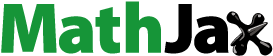
Abstract
Crossover aluminium alloys have recently been introduced as a new class of coarse-grained age-hardenable alloys. Here, we study the evolution of precipitation of the T-phase — -phase — in a 5xxx/7xxx crossover alloy with coarse- and ultrafined microstructures. Both alloys were examined using differential scanning calorimetry, X-ray diffraction and in situ transmission electron microscopy. The ultrafine-grained alloy revealed significant different and accelerated precipitation behaviour due to grain boundaries acting as fast diffusion paths. Additionally, the ultrafine-grained alloy revealed high resistance to grain growth upon heating, an effect primarily attributed to inter-granular precipitation synergistically with trans-granular precipitation of T-phase.
IMPACT STATEMENT
The effect of coarse and ultrafine grains on the T-phase precipitation behaviour in novel aluminium crossover alloys was investigated. Thermal stability of ultrafine grains was achieved through controlled T-phase precipitation.
1. Introduction
To broaden the property profile while simultaneously improving sustainability [Citation1], crossover alloying emerged as a promising strategy for research in the field of aluminium alloys [Citation2]. Such an approach was firstly developed for a crossover alloy merging the 5xxx and 7xxx [Citation2–5] aluminium alloy systems, and recently, it has been used to produce new alloys between 6xxx and 8xxx alloys [Citation6]. In the 5xxx/7xxx crossover system, the T-phase — — was identified as the hardening precipitate. Although the T-phase of the Al–Mg–Zn ternary system is already known for decades [Citation7,Citation8], the scientific interest has been rather low before introducing the crossover concept. Since then, however, the T-phase became the focus of intensive research in materials science. The T-phase is beneficial when used to inhibit grain growth or to generate particle stimulated nucleation [Citation4], or even increase resistance to corrosion and hydrogen damage [Citation9–11]. The age hardening potential by adding Cu and/or Ag was investigated, as reported by Stemper et al. [Citation3,Citation5], as well as by other groups [Citation12,Citation13]. Nevertheless, the precipitation sequence in coarse-grained (CG) Al-based crossover alloys is not yet fully exploited. Several groups presented different precipitation sequences as summarized by Stemper et al. [Citation2]. Cu modifies the precipitation sequence as proposed by Hou et al. [Citation14]: supersaturated solid solution (SSSS)
Guinier-Preston, fully coherent (GPI-zone)
T”, fully coherent (GPII-zone)
intermediate T', semi-coherent
equilibrium T, incoherent. Moreover, Tunes et al. [Citation15] found T-phase surviving upon heavy ion irradiation. Very recently the resistance of a crossover alloy against irradiation was strongly improved by reducing the grain size [Citation16]. Specifically, these ultrafine-grained (UFG) crossover alloys aimed for applications in extreme environments, the precipitation behaviour has not been studied in detail so far, although it is known that a reduction in grain size to the nanometer scale may significantly change the precipitation behaviour [Citation17,Citation18]. The decrease in grain size is not only affecting the precipitation sequence of a given alloy, but consequently also its final mechanical properties [Citation19–22]. The process of precipitation within UFG regime exhibits variations compared to the CG counterpart. For instance, in cases where precipitates exist initially, severe plastic deformation (SPD) can result in the fragmentation or even dissolution of these precipitates into the matrix. This effect can lead to a state resembling a SSSS condition [Citation23]. Conversely, when a SSSS has no initial precipitates, SPD can induce dynamic precipitation [Citation24]. Accelerated precipitation kinetics, as evidenced by Luo et al. [Citation25], highlight an essential distinction compared to the CG material. This expedited precipitation phenomenon is attributed to the considerable density of defects adjacent to grain boundaries (GBs), potentially reaching values of up to
[Citation26]. Moreover, the intermediate precipitation steps are often bypassed [Citation17], leading directly to the precipitation of the equilibrium phase, even at lower temperatures. Therefore, precipitation sequences known from CG alloys need to be revised and reinvestigated. This study aims at systematically closing the knowledge gap in the precipitation behaviour of 5xxx/7xxx crossover alloys in different grain size regimes. The evolution of precipitates in both CG and UFG microstructural regimes is herein investigated through DSC measurements and characterized using X-ray diffraction (XRD) techniques and in situ transmission electron microscopy (TEM). A comprehensive evaluation on the overall thermal stability of the UFG structure is also performed.
2. Materials and methods
The chemical composition of the investigated crossover alloy is Al-4.9Mg-3.7Zn-0.6Cu-0.2Ag (determined via optical emission spectroscopy in wt.-%.). The CG alloys were processed by hot- and cold-rolling from 12 mm to 1.5 mm, followed by solution heat-treatment at min and water quenching. High-pressure torsion (HPT) was carried out under a nominal hydrostatic pressure of 4 GPa for 10 revolutions at a rotational speed of 10 min/revolution using a disk with 12 mm height and 30 mm diameter. The investigations reported in this paper were performed after both the CG and UFG alloys experienced a storage time of 30 days at RT. It is important emphasizing that all thermal analysis experiments were performed at
.
Differential Scanning Calorimetry was carried out using a Netzsch 204DSC F1 Phönix device. Nitrogen was used both as a purge and protective gas (each 20 ml/min).
XRD measurements (Bruker AXS D8 Advance DaVinci diffractometer operating with Cu Kα radiation) of fast cooled samples were performed to identify phases that precipitated. All experiments were performed in Bragg-Brentano geometry. Quantitative data on phase fraction was obtained through Rietveld refinement [Citation27] that was performed using the software package Topas 6 by Bruker. Further details of the Rietveld refinement process for phase fraction estimation can be found elsewhere [Citation28]. In addition, a series of prolonged isothermal aged specimens were measured to obtain information about the near-equilibrium state of the phases. All provided information of phase fraction within this research is corresponding to wt.-%.
Scanning Transmission Electron Microscopy (STEM) was carried out using a Thermo Fisher Scientific Talos F200X electron microscope instrument. Thin foils were prepared by twin jet electro-polishing using a solution of 25 vol.-% nitric acid and 75 vol.-% methanol at a temperature range of to
and a voltage range of 12 to 14 V. High angle annular dark field (HAADF), bright field (BF-TEM) and energy-dispersive X-ray spectroscopy (EDX) measurements were used. In situ heating was carried out using a micro-electro-mechanical system (MEMS) and a Protochips Fusion Select in situ heating/cooling holder with an uncoated e-chip. Preparation for in situ measurements were carried out according to literature [Citation29]. The material was heat-treated within a TEM using a linear heating-rate of
.
Thermodynamic assessments were carried out using Thermocalc 2023a with database TCAL8 to determine the phase fraction of the alloy system upon heating.
3. Results and discussion
3.1. Precipitation sequence
Figure (a,b) showing BFTEM images of the CG and UFG alloy, showcasing the difference in their grain sizes. The CG alloy reaches an average grain size of while for the UFG alloy, the average grain length reaches
and the average grain width
. The precipitation sequence for the CG and UFG alloy determined by DSC is displayed as heat-flow signals in Figure (c). The CG alloy shows exothermic peaks at 34, 233, 271, 306 and
and endothermic peaks at 114 and
. The development of precipitates in the CG alloy shares similarities to findings in experiments conducted by other research groups [Citation14,Citation30,Citation31]. Defect recovery of the UFG alloy was not observed, but it may be overlaid by the precipitation signal in the DSC heat-flow [Citation32].
Figure 1. BFTEM images of (a) the coarse- and (b) ultrafined alloy. (c) shows the DSC heat-flow curves of a coarse-grained (blue continuous line) AlMgCuZnAg crossover alloy after solution heat-treatment (/35 min) and ultrafine-grained (green dashed line) AlMgCuZnAg crossover alloy. The sample was stored at RT for 30 days. The DSC experiments were performed with a linear heating rate of
.

The first peak at has been attributed to the formation of G.P. zones [Citation14,Citation25]. Their partial dissolution can be seen upon further heating to
. G.P. zones have been shown to enhance the age-hardening behaviour of the crossover alloy [Citation12], even more pronounced when Cu and/or Ag is present. [Citation3,Citation33,Citation34].
At , formation of metastable T”-phase precipitates is expected [Citation14]. A peak at
is not reported in the literature and is therefore assumed to be related with the nucleation of metastable T'-phase. It is not clear from literature whether the shoulder region at
is anticipated to be the transformation of T”-phase
T'-phase [Citation14], the transformation of T'
T [Citation35] or nucleation of T-phase [Citation36,Citation37]. The endothermic peak at
represents most likely the dissolution of small-size T'-phase particles [Citation14,Citation30]. The dissolution temperature of T-phase is reported between 430 and
, which was not clearly observable during the DSC run in our experiments [Citation38–40].
Reducing the grain size affects the precipitation behaviour of aluminium alloys [Citation17], but as already mentioned, no comprehensive investigation for 5xxx/7xxx crossover alloys yet are known so far. As can be seen in Figure , the UFG alloy does not show an exothermic peak at low temperatures. Since UFG microstructures are rich in microstructural defects which provide fast diffusion paths [Citation41], G.P. zones may have already formed during RT storage time, so that only their dissolution becomes visible as an endothermic peak at . Such behaviour was also observed in an UFG AA-7075 alloy [Citation42]. The large exothermic peak at
potentially relates to the maximum formation of a metastable phase. The following shoulder may be the transition to a more stable phase with its dissolution at higher temperature. However, no further insight can be derived from the DSC curves.
It is noteworthy that both the CG and UFG alloys exhibit similar characteristics. It is quite feasible that the two exothermic peaks between and
in the CG alloy have merged into one major peak at
in the UFG alloy. Additionally, the precipitation temperature is shifted to lower temperatures, indicating higher precipitation kinetics in the UFG alloy, which can be attributed primarily to accelerated diffusion. As previously indicated, the type of precipitate strongly depends on the Zn/Mg ratio. As reported in [Citation43,Citation44], when the Zn/Mg ratio is low, only T-phase precipitates are observed [Citation3,Citation45]. Hence, given the alloy composition in our study, with a Zn/Mg ratio of 0.72, we expect to find exclusively T-phase particles. To validate these findings alongside our results and to study kinetics of the actual precipitates formed, we conducted XRD measurements at the peaks marked by arrows in Figure .
3.2. Phase evolution
To identify the precipitated phases, XRD measurements were performed. After linear heating the samples to the targeted peak temperatures of ,
,
,
and
for the CG alloy and
,
and
for the UFG alloy, we added an isothermal ageing time of 0, 1, 10 and 100 h, respectively to evaluate kinetics.
The X-ray diffractograms of the CG samples are shown in Figure (a–c). In addition to the diffractograms, also the standard peak positions of the fcc-Al matrix [Citation46] and the T-phase [Citation47] are shown. Note that Bigot et al. [Citation48] observed that the equilibrium T-phase and its precursor exhibit a hardly distinguishable crystal structure. Consequently, XRD does not allow to distinguish between the precursor and the equilibrium T-phase, but can indicate that T-phase or precursors are present.
Figure 2. X-ray diffractograms of the coarse- and ultrafine-grained crossover Al alloy. The samples were heated with a linear heating rate of up to (a)
, (b)
, (c)
and (e)
, (f)
, (g)
, respectively. The plot in in (d) and (h) display the phase fraction of T-phase as a function of temperature and duration of isothermal ageing of the CG alloy and the UFG alloy, respectively. Note that the phase fraction was determined by Rietveld refinement. Black arrows pointing out the increase of reflection peaks.

The lower peak temperatures, in particular and
, are not shown in Figure , because only reflections of the Al matrix were observed. They are thus not displayed in Figure . However, with increasing temperature, reflections peaks of T-phase become more distinct from
/0 h up to
/100 h of isothermal ageing. Their increase is marked with black arrows within Figure . This is also the case for
and
. The increasing intensity of T-phase reflexes with increasing temperature and duration can be interpreted as the progressive formation of precipitates with T-phase structure.
The T-phase fraction in the CG alloy as a function of the ageing time is shown in Figure (d). When isothermal ageing was conducted at ,
, and
in the as-heated conditions (0 h), the phase fractions were measured to be 3.3%, 4.1% and 3.5%, respectively. After 100 h of isothermal ageing, the phase fractions at each temperature were 8.8%, 9.5% and 8.9% indicating an approaching (quasi-)equilibrium state. This also fits very well to calculated values of 11.3%, 9.9% and 8.6% for the T-phase fraction from Thermocalc.
The X-ray diffractograms of the UFG material are displayed in Figure (e–g). Similar to the CG alloy, the UFG alloy shows an intensity increase of reflection peaks of precipitates with T-phase structure with increasing temperature and increasing ageing time.
The T-phase fraction in the UFG alloy as a function of the ageing time is shown in Figure (h). Even in the as-heated state (0 h), volume fraction with a T-phase structure of 1.8%, 3.7% and 7.8% were determined in the relatively low temperature range of ,
and
. It can be assumed that this observation is due to the fact that precipitates in UFG-structured materials can easily form via the benefits of preferential grain boundary diffusion [Citation49]. After 1 h at
the phase fraction increases to 3.1%. When samples are heated at
/1 h and
/1 h, phase fractions of 9.0% and 9.4% were observed. Ageing for 10 h leads to an increase of the phase fraction of the
sample, resulting in 6.3%. Measurements at
and
showing 10.3% and 9.6%, respectively. However, at 100 h of isothermal ageing, all three samples exhibit again a (quasi-)equilibrium. The values of phase fraction for
,
and
are 9.1%, 10.0% and 10.5%, respectively.
In summary, XRD measurements revealed, apart from Al matrix, the sole presence of phases with T-phase structure in both materials. However, the important question of the local position of the precipitates in the UFG material, at GBs or matrix, cannot be derived from XRD data. This will be answered by STEM investigations in the next section.
3.3. Precipitate characteristics
STEM investigations were carried out at ,
and
for the CG alloy and at
and
for the UFG alloy in the as-heated condition, as indicated in Figure . As displayed in Figure (a), the investigations at
revealed for the CG alloy that the main alloying elements Mg and Zn are present in the T-phase (note that no distinction is made between precursors and equilibrium of the T-phase). The elemental mappings does not clearly show an enrichment of Cu and Ag within the precipitate at this state. The morphology appears in a round shape and shows similarities as reported by Stemper et al. [Citation3]. Only very few elongated precipitates can be found as shown in Figure (a) in the HAADF image. The size of the particles is in average
.
Figure 3. STEM HAADF and EDX elemental mappings of the coarse- and ultrafine-grained crossover Al alloy. The samples were heated with a linear heating rate of up to (a)
, (b)
, (c)
for the CG alloy and to (e)
, (f)
for the UFG alloy.

At , the incorporation of Cu and Ag within the T-phase was detected as shown in Figure (b). A detailed examination of the HAADF image reveals that the majority of the precipitates exhibit a spherical morphology. The presence of Cu and Ag within the T-phase suggests their potential role in modifying the characteristics and properties of the precipitates. The particle size increased to
.
At it is visible that Cu and Ag are clearly involved within the particles (Figure (c)). Cu may show a core/shell tendency, but a more detailed investigation is needed to fully clarify this issue. The morphology did not change significantly and their shape is predominantly spherical, but the size increased to
.
The analysis of the UFG alloy at reveals the formation of elongated T-phase, consisting mainly of the alloying elemens Mg and Zn, and distributed preferably discontinuously at GBs (Figure (d)). This observation is an indication that no fully coherent precipitates participate in the first steps of the precipitation sequence, and that increased diffusion along GBs plays an important role. A similar UFG structure is also reported in literature [Citation50,Citation51]. The T-phase thickness (i.e. transverse length) were measured to be
.
When the sample is heated to , precipitation within the matrix is visible in the UFG alloy Figure (e). Precipitation at GBs still occurs discontinuously, but the elongated T-phase slightly increased in thickness (
). At both precipitation sites, all alloying elements are incorporated into the T-phase. Precipitates within the grains appear to have both elongated and round shapes.
3.4. Thermal stability
Another important question arises regarding the thermal stability of both the UFG structure in terms of grain growth (recrystallization) and the T-phase precipitates in terms of growth and dissolution. We investigated this behaviour using in situ TEM heating experiments. The results are shown in Figure . Upon heating to , small precipitates can be seen primarily at GBs, which is consistent with the results presented in Figure . The UFG microstructure has not changed up to
which can presumably be attributed to the pinning effect of T-phase particles on the GBs. At approximately
, coalescence is noted and precipitates grow in size due to Ostwald ripening [Citation52]. These particles, as indicated with an arrow, gradually diminish in size and eventually disappearing completely at
. It should be noted that the volume fraction of T-phase decreases with increasing temperature (solvus temperature according to Thermocalc simulation
). Consequently, the precipitates partially dissolve, exemplified in Figure . Simulatenously, when T-phase particles are dissolving, the average grain size of the UFG microstructure is increasing.
Figure 4. BFTEM images illustrating in situ TEM experiments conducted as a function of temperature on the UFG-AlMgZnCuAg alloy. The alloy underwent heat treatment using a MEMS heating holder, employing a linear heating rate of . Images are extracted from the video file; the scale bar displayed at RT applies to all micrographs.
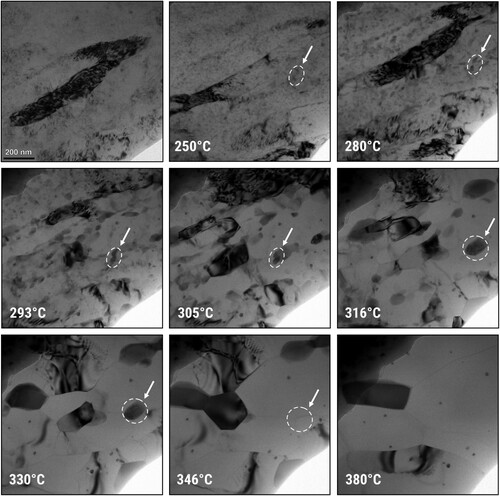
However, the average grain size is still in the UFG regime. Given the significant amount of energy stored in GBs [Citation53], UFG alloys are known to be susceptible to grain growth upon minimal heating [Citation54,Citation55]. Dhal et al. [Citation56] investigated a cryo-rolled AA-2024 alloy and observed the start of recrystallization at . Our study reveals that the grain size of the UFG crossover alloy remains unchanged up to
and undergoes slow grain growth at temperatures beyond
. Finally, the UFG microstructure completely diminishes at
, showcasing the stabilizing effect of the T-phase particles on the UFG structure.
4. Conclusion
Coarse and a novel ultrafine-grained AlMgZnCuAg crossover alloy were investigated and the major differences were revealed using DSC, XRD and (in situ) TEM techniques. Grain size effects on the precipitation sequence were unravelled for an UFG aluminium crossover alloy for the first time. The grain size affects the precipitation behaviour and following conclusions can be drawn:
In both alloys, precipitation is governed by particles with T-phase structure-type. Isothermal ageing at different temperatures up to 100 h did not change their crystal structure.
Kinetics of precipitation is different between CG and UFG alloys. The UFG alloy reaches equilibrium T-phase fraction faster and at lower temperature when compared with the CG alloy. This is most likely due to fast diffusion at GBs.
While for the CG alloy transgranular precipitation dominates, the UFG alloy is characterized by discontinuous precipitates at GBs (intragranular) accompanied by precipitates within the matrix.
Precipitation of the T-phase at GBs leads to a high thermal stability reflected by a resistance to grain growth in the UFG alloy up to
.
CRediT authorship contribution statement
PDW: Conceptualization, Methodology, Investigation, Visualization, Writing - original draft. MAT, OR: Visualization, Writing - review & editing. CK, SG, TK: Investigation, Visualization, Writing - review & editing. PJU: Conceptualization, Supervision, Writing - review & editing. SP: Project administration, Conceptualization, Supervision, Writing - review & editing.
Acknowledgments
PDW and PJU are grateful for discussion with Roland Morak (AMAG Rolling GmbH).
Disclosure statement
No potential conflict of interest was reported by the author(s).
Additional information
Funding
References
- Raabe D, Ponge D, Uggowitzer PJ, et al. Making sustainable aluminum by recycling scrap: the science of ‘dirty’ alloys. Prog Mater Sci. 2022;128:100947. doi: 10.1016/j.pmatsci.2022.100947
- Stemper L, Tunes MA, Tosone R, et al. On the potential of aluminum crossover alloys. Prog Mater Sci. 2022;124:100873. doi: 10.1016/j.pmatsci.2021.100873
- Stemper L, Mitas B, Kremmer T, et al. Age-hardening of high pressure die casting AlMg alloys with Zn and combined Zn and Cu additions. Mater Des. 2019;181:107927. doi: 10.1016/j.matdes.2019.107927
- Samberger S, Weißensteiner I, Stemper L, et al. Fine-grained aluminium crossover alloy for high-temperature sheet forming. Acta Mater. 2023;253:118952. doi: 10.1016/j.actamat.2023.118952
- Stemper L, Tunes MA, Dumitraschkewitz P, et al. Giant hardening response in AlMgZn (Cu) alloys. Acta Mater. 2021;206:116617. doi: 10.1016/j.actamat.2020.116617
- Trink B, Weißensteiner I, Uggowitzer PJ, et al. High Fe content in Al-Mg-Si wrought alloys facilitates excellent mechanical properties. Scr Mater. 2022;215:114701. doi: 10.1016/j.scriptamat.2022.114701
- Raynor G, Hume-Rothery W. Equilibrium between Al2Mg3Zn3 and the primary solid solution in the system aluminium-magnesium-zinc. Trans Faraday Soc. 1948;44:29–36. doi: 10.1039/tf9484400029
- Bergman G, Waugh JL, Pauling L. The crystal structure of the metallic phase Mg32(Zn,Al)49. Acta Crystallogr. 1957;10(4):254–259. doi: 10.1107/S0365110X57000808
- Cao C, Zhang D, Wang X, et al. Effects of Cu addition on the precipitation hardening response and intergranular corrosion of Al-5.2 Mg-2.0 Zn (wt.%) alloy. Mater Charact. 2016;122:177–182. doi: 10.1016/j.matchar.2016.11.004
- Yang X, Chen J, Liu J, et al. A high-strength AlZnMg alloy hardened by the T-phase precipitates. J Alloys Compd. 2014;610:69–73. doi: 10.1016/j.jallcom.2014.04.185
- Wang Y, Sharma B, Xu Y, et al. Switching nanoprecipitates to resist hydrogen embrittlement in high-strength aluminum alloys. Nat Commun. 2022;13(1):1–8.
- Cao C, Zhang D, Zhuang L, et al. Improved age-hardening response and altered precipitation behavior of Al-5.2 Mg-0.45 Cu-2.0 Zn (wt%) alloy with pre-aging treatment. J Alloys Compd. 2017;691:40–43. doi: 10.1016/j.jallcom.2016.08.206
- Mihara M, Marioara CD, Andersen SJ, et al. Precipitation in an Al–Mg–Cu alloy and the effect of a low amount of Ag. Mater Sci Eng A. 2016;658:91–98. doi: 10.1016/j.msea.2016.01.087
- Hou S, Liu P, Zhang D, et al. Precipitation hardening behavior and microstructure evolution of Al–5.1 Mg–0.15 Cu alloy with 3.0 Zn (wt%) addition. J Mater Sci. 2018;53(5):3846–3861. doi: 10.1007/s10853-017-1811-1
- Tunes MA, Stemper L, Greaves G, et al. Prototypic lightweight alloy design for stellar-radiation environments. Adv Sci. 2020;7(22):2002397. doi: 10.1002/advs.v7.22
- Willenshofer PD, Tunes MA, Vo HT, et al. Radiation-resistant aluminium alloy for space missions in the extreme environment of the solar system; 2022. arXiv preprint arXiv:221003397.
- Hu T, Ma K, Topping T, et al. Precipitation phenomena in an ultrafine-grained Al alloy. Acta Mater. 2013;61(6):2163–2178. doi: 10.1016/j.actamat.2012.12.037
- Chrominski W, Lewandowska M. Precipitation phenomena in ultrafine grained Al–Mg–Si alloy with heterogeneous microstructure. Acta Mater. 2016;103:547–557. doi: 10.1016/j.actamat.2015.10.030
- Ralston K, Fabijanic D, Birbilis N. Effect of grain size on corrosion of high purity aluminium. Electrochim Acta. 2011;56(4):1729–1736. doi: 10.1016/j.electacta.2010.09.023
- Bazarnik P, Romelczyk-Baishya B, Kulczyk M, et al. The strength and ductility of 5483 aluminium alloy processed by various SPD methods. In: Materials science forum. Vol. 765. Baech, Switzerland: Trans Tech Publ; 2013. p. 423–428.
- Khan MA, Wang Y, Hamza M, et al. Precipitation behaviour in an Al-Zn-Mg-Cu alloy subjected to high strain rate compression tests. Mater Charact. 2021;180:111398. doi: 10.1016/j.matchar.2021.111398
- Khan MA, Xu C, Hamza M, et al. Enhanced tensile strength in an Al–Zn–Mg–Cu alloy via engineering the precipitates along the grain boundaries. J Mater Res Technol. 2023;22:696–705. doi: 10.1016/j.jmrt.2022.11.155
- Murayama M, Horita Z, Hono K. Microstructure of two-phase Al–1.7 at% Cu alloy deformed by equal-channel angular pressing. Acta Mater. 2001;49(1):21–29. doi: 10.1016/S1359-6454(00)00308-6
- Roven HJ, Liu M, Werenskiold JC. Dynamic precipitation during severe plastic deformation of an Al–Mg–Si aluminium alloy. Mater Sci Eng A. 2008;483–484:54–58. doi: 10.1016/j.msea.2006.09.142
- Luo J, Luo H, Li S, et al. Effect of pre-ageing treatment on second nucleating of GPII zones and precipitation kinetics in an ultrafine grained 7075 aluminum alloy. Mater Des. 2020;187:108402. doi: 10.1016/j.matdes.2019.108402
- Roven HJ, Liu M, Murashkin MY, et al. Nanostructures and microhardness in Al and Al–Mg alloys subjected to SPD. In: Materials science forum, Vol. 604. Baech, Switzerland: Trans Tech Publ; 2009. p. 179–185.
- Young RA. The rietveld method. Oxford: International Union of Crystallography; 1993.
- Kainz C, Schalk N, Saringer C, et al. In-situ investigation of the oxidation behavior of powdered TiN, Ti (C, N) and TiC coatings grown by chemical vapor deposition. Surf Coat Technol. 2021;406:126633. doi: 10.1016/j.surfcoat.2020.126633
- Tunes MA, Quick CR, Stemper L, et al. A fast and implantation-free sample production method for large scale electron-transparent metallic samples destined for MEMS-based in situ S/TEM experiments. Materials. 2021;14(5):1085. doi: 10.3390/ma14051085
- Afify N, Gaber AF, Abbady G, et al. Fine scale precipitates in Al-Mg-Zn alloys after various aging temperatures. Mater Sci Appl. 2011;2(05):427.
- Chemingui M, Ameur R, Optasanu V, et al. DSC analysis of phase transformations during precipitation hardening in Al–Zn–Mg alloy (7020). J Therm Anal Calorim. 2019;136:1887–1894. doi: 10.1007/s10973-018-7856-9
- Shanmugasundaram T, Murty B, Sarma VS. Development of ultrafine grained high strength Al–Cu alloy by cryorolling. Scr Mater. 2006;54(12):2013–2017. doi: 10.1016/j.scriptamat.2006.03.012
- Geng Y, Zhang D, Zhang J, et al. Early-stage clustering and precipitation behavior in the age-hardened Al–Mg–Zn (-Cu) alloys. Mater Sci Eng A. 2022;856:144015. doi: 10.1016/j.msea.2022.144015
- Guo C, Zhang H, Li J. Influence of Zn and/or Ag additions on microstructure and properties of Al-Mg based alloys. J Alloys Compd. 2022;904:163998. doi: 10.1016/j.jallcom.2022.163998
- Afify N, Gaber A, Abbady G. Characterization of the developed precipitates in Al-2 at.% Zn-x at.% Mg, (x= 1.8, 2, 2.4, 3, 4.2). In: Light Metals 2013. Cham: Springer; 2016. p. 431–436.
- Jiang X, Tafto J, Noble B, et al. Differential scanning calorimetry and electron diffraction investigation on low-temperature aging in Al-Zn-Mg alloys. Metall Mater Trans A. 2000;31:339–348. doi: 10.1007/s11661-000-0269-x
- Lang P, Wojcik T, Povoden-Karadeniz E, et al. Thermo-kinetic prediction of metastable and stable phase precipitation in Al–Zn–Mg series aluminium alloys during non-isothermal DSC analysis. J Alloys Compd. 2014;609:129–136. doi: 10.1016/j.jallcom.2014.04.119
- Chuan L, Wang Q, Tang H, et al. Effects of Mg content on microstructure and mechanical properties of low Zn-containing Al-xMg-3Zn-1Cu cast alloys. Trans Nonferrous Met Soc China. 2022;32(3):721–738. doi: 10.1016/S1003-6326(22)65828-X
- Deng Y, Yin Z, Duan J, et al. Evolution of microstructure and properties in a new type 2 mm Al–Zn–Mg–Sc–Zr alloy sheet. J Alloys Compd. 2012;517:118–126. doi: 10.1016/j.jallcom.2011.12.049
- Zhu X, Liu F, Wang S, et al. The development of low-temperature heat-treatable high-pressure die-cast Al–Mg–Fe–Mn alloys with Zn. J Mater Sci. 2021;56:11083–11097. doi: 10.1007/s10853-021-05972-5
- Divinski SV, Reglitz G, Rösner H, et al. Ultra-fast diffusion channels in pure Ni severely deformed by equal-channel angular pressing. Acta Mater. 2011;59(5):1974–1985. doi: 10.1016/j.actamat.2010.11.063
- Zhao Y, Liu J, Topping TD, et al. Precipitation and aging phenomena in an ultrafine grained Al-Zn alloy by severe plastic deformation. J Alloys Compd. 2021;851:156931. doi: 10.1016/j.jallcom.2020.156931
- Graf G, Spoerk-Erdely P, Staron P, et al. Quench rate sensitivity of age-hardenable Al-Zn-Mg-Cu alloys with respect to the Zn/Mg ratio: an in situ SAXS and HEXRD study. Acta Mater. 2022;227:117727. doi: 10.1016/j.actamat.2022.117727
- Polmear I, StJohn D, Nie JF, et al. Light alloys: metallurgy of the light metals. Oxford: Butterworth-Heinemann; 2017.
- Liu T, Wang Q, Tang H, et al. Microstructure and mechanical properties of squeeze-cast Al-5.0 Mg-3.0 Zn-1.0 Cu alloys in solution-treated and aged conditions. Trans Nonferrous Met Soc China. 2020;30(9):2326–2338. doi: 10.1016/S1003-6326(20)65382-1
- Gulyaev AP, Trusova EF. Some physical properties and some solid solutions of Al, Fe and Cu. Zh Tekh Fiz. 1950;20:66.
- Auld J, Williams B. X-ray powder data of T phases composed of aluminium and magnesium with silver, copper or zinc. Acta Crystallogr. 1966;21(5):830–831. doi: 10.1107/S0365110X66003955
- Bigot A, Auger P, Chambreland S, et al. Atomic scale imaging and analysis of T'precipitates in Al-Mg-Zn alloys. Microsc Microanal Microstruct. 1997;8(2):103–113. doi: 10.1051/mmm:1997109
- Rashkova B, Faller M, Pippan R, et al. Growth mechanism of Al2Cu precipitates during in situ TEM heating of a HPT deformed Al–3wt.% Cu alloy. J Alloys Compd. 2014;600:43–50. doi: 10.1016/j.jallcom.2014.02.090
- Nurislamova G, Sauvage X, Murashkin M, et al. Nanostructure and related mechanical properties of an Al–Mg–Si alloy processed by severe plastic deformation. Philos Mag Lett. 2008;88(6):459–466. doi: 10.1080/09500830802186938
- Zhilyaev AP, Gimazov AA, Langdon TG. Recent developments in modelling of microhardness saturation during SPD processing of metals and alloys. J Mater Sci. 2013;48:4461–4466. doi: 10.1007/s10853-013-7155-6
- Voorhees PW. The theory of Ostwald ripening. J Stat Phys. 1985;38:231–252. doi: 10.1007/BF01017860
- Sauvage X, Wilde G, Divinski S, et al. Grain boundaries in ultrafine grained materials processed by severe plastic deformation and related phenomena. Mater Sci Eng A. 2012;540:1–12. doi: 10.1016/j.msea.2012.01.080
- Valiev RZ, Langdon TG. Principles of equal-channel angular pressing as a processing tool for grain refinement. Prog Mater Sci. 2006;51(7):881–981. doi: 10.1016/j.pmatsci.2006.02.003
- Lewandowska M, Wejrzanowski T, Kurzydłowski KJ. Grain growth in ultrafine grained aluminium processed by hydrostatic extrusion. J Mater Sci. 2008;43(23–24):7495–7500. doi: 10.1007/s10853-008-2808-6
- Dhal A, Panigrahi S, Shunmugam M. Precipitation phenomena, thermal stability and grain growth kinetics in an ultra-fine grained Al 2014 alloy after annealing treatment. J Alloys Compd. 2015;649:229–238. doi: 10.1016/j.jallcom.2015.07.098