ABSTRACT
Selective laser melted (SLMed) AlSi10Mg alloys usually fail before necking during tensile tests, which results in inadequate ductility. To overcome this problem, here we introduced Al4C3 nanorods into the primary Al cells of SLMed AlSi10Mg via in-situ chemical reaction. Tensile tests revealed that those in-cell Al4C3 nanorods not only increased the strain-hardening ability of SLMed AlSi10Mg but also delayed the fracture beyond necking. Consequently, 15% of tensile strength increase and 78% of ductility increase were achieved simultaneously. Post-tensile TEM analysis revealed that those in-cell Al4C3 nanorods pinned and accumulated dislocations within cells and thus alleviated stress concentration along cell boundaries.
GRAPHICAL ABSTRACT
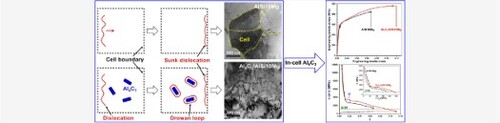
IMPACT STATEMENT
Al4C3 nanorods were introduced into the primary Al cells of selective laser melted AlSi10Mg via in-situ chemical reaction, which enhanced tensile strength and ductility simultaneously.
As an innovative manufacturing technique, selective laser melting (SLM), also known as laser beam melting (LBM) or laser powder bed fusion (LPBF), has drawn extensive attention in multidisciplinary research. Comparing with other additive manufacturing techniques, e.g. electron beam melting and laser metal deposition, SLM is known for its superior printing precision and excellent surface finishing [Citation1], which endues it with an incomparable advantage of near-net-shape forming. This in turn enabled unlimited possibilities with regards to producing complicated and customised components to be used as prototypes or even applied in real world [Citation2].
Up to date, SLM has been employed to fabricate many materials such as steels [Citation3], Ni alloys [Citation4], Ti alloys [Citation5], Mg alloys [Citation6], Al alloys [Citation7] as well as their composites [Citation8]. Within all those metallic alloys, Al alloy is more challenging to be fabricated by SLM. This is mainly attributed to its inherent low density, low fluidity, high thermal conductivity and low laser absorptivity [Citation9]. Beneficial from the high Si content, AlSi10Mg possesses excellent fluidity and castability, which enabled its SLM-processibility over other Al alloys such as AA2024 and AA7075 [Citation10]. As a result, AlSi10Mg is the most extensively investigated Al alloy by SLM [Citation11].
As a conventional cast Al alloy, AlSi10Mg fabricated via die casting process possesses a tensile strength of ∼315 MPa. However, the typical tensile strength of SLMed AlSi10Mg is ∼430 MPa [Citation12], which is about 37% higher than that of casting ones. This is attributed to the unique cellular structure in SLMed AlSi10Mg resulted from the ultra-fast cooling rate of SLM (∼105 K/s [Citation13], ∼1 K/s for sand casting [Citation14], ∼102 K/s for die casting [Citation15]). Such microstructural characteristic induces high strain-hardening rate during the plastic deformation of SLMed AlSi10Mg, resulting in considerable strain hardening to the material [Citation13]. Theoretically, a higher strain-hardening rate would be beneficial to both strength and ductility. However, the SLMed AlSi10Mg fails early before the occurrence of necking phenomenon, which lead to limited ductility (∼6%). Such premature failure was also reported in other alloy systems, which was attributed to stress concentration along microstructural boundaries such as grain/phase boundaries or melting pool boundaries [Citation16,Citation17], and can be remedied by introducing heterogeneous inoculant or intragranular nanophases [Citation18–20]. Herein, we introduced nano-sized graphite into pre-alloyed AlSi10Mg powder via a low energy rocking milling process, which was then used as the feedstock for SLM. Microstructural analysis revealed that the nano-sized graphite reacted with Al during SLM and formed in-situ Al4C3 nanorods within the primary Al cells of SLMed AlSi10Mg. Tensile tests revealed that those in-cell Al4C3 nanorods were capable of alleviating the stress concentration along cell boundaries and preserving the strain-hardening activity beyond the necking point. Our finding may open up a new direction in improving the mechanical properties of SLMed materials.
Pre-alloyed spherical AlSi10Mg powder (15–53 μm in diameter, Xi’an Bright Laser Technologies Co., Ltd, China) was mixed with 0.5 wt.% of nano-sized graphite (∼20 nm in diameter, Jinlei Technology Co., Ltd, China) using a special low energy rocking milling process (RM-05, SEIWA GIKEN Co., Ltd, Japan). Zirconia balls (10 mm in diameter) were used as the milling agent with a ball-to-powder mass ratio of 0.5. The milling process was conducted at a frequency of 60 Hz for 2 h. The as-milled C/AlSi10Mg powder was deposited on an AlSi10Mg substrate without pre-heating using an SLM machine (BLT-S210, Xi’an Bright Laser Technologies Co., Ltd, China) equipped with an ytterbium fiber laser. The wavelength and spot diameter of the laser were 1070 nm and 60 μm, respectively. The SLM parameters were 250 W of laser power, 1100 mm/s of scanning speed, 0.17 mm of hatch spacing and 30 μm of layer thickness. The scanning strategy was strip exposure with a rotation of 67° after each layer. Pure AlSi10Mg without graphite addition was also fabricated using the same SLM parameters as a reference material.
The morphology of powders and microstructure of as-built materials were observed by scanning electron microscopy (SEM, Sigma 300, ZEISS, Germany) equipped with an energy dispersive spectrometer (EDS). Phase identification was realised by X-ray diffraction (XRD, XRD-7000, Shimadzu, Japan) using a Cu Kα radiation source. The grain morphologies of as-built materials were observed using the electron backscattered diffraction (EBSD) technique. The nanoscale microstructure was analyzed by transmission electron microscopy (TEM, Talos F200X, FEI, USA) under different modes including bright field (BF), high-angle annular dark field (HAADF), energy dispersive spectroscopy (EDS) and high-resolution transmission electron microscopy (HRTEM). EBSD samples were prepared by mechanical polishing followed by vibratory polishing using a colloidal silica suspension. TEM samples were prepared using an ion beam milling machine (Model 1050, Fischione, USA). To evaluate the mechanical properties, tensile specimens were machined from as-built materials with the tensile axis perpendicular to the building direction. The gauge dimensions of the tensile specimens were 20 mm in length, 4 mm in width and 2 mm in thickness. Each material was tested for at least three times using a universal mechanical testing machine (INSTRON 3382, Instron, USA) at a constant strain rate of 5 × 10−4 s−1.
Figure (a) shows an SEM image of the as-received nano-sized graphite and Figure (b, c) displays an SEM image of the as-milled C-AlSi10Mg powder and its corresponding C EDS mapping. It can be seen that the low energy rocking milling process employed in this study is effective in dispersing nano-sized graphite on the surface of AlSi10Mg powder. Meanwhile, the spherical morphology of AlSi10Mg powder was maintained, which is essential for the subsequent SLM process [Citation21]. Figure (d) shows the XRD spectra of the as-built materials. Consistent with previous publications [Citation13,Citation22], the XRD spectrum of as-built AlSi10Mg consists peaks corresponding to Al and Si. However, besides peaks for Al and Si, three additional peaks corresponding to Al4C3 are also observable in the XRD spectrum of the AlSi10Mg with nano-sized graphite addition, while no graphite peaks were detected. This indicates that the introduced nano-sized graphite reacted with Al matrix and formed in-situ Al4C3 during fabrication, which could be due to two reasons: high temperature (∼2000 °C) within the molten pool during SLM [Citation23,Citation24]; high reaction tendency between Al and C [Citation25,Citation26]. Figure (e, f) displays EBSD orientation maps of the as-built materials perpendicular to the building direction. It can be found that there are no observable differences between two materials with regards to their grain size, grain orientation, etc.
Figure 1. (a) An SEM image of as-received nano-sized graphite. (b, c) An SEM image showing the morphology of as-milled C/AlSi10Mg powder and its corresponding C EDS mapping. (d) XRD spectra of the as-built materials. (e, f) EBSD orientation maps of the as-built materials perpendicular to the building direction.
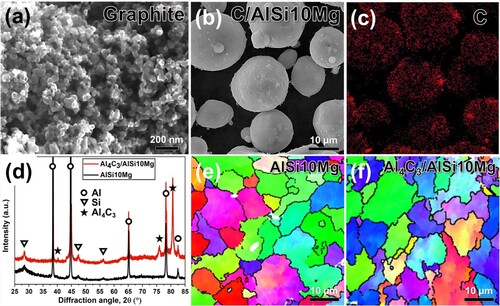
The microstructure of as-built materials was observed using both SEM and TEM. As revealed by the SEM images, SLMed Al4C3/AlSi10Mg (Figure (b)) exhibits a cellular structure, which is similar to SLMed AlSi10Mg (Figure (a)). Figure (c) shows a high magnification TEM image for Al4C3/AlSi10Mg, focusing on an individual cell. Figure (d–f) displays the corresponding EDS mapping for Al, Si and C, respectively. Similar to previous studies on SLMed AlSi10Mg [Citation13,Citation27], the cell in Al4C3/AlSi10Mg is rich in Al and its boundary is made up of alternate Al and Si (Figure (d, e)). It’s worth noting that the C concentration is relatively uniform throughout the area analyzed (Figure (f)), suggesting that there was no obvious nano-sized graphite survived from the SLM process. This is consistent with the XRD analysis results (Figure (d)). On the other hand, HRTEM images (Figure (g, h)) reveal some rod-like phases in Al4C3/AlSi10Mg, as indicated by the arrows in Figure (g). The inset of Figure (h) is a fast Fourier transformation (FFT) image, which verifies that those nanorods are Al4C3, a reaction product of graphite and Al. Figure (i) shows another HRTEM image for the box i in Figure (h). It can be clearly observed that the Al4C3 nanorod is surrounded by Al with the same lattice fringes. Therefore, it can be concluded that the Al4C3 nanorods formed within the primary Al cell, viz. in-cell Al4C3 nanorods. It should be noted that the size of the Al4C3 nanorods formed in this study is extremely small (∼10 nm in length) compared with those (∼200 nm in length) in previous publications [Citation28–30]. This should be attributed to the super-fast cooling rate of SLM (∼105 K/s) [Citation31,Citation32] and beneficial to the tensile properties.
Figure 2. (a, b) SEM images showing the cellular structure of as-built materials. (c) A TEM image of the as-built Al4C3/AlSi10Mg. (d–f) TEM-EDS elemental mapping of (c). (g) A HRTEM image of the as-built Al4C3/AlSi10Mg with arrows indicating the Al4C3 nanorods. (h) A HRTEM image of the boxed area in (g). (i) A HRTEM image of the boxed area in (h).
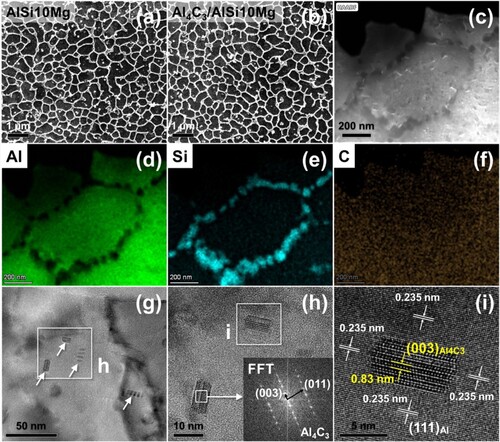
Figure (a) displays the nominal engineering tensile stress–strain curves for both AlSi10Mg and Al4C3/AlSi10Mg, where the points corresponding to 0.2% offset yield strength and ultimate tensile strength (UTS) are marked by squares and circles, respectively. The as-built AlSi10Mg has a UTS of 421 ± 11 MPa and an elongation of 6.7 ± 0.6%. In contrast, the Al4C3/AlSi10Mg possesses a UTS of 482 ± 8 MPa and an elongation of 11.9 ± 1.2%, reflecting 15% of strength increase and 78% of ductility increase. Meanwhile, according to the Hollomon equation [Citation33], the strain-hardening exponent (n, slope of the ln(σ)-ln(ϵ) curve, where σ and ϵ represent true stress and true strain, respectively) for AlSi10Mg and Al4C3/AlSi10Mg was calculated to be 0.237 and 0.256, respectively. Both values are much larger than those of conventional cast Al–Si alloys (∼0.1) [Citation34]. A larger strain-hardening exponent reflects a higher strain-hardening capability. Therefore, SLMed AlSi10Mg alloys exhibit much higher strength compared with cast ones [Citation12,Citation35]. However, the SLMed AlSi10Mg fails before the occurrence of necking phenomenon, which highly restricts its ductility [Citation13]. In comparison, the SLMed Al4C3/AlSi10Mg not only possesses a higher strain-hardening exponent but also reached its theoretical UTS and failed during necking stage. Both factors should be related to the in-cell Al4C3 nanorods introduced.
Figure 3. (a) Engineering tensile stress-strain curves. (b) True tensile stress–strain curves (dashed line) and strain hardening curves (solid lines). Points corresponding to 0.2% offset yield strength and ultimate tensile strength are marked by squares and circles, respectively. The inset of (b) shows strain-hardening rate as a function of the net flow stress (σ-σy), where σy is true yield strength.
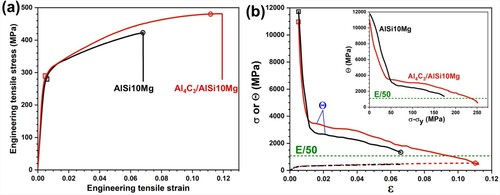
To better understand the effect of Al4C3 nanorods on the strain-hardening behavior of SLMed AlSi10Mg, the strain-hardening rate (Θ, equal to dσ/dϵ) was plotted against true strain (ϵ) in parallel with true stress–strain curves. As shown in Figure (b), after yielding, both materials exhibit rapid Θ decrease followed by slow Θ decrease. This is common to see during tensile deformation of FCC metals [Citation36]. However, for both materials, the overall Θ values are much larger than the upper limit (E/50, where E is Young’s modulus) of strain hardening contributed from dislocations accumulation for FCC metals, which can be also confirmed from the plots of Θ against net flow stress (σ-σy) (inset of Figure (b)). This is attributed to the strengthening effect of Si nanoparticles making up the primary Al cell boundaries (Figure (e)) [Citation13]. In addition, according to the Considère criterion [Citation37], uniform elongation can be maintained as long as Θ is larger than the true stress, viz. dσ/dϵ ≥ σ. In other words, necking occurs when the Θ-ϵ curve and the σ-ϵ curve intersect. Similar to our previous study [Citation13], those two curves for SLMed AlSi10Mg didn’t intersect, indicating an early fracture phenomenon before necking. It’s worth noting that regardless of its higher Θ value in the slow Θ decrease stage, the strain-hardening activity was prolonged in Al4C3/AlSi10Mg and the two curves intersected at ϵ = 11.2%. As a result, simultaneous increase in strength and ductility was achieved.
In general, the additional nano-sized graphite not only increased the Θ value over SLMed AlSi10Mg in its slow decrease stage but also preserved its strain-hardening activity beyond the necking point during tensile deformation. Since there are no observable differences between AlSi10Mg and Al4C3/AlSi10Mg with respect to their texture (Figure (d–f)), grain size (Figure (e, f)) and cell size (Figure (a, b)), the observed differences in mechanical behavior should be attributed solely to the in-cell Al4C3 nanorods introduced. In order to reveal the function of those in-cell Al4C3 nanorods, TEM samples were prepared near the fracture surface of the post-tensile specimen to observe the deformed microstructure. As shown in Figure (c), the dislocations in deformed AlSi10Mg primarily reside along the cell boundaries, while most areas within the cells are absent of dislocations. In comparison, there are much more dislocations distributed uniformly in deformed Al4C3/AlSi10Mg (Figure (f)). It should be noted that even though Al4C3 nanorods are not observable due to their extremely small size and the highly distorted microstructure, based on the cell size in as-built microstructure (Figure (b, c)) and dislocation distribution in deformed microstructure (Figure (f)), one can conclude that plenty of dislocations were introduced into the cells.
Figure 4. A schematic showing the difference of dislocation activity during deformation between (a, b) AlSi10Mg and (d, e) Al4C3/AlSi10Mg. (d, f) Deformed microstructure of AlSi10Mg and Al4C3/AlSi10Mg, respectively.
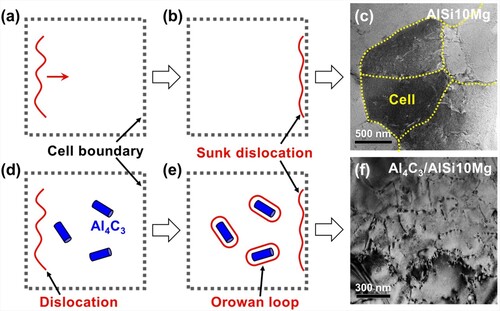
Taking above mentioned into consideration, the effect of in-cell Al4C3 nanorods in the present study can be interpreted as follows. As for SLMed AlSi10Mg, the cells are primarily made up of pure Al atoms (Figure (a)). Therefore, dislocations can easily glide through the cells during tensile deformation and sink along the cell boundaries eventually (Figure (b)). This would result in stress concentration along cell boundaries and lead to premature failure before necking (Figure (b)). As for SLMed Al4C3/AlSi10Mg (Figure (d)), those in-cell Al4C3 nanorods pinned and accumulated dislocations within the cells (Figure (e)), which would not only strengthen the material via Orowan looping mechanism [Citation25] but also alleviate stress concentration along cell boundaries (Figure (f)) and delay early fracture (Figure (b)). Consequently, a simultaneous increase in strength and ductility is achieved (Figure (a)). Similar accomplishments were achieved by others. For example, Liu et al. [Citation19] introduced La2O3 nanoparticles in molybdenum grains via a complex process and improved its strength and ductility simultaneously. Li et al. [Citation20] also developed a nanodispersion-in-nanograins strategy and achieved strength-ductility synergy in both pure Cu and pure Ni. All those results suggest that introducing in-cell/in-grain nano-reinforcement is a promising approach to improving the mechanical properties of metallic alloys.
In order to further reveal the effect of those in-cell Al4C3 nanorods on the tensile properties of SLMed AlSi10Mg, a comparison on tensile properties between this study and those reported in literatures has been made in Figure . As shown by the black symbols within the dotted circle, there are big differences among tensile properties reported in literatures [Citation24,Citation35,Citation38–58], which could be attributed to many reasons, such as laser wavelength and spot diameter, processing parameters, building platform temperature, scanning strategy, etc. The SLMed AlSi10Mg in our study locates at the upper side of the dotted circle, suggesting that a comparable tensile property has been achieved by the present fabrication process. It’s worth noting that with the additional in-cell Al4C3 nanorods, the tensile property improved significantly and is superior to all the SLMed AlSi10Mg in previous publications.
Figure 5. A comparison of tensile properties of SLMed AlSi10Mg [Citation24,Citation35,Citation38–58].
![Figure 5. A comparison of tensile properties of SLMed AlSi10Mg [Citation24,Citation35,Citation38–58].](/cms/asset/402d504f-9bc1-4893-87d3-6011b2bc40e5/tmrl_a_2173028_f0005_oc.jpg)
In summary, this study presented an approach to introducing Al4C3 nanorods within the primary Al cell of SLMed AlSi10Mg via in-situ chemical reaction between nano-sized graphite and Al during SLM. Those in-cell Al4C3 nanorods were only ∼10 nm in size, which could not only increase the strain-hardening rate of SLMed AlSi10Mg in its slow decrease stage but also prolong the strain-hardening activity beyond the necking point during deformation. Consequently, 15% of tensile strength increase and 78% of ductility increase were achieved simultaneously. This study provided an effective strategy to boost the mechanical properties of SLMed AlSi10Mg.
Disclosure statement
No potential conflict of interest was reported by the author(s).
Additional information
Funding
References
- Gu D, Shi X, Poprawe R, et al. Material-structure-performance integrated laser-metal additive manufacturing. Science. 2021;372(6545):1487.
- du Plessis A, Broeckhoven C, Yadroitsava I, et al. Beautiful and functional: A review of biomimetic design in additive manufacturing. Addit Manuf. 2019;27:408–427.
- Li J, Qu H, Bai J. Grain boundary engineering during the laser powder bed fusion of TiC/316L stainless steel composites: New mechanism for forming TiC-induced special grain boundaries. Acta Mater. 2021;226, Article 117605.
- Wu H, Zhang D, Yang B, et al. Microstructural evolution and defect formation in a powder metallurgy nickel-based superalloy processed by selective laser melting. J Mater Sci Technol. 2020;36:7–17.
- Zhao R, Chen C, Shuai S, et al. Enhanced mechanical properties of Ti6Al4 V alloy fabricated by laser additive manufacturing under static magnetic field. Mater Res Lett. 2022;10(8):530–538.
- Liang J, Lei Z, Chen Y, et al. Formability, microstructure, and thermal crack characteristics of selective laser melting of ZK60 magnesium alloy. Mater Sci Eng A. 2022;839:142858.
- Qin Z, Kang N, Zong H, et al. Improved fatigue properties of laser powder bed fusion of Al–4.74Mg–0.70Sc–0.32Zr alloy via hot isostatic pressing. Mater Res Lett. 2022;10(11):720–727.
- Zhou W, Zhou Z, Guo S, et al. Structural evolution mechanism during 3D printing of MXene-reinforced metal matrix composites. Compos Commun. 2022;29
- Aboulkhair NT, Everitt NM, Ashcroft I, et al. Reducing porosity in AlSi10Mg parts processed by selective laser melting. Addit Manuf. 2014;1-4:77–86.
- Tan Q, Zhang J, Sun Q, et al. Inoculation treatment of an additively manufactured 2024 aluminium alloy with titanium nanoparticles. Acta Mater. 2020;196:1–16.
- Fiocchi J, Tuissi A, Biffi CA. Heat treatment of aluminium alloys produced by laser powder bed fusion: A review. Mater Des. 2021;204.
- Zhao L, Song L, Macías JGS, et al. Review on the correlation between microstructure and mechanical performance for laser powder Bed fusion AlSi10Mg. Addit Manuf. 2022;56, Article 102914.
- Chen B, Moon SK, Yao X, et al. Strength and strain hardening of a selective laser melted AlSi10Mg alloy. Scr Mater. 2017;141:45–49.
- Wan J, Qing J, Xu M. Designing a novel graphitic white iron for metal-to-metal wear systems. Metall Mater Trans A. 2019;50(3):1162–1174.
- Yamagata H, Kasprzak W, Aniolek M, et al. The effect of average cooling rates on the microstructure of the Al–20% Si high pressure die casting alloy used for monolithic cylinder blocks. J Mater Process Technol. 2008;203(1-3):333–341.
- Zhao L, Santos Macías JG, Ding L, et al. Damage mechanisms in selective laser melted AlSi10Mg under as built and different post-treatment conditions. Mater Sci Eng A. 2019;764.
- Maconachie T, Leary M, Zhang J, et al. Effect of build orientation on the quasi-static and dynamic response of SLM AlSi10Mg. Mater Sci Eng A. 2020;788.
- Xiao YK, Bian ZY, Wu Y, et al. Effect of nano-TiB2 particles on the anisotropy in an AlSi10Mg alloy processed by selective laser melting. J Alloys Compd. 2019;798:644–655.
- Liu G, Zhang GJ, Jiang F, et al. Nanostructured high-strength molybdenum alloys with unprecedented tensile ductility. Nat Mater. 2013;12(4):344–350.
- Li Z, Zhang Y, Zhang Z, et al. A nanodispersion-in-nanograins strategy for ultra-strong, ductile and stable metal nanocomposites. Nat Commun. 2022;13:1.
- Wang Z, Zhuo L, Yin E, et al. Microstructure evolution and properties of nanoparticulate SiC modified AlSi10Mg alloys. Mater Sci Eng A. 2021;808:140864.
- Li XP, Wang XJ, Saunders M, et al. A selective laser melting and solution heat treatment refined Al–12Si alloy with a controllable ultrafine eutectic microstructure and 25% tensile ductility. Acta Mater. 2015;95:74–82.
- Yin J, Liu W, Cao Y, et al. Rapid prediction of the relationship between processing parameters and molten pool during selective laser melting of cobalt-chromium alloy powder. Simulation and Experiment. J Alloys Compd. 2022;892.
- Wu J, Wang L, An X. Numerical analysis of residual stress evolution of AlSi10Mg manufactured by selective laser melting. Optik (Stuttg). 2017;137:65–78.
- Li X, Zhang Z, Peng Y, et al. In situ synthesized nano-Al4C3 reinforced aluminum matrix composites via friction stir processing. J Mater Res Technol. 2021;14:2658–2664.
- Chen B, Jia L, Li S, et al. In situ synthesized Al4C3 nanorods with excellent strengthening effect in aluminum matrix composites. Adv Eng Mater. 2014;16(8):972–975.
- Albu M, Krisper R, Lammer J, et al. Microstructure evolution during in-situ heating of AlSi10Mg alloy powders and additive manufactured parts. Addit Manuf. 2020;36.
- Jiang Y, Tan Z, Fan G, et al. Reaction-free interface promoting strength-ductility balance in graphene nanosheet/Al composites. Carbon N Y. 2020;158:449–455.
- Han T, Wang F, Li J, et al. Simultaneously enhanced strength and ductility of Al matrix composites through the introduction of intragranular nano-sized graphene nanoplates. Compos Part B Eng. 2021;212:108700.
- Yang L, Han T, Zhang X, et al. Cu Atoms-assisted rapid fabrication of graphene/Al composites with tailored strain-delocalization effect by spark plasma sintering. Mater Res Lett. 2022;10(9):567–574.
- Chen H, Patel S, Vlasea M, et al. Enhanced tensile ductility of an additively manufactured AlSi10Mg alloy by reducing the density of melt pool boundaries. Scr Mater. 2022;221.
- Lam LP, Zhang DQ, Liu ZH, et al. Phase analysis and microstructure characterisation of AlSi10Mg parts produced by Selective Laser Melting. Virtual Phys Prototyp. 2015;10(4):207–215.
- Xu T, Feng Y, Jin Z, et al. Determination of the maximum strain–hardening exponent. Mater Sci Eng A. 2012;550:80–86.
- C/tceres CH, Selling BI. Casting defects and the tensile properties of an A1-Si-Mg alloy. Mater Sci Eng A. 1996;A220:109–116.
- Yan Q, Song B, Shi Y. Comparative study of performance comparison of AlSi10Mg alloy prepared by selective laser melting and casting. J Mater Sci Technol. 2020;41:199–208.
- Kocks UF, Mecking H. Physics and phenomenology of strain hardening: the FCC case. Prog Mater Sci. 2003;48(3):171–273.
- Zhu YT, Wu XL. Ductility and plasticity of nanostructured metals: differences and issues. Mater Today Nano. 2018;2:15–20.
- Kempen K, Thijs L, Van Humbeeck J, et al. Mechanical properties of AlSi10Mg produced by selective laser melting. Phys Proc. 2012;39:439–446.
- Read N, Wang W, Essa K, et al. Selective laser melting of AlSi10Mg alloy: process optimisation and mechanical properties development. Mater Des. 2015;65:417–424.
- Aboulkhair NT, Maskery I, Tuck C, et al. The microstructure and mechanical properties of selectively laser melted AlSi10Mg: the effect of a conventional T6-like heat treatment. Mater Sci Eng A. 2016;667:139–146.
- Li W, Li S, Liu J, et al. Effect of heat treatment on AlSi10Mg alloy fabricated by selective laser melting: microstructure evolution, mechanical properties and fracture mechanism. Mater Sci Eng A. 2016;663:116–125.
- Tradowsky U, White J, Ward RM, et al. Selective laser melting of AlSi10Mg: influence of post-processing on the microstructural and tensile properties development. Mater Des. 2016;105:212–222.
- Takata N, Kodaira H, Sekizawa K, et al. Change in microstructure of selectively laser melted AlSi10Mg alloy with heat treatments. Mater Sci Eng A. 2017;704:218–228.
- Uzan NE, Shneck R, Yeheskel O, et al. Fatigue of AlSi10Mg specimens fabricated by additive manufacturing selective laser melting (AM-SLM). Mater Sci Eng A. 2017;704:229–237.
- Wang L, Jiang X, Guo M, et al. Characterisation of structural properties for AlSi10Mg alloys fabricated by selective laser melting. Mater Sci Technol. 2017;33(18):2274–2282.
- Chen B, Moon SK, Yao X, et al. Comparison study on additive manufacturing (AM) and powder metallurgy (PM) AlSi10Mg alloys. Jom. 2018;70(5):644–649.
- Iturrioz A, Gil E, Petite MM, et al. Selective laser melting of AlSi10Mg alloy: influence of heat treatment condition on mechanical properties and microstructure. Weld World. 2018;62(4):885–892.
- Wang LF, Sun J, Yu XL, et al. Enhancement in mechanical properties of selectively laser-melted AlSi10Mg aluminum alloys by T6-like heat treatment. Mater Sci Eng A. 2018;734:299–310.
- Delahaye J, Tchuindjang JT, Lecomte-Beckers J, et al. Influence of Si precipitates on fracture mechanisms of AlSi10Mg parts processed by selective laser melting. Acta Mater. 2019;175:160–170.
- Girelli L, Tocci M, Gelfi M, et al. Study of heat treatment parameters for additively manufactured AlSi10Mg in comparison with corresponding cast alloy. Mater Sci Eng A. 2019;739:317–328.
- Han Q, Jiao Y. Effect of heat treatment and laser surface remelting on AlSi10Mg alloy fabricated by selective laser melting. Int J Adv Manuf Technol. 2019;102(9-12):3315–3324.
- Wang P, Lei H, Zhu X, et al. Influence of manufacturing geometric defects on the mechanical properties of AlSi10Mg alloy fabricated by selective laser melting. J Alloys Compd. 2019;789:852–859.
- Xiong ZH, Liu SL, Li SF, et al. Role of melt pool boundary condition in determining the mechanical properties of selective laser melting AlSi10Mg alloy. Mater Sci Eng A. 2019;740-741:148–156.
- Zhuo L, Wang Z, Zhang H, et al. Effect of post-process heat treatment on microstructure and properties of selective laser melted AlSi10Mg alloy. Mater Lett. 2019;234:196–200.
- Yang T, Liu T, Liao W, et al. Laser powder bed fusion of AlSi10Mg: Influence of energy intensities on spatter and porosity evolution, microstructure and mechanical properties. J Alloys Compd. 2020;849.
- Zhang H, Wang Y, Wang JJ, et al. Achieving superior mechanical properties of selective laser melted AlSi10Mg via direct aging treatment. J Mater Sci Technol. 2021;108:226–235.
- Ahn SY, Moon J, Choi YT, et al. A precipitation-hardened AlSi10Mg alloy fabricated using selective laser melting. Mater Sci Eng A. 2022;844.
- Chen S, Tan Q, Gao W, Wu G, Fan J, Feng Z, et al. Effect of heat treatment on the anisotropy in mechanical properties of selective laser melted AlSi10Mg. Mater Sci Eng A. 2022;858.