based upon a transient technique. The measurements were performed by putting the sensor between two similar composite plates. The sensor supplied a heat pulse to the sample and the associated change in temperature was recorded. The morphology of the composites was obtained by scanning electron microscopy (SEM). The structures of the obtained NPG-GNPs composites were identified by X-ray diffractometer with the in-situ change of temperatures from 300 to 350 K, the measured profiles were refined with GSAS software. The isobaric calorimetry was performed on Setaram-µDSCVII EVO device. Based on the obtained calorimetry data, the barocaloric entropy change was calculated.
Figure 2 (a) The schematic of the fabrication process of the NPG-GPNs composites. (b) Thermal conductivity evolution with the content of GPNs fillers of the composites, the inset in (b) denotes the fabrication stress influence on the thermal conductivity values of the composites with GPNs fillers content of 41.1 wt%. (c, d, e) SEM images of the cross-section morphology of NPG-GPNs composites plates with GPNs filler content of 9.1, 28.5, and 50 wt%.
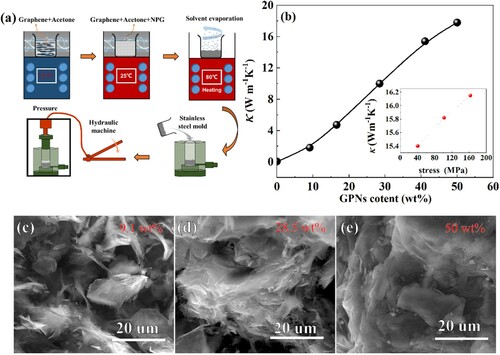
The thermal conductivity (κ) evolution with the weight fraction of GPNs for the in-plane direction of the composites plates is shown in Figure (b). It is seen that κ increases with weight fractions of GNPs. Specifically, when the weight ratio of the GPNs reaches 28.5% and 50%, the thermal conductivity tremendously reaches 10 and 18.4 W m−1K−1. Considering that the thermal conductivity can be well adjusted by the GPNs contents, the appropriate composites with appropriate thermal conductivity can then be utilized in the cooling prototype. Figure (c–e) show the SEM images of the section morphology of the samples with 9.1, 28.5, and 50 wt% GPNs fillers. As seen in the figures, GNPs flakes were dispersed uniformly throughout the matrix. Moreover, with the increasing content, the GPNs fillers provide a three-dimensional network, this network provides a path of lower resistance for phonons to travel [Citation24,Citation25]. The high aspect ratio and large interfacial contact area of GPNs as well as the strong interface between the GPNs and NPG will favor the thermal transport capacity of the composites. As a consequence, with the network becoming more and more connected with the increase of GPNs content, the thermal conductivity continuously increases. However, the thermal conductivity of the composites cannot increase infinitely with the GPNs content, it is because of the thermal resistance between the filler-filler and NPG-filler interfaces [Citation24,Citation25,Citation30]. Moreover, when increasing the stress of fabricating the composite plates, the in-plane thermal conductivity further increases, as shown in the inset of Figure (b). In the polymer-GPN, it has been reported that the physical stress can enforce the van der Walls interaction, causing the polymer to intercalate into the interstices of GNPs layers [Citation25]. The enforced interaction between the two groups of atoms at the two sides of the interface causes the enhancement of the thermal conductivity [Citation24,Citation25]. Hence, in the present case, the increased thermal conductivity of the composites with increasing pressures can be reasonably ascribed to the enhanced interaction between GPN and GNPs. On the around, the enhanced thermal conductivity also implies the penetration of the NPG into GNPs [Citation25].
It is now clear that introducing GPNs fillers can effectively enhance the thermal conductivity of NPG. However, whether the introduced GPNs fillers will influence the phase transition and further the barocaloric effect of NPG remains unclear, hence, in the following, the phase transition and barocaloric effect of the obtained composites will be investigated. NPG adopts an ordered monoclinic structure [Citation5,Citation6], on heating, it undergoes a phase transition to a cubic structure with four molecules per unit cell which owns an orientationally disordered configuration at any typical instant [Citation5]. The structural transition of the pure NPG was identified by XRD patterns with the in-situ change of temperature within 300 K to 350 K, as shown in Figure (a). At 300 K, it is in a monoclinic phase, when the temperature was increased to 310 K, the cubic phase can be indexed from the XRD patterns, indicating the phase transition. The lattice parameters and the cell volume were calculated from the typical diffractions. Figure (b) and (c) further display the XRD patterns measured at different temperatures for the composites with GNPs filler content of 28.5 wt% and 50 wt% respectively. For these two samples, an extra peak residing at 26.8° can be observed. For GPNs, the carbon atoms are bonded covalently in a hexagonal arrangement within their crystal layers and these layers are bonded to each other by weak Van Der Waals forces. The d-spacing between the carbon layers is ∼ 0.335 nm [Citation28,Citation29]. The peaks resided at 26.8° thus corresponding to the (0002) diffraction peaks of the GPNs. The diffraction peaks for the monoclinic structure of NPG can also be observed from the room temperature pattern. For the composites, the monoclinic to the cubic phase transition of NPG can be identified by the diffraction patterns, while the GPNs didn’t change their structure. The results reveal that introducing GPNs fillers does not influence the first-order phase transition of NPG.
Figure 3 The XRD patterns of pure (a) NPG and NPG-GPNs composites with (b) GPNs content of 28.5 wt%, and (c) GPNs content of 50 wt%, measured at various temperatures. The subscripts ‘m' and ‘c' refer to the monoclinic and cubic structures of NPG.
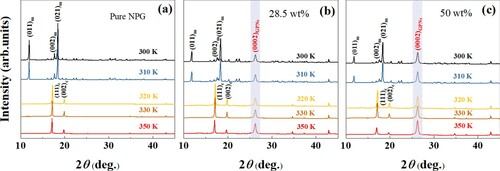
The structural phase transition exhibited above yields sharp heat flow along the heating and cooling process. Figure (a1–a3) show the calorimetry curves on heating and cooling across the first order monoclinic – cubic phase transition, under ambient pressure, 0.25 kbar, 0.5 kbar, 0.75 kbar, and 1 kbar. The baselines were subtracted from the measured dQ/dT curves. To calculate the barocaloric effect, the isobaric entropy curves S’(T, p) at different pressures with respect to a reference value taken at normal pressure and at a temperature T0 freely chosen well below the transition temperatures. The obtained S'(T, p) = S(T, p)−S(250 K, 0) curves on heating and S'(T, p) = S(T, p)−S(380 K, 0) on cooling were shown in Figure (b1–b3) on cooling. Following the isothermal paths of isobaric entropy on cooling, the entropy change ΔS(T, 0 → p) on applying pressure can be obtained. Similarly, by subtracting isobaric entropies at different pressures on heating, the barocaloric entropy change upon unloading of pressure can be calculated. The obtained barocaloric entropy changes with loading and unloading of different pressures were shown in Figure (c1–c3) for the three samples. The maximum entropy changes are 372.4 J kg−1K−1 for the pure NPG under 0 → 1 kbar hydrostatic loading, which is consistent with the previous reports [Citation5–7]. After compositing with the GNPs fillers, the barocaloric entropy change decreases for the same hydrostatic pressure change. The entropy changes were 225 J kg−1K−1 and 122 J kg−1K−1 for the filler content of 28.5 wt% and 50 wt% under 0 → 1 kbar hydrostatic pressure change. This is foreseeable because the GPNs fillers do not participate in the phase transition. It is worth noting that though the barocaloric entropy change is reduced after adding the GNPS filler, its values are still larger than the conventional barocaloric materials [Citation32–42] and makes the composites fascinating. As is seen in Figure , the present NPG-GPNs composites exhibit priorities in both the barocaloric effect and the thermal conductivity.
Figure 4 The dQ/dT curves of the (a1) pure NPG, NPG-GPNs composites with the NPG content of (a2) 28.5 wt%, and (a3) 50 wt%, measured under hydrostatic pressure of 0, 0.25, 0.5, 0.75, and 1.0 kbar. (b1-b3) The corresponding isobaric entropy curves S’(T, p) at different pressures for the three samples. (c1-c3) The barocaloric entropy change for hydrostatic pressure changes of 0 → 0.25 kbar, 0 → 0.5 kbar, 0 → 0.75 kbar, and 0 → 1 kbar for the compression and decompression process.
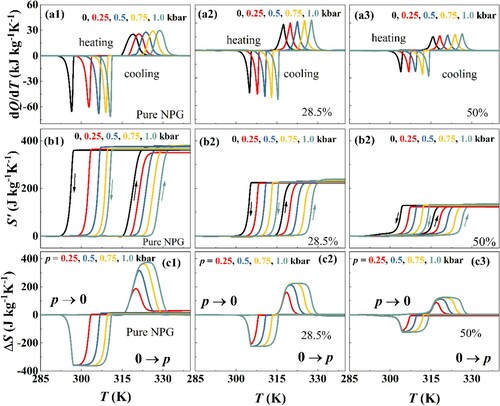
Further analysis reveals that compositing GPNs fillers will promote the reversibility of entropy change of the NPG. The reversible isothermal entropy change/adiabatic temperature change, meaning the accessible entropy change under cycling external fields is closely related to two characters for a material [Citation8,Citation11]. The first one is the thermal hysteresis (ΔThys) of the first-order phase transition, and the second one is the transition temperatures response to the external field. Specifically, the minimum pressure prev above which the reversible entropy change becomes nonzero, or obtaining the reversible entropy/adiabatic temperature change can be identified by these two parameters: prev = ΔThys/(ΔTt/Δp) [Citation8], where ΔThys means the thermal hysteresis at ambient pressure and ΔTt/Δp is transition temperature change rate with pressure. For the present composites, the transition temperature for the heating and cooling process was determined as the temperatures corresponding to the dQ/dT peak values. The transition temperatures for the heating and cooling process are 318 K and 296 K for the pure NPG, and are 316 K and 305 K for the composites with GPNs filler content of 50 wt% respectively. The thermal hysteresis was calculated by subtracting the transition temperatures during the cooling process from the ones during the heating process. The obtained ΔThys at ambient pressure reduces from 22 to 11 K when 50 wt% GPNs fillers were added to the GPN. Further using the transition temperature at different hydrostatic pressures, the ΔTt/Δp of 11 Kkbar−1 can be obtained for the samples during the heating process. The minimum pressure needed to achieve the reversible entropy change for the composites with GPNs filler of 50 wt% is thus 1.0 kbar, which is reduced compared with the 2.0 kbar for the pure NPG. The reversible entropy changes can be characterized as the overlapping between ΔS obtained upon pressure loading (heating) and unloading (cooling) process [Citation8]. Accordingly, for the composites with GPNs filler of 28.5 wt% and 50 wt%, there appears overlapping for the ΔS curves with application and removal of the hydrostatic pressure of 1 kbar, as is seen in Figure (c2) and (c3), while for the pure NPG, there is no overlapping for the ΔS curves (Figure (c1)). The results thus demonstrate that the addition of GPNs filler in NPG is able to reduce the thermal hysteresis of the transition and facilitate the achievement of the reversible entropy change under a relatively small hydrostatic pressure. It has been reported that the thermal hysteresis originates from the friction of the phase boundaries between the parent and production phases [Citation51], and the introduction of porous or the partial removal of grain boundaries through changing the sample geometry will reduce the thermal hysteresis in the MCE materials [Citation52,Citation53]. For the present composites, GPNs act as the framework, in which the NPG penetrates, which resembles the case where the porous was introduced in the sample and may reduce the thermal hysteresis by reducing the interface friction between the parent and production phases during the phase transition.
In conclusion, the thermal conductivity of plastic crystal NPG has been tremendously enhanced using a rather simple method. The GPNs fillers can effectively increase the thermal conductivity of NPG. The SEM images reveal a good interface coupling between NPG and GPNs which is the origin of the large enhancement of the thermal conductivity. The X-ray diffraction with an in-situ change of temperatures shows that the addition of GPNs filler does not influence the phase transition of NPG. The retained phase transition in the composites guarantees the giant barocaloric effect. Further isotropic calorimetry studies reveal the reduction of the thermal hysteresis and a giant barocaloric effect in the sample. This work provides a rather simple method to increase the thermal conductivity of plastic crystals and promotes the potential application of plastic crystals as solid-state refrigerants.
Disclosure statement
No potential conflict of interest was reported by the author(s).
Additional information
Funding
References
- Moya X, Kar-Narayan S, Mathur ND. Caloric materials near ferroic phase transitions. Nat Mater. 2014;13:439–450. doi:https://doi.org/10.1038/nmat3951
- Mañosa L, Planes A. Materials with giant mechanocaloric effects: cooling by strength. Adv Mater. 2017;29:1603607. doi:https://doi.org/10.1002/adma.201603607
- Neese B, Chu BJ, Lu SG, et al. Large electrocaloric effect in ferroelectric polymers near room temperature. Sci. 2008;321:821–823. doi:https://doi.org/10.1126/science.1159655
- Moya X, Mathur ND. Caloric materials for cooling and heating. Sci. 2020;370:797–803. doi:https://doi.org/10.1126/science.abb0973
- Li B, Kawakita Y, Ohira-Kawamura S, et al. Colossal barocaloric effects in plastic crystals. Nat. 2019;567:506–510. doi:https://doi.org/10.1038/s41586-019-1042-5
- Lloveras P, Aznar A, Barrio M, et al. Colossal barocaloric effects near room temperature in plastic crystals of neopentylglycol. Nat Commun. 2019;10:1803. doi:https://doi.org/10.1038/s41467-019-09730-9
- Li FB, Li M, Xu X, et al. Understanding colossal barocaloric effects in plastic crystals. Nat Commun. 2020;11:4190. doi:https://doi.org/10.1038/s41467-020-18043-1
- Aznar A, Lloveras P, Barrio M, et al. Reversible and irreversible colossal barocaloric effects in plastic crystals. J Mater Chem A. 2020;8:639–647. doi:https://doi.org/10.1039/C9TA10947A
- Li JN, Barrio M, Dunstan DJ, et al. Colossal reversible barocaloric effects in layered hybrid perovskite (C10H21NH3)2MnCl4 under Low pressure near room temperature. Adv Funct Mater. 2021;31:2105154. doi:https://doi.org/10.1002/adfm.202105154
- Aznar A, Negrier P, Planes A, et al. Reversible colossal barocaloric effects near room temperature in 1-X-adamantane (X=Cl, Br) plastic crystals. Appl Mater Today. 2021;23:101023. doi:https://doi.org/10.1016/j.apmt.2021.101023
- Zhang Z, Chen YN, Qi J. High-energy x-ray diffraction study on phase transition asymmetry of plastic crystal neopentylglycol. Chin Phys B. 2022;31:036802. doi:https://doi.org/10.1088/1674-1056/ac140c
- Ren QY, Qi J, Yu DH. Ultrasensitive barocaloric material for room-temperature solid-state refrigeration. Nat Commun. 2022;13:2293. doi:https://doi.org/10.1038/s41467-022-29997-9
- Bermúdez-García JM, Sánchez-Andújar M, Castro-Garcúa S, et al. Giant barocaloric effect in the ferroic organic-inorganic hybrid [TPrA][Mn(dca)3] perovskite under easily accessible pressures. Nat Commun. 2017;8:15715. doi:https://doi.org/10.1038/ncomms15715
- von Ranke PJ, Alho BP, da Silva PH. Refrigeration through barocaloric effect using the spin crossover complex {Fe[H2 B(pz)2]2(bipy)}. physica status solidi (b). 2021;258:2100108. doi:https://doi.org/10.1002/pssb.202100108
- Kitanovski A, Plaznik U, Tomc U, et al. Present and future caloric refrigeration and heat-pump technologies. Int J Refrig. 2015;57:288–298. doi:https://doi.org/10.1016/j.ijrefrig.2015.06.008
- Lovell E, Pereira AM, Caplin AD, et al. Dynamics of the first-order metamagnetic transition in magnetocaloric La(Fe,Si)13: Reducing hysteresis. Adv Energy Mater. 2015;5:1401639. doi:https://doi.org/10.1002/aenm.201401639
- Porcari G, Morrison K, Cugini F, et al. Influence of thermal conductivity on the dynamic response of magnetocaloric materials. Int J Refrig. 2015;59:29–36. doi:https://doi.org/10.1016/j.ijrefrig.2015.06.028
- Nielsen KK, Engelbrecht K. The influence of the solid thermal conductivity on active magnetic regenerators. J Appl Phys. 2012;45:145001.
- Weise B, Sellschopp K, Bierdel M, et al. Anisotropic thermal conductivity in epoxy-bonded magnetocaloric composites. J Appl Phys. 2016;120:125103. doi:https://doi.org/10.1063/1.4962972
- Wang XL, Guo QG, Zhong YJ. Heat transfer enhancement of neopentyl glycol using compressed expanded natural graphite for thermal energy storage. Renew Energ. 2013;51:241–246. doi:https://doi.org/10.1016/j.renene.2012.09.029
- Chen SS, Wu QZ, Mishra C, et al. Thermal conductivity of isotopically modified graphene. Nat Mater. 2012;11:203–207. doi:https://doi.org/10.1038/nmat3207
- Veca LM, Meziani MJ, Wang W, et al. Carbon nanosheets for polymeric nanocomposites with high thermal conductivity. Adv Mater. 2009;21:2088–2092. doi:https://doi.org/10.1002/adma.200802317
- Nan CW, Liu G, Lin YH, et al. Interface effect on thermal conductivity of carbon nanotube composites. Appl Phys Lett. 2004;85:3549–3551. doi:https://doi.org/10.1063/1.1808874
- Han ZD, Fina A. Thermal conductivity of carbon nanotubes and their polymer nanocomposites: A review. Prog Polym Sci. 2011;36:914–944. doi:https://doi.org/10.1016/j.progpolymsci.2010.11.004
- Luo TF, Lloyd JR. Enhancement of thermal energy transport across graphene/graphite and polymer interfaces: a molecular dynamics study. Adv Funct Mater. 2012;22:2495–2502. doi:https://doi.org/10.1002/adfm.201103048
- Chu K, Li WS, Dong HF. Role of graphene waviness on the thermal conductivity of graphene composites. Appl Phys A. 2013;111:221–225. doi:https://doi.org/10.1007/s00339-012-7497-y
- Wang Y, Yang CH, Mai YW, et al. Effect of non-covalent functionalisation on thermal and mechanical properties of graphene-polymer nanocomposites. Carbon N Y. 2016;102:311–318. doi:https://doi.org/10.1016/j.carbon.2016.02.069
- Mohsin AR, Aidan W, Andy B, et al. Characterisation of graphite nanoplatelets and the physical properties of graphite nanoplatelet/silicone composites for thermal interface applications. Carbon N Y. 2011;49:4269–4279. doi:https://doi.org/10.1016/j.carbon.2011.06.002
- Valerio C, Carla M, Antonio M, et al. Morphological and structural characterization of polypropylene/conductive graphite nanocomposites. Eur Polym J. 2006;42:3153–3161. doi:https://doi.org/10.1016/j.eurpolymj.2006.08.017
- Yavari F, Fard HR, Pashayi K, et al. Enhanced thermal conductivity in a nanostructured phase change composite due to low concentration graphene additives. J Phys Chem C. 2011;115:8753–8758. doi:https://doi.org/10.1021/jp200838s
- Smith DK, Pantoya ML. Effect of nanofiller shape on effective thermal conductivity of fluoropolymer composites. Compos Sci Technol. 2015;118:251–256. doi:https://doi.org/10.1016/j.compscitech.2015.09.010
- Stern-Taulats E, Planes A, Lloveras P, et al. Barocaloric and magnetocaloric effects in Fe49Rh51. Phys Rev B. 2014;89:214105. doi:https://doi.org/10.1103/PhysRevB.89.214105
- Mañosa L, González-Alonso D, Planes A, et al. Inverse barocaloric effect in the giant magnetocaloric La-Fe-Si-Co compound. Nat Commun. 2011;2:595. doi:https://doi.org/10.1038/ncomms1606
- Aznar A, Lloveras P, Romanini M, et al. Giant barocaloric effects over a wide temperature range in superionic conductor AgI. Nat Commun. 2017;8:1851. doi:https://doi.org/10.1038/s41467-017-01898-2
- Yuce S, Barrio M, Emre B, et al. Barocaloric effect in the magnetocaloric prototype Gd5Si2Ge2. Appl Phys Lett. 2012;101:071906. doi:https://doi.org/10.1063/1.4745920
- de Medeiros LG, de Oliveira NA, Troper A. Giant magnetocaloric and barocaloric effects in Mn(As1−Sb ). J Alloys Compd. 2010;501:177–182. doi:https://doi.org/10.1016/j.jallcom.2010.03.244
- Wu RR, Bao LF, Hu FX, et al. Giant barocaloric effect in hexagonal Ni2In-type Mn-Co-Ge-In compounds around room temperature. Sci Rep. 2015;5:18027. doi:https://doi.org/10.1038/srep18027
- Lloveras P, Stern-Taulats E, Barrio M, et al. Giant barocaloric effects at low pressure in ferrielectric ammonium sulphate. Nat Commun. 2015;6:8801. doi:https://doi.org/10.1038/ncomms9801
- Stern-Taulats E, Lloveras P, Barrio M, et al. Inverse barocaloric effects in ferroelectric BaTiO3 ceramics. APL Mater. 2016;4:091102. doi:https://doi.org/10.1063/1.4961598
- Mañosa L, González-Alonso D, Planes A, et al. Giant solid-state barocaloric effect in the Ni-Mn-In magnetic shape-memory alloy. Nat Mater. 2010;9:478–481. doi:https://doi.org/10.1038/nmat2731
- Matsunami D, Fujita A, Takenaka K, et al. Giant barocaloric effect enhanced by the frustration of the antiferromagnetic phase in Mn3GaN. Nat Mater. 2015;14:73–78. doi:https://doi.org/10.1038/nmat4117
- Lin JC, Tong P, Zhang XK, et al. Giant room-temperature barocaloric effect at the electronic phase transition in Ni1−x FexS. Mater Horiz. 2020;7:2690–2695. doi:https://doi.org/10.1039/C9MH01976F
- Jiménez MJ, Schvval AB, Cabeza GF. Ab initio study of FeRh alloy properties. Comput Mater Sci. 2020;172:109385. doi:https://doi.org/10.1016/j.commatsci.2019.109385
- Fujieda S, Hasegawa Y, Fujita A, et al. Thermal transport properties of magnetic refrigerants La(FexSi1−x)13 and their hydrides, and Gd5Si2Ge2 and MnAs. J Appl Phys. 2004;95:2429–2431. doi:https://doi.org/10.1063/1.1643774
- Kazutaka N, Yasuhiko T, Tomoyoshi M. Thermoelectric properties of molten Bi2 Te3, CuI, and AgI. Appl Phys Lett. 2013;102:033903. doi:https://doi.org/10.1063/1.4788729
- Wada H, Fukuda K, Ohnishi T, et al. Thermal conductivity of giant magnetocaloric Mn compounds. J Alloys Compd. 2019;785:445–451. doi:https://doi.org/10.1016/j.jallcom.2019.01.188
- Zhu F, Lin JC, Jiang WB, et al. Enhanced mechanical properties and large magnetocaloric effect in epoxy-bonded Mn0.98CoGe. Scr Mater. 2018;150:96–100. doi:https://doi.org/10.1016/j.scriptamat.2018.02.044
- Che YY, Shen J, Zhou JC, et al. Thermal conductivity and density of (NH4)2SO4+H2O, NH4NO3+H2O, and (NH4)2SO4+NH4NO3+H2O solutions at T = (278.15 to 333.15) K. J Chem Eng Data. 2012;57:1486–1491. doi:https://doi.org/10.1021/je201390r
- Suemune Y. Thermal conductivity of BaTiO3 and SrTiO3 from 4.5° to 300°K. J Phys Soc Japan. 1965;20:174. doi:https://doi.org/10.1143/JPSJ.20.174
- Ito M, Kuwahara S, Taira A, et al. Ni deficiency effects on martensitic phase transition in Ni2MnGa. Phys B Condens Matter. 2021;611:412794. doi:https://doi.org/10.1016/j.physb.2020.412794
- Wang WH, Chen JL, Liu ZH, et al. Thermal hysteresis and friction of phase boundary motion in ferromagnetic Ni52Mn23Ga25 single crystals. Phys Rev B. 2001;65:012416. doi:https://doi.org/10.1103/PhysRevB.65.012416
- Lyubina J, Schäfer R, Martin N, et al. Novel design of La(Fe,Si)13 alloys towards high Magnetic refrigeration performance. Adv Mater. 2010;22:3735–3739. doi:https://doi.org/10.1002/adma.201000177
- Moore JD, Perkins GK, Bugoslavsky Y. Reducing the operational magnetic field in the prototype magnetocaloric system Gd5Ge4 by approaching the single cluster size limit. Appl Phys Lett. 2006;88:072501. doi:https://doi.org/10.1063/1.2173631