ABSTRACT
The aim of this work is to study the physical, chemical, and mechanical properties of 3 mol% Yttria-stabilized Tetragonal Zirconia Polycrystalline (3Y-TZP) materials doped with varying amounts of iron oxide (0, 400, 800, and 1000 ppm). We carried out full dense consolidation using two different sintering methods: fast-microwave technology at 1200°C and 1300°C, and conventional furnace at 1400°C. It was observed an improvement in density and hardness values, as well as great fracture toughness, and more intense color was achieved resulting in more natural color, similar to that of human teeth, using the microwave technique at 1300°C compared to the conventional method. However, the microwave-sintered specimens exhibited an increase in zirconia grains size and high color intensity along with iron oxide content when compared to conventional process, where the grain size does not vary with the coloring agent content. The results obtained in this work suggest that microwave technology can produce an increase in sintering activity due to the different dielectric properties of 3Y-TZP materials doped with Fe2O3. Another interesting confirmed result is that the addition of Fe2O3 presents a high resistance to low temperature hydrothermal degradation producing a delay in the aging process.
1. Introduction
Currently, there is a huge variety of materials that can be used in dentistry, which can be classified into four groups: metals, ceramics, polymers, and composites [Citation1]. Each group presents advantages and disadvantages. Ceramics stand out from the others because of their excellent mechanical properties, better biocompatibility, and more natural appearance. Nowadays the most important aspect is to maintain or improve the appearance of dental implants, in order to achieve a natural result without breaking the personal esthetic. This is why esthetics has become a new factor to be considered in the material selection process for dental and medical applications.
In attempts to meet the requirements for dental materials and improve strength and toughness, several new ceramic materials and techniques have been developed in recent decades [Citation2]. Among all these new ceramic materials, Yttria-stabilized Tetragonal Zirconia Polycrystalline (Y-TZP) is the most widely used in dentistry [Citation3]. Zirconia has qualities and properties that make it very useful in various fields of application, such as industry, aerospace, and electronics. The origin of the interest in using zirconia as a ceramic biomaterial was due to its good chemical and dimensional stability, mechanical strength and toughness, coupled with a Young’s modulus of approximately the same magnitude as stainless steel alloys [Citation4]. Furthermore, it has better biocompatibility, similar osseointegration and less inflammation than medical titanium alloys [Citation5,Citation6]. Y-TZP materials contain between 1.5 and 3.5 mol% Y2O3 in solid solution as a phase stabilizer in order to achieve almost 100% tetragonal (t) phase content [Citation7]. In nature, it is only possible to obtain zirconia in monoclinic phase with mechanical properties that are lower than tetragonal and cubic zirconia.
In recent years, scientists and researchers have worked on developing new sintering techniques in order to reduce energy consumption and dwell times that can lead to cost reductions. With new techniques, researchers have realized that material properties change considerably depending on the sintering technique, improving the mechanical and microstructure and also their behavior to low-temperature hydrothermal degradation (LTD). Ceramic materials, like zirconia, require high sintering temperatures to achieve full density values, which result in large grain sizes due to Ostwald ripening when traditional sintering techniques are used [Citation8]. Due to this phenomenon, it is very difficult to obtain dense materials with submicrometric grain sizes [Citation9]. Currently, the most promising non-conventional sintering technique is microwave technology, which enables high heating rates (>100°C/min), low dwell times of approximately 10–15 min and lower sintering temperatures. Consequently, this process requires less energy consumption. This represents a significant advantage compared with the Spark Plasma Sintering (SPS) process and the conventional system [Citation10–12]. Also, a disadvantage for the SPS technique is that the samples show a full black color after sintering. This is due to carbon diffusion within the zirconia sample in SPS processing, which is linked to the carbon-rich atmosphere in which it is performed [Citation8] and also, is due to the oxygen vacancies that occur during sintering in a vacuum atmosphere. Many different physical phenomena are involved during the microwave processing of ceramics. The interaction between microwaves and matter takes place through the electric field and magnetic field vectors of the electromagnetic field of microwaves and involves polarization and conduction processes [Citation13]. All these phenomena have been explained in detail by several researchers [Citation12,Citation14–16].
Despite zirconia’s good mechanical, chemical and esthetic properties, more information is required regarding the effects that LTD might produce, a phenomenon known to cause spontaneous “ageing” and loss of mechanical properties in this material [Citation17]. This phenomenon occurs when zirconia is exposed to environments of humidity and temperatures between 20–300°C; these conditions lead to a spontaneous transformation from tetragonal (t) phase to monoclinic (m) phase in the material structure [Citation18]. LTD starts on the surface and penetrates into the material bulk affecting the subsurface region, making it more vulnerable to friction between surfaces. This aging phenomenon is responsible for a significant loss of the mechanical performance of these ceramics, particularly hardness and fracture toughness [Citation19,Citation20].
Regarding esthetics, the main disadvantages of using zirconia as a dental prosthesis are its low translucency and milky-white color. Coloring the zirconia to match the patient’s requirements for esthetic tooth reconstruction is therefore essential. The surface of the zirconia core is generally covered with veneering feldspathic porcelain after final firing [Citation21]. However, the mechanical properties of veneering porcelain are not acceptable for use in dentistry. There are several techniques for coloring Y-TZP prosthesis but nowadays two main approaches are available. In one technique, metal oxides are mixed with starting Y-TZP powder before sintering at high temperature, with this technique successfully leading to reproduction of human teeth shades [Citation22]. Another approach currently used for dental restorations is the infiltration of machined restorations at the pre-sintered stage using chloride solutions of rare earth elements to produce cores of various shades [Citation23–25].
The aim of this study is to evaluate the effect of a small amount of iron oxide on the final density, mechanical, microstructural, and color properties, and the LTD behavior of the zirconia samples obtained using two different sintering techniques: conventional furnace and non-conventional microwave at 2.45 GHz.
2. Materials and methods
Colored zirconia powders stabilized with 3 mol% Y2O3 were obtained using a simple and economic colloidal processing route. In this method, zirconia powders (3Y-TZP, Tosoh Co., Japan) are dispersed in an aqueous solution of iron chloride according to the desired final content of dopant (0 to 1000 ppm of Fe2O3) in the sintered body. The slurry is magnetically stirred for 2 h and then dried in an oven at 120°C for 24 h. After drying, the powders are calcined at 600°C and attrition milled to remove the agglomerates.
This colloidal route, beside to bringing color to the 3Y-TZP material, can also to enhance their dielectric properties at low temperatures with doping of a secondary microwave absorbent material such Fe2O3. The heating of a ceramic material by microwave depends on its dielectric properties. At room temperature, most of the ceramic materials are nearly transparent to microwave radiation due to poor dielectric loss factor, such as the 3Y-TZP material which presents at 25°C a tanδe = 0.0011, while Fe2O3 presents a tanδe = 0.02. But the dielectric loss factor of 3Y-TZP increases rapidly above 600°C (tanδe = 0.15) and 1200°C (tanδe = 1.86) resulting in effective heating at high temperature [Citation26].
The microwave sintering (MW) of specimens was performed in an experimental microwave system with a frequency of 2.45 GHz. The E field has a maximum in the center, where the samples are located in a quartz tube [Citation27]. Specimens were put into a monomode circular cavity that was automatically adjusted to optimize microwave absorption by the material, which made it possible to control the homogeneity of heating rates; the final sintering temperatures were 1200°C and 1300°C, with a holding time of 10 min and normal atmospheric conditions (air). During sintering, it was established that the optimum heating rate was 30°C/min in order to avoid the cracking produced by rapid heating. The specimens were 10 mm in diameter and 2.5 mm in thickness. Sintering temperatures were measured on the sample surface with the aid of an optical pyrometer previously calibrated (emissivity) for the selected temperatures. In this case, due to the abrupt changes of the dielectric properties of zirconia at 300–400°C it was necessary to employ a susceptor of silicon carbide to produce hybrid heating in the microwave cavity. This hybrid heating is explained in previous studies [Citation8,Citation10,Citation27].
For conventional sintering (CS), samples were put into an electric furnace (Carbolite Gero model HTF 1800) at 1400°C with a holding time of 1 h, with a heating rate of 10°C/min and normal atmospheric conditions (air).
The relative densities of samples were determined by the Archimedes method following the ASTM-C-373 standard. A value of 6.05 g/cm3 was used as the theoretical density to estimate the relative density. All samples were polished with 1 µm diamond paste for a mirror shine finish. A Shimadzu HMV-20 micro-indenter for Vickers hardness, Hv, values was used applying 4.9 N for 10 s, and 16 measurements were taken for each specimen. Fracture toughness, KIC, values were calculated by measuring the cracks induced by the application of 98 N load for 10 s, and an image analysis program, with it being calculated by using the formula proposed by Evans et al. [Citation28]. Six measurements were taken in each sample. The microstructure and grain size were analyzed in a field emission scanning electron microscopy (FE-SEM, S4800 Hitachi, Japan) after thermal etching the samples at 100°C below the sintering temperature for 30 min. The grain size was measured using the line interception method following the ASTM E112 standard, with 10 interception lines being traced in each sample. The low-temperature hydrothermal degradation analysis (LTD) of samples was carried out in an autoclave (Raypa model) at 1.6 bar and 125°C. The samples were exposed under the aforementioned conditions for 0 h, 20 h, and 40 h. After LTD the material phases were analyzed with a micro-Raman spectrometer (Horiba-MTB Xplora with a multichannel charge-coupled device (CCD) detector with Peltier effect cooling).
The color of the samples was analyzed using a colorimeter (Minolta CR200) according to the International Commission on Illumination (CIE) coordinates [Citation29]. The L*, a*, and b* parameters were analyzed; where L* indicated the whiteness to blackness index, a* the green to red index, and b* the blue to yellow index. The spot size for each measurement was 6 mm; 4 measurements were conducted for each composition.
3. Results
3.1. Densification
The nomenclature used for 3Y-TZP doped samples with different percentage of iron oxide is as follows: NK00, NK04, NK08, and NK10, which relate to 0, 400, 800, and 1000 ppm of Fe2O3, respectively.
shows the relative density values of the NK samples sintered by microwave and conventional methods, being above 98% for all specimens. The samples obtained by microwave at 1300°C show the highest relative density values, especially the NK08 sample, with a value of 99.5%. At 1200°C the density is lower reaching ~99% for the NK08 and NK10 samples. The effect of the final microwave sintering temperature was of paramount importance, because the microwave samples at 1200°C showed less consolidation than at 1300°C. The porosity of these samples had an important role in the mechanical, low-temperature degradation, and color properties, as will be explained below.
Table 1. Relative density and average grain size of specimens after microwave and conventional sintering
Furthermore, in this case, the addition of small amounts of Fe2O3 improved the densification mechanisms. The addition of iron coloring agent promoted densification until reaching 800 ppm, from when the density started to decrease, as shown in the NK10 samples. Therefore, the NK08 samples – with 800 ppm of Fe2O3 – showed the highest consolidation using the MW method.
Regarding conventional sintering at 1400°C, these values did not follow the same trend as when using microwave technology, as NK00 was the sample with the highest relative density (98,9%). In this case the addition of ppm of Fe2O3 decreased the density to values of 98% in the case of the NK10 sample.
In short, the density values demonstrated that the addition of Fe2O3 as a dopant agent enhances the sintering activity of 3Y-TZP by microwave. These results demonstrate that it is possible to achieve higher relative densities through microwave sintering at lower temperatures and dwell times compared to the conventional method. Therefore, microwave sintering is an excellent alternative for the consolidation of these materials, reducing costs and being an eco-friendlier option.
3.2. Microstructure and grain size
The average grain sizes obtained by the different conditions and sintering methods (MW and CS) are shown in . The differences in average grain size were due to the use of different heating methods.
In CS the heat transfer was performed by the radiation of the resistors to the sample surface and then transferred to the core by conduction. While microwave are absorbed by the material, the sample core is heated and the heat is transferred to the surface by conduction.
In general, the MW samples at 1200°C had a smaller grain size than those sintered by MW at 1300°C. This difference is explained by the lower sintering temperature used. Moreover, the grain size in MW samples increased slightly with the addition of Fe2O3, as shown in . Conversely, all the CS samples showed a similar average grain size – between 237 and 245 nm.
It may be noted in microwave sintering that in addition to the temperature, dielectric properties also depend on the physicochemical properties of the material, such as chemical impurity, density, morphology, etc.
It is possible to see that a small content of iron oxide (<1000 ppm) is effective in promoting grain growth by microwave at same final sintering temperature. The dielectric properties of Fe2O3 (dielectric loss εr’’ = 0.25) at 2.45 GHz frequency and room temperature is higher than 3Y-TZP material (dielectric loss εr’’ = 0.04) [Citation26]. The high dielectric loss factor reinforcement materials behave like a localized susceptor in low loss factor ceramic matrix and work as high energy source due to microwave energy absorption. The conventional heating (conduction) of the matrix is carried out by the localized hybrid heating by reinforcement, and this case also helped by SiC susceptor, till the matrix temperature reaches the critical temperature (>1000°C). After critical temperature, both matrix and the reinforcement absorb microwave energy directly and higher densification rate than CS and with uniform heating is achieved [Citation30]. This effect of iron oxide in the early stages of the microwave densification process suggests a small grain growth in the final stage. Therefore, an enhancement of the initial sintering activity can produce an increase in ZrO2 grain size. This fact is emphasized by the increased iron content. Thus, it could be said that the addition of Fe2O3 as a dopant agent influences the grain size of the sintered material by microwave technology.
The samples obtained by microwave and null content of coloring agent (NK00) showed a smaller grain size, while by the conventional method the grain sizes reached 243 nm for NK00. However, the largest grain size of the NK10 sample was obtained when sintered by MW at 1300°C – 274 nm as can be seen in . This also be due to the fact that the grain size is influenced to a greater extent by the heating mechanisms and fast heating, which are totally different for MW and CS. These grain size differences will be reflected in the mechanical properties, as shown in .
3.3. Mechanical properties
Mechanical properties such as hardness (Hv) and fracture toughness (KIC) are crucial for the application of dental ceramics. Hv and KIC values for all the specimens and both sintering methods are shown in , respectively.
The hardness and density values were closely related. In fact, the hardness values followed the same trend as the density ones, samples with the highest density value show the best hardness as can be seen in . Therefore, the samples obtained at 1300°C by microwave show the highest hardness values between 14 and 15 GPa compared to 1200°C and conventional sintering at 1400°C, whose values are approximately between 12–14 GPa and 12–13 GPa, respectively. The samples obtained by microwave at 1200°C exhibit a slight deviation in terms of hardness due to their differences in densification and porosity.
Regarding fracture toughness, the KIC values were almost equal for all samples, these values being between 4.2 and 4.7 MPa·m1/2. However, the highest KIC values relate to those with the lowest density. As we know, the porosity factor plays an important role in this mechanical property. As can be seen in , the addition of Fe2O3 does not involve a significant change in fracture toughness values; therefore, there is no substantial effect on this mechanical property caused by the addition of iron.
Materials with high hardness and fracture toughness have been achieved through microwave sintering, making this technique quite attractive for the sintering of ceramic materials, thereby reducing sintering temperatures and holding times.
3.4. Low-temperature hydrothermal degradation (LTD)
The study of low-temperature hydrothermal degradation (LTD) was carried out on the samples that showed the best mechanical and microstructural properties and also greater densification. The selected samples were the NK obtained by MW at 1300°C and CS at 1400°C and were exposed to up to 40 h of accelerated degradation conditions.
The exposure time was selected based on the degradation study carried out in previous studies by our research group where t‐ to m‐phase transformation had been detected with Raman spectroscopy after 20 h and before 40 h of exposure [Citation31]. In addition, using the relationship that 1 h translates into 2‐3 years in service for zirconia, 40 h would represent approximately 110‐120 years, a realistic maximum time for an implant or prosthesis to be required to last.
The Raman spectra results for NK samples at different LTD exposure times are shown in . The spectrograms showed the lack of m‐phase in all specimens after 40 h of LTD exposure. Only t‐phase peaks were identified in NK doped materials for both sintering conditions (CS and MW). In the case of the NK00 CS 1400°C sample with 40 h of LTD, this showed a lower susceptibility to LTD to m-phase transformation than NK materials with a coloring agent obtained by the conventional method. These results agree with Presenda et al. [Citation31], where before 40 h of LTD exposure no m‐phase peaks were found using conventional sintering. Presenda et al. also have determined that the microwave sintered sample shows an imperceptible vulnerability to m-phase transformation after 140 h of LTD, while the conventionally sintered sample is definitely affected by LTD-induced transformation, as it already contains a Vm of 30% after 40 h of hydrothermal degradation exposure, despite both samples having similar properties and microstructure. Therefore, it is confirmed that the addition of Fe2O3 delays the aging process in conventional sintering.
Figure 4. Raman shift of samples sintered in CS at 1400°C and MW at 1300°C after 40 h of LTD exposure
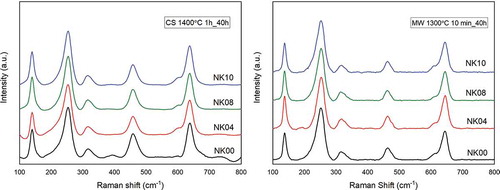
As a result, doped NK materials with an Fe2O3 agent obtained by both technologies have a high resistance to hydrothermal degradation and are suitable for application in dental industry.
3.5. Colorimetry results
The color of doped zirconia sintered samples is ivory, as shown in . Compared with the standard white specimens, said ivory color is a mixture of light yellow and light green according to the values obtained from the color measurements shown in . The addition of iron as a dopant agent makes it possible to tailor the color of dental zirconia. shows that the color for the specimens is uniform, suggesting that iron oxide enters in solid solution into the zirconia structure and is uniformly distributed. It has also been observed that increasing the amount of dopant agent increases the color of the samples and decreases the L* values ().
Table 2. CIELAB coordinates for doped NK samples
Figure 5. Image of zirconia color samples doped with different quantities of Fe2O3 sintered by MW and CS
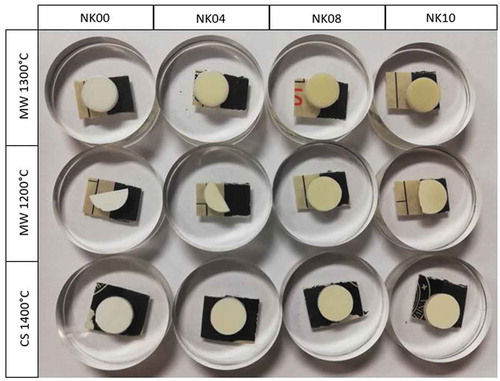
In general, the higher Fe2O3 content the more intense color of the sintered samples. Furthermore, there are differences between two sintering methods, as CS-sintered samples are lighter than MW-sintered samples.
The heating process by microwave technology and conventional (muffle furnace) are very different and have a great influence in the final properties. One advantageous and useful method that allows the modification of the densification mechanisms and faster processing of 3Y-TZP ceramics is microwave sintering [Citation7]. In this case, traditional heat transfer mechanisms are not the driving force for densification. Instead, it is the energy conversion of electromagnetic radiation into heat by the material itself due to the material´s dielectric properties [Citation7,Citation8]. The mechanisms associated with the electric field effects in microwave heating for ceramics are dipolar losses and conduction losses. Conduction losses dominate in metallic and high conductivity materials whereas dipolar losses dominate in dielectric insulators in which dipoles are generated when exposed to external electric field.
The addition of Fe2O3 in a ZrO2 system would lead to the formation of oxygen vacancies because of charge compensation. It is expected that these oxygen vacancies enhance the densification rate and promote the grain boundary mobility [Citation32]. Moreover, the addition of Fe2O3 may induce the large distortion of the surrounding lattice because Fe3+ ion has much smaller size compared with that of Zr4+ ion. This distortion also promotes the grain boundary mobility due to the effect of severely undersized dopant [Citation33]. The Fe3+ (0.55–0.78 Å) radius is much smaller than that of Zr4+ (0.84 Å), Y3+ (1.019 Å) and O2− (1.38 Å). It is known that translucency is lost if Fe3+ segregates at grain boundaries [Citation34], and it is presumed that the same phenomenon could occur in microwave sintering. As a consequence, one possibility that suggests in this work is that Fe3+ ion more preferably segregated at grain boundaries of 3Y-TZP materials obtained by microwave compared by conventional sintering, as the sintering mechanisms are different. Therefore, a more intense color is shown in dense microwave-samples than conventional. FESEM-EPMA analysis was performed to confirm this hypothesis, but it was not detected this segregation due to a low Fe2O3 content in this materials.
On the other hand, it should be noted that the final densification (porosity) also influences in the color. Microwave-sintered samples at different temperatures also have their small color differences due to their variances in density. As well as the differences in density between conventional-sintered samples at 1400°C and microwave at 1300°C (~1%) also have an influences in final color. Therefore, the contribution of porosity is an aspect to keep in mind in the final color.
shows the CIELAB coordinates of the NK samples. The color difference parameter ΔE was calculated between both white and black backgrounds. Mean ΔE values below 3.0 were considered “clinically imperceptible,” ΔE values between 3.0 and 5.0 were considered “clinically acceptable” and ΔE values above 5.0 were considered “clinically unacceptable” [Citation25,Citation30,Citation31]. The contrast ratio (CR) for each specimen was calculated. In all calculations “0” is considered the most transparent and “1” is considered the most opaque.
The color observed in zirconia samples is directly proportional to the amount of dopant agent added. According to the results, a small quantity of dopant agent was required to modify the color of the zirconia sample. Regarding the ΔE values measured, in all the cases they were lower than 2, meaning that they present very slight difference in color, with very good esthetics. Concerning translucency, the contrast ration (CR) value was “1” in all the samples studied, indicating that they are opaque.
The statistical data demonstrate that the tooth color index of L*, a* and b* is around 72, 2 and 19, respectively [Citation35]. A low content of coloring agent (1000 ppm of Fe2O3) in NK10 sintered at 1300°C by microwave is capable of changing the L* index to 85, the a* index to close to −2 and the b* index to close to 15. This range is wide enough to cover most demand for dental prostheses, especially on the cervical segment of the tooth [Citation36].
4. Conclusions
The results obtained in this study suggest that ceramic materials with higher mechanical properties and better LTD resistance can be obtained through microwave sintering at lower temperatures and dwell times. It has been established that the addition of Fe colorant does microwave technique. It should be noted that the small porosity in the samples obtained by the two methods also affects in the color. The addition of >400 ppm Fe2O3 has been shown to delay the aging of LTD. Overall, the addition of Fe2O3 combined with microwave sintering makes it possible to obtain highly dense ceramic materials with outstanding mechanical properties, high resistance to LTD environments and a wide range of color intensities at lower sintering temperatures and shorter dwell times than the conventional method, thereby considerable reducing production costs. This promising technique appears to be an alternative eco-friendly process that could replace porcelain coatings and other expensive techniques that require long processing times.not significantly affect the mechanical properties, but a small amount of coloring agent can cause slight increases in the average grain size as a consequence. Also, the addition of the Fe2O3 in the starting powders provides final sintered pieces of a uniform and natural color. Different color intensities have been obtained using two sintering methods, resulting in a more natural color similar to human teeth in the samples obtained by the microwave technique. It should be noted that the small porosity in the samples obtained by the two methods also affects in the color. The addition of >400 ppm Fe2O3 has been shown to delay the aging of LTD. Overall, the addition of Fe2O3 combined with microwave sintering makes it possible to obtain highly dense ceramic materials with outstanding mechanical properties, high resistance to LTD environments and a wide range of color intensities at lower sintering temperatures and shorter dwell times than the conventional method, thereby considerable reducing production costs. This promising technique appears to be an alternative eco-friendly process that could replace porcelain coatings and other expensive techniques that require long processing times.
Acknowledgments
A. Borrell acknowledges the Spanish Ministry of Economy and Competitiveness for her RyC contract (RYC-2016-20915).
Disclosure statement
No potential conflict of interest was reported by the authors.
Additional information
Funding
References
- Kenneth J. Ciencia de los materiales dentales. Anusavice Elsevier. España: Elsevier; 2004. p. 34.
- Raut A, Rao PL, Ravindranath T. Zirconium for esthetic rehabilitation: an overview. Indian J Dent Res. 2011;22:140–143.
- Kelly JR, Benetti P. Ceramic materials in dentistry: historical evolution and current practice. Aust Dent J. 2011;56:84–96.
- Piconi C, Maccauro G. Zirconia as a ceramic biomaterial. Biomaterials. 1999;20(1):1–25.
- Warashina H, Sakano S, Kitamura S, et al. Biological reaction to alumina, zirconia, titanium and polyethylene particles implanted onto murine calvaria. Biomaterials. 2003;24:3655–3661.
- Depprich R, Zipprich H, Ommerborn M, et al. Osseointegration of zirconia implants compared with titanium: an in vivo study. Head Face Med. 2008;4:1–8.
- Á P, Salvador MD, Peñaranda-Foix FL, et al. Effect of microwave sintering on microstructure and mechanical properties in Y-TZP materials used for dental applications. Ceram Int. 2015;41:7125–7132.
- Borrell A, Salvador MD, Rayón E, et al. Improvement of microstructural properties of 3Y-TZP materials by conventional and non-conventional sintering techniques. Ceram Int. 2012;38:39–43.
- Anselmi-Tamburini U, Garay JE, Munir ZA. Fast low-temperature consolidation of bulk nanometric ceramic materials. Scr Mater. 2006. DOI:10.1016/j.scriptamat.2005.11.015
- Borrell A, Salvador MD, Peñaranda-Foix FL, et al. Microwave sintering of Zirconia materials: mechanical and microstructural properties. Int J Appl Ceram Technol. 2013;10:313–320.
- García-Gañán C, Meléndez-Martínez JJ, Gómez-García D, et al. Microwave sintering of nanocrystalline Ytzp (3 Mol%). J Mater Sci. 2006;41:5231–5234.
- Rybakov KI, Olevsky EA, Krikun EV. Microwave sintering: fundamentals and modeling. J Am Ceram Soc. 2013;96:1003–1020.
- Agrawal DK. Microwave processing of ceramics. Curr Opin Solid State Mater Sci. 1998;3:480–485.
- Baykara T, Günay E, Kara M, et al. Microstructural development during the sintering of sepiolite. Key Eng Mater. 1997;400:872–875.
- Upadhyaya DD, Ghosh A, Dey GK, et al. Microwave sintering of zirconia ceramics. J Mater Sci. 2001;36:4707–4710.
- Borrell A, Salvador MD, Miranda M, et al. Microwave technique: A powerful tool for sintering ceramic materials. Curr Nanosci. 2014;10:32–35.
- Borrell A, Gil L, Presenda A, et al. Influence of relative humidity and low temperature hydrothermal degradation on fretting wear of Y-TZP dental ceramics. Wear. 2019;428–429:1–9.
- Cattani-Lorente M, Scherrer SS, Ammann P, et al. Low temperature degradation of a Y-TZP dental ceramic. Acta Biomater. 2011;7:858–865.
- Zhang F, Vanmeensel K, Inokoshi M, et al. 3Y-TZP ceramics with improved hydrothermal degradation resistance and fracture toughness. J Eur Ceram Soc. 2014;34:2453–2463.
- Lawson S. Environmental degradation of zirconia ceramics. J Eur Ceram Soc. 1995;15:485–502.
- Ban S, Suzuki T, Yoshihara K, et al. Effect of coloring on mechanical properties of dental zirconia. J Med Biol Eng. 2014;34:24–29.
- Cales B. Colored zirconia ceramics for dental application. Bioceramics. 1998;11:591–594.
- Kulkarni NK, Sampath S, Venugopal V. Studies on stabilised zirconia as host phase for the fixation of actinides, rare-earths and sodium. Ceram Int. 2001. DOI:10.1016/S0272-8842(01)00038-4
- Suttor D, Hauptmann H, Schnagl R, et al.Coloring ceramics by way of ionic or complex-containing solutions US 6709694 B1. U.S; 2004.
- Shah K, Holloway JA, Denry IL. Effect of coloring with various metal oxides on the microstructure, color, and flexural strength of 3Y-TZP. J Biomed Mater Res - Part B Appl Biomater. 2008;87:329–337.
- Bhattacharya M, Basak T. A review on the susceptor assisted microwave processing of materials. Energy. 2016;97:306–338.
- Benavente R, Borrell A, Salvador MD, et al. Fabrication of near-zero thermal expansion of fully dense β-eucryptite ceramics by microwave sintering. Ceram Int. 2014;40:935–941.
- Evans AG, Charles EA. Fracture toughness determinations by indentation. J Am Ceram Soc. 1976;59:371–372.
- L’Eclairage CI de. Official recommendations of the international commission on illumination. Publ CIE No15; 1971
- Mishra RR, Sharma AK. Microwave-material interaction phenomena: heating mechanisms, challenges and opportunities in material processing. Compos Part A Appl Sci Manuf. 2016;81:78–97.
- Á P, Salvador MD, Penaranda-Foix FL, et al. Effects of microwave sintering in aging resistance of zirconia-based ceramics. Chem Eng Process Process Intensif. 2017;122:404–412.
- Kao CT, Tuan WH, Liu CY, et al. Effect of iron oxide coloring agent on the sintering behavior of dental yttria-stabilized zirconia. Ceram Int. 2018;44:4689–4693.
- Tilley RJD. Principles and applications of chemical defects. Princ Appl Chem Defects. 1998;1:87–91.
- Zhang Y. Making yttria-stabilized tetragonal zirconia translucent. Dent Mater. 2014;30:1195–1203.
- Luo MR, Cui G, Rigg B. The development of the CIE 2000 colour-difference formula: CIEDE2000. Color Res Appl. 2001;26:340–350.
- Volpato Cl, Frede MC, Philippi AG, et al. Ceramic Materials and Color in Dentistry. Ed. IntechOpen; 2010