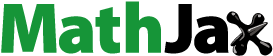
Abstract
Swaged Mo-xLa2O3 alloys (x = 0, 0.3, and 0.6 wt.%) were subjected to different annealing temperatures (Ta), in order to demonstrate the Ta-sensitive La2O3 effect on microstructural evolution and tensile ductility. Although coarse La2O3 particles were detrimental to ductility, nanosized La2O3 particles were found to increase the ductility by highly stabilizing the deformation-induced hierarchical microstructures of lamellar elongated grains with low-angle grain boundaries inside. A competition between the two opposite effects derived from the La2O3 addition led to an unexpected x-dependence of ductility upon different Ta.
GRAPHICAL ABSTRACT

IMPACT STATEMENT
Hierarchical microstructure of laminated grains with numbers of LAGBs, as stabilized by nanoparticles, significantly ductilized Mo alloys, which opens an access to improve the ductility of refractory metals.
1. Introduction
Molybdenum (Mo) and Mo-based alloys are very attractive for many critical high-temperature applications such as in turbine, missile, and fusion reactor components, due to their advantages of high strength, excellent creep-resistance, high thermal conductivity, etc [Citation1–3]. However, the Mo alloys basically suffer from a limited ductility at room temperature (RT) [Citation4–6], which hinders their deep processing and extensive applications. How to improve the RT ductility has been a major goal over the past decades in the Mo community [Citation3,Citation5]. For this purpose, some strategies have been proposed, including (i) adding Rhenium (Re) solute to facilitate dislocation motion and hence improve the plastic deformation (known as solute softening) [Citation7,Citation8]; (ii) reducing impurity concentration at grain boundaries (GBs) to strengthen GBs and thus suppress intergranular fracture [Citation9,Citation10]; (iii) reinforcing Mo alloys with second-phase particles (e.g. carbide and oxide) to refine the grains and also restrain the recrystallization [Citation11,Citation12]. Owing to the high cost of Re, the first strategy with solute softening is seldom applied to large-scale industrial products. In comparison, the addition of second-phase particles, especially rare-earth oxide particles, is capable of realizing the second and the third strategies simultaneously, therefore becomes the most popular approach to increase the RT ductility of Mo alloys. In particular, some of the present authors have prepared ultrafine-grained Mo alloys with a dual distribution of nano-scaled La2O3 particles [Citation13], i.e. a large part within grain interior and the others at grain boundaries. These hierarchical Mo alloys exhibited a superior combination of RT yield strength of ∼820 MPa and elongation up to ∼40% [Citation13]. Although the high yield strength is known to be mainly from the strengthening mechanisms associated with sub-micro grains and nano-sized La2O3 particles, the underlying mechanisms for great ductility of ∼40% tensile elongation have not been well clarified. It was argued that the great ductility should be related to the significantly reduced impurity concentration at GBs (accompanied with the highly increased GBs when the grain size down to sub-micrometer) and the improved dislocation accumulation within the grain interior by nanoparticle pinning [Citation13]. Nevertheless, more microstructural features such as the grain boundary characteristics were insufficiently considered with respect to the ductilizing mechanism in the severely-deformed Mo alloys.
With the widespread use of advanced material preparing technologies and microstructural characterization techniques, low-angle grain boundaries (LAGBs) have been more and more observed in high-performance metal materials [Citation14–18] where the LAGBs were found to play an important role in high thermal stability [Citation14,Citation15] and large plastic deformation [Citation16–18]. Of special interest to note is that a substantial contribution of sub-grains to ductility was most recently evidenced in pure W [Citation19], a metal very similar to the present Mo. Motivated by these findings, we try to better understand the deformation mechanisms in Mo-La2O3 alloys, where the microstructural features will be affected by and interacted with the La2O3 second-phase particles. In this paper, Mo-La2O3 alloys with two different additions (0.3 and 0.6 wt.%) were prepared by swaging technology. Microstructural evolution and mechanical properties of the two Mo-La2O3 alloys after being exposed to different annealing temperatures (Ta) were studied to compare with those of the pure Mo free of La2O3 addition. The variation in La2O3 second-phase particles, coupled with different annealing treatments, led to multi-factor-sensitive microstructures that could be correlated to the mechanical properties by manifesting the deformation mechanisms.
2. Materials and methods
Mo-xLa2O3 alloys (x = 0, 0.3, and 0.6 wt.%, respectively) were prepared by powder metallurgy, where the Mo-La2O3 alloy powders were derived from a liquid–solid mixing method [Citation20,Citation21]. The powders were pressed to cylindrical compact with a diameter of 90 mm via cold isostatic pressing, and then sintered at 1850°C for 4 h in the protection of dry hydrogen. The cylindrical compact was primarily forged into rod with a diameter of 25 mm at 1250°C, subsequently rotary-swaged into rod with a diameter of ∼8 mm at successive decreasing temperatures from 900°C to 600°C. Finally, the rods were annealed at Ta = 1050°C, 1200°C, and 1400°C, respectively, for 1 h. Grains and grain boundaries were examined using a field-emission scanning electron microscope (FEI-NanoSEM450) equipped with an electron backscatter diffraction (EBSD) detector (EDAX-TSL Digital view). Coarse La2O3 particles were observed by scanning electron microscopy (SEM) verios460. Nanosized La2O3 particles and sub-grains structures were characterized by transmission electron microscope (TEM) JEM 2100F. The preparation of EBSD and TEM samples refers to previous publications [Citation13,Citation22–24]. Dog-bone-shaped tensile specimens were machined along the longitude direction of Mo and Mo alloy rod, with gauge sizes of 25 mm in length and 5 mm in diameter. The RT tensile test was conducted on the Instron 5900 testing machine, with a strain rate of 6.67 × 10−4 s−1.
3. Results and discussion
Representative EBSD images of the pure Mo and Mo-La2O3 alloys exposed to different annealing treatments are presented in Figure for comparison. When annealed at 1050°C, the deformed grain structure was unchanged in both the pure Mo and Mo alloys (Figure (a,d,g)), where several sub-grain layers could be frequently observed in lamellar grains. The enhanced recrystallization resistance by La2O3 particle addition began to become apparent with further raising the annealing temperature. In particular, the Mo alloy with 0.6 wt% La2O3 addition (abbreviated as Mo-0.6LaO alloy hereafter) showed an excellent thermal stability that the fine lamellar elongated grains survived even subjected to 1400°C (see Figure (b,c)). In the Mo alloy with 0.3wt.% La2O3 addition (abbreviated as Mo-0.3LaO alloy hereafter), the lamellar elongated grains experienced recovery to some degree and even partial recrystallization at 1200°C-exposure (Figure (e)). Accelerated grain recrystallization or coarsening occurred as Ta increased up to 1400°C, leading to much coarser lamellar grain structure (see Figure (f)). In comparison, the pure Mo without La2O3 displayed a much lower thermal stability. Equiaxed grains were predominantly found in the pure Mo annealed at 1200°C (Figure (h)), indicative of a full recrystallization.
Figure 1. Representative EBSD IPF coloring maps of Mo-0.6LaO alloy (a–c), Mo-0.3LaO alloy (d–f), and pure Mo (g–h) annealed at Ta = 1050°C (a,d,g), 1200°C (b, e, h), and 1400°C (c,f), respectively. Statistical results of the Ta -dependent average grain size are shown in (i).
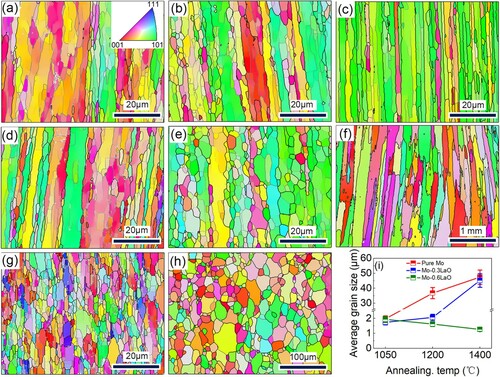
The Ta-dependent average cross-sectional grain size was statistically measured and quantitatively summarized in Figure (i) as a function of the La2O3 addition (or x). The grain size is defined as the spacing of neighboring boundaries along the transverse direction, where the boundaries with a misorientation >10° were automatically counted, despite of the grain morphology and grain volume. The pure Mo and Mo-La2O3 alloys maintained their deformation structure of lamellar elongated grains when annealed at 1050°C, with D being quite close among them. At Ta = 1200°C, D greatly increased in the pure Mo, due to the excited recrystallization behavior. Only a slight increase in D was detected in the 1200°C-annealed Mo-0.3LaO alloy, showing a thermal stability superior to the pure Mo. While at Ta = 1400°C, the Mo-0.3LaO alloy displayed an obviously enlarged D. It is interesting that, within the studied annealing temperature range, the average grain size of Mo-0.6LaO alloy somewhat reduced, rather than increased, by raising Ta. The unexpected Ta-dependent grain size evolution as found in the Mo-0.6LaO alloy should be mainly related to the in-situ recrystallization of small sub-grains that were initially existed within the lamellar grains. As the annealing temperature raised up to 1200°C, the lamellar grain structure still remained in the Mo-0.6LaO alloy, but the sub-grains with low-angle grain boundaries evolved to grains with high-angle grain boundaries (see Figure (e)). The newly-formed grains within original lamellar grains cause the measured grain size reduced by raising the annealing temperature.
Besides grain boundaries, sub-grain boundaries are clearly observed within the grain interior. Figure (a–d) representatively show some magnified EBSD images of the pure Mo annealed at 1050°C (Figure (a)) and 1200°C (Figure (b)), Mo-0.3LaO alloy annealed at 1200°C (Figure (c)), and Mo-0.6LaO alloy annealed at 1400°C (Figure (d)). In these images, the white lines within grain interior represent sub-grain boundaries or low-angle grain boundaries (LAGBs < 10°). Abundant LAGBs were presented in the pure Mo annealed at 1050°C (Figure (a)), while a few LAGBs were survived after exposed to 1200°C (Figure (b)). In comparison, a high-density LAGBs were remained in the Mo-0.3LaO alloy similarly exposed to 1200°C (Figure (c)). In the Mo-0.6LaO alloy, a great number of LAGBs were even evident at Ta = 1400°C (Figure (d)). Figure (e)-(g) compares some statistical results on misorientation angle distribution of the grain/sub-grain boundaries in the pure Mo (Figure (e)), Mo-0.3LaO (Figure (f)), and Mo-0.6LaO alloys (Figure (g)), respectively, annealed at different Ta. Figure (h) shows the percentage of LAGBs (PLAGB) varying with Ta in the three Mo-based materials. Quantitatively, the PLAGB reduced by beyond 70% in the pure Mo when raising Ta from 1050°C to 1200°C, and dropped to ∼ 0 at Ta = 1400°C. In the Mo-0.3LaO alloy, a significant reduction in the PLAGB was found when the Ta was increased from 1200°C (PLAGB > 20%) to 1400°C (PLAGB < 5%). But in the Mo-0.6LaO alloy, a great PLAGB of ∼ 16% still maintained even at Ta = 1400°C. About half of the LAGBs disappeared from Ta = 1050°C to 1400°C, where some LAGBs were transformed into high-angle grain boundaries (HAGBs) after interaction with dislocations. Revealed from the above grain/sub-grain examinations, the recrystallization of Mo-La2O3 alloys is highly dependent on the La2O3 addition and an interaction between Ta and x impacts the evolution of hierarchical microstructures.
Figure 2. Magnified EBSD IPF coloring maps of pure Mo (a, b), Mo-0.3LaO (c), and Mo-0.6LaO (d) annealed at Ta = 1050°C (a,c,d) and 1200°C (b), respectively, to clearly show the LAGBs (white lines within the grain interior). Statistical results on the boundary misorietation distribution in pure Mo (e), Mo-0.3LaO alloy (f), and Mo-0.6LaO alloy (g) annealed at different temperatures. (h) Statistical results of the PLAGB evolving with the annealing temperature and La2O3 addition.
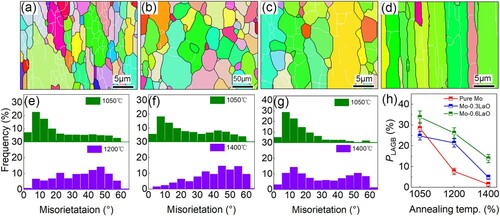
The enhanced thermal resistance and stabilized grain structure in Mo-La2O3 alloys are closely related to the La2O3 addition. In the present work, two sets of La2O3 second-phase particles were produced after the La2O3 addition. The one is coarse La2O3 second -phase particles that have a size in submicrometer scale and are located mainly at GBs (Figure (a)). The other is nanosized La2O3 second-phase particles that are dispersed within the grain interior (Figure (b)). The coarse La2O3 particles are rod-shaped, with an average size (,
: the shortest size or radius,
: the longest size or half length) in several hundred nanometers (Figure (c)) and a volume fraction (fc) of ∼ 0.40 vol.% in the Mo-0.3LaO alloy and ∼ 1.10 vol.% in the Mo-0.6LaO alloy. The nanosized La2O3 particles have a sphere-like shape in an average radius (
) of several tens of nanometers (Figure (d)), with a volume fraction (fn) of ∼ 0.25 vol.% in the Mo-0.3LaO alloy and ∼ 0.40 vol.% in the Mo-0.6LaO alloy. Both the coarse and nanosized La2O3 particles can pin GBs by Zener force [Citation25,Citation26], which stabilizes the GBs and promotes the recrystallization resistance. The Zener pinning force (F) stemmed from second-phase particles is simply expressed as [Citation25]:
(1)
(1) where f and d are the volume fraction and average size of second-phase particles, respectively. Equation (1) hints that the Zener pinning force is proportional to the volume fraction of particles but inversely to the particle size. As the nanosized La2O3 particles have a size several times smaller than that of the coarse particles, the Zener pinning force is predominantly contributed by the nanosized La2O3 particles. Especially, the value of
is higher in the Mo-0.6LaO alloy than that in the Mo-0.3LaO, the Zener pinning force is thus greater in the case of more La2O3 addition.
Figure 3. Representative SEM (a) and TEM (b) images to show the coarse La2O3 particles and nanosized La2O3 particles in the Mo-0.6LaO alloy, respectively. Both particles are respectively indicated by red arrows. Statistical results on the average size (dc or dn) and volume fraction (fc or fn) of the two types of particles (c: coarse La2O3, d: nanosized La2O3 particles).
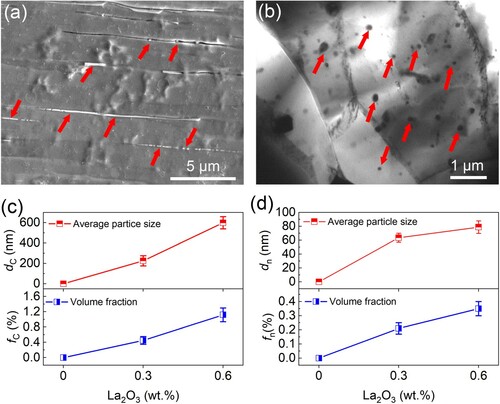
Figure (a) shows RT strain–stress curves of the pure Mo and Mo-La2O3 alloys after annealing at different Ta. The yield strength unsurprisingly increases with La2O3 addition, due to the strengthening contributions mainly from La2O3 second-phase particles and refined grains. In pure Mo, a reduction of ∼ 120 MPa in yield strength is evaluated by elevating Ta from 1050°C to 1400°C (Figure (b)), which is attributed to the grain recrystallization and LAGB/sub-grain disappearance. Similarly, a reduction of ∼ 150 MPa in yield strength is also found in the Mo-0.3LaO alloy as Ta jumps from 1200°C to 1400°C, because of a similar reason. In comparison, the yield strength of thermally-stable Mo-0.6LaO alloy is only slightly reduced. The variation of yield strength with La2O3 addition shows a consistent trend at different Ta (Figure (b)). The La2O3 addition-dependent tensile elongation or ductility, however, is much different at the three annealing temperatures (Figure (c)). At Ta = 1050°C, the tensile elongation monotonically decreases with added La2O3. It completely converses to a monotonical increase at Ta = 1400°C. While at the intermediate annealing temperature of 1200°C, a saddle-like curve is surprisingly observed in the tensile elongation-La2O3 addition correlation, with the maximum ductility highlighted at 0.3wt.% La2O3 addition. The difference in ductility evolution with Ta are resulted from a competition between two opposite effects induced by the La2O3 addition.
Figure 4. (a)Tensile stress vs strain curves of the pure Mo, Mo-0.3LaO alloy, and Mo-0.6LaO alloy annealed at different temperatures. Variation of yield strength (b) and tensile elongation (c) with La2O3 addition at different annealing temperatures. (d) Calculations of normalized elongation evolving with La2O3 addition at different dc, in comparison with the experimental results at Ta = 1050°C.
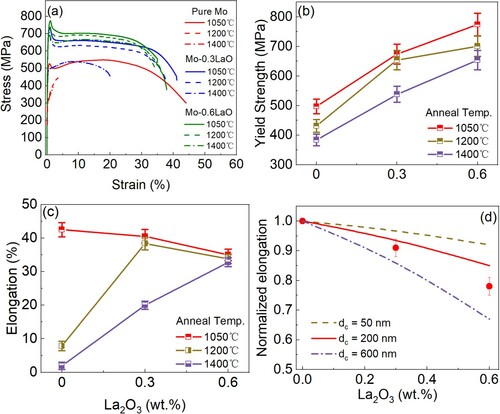
On the one hand, it has been generally proved [Citation13,Citation27–31] that the presence of coarse second-phase particles, in particular those distributed at GBs, should reduce the ductility of alloys. Because of a deformation discrepancy between the coarse particle and the matrix, intense stress concentration or strain concentration is instigated around the particles during plastic deformation. The stress/strain concentration, once accumulated to a critical degree, is destined to cause particle fracture or particle/matrix interface decohesion, which finally activates the microcrack formation and propagation. A micromechanics model has been established [Citation13,Citation27–29] to quantitatively describe the dependence of ductility (or fracture strain ) on the coarse particles as:
(2)
(2) where
is the strain hardening exponent;
,
, and
are the aspect ratio (
), interparticle spacing, and volume fraction of the coarse particles, respectively. It is clearly revealed from the above equation that more La2O3 addition will lead to a greater reduction in ductility because a higher-content coarse La2O3 particles are produced. A normalizing treatment was performed by following that in our previous publications [Citation27–29]. The lines in Figure (d) are calculations of the normalized ductility or normalized
as a function of La2O3 addition at different
, where the ductility of pure Mo (
→ 0) is chosen as the standard for normalization [Citation27–29] and
taken as ∼ 10 as experimentally determined. The calculations, in broad agreement with experimental results at Ta = 1050°C, quantitatively demonstrate the reduction in ductility caused by the addition-derived coarse La2O3 particles. As the grain size and LAGBs are close among the three Mo-based materials at Ta = 1050°C, their ductility is more controlled by the coarse La2O3 particles that reduce plastic deformation by acting as crack initiators or as preferential crack propagating paths.
On the other hand, the nanosized La2O3 particles that are also derived from the addition will promote the ductility by stabilizing the lamellar grain structure and LAGBs inside. Firstly, the lamellar grain structure in thin size (∼ 2 µm) contains a great number of near-parallel grain boundaries along the sample axis (or tensile direction). Upon applied loading, microcracks initially produced will be strongly constrained by these GBs [Citation32,Citation33], which splits the elongated grains into separate grain segments. Subsequently, cracking along GBs (or grain-boundary delamination) will be triggered in the region of triaxial stress or high strain regions to leave ligaments of the grain segments that are stretched to failure under plane stress conditions, resulting in a high amount of plasticity for each grain ligament [Citation5,Citation32–34]. This ductile laminate failure mode is a kind of thin sheet ductilizing, which changes the macroscopic plane strain condition to microscopic plane stress condition. Similar ductilizing (or toughening) mechanisms have been recently observed in steels [Citation35] and high-entropy alloys [Citation36]. Furthermore, Some representative SEM images are presented in Figure to compare the fracture surface among the pure Mo and Mo alloys, from which significant differences are evident. The recrystallized pure Mo with equiaxial grains (Figure (a and d)) showed a brittle intergranular fracture surface, whereas the Mo-0.3LaO alloy with coarse lamellar grains structure fractured in a quasi-cleavage mode (Figure (b and e)). On the contrary, the Mo-0.6LaO with a fine lamellar grain structure displayed a typical necking fracture surface, where a large number of secondary intergranular cracks were observed (Figure (c and f)), indicative of a laminate failure mechanism. From the comparison in Figure , it is evident that fine lamellar grains lead to improved ductility. This indicates that the particles have an effect on the ductility by stabilizing the fine lamellar grain structure. Secondly, the LAGBs are capable of promoting the plastic deformation in the BCC-structure Mo. The inferior lattice coherency of HAGBs will hinder the dislocation movement and lead to dislocation pile-ups and tangles, which have been shown to be crack nucleation sites [Citation37]. Whereas LAGBs have much more coherent crystal lattices and are equivalent to dislocations array at the boundary, since LAGBs have misorientation angles less than 10°. According to the selection rules for dislocation transfer at grain boundaries [Citation38,Citation39], boundaries parallel to both slip planes and directions are the most favorable orientation for dislocation transfer, and the angle between the incoming and outgoing slip planes should be minimized when they are not parallel. Based on these selection rules, LAGBs provide a more ideal pathway for dislocations across boundaries and avoid stress concentration at boundaries. Moreover, the segments of dislocation networks within LAGBs could serve as Frank-Read or Bardeen–Herring sources, providing sites for dislocation nucleation and boosting the dislocation activities [Citation40]. A positive effect of LAGBs on ductility has been recently proved in W alloys [Citation19], which should be also applicable to the Mo alloys.
Figure 5. Representative SEM images to compare the fracture surface of pure Mo annealed at 1200°C (a,d), Mo-0.3LaO (b,e), and 0.6 LaO (c f) at 1400°C.
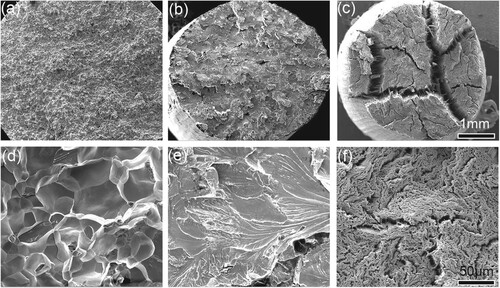
The competition between negative effect associated with coarse La2O3 particles (increased microcrack nucleation) and positive effect derived from nanosized La2O3 particles (stabilized lamellar grain structure with LAGBs) is responsible for the difference in ductility evolution with Ta as shown in Figure (c). At Ta = 1050°C, both lamellar grain structure and LAGBs are comparable among the three Mo-based materials, coarse La2O3 particles are thus the controlling factor that dominates the ductility. Since the coarse La2O3 particles increase with addition, a monotonic reduction in ductility is observed by raising the La2O3 addition. At Ta = 1200°C, deformation structure has been recrystallized in pure Mo with positive effect disappeared. The ductility of pure Mo reduced greatly. While the Mo-0.3LaO alloy still hold lamellar grain structure with a high density of LAGBs, which as before prevails over the negative effect from coarse La2O3 particles and leads to the greatest ductility. At Ta = 1400°C, however, the nanosized La2O3 particles were no longer effective in stabilizing the deformation structures in the Mo-0.3LaO alloy. The negative effect from coarse La2O3 particles converted to the predominant one, inducing a huge drop in ductility. But the deformation structures were preserved in the Mo-0.6LaO alloy due to the more nanosized La2O3 particles. The positive effect kept on countering the negative effect, resulting in a ductility greater than the Mo-0.3LaO alloy. It is evident that the nanoparticle-stabilized microstructural hierarchy enables the Mo-La2O3 alloys to reach a high thermal-resistance and a great ductility.
4. Conclusion
In summary, we demonstrate in this paper that the hierarchical microstructures of lamellar grains and high-density low-angle grain boundaries play an important role in ductilizing the Mo alloys. The La2O3 addition, although introducing coarse La2O3 particles that are detrimental to the ductility, disperses nanosized La2O3 particles to highly stabilize the deformation structures and effectively promote the plastic deformation. A competition between the negative effect and the positive effect could be tuned by the annealing temperature, which well explains the experimental findings that the addition-dependent ductility varied with annealing temperature. Compared with the pure Mo, 0.6wt.% La2O3 addition significantly increases the recrystallization resistance and the ductility has elevated over 10 times when annealed at 1400°C. This work highlights the hierarchical microstructures in ductilizing the Mo toward high performance with extended stable temperature range.
Disclosure statement
No potential conflict of interest was reported by the author(s).
Additional information
Funding
References
- Perepezko JH. The hotter the engine, the better. Science. 2009;326:1068–1069.
- Dimiduk DM, Perepezko JH. Mo-Si-B alloys: developing a revolutionary turbine-engine material. MRS Bull. 2003;28:639–645.
- El-Genk MS, Tournier J-M. A review of refractory metal alloys and mechanically alloyed-oxide dispersion strengthened steels for space nuclear power systems. J Nucl Mater. 2005;340:93–112.
- Sturm D, Heilmaier M, Schneibel JH, et al. The influence of silicon on the strength and fracture toughness of molybdenum. Mater Sci Eng A. 2007;463:107–114.
- Cockeram BV. The fracture toughness and toughening mechanism of commercially available unalloyed molybdenum and oxide dispersion strengthened molybdenum with an equiaxed, large grain structure. Metall Mater Trans A. 2009;40:2843–2860.
- Gunter IM, Schneibel JH, Kruzic JJ. Ductility and fracture toughness of molybdenum with MgAl2O4 additions. Mater Sci Eng A. 2007;458:275–280.
- Mueller AJ, Bianco R, Buckman RW. Evaluation of oxide dispersion strengthened (ODS) molybdenum and molybdenum–rhenium alloys. Int J Refract Met Hard Mater. 2000;18:205–211.
- Medvedeva NI, YuN G, Freeman AJ. Solid solution softening in BCC Mo alloys: effect of transition-metal additions on dislocation structure and mobility. Phys Rev B. 2005;72:134107.
- Miller MK, Kenik EA, Mousa MS, et al. Improvement in the ductility of molybdenum alloys due to grain boundary segregation. Scr Mater. 2002;46:299–303.
- Hiratsuka K, Watanabe K, Hashimoto I, et al. Effects of interstitial impurities on the grain-boundary strength of molybdenum. Philos Mag A. 1996;74:465–476.
- Cockeram BV. The mechanical properties and fracture mechanisms of wrought low carbon arc cast (LCAC), molybdenum–0.5pct titanium–0.1pct zirconium (TZM), and oxide dispersion strengthened (ODS) molybdenum flat products. Mater Sci Eng A. 2006;418:120–136.
- Ki Yoo M, Hiraoka Y, Kurishita H, et al. Recrystallization of TiC dispersion Mo-alloy. Int J Refract Met Hard Mater. 1996;14:355–364.
- Liu G, Zhang GJ, Jiang F, et al. Nanostructured high-strength molybdenum alloys with unprecedented tensile ductility. Nat Mater. 2013;12:344–350.
- Lu K. Stabilizing nanostructures in metals using grain and twin boundary architectures. Nat Rev Mater. 2016;1:1–13.
- Liu XC, Zhang HW, Lu K. Strain-induced ultrahard and ultrastable nanolaminated structure in nickel. Science. 2013;342:337–340.
- Li Y, Zhang Z, Vogt R, et al. Boundaries and interfaces in ultrafine grain composites. Acta Mater. 2011;59:7206–7218.
- Liu B, Eisenlohr P, Roters F, et al. Simulation of dislocation penetration through a general low-angle grain boundary. Acta Mater. 2012;60:5380–5390.
- Ren C, Fang ZZ, Xu L, et al. An investigation of the microstructure and ductility of annealed cold-rolled tungsten. Acta Mater. 2019;162:202–213.
- Xie XF, Xie ZM, Liu R, et al. Hierarchical microstructures enabled excellent low-temperature strength-ductility synergy in bulk pure tungsten. Acta Mater. 2022;228:117765.
- Zhang GJ, Sun YJ, Zuo C, et al. Microstructure and mechanical properties of multi-components rare earth oxide-doped molybdenum alloys. Mater Sci Eng A. 2008;483–484:350–352.
- Cheng PM, Zhang ZJ, Zhang GJ, et al. Low cycle fatigue behaviors of pure Mo and Mo-La2O3 alloys. Mater Sci Eng A. 2017;707:295–305.
- Cheng PM, Zhang GJ, Zhang JY, et al. Coupling effect of intergranular and intragranular particles on ductile fracture of Mo–La2O3 alloys. Mater Sci Eng A. 2015;640:320–329.
- Cheng PM, Li SL, Zhang GJ, et al. Ductilizing Mo–La2O3 alloys with ZrB2 addition. Mater Sci Eng A. 2014;619:345–353.
- Primig S, Leitner H, Knabl W, et al. Textural evolution during dynamic recovery and static recrystallization of molybdenum. Metall Mater Trans A. 2012;43:4794–4805.
- Andersen I, Grong Ø. Analytical modelling of grain growth in metals and alloys in the presence of growing and dissolving precipitates—I. Normal grain growth. Acta Metall Mater. 1995;43:2673–2688.
- Jones MJ, Humphreys FJ. Interaction of recrystallization and precipitation: the effect of Al3Sc on the recrystallization behaviour of deformed aluminium. Acta Mater. 2003;51:2149–2159.
- Liu G, Zhang GJ, Ding XD, et al. The influences of multiscale-sized second-phase particles on ductility of aged aluminum alloys. Metall Mater Trans A. 2004;35:1725–1734.
- Liu G, Sun J, Nan C-W, et al. Experiment and multiscale modeling of the coupled influence of constituents and precipitates on the ductile fracture of heat-treatable aluminum alloys. Acta Mater. 2005;53:3459–3468.
- Liu G, Zhang GJ, Wang RH, et al. Heat treatment-modulated coupling effect of multi-scale second-phase particles on the ductile fracture of aged aluminum alloys. Acta Mater. 2007;55:273–284.
- Goods SH, Brown LM. Overview No. 1: the nucleation of cavities by plastic deformation. Acta Metall. 1979;27:1–15.
- Hahn GT, Rosenfield AR. Metallurgical factors affecting fracture toughness of aluminum alloys. Metall Trans A. 1975;6:653–668.
- Cockeram BV. Measuring the fracture toughness of molybdenum-0.5 pct titanium-0.1 pct zirconium and oxide dispersion-strengthened molybdenum alloys using standard and subsized bend specimens. Metall Mater Trans A. 2002;33:3685–3707.
- Cockeram BV. The fracture toughness and toughening mechanisms of wrought low carbon arc cast, oxide dispersion strengthened, and molybdenum-0.5 pct titanium-0.1 pct zirconium molybdenum plate stock. Metall Mater Trans A. 2005;36:1777–1791.
- Cockeram BV. The role of stress state on the fracture toughness and toughening mechanisms of wrought molybdenum and molybdenum alloys. Mater Sci Eng A. 2010;528:288–308.
- Liu L, Yu Q, Wang Z, et al. Making ultrastrong steel tough by grain-boundary delamination. Science. 2020;368:1347–1352.
- Shi P, Li R, Li Y, et al. Hierarchical crack buffering triples ductility in eutectic herringbone high-entropy alloys. Science. 2021;373:912–918.
- Robertson IM, Lee TC, Subramanian R, et al. The effect of grain boundary chemistry on the slip transmission process through grain boundaries in Ni3Al. MRS Online Proc Libr. 1991;238:357–367.
- Shen Z, Wagoner RH, Clark WAT. Dislocation and grain boundary interactions in metals. Acta Metall. 1988;36:3231–3242.
- Clark WAT, Wagoner RH, Shen ZY, et al. On the criteria for slip transmission across interfaces in polycrystals. Scr Metall Mater. 1992;26:203–206.
- Reiser J, Hoffmann J, Jäntsch U, et al. Ductilisation of tungsten (W): on the shift of the brittle-to-ductile transition (BDT) to lower temperatures through cold rolling. Int J Refract Met Hard Mater. 2016;54:351–369.