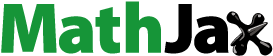
ABSTRACT
Nb alloys with high strength and relatively low density are sought for high-temperature applications. However, due to strain softening, conventional Nb alloys often exhibit insufficient high-temperature strengths. Here we report a strategy to design a novel lightweight and thermally-stable Nb alloy by combining the notion of eutectics and refractory carbide. The resulting Nb2MoWC0.96 eutectic alloy exhibits a high-temperature specific compressive strength of 77.2 MPa/·cm3·g1 at 1673 K with a retained engineering plasticity of 37.5%, both are notably higher than the existing Nb and Nb-containing alloys. This work demonstrates that both the strength and plasticity of Nb alloys can be further optimized with refractory carbide and eutectics.
GRAPHICAL ABSTRACT
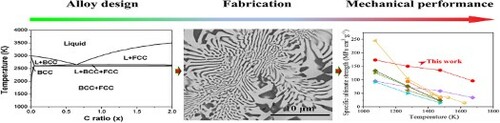
IMPACT STATEMENT
Combining the notion of eutectics with refractory carbide makes high strength, large plasticity Nb alloy with good microstructural stability.
Low-density high-temperature alloys are sought for applications in the aerospace and weapons industries. For example, advanced aero-engines and gas turbines require an operating temperature higher than 1273 K. Pure Nb has a high melting point of 2741 K and a low density of 8.57 g/cm3, making it an ideal element to be used at high temperatures. Also, owing to a good combination of high strength and high ductility, Nb alloys are often used as thermal protection and structural materials in aerospace, high-temperature reactors, and the aviation industry [Citation1-3]. Often, based on their strength values, low-, medium-, and high-strength Nb alloys are classified. Conventionally, alloying elements such as W, Mo, Ta, and V are added to improve the high-temperature strength of Nb alloys based on strong solid solution strengthening [Citation4-6]. However, their strength values are insufficient to meet a higher requirement as next-generation materials for aerospace engines [Citation7,Citation8]. For example, the commercially available high-strength Nb alloys, the F-48 (Nb-15W-5Mo-1Zr-0.1C) and C-3009 (Nb-22.4Hf-5.9W) alloys have compressive yield strength of 210 and 388 MPa at 1473 K, respectively [Citation7,Citation9]. These strength values are notably lower than those of Nb-containing alloys (i.e. 868 MPa for C0.25Hf0.25NbTaW0.5, and 673 MPa for HfMo0.5NbTiV0.5Si0.7) [Citation10,Citation11].
To further improve the strength of single-phase Nb alloys, the introduction of second phases such as Nb2C and Nb3Al is required [Citation3,Citation12]. However, the introduction of excessive second phases could lead to a significant loss in plasticity, mainly because of the easy crack formation during deformation, due to the weak interfacial bonding between the main phase and the second phase(s). For example, Nb-Si alloys (i.e. NbxMoyW-10Ti-18Si, x = 10 and 20, y = 0,5,10, and 15 in mol.%) consisting of an Nb-rich solid solution phase and a silicide phase exhibited a yield strength of about 400–800 MPa in compression mode at 1670 K, owing to a high-volume fraction (>40%) of the silicide phase [Citation4,Citation13]. Despite the high strength, the Nb-Si alloys suffer from crack initiation from interfacial decohesion [Citation14,Citation15].
Recently, a new class of refractory high-entropy alloys composed of multi-principal elements has exhibited a high strength at high temperatures owing to a strong solid solution strengthening [Citation16]. For example, equiatomic NbMoTaW and VNbMoTaW alloys were reported to have a high strength of above 420 MPa in compression at 1673 K [Citation16], which are notably higher as compared with their dilute alloys [Citation17]. Further, a higher strength can be achieved through the introduction of a second phase [Citation10,Citation13,Citation19]. For example, the Re0.5MoNbW(TaC)0.5 alloy consisting of a solid solution phase and a carbide phase exhibited an ultrahigh yield strength of 901 MPa in compression at 1473 K [Citation20], owing to the combination of a stable eutectic structure with a carbide phase of multi-principal-element-mixing. However, the density of this alloy (15.01 g/cm3) is significantly higher than those of Nb alloys having a density of 7.40–13.71 g/cm3 [Citation21].
To further improve the high-temperature strength while reducing the density of the carbide-reinforced eutectic high-entropy alloys, we redesign the alloy by tuning the chemical compositions so that the density is comparatively low as compared to the lightweight Nb alloys.
A compositionally optimized Nb2MoWC0.96 alloy with a molar ratio of 2: 1: 1: 0.96 was fabricated by arc melting high purity (better than 99.99%) Nb, Mo, W, and C powders under an argon atmosphere. Each alloy ingots were remelted five times to ensure chemical homogeneity. The samples had a diameter of about 20 mm and a thickness of about 8 mm. To evaluate thermal stability, the as-cast samples were sealed in Quartz tubes filled with high-purity argon and then annealed at 1573 K for 10 and 30 h in an electric furnace, respectively. The samples were then subsequently furnace-cooled to room temperature. Compression tests were conducted on cylindrical specimens with a dimension of Φ 4 mm × 6 mm at 1073, 1273, 1473, and 1673 K under an argon atmosphere using a Gleeble-3500 thermal simulator at a strain rate of 1×10−3 S−1. The engineering strain was calibrated using an extensometer.
The crystal structure was measured using an X-ray diffractometer (XRD) with a Cu target at a scanning rate of 1 degree/min. The microstructure was characterized using a scanning electron microscope (SEM, Quanta FEG250) equipped with a back-scattered electron (BSE) detector, and an electron backscatter diffraction (EBSD) detector. The EBSD data were analyzed using AZteccrystal software. Fine microstructure and chemical compositions were measured using a transmission electron microscope (TEM, Tecnai G2 F20) equipped with a high-angle annular dark-field (HAADF) detector and energy dispersive X-ray spectroscopy (EDS) detector.
Figure (a,b) show an XRD pattern and SEM-BSE images of the Nb2MoWC0.96 alloy, which reveal a lamellar eutectic microstructure consisting of alternating BCC and FCC-type NbC phases. The lattice constants of the BCC and NbC phases were identified to be a = 0.3224 nm and a = 0.4451 nm, respectively. Chemical analysis by TEM-EDS reveals that the BCC phase is partitioned by multiple elements with a composition of W33.1Nb32.5Mo30.2C4.2 (at. %) [Figure (c)]. Based on the chemical composition, the configurational entropy value (ΔS) is calculated to be 1.23 R provided that elements are randomly distributed, this value falls within the range of medium entropy alloy (0.69 R<ΔS < 1.61 R). By contrast, the NbC is a dilute carbide phase with a composition of (Nb53.4Mo5.5W5.5)64.4C35.6 [Figure (c) and Table ]. Microstructure analysis by high-resolution scanning TEM (STEM) shows that the BCC phase contains a low density of dislocations, while the NbC phase shows several stacking faults [Figure (d)], and the BCC/NbC phase interface shows a zig-zag morphology with visible misfit dislocations. The orientation relationship of the BCC and NbC phases is determined as the Kurdjumov-Sachs (K-S), namely [−111]BCC//[011]FCC-MC and (01-1)BCC//(−200)FCC-MC [Figure (f)].
Figure 1. Microstructure of the as-cast Nb2MoWC0.96 alloy. (a) XRD pattern and (b) SEM-BSE images show a fully eutectic microstructure. (c) HAADF-STEM image and the corresponding EDS maps show element distribution. (d) HADDF-STEM image of the eutectic structure. (e) HRTEM image of the BCC/NbC interface and the corresponding FFT patterns
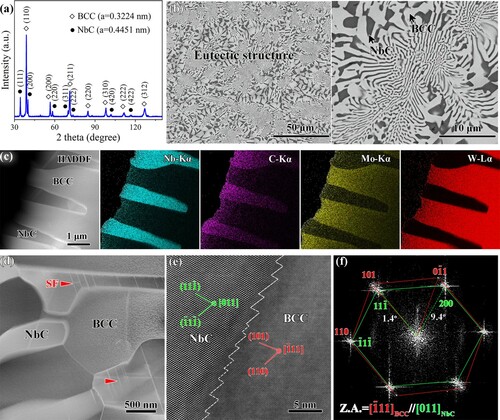
Table 1. Chemical composition of the phases measured by TEM-EDS.
The phase stability of the alloy was evaluated by theoretical calculation of phases and supported by phase analysis using XRD. Figure (a) shows a pseudo-binary phase diagram of (Nb2MoW)-C alloys calculated using the Fastsage software. The phase diagram exhibits a eutectic reaction with a reaction product of BCC and FCC (NbC) phases. The two phases remain stable during the solidification process without precipitation of new phases, supporting high thermal stability of the predicted BCC and FCC (NbC) phases. Figure (b) displays XRD patterns of the Nb2MoWC0.96 alloy annealed at 1573 K for 10 and 30 h, respectively. A second phase was not detectable in the XRD patterns, and a noticeable peak shift was also not observed, confirming again the high thermal stability of phases. This excellent phase stability is further supported by the fact that noticeable microstructure changes such as interfacial migration accompanied by grain coarsening were not observed in the alloy [Figure (c)].
Figure 2. (a) Calculated pseudo-binary phase diagram of Nb2MoWCx alloys. (b) XRD patterns of the as-cast and annealed Nb2MoWC0.96 samples. (c) SEM-BSE images of the as-cast and annealed Nb2MoWC0.96 samples.
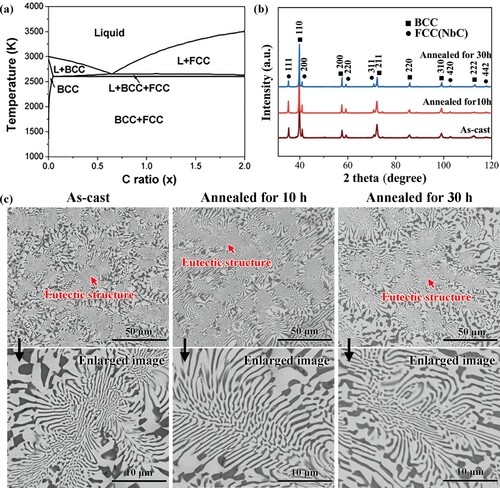
Uniaxial compression tests were conducted to evaluate the mechanical properties of the alloy. Figure (a, b) shows engineering and converted true stress-strain curves of the as-cast Nb2MoWC0.96 alloy compressed 1073 K to 1673 K with an interval of 200 K. The yield strength and compressive strength values of the Nb2MoWC0.96 alloy at varying temperatures are summarized in Table . Figure (c, d) displays the summarized temperature-dependent yield strength and ultimate strength normalized by their densities (Table ), these values are then compared with those of existing Nb and Nb-containing alloys tested under compression [Citation13,Citation19-24]. Notably, both specific yield strength and ultimate strength of the Nb2MoWC0.96 alloy are significantly higher than those of reported Nb and Nb-containing alloys particularly at high-temperature regime (i.e. >1273 K) because of the excellent resistance to high temperature softening.
Figure 3. (a, b) Engineering and true stress-strain curves of the as-cast Nb2MoWC0.96 alloy at varying compression temperatures. (c-d) A comparison of specific strength and specific ultimate strength of the Nb2MoWC0.96 alloy with reported Nb and Nb-containing alloys [Citation13,Citation19-24].
![Figure 3. (a, b) Engineering and true stress-strain curves of the as-cast Nb2MoWC0.96 alloy at varying compression temperatures. (c-d) A comparison of specific strength and specific ultimate strength of the Nb2MoWC0.96 alloy with reported Nb and Nb-containing alloys [Citation13,Citation19-24].](/cms/asset/bb876f15-fda9-4deb-a31c-623d3cce5a34/tmrl_a_2133977_f0003_oc.jpg)
Table 2. Compressive properties of the as-cast Nb2MoWC0.96 alloy at varying temperatures.
Table 3. Calculated theoretical densities of various Nb and Nb-containing alloys.
SEM-EBSD experiments were conducted to investigate the post-deformation microstructure of the Nb2MoWC0.96 alloy to clarify the strengthening mechanism. The values GNDs of Nb and NbC in the as-cast and high compression temperatures are summarized in Table . SEM-EBSD maps reveal a neglectable low dislocation density in the as-cast BCC and NbC phases (Figure ). After compression at 1073 K, a high density of dislocations is observed in both the BCC phase and NbC carbide phase. The dislocation density further increases with compression temperatures, as displayed in maps containing geometrically necessary dislocations (GNDs). Further increasing the compression temperature to 1673 K, however, a decrease in GNDs is observed, indicating that a recovery and recrystallization in the BCC and NbC phase took place during compression. As is revealed by the microstructures in Figure , the critical temperature for recrystallization is around 1673 K. Below this critical temperature, recovery should have taken place. However, the increased dislocation density upon increasing temperatures suggests that the speed for dislocation annihilation via recovery does not match with the accumulation of dislocations by a larger plastic strain with increasing deformation temperatures.
Figure 4. EBSD maps of the as-cast and compressed Nb2MoWC0.96 alloy reveal the changes in the density of GNDs and orientation relationships between the BCC and NbC phases. (a) Phase maps, (b) IPF maps, (c) GND maps.
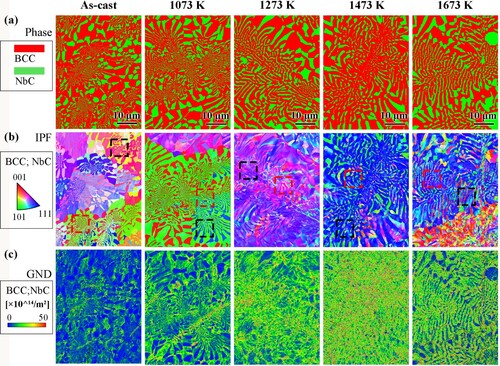
Table 4. GNDs of Nb and NbC in the as-cast and high compression temperatures.
Similar to the microstructure observed by TEM, the orientation relationship detected by SEM-EBSD reveals that the as-cast alloy near accommodates the K-S orientation relationship (Figure and ), while locally the lamellar structure adopts a neater K-S relationship. Upon compression at high temperatures, the local orientation relationship nearly retains locally, despite the K-S orientation seems to be destroyed from the pole figures of the whole area, due to the increased defect density and the occurrence of recrystallization.
Figure 5. EBSD pole figures of BCC and NbC phases from (a) whole area, (b) area 1 (black square), (c) area 2 (black square) of Figure (b).
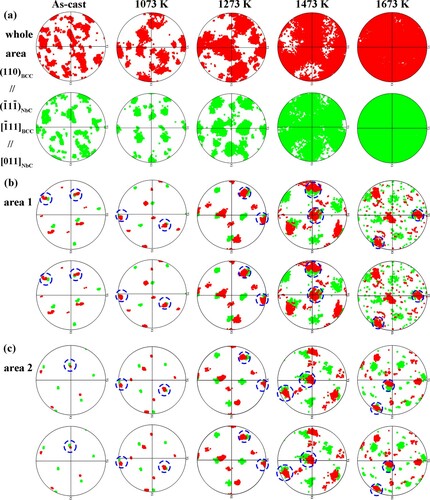
Post-deformation microstructure was further observed by TEM to unveil the fine structure of dislocations. Figure (a–d) are HAADF-STEM images of the as-cast alloy compressed at varying temperatures. These images reveal a high density of wavy dislocations within the BCC phase in all the samples. By contrast, numerous stacking fault (SF) ribbons are observed in samples compressed at 1073 K [Figure (a)], these SF ribbons are verified by HAADF-STEM observations as a mixture of both intrinsic stacking faults (ISFs) and hexagonal close-packed (HCP) phase [Figure (e)]. Further increasing the compression temperature results in a reduction in SF density. As displayed in Figure (a–c), a notable transition of deformation mode from SFs to mixed SFs and dislocations in the FCC carbide phase are observed. Upon compression at 1673 K, recrystallization along with reduced SF and dislocation density takes place [Figure (d)]. Despite recrystallization, the BCC/NbC eutectic interface remains stable without a significant change in its orientation relationship [Figure (f)]. It is worth noting that a transition of deformation mode from SFs to mixed SFs and dislocations are observed [Figure (a–c)]. This transition could be associated with activation of slip systems at increasing temperatures, which promotes dislocation nucleation at phase boundaries. At 1083 K, only partial dislocations are generated at the phase interface and propagate into grain interior. With deformation temperature increased to 1273 K, the generation of both mixed partial and full dislocations is observed.
Figure 6. (a-d) HAADF-STEM images of the compressed Nb2MoWC0.96 alloy at varying temperatures. (e) atomic structure of stacking fault ribbons in the NbC phase. (f) HRTEM and the corresponding FFT patterns of the BCC/NbC phase interface.
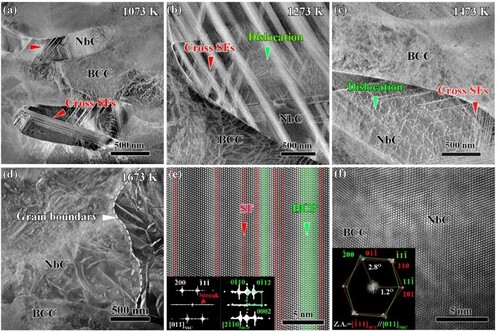
This work reports the design of a high-strength lightweight Nb alloy by combining the eutectics with refractory carbide. The resulting Nb2MoWC0.96 eutectic alloy exhibited a high strength at high temperatures owing to the excellent microstructure stability. This is in sharp contrast to the reported Nb and Nb-containing alloys in which grain coarsening and grain boundary sliding are often observed at high temperatures [Citation14,Citation25-27].
To clarify the high thermal stability of the lamellar eutectic structure, a defect migration speed VF is calculated as per the defect migration theory [Citation28]:
(1)
(1)
where D is the diffusion coefficient, γ is the surface tension between the two phases, the BCC solid solution phase is regarded as solvent and the NbC as solute, Cα and Cβ are solute concentrations of the two phases (Cα > Cβ) (α and β represent the BCC and NbC phases, respectively), λ is the average lamellae spacing of the eutectic structure in the as-cast alloy and is 550 nm on average (Figure ), λBCC is the average lamellar thickness of the as-cast BCC phase (about 250 nm). VBCC is the partial molar volume of the BCC phase [Citation29]. It is noted that that the interface migration is far more complicated than that simply described by the diffusion of solutes. However, this calculation with the simple model provides a qualitative estimation.
The calculated ln (2λ /λα) and (Cα–Cβ) are positive, thereby the value of VF is positive. The positive sign indicates that the eutectic structure is unstable, which is opposite to our observation that microstructure is highly stable at high temperatures. This in turn suggests that the value of VF would be extremely small and the diffusion coefficient D is tiny. Conversely, the high thermal stability of the eutectic structure is considered to arise from slow diffusion in the Nb2MoWC0.96 alloy. Thermodynamically, the configurational entropy of the BCC phase is calculated to be 1.23 R (where R is the gas constant) based on its chemical composition (Table ), this value is notably larger than those of dilute alloys with an entropy value of less than 0.69 R [Citation30]. In general, a slow diffusion could arise from the high configuration entropy effect. It has been pointed out that in the Al0.5CoCrCuFeNi HEAs, the sluggish diffusion kinetics ensures that the equilibrium phase at a high temperature can be frozen to room temperature even by conventional annealing treatments [Citation31]. They carried out extensive thermodynamic calculations of the Gibbs free energy difference (ΔG) between the solid solution and intermetallic phases by the Miedema model and revealed a delayed diffusion kinetics resulting from the high-entropy effect.
Upon compression, the BCC/NbC phase interface remained stable at high a temperature up to 1673 K (Figure ). To characterize the dissimilar interface quantitively, a mismatching degree factor between the BCC and NbC phases in the as-cast and 1474 K-compressed alloy is calculated with measured interplanar distances (d) and mismatch angles. For the as-cast alloy, the mismatch angle between (11-1)NbC and (101)BCC is estimated to be ∼1.4 degrees, and the d11-1 is 0.269 nm for the NbC phase while the d101 is 0.253 nm for the BCC phase. Therefore, the mismatch parameter (δ1) between (11-1 )NbC and (101)BCC is calculated as follows [Citation32]:
(2)
(2)
Likewise, the mismatch parameter (δ2) between (200)NbC and (0
1)BCC and δ3 between (
)NbC and (110)BCC are calculated to be 0.057 and 0.112, respectively. Herein, the average mismatch parameter δ is estimated as:
(3)
(3)
The calculated mismatch parameter (δ) falls between 0.05 and 0.25, supporting the semi-coherent nature of the interface. The result also demonstrates that the semi-coherent interface remains almost unchanged after high-temperature compression, further confirming the high thermal stability of the alloy.
Conversely, at a deformation temperature below 1673 K, the thermal stability of the alloy is dominated by interfacial stability. However, dislocation activity becomes a major factor in controlling thermal stability when temperature increases beyond 1673 K [Citation33], strong evidence is shown that an obvious recrystallization at 1673 K is observed, which took place at the expense of reduced dislocation density as shown in Table .
To conclude, a lightweight Nb eutectic alloy with a dual-phase structure was designed and fabricated. The resulting Nb2MoWC0.96 exhibited a high strength at high temperatures along with excellent microstructural stability. The main findings are listed below:
The as-cast Nb2MoWC0.96 alloy was composed of alternating BCC and FCC-type NbC phases. The composition and microstructure of the Nb2MoWC0.96 composite remained stable after annealing at 1573 K for 30 h, revealing excellent microstructural stability.
The Nb2MoWC0.96 alloy has an excellent combination of high strength and plasticity while achieving a comparable low density with conventional Nb and Nb-containing alloys.
The excellent microstructure stability below 1673 K is supposed to originate from a low diffusion coefficient of the BCC solid solution phase owing to a high configuration entropy, as well as from a small mismatch of coherent phase interface. At temperatures beyond 1673 K, dislocation activity plays a major role in controlling thermal stability.
Tensile ductility could be expected by proper thermomechanical treatment of the cast alloy because of the high plasticity of the fabricated Nb alloy.
Competing interests
The authors declare that they have no known competing financial interests or personal relationships that could have appeared to influence the work reported in this paper.
Data and materials availability
All data are reported in the paper.
Acknowledgments
This work was financially supported by the Young Scientists Fund of the National Natural Science Foundation of China (No. 52001120), Hunan Provincial National Science Fund for Distinguished Young Scholars under grant number 2022JJ10015, the State Key Laboratory of Advanced Metals and Materials (No. 2021-Z09), University of Science & Technology Beijing, China. Q.Q.W. acknowledges the financial support from the Excellent Postdoctoral Innovative Talents Program of Hunan Province (No. 2021RC2043). P.X. was supported by Hunan Provincial Natural Science Foundation of China (2022JJ30146). Professor Jianghua Chen and Professor Cuilan Wu are appreciated for their kind support in research funding.
Disclosure statement
No potential conflict of interest was reported by the author(s).
Additional information
Funding
References
- Wei W, Wang H, Zou C, et al. Microstructure and oxidation behavior of Nb-based multi-phase alloys. Mater Des. 2013;46:1–7.
- Tanaka R, Kasama A, Fujikura M, et al. Research and development of niobium-based superalloys for hot components of gas turbines. Miner Met Mater Soc. 2004;2:89–98.
- Vishwanadh B, Vaibhav K, Jha SK, et al. Development of Nb-1%Zr-0.1%C alloy as structural components for high temperature reactors. J Nucl Mater. 2012;427:350–358.
- Sha J, Hirai H, Tabaru T, et al. Effect of carbon on microstructure and high-temperature strength of Nb-Mo-Ti-Si in situ composites prepared by arc-melting and directional solidification. Mater Sci Eng A. 2003;343:282–289.
- Chan KS. Alloying effects on fracture mechanisms in Nb-based intermetallic in-situ composites. Mater Sci Eng A. 2002;329-331:513–522.
- Tan Y, Tanaka H, Ma C, et al. Solid-Solution strengthening and high-temperature compressive strength of Nb-X alloys (X=Ta, V, Mo and W). J Jpn Inst Met. 2000;64:559–565.
- Ning X. Composition and properties of niobium alloys from Russia and USA(III). Rare Metals Lett. 2002;9:22–23.
- Ding R, Jones IP, Jiao H. Effect of carbon on the microstructures and mechanical properties of as cast Nb-base alloy. Mater Sci Eng A. 2008;485:92–98.
- Senkov ON, Rao SI, Butler TM, et al. Ductile Nb alloys with reduced density and cost. J Alloys Compd. 2019;808:151685.
- Liu Y, Zhang Y, Zhang H, et al. Microstructure and mechanical properties of refractory HfMo0.5NbTiV0.5Six high-entropy composites. J Alloys Compd. 2017;694:869–876.
- Wu S, Qiao D, Zhang H, et al. Microstructure and mechanical properties of C Hf0.25NbTaW0.5 refractory high-entropy alloys at room and high temperatures. J Mater Sci Technol. 2022;97:229–238.
- Soboyejo WO, Ye F, Dipasquale J, et al. An investigation of the fatigue and fracture behavior of multicomponent Nb-11Al-41Ti-1.5Mo-1.5Cr intermetallic. J Mater Sci. 1999;34:3567–3575.
- Kim WY, Tanaka H, Kasama A, et al. Microstructure and room temperature fracture toughness of Nbss/Nb5Si3 in situ composites. Intermetallics. 2001;9:827–834.
- Sha J, Hirai H, Ueno H, et al. Mechanical properties of as-cast and directionally solidified Nb-Mo-W-Ti-Si in-situ composites at high temperatures. Metall Mater Trans A. 2003;34:85–94.
- Sha J, Hirai H, Tabaru T, et al. Effect of W addition on compressive strength of Nb-10Mo-10Ti-18Si-base in-situ composites. Mater Trans JIM. 2000;41:1125–1128.
- Senkov ON, Wilks GB, Scott JM, et al. Mechanical properties of Nb25Mo25Ta25W25 and V20Nb20Mo20Ta20W20 refractory high entropy alloys. Intermetallics. 2011;19:698–706.
- Sergi A, Khan RHU, Georgilas K, et al. Powder HIP of pure Nb and C-103 alloy: The influence of powder characteristics on mechanical properties. Int J Refract Met Hard Mater. 2022;104:105803.
- Soejima Y, Heima A, Akamine H, et al. Comparison of in situ SEM and TEM observations of thermoelastic martensitic transformation in Ti-Ni shape memory alloy. Mater Trans. 2020;61:2107–2114.
- Tabaru T, Hanada S. High temperature strength of Nb3Al-base alloys. Intermetallics. 1998;6:735–739.
- Wei Q, Luo G, Tu R, et al. High-temperature ultra-strength of dual-phase Re0.5MoNbW(TaC)0.5 high-entropy alloy matrix composite. J Mater Sci Technol. 2021;84:1–9.
- Wei Q, Xu X, Shen Q, et al. Metal-carbide eutectics with multiprincipal elements make superrefractory alloys. Sci Adv. 2022;8:eabo2068.
- Wojcik CC. High-temperature niobium alloys. Adv Mater Process. 1998;154:27–30.
- Guo NN, Wang L, Luo LS, et al. Microstructure and mechanical properties of refractory MoNbHfZrTi high-entropy alloy. Mater Des. 2015;81:87–94.
- Senkov ON, Woodward CF. Microstructure and properties of a refractory NbCrMo0.5Ta0.5TiZr alloy. Mater Sci Eng A. 2011;529:311–320.
- Senkov ON, Scott JM, Senkova SV, et al. Microstructure and elevated temperature properties of a refractory TaNbHfZrTi alloy. J Mater Sci. 2012;47:4062–4074.
- Juan CC, Tsai MH, Tsai CW, et al. Enhanced mechanical properties of HfMoTaTiZr and HfMoNbTaTiZr refractory high-entropy alloys. Intermetallics. 2015;62:76–83.
- Senkov ON, Senkova SV, Miracle DB, et al. Mechanical properties of low-density, refractory multi-principal element alloys of the Cr-Nb-Ti-V-Zr system. Mater Sci Eng A. 2013;565:51–62.
- Balluffi RW, Allen S, Carter WC. Kinetics of materials. Hoboken: John Wiley & Sons; 2005.
- Lin LY, Courtney TH. Direct observations of lamellar fault migration in the Pb-Sn eutectic. Metall Mater Trans B. 1974;5:513–514.
- Yeh JW. Recent progress in high-entropy alloys. Eur J Control. 2006;31:633–648.
- Ng C, Guo S, Luan J, et al. Entropy-driven phase stability and slow diffusion kinetics in an Al0.5CoCrCuFeNi high entropy alloy. Intermetallics. 2012;31:165–172.
- Bramfitt BL. The effect of carbide and nitride additions on the heterogeneous nucleation behavior of liquid iron. Metall Trans. 1970;1:1987–1995.
- Li LL, Su YQ, Beyerlein IJ, et al. Achieving room-temperature brittle-to-ductile transition in ultrafine layered Fe-Al alloys. Sci Adv. 2020;6:eabb66.