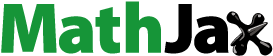
Abstract
A high-strength binary Mg–15Gd alloy plate, prepared by the conventional extrusion, warm-rolling and aging, exhibits an excellent mechanical property with 504, 518 MPa and 4.5% for yield strength, ultimate tensile strength and elongation, which is mainly attributed to the nano substructure with boundary segregation of Gd atoms, the high-density nano clusters induced by dislocations in the interior of grains, the high-density dynamical precipitates with submicron size, and the strong basal texture.
GRAPHICAL ABSTRACT
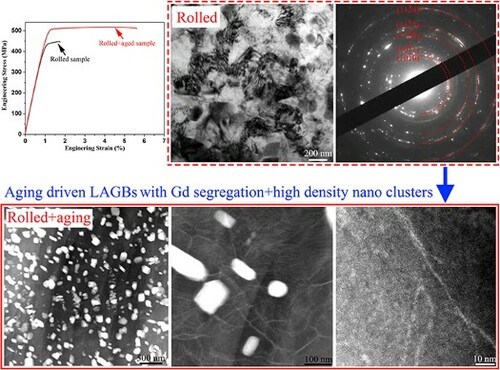
IMPACT STATEMENT
A new strengthening mechanism involving the nano substructure with Gd segregation, high-density nano Gd clusters induced by dislocations, and high-density dynamical precipitates has been found in Mg–Gd binary alloys.
1. Introduction
Magnesium (Mg) alloys have extensive application prospects in automotive, aerospace, electronic products and other fields as light structural materials due to their low density and high specific strength. Alloying rare earth (RE) element into Mg to obtain a highstrength is explored by using many preparation methods [Citation1–8]. The Mg–Y–Zn alloy prepared by rapidly solidified powder metallurgy exhibits a high strength due to the presence of fine grains and dispersion of long period stacking ordered structures [Citation1]. A high-strength Mg–8.5Gd–2.3Y–1.8Ag–0.4Zr (wt. %) alloy plate prepared by hot rolling is mainly strengthened due to the high-density stacking faults with nanoscale spacing [Citation2]. The high-strength in Mg–1.8Gd–1.8Y–0.7Zn–0.2Zr (at.%) alloy, fabricated by hot extrusion followed by aging, is attributed to the fine precipitates from the aging and dynamic precipitates at the grain boundaries of dynamically recrystallized grains [Citation3]. The high strength for the bimodal-structure Mg–13Gd alloys, prepared by low temperature and low extrusion ratio, is mainly attributed to the strong texture and the high-density prismatic precipitates [Citation4]. Besides, the Mg–Gd–Y–Zr alloy prepared by rotary swaging reaches an ultrahigh strength, which is mainly attributed to the nano-grain, intra-granular Gd-rich clustering, inter-granular solutes segregation, β’ precipitate, dislocation and solution strengthening contributions [Citation5].
The strengthening modes for Mg alloys are generally dependent on grain boundaries (fine grains, bimodal structure, nano grains), dislocations, texture, precipitates (dynamical precipitates during deformation or prismatic precipitates during heat treatment), as well as the solid solution of solute into the matrix [Citation6–15]. It is worthy to note that the grain boundary strengthening has limited contribution to the enhancement of the strength of Mg alloys, usually less than 400 MPa. The strong texture, high-density precipitates, solute segregation and atoms clustering are commonly considered to combine with the grain boundary strengthening for further improving the strength of Mg alloys.
Though lots of investigations are done for enhancing the high strength in Mg alloys, it is still a great challenge to achieve an industrial production of Mg alloys with high strength above 500 MPa. In this study, the proper conventional extrusion process is chosen for achieving a fine-grained Mg–Gd binary alloy with a complete dynamical recrystallized (DRXed) microstructure. Subsequently, nano substructures and high-density dislocations without twins can be introduced into the fine-grained Mg–Gd binary alloy by warm rolling. The nano substructure promotes further formation of the Gd segregation on the low angle grain boundaries (LAGBs), and the high-density dislocations can effectively help to form high-density clusters with a several nanometer size within matrix during aging. Thus, the high-strength Mg–15Gd binary alloy mainly strengthened by the nano substructure with Gd segregation and the high-density nano clusters is successfully fabricated.
2. Materials and methods
Mg–15Gd (wt.%) alloy with the actual composition of 85.3Mg–14.7Gd (wt.%) detected by inductively coupled plasma spectrometry was prepared by semi-continuous casting method and the raw materials used were commercial purity magnesium Mg (99.9%, wt.%) and Mg–30Gd (wt.%) master alloy. The alloy was melted at 750 °C and then poured into a cooled crystallizer at 720 °C to prepare the billet. Cylindrical-shaped samples with a height of 100 mm and a diameter of 90 mm were cut from the billet. The cylindrical samples were homogenized at 500 °C for 24 h and then quenched in warm water above 80 °C. These homogenized samples were kept in furnace for 0.5 h at 325 °C, and then extruded. The extrusion chamber temperature of 340 °C, the mold temperature of 330 °C, the ram speed of 0.2 mm/s and the extrusion ratio of 28 were chosen. Finally, an extruded bar with a diameter of 17 mm was produced, which was named as E sample. Plates with a dimension of 100 mm × 10 mm × 2 mm were cut from the extruded bars, and then the plates were preheated at 270 °C for 10 min in a resistance furnace, and mill rolls were heated to 250 °C by the resistance heater. Then single pass large-strain warm rolling was conducted with thickness reductions of 60%, which resulted in rolled sheets with 0.8 mm in thickness, and the rolling direction (RD) was parallel to the extruded direction (ED). The normal direction is abbreviated as ND, the transverse direction is abbreviated as TD and the rolled Mg–15Gd sample was named as E + R sample. Some rolled samples were aged at 200 °C for 0.5 h, which were named as E + R+A samples. The schematic flow diagram of material processing is shown in supplementary Figure S1.
Tensile plates with a gauge length of 33 mm, a width of 6 mm and a thickness of 0.75 mm were tested using a Shimadzu Autograph AG-I (500 kN) with an initial strain rate of 10−3/s at room temperature. The tensile direction is parallel to RD, and three tests with same parameters were done for reproducibility. The microstructure of extruded sample was characterized by a FEI Nova 400 scanning electron microscope equipped with Oxford HKL Channel 5 electron backscattered diffraction (EBSD) detector. EBSD sample was prepared by mechanical polishing followed by Ar ion milling. X-ray diffraction (XRD) (Rigaku D/max-2500 PC) technique in a Cu Kα radiation at 40 kV and 150 mA was used to study the overall texture evolution of rolled and aged plates. The {1010} and {0002} pole figures were measured up to a maximum tilt angle of 70°. The sample for XRD measurement was prepared by mechanical polishing and the same position of one sample before and after aging is chosen for macrotexture measurement. The microstructure was characterized by a JEOL JEM-2100F transmission electron microscope (TEM) operated at 200 kV and a Cs-corrected FEI Titan G2 60–300 ChemiSTEM operated at 300 kV. The thin foil samples for TEM observation were prepared using low energy ion beam thinning technique.
3. Results
Figure shows the EBSD analysis and TEM image for E sample, which contains a weak texture with the maximum intensity of 2.1, an average grain size of ∼1 µm. A high-volume fraction of dynamical Mg5Gd precipitates [Citation4,Citation16,Citation17], which have an average diameter of ∼150 nm, can be also detected. Figure (a) shows the tensile curves of the E + R sample and the E + R+A sample. The yield strength, ultimate tensile strength and elongation are 435 MPa, 447 MPa and 0.8%, respectively for the E + R sample, and correspond to 504 MPa, 518 MPa, and 4.5% for the E + R+A sample. The yield strengths and elongations for present Mg–15Gd alloy and other reported Mg–Gd–(Zr) and Mg–Gd–Y–Zr alloys with similar chemical compositions are compared and shown in supplementary Figure S2. Note that the strength of the E + R+A sample is superior to the recently reported Mg–Gd–(Zr) and Mg–Gd–Y–Zr alloys [Citation18–24]. Figure (b,c) exhibits the {0002} and {10-10} pole figures of the E + R sample and the E + R+A sample from the XRD measurement. The texture contains mainly a component of {0002} plane parallel to RD–TD plane and , and the maximum texture intensity is 4.4 for the E + R sample and 5.8 for the E + R+A sample. It shows also the {0002} plane parallel to RD–TD plane is strengthened and the
is weakened after aging. Figure shows the TEM images of the E + R sample. The high-density dynamical precipitates with a volume fraction of ∼40% and an average size of ∼150 nm can be observed in Figure (a). It is noted that many grains or substructures with nanometer size should be contained in the E + R sample, as observed from the diffraction rings of α-Mg in Figure (b). The high-density dislocations without twins can be observed in the magnified microstructure in Figure (c). Figure (d) exhibits the HAADF image of the magnified microstructure, where the segregation of Gd atoms on the high-density dislocations within grains cannot be observed. Figure (e) shows the magnified image of the red rectangle in (d) for the boundary observation, and the corresponding selected area electron diffraction (SAED) pattern is shown in Figure (f), indicating the segregation of Gd atoms distributes mainly along the low angle grain boundary with a misorientation angle of ∼ 4°.
Figure 1. EBSD and TEM images for E sample. (0002) pole figures (a), IPF maps with the reference direction parallel to ED (b), and TEM image of the microstructure containing the equiaxed grains and dynamical precipitates (c).
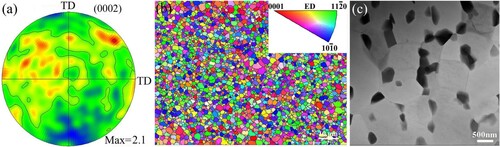
Figure 2. Tensile engineering stress–strain curves for the E + R sample and the E + R+A sample (a), XRD texture for the E + R sample (b) and the E + R+A sample (c).
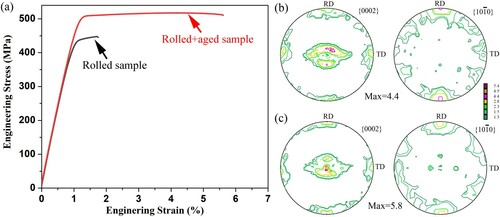
Figure 3. TEM images of the E + R sample: (a) microstructure containing the high-density dynamical precipitates and fine grains; (b) the diffraction pattern corresponding to the (a);(c)the magnified microstructure for dislocations observation; (d) HAADF image of the magnified microstructure; (e) Magnified HAADF image of the red rectangle in (d) for the low angle boundary observation; (f) corresponding to the diffraction pattern of the microstructure in (e). (For interpretation of the references to colour in this figure legend, the reader is referred to the web version of this article.)
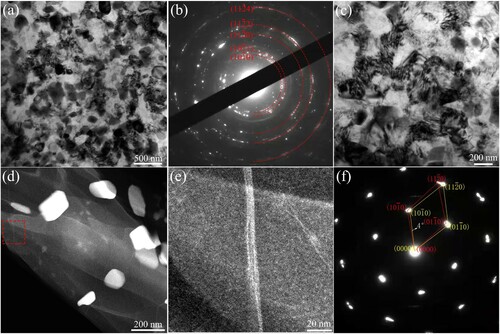
Figure shows the TEM images for the E + R+A sample. The high-density Mg5Gd precipitates (the bright particles) with a volume fraction of ∼40% and an average size of ∼150 nm are uniform in the E + R+A sample (Figure (a)), which are similar to those in the E + R sample (Figure (a)) mainly formed during the extrusion and the rolling. Figure (b) exhibits more segregation of Gd atoms on dislocations and LAGBs, which make a distinct contrast at the trace of dislocation and boundary when it is observed under the HAADF condition, suggesting there are high-density dislocations and LAGBs with the segregation of Gd atoms existing in the matrix. The recovery accompanied with the decrease of dislocation density occurs generally during aging, which causes the formation of more LAGBs in the E + R+A sample compared with those in the E + R sample. For the E + R+A sample, the high-density dislocations still exist in the matrix, though the recovery of some dislocations occurs. To further analyze the microstructure evolution during aging, the matrix region without the dynamical precipitate as indicated by the red rectangle (Figure (c)) is observed using an electron beam parallel to the [0001]Mg, and the satellite reflection spots pointed by the red arrows (Figure (d)) indicate there are Gd clusters distributing along the dislocations within the grain, and also suggest that no new phase is formed in the matrix, which is similar to the research result in aged Mg–Gd–Ag alloys [Citation11]. Figure (e) shows the HAADF image of the magnified microstructure at the red circle region in Figure (c), where the trace of Gd segregation along the dislocations within the grain can be clearly observed. Figure (f) shows the magnification of the matrix marked by red rectangle region in Figure (e), the dislocations lying on the (0001) plane have a clear trace observed by the HAADF due to the Gd atoms segregation on those dislocations. High-density dislocations containing basal and non-basal types can be formed during warm rolling, and many dislocations must have a certain angle with the (0001) crystal plane rather than lying on the (0001) plane. Thus, many clusters with a size of several nanometer (pointed by the red arrows) formed along the dislocations within the matrix are observed due to Gd atoms segregation on the segment of dislocations on the (0001) plane (Figure (f)). The several nanometer clusters (pointed by the red arrows in Figure (g)) are observed by the high resolution TEM (HRTEM), where the satellite reflection spot, pointed by the yellow arrows in Figure (g), in the Fast Fourier Transform (FFT) for the clusters is consistent with that in Figure (d). (For interpretation of the references to colour in this figure legend, the reader is referred to the web version of this article.)
Figure 4. TEM images for the E + R+A alloy: (a) HAADF image of the microstructure containing the high-density dynamical precipitates; (b) HAADF image of the magnified microstructure containing more dislocation boundaries; (c) microstructure containing dynamical precipitates and the matrix; (d) the diffraction pattern corresponding to the matrix region indicated by the red circle in c, and an electron beam parallel to the [0001]Mg is used; (e) HAADF image of the magnified microstructure at the red circle region in (c); (f) the magnified matrixmicrostructure at the red rectangle region in (e); (g) HRTEM image for the matrix containing the several-nanometer clusters and correspond to FFT.
![Figure 4. TEM images for the E + R+A alloy: (a) HAADF image of the microstructure containing the high-density dynamical precipitates; (b) HAADF image of the magnified microstructure containing more dislocation boundaries; (c) microstructure containing dynamical precipitates and the matrix; (d) the diffraction pattern corresponding to the matrix region indicated by the red circle in c, and an electron beam parallel to the [0001]Mg is used; (e) HAADF image of the magnified microstructure at the red circle region in (c); (f) the magnified matrixmicrostructure at the red rectangle region in (e); (g) HRTEM image for the matrix containing the several-nanometer clusters and correspond to FFT.](/cms/asset/87ac8d5a-4aaf-49ef-858c-f8de3873fb85/tmrl_a_2086834_f0004_oc.jpg)
4. Discussion
The complete DRXed microstructure with a fine grain size, a weak texture and a high density of dynamical precipitates in the extruded Mg–15Gd binary sample (E sample), which is generally easily formed in Mg alloys using a low temperature extrusion process [Citation25], exhibits an excellent deformation ability when it is rolled at 270 °C. Therefore, a large thickness reduction of 60% can be obtained by a single pass rolling. The main deformation mode is dislocations slip without twinning during rolling due to the fine-sized grain, the ample submicron dynamical precipitates, as well as the high rolling temperature [Citation26–28]. The ∼1 µm fine grains with random grain orientation for the E sample promote dislocation slip during warm rolling, and the submicron dynamical precipitates can increase the density of dislocations by the interaction with the dislocations. Thus, the high-density dislocations containing both the basal and non-basal types can be formed during rolling. In view of the strong texture with a component of {0002} plane parallel to RD–TD plane and formed during the rolling, recovery instead of recrystallization is dominant at a rolling temperature of 270 °C, which facilitates the formation of the nano substructure due to the low migration rate of boundaries under the relatively low temperature. Accordingly, warm rolling using a single pass causes the formation of the nano substructures and the high-density dislocations, which is different from the common high-density dislocations and/or twins created by cold rolling or the recrystallized microstructure generated by hot rolling. For the E + R+A sample (Figure (c)), the texture is not weakened due to lack of static recrystallization, suggesting recovery accompanied with the rearrangement of the high-density dislocations readily occurs during aging at 200 °C. Under the driving force of thermal energy, dislocation reaction and rearrangement transform high-density dislocations into LAGBs for lowering the excess free energy (Figure (b)) [Citation29], which causes the formation of more nano substructures with the decrease of dislocation density and the increase of LAGBs. The stronger texture in E + R+A sample is formed during aging, which is closely related to a lower dislocation density, formation and migration of LAGBs. Further investigation on the texture evolution mechanism during aging is highly desired.
Compared with the high-density dislocations, the LAGBs can act as nucleation sites of new dislocation sources, and dislocations can successfully propagate from the LAGBs to contribute the plastic deformation during tensile test [Citation30]. Moreover, segregation of Gd atoms on the dislocations can decrease the local elastic distortion in the matrix caused by the high-density dislocations and the substitutional solid solution of Gd atoms, which improves the ductility of the E + R+A sample. As a result, a high ductility in the E + R+A sample is closely related to the formation of more LAGBs due to dislocation recovery, while a low ductility obtained in the E + R sample is mainly attributed to the high-density dislocations within the matrix.
More importantly, the yield strength has a significant increase after aging, compared with the E + R sample. For the fine-grained and age-hardening Mg–Gd based alloys, a high-volume fraction of dynamical precipitates with a submicron level size can be commonly formed during the extrusion process, which exhibits a weak age-hardening response due to a low-volume fraction of the prismatic β'-Mg7Gd precipitates within grains [Citation17,Citation31,Citation32]. In this research, Gd atoms segregate on the boundaries of nano substructure and numerous dynamical precipitates are formed during rolling (Figure (d,e)). Hence, the concentration of Gd segregation on dislocation lines is so low that the new phase of prismatic β'-Mg7Gd precipitates cannot be formed due to the lack of enough Gd atoms in matrix during aging. It is reported that Gd tends to segregate to form the Gd-rich clusters along the incoherent tilt grain boundaries for the reduction in free energy in the Mg–0.2Gd (at. %) alloy [Citation33]. In the present study, the high-density dislocations are contained in the fine-grained Mg–15Gd alloy, and the Gd atoms can further segregate on dislocations within grains due to the low energy barrier for solute diffusion during aging, as proven by the HAADF results in Figure (e,f). Therefore, the high-density clusters with several nanometers in the interior of α-Mg grains are mainly formed along the dislocation lines in the E + R+A sample (Figure (f,g)). It should be noted that sufficient solute clusters must provide a dragging effect on the dislocation motion, which play a crucial role in enhancing the strength (Figure (a)). Differently, there is no clusters in the complete DRXed microstructure of the Mg–Gd binary alloy because of a limited number of dislocations for Gd segregation, thus the alloy shows little age-hardening response [Citation17,Citation31,Citation32]. In addition, more LAGBs with Gd segregation in the E + R+A sample are capable of hindering the motion of dislocations and exert a positive effect on strengthening. Actually, the contribution of solid solution strengthening is reduced due to the segregation and the clusters of Gd atoms. The density of dislocations decreases due to occurrence of recovery during aging, and the corresponding dislocation hardening is expected to decrease. Obviously, the decrease in strength caused by potential softening mechanisms can be compensated through strengthening mechanisms caused by the segregation on LAGBs and the clusters in matrix of Gd atoms. It is thus concluded that a high yield strength of 504 MPa in the E + R+A sample is attributed to the nano substructure with boundary segregation of Gd atoms, the high-density nano clusters caused by dislocations, the high-density submicron dynamical precipitates, and the strong basal texture.
5. Conclusions
A high-strength binary Mg–15Gd alloy plate is successfully fabricated by the conventional extrusion, warm-rolling and aging. The alloy exhibits an excellent mechanical property with a yield strength of 504 MPa, ultimate tensile strength of 518 MPa, and elongation of 4.5%. The high-density dynamical precipitate uniformly distributed in binary Mg–15Gd alloy is formed mainly during extrusion, which facilitates the formation of high-density dislocations and LAGBs during warm-rolling. Subsequently, the nano substructure with boundary segregation of Gd atoms and the high-density nano clusters within grains are caused by the high-density dislocations during aging. The remarkably high strength in binary Mg–15Gd alloy plate is attributed to the nano substructure with boundary segregation of Gd atoms, the high-density nano clusters caused by dislocations, the high-density dynamical precipitates with submicron size of ∼150 nm, and the strong basal texture.
Supplemental Material
Download MS Word (395.4 KB)Acknowledgements
The authors are grateful for the facilities and technical supports provided by Shenyang University of Chemical Technology and Northeastern University.
Disclosure statement
No potential conflict of interest was reported by the author(s).
Additional information
Funding
References
- Inoue A, Kawamura Y, Matsushita M K, et al. Novel hexagonal structure and ultrahigh strength of magnesium solid solution in the Mg-Zn-Y system. J Mater. Res. 2001;16:1894–1900.
- Jian WW, Cheng GM, Xu WZ, et al. Ultrastrong Mg alloy via nano-spaced stacking faults. Mater. Res. Lett. 2013;1:61–66.
- Homma T, Kunito N, Kamado S. Fabrication of extraordinary high-strength magnesium alloy by hot extrusion. Scripta Mater. 2009;61:644–647.
- Li RG, Li HR, Pan HC, et al. Achieving exceptionally high strength in binary Mg-13Gd alloy by strong texture and substantial precipitates. Scripta Mater. 2021;193:142–146.
- Wan YC, Tang B, Gao YH, et al. Bulk nanocrystalline high-strength magnesium alloys prepared via rotary swaging. Acta Mater. 2020;200:274–286.
- Li RG, Nie JF, Huang GJ, et al. Development of high strength magnesium alloys via combined processes of extrusion, rolling and ageing. Scripta Mater. 2011;64:950–953.
- Zhang Y, Rong W, Wu YJ, et al. Achieving ultra-high strength in Mg-Gd-Ag-Zr wrought alloy via bimodal-grained structure and enhanced precipitation. J. Mater. Sci. Technol. 2020;54:160–170.
- Panigrahi SK, Mishra RS, Brennan RC, et al. Achieving extraordinary structural efficiency in a wrought magnesium rare earth alloy. Mater. Res. Lett. 2020;8:151–157.
- Zheng RX, Du JP, Gao S, et al. Transition of dominant deformation mode in bulk polycrystalline pure Mg by ultra-grain refinement down to sub-micrometer. Acta Mater. 2020;198:35–46.
- Kim YM, Mendis C, Sasaki T, et al. Static recrystallization behaviour of cold rolled Mg-Zn-Y alloy and role of solute segregation in microstructure evolution. Scripta Mater. 2017;136:41–45.
- Yamada K, Hoshikawa H, Maki S, et al. Enhanced age-hardening and formation of plate precipitates in Mg-Gd-Ag alloys. Scripta Mater. 2009;61:636–639.
- Sun HQ, Shi YN, Zhang MX, et al. Plastic strain-induced grain refinement in the nanometer scale in a Mg alloy. Acta Mater. 2007;55:975–982.
- Kim WJ, Jeong HG, Jeong HT. Achieving high strength and high ductility in magnesium alloys using severe plastic deformation combined with low-temperature aging. Scripta Mater. 2009;61:1040–1043.
- Liu BY, Liu F, Yang N, et al. Large plasticity in magnesium mediated by pyramidal dislocations. Science. 2019;365:73–75.
- Wu ZX, Curtin WA. The origins of high hardening and low ductility in magnesium. Nature. 2015;526:62–67.
- Li RG, Dai YQ, Song PF, et al. Simultaneous enhancement of strength and ductility by aging treatment in fine-grained Mg-13Gd alloy. Mater Sci Eng A. 2021;818:141441.
- Li RG, Xin RL, Liu Q, et al. Effect of Ag addition on microstructure and mechanical properties of Mg-14Gd-0.5Zr alloy. Mater. Charact. 2015;109:43–49.
- Hong M, Shah SSA, Wu D, et al. Ultra-high strength Mg-9Gd-4Y-0.5Zr alloy with bi-modal structure processed by traditional extrusion. Met. Mater. Int. 2016;22:1091–1097.
- Wang R, Dong J, Fan LK, et al. Microstructure and mechanical properties of rolled Mg-12Gd-3Y-0.4Zr alloy sheets. Trans. Nonferrous Met. Soc. China. 2008;18:s189–s193.
- Li X, Qi W, Zheng K, et al. Enhanced strength and ductility of Mg-Gd-Y-Zr alloys by secondary extrusion. J. Magnes Alloy. 2013;1:54–63.
- Li X, Liu C, Al-Samman T. Microstructure and mechanical properties of Mg-12Gd-3Y-0.6Zr alloy upon conventional and hydrostatic extrusion. Mater. Lett. 2011;65:1726–1729.
- Yu ZJ, Xu C, Meng J, et al. Effects of extrusion ratio and temperature on the mechanical properties and microstructure of as-extruded Mg-Gd-Y-(Nd/Zn)-Zr alloys. Mater Sci Eng A. 2019;762:138080.
- Wang YF, Zhang F, Wang YT, et al. Effect of Zn content on the microstructure and mechanical properties of Mg-Gd-Y-Zr alloys. Mater Sci Eng A. 2019;745:149–158.
- Liu SS, Liu H, Chen X, et al. Effect of texture on deformation behavior of heterogeneous Mg-13Gd alloy with strength–ductility synergy. J. Mater. Sci. Technol. 2022;113:271–286.
- Zhang JY, Peng P, Luo AA, et al. Dynamic precipitation and enhanced mechanical properties of ZK60 magnesium alloy achieved by low temperature extrusion. Mater Sci Eng A. 2022;829:142143.
- Barnett MR. A rationale for the strong dependence of mechanical twinning on grain size. Scripta Mater. 2008;59:696–698.
- Zhang BP, Geng L, Huang LJ, et al. Enhanced mechanical properties in fine-grained Mg-1.0Zn-0.5Ca alloys prepared by extrusion at different temperatures. Scripta Mater. 2010;63:1024–1027.
- Zhang D, Wen H, Arul Kumar M, et al. Yield symmetry and reduced strength differential in Mg-2.5Y alloy. Acta Mater. 2016;120:75–85.
- Xiao LR, Chen XF, Cao Y, et al. Solute segregation assisted nanocrystallization of a cold-rolled Mg-Ag alloy during annealing. Scripta Mater. 2020;177:69–73.
- Chen SJ, Yu Q. The role of low angle grain boundary in deformation of titanium and its size effect. Scripta Mater. 2019;163:148–151.
- Li RG, Zhao DY, Zhang JH, et al. Room temperature yielding phenomenon at extruded or/and aged Mg-14Gd-2Ag-0.5Zr alloy with fine-grained microstructure. Mater Sci Eng A. 2020;787:139551.
- Li RG, Shafqat HB, Zhang JH, et al. Cold-working mediated converse age hardening responses in extruded Mg-14Gd-2Ag-0.5Zr alloy with different microstructure. Mater Sci Eng A. 2019;748:95–99.
- Liu ZQ, Qian Q, Jiang Y. Incoherent tilt grain boundaries stabilized by stacking faults and solute-cluster segregation: a case-study of an Mg-Gd alloy. Mater. Res. Lett. 2020;8:268–274.