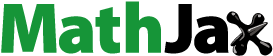
ABSTRACT
The precipitation hardening is widely applied to strengthen Al alloys. Here, we report an alternative way to achieve high-strength Al alloys via forming the dislocation gradient through pre-torsion. Remarkably, the gradient Al alloys exhibit a sharp increase in ultimate tensile strength up to 605 MPa yet nearly without reducing the uniform elongation, thereby outperforming their counterparts. The superior strength–ductility combination is ascribed to the excellent strengthening and strain hardening effects stemming from the substantial hetero-deformation-induced hardening in the coarse-grained gradient Al alloys. Our study thus paves a new way to improve the mechanical properties of Al alloys.
GRAPHICAL ABSTRACT
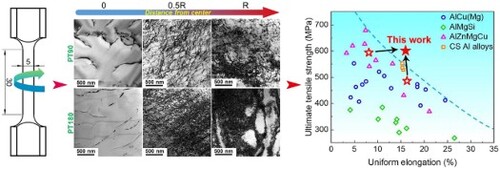
IMPACT STATEMENT
The gradient distribution of dislocations significantly increases the strength of the Al alloy with the neglectable reduction in uniform elongation, which enables exceptional mechanical properties that outperform the peak-aged counterpart.
1. Introduction
Al alloys belong to one of the most widely used structural materials in industries due to their excellent formability, high specific mechanical properties, and good corrosion resistance [Citation1,Citation2]. By far, precipitation hardening is of great prominence for Al alloys in pursuit of high strength [Citation3]. The common way is to age the supersaturated solid solution of Al alloys in relatively low temperatures to induce the formation of precipitates by controlling the decomposition of the matrix [Citation4], which involves nucleation, growth and coarsening of precipitates. The precipitation of Al–Zn–Mg–Cu (7XXX) alloys, typical examples of high-strength ones for aerospace and transportation applications [Citation5], occurs following the sequences of Guinier–Preston (GP) zones, , and
(MgZn2) [Citation6,Citation7]. The fine distribution of a high number density of GPs and
are desirable in Al–Zn–Mg–Cu alloys, as the uniformly dispersed precipitates strongly impede the dislocation movements and thus, offer substantial strengthening effects [Citation8].
Recently, Sun et al. [Citation9] performed a cyclic deformation on Al alloys to mediate the dynamic precipitation of very fine solute clusters. The resulting cyclic-strengthened alloys exhibited comparable strengths and elongations to their counterparts undergoing thermal treatments. The strength of these alloys can be further improved by conducting subsequent heat treatment, which arises from the formation of a very high number density of precipitates assisted by the pre-existence of clusters [Citation10]. The strategy of cyclic strengthening was further extended to enhance the fatigue resistance of Al alloys, due to the dynamical healing of inherent weak points in the microstructure [Citation11]. However, precipitation strengthening is still inevitable to achieve high-strength Al alloys, though different pathways were employed.
In this study, we demonstrate an alternative pathway to achieve high strength and large plasticity in Al alloys via creating dislocation gradient structures. As a representative group of heterogeneous materials, gradient structure materials, such as the grain size gradient pure Cu [Citation12,Citation13], hierarchy nano twining gradient steels and Cu [Citation14,Citation15], and dislocation cell gradient high-entropy alloy [Citation16], enable to significantly increase the strength while retain the ductility, when comparing to their homogenous counterparts. Enlightened by such advances, we design a dislocation gradient 7050 Al alloy by conducting the torsion treatment. The yield strength increases with the increase of pre-torsion angles, nearly without sacrificing the uniform tensile elongation. Remarkably, the alloy with pre-torsion of 180° shows higher ultimate tensile strength and further doubles the uniform elongation compared to the peak-aged alloy, indicating an attractive tactic to develop high-performance Al alloys.
2. Materials and methods
The commercialized 7050 Al alloys (Al–6.96 Zn–1.99 Mg–2.07 Cu–0.09 Zr–0.036 Si–0.10 Fe, wt.%) are chosen in this study. The as-received alloys were homogenized at 475°C for 5 h, followed by water quenching. For comparison, a peak-aged treatment (referred to as T6) was performed at 120°C for 24 h. The configuration of the Al alloy specimen is sketched in Figure (a). The measured diameter of the gauge segment of the cylinder specimen is 5 mm, with a gauge length of 30 mm. The pre-torsion and subsequent tensile tests under extensometer-measured strain control were conducted by using MTS 858 Mini Bionix II axial/torsional test system. The pre-torsion was conducted with an angular rate of 60°/min, and the tension was performed with a strain rate of 10−3 s−1. The pre-torsion angles were implemented as 90° and 180°, denoted as PT90 and PT180 respectively. Tensile tests and load-unloading-reloading (LUR) tensile tests were conducted by using an MTS 793 machine with a tensile rate of 10−3 s−1 at room temperature. The hardness along the radial direction was measured by using an FEI-VM50 PC Vickers hardness testing tester, with the indentation load of 200 g and dwelling time of 15 s. The hardness value is the average of 6 indentations, with the interval of ∼0.25 mm between each indentation to express gradient distribution along the radius direction.
Figure 1. (a) Geometric size of the specimens. (b) EBSD IPF map of the homogenized Al alloy. (c) Bright field TEM image showing the existence of dispersoids. (d) HRTEM image along the [001]Al zone axis; the inserted FFT confirms the structure of Al3Zr.
![Figure 1. (a) Geometric size of the specimens. (b) EBSD IPF map of the homogenized Al alloy. (c) Bright field TEM image showing the existence of dispersoids. (d) HRTEM image along the [001]Al zone axis; the inserted FFT confirms the structure of Al3Zr.](/cms/asset/91a154a1-3bd6-4dfe-86b0-6ae5d692f3ad/tmrl_a_2151851_f0001_oc.jpg)
Electron backscatter diffraction (EBSD) analysis was performed on an FEI Helios Nano Lab G3 UC scanning electron microscopy (SEM) operating at 20 kV. The specimens for EBSD examinations were prepared by mechanical polishing using diamond suspension and colloidal silica suspension. Microstructures were further examined by a Talos F200X transmission electron microscopy (TEM) with an energy-dispersive X-ray spectroscopy (EDS) system at an acceleration voltage of 200 kV. The TEM thin foils were prepared by twin-jet electropolishing and ion-beam thinning. Atom probe tomography (APT) experiments using the local electrode atom probe instruments (CAMECA LEAP 5000 XR) were performed for the pre-torsion sample prepared by FEI Helios Plasma focused ion beam (PFIB) with a Xe source.
3. Results and discussion
The EBSD map in Figure (b) shows the microstructure of the homogenized Al alloy. A single face-centered cubic (FCC) phase structure is detected with a relatively coarse grain size of ∼100 µm (Supplementary Fig. S1). No texture is detected in this alloy based on the inverse pole figure (IPF) map (Figure (b)). This is ascribed to the long-time solid solution treatment, which enables to eliminate the possible pre-existing texture and allows the growth of grain size. The zoom-in bright field (BF) TEM image in Figure (c) depicts that a small number of precipitates (size of 15-30 nm) exist in the matrix. The further high-resolution TEM image and corresponding fast Fourier transform (FFT) pattern indicate that they are the L12-ordered Al3Zr phases [Citation17]. Such small inclusions are typically seen in 7050 Al alloys after homogenization [Citation18], exacting a neglectable effect on mechanical properties in this study due to their extremely low volume fraction (∼0.3%).
We then performed torsion deformation with the angles of 90° and 180° on the homogenized Al alloy. Due to the very high stacking fault energy in Al alloys, the stacking fault, mechanical twinning and deformation-induced phase transformation are unable to occur upon loading [Citation19], while instead, the deformation is governed by dislocation slip [Citation20]. Thus, the rewarding strain hardening mechanisms such as twining-induced plasticity (TWIP) [Citation21,Citation22] and phase transformation-induced plasticity (TRIP) [Citation23,Citation24] are absent. The mechanical performance relies on the tunning of dislocation activities. As shown in Figure , the torsion treatment creates the dislocation gradient in current Al alloys, of which the density of dislocations increases along the radial direction. In the PT90 alloy, very few dislocations are detected in the center, while the tangled dislocations are observed in the middle region, and ultimately, dislocation walls filled with a high density of dislocations are found at the surface. When the pre-torsion angle increases to 180°, higher densities of dislocations can be seen at both surface and middle regions, as compared Figure (b,c) with Figure (e,f). However, both PT90 and PT180 show very similar low densities of dislocations at the center region, though the torsion angle increases, which is due to the unique feature of torsion deformation.
Figure 2. Cross-sectional bright field TEM images showing microstructures of (a-c) PT90 and (d-f) PT180 samples at the region of r = 0, 0.5R, and R, respectively. R represents the radius of the sample.
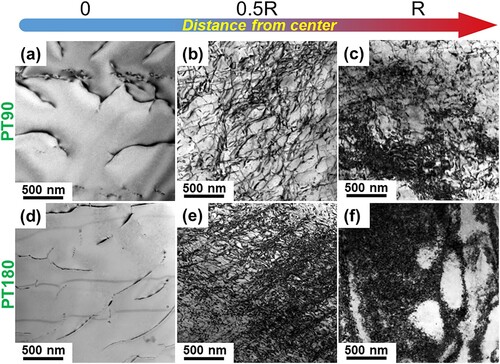
We did not detect the grain size refinement of the Al alloy after the torsion treatment, as shown by IPF maps in Supplementary Fig. S2. Although the average grain sizes are slightly different in different samples (see Supplementary Fig. S1 and Fig. S2), the variation of grain size in this range has little effect on yield strength according to the Hall–Petch relationship in our study. Unlike the formation of gradient structure via surface treatments, which usually induce the nanograins at the surface layer [Citation25], the torsion deformation did not refine the grain size due to the unique linear strain distribution. A similar phenomenon is seen in torsion-treated TWIP steels [Citation14] and high-entropy alloys [Citation26] as well.
We further performed the APT analysis to determine whether the chemical element partitioning occurred during the torsion treatment. The heat produced by the torsion deformation may accelerate the ageing procedures and, thus causes the possible phase decomposition of the matrix. With the aid of PFIB sample preparation method, we lifted out a tip at the very edge of the specimen, in which the strain and the associated heating are the highest. The atomic maps for Al, Zn, Mg, and Cu are shown in Figure , indicating the homogeneous distribution of elements. In order to further rule out the existence of clusters, we conducted the first-order nearest-neighbor separation distances between Al and other solute atoms in the APT datasets. The corresponding experimental data is very close to the ideal random distribution, which confirms the missing precipitation due to the very short loading time in torsion deformation. The grain boundary segregation during the torsion deformation was not investigated, because it’s possible influence on mechanical properties is neglectable in our Al alloy with a very coarse grain size (∼100 µm).
Figure 3. (a) Atomic maps for individual elements at the surface region of PT180 sample. (b) The nearest-neighbor distribution of Mg, Zn, and Cu atoms.
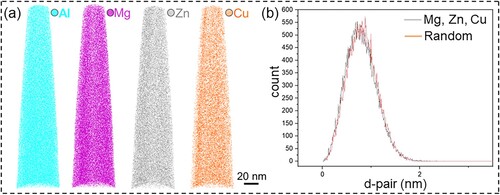
The mechanical performance of the Al alloys with pre-torsion is examined by the uniaxial tensile test, and the engineering stress–strain curves are shown in Figure (a). The curve of the Al alloy without pre-torsion is also shown for comparison (referred to as PT0). Both the yield strength and ultimate tensile stress increase with increasing the torsion angle, and surprisingly, the uniform tensile elongation is nearly free of reduction. For example, the ultimate tensile stress (UTS) raises sharply from 486 MPa for the PT0 alloy to 605 MPa for the PT180 alloy, while the uniform tensile elongation nearly remains at the same level (from 16.1% to 15.6%). The intriguing mechanical properties of the PT180 alloy are further supported by comparing with the T6 peak-aged alloy, of which a high number density of nanoscale precipitates with an average size of ∼5 nm form (Figure (b)). These nanoprecipitates were identified as η’ phases enriching Mg and Zn (see Supplementary Fig. S3). By comparison, the PT180 alloy not only doubles the uniform elongation from 8% to 16%, but also shows the UTS of 605 MPa that is higher than the 594 MPa for the T6 alloy. Such a superior combination of strength and ductility outperforms other high-strength Al alloys, including the typical precipitation strengthening AlCu(Mg) (2XXX) [Citation27–30], AlMgSi (6XXX) [Citation31,Citation32], AlZnMgCu (7XXX) [Citation33–35] alloys and cyclic strengthening (CS) Al alloys [Citation9], as seen in Figure (c). This indicates that a rewarding alternative pathway to enhance the mechanical properties of Al alloys by dislocation gradient, rather than the precipitation strengthening.
Figure 4. (a) Engineering stress–strain curves of the PT0, PT90, and PT180 alloys. (b) Comparison of engineering stress–strain curves between PT180 and T6 (peaked aged sample); the inserted bright field TEM micrograph showing the dense distribution of precipitates in the T6 sample. (c) Maps of UTS versus uniform elongation of Al alloys reported previously; the data of the tensile properties of reported Al alloys were listed in Supplementary Table 1.
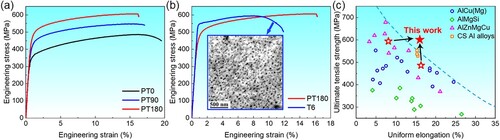
To unveil the underlying mechanisms, we investigated the deformation microstructure and strain hardening. The hardness evolution along the radial direction is shown in Figure (a). Prior to loading, the hardness of the PT180 is 138 HV at the center, similar to the PT0 alloy, while this value increases up to 178 HV at the surface, suggesting a typical gradient distribution owing to the torsion deformation-induced strain distribution. After the tensile deformation, the hardness values are close from the center to surface, all of which show the high value of 208 HV. This indicates the heterogeneous deformation and strain accommodation. We also conducted the LUR tests to determine the hetero-deformation-induced (HDI) stress (see Figure (c)). As shown in Figure (d), the HDI stress is much higher in the PT180 alloy than that of the PT0 alloy, e.g. ∼350 MPa vs. ∼225 MPa at 6% strain, which plays a critical role in achieving excellent mechanical properties.
Figure 5. (a) Hardness evolution along the radial direction. (b) The plot of strain hardening rate versus true strain of PT0 and PT 180 alloys; the inset shows the corresponding true stress–strain curves. (c) LUR curves of PT0 and PT180 alloys. (d) Comparison of the HDI stress as a function of true strain between PT0 and PT180 alloys.

Precipitation strengthening acts as one of the most effective strengthening mechanisms in Al–Zn–Mg–Cu alloys [Citation3]. Though the substantial strengthening effect it offers precipitates typically induce more local stress concentration upon deformation that reduces the plasticity [Citation36]. Remarkably, our gradient dislocation structure provides a significant strengthening effect nearly without compromising the ductility, leading to excellent mechanical properties that outcompete the counterparts (see Figure (c)). A large number of gradient dislocations formed in the process of pre-torsion deformation offer the significant strengthening effect. Besides, the cell-block dislocation configurations formed in the surface regions can resist dislocation motion [Citation16], which thus contributes to additional hardening. All of these give rise to the great increase in the yield strength. Meanwhile, the resulting strain gradient promotes the proliferation and interaction of dislocations during tensile deformation, producing the unique HDI hardening to stabilize the plastic deformation.
The contributions of HDI hardening, which is generated by the attractive dislocation gradient structure, can rationalize the enhanced strength-ductility combination [Citation37,Citation38]. For the current Al alloy, the gradient distribution of dislocations formed by pre-torsion leads to the formation of soft domains (at the center) and hard domains (at the surface) in the alloy. However, after tension to fracture, the hardness along the radial direction tends to be uniform, as shown in Figure (a). Therefore, HDI stress is induced to coordinate deformation in complex stress/strain states during the process of heterogamous tensile deformation [Citation39]. Such HDI stress is typically opposite to the direction of the applied stress, thus hindering the emission of dislocations at the dislocation source and the long-range movement of dislocations, which contributes to strong additional strengthening and hardening [Citation40]. Consequently, the persistent effect of high HDI hardening obtains enough work hardening and brings considerable strength and ductility in the gradient structure Al alloy.
In addition, the large grain size of the present Al alloy enables to fully make use of the strengthening and strain hardening effects from HDI stress. The fine grain size is able to impede the dislocation motion and provide strong strengthening effects due to the high strain hardening rate at the original deformation. However, this usually leads to the rapidly drop in strain hardening rate at medium and high levels of deformation [Citation41]. On the contrary, the strain hardening behavior of the coarse grain size material is mainly controlled by the interaction of dislocations within the grains, and the dislocation annihilation at grain boundaries rarely produces a marked effect, which ensures stable work hardening capability [Citation42,Citation43]. Hence, the plastic deformation can proceed steadily in the gradient structure Al alloy with coarse grains, which enables to exhaust the HDI hardening that strongly benefits the mechanical properties.
4. Conclusion
In summary, the gradient Al alloy shows a sharp increase in the strength with the neglectable influence on uniform elongation, leading to the excellent combination of strength up to 605 MPa and large uniform elongation of ∼16%. The resulting gradient Al not only shows a higher UTS but also doubles the uniform elongation when compared to the peak-aged peer, which outcompetes other high-strength aluminum alloys. The coarse grain-sized gradient Al alloys enable to fully exploit the strengthening and strain hardening ability from the HDI hardening, accounting for the excellent mechanical performance. The present tactic of designing heterogeneous structured materials to achieve Al alloys with superior mechanical properties further offers guidance for the future development of high-performance Al alloys.
Supplemental Material
Download MS Word (3.1 MB)Acknowledgements
We would like to thank Prof. Xiaogang Wang at Hunan University for his help with LUR tests.
Disclosure statement
No potential conflict of interest was reported by the author(s).
Additional information
Funding
References
- Stemper L, Tunes MA, Tosone R, et al. On the potential of aluminum crossover alloys. Prog Mater Sci. 2022;124:100873.
- Sercombe TB, Schaffer GB. Rapid manufacturing of aluminum components. Science. 2003;301:1225–1227.
- Chen Y, Weyland M, Hutchinson CR. The effect of interrupted aging on the yield strength and uniform elongation of precipitation-hardened Al alloys. Acta Mater. 2013;61:5877–5894.
- Yang Z, Banhart J. Natural and artificial ageing in aluminium alloys – the role of excess vacancies. Acta Mater. 2021;215:117014.
- Zhao H, Chakraborty P, Ponge D, et al. Hydrogen trapping and embrittlement in high-strength Al alloys. Nature. 2022;602:437–441.
- Löffler H, Kovacs I, Lendvai J. Decomposition processes in Al-Zn-Mg alloys. J Mater Sci. 1983;18:2215–2240.
- Liu JZ, Chen JH, Yang XB, et al. Revisiting the precipitation sequence in Al–Zn–Mg-based alloys by high-resolution transmission electron microscopy. Scr Mater. 2010;63:1061–1064.
- Chen JZ, Lv LX, Zhen L, et al. Precipitation strengthening model of AA 7055 aluminium alloy. Acta Metall Sin. 2021;57:353–362.
- Sun WW, Zhu YM, Marceau R, et al. Precipitation strengthening of aluminum alloys by room-temperature cyclic plasticity. Science. 2019;363:972–975.
- Shi L, Baker K, Young R, et al. The effect of chemical patterning induced by cyclic plasticity on the formation of precipitates during aging of an Al–Mg–Si alloy. Mater Sci Eng A. 2021;815:141265.
- Zhang Q, Zhu YM, Gao X, et al. Training high-strength aluminum alloys to withstand fatigue. Nat Commun. 2020;11:5198.
- Fang TH, Li WL, Tao NR, et al. Revealing extraordinary intrinsic tensile plasticity in gradient nano-grained copper. Science. 2011;331:1587–1590.
- Long JZ, Pan QS, Tao NR, et al. Residual stress induced tension-compression asymmetry of gradient nanograined copper. Mater Res Lett. 2018;6:456–461.
- Wei YJ, Li YQ, Zhu LC, et al. Evading the strength-ductility trade-off dilemma in steel through gradient hierarchical nanotwins. Nat Commun. 2014;5:3580.
- Cheng Z, Zhou HF, Lu QH, et al. Extra strengthening and work hardening in gradient nanotwinned metals. Science. 2018;362:eaau1925.
- Pan QS, Zhang LX, Feng R, et al. Gradient-cell–structured high-entropy alloy with exceptional strength and ductility. Science. 2021;374:984–989.
- Cassell AM, Robson JD, Race CP, et al. Dispersoid composition in zirconium containing Al-Zn-Mg-Cu (AA7010) aluminium alloy. Acta Mater. 2019;169:135–146.
- Su JQ, Nelson TW, Mishra R, et al. Microstructural investigation of friction stir welded 7050-T651 aluminium. Acta Mater. 2003;51:713–729.
- Minor AM, Asif SA, Shan Z, et al. A new view of the onset of plasticity during the nanoindentation of aluminium. Nat Mater. 2006;5:697–702.
- Oh SH, Legros M, Kiener D, et al. In situ observation of dislocation nucleation and escape in a submicrometre aluminium single crystal. Nat Mater. 2009;8:95–100.
- De Cooman BC, Estrin Y, Kim SK. Twinning-induced plasticity (TWIP) steels. Acta Mater. 2018;142:283–362.
- Wang ZW, Lu WJ, An FC, et al. High stress twinning in a compositionally complex steel of very high stacking fault energy. Nat Commun. 2022;13:3598.
- Li Z, Pradeep KG, Deng Y, et al. Metastable high-entropy dual-phase alloys overcome the strength-ductility trade-off. Nature. 2016;534:227–230.
- An XL, Wang ZW, Ni S, et al. The tension-compression asymmetry of martensite phase transformation in a metastable Fe40Co20Cr20Mn10Ni10 high-entropy alloy. Sci China Mater 2020;63:1797–1807.
- Lei YB, Wang ZB, Xu JL, et al. Simultaneous enhancement of stress- and strain-controlled fatigue properties in 316L stainless steel with gradient nanostructure. Acta Mater. 2019;168:133–142.
- Wu WQ, Guo L, Liu B, et al. Effects of torsional deformation on the microstructures and mechanical properties of a CoCrFeNiMo0.15 high-entropy alloy. Philos Mag. 2017;97:3229–3245.
- Qu Z, Zhang ZJ, Yan JX, et al. Examining the effect of the aging state on strength and plasticity of wrought aluminum alloys. J Mater Sci Technol. 2022;122:54–67.
- Liu XH, Liu YZ, Zhou ZG, et al. A combination strategy for additive manufacturing of AA2024 high-strength aluminium alloys fabricated by laser powder bed fusion: role of hot isostatic pressing. Mater Sci Eng A. 2022;850:143597.
- Zheng RX, Sun YB, Ameyama K, et al. Optimizing the strength and ductility of spark plasma sintered Al 2024 alloy by conventional thermo-mechanical treatment. Mater Sci Eng A. 2014;590:147–152.
- Ma YW, Choi JW, Yoon KB. Change of anisotropic tensile strength due to amount of severe plastic deformation in aluminum 2024 alloy. Mater Sci Eng A. 2011;529:1–8.
- Mehta A, Zhou L, Huynh T, et al. Additive manufacturing and mechanical properties of the dense and crack free Zr-modified aluminum alloy 6061 fabricated by the laser-powder bed fusion. Addit Manuf. 2021;41:101966.
- Yan WL, Liu XH, Huang JY, et al. Strength and ductility in ultrafine-grained wrought aluminum alloys. Mater Design. 2013;49:520–524.
- Zhao YH, Liao XZ, Cheng S, et al. Simultaneously increasing the ductility and strength of nanostructured alloys. Adv Mater. 2006;18:2280–2283.
- Yoder JK, Griffiths RJ, Yu HZ. Deformation-based additive manufacturing of 7075 aluminum with wrought-like mechanical properties. Mater Design. 2021;198:109288.
- Leng L, Zhang ZJ, Duan QQ, et al. Improving the fatigue strength of 7075 alloy through aging. Mater Sci Eng A. 2018;738:24–30.
- Liu G, Sun J, Nan CW, et al. Experiment and multiscale modeling of the coupled influence of constituents and precipitates on the ductile fracture of heat-treatable aluminum alloys. Acta Mater. 2005;53:3459–3468.
- Zhu YT, Wu XL. Perspective on hetero-deformation induced (HDI) hardening and back stress. Mater Res Lett. 2019;7:393–398.
- Zhu YT, Ameyama K, Anderson PM, et al. Heterostructured materials: superior properties from hetero-zone interaction. Mater Res Lett. 2020;9:1–31.
- Yang MX, Pan Y, Yuan FP, et al. Back stress strengthening and strain hardening in gradient structure. Mater Res Lett. 2016;4:145–151.
- Dickson JI, Boutin J, Handfield L. A comparison of two simple methods for measuring cyclic internal and effective stresses. Mater Sci Eng. 1984;64:L7–L11.
- Chrominski W, Lewandowska M. The importance of microstructural heterogeneities in the work hardening of ultrafine-grained aluminum, studied by in-situ TEM straining and mechanical tests. Mater Sci Eng A. 2019;764:138200.
- Yasnikov IS, Kaneko Y, Uchida M, et al. The grain size effect on strain hardening and necking instability revisited from the dislocation density evolution approach. Mater Sci Eng A. 2022;831:142330.
- Wang BB, Xie GM, Wu LH, et al. Grain size effect on tensile deformation behaviors of pure aluminum. Mater Sci Eng A. 2021;820:141504.