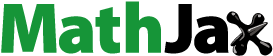
Abstract
The creep mechanism of a Co-based single-crystal (SX) superalloy at 760°C/800 MPa (∼90% yield strength) was revealed and differed from those of Re-containing Ni-based SX superalloys. Experimental alloy displays superior creep resistance in the early creep stage, likely due to the accumulation of matrix dislocations and W segregation-assisted shearing of γ′ phase by leading Shockley partial dislocations instead of Co and Cr segregation a < 112> SF ribbons in Re-containing Ni-based SX superalloys during the accelerating creep stage. Segregation-assisted local χ/η phase transformations at SFs stabilize and enhance SF interactions, contributing to the subsequent slow accelerating creep stage.
1. Introduction
The discovery of γ′-strengthened Co-based superalloys has attracted much attention due to the analogous γ/γ′ microstructure and higher melting temperature compared to the widely used Ni-based superalloys [Citation1–4] for the aero-engines or gas turbines. Good creep performance in wide temperature (700∼1200°C) and stress (100∼800 MPa) ranges is required due to the harsh operation environment [Citation5–7]. In some Re-containing Ni-based single-crystal (SX) superalloys, the creep behavior at low temperature/high stress (especially 80∼90% yield strength) is different from that at high temperature/low stress by generating a high primary creep strain (ε>3%), occurred before the steady or secondary creep stage, instead of minor strain (ε<0.5%) in the early creep stage [Citation6,Citation8,Citation9]. This is crucial for the safety service of high-temperature engineering components. Until now, much research has been performed for the compositional optimization [Citation10–12] and creep mechanism at high temperatures (>850°C) [Citation12–15] of γ′-strengthened Co-based SX superalloys. Limited research has been reported on the creep performance at low temperatures/high stress [Citation16,Citation17].
Until now, two types of γ′-strengthened Co-based alloys have been mainly developed, such as the Co-Al-W-based (abbreviated as Co-based) and engineering-oriented CoNi-based superalloys featured by the Ni addition (∼30at.%) and the reduction of W [Citation10,Citation11,Citation18,Citation19]. Both exhibit comparable creep properties with the 1st-generation Ni-based SX superalloys at high temperatures. While the Co-based SX superalloy shows a different creep performance from the CoNi-based SX superalloy at 760°C and similar equivalent stresses (∼90% yield strength) in our previous research [Citation17,Citation20]. In the early creep stage, minimal primary creep strain (ε<0.15%) was observed in the Co-based SX superalloy, and no local maximum creep rate was detected as the CoNi- or Re-containing Ni-based SX superalloys [Citation5,Citation21] after the initial local minimum creep rate, indicating a superior creep resistance. The initial creep performance of the Co-based SX superalloy is close to 1st-generation Ni-based SX superalloys [Citation22–24]. However, the preliminary work [Citation17] was only performed at a lower creep strain (ε<∼1%), which may be too low to capture the overall creep features in Co-based SX superalloys.
In addition, considering the compositional features among the Co-, CoNi- and Ni-based superalloys, the variation of formation energies, such as stacking faults (SFs), including complex and superlattice intrinsic/extrinsic stacking faults (CISF/SESF and SISF/SESF), and anti-phase boundaries (APBs), also affect the creep performance. Some researchers have found that the creep resistance of Ni-based superalloys is significantly improved after the local χ/η phase transformations at SISF/SESF [Citation25–27]. This may also contribute to the creep resistance of Co-based SX superalloys at 760°C/high stress. Moreover, how they affect the subsequent evolution of deformation substructures is critical to understanding the creep mechanism at a higher strain.
Thus, combined with our preliminary work [Citation17,Citation20] this study investigated a completed creep behavior of a Co-based SX superalloy at 760°C and ∼90% yield strength to make a reasonable comparison, different yield strengths considered, with the existing research in Ni-based SX superalloys [Citation8,Citation23,Citation28]. The superior creep resistance in the early creep stage was analyzed based on the interaction between γ/γ′ microstructure and deformation substructure. Meanwhile, the effect of elemental segregations at the SFs on the evolution of the deformation substructures was also discussed. This work is meaningful for thoroughly understanding the creep mechanisms in different types of γ′-strengthened superalloys and improving the creep resistance of engineering-oriented CoNi-based superalloys.
2. Materials and methods
Details of the casting procedure, sample preparation and initial γ/γ′ microstructure of the experimental Co-7Al-8W-1Ta-4Ti (at.%) SX superalloy, alloy TaTi, have been previously reported in our previous work [Citation13,Citation17,Citation29–31]. The specimens with [001] orientation (3.4∼10.1° deviation) were tensile-creep deformed at 760°C/800 MPa (∼90% yield strength) [Citation17]. The microstructural parameters, such as the volume fraction (Vγ′), area equivalent diameter (dγ′)/raft thickness (Dγ′) of the γ′ phase and the width of γ channel (Dγ), were analyzed by a ZEISS SUPRA 55 field emission scanning electron microscope (SEM). In contrast, the deformation substructures were observed using a JEOL JEM-2200FS transmission electron microscope (TEM) operating at 200 kV in the scanning TEM (STEM) mode. Some deformation substructures were also investigated using a probe-corrected Titan Themis3 TEM operating at 300 kV with a Super-X detector for the high-resolution images and energy-dispersive X-ray spectroscopy (EDX) analysis [Citation32].
3. Results and discussion
Figure compares creep curves between the alloy TaTi and a Re-containing CMSX-4 type alloy (ERBO/1-3Re) [Citation5] at ∼760°C/800 MPa. The creep life of alloy TaTi was ∼854 h (ε = ∼11%), as shown in Figure (a). The relatively low ruptured creep strain can be ascribed to the high Vγ′ and the commonly observed brittleness of the ordered γ′ phase at ∼760°C [Citation2,Citation6]. In contrast, the creep life of ERBO/1-3Re is ∼530 h, lower than alloy TaTi. Meanwhile, a high primary creep strain (∼3%) was observed in ERBO/1-3Re before the steady or secondary creep stage [Citation33]. Very limited primary creep strain (ε<0.15%) was detected in alloy TaTi (See detail in Supplementary Materials-Figure S1). Figure (b) shows that the creep rate of alloy TaTi decreased to ∼2.8 × 10−9s−1 with ε = ∼0.08% (t = ∼60 h) in the decelerating creep stage (I) and dramatically increased to ∼1.2 × 10−8s−1 with a higher speed until ε = ∼0.3% (t = ∼122 h) in the accelerating creep stage (II). Subsequently, the slope between the creep rate and time decreased obviously, and the creep rate slowly increased until the creep fractured, defined as the slow accelerating creep stage (III). This process is analogous to some 1st-generation Ni-based SX superalloys [Citation22–24] but differs from the commonly observed double minimum creep behavior in ERBO/1-3Re [Citation5] and other Re-containing Ni- [Citation8,Citation9,Citation23,Citation34] or CoNi-based SX superalloys [Citation17,Citation20] at low temperature/high stress. It is also similar to the cases at 900°C/420 MPa [Citation30,Citation35] and 1000°C/137 MPa [Citation13,Citation29] in alloy TaTi, a W-free CoNi-based superalloy at 800∼900°C/200∼500 MPa [Citation36], or a W-containing CoNi-based superalloy [Citation14] at 850°C/400 MPa. To address these concerns, four interrupted tests (ε = ∼0.06%, ∼0.2%, ∼1% and ∼5%) were performed as labeled by the solid circles in Figure (b). Details about the reproducibility of creep curves can be referred to the Supplementary Materials-Figure S2.
Figure 1. Comparison of creep curves between the alloy TaTi and a Re-containing CMSX-4 type alloy (ERBO/1-3Re) [Citation5] at ∼760°C/800 MPa. (a) Creep strain vs. time; (b) creep rate vs. creep strain.
![Figure 1. Comparison of creep curves between the alloy TaTi and a Re-containing CMSX-4 type alloy (ERBO/1-3Re) [Citation5] at ∼760°C/800 MPa. (a) Creep strain vs. time; (b) creep rate vs. creep strain.](/cms/asset/0eadb6ba-3bec-4001-a271-6b870c6423f4/tmrl_a_2362288_f0001_oc.jpg)
Figure shows the typical γ/γ′ microstructures of alloy TaTi at 760°C/800 MPa with different creep times and strains. The γ′ precipitates remained cuboidal, and the features of the γ/γ′ microstructures were similar from the decelerating creep stage to the onset of the slow accelerating stage. Thus, only the γ/γ′ microstructure at t = ∼160 h and ε = ∼1% was shown in this study (Figure (a1) and (b1)). Subsequently, the directional coarsening and connection process along the tensile axis-[001] began due to the positive γ/γ′ misfit [Citation29,Citation30]. Labyrinth-like γ/γ′ microstructure [Citation37] formed in the horizontal sections, as shown in Figure (a2) and (a3). Concurrently, the P-type rafting microstructure [Citation30] started to form. The γ channels normal to the [001] direction gradually disappeared until creep rupture. Some γ channels were even enclosed by the γ′ precipitates, as viewed from the longitudinal sections (Figure (b2) and (b3)). Overall, the Vγ′ remained stable, while the dγ′/Dγ′ and the Dγ slightly increased as the creep proceeded, as listed in Table .
Figure 2. SEM images showing the typical γ/γ′ microstructures of alloy TaTi at 760°C/800 MPa with different creep times and strains. (a) horizontal sections; (b) longitudinal sections; (1) ε = ∼1.0%, t = ∼160 h; (2) ε = ∼5%, t = ∼608 h; (3)ε = ∼11%, t = ∼854 h.
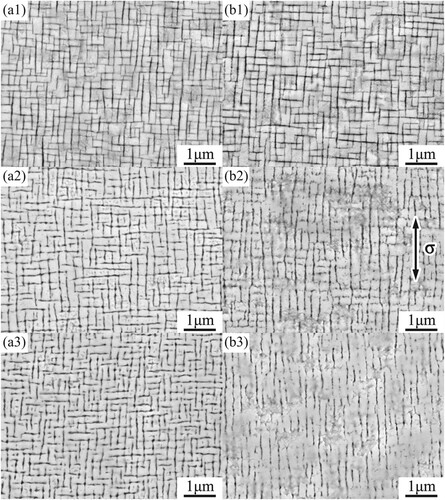
Table 1. Evolution of the volume fraction (Vγ′), area equivalent diameter (dγ′)/raft thickness (Dγ′) of γ′ phase and the width of γ channel (Dγ) during the creep at 760°C/800 MPa in alloy TaTi.
Figure exhibits the typical deformation substructures of alloy TaTi at 760 °C/800 MPa in different creep stages with a beam direction (B) of [100]. In the decelerating creep stage (ε = ∼0.06%), it was dominated by the unevenly distributed dislocations cross slipped in γ channels or at γ/γ′ interfaces as well as SFs occasionally observed in γ′ precipitates, as shown in Figure (a). In contrast, dislocations tangled in γ channels and individual SFs expanding through the γ/γ′ microstructure were prevalent in the accelerating creep stage at ε = ∼0.2% (Figure (b)). After that, the creep process was governed by the high density of dislocation networks and SF interactions at the onset of the slow accelerating creep stage (ε = ∼1%, Figure (c)). As the creep proceeded, the density of dislocation networks and SF interactions further increased (ε = ∼5%, Figure (d)) in the rafting microstructure until creep fracture (not shown in this study). Rare APBs were observed in γ′ precipitates throughout the creep process.
Figure 3. STEM images showing the typical deformation substructures of alloy TaTi at 760°C/800 MPa in different creep stages, B = [100]. (a) decelerating creep stage, ε = ∼0.06%; (b) accelerating creep stage, ε = ∼0.2%; slow accelerating creep stage at (c) ε = ∼1% and (d) ε = ∼5%.
![Figure 3. STEM images showing the typical deformation substructures of alloy TaTi at 760°C/800 MPa in different creep stages, B = [100]. (a) decelerating creep stage, ε = ∼0.06%; (b) accelerating creep stage, ε = ∼0.2%; slow accelerating creep stage at (c) ε = ∼1% and (d) ε = ∼5%.](/cms/asset/aa777f58-6dd1-4321-a17f-9ff178fb32e2/tmrl_a_2362288_f0003_ob.jpg)
Types of all SFs in γ′ precipitates were determined to be SISF or SESF. Figure exhibits the HAADF-STEM image and corresponding EDX elemental mapping (at.%) of a SISF at 760°C/800 MPa with ε = ∼1% (t = ∼160 h), B = [110]. The elemental segregation behavior is similar to the cases at 900°C [Citation38,Citation39] and 1000°C [Citation31,Citation40]. W was observed to enrich at the SISF, indicating a local χ phase transformation by the ordered lattice stacking sequences [Citation38], while Co and Al were depleted. No apparent segregation behavior was detected for Ta and Ti compared to the surrounding γ′ region. The SISF and SESF have similar elemental segregation behavior.
Figure 4. HAADF-STEM image and corresponding EDX elemental mapping (at.%) of a SISF at 760°C/800 MPa with ε = ∼1% (t = ∼160 h), B = [110].
![Figure 4. HAADF-STEM image and corresponding EDX elemental mapping (at.%) of a SISF at 760°C/800 MPa with ε = ∼1% (t = ∼160 h), B = [110].](/cms/asset/62e4a79e-f54d-49d9-b0c0-7e165fbae51a/tmrl_a_2362288_f0004_oc.jpg)
The results above indicate that alloy TaTi exhibits similar creep mechanisms in a wide temperature range (760∼1000°C) at their typical stresses [Citation13,Citation30]. Dislocation movements in the γ matrix dominate the initial decelerating creep stage. After the shearing of γ′ precipitates by the leading partial dislocations of SFs, the creep rate rapidly increases (accelerating creep stage). Subsequently, the SF interactions strengthen the γ′ precipitates and contribute to the following global steady-state [Citation13,Citation30] or the slow accelerating creep stages in this study.
Table lists the creep properties of various SX superalloys at ∼760 °C/high stress (80%∼90% yield strength). Compared to the widely reported Ni-based SX superalloys [Citation5,Citation8,Citation9,Citation23,Citation24,Citation28,Citation34], alloy TaTi is characterized by a longer time for ε = 1%, indicating a high creep resistance in the early creep stage, and rupture life. In addition, it is noteworthy that alloy TaTi exhibits a similar creep behavior with Re-free 1st-generation Ni-based SX superalloys [Citation23], which is different from some Re-containing superalloys (2nd∼4th generation) [Citation5,Citation23,Citation34] by the limited primary creep strain and absence of local maximum creep rate, also called as primary creep rate, in the early creep stage (Figure ). High primary creep strain (>2%) occurs within a short period (primary creep time).
Figure 5. Schematic diagram of the interactions between γ/γ′ microstructures and deformation substructures in different creep stages of (a) ERBO/1-3Re [Citation5] and (b) alloy TaTi at low temperature/high stress. (1) accelerating, (2) middle and (3) late stages of the creep process.
![Figure 5. Schematic diagram of the interactions between γ/γ′ microstructures and deformation substructures in different creep stages of (a) ERBO/1-3Re [Citation5] and (b) alloy TaTi at low temperature/high stress. (1) accelerating, (2) middle and (3) late stages of the creep process.](/cms/asset/d79b931e-5980-4a5a-9c71-ca7df2dcb880/tmrl_a_2362288_f0005_oc.jpg)
Table 2. Creep properties of various single-crystal superalloys at ∼760 °C/high stress (80%∼90% yield strength) [Citation5,Citation23,Citation34].
Due to the similar creep performance between Re-containing Ni-based SX superalloys, this study selected ERBO/1-3Re as an example to compare with alloy TaTi (similar to Re-free Ni-based SX superalloys). The deformation substructures in γ′ phase of the two alloys differ during the critical creep stages [Citation5,Citation17,Citation20,Citation28], as listed in Table . Figure shows the two creep rate curves normalized by their ruptured strains (to compare curve shape conveniently). Obviously, their creep behaviors have differed since the start of the accelerating creep stage.
Table 3. Evolution of substructures in γ′ phase of different SX superalloys during the critical creep stages at low temperature/high stress [Citation5,Citation28].
3.1. Formation of accelerating creep stage
It is almost a consensus in Ni-based SX superalloys that the accelerating creep stage results in the high primary creep strain due to the activation of coplanar a < 112 > SF ribbons in the γ′ phase [Citation8,Citation9]. For ERBO/1-3Re [Citation41,Citation42], the ribbons (SISF-APB-SESF, Figure (a1)) shear through the γ/γ′ microstructure at 750°C/800 MPa. To simplify the schematics, the SISF and SESF are labeled with the same red lines in Figure . After the movement of trailing partial dislocation of SESF, the γ′ lattice is restored without introducing extra defects. In contrast, the shearing of γ′ phase by the leading Shockley partial dislocation contributes to the rapid increase of creep rate in alloy TaTi [Citation31,Citation40]. Individual SFs form trailing the Shockley partial dislocation (Figure (b1)). Compared to ERBO/1-3Re, extra energy is required to overcome the constant increase of SF regions.
On the other hand, the a < 112 > type dislocations in the Ni-based SX superalloys are thought to originate from the fundamental synthesis reaction of two dislocations with different Burger vectors: a/2 < 011>+a/2 < 101>→a/2 < 112>→a/3 < 112>+SISF/SESF + a/6 < 112> [Citation8,Citation9,Citation22]. This is an energetically favorable process that can even be self-activated due to the reduction of lattice distortion energy and the low-energy state of SISF/SESF [Citation22]. In our previous work [Citation31,Citation40], the dissociation reaction of matrix dislocation (a/2 < 011>→a/6<
12>+CISF + a/6 < 121>) is prevalent in alloy TaTi, generating the Shockley partial dislocation shearing the γ′ phase. However, due to the high-energy state of the CISF, this process is less favorable than the synthesis reaction in Ni-based SX superalloys. Local elemental segregation at the CISF is needed to further the shearing process.
Based on the dislocation analysis above, the γ′ shearing process by the coplanar a < 112> SF ribbons in the Ni-based SX superalloys seems more favorable than by the leading Shockley partial dislocation investigated Co-based SX superalloys. Although the equivalent stress level has been considered based on the corresponding yield strength, it is still challenging to quantify the difference in the accelerating creep stages of two types of alloys, even for the different Ni-based SX superalloys only [Citation23]. According to the Ni-based SX superalloys [Citation21–23], the large amplitude of primary creep is unambiguously associated with heterogeneous deformation involving shearing of the γ′ precipitates, while the accumulation of matrix dislocations due to the Orowan mechanism promotes a rapid and strong hardening of the alloy that limits the primary creep rate and strain. Besides the dislocation reactions, the competition between the two mechanisms also depends on the interaction of multiple factors, such as γ/γ′ microstructure, relative strength between γ and γ′ phases and misfit.
In terms of the γ/γ′ microstructure, both alloys have high Vγ′. Moreover, the Vγ′ of alloy TaTi (∼80%) is higher than that of ERBO/1-3Re (∼75%) [Citation41] and almost all the Ni-based superalloys [Citation6], which results in the narrower Dγ and the corresponding higher Orowan stress for the dislocation by-passing the γ′ precipitates. This tends to restrain the dislocation hardening of the γ phase. However, cross-slipped and tangled matrix dislocations (Figure (a) and (b)) were observed in alloy TaTi, which indicates a good γ hardening effect. Obviously, the difference of γ/γ′ microstructure between the two alloys cannot explain the suppression of primary creep strain (Table ) in alloy TaTi.
For the relative strength between γ and γ′ phases, the excellent solution-strengthening effect of Re in Ni-based SX superalloys has been widely accepted, which improves the deformation resistance of γ matrix and contributes to the primary creep strain, as indicated in Table . In addition, Co and Re are also assumed to decrease the SF energy of the alloy, thus promoting the γ′ shearing process [Citation33]. However, some results also indicate that the Re-free alloys have an SF energy comparable to the Re-containing alloys [Citation23]. In alloy TaTi, the main strengthening elements (W, Ta and Ti) have been investigated to segregate towards the γ′ phase [Citation31]. This induces a lower solution-strengthening effect, which favors the dislocation movements in the γ matrix, limiting the primary creep strain. In contrast, W tends to be distributed uniformly in the Ni-based SX superalloys with/without Re addition [Citation26,Citation27]. Hence, the relative strength between γ and γ′ phases in alloy TaTi is assumed to be lower than ERBO/1-3Re and other Ni-based SX superalloys.
The misfit stress comes from the difference of γ/γ′ lattice parameters. At the beginning of creep deformation, the local stress in the γ channel is a superposition of the external and misfit stresses. The high misfit has been verified to promote matrix dislocation spreading when external stress is applied [Citation36]. A similar case can be found in the 4th-generation Ni-based SX superalloys, where the primary creep strain is significantly reduced at 760°C/840 MPa with increased misfit [Citation23]. Compared to Ni-based superalloys, Co-based superalloys [Citation29] usually exhibit higher absolute misfits due to the lower elastic modulus of γ and γ′ phases [Citation43]. In alloy TaTi, the misfit is measured to be +0.95% at 900°C [Citation30] and +0.44% at 1000°C [Citation29]. Thus, a misfit of >+0.95%, higher than typical Ni-based SX superalloys [Citation44], is expected at 760°C. Accordingly, combined with the low relative strength between γ and γ′ phases mentioned before, the high density of matrix dislocations in alloy TaTi in the early creep stage can be rationalized, so does the limited primary creep strain. More work is underway to further explain the superior creep resistance in alloy TaTi.
3.2. Elemental segregation on the evolution of deformation substructure
In addition, some researchers have proposed that the elemental segregation at SFs also affects the shearing process of γ′ phase by the Suzuki lock mechanism on <112> 111 slip [Citation45]. As shown in Table and Figure , the evolutions of deformation substructures in the two alloys differ during creep. Especially during the late creep stage, dislocation pairs (Figure (a3)) and SF interactions (Figure (b3)) govern the creep deformation in the ERBO/1-3Re and alloy TaTi, respectively. Moreover, the elemental segregations at SFs in the two alloys also differ, as shown in the right arrow of Figure . Thus, how the elemental segregations affect the evolution of deformation substructures is critical for understanding the creep mechanism in different γ′-strengthened superalloys.
Co and Cr are commonly enriched at the SISF/SESF in ERBO/1-3Re [Citation5], while W is for alloy TaTi. The former prefers to induce the γ phase transformation, which favors the shearing of γ′ phase by the a < 112> SF ribbons and primary creep strain. Subsequently, the interfacial dislocation becomes stable with the increased strain, making it challenging to react to new a < 112 > dislocations or SF ribbons [Citation8,Citation28]. Moreover, the expansion of pre-existing SF ribbons will be terminated by the dense γ/γ′ interfacial dislocations and recombine into the a < 112 > dislocations. Thus, dislocation pairs dominate the late creep stage, and SF density significantly decreases (Figure (a3)) [Citation5,Citation28]. Additionally, in some research on Ni-based superalloys [Citation25,Citation26], the stability of the SF configurations is thought to be correlated with their local elemental segregation. W, Ti or Ta enrichment stabilizes the SF configurations by triggering the local phase transformation. The addition of Ta has been reported to stabilize the SF configurations in the late creep stage and reduce the primary creep strain in a Re-containing Ni-based SX superalloy [Citation21]. More in-situ work is needed to explain the evolution of SF density in Ni-based superalloys. Differently, W segregation in alloy TaTi contributes to the CISF/CESF→SISF/SESF→χ/η transformation [Citation40], which inhibits the shearing of the γ′ phase by trailing partial dislocations and stabilizes the SF configurations. No a < 112> SF ribbon (SISF-APB-SESF) was detected in alloy TaTi. This is also a critical factor limiting the primary creep strain in the accelerating creep stage. Therefore, with the formation of rafting γ/γ′ microstructure (Figure (b2∼b3)), matrix dislocations prefer to dissociate and shear the γ′ phase by the leading Shockley partial dislocations. Thus, the density of SFs increased until the creep rupture in alloy TaTi, as shown in Figure (c2∼c3).
By comparing the two different creep behaviors in the two γ′-strengthened superalloys, the low relative strength between γ and γ′ phases, high misfit and segregation-assisted local χ/η phase transformations at SFs are critical factors for limiting the primary creep strain and improving creep resistance in the early creep stage of alloy TaTi at low temperature/high stress. Our previous work [Citation17,Citation20] and recent research show that the CoNi-based SX superalloys have a creep performance comparable to the ERBO/1-3Re. Thus, similar strategies can be applied to improve their creep resistance in the early creep stage at low temperature/high stress.
4. Conclusion
In this study, the tensile creep performance of a Co-based SX superalloy was systematically revealed for the first time and found to be distinct from those of Re-containing Ni-based SX superalloys by the limited primary creep strain and absence of a local maximum creep rate at ∼760°C and equivalent high stress (80∼90% yield strength). The superior creep resistance in the early creep stage is ascribed to the prevalent dislocation movements in γ channels and W segregation-assisted γ′ shearing process by the leading Shockley partial dislocation instead of Co and Cr segregation a < 112> SF ribbon in Re-containing Ni-based SX superalloys in the accelerating creep stage. Moreover, W segregates at SFs and promotes the local χ/η phase transformations, which stabilizes the SF configurations and enhances the SF interactions after the accelerating creep stage, resulting in the subsequent slow accelerating creep stage.
Supplemental Material
Download MS Word (141.5 KB)Disclosure statement
No potential conflict of interest was reported by the author(s).
Data availability
The raw/processed data required to reproduce these findings cannot be shared at this time as the data also forms part of other ongoing studies.
Additional information
Funding
References
- Sato J, Omori T, Oikawa K, et al. Cobalt-base high-temperature alloys. Science. 2006;312:90–91. doi:10.1126/science.1121738
- Suzuki A, Inui H, Pollock TM. L12-strengthened cobalt-base superalloys. Annu Rev Mater Res. 2015;45:345–368. doi:10.1146/annurev-matsci-070214-021043
- Titus MS, Suzuki A, Pollock TM. Creep and directional coarsening in single crystals of new γ-γ′ cobalt-base alloys. Scr Mater. 2012;66:574–577. doi:10.1016/j.scriptamat.2012.01.008
- Lee CS. Precipitation-hardening characteristics of ternary cobalt-aluminum-X alloys. Tucson: The University of Arizona; 1971.
- Wu X, Makineni SK, Liebscher CH, et al. Unveiling the Re effect in Ni-based single crystal superalloys. Nat Commun. 2020;11:389, doi:10.1038/s41467-019-14062-9
- Reed RC. The superalloys fundamentals and applications. Cambridge: Cambridge University Press; 2006.
- Caron P, et al. High γ′ solvus new generation nickel-based superalloys for single crystal turbine blade applications. In: Pollock TM, Kissinger RD, Bowman RR, editor. Superalloys 2000. Warrendale, PA: TMS; 2000. p. 737–746.
- Rae CMF, Reed RC. Primary creep in single crystal superalloys: origins, mechanisms and effects. Acta Mater. 2007;55:1067–1081. doi:10.1016/j.actamat.2006.09.026
- Rae CMF, Matan N, Reed RC. The role of stacking fault shear in the primary creep of [001]-oriented single crystal superalloys at 750°C and 750 MPa. Mater Sci Eng A. 2001;300:125–134. doi:10.1016/S0921-5093(00)01788-3
- Li W, Li L, Antonov S, et al. Effects of Cr and Al/W ratio on the microstructural stability, oxidation property and γ′ phase nano-hardness of multi-component Co–Ni-base superalloys. J Alloys Compd. 2020;826:154182, doi:10.1016/j.jallcom.2020.154182
- Li W, Li L, Antonov S, et al. High-throughput exploration of alloying effects on the microstructural stability and properties of multi-component CoNi-base superalloys. J Alloys Compd. 2021;881:160618, doi:10.1016/j.jallcom.2021.160618
- Titus MS, Mottura A, Babu Viswanathan G, et al. High resolution energy dispersive spectroscopy mapping of planar defects in L12-containing Co-base superalloys. Acta Mater. 2015;89:423–437. doi:10.1016/j.actamat.2015.01.050
- Lu S, Antonov S, Li LF, et al. Two steady-state creep stages in Co-Al-W-base single-crystal superalloys at 1273 K/137 MPa. Metall Mater Trans A. 2018;49:4079–4089. doi:10.1007/s11661-018-4776-z
- Lenz M, Eggeler YM, Müller J, et al. Tension/compression asymmetry of a creep deformed single crystal Co-base superalloy. Acta Mater. 2019;166:597–610. doi:10.1016/j.actamat.2018.12.053
- Shi L, Yu JJ, Cui CY, et al. The creep deformation behavior of a single-crystal Co-Al-W-base superalloy at 900°C. Mater Sci Eng A. 2015;635:50–58. doi:10.1016/j.msea.2015.03.063
- Titus MS, Rettberg LH, Pollock TM, et al. High temperature creep of γ′-containing CoNi-based superalloys. In: Hardy M, Huron E, Glatzel U, editor. Superalloys 2016. Warrendale, PA: TMS; 2016. p. 141–148.
- Lu S, Luo Z, Li L, et al. Comparison of creep mechanisms between Co-Al-W- and CoNi-based single crystal superalloys at low temperature and high stresses. Metall Mater Trans A. 2023;54:1597–1607. doi:10.1007/s11661-022-06892-y
- Lu S, Zou M, Zhang X, et al. Data-driven “cross-component” design and optimization of γ′-strengthened Co-based superalloys. Adv Eng Mater. 2023;25:2201257, doi:10.1002/adem.202201257
- Li W, Li L, Wei C, et al. Effects of Ni, Cr and W on the microstructural stability of multicomponent CoNi-base superalloys studied using CALPHAD and diffusion-multiple approaches. J Mater Sci Technol. 2021;80:139–149. doi:10.1016/j.jmst.2020.10.080
- Lu S, Luo Z, Lu F, et al. Creep performance in a CoNi-based single crystal superalloy with super-high γ′ volume fraction at 760 °C and equivalent high stress. J Mater Res Technol. 2024;29:4870–4880. doi:10.1016/j.jmrt.2024.02.217
- Ge Z, Xie G, Lu Y, et al. Influence of Ta on the intermediate temperature creep behavior of a single crystal superalloy. Mater Sci Eng A. 2022;831:142160, doi:10.1016/j.msea.2021.142160
- Long H, Liu Y, Kong D, et al. Shearing mechanisms of stacking fault and anti-phase-boundary forming dislocation pairs in the γ′ phase in Ni-based single crystal superalloy. J Alloys Compd. 2017;724:287–295. doi:10.1016/j.jallcom.2017.07.020
- Diologent F, Caron P. On the creep behavior at 1033K of new generation single-crystal superalloys. Mater Sci Eng A. 2004;385:245–257. doi:10.1016/S0921-5093(04)00925-6
- Han GM, Yu JJ, Sun YL, et al. Anisotropic stress rupture properties of the nickel-base single crystal superalloy SRR99. Mater Sci Eng A. 2010;527:5383–5390. doi:10.1016/j.msea.2010.05.051
- Smith TM, Zarkevich NA, Egan AJ, et al. Utilizing local phase transformation strengthening for nickel-base superalloys. Commun Mater. 2021;2:106, doi:10.1038/s43246-021-00210-6
- Smith TM, Good BS, Gabb TP, et al. Effect of stacking fault segregation and local phase transformations on creep strength in Ni-base superalloys. Acta Mater. 2019;172:55–65. doi:10.1016/j.actamat.2019.04.038
- Smith TM, Esser BD, Antolin N, et al. Phase transformation strengthening of high-temperature superalloys. Nat Commun. 2016;7:13434, doi:10.1038/ncomms13434
- Wu X, Wollgramm P, Somsen C, et al. Double minimum creep of single crystal Ni-base superalloys. Acta Mater. 2016;112:242–260. doi:10.1016/j.actamat.2016.04.012
- Xue F, Zhou HJ, Shi QY, et al. Creep behavior in a γ′ strengthened Co–Al–W–Ta–Ti single-crystal alloy at 1000 °C. Scr Mater. 2015;97:37–40. doi:10.1016/j.scriptamat.2014.10.015
- Zhou H, Li L, Antonov S, et al. Sub/micro-structural evolution of a Co-Al-W-Ta-Ti single crystal superalloy during creep at 900°C and 420 MPa. Mater Sci Eng A. 2020;772:138791, doi:10.1016/j.msea.2019.138791
- Lu S, Antonov S, Li LF, et al. Atomic structure and elemental segregation behavior of creep defects in a Co-Al-W-based single crystal superalloys under high temperature and low stress. Acta Mater. 2020;190:16–28. doi:10.1016/j.actamat.2020.03.015
- Hoeft H, Schwaab P. Investigations towards optimizing EDS analysis by the Cliff-Lorimer method in scanning transmission electron microscopy. X-Ray Spectrom. 1988;17:201–208. doi:10.1002/xrs.1300170509
- Drew GL, Reed RC, Kakehi K, et al. Single crystal superalloys: the transition from primary to secondary creep. In: Green KA, Pollock TM, Harada H, editor. Superalloys 2004. Warrendale, PA: TMS; 2004. p. 127–136.
- Qu P, Yang W, Liu C, et al. Creep anisotropy dominated by orientation rotation in Ni-based single crystal superalloys at 750 °C/750 MPa. J Mater Sci Technol. 2024;186:91–103. doi:10.1016/j.jmst.2023.10.055
- Zhou HJ, Chang H, Feng Q. Transient minimum creep of a γ′ strengthened Co-base single-crystal superalloy at 900 °C. Scr Mater. 2017;135:84–87. doi:10.1016/j.scriptamat.2017.03.031
- Sharma A, Mondal C, Makineni SK, et al. Exploring the correlation between microscopic mechanisms and macroscopic behaviour in creep of a directionally solidified tungsten-free γ/γ′ CoNi-base superalloy. Acta Mater. 2022;228:117738, doi:10.1016/j.actamat.2022.117738
- Hobbs RA, Brewster GJ, Rae CMF, et al. Evaluation of ruthenium-bearing single crystal superalloys-a design of experiments. In: Reed RC, Green KA, Caron P, editor. Superalloys 2008. Warrendale, PA: TMS; 2008. p. 171–180.
- Titus MS, Rhein RK, Wells PB, et al. Solute segregation and deviation from bulk thermodynamics at nanoscale crystalline defects. Sci Adv. 2016;2:e1601796, doi:10.1126/sciadv.1601796
- Titus MS, Eggeler YM, Suzuki A, et al. Creep-induced planar defects in L12-containing Co- and CoNi-base single-crystal superalloys. Acta Mater. 2015;82:530–539. doi:10.1016/j.actamat.2014.08.033
- Lu S, Antonov S, Xue F, et al. Segregation-assisted phase transformation and anti-phase boundary formation during creep of a γ′-strengthened Co-based superalloy at high temperatures. Acta Mater. 2021;215:117099, doi:10.1016/j.actamat.2021.117099
- Parsa AB, Wollgramm P, Buck H, et al. Advanced scale bridging microstructure analysis of single crystal Ni-base superalloys. Adv Eng Mater. 2015;17:216–230. doi:10.1002/adem.201400136
- Wollgramm P, Wu X, Eggeler G, et al. On the temperature dependence of creep behavior of Ni-base single crystal superalloys. In: Hardy M, Huron E, Glatzel U, editor. Superalloys 2016. Warrendale, PA: TMS; 2016. p. 711–718.
- Yan H-Y, Coakley J, Vorontsov VA, et al. Alloying and the micromechanics of Co–Al–W–X quaternary alloys. Mater Sci Eng A. 2014;613:201–208. doi:10.1016/j.msea.2014.05.044
- Brückner U, Epishin A, Link T. Local X-ray diffraction analysis of the structure of dendrites in single-crystal nickel-base superalloys. Acta Mater. 1997;45:5223–5231. doi:10.1016/S1359-6454(97)00163-8
- Diologent F, Caron P. Creep behaviour at 760°C of two nickel-based single crystal superalloys. Mater Sci Forum. 2003;426–432:725–730. doi: 10.4028/www.scientific.net/MSF.426-432.725