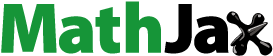
Abstract
A Mg-6Li-3Al-1Sn (LAT631) alloy with a bimodal-grained structure was prepared via hot extrusion, followed by room temperature rotary swaging (RTRS). The as-extruded LAT631 alloy undergoes dynamical recrystallization, and massive twins are introduced during RTRS. Especially, Al segregation is generated with massive Al solutes surrounding Sn-rich particles via RTRS. Introducing twins and Al-rich segregation are critical factors for enhancing strength, and the increased proportion of DRXed grains is beneficial to improving the elongation in RSed alloy. This research demonstrates that strategic control of recrystallization and segregation by rotary swaging provides an innovative approach to optimizing the mechanical properties of Mg-Li alloys.
IMPACT STATEMENT
This paper proposes a potential solution of Al segregation combined with precipitates for optimizing mechanical properties in ultra-light bulk Mg-Li alloys.
Mg alloys as the lightest metallic structure materials, have drawn great attention due to their low density, high plasticity, good specific strength, high specific stiffness, etc. [Citation1–4]. Moreover, it is widely accepted that the development of Mg-Li alloys can effectively promote the lightweight process in the aerospace, weapon industries and 3C et al. [Citation5]. However, Mg-Li alloys still have critical issues, such as the difficulty in balancing the ultra-lightness and high strength, over-aging, relatively poor stability and poor high-temperature resistance, which significantly limit the engineering applications of Mg-Li alloys. Recently, many strategies for the strengthening of Mg-Li alloys have been promoted, such as alloying, deformation, heat treatment and composite [Citation6, Citation7]. For instance, Wu et al. [Citation8] prepared a dual phase Mg-9Li-3Al-1Zn alloy by solution treatment, rolling and aging. After rolling, the ultimate tensile strength (UTS) and elongation (EL) of the as-rolled Mg-9Li-3Al-1Zn alloy were 293 MPa and 9.2%. Besides, our previous study [Citation9] indicated that adding Al and Sn elements strengthens Mg-Li alloy via traditional extrusion, resulting in the UTS of 324 MPa and EL of 11.9%. In addition, Bian et al. [Citation10] investigated the effect of equal channel angular pressing (ECAP) on the microstructure evolution and mechanical properties of dual-phase Mg-Li alloy. They indicated that coarse AlLi and Mg2Si phases constituent particles were broken and accelerated the refinement and uniform redistribution of α-Mg dendrites during ECAP, resulting in the formation of small blocky α-Mg grains, which is beneficial for the increase of mechanical properties. Although plastic deformation such as extrusion, rolling and even ECAP efficiently enhance the strength and improve the microstructure of Mg-Li alloys, the comprehensive mechanical properties of Mg-Li alloys still need further improvement to overcome the barrier to their broader applications.
Rotary swaging (RS) is a widely used industrial method to produce metal bars and wires, which can improve the mechanical properties of metallic materials during the process [Citation11, Citation12]. The RS process forges the alloy bar via the high-frequency radial reciprocating motion of the die, with the alloy bar rotating and moving axially. As a result, the RSed bar bears radial compression and length extension deformation by swaging the die. By RS, many types of nanostructures can be introduced into Mg alloys, such as nanoscale precipitates, stacking faults, nano-grains, etc. [Citation13–15], effectively enhancing the mechanical properties. Yang et al. [Citation14] reported that massive stacking faults and twins were introduced in a Mg-4Li-3Al-3Zn alloy by multi-pass low-strain RS, leading to an ultra-high UTS of 405 MPa and a moderate EL of 5%, respectively. Natalia Martynenko et al. [Citation16] investigated the effect of three deformation methods (ECAP, RS and multiaxial deformation) on the microstructure and mechanical properties of Mg-Y-Nd-Zr alloys, and the RSed alloy exhibited a higher UTS of 416 MPa compared to other processes, whereas the plasticity decreased to ∼7.9%. Moreover, Liu et al. [Citation17] reported that rare earth elements segregated along nanocrystalline grain boundaries after RS and aging, which enhanced the blocking effect of grain boundaries and increased the critical stress required for the dislocation slipping and transferring across. Notwithstanding the attempts to improve the mechanical properties of Mg alloys by RS, an optimized combination of strength and plasticity is still hard to achieve. In addition, a review of published literature shows that the effect of rotary swaging on the mechanical properties of Mg-Li alloys still needs further investigation. Since Mg-Li alloys are sensitive to temperature, high deformation temperature tends to induce grain coarsening and degradation of mechanical properties [Citation18]. Therefore, we prepared Mg-Li-Al-Sn alloy and utilized a multi-pass RTRS process with low strain to investigate the mechanical properties and microstructure evolution induced by rotary swaging deformation in Mg-Li alloy and to achieve the strength-ductility synergy enhancement of Mg-Li alloy, which can provide an effective and controllable design strategy for Mg alloys.
Mg-6Li-3Al-1Sn (LAT631, in wt.%) ingots were prepared by vacuum melting. The as-cast billet with a size of Φ80 mm × 45 mm was heated to 553 K, held 0.5-1 h, and then extruded at 553 K with an extrusion ratio of 28:1. After extrusion, the as-extruded alloy was cooled by water immediately. Then, the extruded bar was further deformed via RS at room temperature without any intermediate annealing. The diameter of the as-extruded LAT631 bar was reduced from 16 mm to 13.2 mm by 12 RS passes with a low strain (0.025-0.03) for each pass. The density of the LAT631 alloy was measured by Archimedes principle in absolute alcohol (purity of 99.7%).
Samples for microstructure observation by an optical microscope (OM, OLYMPUS PMG3) and a scanning electron microscope (SEM, JSM-7800F) were taken from as-cast billet, the longitudinal sections of as-extruded and RSed bars. The phase analysis was carried out by X-ray diffraction (XRD, D/max-2500pc). The samples for transmission electron microscopy (TEM), high-resolution transmission electron microscopy (HRTEM), and high-angle annular dark-field scanning transmission electron microscopy (HAADF-STEM) observations were performed on Talos F200S or FEI Tecnai F30. The JEM-F200 microscope equipped with a Cs corrector and electronic energy loss spectrometer (EELS) was used to characterize the Li element distribution. The tensile specimens with a gauge length of 8 mm and a cross-sectional area of 3 mm × 2 mm were cut from the as-cast, as-extruded and RSed alloys (The sampling position of as-extruded and RSed alloys was cut from the edge position of the alloy bars and samples were machined along the longitudinal direction), and tensile tests were conducted using a universal testing machine (UTM4104) with a strain rate of 110−3 s−1.
Figure shows the mechanical properties of LAT631 alloys in different processing conditions. The yield strength (YS), UTS and EL of the as-cast alloy were 88 ± 6.5 MPa, 178 ± 11 MPa and 20.4 ± 2.5%. After extrusion, the YS, UTS and EL of the as-extruded alloy reached 156 ± 7.7 MPa, 259 ± 2.4 MPa and 17.2 ± 1.5%, respectively. The YS, UTS and EL of RSed alloy were 296 ± 6.7 MPa, 356 ± 2.1 MPa and 19.2 ± 1.6%, respectively. Evidentially, the RSed alloy achieved an excellent strength-ductility synergy compared with the as-cast and as-extruded counterparts (Figure b). In addition, it is worthwhile to note that the density of Mg-6Li-3Al-1Sn alloy is only ∼1.591 g/cm3, inferring a super high specific strength of ∼223 kNmkg−1, which is higher than other reported Mg-Li alloys as shown in Figure c.
Figure 1. (a) Engineering stress-strain curves of Mg-6Li-3Al-1Sn alloys in various conditions; (b) Ultimate tensile strength vs. elongation of Mg-Li alloys in different deformation conditions and the currently studied alloys [Citation14, Citation19–26]. (c) Specific strength vs. elongation of Mg-Li alloys and the currently studied alloys [Citation19, Citation21, Citation26–28].
![Figure 1. (a) Engineering stress-strain curves of Mg-6Li-3Al-1Sn alloys in various conditions; (b) Ultimate tensile strength vs. elongation of Mg-Li alloys in different deformation conditions and the currently studied alloys [Citation14, Citation19–26]. (c) Specific strength vs. elongation of Mg-Li alloys and the currently studied alloys [Citation19, Citation21, Citation26–28].](/cms/asset/9580c5da-3d37-43c2-86b7-8a9474cb8eea/tmrl_a_2278589_f0001_oc.jpg)
The OMs and inverse pole figure (IPF) orientation maps (Figure a-f) show the microstructure evolution of LAT631 in different processing conditions. The as-cast LAT631 alloy displayed a typical dual-phase structure. The white coarse grains were the α-Mg phase and the surrounding gray grains were the β-Li phase. Meanwhile, many small second-phase particles were distributed along the grain boundary. The average grain size of α-Mg in the as-cast alloy was ∼118 μm. After extrusion, the as-extruded alloy consisted of refined dynamically recrystallized (DRXed) and coarse un-dynamically recrystallized (unDRXed) grains. Fine particles were uniformly distributed at the grain and phase boundaries in the as-extruded alloy. The average DRXed grain size in the as-extruded and RSed LAT631 alloy was 3.1 and 3.2 μm, respectively, implying that the grain size of the LAT631 alloys did not change significantly after RS. It is worth noting that many twins were generated in the un-DRXed grains in the RSed alloys. The fraction of unDRXed grains in the as-extruded alloy was approximately 26.9%. In contrast, the RS process promoted the formation of DRXed grains, resulting in a decrease in the fraction (16.9%) of unDRXed grains in the RSed alloy. According to the IPF orientation maps and corresponding misorientation distribution, the twins mainly consisted of double twins (DTW) and tension twins (TTW). As shown in Figure g, both the as-extruded and RSed alloys were mainly composed of α-Mg, β-Li phase, LiMgAl2, Mg2Sn and Li2MgSn (Because Mg2Sn and Li2MgSn have the same crystal structure and very close lattice constants [Citation29], they are collectively called Sn-rich particles).
Figure 2. Microstructures and phase contents of Mg-6Li-3Al-1Sn alloys in different conditions: (a-b) OM and IPF images of as-cast alloy; (c-d) OM and IPF images of as-extruded alloy; (e-f) OM and IPF images of the RSed alloy; (g) The corresponding misorientation distributions of the RSed alloy. (h) XRD patterns of the as-extruded and RSed alloys.
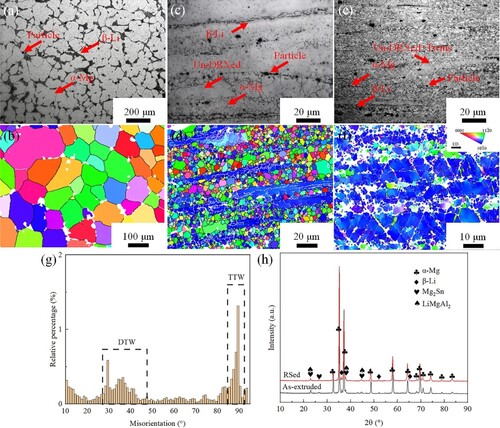
Microstructures of LAT631 alloys in different conditions were further characterized by TEM. A small amount of rod-like second-phase particles were distributed inside α-Mg grains of the as-cast alloy with a size of 1–2 μm. After extrusion, the rod-like particles were transformed into nano-spheric particles with a uniform distribution in the as-extruded grains. As shown in Figure d, plenty of twins were introduced in the RSed alloy. Besides, massive dislocations were observed in the β-Li phase. As is well known, the Li addition plays an important role in enhancing the plasticity of Mg alloys. In this work, the relatively soft β-Li phase was contributed to coordinate the deformation process [Citation30]. Moreover, the average size of nano precipitates in the as-extruded and RSed alloys was 23.4 and 27.5 nm, respectively, indicating that the size of precipitates did not change much after RS.
Figure 3. The microstructure of LAT631 alloys in different conditions observed by TEM and HRTEM, TEM images: (a) The microstructure containing rod-like precipitates in the as-cast alloy; (b) The microstructure containing nano-spheric precipitates in the as-extruded alloy; (c) The microstructure containing nano-spheric precipitates in the RSed alloy; (d) Nano twins in the RSed alloy; (e) β-Li grain in the RSed alloy; (f) HRTEM image of Sn-rich precipitate in the RSed alloy.
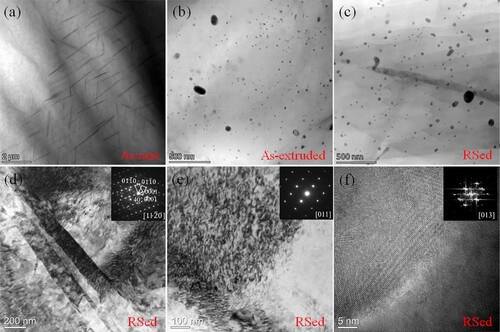
According to the results of HADDF-STEM, rod and spherical precipitates are rich in Sn (Figure a-c), which can be judged as Mg2Sn or Li2MgSn phase according to the above experimental results. However, compared to the as-extruded alloy (Figure b), the enrichment of Al element around the Sn-rich phase and Al-rich segregation can be clearly found in the RSed alloy (Figure c). The process of precipitation and segregation of LAT631 alloy in different conditions is schematically illustrated in Figure m. Since the solid solubility of Al in Mg is much less than 3 wt.% at room temperature [Citation31], it can be assumed that the increment of strain induced the segregation of Al elements that were originally solidly solved in the matrix. Besides, due to the existence of an interface between the second phase particles and the matrix, the Al atoms tended to segregate near the phase boundaries. Sasaki et al. [Citation32] indicated that Al and Zn elements attracted the vacancy clusters to form GP zones during extrusion, resulting in a good strengthening effect in severely deformed Mg alloys. In this study, the cumulative deformation activated the formation of Al segregation in the RSed alloy.
Figure 4. HAADF-STEM images of LAT631 alloys: (a) As-cast; (b) As-extruded; (c) RSed; (d-f) The distribution of Mg; (g-i) The distribution of Al; (j-l) The distribution of Sn; (m) The schematic diagram of Al segregation in LAT631 alloys.
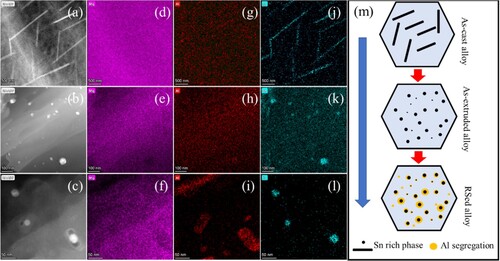
Figure a-c displays that dislocations were hindered by Sn-rich precipitates with Al segregation, indicating that the Al segregation can improve the mechanical properties of the RSed alloy by pining dislocation slip. Besides, the distribution of Li was characterized by EELS (Figure d-g). The Li content was higher in the region where the particles were present (Sn-rich particles area represented by the particle, simplified to ‘P’) and lower in the region where the Al element was offset (Al element segregation area represented by segregation, simplified to ‘S’), suggesting that Li atoms did not participate in the Al segregation process (Figure h and i), due to the Sn-rich particles including Li2MgSn.
Figure 5. (a) STEM image of RSed alloy; (b) HAADF-STEM image of partial enlargement in (a); (c) The distribution of Al and Sn in (b); (d-g) STEM image and related EDS mapping of precipitates in RSed alloy, (h) The distribution of Li along the red line; (i) The distribution of Li along the yellow line marked (‘S’ represents the segregation area of Al element, and ‘P’ represents the Sn-rich particle area.)
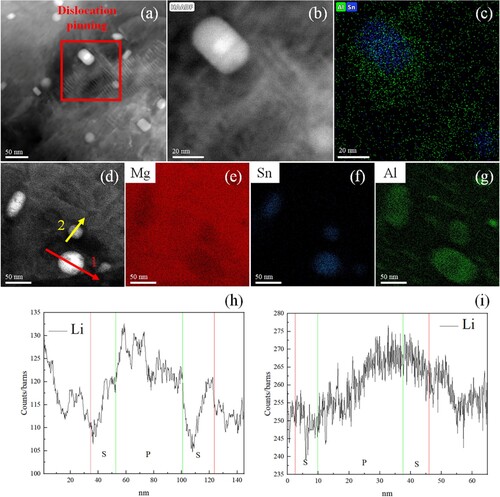
In this study, due to the increasing strain, the mechanical properties of LAT631 alloy are improved by extrusion and further RTRS with a high density of twins (Figure ) and Al segregation (Figure ). After extrusion, the volume fraction of unDRXed region is a ∼26.9% in the as-extruded alloy. In contrast, the RSed alloy exhibited a smaller proportion (16.9%) of unDRXed grains than the extruded alloy. Due to Mg belonging to the close-packed hexagonal crystal structure and having only three independent slip systems at room temperature, the deformation process cannot completely depend on dislocation slip. In general, basal slip and twins are commonly activated to coordinate the plastic deformation at room temperature [Citation33]. In the coarse unDRXed region, the high-frequency change of loading direction promotes the activation of twinning. The twinning boundaries as a region of high distortion energy induce dynamical recrystallization with increasing strain [Citation34]. As a result, the cumulative strain from RS promotes the recrystallization process, which enhances the RSed alloy's plasticity. Furthermore, massive twins as an obstacle to dislocation movement enable the strength elevation during the tensile deformation [Citation14, Citation16]. In addition, the β-Li phase as a soft phase existing in the RSed alloy coordinates the deformation process of the alloy, which is beneficial to the improvement of the plasticity.
Regarding the RSed LAT631 alloys, the increasing strain noticeably promotes Al solutes segregated around the Sn-rich precipitates. Firstly, the segregation of elements with low solubility is expected in the strong deformation process, which helps stabilize the microstructures [Citation35]. Xiao et al. [Citation36] indicated that Ag solutes preferred to segregate at the region of dislocation entanglements and grain boundary to reduce the local elastic distortions in the cold-rolled Mg-Ag alloy. In the present study, the Sn-rich precipitates with Al segregation in the RSed LAT631 alloy significantly hinder the dislocation movement, resulting in dislocations entanglement. This interaction of dislocations with the precipitates stimulates the segregation of Al elements in the boundaries of the particles. Secondly, the addition of elements, such as Li, Gd, Zn, and so on [Citation37, Citation38], in deformed Mg alloy will facilitate the generation of nano precipitates, resulting in the refinement of grain and a good strengthening effect [Citation39]. Similarly, the formation of clusters and precipitates was observed in Mg-8Gd-3Y-0.4Zr alloy with a high strength of 630 MPa and an insufficient ductility of 5% after RTRS [Citation11]. Moreover, it was observed [Citation40] that the segregation of Al on dislocations after ECAP in Mg-4Li-4Al-2RE alloy, and the increasing strain reduced the Al solubility in Mg matrix and the addition of Li stimulated the formation of Al segregation. It is also reported [Citation41] that Gd tends to segregate on the boundaries of nano substructure and numerous dynamical precipitates are formed during rolling, which is beneficial for the improvement of mechanical properties. Besides, in a multi-pass low strain rotary swaging process, substantial compressive stress and shear strain are introduced in RSed alloys, resulting in the generation of twins and the formation of segregation. The movement of dislocations will be prohibited by twins, contributing to the higher strength than that in as-extruded alloy. Therefore, the deformation twins and segregation play an essential role in improving the strength of LAT631 alloy. In addition, compared with other RSed Mg or Mg-Li alloys [Citation14, Citation42], LAT631 alloy exhibits excellent synergy of strength and plasticity. The addition of Li can better coordinate the deformation process of the alloy due to the substantial decrease of the c/a ratio [Citation1], and more refined grains are formed with low multi-pass strain in LAT631 alloy, which is beneficial for the improvement of plasticity.
In summary, this work has reported a strength-ductility synergy enhancement of Mg-Li alloys via RTRS. Unlike conventional extrusion methods, RTRS not only introduces massive twins and promotes the dynamic recrystallization in Mg-6Li-3Al-1Sn alloys, but also introduces Al segregation into the RSed alloy, which solves the strength-ductility dilemma. As a result, the strength and ductility of Mg-6Li-3Al-1Sn alloy are simultaneously improved. The YS, UTS and EL of the RSed alloy are 296 ± 6.7 MPa, 356 ± 2.1 MPa and 19.2 ± 1.6%, respectively, and the specific strength of the RSed alloy is 223 kNmkg−1. Therefore, this study provides a strategy for developing Mg alloys with high strength and plasticity.
Acknowledgment
We acknowledge Prof. Hao Zhou from the Nanjing University of Science and Technology for supporting the rotary swaging experiments.
Disclosure statement
No potential conflict of interest was reported by the author(s).
Additional information
Funding
References
- Ji H, Wu GH, Liu WC, et al. Origin of the age-hardening and age-softening response in Mg-Li-Zn based alloys. Acta Mater. 2022;226:117673, doi:10.1016/j.actamat.2022.117673
- Zha M, Wang SQ, Wang T, et al. Developing high-strength and ductile Mg-Gd-Y-Zn-Zr alloy sheet via bimodal grain structure coupling with heterogeneously-distributed precipitates. Mater Res Lett. 2023;11:772–780. doi:10.1080/21663831.2023.2235375
- Wang T, Zha M, Du CF, et al. High strength and high ductility achieved in a heterogeneous lamella-structured magnesium alloy. Mater Res Lett. 2023;11:187–195. doi:10.1080/21663831.2022.2133976
- Gao YP, Zhao L, Zha M, et al. Twinning-induced plasticity with multiple twinning modes and disclinations in Mg alloys. Int. J. Plast. 2023;164:103595, doi:10.1016/j.ijplas.2023.103595
- Peng X, Liang XL, Liu WC, et al. High-cycle fatigue behavior of Mg-8Li-3Al-2Zn-0.5Y alloy under different states. Magnes Alloy. 2021;9(5):1609–1618. doi:10.1016/j.jma.2020.07.012
- Jeong HT, Kim WJ. Critical review of superplastic magnesium alloys with emphasis on tensile elongation behavior and deformation mechanisms. J Magnes Alloy. 2022;10(5):1133–1153. doi:10.1016/j.jma.2022.02.009
- Peng P, Yan XT, Zheng WC, et al. Microstructure and mechanical properties of heat-treated Mg-6.2Li-3.5Al-3Y alloy. Mater Sci Eng: A. 2022;857:144039, doi:10.1016/j.msea.2022.144039
- Li M, Xie DS, Li JR, et al. Realizing ultra-fine grains and ultra-high strength in conventionally extruded Mg-Ca-Al-Zn-Mn alloys: the multiple roles of nano-precipitations. Mater Charact. 2021;175:111049, doi:10.1016/j.matchar.2021.111049
- Zhou G, Yang Y, Zhang HZ, et al. Microstructure and strengthening mechanism of hot-extruded ultralight Mg-Li-Al-Sn alloys with high strength. J Mater Sci Technol. 2022;103:186–196. doi:10.1016/j.jmst.2021.07.009
- Liu XW, Bian LP, Tian F, et al. Microstructural evolution and mechanical response of duplex Mg-Li alloy containing particles during ECAP processing. Mater Charact. 2022;188:111910, doi:10.1016/j.matchar.2022.111910
- Wan YC, Tang B, Gao YH, et al. Bulk nanocrystalline high-strength magnesium alloys prepared via rotary swaging. Acta Mater. 2020;200:274–286. doi:10.1016/j.actamat.2020.09.024
- Mao QZ, Liu YF, Zhao YH. A review on mechanical properties and microstructure of ultrafine grained metals and alloys processed by rotary swaging. J Alloy Compd. 2022;896:163122, doi:10.1016/j.jallcom.2021.163122
- Chen X, Liu CM, Jiang SN, et al. Fabrication of nanocrystalline high-strength magnesium−lithium alloy by rotary swaging. Adv Eng Mater. 2022;24:2100666, doi:10.1002/adem.202100666
- Yang Y, Chen X, Nie JF, et al. Achieving ultra-strong magnesium-lithium alloys by low-strain rotary swaging. Mater Res Lett. 2021;9:255–262. doi:10.1080/21663831.2021.1891150
- Estrin Y, Martynenko N, Lukyanova E, et al. Effect of rotary swaging on microstructure, texture, and mechanical properties of a Mg-Al-Zn alloy. Adv Eng Mater. 2020;22(1):1900506, doi:10.1002/adem.201900506
- Martynenko N, Lukyanova E, Anisimova N, et al. Improving the property profile of a bioresorbable Mg-Y-Nd-Zr alloy by deformation treatments. Materialia. 2020;13:100841, doi:10.1016/j.mtla.2020.100841
- Huang ZY, Liu CM, Jiang SN, et al. Achieving high-strength nanocrystalline WE43 Mg alloy by a combination of cold rotary swaging and aging treatment. Vaccum. 2022;197:110840, doi:10.1016/j.vacuum.2021.110840
- Zhao J, Jiang BC, Dai ZC, et al. Microstructure, texture, and tensile properties of Mg-3Li alloy extruded at different temperatures. J Mater Eng Perform. 2022;31(7):5782–5789. doi:10.1007/s11665-022-06625-7
- Zou Y, Zhang LH, Li Y, et al. Improvement of mechanical behaviors of a superlight Mg-Li base alloy by duplex phases and fine precipitates. J Alloy Compd. 2018;735:2625–2633. doi:10.1016/j.jallcom.2017.12.025
- Zhang X, Su KQ, Kang HJ, et al. Improving the mechanical properties of duplex Mg-Li-Zn alloy by mixed rolling processing. Mater Today Commun. 2022;31:103538, doi:10.1016/j.mtcomm.2022.103538
- Sun JW, Ding DH, Liu WC, et al. Strength and elastic modulus enhancement in Mg-Li-Al matrix composites reinforced by ex situ TiB2 particles via stir casting. J Magnes Alloy. 2022; In Press, doi:10.1016/j.jma.2022.09.020
- Bian LP, Liu XW, Wang T, et al. Influence of various initial microstructures on microstructure and mechanical property of ECAP processed Mg-8.4Li-3.58Al-0.36Si-0.05Ti-0.01B alloys. Mater Sci Eng: A. 2023;872:144022, doi:10.1016/j.msea.2022.144022
- Guo YH, He XC, Dai YB, et al. Characterization of hot extrusion deformation behavior, texture evolution, and mechanical properties of Mg-5Li-3Sn-2Al-1Zn magnesium alloy. Mater Sci Eng: A. 2022;858:144136, doi:10.1016/j.msea.2022.144136
- Liao G, Wu G, Liu W, et al. Microstructure evolution and enhanced fatigue behavior in the Mg-10Li-5Zn-0.5Er alloys micro-alloyed with Yb. J Magnes Alloy. 2022. doi:10.1016/j.jma.2022.07.017
- Wang JH, Jin Y, Wu RZ, et al. Simultaneous improvement of strength and damping capacities of Mg-8Li-6Y-2Zn alloy by heat treatment and hot rolling. J Alloy Compd. 2022;927:167027, doi:10.1016/j.jallcom.2022.167027
- Song WJ, Liu J, He S, et al. Microstructure and mechanical properties of as-cast ultralight and high strength Mg-10Li-3Al-3Zn-xY alloy with multi-precipitates. Mater Charact. 2022;189:111972, doi:10.1016/j.matchar.2022.111972
- Zhou G, Yang Y, Sun L, et al. Tailoring the microstructure, mechanical properties and damping capacities of Mg-4Li-3Al-0.3Mn alloy via hot extrusion. J Mater Res Technol. 2022;19:4197–4208. doi:10.1016/j.jmrt.2022.06.100
- Ji Q, Wang Y, Wu RZ, et al. High specific strength Mg-Li-Zn-Er alloy processed by multi deformation processes. Charact Mater. 2020;160:110135, doi:10.1016/j.matchar.2020.110135
- Jiang B, Zeng Y, Zhang MX, et al. Effects of Sn on microstructure of as-cast and as-extruded Mg-9Li alloys. Nonferrous Met Soc China. 2013;23(4):904–908. doi:10.1016/S1003-6326(13)62546-7
- Li CQ, He YB, Huang HP. Effect of lithium content on the mechanical and corrosion behaviors of HCP binary Mg-Li alloys. J Magnes Alloy. 2021;9(2):569–580. doi:10.1016/j.jma.2020.02.022
- Brennan S, Bermudez K, Kulkarni N, et al. Interdiffusion in the Mg-Al system and intrinsic diffusionin β-Mg2Al3. Metall Mater Sci A. 2012;43(11):4043–4052. doi:10.1007/s11661-012-1248-8
- Sasaki TT, Lin JY, Yi P, et al. Deformation induced solute segregation and G.P. zone formation in Mg-Al and Mg-Zn binary alloys. Scr Mater. 2022;220:114924, doi:10.1016/j.scriptamat.2022.114924
- Peng JH, Zhang Z, Huang JA, et al. The effect of grain size on texture evolution and mechanical properties of an AZ31 magnesium alloy during cold-rolling process. J Alloy Compd. 2020;817:153302, doi:10.1016/j.jallcom.2019.153302
- Lv BJ, Wang S, Gao FH, et al. {101¯ 2} twin-twin intersection-induced lattice rotation and dynamic recrystallization in Mg-6Al-3Sn-2Zn alloy. J Magnes Alloy. 2022; In Press, doi:10.1016/j.jma.2022.08.006
- Dillon SJ, Tang M, Carter W, et al. Complexion: A new concept for kinetic engineering in materials science. Acta Mater. 2007;55(18):6208–6218. doi:10.1016/j.actamat.2007.07.029
- Xiao LR, Chen XF, Cao Y, et al. Solute segregation assisted nanocrystallization of a cold-rolled Mg-Ag alloy during annealing. Scr Mater. 2020;177:69–73. doi:10.1016/j.scriptamat.2019.10.012
- Yu ZJ, Huang YD, Liu LL, et al. New strategy to solve the ambient strength-ductility dilemma in precipitation-strengthened Mg-Gd alloys via Li addition. Scr Mater. 2022;220:114901, doi:10.1016/j.scriptamat.2022.114901
- Mouhib F, Pei R, Erol B, et al. Synergistic effects of solutes on active deformation modes, grain boundary segregation and texture evolution in Mg-Gd-Zn alloys. Mater Sci Eng: A. 2022;847:143348, doi:10.1016/j.msea.2022.143348
- Cao Y, Ni S, Liao XZ, et al. Structural evolutions of metallic materials processed by severe plastic deformation. Mater Sci Eng: R Rep. 2018;133:1–59. doi:10.1016/j.mser.2018.06.001
- Minarik P, Cizek J, Vesely J, et al. Nanocrystalline aluminium particles inside Mg-4Li-4Al-2RE magnesium alloy after severe plastic deformation. Mater Charact. 2017;127:248–252. doi:10.1016/j.matchar.2016.12.021
- Li RG, Yan Y, Pan HC, et al. Achieving a high-strength binary Mg–15Gd alloy by nano substructure with Gd segregation and nano clusters. Mater Res Lett. 2022;10:682–689. doi:10.1080/21663831.2022.2086834
- Chen X, Liu C, Jiang SN, et al. Effect of yttrium on nanocrystallization of magnesium alloys during cold rotary swaging. Mater Charact. 2022;184:111696, doi:10.1016/j.matchar.2021.111696