Abstract
Oxide dispersion strengthened tungsten (ODS-W) alloy was prepared by chemical method, conventional sintering and hot-rolling method, which breaks through the research bottleneck of preparing tungsten alloys with excellent comprehensive mechanical properties. More specifically, it can exhibit ultrahigh strength and superior toughness when tested at 200°C. In addition, the nil ductility temperature (NDT) can also dramatically decrease to 100–150°C. The bimodal structure formed by the uneven distribution of yttria and the lamellar structure formed by hot rolling in this ODS-W alloy provide a feasible way to develop other engineering materials with ultra-high strength and ductility.
GRAPHICAL ABSTRACT

IMPACT STATEMENT
W-Y2O3 alloy with bimodal and lamellar structures prepared by wet chemical method and hot rolling process exhibits excellent combination of ultra-high strength and toughness.
Introduction
Among all refractory metal materials, tungsten has the highest melting point (3410 °C). It exhibits high-temperature strength, high thermal conductivity and creep resistance, low thermal expansion coefficient and sputtering rate [Citation1–3]. All of these excellent properties make tungsten very important for high-temperature structural materials, such as plasma-facing materials in future fusion reactors and key components in rockets and missiles [Citation4,Citation5]. However, the high ductile-brittle transition temperature of pure tungsten makes it exhibit inherent brittleness at lower temperatures, limiting the workability of tungsten materials. Meanwhile, the inherent recrystallization brittleness and irradiation brittleness of pure tungsten also cause it to crack prematurely in service. Therefore, it is necessary to take effective measures to improve the ductility or toughness of pure tungsten and tungsten alloys. In recent years, many researchers have been exploring ways to improve the properties of tungsten-based materials. For example, cold-rolled tungsten foil with a thickness of 100 µm has ultrahigh strength and room temperature ductility [Citation6]. Some studies have shown under the combined effect of microalloying and hot rolling, the W-Zr-Y2O3 alloy, which is composed of fine equiaxed sub-grains, elongated parent phase grains and dispersed nano particles, has been strengthened and toughened simultaneously [Citation7]. Recently, a combined hydrothermal and freeze-drying method was proposed to prepare Y2O3@W composite powders. The alloy obtained by low-temperature sintering and subsequent high-energy-rate forging of composite powder has the second phase nanoparticles distributed within the tungsten grains. This special structure makes the alloy ductile even at room temperature [Citation8]. All of the above methods have improved the plasticity of tungsten alloys, but the strength has been sacrificed to a great degree. In addition, they are all small-sized samples, and the possibility of large-scale production has not been explored.
It is well known that the brittle fracture of tungsten alloy mainly occurs at grain boundaries, where impurity elements such as O and N are enriched, and the alloy prepared by traditional powders metallurgy usually exhibits low density and has high angle grain boundaries (HAGBs), then aggravating the tendency of brittle fracture. In comparison, the wet chemical methods can effectively reduce the effects of impurity elements and improve sintering densification [Citation9,Citation10]. Besides, adding rare earth elements (such as Y, La, Hf, etc.) in tungsten-based alloys to form high-temperature stable oxides (Y2O3, La2O3, HfO2, etc.), which can reduce the concentration of O element at grain boundaries [Citation11]. Besides, the hot rolling process can significantly eliminate pores and obtain almost completely dense alloys. In our work, the bulk W-0.5 wt.% Y2O3 (WY) alloy with bimodal structure of small-sized equiaxed grains and elongated parent grains composed of fine sub-grains is prepared by wet chemical method, conventional sintering and hot rolling process. The relative density of this alloy is up to 99.7% (by Archimedes principle), which improves the strength of tungsten grain boundaries. In addition, a large number of low angle grain boundaries (LAGBs) are generated during the preparation process, which not only enables the alloy to maintain high strength, but also to achieve excellent plasticity synergistically.
Experimental methods
The WY alloy was prepared by the co-deposition wet chemical method, conventional sintering and hot-rolling process. Ammonium paratungstate (APT, (NH4)10[H2W12O42]·4H2O, 99.5%) and yttrium nitrate hexahydrate (Y(NO3)3·6H2O, 99.99%) were used as starting materials for preparing composite powder. The specific process of the preparation and reduction of composite powder precursors was mentioned in our previous report [Citation12]. Enough composite powder was provided for subsequent sintering and hot rolling by repeated experiments. Firstly, all reduced powder was pressed by cold isostatic pressing. Under the flowing hydrogen, the temperature was raised to 2200°C at the rate of 5°C min−1, and kept at 2200°C for 6 h in a box furnace. It was then cooled down to room temperature in hydrogen atmosphere. The sintered block was subsequently hot rolled to 2.3 mm (the original thickness was about 19 mm) at 1650°C. The rolled sample was annealed at 1150°C for 30 min. Tensile tests were performed in air on an Instron 5967 machine at a constant strain rate of 2 × 10−4 s−1 with a 25 mm extensometer. Dog-bone tensile specimens were tested along the rolling direction at 100°C to 600°C, and three specimens were tested for each tested condition. The microstructures were characterized by field emission scanning electron microscopy (SEM, Hitachi Model No. S 4800) and transmission electron microscopy (TEM, JEM-2100) equipped with energy-dispersive X-ray spectroscopy (EDX) detectors. Electron Backscatter Diffraction Pattern (EBSD) mappings were collected using a field emission scanning electron microscopy (SEM, JSM-7800F) equipped with a CRYSTAL detector (NordlysMax2) to characterize the microstructure of specimens. The scan step size was set to 0.15 µm, and the critical angle was set to 2° for distinguishable grains. Furthermore, the minimum size identifiable was set to 0.5 µm when counting grains.
Results and discussion
The engineering stress–strain curves of the WY alloy at different temperatures are presented in Figure (a). When tested at 100°C, the sample breaks below the yield stress, which is a typical brittle fracture with an elongation of almost zero. When rises to 150°C, the WY alloys show tensile plasticity and the elongation to failure (EL) increases from 0.6% to 11%, indicating that its NDT is between 100°C and 150°C, which is nearly 100°C lower than that of conventional WY alloys [Citation13]. The ultimate tensile strength (UTS) is also significantly increased to 1170 MPa. It is worth noting that our prepared WY alloy possesses an intriguing combination of ultrahigh UTS of 1.0 GPa and fairly high EL of 26% when tested at 200°C. However, the uniform elongation is only 2.10% indicated by the triangular symbol. The reason is related to the fact that the second phase particles in our WY alloy are mainly distributed at grain boundaries, which will be showed below. In the early stages of loading, the moving dislocations cannot be pinned effectively within the W grain interior, and large stress concentrations can also be introduced by these intergranular particles, leading to microcracks along the grain boundaries and low strain hardening ability of the present WY alloy [Citation8,Citation14]. Inevitably, the EL of WY alloy decreases when the temperature is higher than 200°C. Similar phenomena have also been found in other reports [Citation7,Citation15]. Even so, the present WY alloy also has significantly improved mechanical properties, its UTS is as high as 700 MPa, which is nearly 200 MPa higher than the values in the literature [Citation13–16], and the EL reaches 12% at 600°C, demonstrating that the plasticity of our WY alloy is improved without excessive sacrifice of strength when tested at elevated temperatures. In a word, this combination of wet chemical and hot rolling methods provides the possibility of preparing tungsten-based alloys with excellent mechanical properties and structural stabilities at lower or elevated temperatures.
Figure 1. (a) Tensile engineering stress–strain curves at different temperatures, the insert depicts the size of tensile samples. (b) comparison of strength and ductility between our prepared WY alloy and W foils, deformed pure W or tungsten alloys at 200 °C.
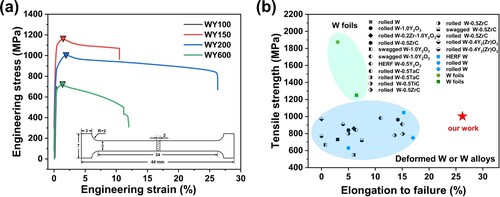
We also compared the mechanical properties of our prepared alloys with those of pure W and W alloys at 200°C. It can be found that the EL of tungsten foil is lower than 5%, and the UTS is up to 1.9 GPa (Figure (b)), which is significantly higher than that of the deformed W or W alloys [Citation17]. However, because of different preparation process and sample size of the W foils, we only compared the mechanical properties of our WY alloy with other deformed oxide [Citation7,Citation8,Citation13,Citation18] or carbide [Citation11,Citation19–24] dispersion strengthened tungsten alloy and pure tungsten [Citation6,Citation25–27] in literature and found that our present WY alloy exhibits excellent strength and outstanding ductility when tested at 200°C, and the EL is nearly 50% higher than the best value [Citation6].
Figure shows the fracture surface morphologies of our prepared WY alloy at different test temperatures. It can be seen that at lower temperatures (100 and 150 °C, Figure (b,c)), there is mainly a combination of intergranular and transgranular cleavage fracture. The intergranular fracture mainly occurs at fine equiaxed grain boundaries (see the red circles in Figure (b)), while the transgranular cleavage fracture occurs within larger grains, accompanied by gradual elongation and deformation of W grains (Figure (c)). This is because during hot rolling process, significant dislocations can be accumulated within the larger elongated grains, which can carry higher plastic strain than fine grains due to its larger strain hardening ability, thus ensuring the high plasticity of the larger grains [Citation28–30]. In addition, the cracks are preferentially distributed along the elongated grain boundaries (indicated in Figure (c)), which will be explained below. For fine grains (submicron), the plasticity is relatively poor due to the lack of dislocation storage capacity when comparing with large grains (tens of microns). However, according to Hall-Petch relationship, for micron and even submicron grains, the finer the grains, the higher the yield strength of the material [Citation31]. Therefore, the bimodal structure consisting of larger elongated grains and fine equiaxed grains can be combined to synergistically strengthen and toughen the alloy. As shown in Figure (a), a lamellar structure along the rolling direction can be formed in our hot-rolled WY alloy, which can cause delamination fracture during the tensile test. Moreover, due to the high strength of our WY alloy (1.0 GPa), the tensile stress state of the material changes from plane-strain conditions to plan-stress conditions, which also provides the external force conditions for delamination fracture. Specifically, the fracture surfaces at 200°C shows that delamination cracks occur across the whole fracture surface (see Figure (d)). This is due to the high stability of the structure within the elongated grains and the relatively low cohesion at the interface, making it the preferential sites for the initiation of the delamination cracks. Furthermore, numerous interfaces can be generated during the delamination process, increasing energy consumption, and the secondary cracks can extend into the grain interior perpendicular to the delamination direction (Figure (d)), which can also blunt the crack tip and thereby increases the fracture toughness of WY alloy [Citation32]. As mentioned above, our prepared WY alloy can achieve unprecedented TE at 200°C, which is closely related to this delamination fracture caused by the lamellar structure, consistent with the recent result reported by Xie et al. [Citation26]. However, as shown in Figure (e), different from the fracture surface at 200°C, ductile avulsion and interface rupture of W grains with the lamellar structure gradually dominate the fracture mode of WY alloy. Thus it follows that the reduced ductility of WY alloy at high-temperature is closely linked to the ductile avulsion and interface rupture of W grains [Citation8]. Moreover, high-temperature could activate dislocation climbing, which can decrease the back stress of pile-ups, increase plastic slip deformation (see the necking in Figure (f), denoted by yellow dotted line), and relieve the stress concentration at the grain boundaries, contributing to the decrease of strength [Citation33,Citation34]. All of these may illuminate why the strength and ductility of WY alloy decrease at 600°C.
Figure 2. (a) The SEM image of hot-rolled WY alloy along RD-ND surface. SEM images of tensile fracture surfaces at (b) 100 °C, (c) 150 °C, (d) 200 °C, (e, f) 600 °C, and (f) is along RD-ND surface. RD, ND denote rolling and normal direction, respectively.
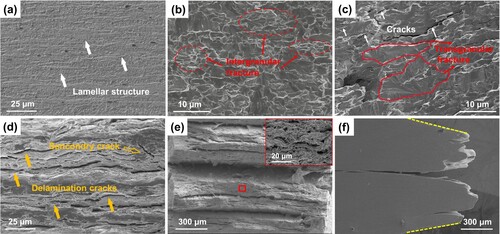
Next, the morphologies of bimodal structure of WY alloy prepared in our work were further analyzed. The grain map along the rolling surface shows that the microstructure exhibits a bimodal structure consisting of larger elongated grains and fine equiaxed grains (Figure (a), denoted by white and black circles, respectively). The larger W grains are significantly elongated parallel to the rolling direction, and the average length and width of the deformed grains are calculated to be 10.77 and 1.87 µm, corresponding to an aspect ratio of about 6/1. The inverse polar figure (IPF) mapping indicates that larger tungsten grains possess a <111> direction (in blue) and fine grains possess a <001> direction (in red) parallel to the rolling direction (Figure (b)). In corresponding grain boundary distribution map (Figure (c,f)), it can be further observed that more than 75% of which are LAGBs (<15°, red and green lines), which are mainly distributed within the elongated parent grains, effectively weakening the anisotropy, and thus inhibiting the initiation and propagation of cracks within the elongated grains. This is the reason why the cracks are preferentially distributed along the elongated grain boundaries, as observed in Figure (b). In contrast, fine equiaxed grain boundaries are mainly composed of HAGBs (blue lines). Taking grain boundaries above 2° and grains larger than 0.5 µm into account, the average grain size is 2.97 µm measured by intercept method (Figure (e)). What’s more, the kernel average misorientation (KAM) map shows the deformation of our prepared WY alloy. The black particles (denoted by arrows) in Figure (b,d) indicate that the second-phase particles mainly distribute in fine grain regions. In areas without second-phase particles, tungsten grains grow into large elongated grains with greater deformation degrees and defect density (see Figure (d)), which further demonstrates that large grains have larger ability to accumulate dislocation and to strain hardening than fine grains.
Figure 3. EBSD characterization of the present WY alloy. (a) grain map, (b) inverse pole figure (IPF) map, (c) image quality (IQ) map with superimposed grain boundaries, (d) kernel average misorientation (KAM) map, (e) grain size distribution and (f) grain boundary misorientation distribution map. TD denote transverse direction. The black particles in the figure indicate the doped second phase.
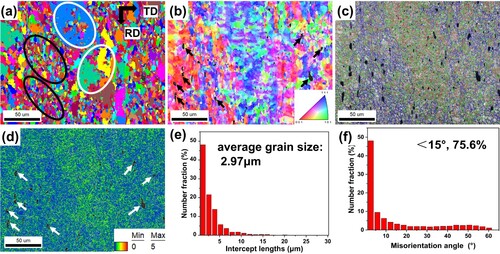
Next, SEM and TEM analysis were performed to characterize the distribution of second-phase particles in WY alloy detailedly. As shown in Figure (a), and almost all second-phase particles are unevenly distributed at tungsten grain boundaries, with an average size of about 1.1um (after counting nearly 500 particles). The concentrated distribution of second-phase particles enables some tungsten grains to maintain fine size because the particles located at the grain boundaries can seriously hinder the migration of tungsten grain boundaries, thereby inhibiting the growth of tungsten grains (yellow circles). On the contrary, due to less impediment, the tungsten grains without second-phase particles are easy to grow up to larger grains [Citation14,Citation35], which can be elongated along the deformation direction during the subsequent hot rolling, as shown by the white circles in Figure (a) and Figure (a). Thus, the uneven distribution of oxide particles produced by wet chemical method leads to the bimodal structure of tungsten grains [Citation36], which is respectively consisted of small-sized equiaxed grains and elongated parent grains composed of fine sub-grains. For plasticity of the alloy, the finer the grains are, the lower the density of impurities and dislocations at grain boundaries are, thus reducing the possibility of crack initiation. More grain boundaries generated by sub-grains will also hinder crack growth, thus delaying the occurrence of fracture and improving the toughness of the alloy [Citation35].
Figure 4. (a) Distribution of oxide particles, the inset is the particle size distribution statistics, (b) EDS spectrum of oxide particles, including W, Y and O elements, (c) TEM image and the corresponding SAED patterns of oxide particle (marked with A) and W matrix (marked with B), (d) HRTEM image of the interface between matrix and particle (yellow circle in c), (e, f) tangled dislocations denoted by red arrows.
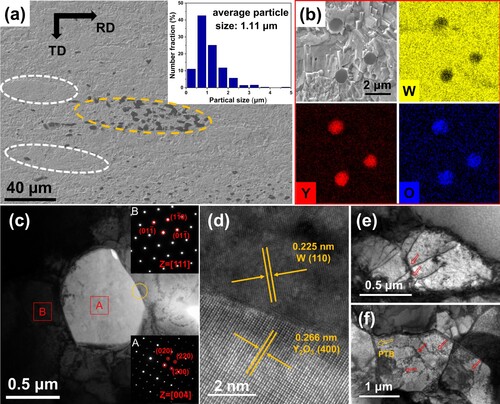
The magnified EDS maps for W, Y, and O indicate that the dark particles are Y2O3 (Figure (b)). And the corresponding selected area electron diffraction (SAED) taken from [111]W zone axis (Figure (c)) are applied to further clarify the phase structure in rolled WY alloy, revealing that the two phases are W-matrix phase with body-centered cubic (bcc) structure and Y2O3 phase with face-centered cubic (fcc) structure. High resolution transmission electron microscope (HRTEM) verifies that the crystal plane spacing of the matrix and particles is 0.225 and 0.266 nm, respectively (Figure (d)), and there is an incoherent interface between these two phases. According to the Powder Diffraction File (PDF) card, the two crystal planes agree well with the theoretical crystal plane spacing values of bcc W (110) and fcc Y2O3 (400), respectively. Continuous plastic deformation will increase the density of dislocations and make them interact with each other, resulting in entangled dislocations and the formation of cell substructures (Figure (e,f)). Furthermore, hot rolling provides a driving force at high-temperatures, so the occurrence of dynamic recovery processes is promoted, and dislocations within cells slide toward the cell wall, finally resulting in a decrease of dislocation density within cells. As the plastic deformation process proceeds, dislocations proliferate and disappear to a balance state, which are mainly distributed at the cell wall. During the whole process, a change from polygonized dislocation walls (PDWs) to a more stable partial transition boundaries (PTBs) occurs, resulting in a distinct sub-grain boundary with equiaxed microstructures (Figure (f)). As mentioned earlier, the deformation of grains during hot rolling will lead to the accumulation of a large number of dislocations in grains. The Y2O3 particles interact with dislocations to form dislocation entanglement, which improves the deformation resistance of W grains. In addition, during the hot rolling process, a large number of LAGBs are generated with the dynamic recovery process, which can block the movement of dislocations, thus improving the strength of the WY alloys.
Conclusions
In summary, a novel strategy has been proposed to improve the mechanical properties of the ODS-W alloy, which is prepared by improved wet chemical method, conventional sintering and hot rolling process. The NDT of our prepared WY alloy was between 100-150°C, much lower than most tungsten alloys reported previously. Moreover, our prepared WY alloy exhibits an excellent combination of strength and toughness, with a UTS of 1.0 GPa and an EL of 26% when tested at 200°C. And at 600°C, the tensile strength of this alloy is still higher than 700 MPa. After conventional sintering and hot rolling of the composite powder prepared by the improved wet chemical method, the inhomogeneous distributions of Y2O3 particles lead to the bimodal grain structure of WY alloy. This bimodal grain structure of small-sized equiaxed grains and elongated coarse parent grains composed of fine sub-grains, along with the lamellar structure contribute to the fascinating balance between strength and toughness of our prepared WY alloy.
Disclosure statement
No potential conflict of interest was reported by the author(s).
Additional information
Funding
References
- Li Z, Chen YB, Wei SZ, et al. Flow behavior and processing map for hot deformation of W-1.5ZrO2 alloy. J Alloy Compd. 2019;802:118–128. doi:10.1016/j.jallcom.2019.06.179.
- Yu M, Wang K, Zan X, et al. Hardness loss and microstructure evolution of 90% hot-rolled pure tungsten at 1200–1350°C. Fusion Eng Des. 2017;125:531–536. doi:10.1016/j.fusengdes.2017.05.072.
- Huang L, Jiang L, Topping TD, et al. In situ oxide dispersion strengthened tungsten alloys with high compressive strength and high strain-to-failure. Acta Mater. 2017;122:19–31. doi:10.1016/j.actamat.2016.09.034.
- Richter A, Anwand W, Chen C-L, et al. Evaluation of defect formation in helium irradiated Y2O3 doped W-Ti alloys by positron annihilation and nanoindentation. J Nucl Mater. 2017;494:294–302. doi:10.1016/j.jnucmat.2017.07.039.
- Lee KH, Cha SI, Ryu HJ, et al. Effect of two-stage sintering process on microstructure and mechanical properties of ODS tungsten heavy alloy. Mater Sci Eng A. 2007;458(1-2):323–329. doi:10.1016/j.msea.2007.01.118.
- Nogami S, Hasegawa A, Fukuda M, et al. Tungsten modified by potassium doping and rhenium addition for fusion reactor applications. Fusion Eng Des. 2020;152:114214. doi:10.1016/j.fusengdes.2019.111445.
- Xie ZM, Liu R, Zhang T, et al. Achieving high strength/ductility in bulk W-Zr-Y2O3 alloy plate with hybrid microstructure. Mater Design. 2016;107:144–152. doi:10.1016/j.matdes.2016.06.012.
- Dong Z, Ma ZQ, Yu LM, et al. Achieving high strength and ductility in ODS-W alloy by employing oxide@W core-shell nanopowder as precursor. Nat Commun. 2021;12(1):5052. doi:10.1038/s41467-021-25283-2.
- Hu WQ, Dong Z, Yu LM, et al. Synthesis of W-Y2O3 alloys by freeze-drying and subsequent low temperature sintering: Microstructure refinement and second phase particles regulation. J Mater Sci Technol. 2020;36:84–90. doi:10.1016/j.jmst.2019.08.010.
- Dong Z, Ma ZQ, Liu YC. Accelerated sintering of high-performance oxide dispersion strengthened alloy at low temperature. Acta Mater. 2021;220:117309. doi:10.1016/j.actamat.2021.117309.
- Miao S, Xie ZM, Zeng LF, et al. Mechanical properties, thermal stability and microstructure of fine-grained W-0.5 wt.% TaC alloys fabricated by an optimized multi-step process. Nucl Mater Energy. 2017;13:12–20. doi:10.1016/j.nme.2017.09.002.
- Dong Z, Liu N, Hu WQ, et al. Controlled synthesis of high-quality W-Y2O3 composite powder precursor by ascertaining the synthesis mechanism behind the wet chemical method. J Mater Sci Technol. 2020;36:118–127. doi:10.1016/j.jmst.2019.05.067.
- Xie ZM, Liu R, Miao S, et al. Effect of high temperature swaging and annealing on the mechanical properties and thermal conductivity of W-Y2O3. J Nucl Mater. 2015;464:193–199. doi:10.1016/j.jnucmat.2015.04.050.
- Liu G, Zhang GJ, Jiang F, et al. Nanostructured high-strength molybdenum alloys with unprecedented tensile ductility. Nat Mater. 2013;12(4):344–350. doi:10.1038/NMAT3544.
- Lian YY, Liu X, Feng F, et al. Mechanical properties and thermal shock performance of W-Y2O3 composite prepared by high-energy-rate forging. Phys Scripta. 2017;T170:014044. doi:10.1088/1402-4896/aa8f2d.
- Tan XY, Luo LM, Chen HY, et al. Mechanical properties and microstructural change of W-Y2O3 alloy under helium irradiation. Sci Rep. 2015;5:12755. doi:10.1038/srep12755.
- Bonk S, Hoffmann J, Hoffmann A, et al. Cold rolled tungsten (W) plates and foils: Evolution of the tensile properties and their indication towards deformation mechanisms. Int J Refract Met Hard Mater. 2018;70:124–133. doi:10.1016/j.ijrmhm.2017.09.007.
- Zhao ZH, Yao G, Luo LM, et al. Tensile fracture behavior and texture evolution of a hot-rolled W-Y2(Zr)O3 alloy. J Nucl Mater. 2021;554:153080. doi:10.1016/j.jnucmat.2021.153080.
- Xie ZM, Liu R, Miao S, et al. Extraordinary high ductility/strength of the interface designed bulk W-ZrC alloy plate at relatively low temperature. Sci Rep. 2015;5:16014. doi:10.1038/srep16014.
- Miao S, Xie ZM, Zhang T, et al. Mechanical properties and thermal stability of rolled W-0.5wt% TiC alloys. Mater Sci Eng A. 2016;671:87–95. doi:10.1016/j.msea.2016.06.049.
- Xie ZM, Miao S, Liu R, et al. Recrystallization and thermal shock fatigue resistance of nanoscale ZrC dispersion strengthened W alloys as plasma-facing components in fusion devices. J Nucl Mater. 2017;496:41–53. doi:10.1016/j.jnucmat.2017.09.022.
- Liu R, Xie ZM, Yang JF, et al. Recent progress on the R&D of W-ZrC alloys for plasma facing components in fusion devices. Nucl Mater Energy. 2018;16:191–206. doi:10.1016/j.nme.2018.07.002.
- Yin C, Terentyev D, Pardoen T, et al. Tensile properties of baseline and advanced tungsten grades for fusion applications. Int J Refract Met Hard Mater. 2018;75:153–162. doi:10.1016/j.ijrmhm.2018.04.003.
- Miao S, Xie ZM, Yang XD, et al. Effect of hot rolling and annealing on the mechanical properties and thermal conductivity of W-0.5wt.% TaC alloys. Int J Refract Met Hard Mater. 2016;56:8–17. doi:10.1016/j.ijrmhm.2015.12.004.
- Shen TL, Dai Y, Lee Y. Microstructure and tensile properties of tungsten at elevated temperatures. J Nucl Mater. 2016;468:348–354. doi:10.1016/j.jnucmat.2015.09.057.
- Xie XF, Xie ZM, Liu R, et al. Hierarchical microstructures enabled excellent low-temperature strength-ductility synergy in bulk pure tungsten. Acta Mater. 2022;228:117765. doi:10.1016/j.actamat.2022.117765.
- Deng HW, Xie ZM, Wang YK, et al. Mechanical properties and thermal stability of pure W and W-0.5 wt%ZrC alloy manufactured with the same technology. Mater Sci Eng A. 2018;715:117–125. doi:10.1016/j.msea.2017.12.112.
- Kumar KS, Van Swygenhoven H, Suresh S. Mechanical behavior of nanocrystalline metals and alloys. Acta Mater. 2003;51(19):5743–5774. doi:10.1016/j.actamat.2003.08.032.
- Ma E. Eight routes to improve the tensile ductility of bulk nanostructured metals and alloys. JOM. 2006;58(4):49–53. doi:10.1007/s11837-006-0215-5.
- Feng F, Wang JB, Lian YY, et al. Achieving low-temperature tensile ductility in a swaged W-Y2O3 alloy. Mater Sci Eng A. 2022;857:144109. doi:10.1016/j.msea.2022.144109.
- Hansen N. Boundary strengthening in undeformed and deformed polycrystals. Mater Sci Eng A. 2005;409(1-2):39–45. doi:10.1016/j.msea.2005.04.061.
- Liu L, Yu Q, Wang Z, et al. Making ultrastrong steel tough by grain-boundary delamination. Science. 2020;368:1347–1352. doi:10.1126/science.aba9413.
- Huang MS, Li ZH, Tong J. The influence of dislocation climb on the mechanical behavior of polycrystals and grain size effect at elevated temperature. Int J Plasticity. 2014;61:112–127. doi:10.1016/j.ijplas.2014.06.002.
- Ayas C, van Dommelen JAW, Deshpande VS. Climb-enabled discrete dislocation plasticity. J Mech Phys Solids. 2014;62:113–136. doi:10.1016/j.jmps.2013.09.019.
- Wang CJ, Huang H, Wei SZ, et al. Strengthening mechanism and effect of Al2O3 particle on high-temperature tensile properties and microstructure evolution of W-Al2O3 alloys. Mater Sci Eng A. 2022;835:142678. doi:10.1016/j.msea.2022.142678.
- Liu N, Dong Z, Ma Z, et al. Eliminating bimodal structures of W-Y2O3 composite nanopowders synthesized by wet chemical method via controlling reaction conditions. J Alloy Compd. 2019;774:122–128. doi:10.1016/j.jallcom.2018.09.310.