ABSTRACT
The 5 at% Cr3C2 particles were mixed with AlCoCrFeNi high entropy alloy powder particles and then selectively laser melted. The addition caused full columnar-to-equiaxed grain transition (CET) and significant grain refinement. The inter-dendritic regions and grain boundaries (GBs) of the as-fabricated sample were segregated with Cr and C, which led to the formation of an FCC belt/network structure along GBs. The grain interior was dominated by BCC/B2 and sporadically decorated by Cr7C3 particles. The partitioning of Cr and C into liquid ahead of the solidification front, which may have generated significant constitutional supercooling, is believed to be responsible for the full CET.
GRAPHICAL ABSTRACT
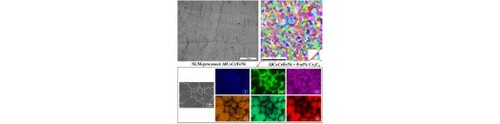
IMPACT STATEMENT
The present study introduces a small fraction of Cr3C2 particles into AlCoCrFeNi high entropy alloy and successfully enables full columnar-to-equiaxed grain transition and significant grain refinement during selective laser melting.
1. Introduction
Selective laser melting (SLM) is well known for its outstanding near-net-shape manufacturing capability that offers great design flexibility and enables a high level of product customization. On the other hand, it is also known for its unique processing characteristics such as high thermal gradients in melt pools, high cooling rates and complex thermal cycling [Citation1–3]. The steep thermal gradients within melt pools usually result in epitaxial grain growth and thus in the formation of coarse columnar grains and strong texture that can cause mechanical property anisotropy [Citation4–9]. The inhomogeneous thermal distribution and high cooling rates within a build during SLM usually cause the development of high internal stresses, which, together with a large columnar grain structure, can lead to hot tearing in some kinds of metallic materials [Citation7–15]. It is very common in a number of high-strength nickel-based superalloys [Citation7,Citation8], aluminum alloys [Citation9–11], and titanium aluminides [Citation12,Citation13]. It has also been observed in SLM-processed high-strength high entropy alloys (HEAs), such as AlCoCrFeNi [Citation14–18], which are usually considered promising for structural or engineering applications [Citation14–18]. Owing to the hot tearing issue, the near-net-shape manufacturing potential of SLM cannot be fully exploited to expand the application of high-strength HEAs.
One effective strategy to deal with hot tearing is to promote columnar-to-equiaxed transition (CET) and grain refinement during SLM. So far, the most common approach to promote CET during SLM is to introduce potent nucleants to promote the formation of new equiaxed crystals. This route has been proven to be particularly effective for SLM-processed aluminum and its alloys. Al3X-forming elements, such as Zr, Sc, Ti, Ni, and Nb, were usually added to aluminum or its alloys prior to SLM processing. Potent heterogeneous nucleants, Al3X (i.e. X = Zr, Sc, Ti, and Ni), which constitute low mismatch with the matrix, were then formed during SLM and significantly promoted the CET and grain refinement [Citation9,Citation19–22]. Concurrent with this effect is the full suppression of hot tearing during SLM of aluminum alloys. Many other metallic materials, such as nickel-base superalloys and HEAs, however, are less lucky with this approach due to the lack of suitable and potent inoculants.
Recently, the addition of carbon into high or medium entropy alloys, such as AlCoCrFeNi, CrFeCoNi, and CrCoNi, through the conventional melting and casting method was found to have promoted grain refinement by enhancing constitutional supercooling in the liquid ahead of the solidification fronts [Citation23–25]. For example, the addition of C in AlCoCrFeNi through casting led to the segregation and accumulation of C along grain boundaries during solidification, which is not only good for the development of large constitutional supercooling and thus grain nucleation but also helpful in inhibiting grain growth [Citation24]. Li et al. [Citation26] found that the addition of WC particles into CoCrFeMnNi HEA through direct laser deposition (DLD) led to remarkable grain refinement by forming carbide particles during solidification that may have acted as effective heterogeneous nucleation sites. However, it is noted that there is a lack of reports on the influence of the addition of C or carbides on the microstructural evolution of HEAs during SLM. It is well established that as compared with conventional casting and DLD, SLM usually demonstrates much higher cooling rates (104–106°C/s) and higher thermal gradients within melt pools. With such extreme processing characteristics, whether the addition of carbon or carbides can either enhance constitutional supercooling ahead of the solid/liquid front or lead to the formation of potent carbide nucleants during solidification so that both CET and grain refinement of HEAs can be achieved remains unknown. So does the effectiveness of the addition in improving the SLM processibility of AlCoCrFeNi. Thus, in this study, we add a small amount of Cr3C2 into AlCoCrFeNi through powder mixing and SLM to investigate the role of the addition in the microstructural evolution and solidification behavior of the alloy. The influence of the addition on the SLM processibility of the alloy and mechanical properties will also be examined.
2. Materials and methods
Argon atomized equimolar AlCoCrFeNi HEA powder with a particle size range of 15–53 µm and Cr3C2 powder a particle size range of 2–3 µm were used in the present study. According to a previous study [Citation24], the addition of 2 at% C into AlCoCrFeNi HEA through the conventional casting method can result in significant grain refinement and improvement in yield strength and compressive strength of the HEA. Thus, in this study, 5 at% Cr3C2 powder particles, equal to addition of 2 at% C, were mixed with the HEA powder particles (referred to as HEA-Cr3C2 hereinafter) in an argon atmosphere using a horizontal ball mill (Figure (a)) [Citation27]. A ball-to-powder weight ratio of 4:1 and balls with a diameter of 5 mm were used for the powder mixing. The milling process took 20 min with a shaft rotation speed of 600 rpm. Both the pure HEA powder and the HEA-Cr3C2 powder mixture were then processed using a Renishaw AM 400 system. Samples with a dimension of 10 × 10 × 5 mm3 were built under a modulated pulsed laser mode in an argon atmosphere for microstructural characterization. A laser power of 400 W, a point exposure duration of 90 µs, and a powder layer thickness of 50 µm, which led to a very low porosity level (<0.1%), were selected to process the powder materials. The point distance and hatch distance were set to be 60 and 90 µm, respectively. The as-fabricated samples were longitudinally sectioned by electrical discharge machining (EDM) and then ground using SiC papers from 320 grit up to 4000 grit before being polished using 3 µm diamond suspension and colloidal silica suspension (or OPS solution). Some of the as-polished samples were analyzed using the electron backscattered diffraction technique (EBSD) with a step size of 500 nm. The samples were then etched and examined using optical microscopy (OM) and scanning electron microscopy (SEM). A Leica DM4000 OM machine and a Zeiss SUPRA55 SEM machine, and an FEI Quanta 450 SEM machine, which was equipped with an EBSD detector, were used for the microstructural characterization. Transmission electron microscopy (TEM), high-resolution TEM (HRTEM), and energy dispersive X-ray spectroscopy (EDS) studies were also performed on some of the as-fabricated samples. Disc specimens of 3 mm in diameter were machined out of the samples and ground into a thickness of 50–100 µm and then electro-polished or ion beam milled to perforation using a Gatan 691-type ion beam thinner. The TEM and HRTEMstudies were conducted using an FEI TecnaiG20 FEG TEM microscope fitted with an Oxford EDS detector. The Vickers hardness tests were conducted in a Future-Tech FM-800 microhardness testing system using a load of 300 gf and a dwell time of 20 s.
Figure 1. (a) Schematic illustration of the horizontal ball mill used in the current study; SEM micrographs showing particle distribution and morphology of (b) the as-received HEA powder and (c) the HEA-Cr3C2 powder mixture, (d) particle surface structure of the HEA-Cr3C2 powder mixture; (e and f) EDS mapping result of the surface of a HEA particle assembled by fine Cr3C2 powder particles shown in (d).
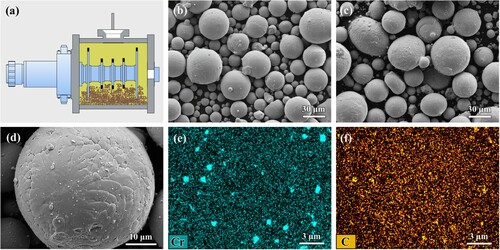
3. Results and discussion
Figure (b,c) shows the particle distribution and morphologies of the as-received HEA powder and the HEA-Cr3C2 powder mixture, respectively. It is obvious that the as-received HEA powder shows a homogeneous particle size distribution and these particles are generally spherical or near-spherical, which are good for powder spreading during SLM. After short-duration mixing with the 5 at% fine Cr3C2 particles using the horizontal ball mill, the majority of the HEA particles remain spherical or near-spherical as shown in Figure (c,d). The ultrafine Cr3C2 particles have been uniformly assembled onto the HEA powder particle surfaces, as shown in Figure (d–f), which would be undoubtedly beneficial for the development of good chemical and microstructural homogeneity during the subsequent SLM processing. In addition to EDS mapping analysis, some of the ultrafine particles adhered to the large powder particle surfaces were also subjected to point EDS analysis and the results are included in Table S1. It is shown that the ultrafine particles are mainly enriched in Cr and C, further confirming that they are indeed Cr3C2 particles. In contrast, the large particles mainly contain Al, Co, Cr, Fe, and Ni elements and show a near equiatomic proportion, indicating that they are the AlCoCrFeNi HEA powder particles.
Figure shows the grain structures along the longitudinal sections of the as-built HEA and HEA-Cr3C2 samples. It is obvious that the HEA sample is dominated by large columnar grains, as shown in Figure (a,b). This is the typical microstructure of SLM-processed AlCoCrFeNi, which is the result of steep thermal gradients and rapid cooling rates of melt pools during solidification and is consistent with previous reports [Citation16,Citation28]. Meanwhile, with the formation of large columnar grains and potentially high internal stress, many cracks were observed to be along many columnar grain boundaries (Figure S1(a,b)). With the addition of Cr3C2, the large columnar grains disappeared, and ultra-fine equiaxed grains formed (Figure (c,d)). The sizes of the equiaxed grains in the HEA-Cr3C2 sample are generally several microns, which are two orders of magnitude smaller than those in the Cr3C2-free HEA sample. The results indicate that both CET and grain refinement have been completely activated during SLM with the addition of Cr3C2. With the significant grain refinement, the grain boundary cracks associated with large columnar grains have been completely suppressed. However, due to stress buildup at the root of the build during SLM, cracks still formed from the bottom and propagated upwards (Figure S1(c)). The upper regions are completely free from cracks (Figure S1(d)), thanks to the grain refinement. In the intact areas, the interlayer boundary regions tend to contain relatively larger equiaxed and polygonal grains as compared with the interior of solidified melt pools, which is generally dominated by finer dendritic grains (Figure (c,d)). This can be associated with thermal cycling and reheating on the previous solidified layers. The surface and subsurface regions of the previous solidified layer may have experienced relatively high-temperature remelting or reheating during the subsequent powder layer processing, which promoted coarsening and coalescing of fine grains in the interlayer interfacial regions.
Figure 2. OM micrographs showing grain structures in the SLM-processed (a and b) HEA and (c and d) HEA-Cr3C2 samples. The arrows in (c) and (d) refer to interlayer boundary regions where relatively larger equiaxed grains dominate, in contrast to the finer grains present within the interior of solidified melt pools.
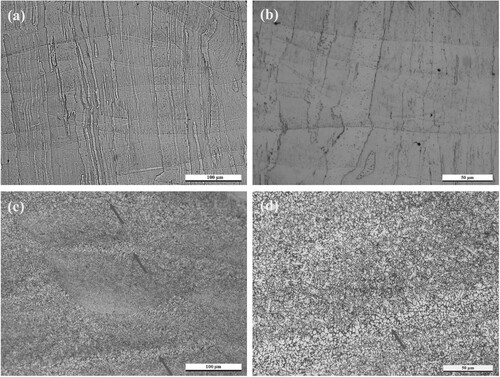
Figure shows the microstructural details in the HEA-Cr3C2 sample. Again, it is shown that the central region of a solidified melt pool is dominated by a fine dendrite structure (Figure (c,e)), while the interlayer boundary region mainly consists of relatively larger near-spherical or polygonal equiaxed grains (Figure (d)). Both the grain boundary (GB) regions and inter-dendritic regions were found to contain belt or stripe structures (Figure (c–e)), leading to the development of a network structure along the GBs. According to EDS mapping results, as shown in Figure (f), these GB or inter-dendritic belt structures tend to be segregated with Cr and C. Point TEM-EDS analysis results in Table further confirm that the belt structures are enriched in Cr and C but depleted in Al. The segregation of Cr and C along inter-dendritic regions and GBs indicate that these elements have been expelled into the liquid ahead of the solidification front during solidification. This is in agreement with the HEA-C phase diagram, which shows that the solute of C has a partition coefficient of k < 1 [Citation23], which means that C would be rejected ahead of the solid–liquid interface during solidification. It is analogous to the segregation of Hf, Ti, Ta, and W at cell walls in SLM-processed CM247LC and the segregation of Cr and Mo at cell walls and GBs in SLM-processed 316L stainless steel as reported in Refs. [Citation29–32]. The partitioning of Cr and C to the liquid, in turn, would generate constitutional supercooling in the liquid ahead of the solidification front and thus promote the nucleation of new equiaxed crystals. This should be the main reason for the acquisition of full CET in the present study. The enrichment of solutes in a diffusion layer ahead of the advancing solid/liquid interface is also believed to restrict grain growth since the solutes diffuse slowly [Citation23]. The mechanism of achieving full CET and grain refinement in the present study is obviously different from the nucleant-induced heterogeneous nucleation mechanism that has been widely observed and applied in many previous studies, especially those on SLM-processed aluminum alloys [Citation19–22]. As such, the current study provides a new strategy to promote CET and grain refinement during metallic SLM, i.e. promoting micro-segregation by adding particles or elements that are liable to partition to the liquid during solidification.
Figure 3. (a–e) SEM micrographs showing the microstructure in the SLM-processed HEA-Cr3C2 sample; (f) SEM micrograph and EDS mapping results on an interlayer boundary region of the SLM-processed HEA-Cr3C2 sample. Regions b and c in (a) correspond to the magnified micrographs of (b) an interlayer boundary region and (c) a region within a solidified melt pool, respectively. Regions d and e correspond to the magnified micrographs of (d) and (e).
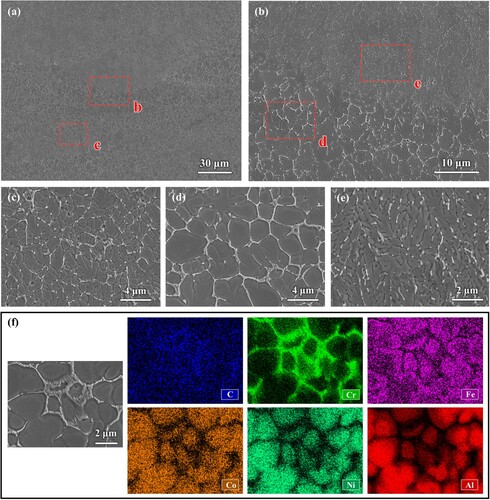
Table 1. Point TEM-EDS analysis results on a GB belt structure, a grain interior/matrix area, and a carbide particle in the SLM-processed HEA-Cr3C2 sample (in at%).
Figure (a) shows the EBSD inverse pole figure (IPF) color map of the grain structure in the HEA-Cr3C2 sample. It is clear that the sample consists of both fine equiaxed grain regions and relatively larger grain regions, which is consistent with the above OM and SEM observations. The grains tend to be highly randomly oriented and thus the texture tends to be really weak. This is also confirmed by the very low maximum multiples of the uniform distribution (MUD) values in the pole figure shown in Figure (b). Quantitative analysis based on the EBSD data shows that the grain sizes in the HEA-Cr3C2 sample are between 0.5 µm and 10 µm in diameter with the majority of them falling between 2 µm and 5 µm; see Figure (c). Moreover, there is a significantly high fraction of high angle grain boundaries (HAGBs) in the sample. According to Figure (d), more than 95% GBs are HAGBs (grain boundary angles ≥15°), which obviously accounts for the low texture level in the current sample, thanks to the development of equiaxed grain structure. Quantitative analysis of the grain aspect ratio and grain shape circularity was also conducted; Figure (e,f). It is shown that grains with aspect ratio values larger than 0.3, which can be regarded as equiaxed grains, account for >96.4% of all grains. According to Hunt [Citation33], when the volume fraction of equiaxed crystals exceeds a critical value of 49%, the columnar growth will be prohibited and a fully equiaxed grain microstructure will be achieved. This is definitely the case for the current study.
Figure 4. (a) EBSD IPF color map showing the grain structure and (b) pole figures showing the texture, (c) grain size distribution, (d) grain boundary misorientation distribution, (e) grain aspect ratio distribution, and (f) statistics of the grain shape circularity in the SLM-processed HEA-Cr3C2 sample. RD is the sample building direction.
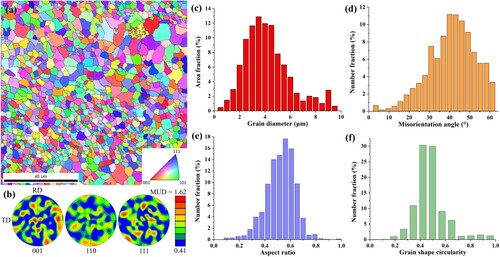
To identify the phase structure in the as-fabricated HEA-Cr3C2 sample, TEM has been employed to investigate the material. The results are shown in Figure . Selected area diffraction patterns (SAED) and dark-field (DF) images taken from a (100) superlattice spot from grain interior show that the grain interior or matrix area contains both disordered BCC and ordered B2 phase, which should be the result of spinodal decomposition that may have occurred during solidification after SLM. Similar BCC + B2 microstructure has been observed in other Al-rich HEAs during solidification [Citation34,Citation35]. The GB belt structure is identified to be the FCC phase. HRTEM images and Fast Fourier Transformation (FFT) pattern on the matrix area and the GB belt structure further confirm that the matrix is BCC/B2 phase while the GB belt structure is the FCC phase; see Figure (h–l). Measurement on the HRTEM image of the matrix gives rise to an interplanar spacing of 2.04 Å in two orientations, which correspond to (011) and (110) crystal planes of the BCC/B2 phase. The GB belt structure, however, possesses interplanar spacing of 1.84 and 2.08 Å in two directions, which correspond to the (111) and (002) crystal planes of the FCC phase, respectively. The formation of the FCC phase along GBs should be the result of segregation of C and Cr, which caused depletion of Al in these regions (Table ) and promoted BCC/B2 → FCC transformation at GBs during solidification. Moreover, according to Qin et al. [Citation24], the addition of C to a HEA can increase electronegativity and thus the interatomic forces of the alloy, which would promote the formation of the FCC phase. Here in the present study, the significant enrichment of C at GBs would definitely elevate the electronegativity and interatomic forces in these regions, which favors the BCC/B2 → FCC transformation. The presence of FCC belt/network structure along inter-dendritic regions and GBs would help impede grains from abnormal coarsening and coalescing during subsequent SLM processing or thermal cycling.
Figure 5. (a–c) Bright-field (BF) TEM micrographs showing fine grains, intergranular stripes, and particles inside grains of the HEA-Cr3C2 sample; The inset in (a) showing the DF TEM micrograph of the BCC/B2 matrix; Selected area diffraction patterns of (d) the BCC/B2 matrix, (e) the FCC phase and (f) Cr7C3 carbide indicated by the red circles shown in (a), (b) and (c), respectively; (g) BF TEM micrograph and (h) HRTEM image of the interface between the matrix and an intergranular belt structure; HRTEM micrographs and FFT patterns of (i and j) the B2 matrix and (k and l) an FCC belt structure indicated by the two square frames in (h), respectively.

Within some grain interiors, some precipitates that are enriched in Cr and C (Table ) can be observed occasionally (Figure (c)). These particles are identified to be Cr7C3 carbides based on the SAED obtained from them (Figure (f)). However, since the population of Cr7C3 carbides in the sample is highly limited, it is unlikely that the CET and grain refinement are the results of heterogeneous nucleation on the Cr7C3 carbides. Also, given that the melting point of Cr3C2 (1895°C) is higher than that of Cr7C3 particles (1766°C) and that no Cr3C2 was observed in the as-fabricated samples, it is reasonable to believe that the Cr3C2 particles have been fully melted during SLM and that the Cr7C3 carbides should have formed from the liquid during solidification. It is also noted that Cr23C6 (with a melting point of 1576°C) is usually formed in as-cast C-containing HEAs [Citation24], while Cr7C3 possesses higher stability at high temperatures [Citation25]. Thus, the presence of Cr7C3 instead of Cr23C6 in the current as-fabricated sample should be the result of extremely high cooling rates after SLM, which may have suppressed the transformation of Cr7C3 into Cr23C6.
Table shows the microhardness of the SLM-processed HEA and HEA-Cr3C2 samples. The former shows a microhardness around 560 HV. With the addition of Cr3C2, the microhardness has been remarkably improved. Thus, those regions containing fine dendritic grains show a microhardness of 590 HV, while the inter-layer regions with relatively larger equiaxed grains show a microhardness of 612 HV. The improvement in microhardness with the addition of Cr3C2 could be attributed to the refined grain structure and the solid solution of interstitial C in the matrix (Table ). That those regions containing larger equiaxed grains in the SLM-processed HEA-Cr3C2 sample show higher microhardness than the regions consisting of finer dendritic grains could be because the latter contain not only FCC along GBs but also FCC along inter-dendritic regions, which should have softened the regions.
Table 2. Microhardness of the SLM-processed HEA and HEA-Cr3C2 samples.
4. Conclusions
The addition of 5 at% Cr3C2 into AlCoCrFeNi alloy through SLM has led to full CET and significant grain refinement, which resulted in improvement in microhardness. The partitioning of Cr and C to the liquid ahead of the solidification front, which may have generated significant constitutional supercooling in the liquid, should have been responsible for the full CET. The segregation of Cr and C at GBs also led to a bimodal microstructure in the as-fabricated sample, i.e. the development of BCC/B2 grain interior and GB FCC belt structure/network. The present work indicates that by selecting a proper type of additive powder could a full CET be achieved in an AM-processed alloy.
Supplemental Material
Download MS Word (956.6 KB)Disclosure statement
No potential conflict of interest was reported by the author(s).
Data availability statement
The data that support the findings of this study are available from the corresponding author upon request.
Additional information
Funding
References
- Bermingham MJ, StJohn DH, Krynen J, et al. Promoting the columnar to equiaxed transition and grain refinement of titanium alloys during additive manufacturing. Acta Mater. 2019;168:261–274.
- Yuan PP, Gu DD. Molten pool behaviour and its physical mechanism during selective laser melting of TiC/AlSi10Mg nanocomposites: simulation and experiments. J Phys D: Appl Phys. 2015;48:035303.
- Marshall GJ, Young II WJ, Thompson SM, et al. Understanding the microstructure formation of Ti-6Al-4V during direct laser deposition via in-situ thermal monitoring. JOM. 2016;68:778–790.
- Qiu CL, Adkins NJE, Attallah MM. Microstructure and tensile properties of selectively laser-melted and of HIPed laser-melted Ti–6Al–4V. Mater Sci Eng A. 2013;578:230–239.
- Simonelli M, Tse YY, Tuck C. On the texture formation of selective laser melted Ti-6Al-4V. Metall Mater Trans A. 2014;45:2863–2872.
- Qiu CL, Liu Q. Multi-scale microstructural development and mechanical properties of a selectively laser melted beta titanium alloy. Addit Manuf. 2019;30:100893.
- Chauvet E, Kontis P, Jagle EA, et al. Hot cracking mechanism affecting a non-weldable Ni-based superalloy produced by selective electron beam melting. Acta Mater. 2018;142:82–94.
- Qiu CL, Chen HX, Liu Q, et al. On the solidification behaviour and cracking origin of a nickel-based superalloy during selective laser melting. Mater Charact. 2019;148:330–344.
- Martin JH, Yahata BD, Hundley JM, et al. 3D printing of high-strength aluminium alloys. Nature. 2017;549:365–369.
- Mehta A, Zhou L, Huynh T, et al. Additive manufacturing and mechanical properties of the dense and crack free Zr-modified aluminum alloy 6061 fabricated by the laser-powder bed fusion. Addit Manuf. 2021;41:101966.
- Opprecht M, Garandet J, Roux G, et al. A solution to the hot cracking problem for aluminium alloys manufactured by laser beam melting. Acta Mater. 2020;197:40–53.
- Tang HP, Yang GY, Jia WP, et al. Additive manufacturing of a high niobium-containing titanium aluminide alloy by selective electron beam melting. Mater Sci Eng A. 2015;636:103–107.
- Liu WP, Dupont JN. In-situ reactive processing of nickel aluminides by laser-engineered net shaping. Metall Mater Trans A. 2003;34A:2633–2641.
- Sun Z, Tan XP, Descoins M, et al. Revealing hot tearing mechanism for an additively manufactured high-entropy alloy via selective laser melting. Scripta Mater. 2019;168:129–133.
- Luo SC, Zhao CY, Su Y, et al. Selective laser melting of dual phase AlCrCuFeNix high entropy alloys: formability, heterogeneous microstructures and deformation mechanisms. Addit Manuf. 2020;31:100925.
- Niu PD, Li RD, Yuan TC, et al. Microstructures and properties of an equimolar AlCoCrFeNi high entropy alloy printed by selective laser melting. Intermetallics. 2019;104:24–32.
- Sun ZJ, Tan XP, Wang CC, et al. Reducing hot tearing by grain boundary segregation engineering in additive manufacturing: example of an AlxCoCrFeNi high-entropy alloy. Acta Mater. 2021;204:116505.
- Karlsson D, Marshal A, Johansson F, et al. Elemental segregation in an AlCoCrFeNi high-entropy alloy - a comparison between selective laser melting and induction melting. J Alloys Compd. 2019;784:195–203.
- Zhou L, Pan H, Hyer H, et al. Microstructure and tensile property of a novel AlZnMgScZr alloy additively manufactured by gas atomization and laser powder bed fusion. Scripta Mater. 2019;158:24–28.
- Zhang JL, Gao JB, Song B, et al. A novel crack-free Ti-modified Al-Cu-Mg alloy designed for selective laser melting. Addit Manuf. 2021;38:101829.
- Deng JW, Chen C, Liu XC, et al. A high-strength heat-resistant Al-5.7Ni eutectic alloy with spherical Al3Ni nano-particles by selective laser melting. Scripta Mater. 2021;203:114034.
- Martin JH, Yahata B, Mayer J, et al. Grain refinement mechanisms in additively manufactured nano-functionalized aluminum. Acta Mater. 2020;200:1022–1037.
- Liu XW, Liu L, Liu G, et al. The role of carbon in grain refinement of cast CrFeCoNi high-entropy alloys. Metall Mater Trans A. 2018;49:2151–2160.
- Qin G, Xue WT, Chen RR, et al. Grain refinement and FCC phase formation in AlCoCrFeNi high entropy alloys by the addition of carbon. Materialia. 2019;6:100259.
- Liu XW, Laplanche G, Kostka A, et al. Columnar to equiaxed transition and grain refinement of cast CrCoNi medium-entropy alloy by microalloying with titanium and carbon. J Alloys Compd. 2019;775:1068–1076.
- Li JF, Xiang S, Luan HW, et al. Additive manufacturing of high-strength CrMnFeCoNi high-entropy alloys-based composites with WC addition. J Mater Sci Tech. 2019;35:2430–2434.
- Wang ZC, Wang XT, Chen X, et al. Complete columnar-to-equiaxed transition and significant grain refinement in an aluminium alloy by adding Nb particles through laser powderbed fusion. Addit Manuf. 2022;51:102615.
- Jiang Q, Zhang PL, Yu ZS, et al. Alcocrfeni high entropy alloy fabricated via selective laser melting reinforced by Fe-based metallic glass. Mater Lett. 2022;307:130994.
- Wang XQ, Carter LN, Pang B, et al. Microstructure and yield strength of SLM-fabricated CM247LC Ni-superalloy. Acta Mater. 2017;128:87–95.
- Wang YM, Voisin T, Mckeown JT, et al. Additively manufactured hierarchical stainless steels with high strength and ductility. Nature Mater. 2018;17:63–71.
- Gorsse S, Hutchinson C, Gouné M, et al. Additive manufacturing of metals: a brief review of the characteristic microstructures and properties of steels. Sci Tech Adv Mater. 2017;18:584–610.
- Liu Q, Wang GQ, Qiu CL. On the role of dynamic grain movement in deformation and mechanical anisotropy development in a selectively laser melted stainless steel. Addit Manuf. 2020;35:101329.
- Hunt JD. Steady-state columnar and equiaxed growth of dendrites and eutectic. Mater Sci Eng. 1984;65:75–83.
- Guo S, Ng C, Liu CT. Sunflower-like solidification microstructure in a near-eutectic high-entropy alloy. Mater Res Lett. 2013;1(4):228–232.
- Gou SY, Li SC, Hu HL. Surface hardening of CrCoFeNi high-entropy alloys via Al laser alloying. Mater Res Lett. 2021;9(10):437–444.