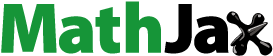
Abstract
The metastable-stable transition and rapid coarsening of metastable D022 phase remains its Achilles hell, restricting the application of D022-strengthened alloys at service temperatures higher than 650°C. Hence, it is crucial to improve thermal stability of D022 phase. In this work, we report an 800°C-stable D022-Ni3(W0.24Ti0.38Ta0.19Nb0.19) superlattice in the Ni58Cr23Fe10W5Ti2Ta1Nb1 MEA. Experimental results and theoretical analysis showed that the exceptional thermal stability is due to Nb-sublattice occupying elements, low diffusivity of W, and extremely small lattice misfit between the D022 phase and FCC matrix. These findings shed lights on developing high-performance D022-hardened alloys capable of operating at temperatures above 650°C.
High entropy alloys (HEAs) and medium entropy alloys (MEAs) with face centered cubic (FCC) structure have shown the highest fracture toughness [Citation1–3] of metallic materials, stimulating a broad exploration of their strengthening and toughening mechanisms. Comparing the strengthening mechanisms of reported alloys [Citation4–10], it is found that precipitation strengthening is a powerful strategy. Of particular interest, D022 () phase is one of the most efficient precipitates to strengthen FCC alloys without sacrificing ductility significantly to date [Citation9, Citation11, Citation12]. D022 phase with a volume fraction of ∼7% contributes strength of about 700 MPa because of its combined ordering strengthening and coherency strengthening [Citation9]. However, D022 phase undergoes rapid coarsening and transforms into
(D0a) or
(D019) phase upon continued aging at around 650°C [Citation13–15], resulting in a substantial degradation in mechanical properties. Hereinto, one of the critical challenges for D022-hardened alloys is to improve the thermal stability of D022 phase.
In Ni-based superalloys, microalloying has been found useful in enhancing the stability of Ni3Nb-type D022 phase. For example, changing the local (Al + Ti)/Nb ratio suppresses the coarsening of D022-Ni3Nb precipitates in IN718 [Citation16–21]. The first-principles calculation indicates that Nb-sublattice occupiers like Ti, Ta and W thermodynamically stabilize the Ni3Nb-type D022 phase [Citation12, Citation22, Citation23]. Despite these insightful understandings, to the best of authors’ knowledge, the D022 phase in IN718 still transforms into a D0a phase quickly at 700°C. Fortunately, Gao et al. [Citation24] recently reported a new Ni3(Cr0.2W0.4Ti0.4)-D022 phase that is thermo-stable at 700°C, giving us opportunities to develop D022 phase that is stable at an even higher temperature. However, the coarsening behavior and phase-stability mechanism of the Ni3(Cr0.2W0.4Ti0.4)-D022 phase did not get adequate scientific attention. It also remains unknown if the microalloying could further improve the thermostability of this new D022 phase. Meantime, the extensive works of other intermetallic particles in high entropy alloys provide a key insight for our research about the phase stability of D022 [Citation25, Citation26].
Therefore, we in this study developed a Ni58Cr23Fe10W5Ti2Ta1Nb1 MEA based on the NiCrFe-based system [Citation10] and investigated its precipitation behaviors and mechanical properties using systematic experimental and theoretical methods. Our results showed that a Ni3(W0.24Ti0.38Ta0.19Nb0.19)-D022 phase precipitates in this MEA and this new superlattice is thermally stable at 800°C. The origins of this exceptional thermostability have been revealed using experimental and theoretical analysis.
Elements of Ni, Cr, Fe, W, Ti, Ta and Nb with high purity (>99.9 wt.%) were used as raw materials. The Ni58Cr23Fe10W5Ti2Ta1Nb1 MEA were prepared using arc melting in an argon atmosphere and casted into a copper mold with the dimension of 50 × 10 × 5 mm3. The as-cast samples were first solution-treated at 1200°C for 48 h and then cold-rolled to approximately 1.5 mm along the longitudinal direction, followed by recrystallization at 1200°C for ∼2 min. Subsequently, isothermal aging treatments were applied to the MEA at 800°C, 750°C and 700°C at various times. All the heat treatment procedures described here were finished by water quenching. The SEM samples were polished down to 0.04 μm colloidal silica or electron-polished finish, and then analyzed by scanning electron microscope equipped with BSE and EDS detector (SEM, Tescan MIRA3). Rigaku d/max-2550 obtained the X-ray diffraction (XRD) patterns of the samples with a monochromator. For the transmission electron microscope (TEM, FEI Themis Z) analysis, sheet samples with a thickness of 0.5 mm were first cut from the annealed samples by electrical discharged machining (EDM) and then mechanically ground to a thickness of ∼70 μm using SiC papers. Afterward, the samples were punched into 3-mm-diameter discs and thinned by a twin-jet polishing technique. ImageJ software was used for image analysis and Pandat software with the newest MEA database was used to predict the precipitation behavior. For mechanical tests, the dog-bone specimens with a gauge dimension of 12.5 × 1.2 × 3 mm3 were prepared for the tensile test with a strain rate of 1 × 10−3 s−1 in the universal testing machine (TSMT) at room temperature.
Figure shows the microstructures of the Ni58Cr23Fe10W5Ti2Ta1Nb1 MEA aged at 800°C for 12 h. Figure (a1) presents typical fine recrystallized equiaxed grains, and there are phases enriched in W inside the grain and at the grain boundaries. The
phase itself shows very small volume fraction and little influence on the strength of our previous results [Citation10]. Figure (a2) depicts the nano-sized lens-shaped precipitates within the grain. TEM analysis was devoted to confirming the structures of these nano-sized precipitates. Figure (b) exhibits a typical dark-field TEM image of the disk-shaped precipitates with different crystallographic orientations. The disk-shaped precipitates are ∼55 nm in length and ∼20 nm in width. Figure (c) demonstrated the FCC crystal structure of the matrix and the D022 structure of the disk-shaped precipitates using selective area diffraction patterns. The orientation relationship between the D022 phase and matrix follows [100]γ″//[001]m, [010]γ″//[001]m, and[001]γ″//[001]m. Furthermore, compositional analysis by TEM-EDS indicates that the Ni, W, Ti, Ta and Nb elements have a strong tendency to partitioning into the D022 phase as shown in Figure (d). The quantitative chemical compositions of the D022 phase and FCC matrix obtained from the TEM-EDS-point result are shown in Table , and the present high-entropy D022 phase follows the Ni3(W0.24Ti0.38Ta0.19Nb0.19) stoichiometry. High-resolution TEM observation (Figure (e)) reveals the fully coherent interface between ordered D022 phases and disordered FCC matrix by fast fourier transform (FFT) and inverse fast fourier transform (IFFT) analysis, circled by dotted boxes of f1 (green), f2 (blue) and g (orange), respectively. For the ordered A3B-type D022 superlattices, the red dot represents the A sublattice sites, and similarly, the black dot represents the B sublattice sites in Figure (g). Besides, the lattice misfit of the FCC matrix and D022 phase is calculated to be ∼0.56% along the a-axis.
Figure 1. Microstructural features of the Ni58Cr23Fe10W5Ti2Ta1Nb1 MEA aged at 800°C for 12 h: (a) SEM images showing the typical microstructures, (b) Dark-field image showing the D022 phase, (c) low-index diffraction patterns taken along [001]m, [011]m and [12]m zone axes of the matrix, (d) High-magnification microstructure of the MEA with the corresponding TEM-EDS element mappings of Ni, W, Ti, Ta and Nb elements, and (e) High resolution TEM image showing D022 precipitate coherent with FCC matrix by FFT (marked as f1 and f2) and IFFT (marked as g).
![Figure 1. Microstructural features of the Ni58Cr23Fe10W5Ti2Ta1Nb1 MEA aged at 800°C for 12 h: (a) SEM images showing the typical microstructures, (b) Dark-field image showing the D022 phase, (c) low-index diffraction patterns taken along [001]m, [011]m and [112]m zone axes of the matrix, (d) High-magnification microstructure of the MEA with the corresponding TEM-EDS element mappings of Ni, W, Ti, Ta and Nb elements, and (e) High resolution TEM image showing D022 precipitate coherent with FCC matrix by FFT (marked as f1 and f2) and IFFT (marked as g).](/cms/asset/2f2b7684-e783-4fd2-b6e1-bad8803f6645/tmrl_a_2309271_f0001_oc.jpg)
Table 1. Chemical compositions of D022 phase and matrix obtained from TEM-EDS (at.%).
We further reveal the thermal stability of this newly developed Ni3(W0.24Ti0.38Ta0.19Nb0.19)-D022 phase by annealing at 700–800°C for 12–144 h based on Fig. S1 and S2 (see details in ‘Supplementary materials’). The typical SEM micrographs of nanoparticles were carried out to track the coarsening behavior of the D022 phase under different aging conditions. As shown in Figure , there are two mutually vertical ellipsoidal variants and a spherical variant, which is consistent with that in Figure (b). Furthermore, as long as the annealing time is prolonged or the aging temperature is increased, the size of D022 precipitates increased to varying degrees while kept the disk shape. We quantitatively evaluate the average major axis size and volume fraction of nanoparticles in the MEA with the variation of annealing time at different temperatures in Fig. S3. Based on the Lifshitz-Slyozov-Wagner (LSW) theory, the relationship between the average major axis size of D022 nanoparticles and aging time can be written as follows: , where
is the average major axis size of D022 nanoparticles at the aging time of t, k is the coarsening rate constant. The corresponding normalized particle size distributions (PSD) histograms analyzed by commercial ImageJ software are also presented accordingly, as shown in Figure . For a clear comparison, the distribution functions predicted by the MLSW model are plotted here (blank curves) [Citation27]. It is evident that the size distribution of the D022 nanoparticles in the MEA is in reasonable agreement with the prediction by the LSW theory.
Figure 2. SEM images and the particle size distribution of the MEA aged at different temperatures revealing the ripening of D022 precipitates, (a) 800°C, (b) 750°C, and (c) 700°C.
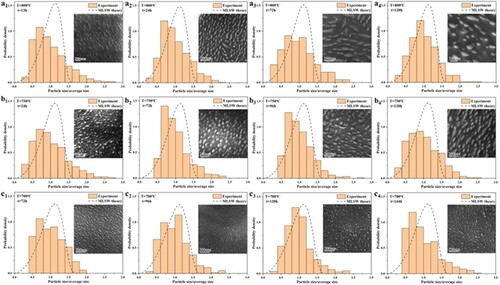
It is generally recognized that the Ni3Nb phases with D022 superlattices gradually transform into (D0a) phase with needle-shape or
(D019) phase with lath-shape [Citation13, Citation14, Citation28, Citation29]. Therefore, to assess the extent to the thermal stability of the D022 phase in the MEA during the longer-term thermal exposure, and the MEA was investigated by annealing at 800°C for 240–720 h. Stunningly, the current D022 phase still showed disc-shaped morphologies without an obvious change during long-term exposure at 800°C in the Ni58Cr23Fe10W5Ti2Ta1Nb1 MEA in Figure (a), and XRD test also supports that no new phase was found, as shown in Fig. S4, demonstrating the good thermal stability of Ni3(W0.24Ti0.38Ta0.19Nb0.19)-D022 phase at 800°C. The coarsening rate of our investigated MEA and Inconel 718, modified Inconel 718 superalloy [Citation30–32] are compared in Figure (b), the Ni58Cr23Fe10W5Ti2Ta1Nb1 MEA shows a lower coarsening rate based on the LSW theory.
Figure 3. (a) SEM images of the MEA during long-term exposure at 800°C revealing the ripening of D022 precipitates, (b) Comparison of coarsening rate for present work and previous work (Alloy718 [Citation30], IN718 [Citation32] and M718 [Citation31])
![Figure 3. (a) SEM images of the MEA during long-term exposure at 800°C revealing the ripening of D022 precipitates, (b) Comparison of coarsening rate for present work and previous work (Alloy718 [Citation30], IN718 [Citation32] and M718 [Citation31])](/cms/asset/2172ff54-6ebc-46b2-be0b-d33a4345be85/tmrl_a_2309271_f0003_oc.jpg)
The observed exceptional phase stability of Ni3(W0.24Ti0.38Ta0.19Nb0.19)-D022 phase could be understood from the following aspects. First, in the current study, the alloying elements of Ti, Ta and W are more inclined to occupy the Nb sublattice (Table ), which can thermodynamically stabilize the -Ni3Nb with D022 superlattices according to first–principles calculations [Citation12]. Second, the important alloying parameters that determine the crystal structure of precipitates, i.e. valence electron concentrations (VEC) [Citation9] and the atomic-radius ratio (
) [Citation33], of Ni3(W0.24Ti0.38Ta0.19Nb0.19)-D022 also indicate its enhanced phase stability. Based on reported data in Fig. S5, we found that the D022 phase tends to be stable when the two alloying parameters range in 8.588 < VEC < 8.75, 0.9307<
<0.9707. The two values of the Ni3(W0.24Ti0.38Ta0.19Nb0.19) phase in this study were 8.715 and 0.9437, respectively, tending to stabilize its D022 structure. It seems plausible that, by varying gradually the radius ratio
and VEC strategy, the stacking types of ordered A3B-type precipitation may undergo a transformation, improving high thermal stability of ordered A3B-type precipitation. However, designing new alloys (without much trial and error) to get precipitates with high thermal stability is still an open question and needs elaborate study. Last but not least, we calculated the phase diagram of the in Ni58Cr23Fe10W5Ti2Ta1Nb1 MEA based on the Pandat software with the latest MEA database, as shown in Fig. S1, D022 phases can stably exist at 800°C against the transformation to the D0a or D019 phase. This strongly supports that the designed D022 phase exhibits excellent thermostability at 800°C.
The slower coarsening kinetics in Ni58Cr23Fe10W5Ti2Ta1Nb1 MEA are mainly related to two considerations. On the one hand, Ni3(W0.24Ti0.38Ta0.19Nb0.19)-D022 phases are probably controlled by the diffusivity of W, which is the slowest diffusers in Ni [Citation34, Citation35], but Ni3Nb-D022 phases in Inconel 718 and modified Inconel 718 superalloy are governed by the diffusivity of Nb. This low diffusivity of W significantly reduces the migration rate of the phase interface. And one the other hand, the D022 phase has a relatively large lattice misfit of ∼3% with the FCC matrix along the c-axis, while a smaller misfit of < 1% along the a-axis in Inconel 718 superalloy [Citation36]. Nevertheless, in Ni58Cr23Fe10W5Ti2Ta1Nb1 MEA, the drastically reduced lattice misfit (about 2.6% along the c-axis while 0.56% along the a-axis) should lower the elastic misfit energy [Citation37–39], leading to a substantial reduction in the driving force for coarsening.
The tensile properties of the MEA are exhibited in Figure (a). The yield strength and ultimate tensile strength of the MEA aged at 800°C for 12 h were measured to be ∼1 GPa and ∼1.4 GPa. In addition, the fracture elongation is approximately 33%. In addition, Fig. S6 shows the tensile properties of the MEA aged at 700°C and 750°C and Fig. S7 exhibits the fracture graphs for the failed samples at room temperature tensile test. To highlight the superior combination of mechanical properties and thermal stability of the Ni58Cr23Fe10W5Ti2Ta1Nb1 MEA in the current work, we compare it with other reported D022-strengthened HEAs in Figure (b). We take the temperature that the D022 phase is thermostable as the horizontal axis and the yield strength as the vertical axis. Notably, the current D022 phase shows great superiority by being not only stable at a higher temperature but also stronger than those reported HEAs and superalloys. We also evaluated the thermal response of the Ni58Cr23Fe10W5Ti2Ta1Nb1 MEA aged at 800°C for 12 h by measuring the variation in yield strength at elevated temperatures in Fig. S8, and a yield strength about 800 MPa is maintained at temperatures from 600°C to 700°C. Fig. S9 shows the fracture graphs for the failed samples at high temperature tensile test.
Figure 4. (a) Room-temperature tensile stress–strain curves of the MEA aged at 800°C for different times, (b) The comparative results of yield strength and annealing temperature with the reported D022-strengthened HEAs and superalloys, Ni2.1CoCrFe0.5Nb0.2 [Citation40], CoCrFeNiNb0.25 [Citation9], Ni2.1CoCrFe0.5Nb0.2 [Citation41], Cr22Co22Ni48Nb4V4 [Citation42], Ni2CrCoNb0.15 [Citation43], CoCrNi1.5Nb0.2 [Citation44], Ni66Cr26W6Ti2 [Citation45], Ni57.6Cr19.2Fe19.2Nb4 [Citation46], Inconel 625[Citation47], Inconel 718[Citation48].
![Figure 4. (a) Room-temperature tensile stress–strain curves of the MEA aged at 800°C for different times, (b) The comparative results of yield strength and annealing temperature with the reported D022-strengthened HEAs and superalloys, Ni2.1CoCrFe0.5Nb0.2 [Citation40], CoCrFeNiNb0.25 [Citation9], Ni2.1CoCrFe0.5Nb0.2 [Citation41], Cr22Co22Ni48Nb4V4 [Citation42], Ni2CrCoNb0.15 [Citation43], CoCrNi1.5Nb0.2 [Citation44], Ni66Cr26W6Ti2 [Citation45], Ni57.6Cr19.2Fe19.2Nb4 [Citation46], Inconel 625[Citation47], Inconel 718[Citation48].](/cms/asset/bdf0eadb-db67-45e4-bbc3-cb7efddbf6d6/tmrl_a_2309271_f0004_oc.jpg)
In summary, we developed a new D022-strengthened Ni58Cr23Fe10W5Ti2Ta1Nb1 MEA and investigated its thermostability using SEM, TEM, and CALPHAD. Exceptionally, a new D022 phase with a stoichiometry of Ni3(W0.24Ti0.38Ta0.19Nb0.19) precipitates from the FCC matrix and stably exists after aging for up to 720 h at 800°C. The coarsening behavior of this newly developed D022 phase was controlled by Lifshitz-Slyozov-Wagner (LSW) theory. We attributed this excellent coarsening resistance to the low diffusivity of W and the extremely small lattice misfit between the D022 phase and FCC matrix. Furthermore, the Ni3(W0.24Ti0.38Ta0.19Nb0.19)-D022 phase shows superior strengthening effect even after long-term thermal exposure at 800°C. These findings provide the possibility to design high performance D022-strengthened alloys with excellent thermal stability.
Supplemental Material
Download MS Word (4.5 MB)Disclosure statement
No potential conflict of interest was reported by the author(s).
Additional information
Funding
References
- Gludovatz B, Hohenwarter A, Catoor D, et al. A fracture-resistant high-entropy alloy for cryogenic applications. Science. 2014;345(6201):1153–1158. doi:10.1126/science.1254581
- Hilhorst A, Jacques PJ, Pardoen T. Towards the best strength, ductility, and toughness combination: high entropy alloys are excellent, stainless steels are exceptional. Acta Mater. 2023;260:119280. doi:10.1016/j.actamat.2023.119280
- Yang B, Ma L, Zhao P. Effect of boron on the microstructure and mechanical properties of as-cast and annealed CrFeNi medium-entropy alloys. Mater. Sci. Eng.: A. 2023;863:144524. doi:10.1016/j.msea.2022.144524
- Miracle DB, Senkov ON. A critical review of high entropy alloys and related concepts. Acta Mater. 2017;122:448–511. doi:10.1016/j.actamat.2016.08.081
- Lin K-H, Tseng C-M, Chueh C-C, et al. Different lattice distortion effects on the tensile properties of Ni-W dilute solutions and CrFeNi and CoCrFeMnNi concentrated solutions. Acta Mater. 2021;221:117399. doi:10.1016/j.actamat.2021.117399
- Huang H, Wang J, Yang H, et al. Strengthening CoCrNi medium-entropy alloy by tuning lattice defects. Scr. Mater. 2020;188:216–221. doi:10.1016/j.scriptamat.2020.07.027
- Sun SJ, Tian YZ, Lin HR, et al. Transition of twinning behavior in CoCrFeMnNi high entropy alloy with grain refinement. Mater. Sci. Eng.: A. 2018;712:603–607. doi:10.1016/j.msea.2017.12.022
- Zhao YL, Yang T, Li YR, et al. Superior high-temperature properties and deformation-induced planar faults in a novel L12-strengthened high-entropy alloy. Acta Mater. 2020;188:517–527. doi:10.1016/j.actamat.2020.02.028
- He F, Chen D, Han B, et al. Design of D022 superlattice with superior strengthening effect in high entropy alloys. Acta Mater. 2019;167:275–286. doi:10.1016/j.actamat.2019.01.048
- Lin M, Yang Z, Shi X, et al. Effective combination of solid solution strengthening and precipitation hardening in NiCrFeWTiAl multi-principal element alloys. J. Alloys Compd. 2023;933:167738. doi:10.1016/j.jallcom.2022.167738
- Haftlang F, Kim HS. A perspective on precipitation-hardening high-entropy alloys fabricated by additive manufacturing. Mater. Des. 2021;211:110161. doi:10.1016/j.matdes.2021.110161
- Gong X, Xu W-W, Cui C, et al. Exploring alloying effect on phase stability and mechanical properties of γ″-Ni3Nb precipitates with first-principles calculations. Mater. Des. 2020;196:109174. doi:10.1016/j.matdes.2020.109174
- He F, Wang Z, Wang J, et al. Abnormal γ″ - ϵ phase transformation in the CoCrFeNiNb0.25 high entropy alloy. Scr. Mater. 2018;146:281–285. doi:10.1016/j.scriptamat.2017.12.009
- Shi R, McAllister DP, Zhou N, et al. Growth behavior of γ'/γ'’ coprecipitates in Ni-Base superalloys. Acta Mater. 2019;164:220–236. doi:10.1016/j.actamat.2018.10.028
- Pickering EJ, Mathur H, Bhowmik A, et al. Grain-boundary precipitation in Allvac 718Plus. Acta Mater. 2012;60(6):2757–2769. doi:10.1016/j.actamat.2012.01.042
- Theska F, Nomoto K, Godor F, et al. On the early stages of precipitation during direct ageing of Alloy 718. Acta Mater. 2020;188:492–503. doi:10.1016/j.actamat.2020.02.034
- Fu SH, Dong JX, Zhang MC, et al. Alloy design and development of INCONEL718 type alloy. Mater. Sci. Eng.: A. 2009;499(1):215–220.
- Detor AJ, DiDomizio R, Sharghi-Moshtaghin R, et al. Enabling large superalloy parts using compact coprecipitation of γ′ and γ′′. Metall Mater Trans A. 2018;49(3):708–717. doi:10.1007/s11661-017-4356-7
- Qiao Z, Li C, Zhang H-j, et al. Evaluation on elevated-temperature stability of modified 718-type alloys with varied phase configurations. Int. J. Miner. Metall. 2020;27(8):1123–1132. doi:10.1007/s12613-019-1949-8
- Cozar R, Pineau A. Morphology of y’ and y” precipitates and thermal stability of inconel 718 type alloys. Metallurgical Transactions. 1973;4(1):47–59. doi:10.1007/BF02649604
- Mignanelli PM, Jones NG, Pickering EJ, et al. Gamma-gamma prime-gamma double prime dual-superlattice superalloys. Scr. Mater. 2017;136:136–140. doi:10.1016/j.scriptamat.2017.04.029
- Kobayashi S, Sato K, Hayashi E, et al. Alloying effects on the phase equilibria among Ni(A1), Ni3Al(L12) and Ni3 V(D022) phases. Intermetallics. 2012;23:68–75. doi:10.1016/j.intermet.2011.12.008
- Xiong ZY, Xu WW, Gong XG, et al. Accelerating optimization of IN718 by mapping alloying effects on phase stabilities and mechanical properties using high-throughput calculations. Mater. Des. 2022;217:110603. doi:10.1016/j.matdes.2022.110603
- Gao X, Hu R, Luo G. The effect of Ti on precipitation of fully coherent DO22 superlattice in an Ni-Cr-W-based superalloy. Scr. Mater. 2017;134:15–19. doi:10.1016/j.scriptamat.2017.02.037
- Jain H, Shadangi Y, Chakravarty D, et al. Low-density Fe40Mn19Ni15Al15Si10C1 high entropy steel processed by mechanical alloying and spark plasma sintering: Phase evolution, microstructure and mechanical properties. Mater. Sci. Eng.: A. 2023;869:144776. doi:10.1016/j.msea.2023.144776
- Jain H, Shadangi Y, Chakravarty D, et al. High entropy steel processed through mechanical alloying and spark plasma sintering: alloying behaviour, thermal stability and mechanical properties. Mater. Sci. Eng.: A. 2022;856:144029. doi:10.1016/j.msea.2022.144029
- Streitenberger P. Analytical description of phase coarsening at high volume fractions. Acta Mater 2013;61(13):5026–5035. doi:10.1016/j.actamat.2013.04.042
- Xia GH, Ma ZL, Xu ZQ, et al. Novel high-entropy alloys with high-density ϵ-D019 and abnormal phase transformation. Scr. Mater. 2021;199:113893. doi:10.1016/j.scriptamat.2021.113893
- Li RB, Yao M, Liu WC, et al. Isolation and determination for δ, γ′ and γ″ phases in Inconel 718 alloy. Scr. Mater. 2002;46(9):635–638. doi:10.1016/S1359-6462(02)00041-6
- Jouiad M, Marin E, Devarapalli RS, et al. Microstructure and mechanical properties evolutions of alloy 718 during isothermal and thermal cycling over-aging. Mater. Des. 2016;102:284–296. doi:10.1016/j.matdes.2016.04.048
- Jianxin D, Xishan X, Shouhua Z. Coarsening behavior of γ″ precipitates in modified inconel 718 superalloy. Scr Metall Mater. 1995;33(12):1933–1940. doi:10.1016/0956-716X(95)00446-3
- Han Y-f, Deb P, Chaturvedi MC. Coarsening behaviour of γ″- and γ′-particles in Inconel alloy 718. Met Sci. 1982;16(12):555–562. doi:10.1179/030634582790427118
- Yang T, Zhao YL, Liu WH, et al. Ductilizing brittle high-entropy alloys via tailoring valence electron concentrations of precipitates by controlled elemental partitioning. Mater. Res. Lett. 2018;6(10):600–606. doi:10.1080/21663831.2018.1518276
- Sudbrack CK, Ziebell TD, Noebe RD, et al. Effects of a tungsten addition on the morphological evolution, spatial correlations and temporal evolution of a model Ni–Al–Cr superalloy. Acta Mater. 2008;56(3):448–463. doi:10.1016/j.actamat.2007.09.042
- Campbell CE, Boettinger WJ, Kattner UR. Development of a diffusion mobility database for Ni-base superalloys. Acta Mater. 2002;50(4):775–792. doi:10.1016/S1359-6454(01)00383-4
- Zhang RY, Qin HL, Bi ZN, et al. γ″ variant-sensitive deformation behaviour of Inconel 718 superalloy. J. Mater. Sci. Technol. 2022;126:169–181. doi:10.1016/j.jmst.2022.03.018
- Lu W, Luo X, Huang B, et al. Excellent thermal stability and their origins in γ′ precipitation-strengthened medium-entropy alloys. Scr. Mater. 2022;212:114576. doi:10.1016/j.scriptamat.2022.114576
- Zhuang X, Antonov S, Li L, et al. Effect of alloying elements on the coarsening rate of γʹ precipitates in multi-component CoNi-based superalloys with high Cr content. Scr. Mater. 2021;202:114004. doi:10.1016/j.scriptamat.2021.114004
- He F, Zhang K, Yeli G, et al. Anomalous effect of lattice misfit on the coarsening behavior of multicomponent L12 phase. Scr. Mater. 2020;183:111–116. doi:10.1016/j.scriptamat.2020.03.030
- Wang F, Guo Y, Liu Q, et al. A novel D022 precipitation-hardened Ni2.1CoCrFe0.5Nb0.2 high entropy alloy with outstanding tensile properties by additive manufacturing. Virtual Phys Prototyp. 2023;18(1):e2147553. doi:10.1080/17452759.2022.2147553
- Zhou K, Wang Z, He F, et al. A precipitation-strengthened high-entropy alloy for additive manufacturing. Addit. Manufact. 2020;35:101410. doi:10.1016/j.addma.2020.101410
- Pan Y, Dong A, Zhou Y, et al. Enhanced strength-ductility synergy in a novel V-containing γ″-strengthened CoCrNi-based multi-component alloy. Mater. Sci. Eng.: A. 2021;816:141289. doi:10.1016/j.msea.2021.141289
- Xue P, Zhu L, Xu P, et al. Effect of heat treatment on microstructure and mechanical properties of in-situ synthesized Ni2CrCoNb0.16 multi-principal element alloy manufactured by directed energy deposition. Mater. Sci. Eng.: A. 2023;862:144398. doi:10.1016/j.msea.2022.144398
- Zhou H, Lin Y, Chen F, et al. Effect of precipitation behavior on mechanical properties of a Nb-containing CoCrNi-based high-entropy alloy. Met. Mater. Int. 2023;29(3):674–692. doi:10.1007/s12540-022-01265-x
- Gao X, Hu R, Yang J. The effect of Ni3(Cr0.2W0.4Ti0.4) particles with DO22 structure on the deformation mode and mechanical properties of the aged Ni-Cr-W-Ti alloy. Scr. Mater. 2018;153:44–48. doi:10.1016/j.scriptamat.2018.04.029
- Lu W, Luo X, Yang Y, et al. Co-free non-equilibrium medium-entropy alloy with outstanding tensile properties. J. Alloys Compd. 2020;833:155074. doi:10.1016/j.jallcom.2020.155074
- Marchese G, Lorusso M, Parizia S, et al. Influence of heat treatments on microstructure evolution and mechanical properties of Inconel 625 processed by laser powder bed fusion. Mater. Sci. Eng.: A. 2018;729:64–75. doi:10.1016/j.msea.2018.05.044
- Kermani F, Shoja-Razavi R, Zangenemadar K, et al. An investigation into the effect of scanning pattern and heat treatment on the mechanical properties of Inconel 718 in the direct metal deposition process. J. Mater. Res. Technol. 2023;24:4743–4755. doi:10.1016/j.jmrt.2023.04.109