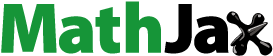
Abstract
Laser powder bed fusion (LPBF) is an additive manufacturing technology for metals. Ti-6Al-4V (Ti64) is a frequently used material for LPBF, but as-built LPBF-Ti64 has poor ductility that limits its usage. Herein, we study how the Al content will affect the microstructure and mechanical properties of LPBF Ti-xAL-4 V alloys (x = 4, 6, 8, wt.%). The materials’ strength increases with Al%. Both Ti-4Al-4V (Ti44) and Ti-8Al-4V (Ti84) alloys exhibit higher work hardening and uniform elongation values than Ti64. This outcome is attributed to activation of multiple slip modes in Ti44 and a more heterogeneous microstructure in Ti84.
GRAPHICAL ABSTRACT

IMPACT STATEMENT
This paper reports that work hardening and uniform elongation values of LPBF Ti-xAl-4 V alloys do not monotonically change with the Al content. Instead, the conventional Ti-6Al-4V exhibits the least values.
1. Introduction
Laser Powder Bed Fusion (LPBF) is an additive manufacturing technology for making metal components [Citation1,Citation2]. It uses a fine laser beam to selectively fuse regions of a metal powder bed to build the component layer-by-layer. LPBF Ti-6Al-4V (Ti64) features a hierarchical structure of acicular martensitic α’ needles within columnar prior-β grains [Citation3], which is drastically different from the two-phase α+β microstructure (fully lamellar, bi-modal, or fully equiaxed) typically found in this commercial alloy. Compared to Ti64 by traditional manufacturing processes (e.g. rolling, forging, etc.), LPBF Ti64 usually exhibits lower work hardening and ductility [Citation4–6]. These issues significantly limit the usage of LPBF Ti64 in the aerospace industry (the biggest consumer of titanium), which has stringent safety standards.
Post-processing heat treatment can increase the ductility of LPBF Ti64, during which the brittle α’ phase will decompose into a two-phase α+β microstructure [Citation4–8]. However, heat treatment increases the overall processing time and cost. Designing new titanium alloy compositions specifically for LPBF is a more challenging but also more rewarding strategy. Zhang et al. [Citation9] showed that, powders from partial homogenization of Ti-6Al-4V and a small amount of 316L stainless steel melts can be used for LPBF processing, and the as-built material exhibits both high work hardening and high ductility. Recently, we reported that the microstructure and mechanical properties of LPBF titanium alloys can be engineered by adjusting the aluminum (Al) content in Ti-Al-V alloys [Citation10].
In the present work, we further study the effect of Al content on the microstructure and mechanical properties of LPBF Ti alloys. Ti-xAl-4 V alloys (x = 4, 6, 8, wt.%) were fabricated using pre-alloyed powders under the same LPBF building parameters. The alloys’ strength increases with the Al content. Interestingly, both Ti44 and Ti84 exhibit higher work hardening and uniform elongation values than Ti64. This outcome can be attributed to the activation of multiple slip modes in Ti44 and a more heterogenous microstructure in Ti84, respectively.
2. Materials and methods
Pure Ti (99.9%), pure Al (99.9%), and an Al-58wt.% V master alloy were melted in a vacuum arc remelting (VAR) furnace to fabricate cast billets with nominal compositions of Ti-4Al-4V, Ti-6Al-4V, and Ti-8Al-4V (wt.%). The billets were forged and machined to produce a cylindrical rod with a diameter of 50 mm. The rods were atomized into powders using an ALD EIGA 50–500 equipment. All three types of powders were sieved to have diameters ranging from 15 μm to 53 μm. Powders of each alloy were loaded into an EOSINT M280 machine for LPBF processing with the following building parameters: laser power = 280 W, scan speed = 1200 mm/s, hatch spacing = 140 μm, layer thickness = 30 μm, and substrate preheating temperature = 100 °C. The scan path was rotated by 67° between each layer. For each alloy, bulk bars with the dimension of 12 × 12 × 80 mm3 were built, whose longitudinal axes were parallel to the building direction (BD). The chemical compositions of the as-built Ti44, Ti64, and Ti84 bars were measured by inductively coupled plasma atomic emission spectroscopy (ICP-AES) and shown in .
Table 1. Chemical compositions (wt%) of the as-built Ti44, Ti64, and Ti84 bars.
X-ray diffraction (XRD, step size = 0.02°, Mini Flex 600) was performed for phase identification. Electron backscatter diffraction (EBSD) were taken using a TESCAN GAIA3 scanning electron microscope (SEM) equipped with the HKL Channel 5 EBSD system (Oxford Instruments). The EBSD data was analyzed using the OIMTM 8.1 software (EDAX, Inc.) and an associated MATLAB plugin MTEX (Version 5.60). We further used a Talos F200X G2 transmission electron microscope (TEM) to characterize the finer microstructure.
Flat dog-bone tensile specimens with the gauge dimensions of 18 mm (Length) × 3.4 mm (Width) ×2.0 mm (Thickness) were extracted from the Ti44, Ti64 and Ti84 bars, respectively. Tensile tests were performed on a Zwick-100 kN instrument equipped with an extensometer at the strain rate of 1.0 × 10−4 s−1. Three Ti44 specimens, two Ti64 specimens, and three Ti84 specimens were tested. Loading-unloading-reloading (LUR) tests were additionally performed on an Instron 5982 machine with a video extensometer at a strain rate of 1.0 × 10−4 s−1. During the LUR tests, specimens were unloaded under load control at various strains to 20N and then reloaded under displacement control at a strain rate of 1.0 × 10−4 s−1 to produce stress–strain hysteresis loops.
3. Results
3.1. Phase identification
shows the XRD profiles of the three alloys in the as-built state. Each material shows α′ peaks only. Ti3Al precipitates are often observed in titanium alloys with Al > 6 wt% by conventional manufacturing processes [Citation11,Citation12]. Nevertheless, no Ti3Al peaks are observed in LPBF Ti84, likely because of the ultra-high solidification speed. From the XRD profiles, lattice parameters and the c/a ratios of these three alloys are estimated: Ti44, a = 2.933 Å, c = 4.673 Å, c/a = 1.593; Ti64, a = 2.930 Å, c = 4.670 Å, c/a = 1.594; Ti84, a = 2.926 Å, c = 4.670 Å, c/a = 1.596. This result agrees with previous studies that reported the c/a ratios of Ti-Al alloys increasing with the Al content [Citation11].
3.2. Microstructure of LPBF-Ti alloys
(b) shows the EBSD maps of as-built Ti44, Ti64 and Ti84 alloys. All three alloys consist of α’ laths. The α’ laths were formed due to the martensitic transformation of the prior-β grains during the rapid cooling in LPBF. We reconstructed the prior-β grains from the crystal orientations of the α’ laths using the MTEX code [Citation13], and the reconstruction results are shown in (a). The prior-β grains in Ti64 and Ti84 are large and columnar. The prior-β grains in Ti44, however, are apparently smaller and more equiaxed. Using the Image-Pro Plus software, the average widths of prior-β grains in Ti44, Ti64, and Ti84 are 33 ± 25 μm, 49 ± 32 μm, and 124 ± 23 μm, respectively.
Figure 2. Comparison of the microstructures in as-built Ti44, Ti64, and Ti84. (a) Reconstructed prior-β grains from the (b) EBSD inverse pole figure maps of α’ laths. (c) Magnified images of the black boxes in (b). (d) Width distributions of the primary α’ lath in the three alloys.
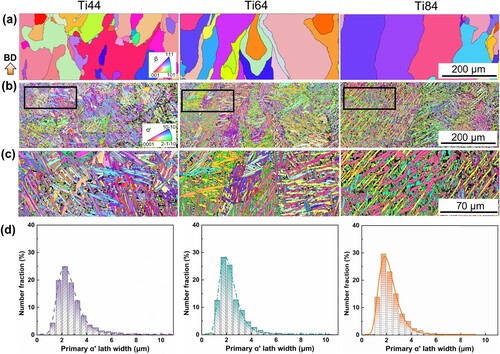
(c) shows magnified images of the black boxes in (b). The lenticular α’ laths are called primary α’ [Citation14]. We measured the widths (d) of indexed primary α’ laths in Ti44, Ti64, and Ti84 alloys, and their distributions are shown in (d). The width distributions can be fitted by a lognormal function: , where A, B, and C are constants. From the fitting, the average widths of primary α’ laths in Ti44, Ti64, and Ti84 are 2.8 ± 1.3 μm, 2.4 ± 1.0 μm, and 2.3 ± 0.9 μm, respectively.
It is known that LPBF titanium alloys often consist of a hierarchical martensitic microstructure [Citation14]. Figure (a-c) shows bright field TEM images of Ti44, Ti64, and Ti84. At this scale, Ti44 shows sub-micron α’ laths, which are called secondary α’. Ti64 and Ti84 also have secondary α’, but finer α’ laths (i.e. ternary α’) are also present in their microstructures. The average widths of secondary/ternary α’ laths in Ti44, Ti64, and Ti84 are 0.40 ± 0.29 μm, 0.30 ± 0.24 μm, and 0.21 ± 0.22 μm, respectively. We use a value of 0.40 μm to distinguish between secondary and ternary α’ laths. (d-f) show the width distributions of secondary/ternary α’ laths in the three alloys. The area fractions of secondary α’ laths (fsec) in Ti64 and Ti84 are measured to be 72% and 52%, respectively. The secondary α’ laths in Ti84 are constrained by ternary α’ laths. (g-i) illustrates the difference in the microstructures of Ti44, Ti64 and Ti84.
3.3. Tensile properties
shows the tensile stress–strain curves of the three as-built materials. From the curves, the yield strength (YS), ultimate tensile strength (UTS), uniform elongation (εu), fracture elongation (εf), and work hardening exponent (n) values are summarized in . n is defined by the Hollomon’s equation: [Citation15], where σ and ε are true stress and true strain values.
Figure 4. Tensile properties of the three materials. (a, b) Stress-strain curves of Ti44, Ti64, and Ti84 specimens. (c) Work hardening rates in the three alloys. (d) Comparing the YS and uniform elongation values of Ti44, Ti64, and Ti84 with other as-built LPBF Ti64 in the literature [Citation3,Citation10,Citation16–22].
![Figure 4. Tensile properties of the three materials. (a, b) Stress-strain curves of Ti44, Ti64, and Ti84 specimens. (c) Work hardening rates in the three alloys. (d) Comparing the YS and uniform elongation values of Ti44, Ti64, and Ti84 with other as-built LPBF Ti64 in the literature [Citation3,Citation10,Citation16–22].](/cms/asset/94ab4740-442d-4e9e-98e7-88c04c401571/tmrl_a_2165418_f0004_oc.jpg)
Table 2. UTS, YS, εu, εf, and n values for Ti44, Ti64, and Ti84.
The three alloys’ YS increases while their εf decreases with the Al content. Notably, both Ti44 and Ti84 exhibit higher εu and n than Ti64. The higher work hardening in Ti44 and Ti84 delays the necking of these specimens,causing higher εu. (d) compares the YS and uniform elongation values of Ti44, Ti64, and Ti84 with other as-built LPBF Ti64 in the literature. With a higher Al%, Ti84 exhibits a simultaneous increase in strength and uniform elongation compared to regular LPBF Ti64.
4. Discussion
From the limited number of tensile specimens in , both Ti44 and Ti84 exhibit higher work hardening and uniform elongation values than Ti64. In our previous study, we have shown that LPBF Ti44 has a smaller CRSSprism/CRSSbasal ratio (∼1.19) than that in LPBF Ti64 (∼1.33) [Citation10]. Therefore, Ti44 is more likely to activate both basal and prismatic slips during plastic deformation, which enhances its work hardening and uniform elongation. Ti44 and Ti64 show a typical trade-off between strength and ductility.
A more interesting result is that Ti84 exhibits a simultaneous increase in strength and uniform elongation compared to Ti64. Indeed, the average εu of Ti84 (4.1 ± 0.05%) is only slightly higher than that of Ti64 (3.7 ± 0.03%), but this difference is still important, given the small standard deviation values. As a substitutional solute, the addition of Al increases the CRSS of both basal and prismatic slip, but the strengthening effect on prismatic slip is much more significant than on basal slip [Citation23]. Therefore, we presume that the CRSSprism/CRSSbasal ratio in Ti84 will be larger than that in Ti64, making basal slip even more dominant in Ti84. So, instead of the activation of multiple slip modes, the higher work hardening and uniform elongation in Ti84 than those in Ti64 must be attributed to other reasons. Both Ti64 and Ti84 exhibit heterogeneous microstructure, featured by a mixture of secondary and ternary α’ laths. During the deformation of such materials, plastic deformation occurs first in the soft zones (i.e. secondary α’) while the hard zones (i.e. fine grains) are less deformed. To accommodate the strain gradient, in front of the interface between soft and hard zones, geometrically necessary dislocations (GNDs) are accumulated. Those GNDs will exert a long-range back stress in soft zones and a forward stress in hard zones [Citation24–27]. The former allows soft zones to sustain the higher applied stress, while the latter increases the stress in hard zones to attenuate the strain incompatibility. Their cooperative action produces hetero-deformation induced (HDI) hardening, which is responsible for the enhanced work hardening and ductility of various heterostructured materials [Citation28,Citation29].
Previous studies indicate that HDI hardening depends on the size, geometry, and distribution of the heterogenous zones [Citation24]. For instance, Wu et.al [Citation27] developed a pure Ti sheet by asymmetrical rolling and partial recrystallization annealing to obtain a heterogeneous lamella structure: coarse, elongated grains with a volume fraction of ∼25% were fully constraint by un-recrystallized ultra fine grains. This microstructure produces strong HDI hardening, so that the Ti sheet exhibits both high ductility and high strength. It was proposed that two structural features are important for HDI hardening: (1) a relatively low volume fraction of the soft zones (about 20∼30%), and (2) complete constraint of the soft zones (e.g. coarse grains) by the hard zones (e.g. fine grains).
From , volume fractions of secondary α′ laths in Ti84 and Ti64 are 52% and 72%, respectively. As shown in , secondary α′ laths in Ti84 are almost completely constrained by ternary α′ laths, while secondary α′ laths in Ti64 are less constrained. In this sense, the microstructure in Ti84 will lead to stronger HDI hardening than Ti64.
To corroborate the above theory, LUR tests were conducted to assess the HDI hardening in Ti44, Ti64, and Ti84. The results are shown in . The hysteresis loops (i.e. Bauschinger effect) in the unloading-reloading curves ((a)) indicate the existence of HDI hardening. (b) compares the shapes of the fourth hysteresis loop in Ti44, Ti64, and Ti84. As Al content increases, the unloading-reloading hysteresis loop becomes wider, suggesting the HDI hardening effect becomes stronger.
Figure 5. (a) Stress-strain curves from the LUR test of Ti44, Ti64, and Ti84. (b) The fourth hysteresis loops in the three alloys. (c) Schematic of calculating the HDI stress. (d) Evolutions of the HDI stress values in Ti44, Ti64, and Ti84.
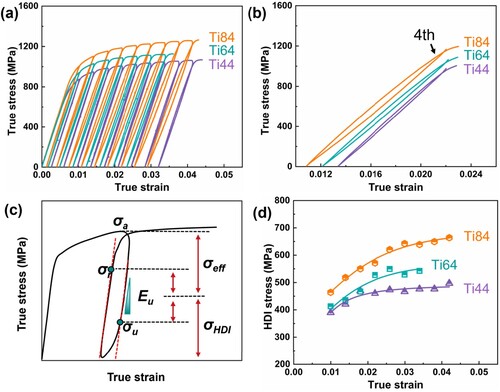
We calculated the HDI stress values (σHDI) in Ti44, Ti64, and Ti84 following the procedure proposed by Yang et al. [Citation30], as schematically shown in (c):
(1)
(1)
where σr is the reload yield stress, σu is the unload yield stress. Here, the slope reduction of effective Young’s modulus (Eu) by 5% is used as the criterion to determine σr and σu [Citation30].
(d) shows the calculated HDI stress values in Ti44, Ti64, and Ti84. Apparently, Ti84 has higher HDI stress values than Ti64 and Ti44, especially in later deformation. The total increase of σHDI in Ti84 is about 198 MPa during the plastic deformation, which is larger than that in Ti64 (≈146 MPa) and in Ti44 (≈95 MPa). This HDI hardening may explain LPBF Ti84 having higher work hardening and uniform elongation than Ti64.
The fracture elongation values in Ti84 are notably lower than Ti64. When both the secondary and ternary α′ laths deformed plastically (i.e. the end of HDI hardening), the lack of non-basal slip in Ti84 would make it difficult to accommodate local stress concentration, so cracks could quickly form to cause fracture. To improve the fracture elongation, it will be necessary to employ strategies such as mid-temperature heat treatment to induce non-basal slip while retain the heterostructure. Further studies are needed to explore that possibility.
5. Conclusions
In this work, we study the effect of Al content on the microstructure and mechanical properties of Ti-xAl-4 V alloys (x = 4, 6, 8, wt.%). The main conclusions are summarized below:
All three alloys contain the α’ phase only. Each alloy exhibits a hierarchical microstructure characterized by prior-β grains, primary α’ laths, and secondary/ternary α’ laths. The area fractions of ternary α’ laths increase with the Al content. The secondary α’ laths in Ti84 are almost fully constrained by ternary α’ laths.
The three alloys’ strength increases with the Al content. Both Ti44 and Ti84 exhibit higher work hardening and uniform elongation values than Ti64. This outcome is attributed to the activation of multiple slip modes in Ti44 and a stronger HDI hardening effect in Ti84.
Acknowledgments
The materials used for this study were fabricated by the Falcontech company. We thank Dr. Zesheng You for the assistance in the LUR tests.
Declaration of interest statement
No potential conflict of interest was reported by the author(s).
Disclosure statement
No potential conflict of interest was reported by the author(s).
Additional information
Funding
References
- DebRoy T, Wei HL, Zuback JS, et al. Additive manufacturing of metallic components - process, structure and properties. Prog Mater Sci. 2018;92:112–224.
- Gu D, Shi X, Poprawe R, et al. Material-structure-performance integrated laser-metal additive manufacturing. Science. 2021;372:1487.
- Vilaro T, Colin C, Bartout JD. As-fabricated and heat-treated microstructures of the Ti-6Al-4V alloy processed by selective laser melting. Metall Mater Trans A. 2011;42:3190–3199.
- Zhang D, Wang L, Zhang H, et al. Effect of heat treatment on the tensile behavior of selective laser melted Ti-6Al-4V by in situ X-ray characterization. Acta Mater. 2020;189:93–104.
- Cao S, Zou Y, Lim CVS, et al. Review of laser powder bed fusion (LPBF) fabricated Ti-6Al-4V: process, post-process treatment, microstructure, and property. Light: Adv Manuf. 2021;2:313–332.
- Liu S, Shin YC. Additive manufacturing of Ti-6Al-4V alloy: a review. Mater Design. 2019;164:107552.
- Li CL, Hong JK, Narayana PL, et al. Realizing superior ductility of selective laser melted Ti-6Al-4V through a multi-step heat treatment. Mater Sci Eng A. 2021;799:140367.
- Cao S, Chu R, Zhou X, et al. Role of martensite decomposition in tensile properties of selective laser melted Ti-6Al-4V. J Alloys Compd. 2018;744:357–363.
- Zhang TL, Huang ZH, Yang T, et al. In situ design of advanced titanium alloy with concentration modulations by additive manufacturing. Science. 2021;374:478–482.
- Wang L, Song Z, Zhang X, et al. Developing ductile and isotropic Ti alloy with tailored composition for laser powder bed fusion. Addit Manuf. 2022;52:102656.
- Fitzner A, Prakash DGL, Fonseca JQD, et al. The effect of aluminium on twinning in binary alpha-titanium. Acta Mater. 2016;103:341–351.
- Radecka A, Bagot PAJ, Martin TL, et al. The formation of ordered clusters in Ti-7Al and Ti-6Al-4V. Acta Mater. 2016;112:141–149.
- Niessen F, Nyyssönen T, Gazder AA, et al. Parent grain reconstruction from partially or fully transformed microstructures in MTEX, 2021. http://arxiv.org/abs/2104.14603.
- Yang J, Yu H, Yin J, et al. Formation and control of martensite in Ti-6Al-4V alloy produced by selective laser melting. Mater Design. 2016;108:308–318.
- Hosford WF. Mechanical behavior of materials. New York: Cambridge University Press; 2005.
- Qiu C, Adkins JEN, Attallah MM. Microstructure and tensile properties of selectively laser-melted and of HIPed laser-melted Ti-6Al-4V. Mater Sci Eng A. 2013;578:230–239.
- Baghi AD, Nafisi S, Hashemi R, et al. Experimental realisation of build orientation effects on the mechanical properties of truly as-built Ti-6Al-4V SLM parts. J Manuf Process. 2021;64:140–152.
- Vrancken B, Thijs L, Kruth JP, et al. Heat treatment of Ti6Al4 V produced by selective laser melting: microstructure and mechanical properties. J Alloys Compd. 2012;541:177–185.
- Kasperovich G, Hausmann J. Improvement of fatigue resistance and ductility of TiAl6V4 processed by selective laser melting. J Mater Process Tech. 2015;220:202–214.
- Voisin T, Calta NP, Khairallah SA, et al. Defects-dictated tensile properties of selective laser melted Ti-6Al-4V. Mater Design. 2018;158:113–126.
- Sun S, Zhang D, Palanisamy S, et al. Mechanical properties and deformation mechanisms of martensitic Ti6Al4 V alloy processed by laser powder bed fusion and water quenching. Mater Sci Eng A. 2022;839:142817.
- Xu W, Brandt M, Sun S, et al. Additive manufacturing of strong and ductile Ti–6Al–4V by selective laser melting via in situ martensite decomposition. Acta Mater. 2015;85:74–84.
- Williams JC, Baggerly RG, Paton NE. Deformation behavior of HCP Ti-Al alloy single crystals. Metall Mater Trans A. 2002;33:837–850.
- Zhu YT, Ameyama K, Anderson PM, et al. Heterostructured materials: superior properties from hetero-zone interaction. Mater Res Lett. 2021;9:1–31.
- Wu XL, Zhu YT. Heterogeneous materials: a new class of materials with unprecedented mechanical properties. Mater Res Lett. 2017;5:527–532.
- Fang XT, He GZ, Zheng C, et al. Effect of heterostructure and hetero-deformation induced hardening on the strength and ductility of brass. Acta Mater. 2020;186:644–655.
- Wu XL, Yang MX, Yuan FP, et al. Heterogeneous lamella structure unites ultrafine-grain strength with coarse-grain ductility. Proc Natl Acad Sci USA. 2015;112:14501–14505.
- Zhu Y, Wu X. Perspective on hetero-deformation induced (HDI) hardening and back stress. Mater Res Lett. 2019;7:393–398.
- Zhu YT. Introduction to heterostructured materials: a fast emerging field. Metall Mater Trans A. 2021;52:4715–4726.
- Yang M, Pan Y, Yuan F, et al. Back stress strengthening and strain hardening in gradient structure. Mater Res Lett. 2016;4:145–151.