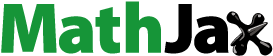
ABSTRACT
Al2O3/glass/hBN composites were successfully fabricated for the LTCC applications. Alignment and homogeneous distribution of the platelet hBN particles during tape casting allowed high hBN (5 wt%) loading as well as facilitated densification at 800°C (density of 2.65 g/cm3, apparent porosity of 0.7%). XRD results proved that hBN neither chemically reacted with the other phases nor decomposed with temperature, which was critical to increase thermal conductivity and at the same time to decrease dielectric constant. Dielectric constant of the dense composites decreased (or, alternatively, enhanced) with increasing hBN content from 7.3 for the 0 wt% hBN to 6.55 for the 5 wt% hBN at 5 MHz. In addition, hBN addition strongly improved the mean thermal conductivity from 1.86 W/m·K for the 0 wt% hBN to 2.43 W/m·K for the 5 wt% hBN between 75°C and 250°C. Therefore, the hBN phase itself effectively optimized both dielectric and thermal properties at the same time and made the Al2O3/glass/hBN composites a promising candidate for the LTCC applications.
1. Introduction
Thin, lightweight and multifunctional electronic components are attracting considerable attention due to the rapid growth of wireless communication systems and microwave devices such as those used in the automotive, medical and telecommunication. Low temperature co-fired ceramic (LTCC) technology allows manufacturing of 3D ceramic modules with embedded components and metal electrodes [Citation1,Citation2]. Glass/ceramic composites are widely used in the LTCC applications due to having some optimized mechanical, dielectric and thermal properties such as low-temperature densification (<950°C) to apply common electrode material (e.g. silver that melts at 961°C), low dielectric loss (0.0007–0.006 at 1 MHz) and low dielectric constant (3.8–9.2 at 1 MHz) to control signal propagation delay, good thermal conductivity (2.0–4.5 W/m·K) to dissipate heat, a matched thermal expansion coefficient (4.5–7.5 ppm/K) to silicon semiconductor to prevent or minimize thermal stress damage and high strength (Young’s modulus of 80–150 GPa, flexural strength of 116–320 MPa) for more efficient and reliable packaging [Citation1]. Addition of low melting glasses has been adopted to lower densification temperature and to optimize physical properties. Luo et al. [Citation3] investigated CaO-B2O3-SiO2 glass/Al2O3 composites and reported that Al2O3/50 wt% glass was fully densified at 875°C and had a dielectric constant (loss) of 8.06 (0.0012) at 7 GHz and a thermal conductivity of 3.1 W/m·K. Li et al. [Citation4] densified CaO-Al2O3-SiO2 glass-ceramic at 850ºC and reported a dielectric constant (loss) of 5.5 (0.002) at 1 MHz. Luo et al. [Citation5] studied the effect of CaO on CaO–Al2O3–B2O3–SiO2 glass/Al2O3 composites produced by the tape casting method. The composites with 9 wt% CaO sintered at 850ºC had a dielectric constant (loss) of 7.99 (0.0018) at 7 GHz. Ren et al. [Citation6] reported a dense CaO–Al2O3–B2O3–SiO2 glass (Ca/Mg = 4.30)/Al2O3 composite with anorthite crystallization after sintering at 875°C. The composite had a dielectric constant (loss) of 8.02 (0.0011) at 10 MHz and a mean thermal conductivity of 2.63 W/m·K between 25ºC and 200ºC.
Hexagonal boron nitride (hBN) is an important material in terms of its high thermal conductivity (59 W/m·K parallel and 33 W/m·K perpendicular to basal plane at 25°C [Citation7], an averaged thermal conductivity of 33.5 W/m·K at 25°C [Citation8], 20.4 W/m·K (parallel to hot-press direction) and 110.57 W/m·K (perpendicular to hot-press direction) in textured hBN/CaO-Y2O3-Al2O3 [Citation9]) and very low thermal expansion coefficient (1 ppm/°C along the a/b axis, 4.1 ppm/°C along the c axis) and low dielectric constant (4–4.4 at 1 MHz [Citation7,Citation10], 4.5 and dielectric loss = 0.0003 at 1–10 GHz [Citation11]). hBN is often used as an additive to modify thermomechanical and dielectric properties [Citation12]. Li et al. [Citation13] added 10.3 wt% and 50 wt% hBN to barium aluminosilicate (BAS) and increased thermal conductivity from 2.6 to 7.2 W/m·K at 100°C. Hong et al. [Citation14] studied densification and dielectric properties of calcium aluminoborosilicate glass with AlN, BN, and Si3N4 filler additions. AlN and Si3N4 additions favored anorthite crystallization after 850ºC, as contrary to BN that initiated no anorthite crystallization even at 1050ºC. A dense sample with 30 wt% AlN was produced at 850°C and had a dielectric constant (loss) of ~7.2 (~0.003) at 1 MHz. Highly porous samples with BN and Si3N4 fillers had much lower dielectric constants due to insufficient densification.
In our previous study [Citation15], 20 to 60 wt% glass (CaO-SiO2-Al2O3 based)/Al2O3 composites were studied for functional (e.g., LTCC) and structural (e.g., radome) applications. As the glass ratio was increased, the sintering temperature decreased from 1350°C for the 20 wt% glass to 850°C for the 60 wt% glass. Also, the dielectric constant decreased with increasing glass ratio from 8.76 (20 wt% glass) to 7.32 (60 wt% glass) at 5 MHz. However, the composite with 60 wt% glass, suitable for the LTCC, had a low thermal conductivity of 0.98 W/m·K at 75ºC (and a mean value of 1.23 W/m·K between 75°C and 250°C). In this study, platelet hBN was added at various ratios from 1 to 10 wt% in order to increase thermal conductivity and at the same time to decrease dielectric constant, which is strongly required for the LTCC applications. hBN was particularly selected for a dual purpose due to its high thermal conductivity and low dielectric constant. To the best of our knowledge, hBN/(CaO-SiO2-Al2O3 based) glass/Al2O3 composites have not been reported in the literature. Densification, phase formation, microstructural development, thermal and dielectric properties of the composites were investigated and compared with the literature and commercial products.
2. Materials and methods
Alumina (Al2O3, purity 99.78%, Almatis, CT 3000 SG), commercial glass (CaO-Al2O3-SiO2 based; Gizem Frit, Turkey) and hexagonal boron nitride (hBN, Boren, Turkey) were used as starting materials. Experimental details were given in our previous study [Citation15] but briefly explained here. A binder burnout process for Al2O3 powder was applied at 600°C for 30 minutes to remove binder from granulated powder. Al2O3 and glass granules were separately ball-milled in ethanol for 24 h. Then, a composition of 45 wt% Al2O3 and 55 wt% glass mixture (hereafter abbreviated as G55) was mixed with hBN at 1, 2.5, 5 and 10 wt% by ball milling for 24 h in ethanol with a ready-to-use vinyl-based binder solution (polyvinyl butryral and dibutyl phthalate as binder and plasticizer, methyl ethyl ketone and ethyl alcohol as the solvent) (TC-S1, MSE Teknoloji Inc., Turkey). The Al2O3/glass/hBN composites will be hereinafter referred to as G55, G55-1, G55-2.5, G55-5, and G55-10, which corresponds to 0, 1, 2.5, 5 and 10 wt% hBN, respectively. The samples were pressed at 100 MPa using a uniaxial press. They were sintered at various temperatures in the range of 800–900°C for 1 h in air, with a heating rate of 5°C/min. Archimedes method was used to measure bulk density. The G55-5 and G55-10 samples were also processed by cold isostatic pressing method at 250 MPa and by tape casting. Powders were mixed with a ready-to-use vinyl-based binder solution at 50 wt% solid loading, using a high-speed mixer (FlackTek, DAC 150.1 FVZ) run at 3500 rpm for 5 min and then tape-casted on a silicon-coated Mylar film at a casting rate of 5 cm/sec with a blade gap of 250 μm. After drying at room temperature, green samples were cut into desired sizes. The green tapes were put on top of each other, kept at 80°C for 30 minutes and then laminated by applying 50 MPa for 10 minutes. Binder burnt-out was carried out at 600°C for 30 min with a slow heating rate of 1°C/min and then sintered in air at 800°C for 1 h with a 5°C/min heating and cooling rate. The phase identification was checked on the samples polished and annealed at 500°C for 30 min, by an X-ray diffractometer (Rigaku, Miniflex600) with Cu/Kα radiation and a scan rate of 2°/min. Microstructure development and elements were examined by a Scanning Electron Microscopy equipped with an Energy Dispersive Spectroscopy (SEM-EDS, Hitachi SU1000). The thermal conductivity (k) was calculated by multiplying specific heat (Cp), thermal diffusivity (α) and density. The specific heat was measured by a differential scanning calorimeter (DSC, Netzsch STA 449F3A) and the thermal diffusivity was determined by a laser flash apparatus (Netzsch LFA 457). The BET method was used to measure the specific surface area (Quantachrome ASiQwin). The dielectric constant (K) and loss were measured by using an inductance–capacitance–resistance meter (Hioki IM3570).
3. Results and discussion
Spray-granulated Al2O3 powder after burnout and mm-sized glass flakes were first separately ball-milled for 24 h to decrease particle size. Al2O3 powder had a d50 = 0.5 μm and SSA = 6.44 m2/g, glass powder had a d50 = 2.13 μm and SSA = 1.89 m2/g. Its sintering, softening, sphere, half sphere and melting temperatures were 726°C, 852°C, 958°C, 1088°C and 1180°C, respectively. The glass composition comprised 65.8 wt% SiO2, 15.1 wt% Al2O3, 11.7 wt% CaO, 4 wt% Na2O and 3.4 wt% K2O [Citation15]. As-received plate-like hBN had an SSA = 18.23 m2/g and averaged mean thickness of 91 nm ±19 nm and mean diameter of 1.1 μm ±0.6 μm as determined from SEM.
shows densification and apparent porosity (AP) of the dry-pressed samples as a function of hBN content and temperature. The solid lines are drawn to guide the eye. In general, as the hBN content increased, bulk densities decreased at each sintering temperature due to lower density of hBN (e.g., the theoretical density of Al2O3 = 3.93 g/cm3, glass = 2.43 g/cm3 and hBN = 2.1 g/cm3 [Citation7], respectively). Correspondingly, the AP decreased with increasing densification. The G55-10 bulk densities were the lowest at all temperatures. The bulk densities and respective densification temperatures for each composite were decided based on the lowest AP and water absorption (WA) as calculated from the Archimedes method. Maximum densification was attained at 800ºC for the G55 (2.89 g/cm3, AP = 0.13% and WA = 0%), G55-1 (2.81 g/cm3, AP = 0.17% and WA = 0.16%), G55-2.5 (2.75 g/cm3, AP = 0.23% and WA = 0.08%), and at 900°C for the G55-5 (2.48 g/cm3 and AP = 0.05% and WA = 0.02%) and for the G55-10 (2.28 g/cm3 AP = 14.87% and WA = 6.51%). The G55-5 and G55-10 samples had lower densities even after they were sintered at higher temperatures. Therefore, they were fabricated by other methods such as cold isostatic pressing (CIP) and tape casting to improve densification further at high hBN loadings. compares the densification and AP of the samples fabricated via different methods and sintered at 800°C. Bulk densities were 2.54 g/cm3 and 2.28 g/cm3 for the G55-5 and G55-10 samples prepared by CIP, respectively. The bulk density increased to 2.65 g/cm3 and the AP decreased to 0.7% with a WA of 0.26% for the G55-5 prepared by tape casting. In other words, the densification temperature was successfully decreased from 900°C to 800°C by changing the fabrication method from dry pressing to tape casting for the G55-5 samples. Note that the G55-10 was not successfully processed by tape casting due to the very high viscosity of the suspension caused by the shape and high surface area of the hBN phase. These results suggest that a homogenous particle packing in the green body was provided by tape casting (or colloidal processing) method due to dispersion of the plate-like hBN particles, which allowed high hBN loading into the dense Al2O3/glass structure. Similar effects of the platelet hBN particles on densification were reported in barium aluminosilicate (BaAl2Si2O8, BAS)/hBN (10 to 50 wt%) composites fabricated by hot pressing at 1500°C [Citation16]. The bulk density decreased from 3.18 g/cm3 at 10 wt% hBN without any visible micro-cracks to 2.22 g/cm3 at 50 wt% hBN with cracks and voids. Cho et al. [Citation17] also reported limited densification in AlN (5–20 vol%)-hBN ceramics due to porosity formation induced by plate-like hBN shape.
illustrates XRD patterns of the dry-pressed composites sintered at 800°C. The polished samples were annealed at 500°C to relieve mechanical stress before the measurements. Al2O3 (Corundum, Card number: 00–010-0173) was the main crystalline phase for each composition. Anorthite (Ca,Na)(Si,Al)4O8 (Card number: 00–041-1481) and hBN (Card number: 01–074-1977) phases are also marked on the patterns. Anorthite crystallization was only discernable but the main hBN peak intensity at 2θ = 26.6° increased from the G55-1 to G55-10, which indicates that hBN neither chemically reacted with the other phases nor decomposed with temperature. Chemical stability of hBN is extremely important at helping decrease dielectric constant and increase the thermal conductivity of the composites. compares phase evolution as a function of temperature for the G55-5 samples fabricated by dry pressing and tape casting. The most distinguishing feature between them was the orientation of the hBN particles (i.e., basal plane (0002)) during tape casting, which also considerably contributed densification at 800°C (see ) by inhibiting porosity resulted from mainly hBN agglomeration. Anorthite phase formed and its amount considerably increased with increasing temperature for the tape-cast samples. The intensities of the anorthite peak at 2θ~27.9° and Al2O3 peak at 2θ~25.5° (i.e., IAnorthite/IAl2O3) were used to qualitatively calculate anorthite ratio with temperature. Note that the main Al2O3 peak at 2θ~35.1° was not used due to a background hump (see the Glass XRD pattern in ). The intensity ratio is about 0.04 for both dry-pressed and tape-cast samples sintered at 800°C (i.e., almost no anorthite formation based on XRD detection limit), 0.73 for the Tape-850°C and 1.29 for the Tape-900°C samples. The densification levels also changed with temperature, that is, 2.65 g/cm3 (AP = 0.7%) at 800°C, 2.63 g/cm3 (AP = 0.95%) at 850°C, and 2.49 g/cm3 (AP = 8.71%) at 900°C. These results indicate that sintering temperature is important to control both densification and phase evolution, which is critical for dielectric and thermal properties.
Figure 4. XRD patterns of the dry-pressed and tape-casted G55-5 samples sintered at various temperatures
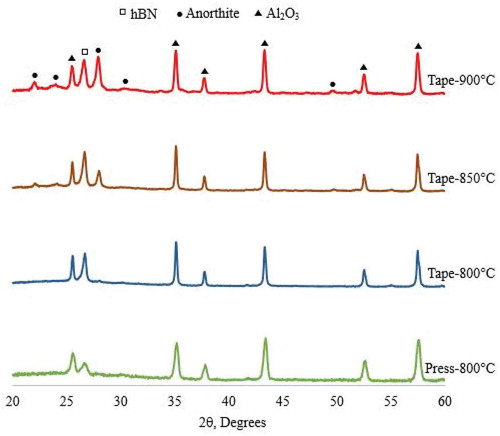
shows SEM pictures of the samples sintered at 800°C. Al2O3 particles were uniformly dispersed in the G55 sample without any visible pores. The dry-pressed G55-2.5 and G55-5 samples had visible pores in regions where the hBN particles were mainly agglomerated or randomly oriented, as shown by the arrows in . However, the tape-casted G55-5 sample had mostly dispersed and aligned platelet hBN particles (See also XRD pattern in ) as shown by the arrows in , which inhibited pore formation and correspondingly enhanced densification, as supported by . Because the LTCC process requires tape casting to fabricate thin dielectric layers, dense G55-5 sample preparation by tape casting is critical for reliable property characterizations at high hBN loadings.
Figure 5. SEM pictures of the samples sintered at 800°C; (a) G55, (b) G55-2.5 hBN, (c) dry-pressed G55-5 hBN and (d) tape-casted G55-5 hBN
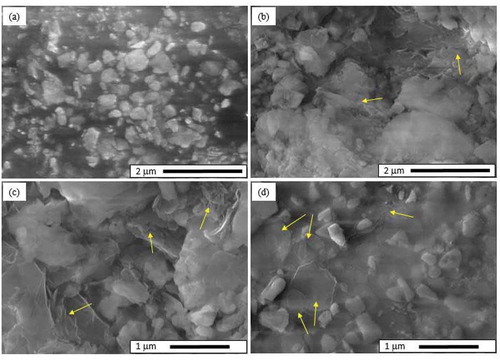
The dielectric properties of a material are dependent mainly on several factors such as glass content, porosity (or densification) and crystalline phases present. shows the hBN dependence of the dielectric constant (K) and loss measured at 5 MHz for the samples sintered at 800°C. The dashed lines are drawn to guide the eye. The G55, G55-1 and G55-2.5 specimens were produced by dry pressing, and the G55-5 sample was produced by tape casting. Note that K (loss) = 10.19 (0.0018) and K (loss) = 6.37 (0.0016) at 5 MHz for Al2O3 and glass end compositions, respectively. In general, K decreased with increasing hBN content and it was almost leveled off after 2.5 wt% hBN. In other words, the K values at 5 MHz were 7.3 for the G55, 7.2 for the G55-1, 6.6 for the G55-2.5 and 6.55 for the G55-5. Because all samples had almost near zero AP (i.e., less than 0.7%) and WA (i.e., less than 0.3%), the decrements (or, alternatively, enhancement) in K were mainly attributed to the lower K of hBN (K = 4–4.4 at 1 MHz [Citation7,Citation10], K = 4.5 and loss = 0.0003 at 1–10 GHz [Citation11]). Note that the G55-10 sample prepared by dry pressing had a much lower K = 5.17 at 5 MHz due to very high porosity (AP = 19.8%). also compares the effect of sintering temperature on K for the tape-casted G55-5 samples. K slightly increased from 6.55 to 6.76 when the sintering temperature was increased from 800ºC to 850ºC although both samples had similar density and AP, which can be attributed to more anorthite crystallization (e.g., intensity ratio increased from 0.04 to 0.73). The K (loss) values at 1 MHz for single crystal and amorphous anorthite are 7.14 (0.0011) and 7.5 (0.0024), respectively [Citation18]. Therefore, anorthite crystallization gave rise to higher K. However, the sample sintered at 900ºC had a lower K = 6.24 due to its higher AP = 8.71%, despite its much higher anorthite crystallization (e.g., intensity ratio of 1.29). Therefore, porosity (K = 1 [Citation19]) tends to decrease and anorthite tends to increase overall K of the composites. Porosity was reported to decrease K for Al2O3, SiO2, Si3N4 and BN ceramics [Citation11]. Similar hBN and porosity effects were also observed in other systems such as hBN/Si3N4 composites [Citation14,Citation20]. Particularly, full densification (or near zero AP) without in-situ anorthite crystallization is very critical at reducing K because signal propagation delay is one of the most important parameters directly associated with it in the LTCC electronic packaging:
where td is propagation delay (sec), l (m) is the metal line length and c is the speed of light (m/sec). It is obvious that a reduction in K is strongly required for high-speed signal transmission [Citation21,Citation22]. also shows that dielectric loss was almost constant up to 2.5 wt% hBN (e.g., 0.0057–0.0063) and then increased to 0.013 at 5 wt% hBN for the samples sintered at 800ºC. Dielectric loss was relatively higher for the G55-5 samples sintered at 850ºC (e.g., 0.031) and 900ºC (e.g., 0.024), which may be attributed to the porosity and/or composition. Because each component (e.g., Al2O3, hBN and in-situ crystallized anorthite, and glass) has a loss value between 0.0003 and 0.0024, porosity may be responsible for increasing the loss. Porosity definitely decreases K due to K = 1 for air [Citation19] but has various results on the loss behavior such that it decreased the loss for BN and Si3N4 while increased it for Al2O3 and SiO2 ceramics [Citation11]. Because the composites had dominantly Al2O3 and SiO2 in the compositions, they possibly controlled the overall loss with increasing porosity (e.g., AP = 0.13% for the G55, AP = 0.17% for the G55-1, AP = 0.23% for the G55-2.5 and AP = 0.7% for the G55-5 at 800°C). Porosity was reported to decrease loss in the hBN/Si3N4 composites as well [Citation20].
A high thermal conductivity (k) is strongly desired at the LTCC applications for a more efficient and reliable packaging to dissipate heat generated during service. Heat removal has become even more critical with increasing needs to produce high density and high power devices operating at high speeds [Citation21,Citation23]. compares k of the samples sintered at 800°C. The G55, G55-1, G55-2.5 and G55-10 samples were produced by dry pressing and the G55-5 sample was produced by tape casting. In general, the temperature dependence between 75°C and 250°C almost remained constant for each set. A high k of hBN [Citation7,Citation8] considerably improved the overall k of the composites. Note that the end compositions Al2O3 and glass have k = 36 W/m·K [Citation24] and k = 0.85 W/m·K [Citation25] at 25°C, respectively. The mean k values between 75°C and 250°C are 1.86 W/m·K for the G55, 2.09 W/m·K for the G55-1, 2.17 W/m·K for the G55-2.5 and 2.43 W/m·K for the G55-5. Similar trend was also observed in the hBN/BAS system such that k increased from 2.5 W/m·K (10 wt% hBN) to 7.2 W/m·K (50 wt% hBN) at 100°C [Citation13]. k decreased to 2.24 W/m·K for the G55-10 due to the porosity effect (i.e., higher AP or low densification). A mean k of 1.37 W/m·K between 75°C and 250°C was measured for the composite without hBN (i.e., the G55) sintered at 850°C [Citation15] due possibly to anorthite crystallization (intensity ratio of 0.83) because the intensity ratio was 0.04 for the sample sintered at 800°C. In actual fact, the G55-5 composite must have reached to a higher k because aligned platelet hBN particles had a lower k perpendicular to the basal plane (or along the c axis or the k measurement direction) [Citation7,Citation9]. Note that the dry-pressed composites had averaged (or isotropic) k values due to random orientation of the hBN particles, as compared to the anisotropic k values due to the aligned particles during tape casting (see ). Therefore, a higher k is expected parallel to the basal plane (or, alternatively, a faster heat dissipation toward the edges of the LTCC modules). Similar anisotropic thermal and mechanical properties were also reported in the hot-pressed Al2O3/hBN composites [Citation26]. It was determined in our earlier study [Citation15] that silver electrode was applied on the tape-cast layers and successfully co-fired at 850°C, stating that dense ceramics were fabricated without any additional phase, microcracking or shape distortion. The dielectric and thermal properties reveal that hBN addition enhanced K and k up to 5 wt% hBN provided that the AP was near zero. Furthermore, it is definitely worth investigating the (anisotropic) properties based on densification and distribution of phases (e.g., amorphous and crystalline anorthite, possible dissolution of Al2O3 in glass, change in glass composition/network with temperature, hBN agglomeration and/or alignment, etc.) in order to fully understand the processing–property relationship.
Ceramic fabrication method and sintering temperature are important parameters to control densification (e.g., porosity effect) and phase formation (e.g., anorthite phase effect), which ultimately affects final dielectric and thermal properties. Some commercial LTCC dielectric and thermal properties are as follows: Kyocera [Citation27] (GL330: K = 7.8 at 1 MHz, k = 4.3 W/m·K and GL771: K = 5.3 at 1 MHz, k = 2 W/m·K); Micro Systems Engineering [Citation28] (951AT: sinterable at 900ºC, K = 7.8 at 3 GHz, k = 2.8 W/m·K and 943A5: K = 7.4 at 3 GHz, k = 4.9 W/m·K); Heraeus [Citation29] (X200: sinterable at 880ºC, K = 8.8–9.5 at 30 MHz, k = 3 W/m·K); Ferro [Citation30] (L8: sinterable at 850ºC, K = 7.2 ± 0.2 at 10 GHz, k = 2 W/m·K and A6M/A6M-E: sinterable at 850ºC, K = 5.7 ± 0.2 at 10 GHz, k = 2 W/m·K). In general, high k comes with high K such as K = 8.06 at 7 GHz and k = 3.1 W/m·K in the CaO-B2O3-SiO2 glass/Al2O3 composite [Citation3], and k = 7.2 W/m·K and K = 11.3 at 1 MHz for BiO3-ZnO-B2O3-SiO2 glass/40 wt% Al2O3 composite with a secondary ZnAl2O4 phase after sintered at 900°C [Citation31]. The G55-5 sample has comparable dielectric and thermal properties to the commercial products with a densification temperature of 800ºC, K = 6.55 at 5 MHz and k = 2.43 W/m·K between 75°C and 250°C. Therefore, hBN phase effectively optimizes the dielectric and thermal properties and makes the G55 composition a potential candidate for the LTCC applications.
4. Conclusions
Al2O3/glass/hBN composites were successfully fabricated for the LTCC applications. Maximum densification was attained at 800ºC for the 0–2.5 wt% hBN composites and at 900°C for the 5–10 wt% hBN composites. The 5 wt% hBN composite was densified at 800ºC when the fabrication method was changed to tape casting due to alignment and homogeneous distribution of the hBN particles within the Al2O3/glass structure. XRD results proved that hBN neither chemically reacted with the other phases nor decomposed with temperature, which was critical to increase thermal conductivity to decrease dielectric constant at the same time. Dielectric constant of the dense composites decreased (or, alternatively, enhanced) with increasing hBN content such that the dielectric constant at 5 MHz was 7.3 for the 0 wt% hBN and 6.55 for the 5 wt% hBN composites. Anorthite crystallization started at 850ºC and slightly increased the dielectric constant to 6.76. Therefore, full densification without in-situ anorthite crystallization was very important at reducing dielectric constant to lower signal propagation delay. In addition, hBN addition strongly improved mean thermal conductivity from 1.86 W/m·K for the 0 wt% hBN to 2.43 W/m·K for the 5 wt% hBN between 75°C and 250°C. The 5 wt% hBN composite had comparable dielectric and thermal properties to the commercial products with a densification temperature of 800ºC (density of 2.65 g/cm3, apparent porosity of 0.7% and water absorption of 0.26%). Therefore, the hBN phase itself effectively optimized both dielectric and thermal properties at the same time and made the Al2O3/glass/hBN composites a promising candidate for the LTCC applications.
Acknowledgments
This research did not receive any specific grant from funding agencies in the public, commercial, or not-for-profit sectors.
Disclosure statement
There are no relevant financial or non-financial competing interests to report.
References
- Sebastian MT, Jantunen H. Low loss dielectric materials for LTCC applications: A review. Int Mater Rev. 2008;53(2):57–90.
- Muller R, Meszaros R, Peplinski B, et al. Dissolution of alumina, sintering, and crystallization in glass ceramic composites for LTCC. J Am Ceram Soc. 2009;92[8]:1703–1708.
- Luo X, Rena L, Xia Y, et al. Microstructure, sinterability and properties of CaO-B2O3-SiO2 glass/Al2O3 composites for LTCC application. Ceram Int. 2017;43(9):6791–6795.
- Luo X, Ren L, Xia Y, et al. Crystallization, microstructures and properties of low temperature co-fired CaO-Al2O3-SiO2 glass-ceramic. J Electroceram. 2016;37(1–4):145–150.
- Luo X, Ren L, Xie W, et al. Microstructure, sintering and properties of CaO–Al2O3–B2O3–SiO2 glass/Al2O3composites with different CaO contents. J Mater Sci: Mater Electron. 2016;27:5446–5451.
- Ren L, Zhang M, Zhou H. Application of composite binders in the fabrication of LTCC green tape based on the borosilicate glass/Al2O3 system with optimized Ca/Mg ratios. Ceram Int. 2020;8. DOI:10.1016/j.ceramint.2020.07.087.
- Chiang TH, Hsieh TEA. Study of encapsulation resin containing hexagonal boron nitride (hBN) as inorganic filler. J. Inorganic Organometallic Polym Mat. 2006 16(2).
- https://www.lowerfriction.com [Internet]. Canada: [cited 2020 Sep 7]. Available from: https://www.lowerfriction.com/pdf/11.pdf.
- Tian Z, Wang Y, Zhang Z. et al. The effects of holding time on grain size, orientation degree and properties of h-BN matrix textured ceramics. Mat Che and Phy. 2020; 248–122916.
- www.makeitfrom.com [Internet]. [cited 2020 Sep 11]. Available from: www.makeitfrom.com/material-properties/Hexagonal-Boron-Nitride-BN.
- Cary RH. Avionic Radome materials, advisory group for aerospace research and development. France; 1974. Technical Editing and Reproduction Ltd.,: London.
- Duan X, Yang Z, Chen L, et al. Review on the properties of hexagonal boron nitride matrix composite ceramics. J Eur Ceram Soc. 2016;36(15):3725–3737.
- Li Q, Cai D, Yang Z, et al. Thermal properties and thermal shock resistance of BAS-BN composite ceramics. Ceram Int. 2019;45(7):8181–8187.
- Hong KP, Choi IJ, Jung JW, et al. Densification, crystallization, and dielectric properties of AlN, BN, and Si 3 N 4 filler-containing LTCC Materials. Int J Applied Ceram Tech. 2013;10(S1):E25–E32.
- Dursun GM, Duran C. Glass alumina composites for functional and structural applications. Ceram Int. 2013;10(9):12550–12557.
- Li Q, Cai D, Yang Z, et al. Effects of BN on the microstructural evolution and mechanical properties of BAS-BN composites. Ceram Int. 2019;45(2):1627–1633.
- Cho WS, Piao ZH, Lee KJ, et al. Microstructure and mechanical properties of AlN–hBN based machinable ceramics prepared by pressureless sintering. J Eur Ceram Soc. 2007;27(2–3):1425–1430.
- Shannon RD, Dickinson JE, Rossman GE. Dielectric constants of crystalline and amorphous spodumene, anorthite and diopside and the oxide additivity rule. Phys Chem Minerals. 1992;19:148–156.
- Penn SJ, Alford NM, Templeton A, et al. Effect of porosity and grain size on the microwave dielectric properties of sintered alumina. J Am Ceram Soc. 2005;80(7):1885–1888.
- Wang S, Jia D, Yang Z, et al. Effect of BN content on microstructures, mechanical and dielectric properties of porous BN/Si3N4 composite ceramics prepared by gel casting. Ceram Int. 2013;39(4):4231–4237.
- Imanaka Y. Multilayered low temperature cofired ceramics (LTCC) technology. JAPAN: Fujitsu Laboratories Press; 2005.
- Mattox DM, Gurkovich SR, Olenick A, et al. Low Dielectric Constant, alumina-compatible, Co-Fired multilayer substrate. In: Wachtman JBJ, editor. Proceedings of Cofire Technology: ceramic Engineering and Science. Vol. 9. 1988. pp. 1567–1578.The American Ceramic Society, Inc: Brooksedge Plaza Drive Westerville.
- Chowdhry U. Sleight AW Ceramic substrates for microelectronic packaging. Annu Rev Mater Sci. 1987;17(1):323–340.
- Shackelford JF, Doremus RH Ceramic and glass materials: structure, properties and processing, (2008).
- Lide DR. CRC handbook of chemistry and physics. Washington(DC): eBook; 2003. p. 3485.
- Rutkowski P, Piekarczyk W, Stobierski L, et al. Anisotropy of elastic properties and thermal conductivity of Al2O3/h-BN composites. J Therm Anal Calorim. 2014;115:461–466.
- https://global.kyocera.com [Internet]. Kyocera, LTCC Data Sheet, [cited 2020 Sep 11]. Available from: https://global.kyocera.com/prdct/semicon/material/
- https://www.mst.com [Internet]. Switzerland: Micro Systems Engineering GmbH (MSE) Data Sheet [cited 2020 Sep 11]. Available from: https://www.mst.com/msegmbh/products_services/substrates/ltcc/ltcc_properties/index.html
- https://www.heraeus.com [Internet]. Germany: Heraeus, Commercial LTCC Data Sheet [cited 2020 Sep 11]. Available from: https://www.heraeus.com/media/media/het/doc_het/products_and_solutions_het_documents/thick_film/thick_film_data_sheets/passive_components/ltcc/LTCC_Materials_X200.pdf
- https://www.etsmtl.ca.[Internet].France:, Ferro, LTCC Data Sheet, Sheet [cited 2020 Sep 11]. Available from: https://www.etsmtl.ca/Unites-de-recherche/LTCC/Services-offerts/Ferro_A6M.pdf.
- Induja IJ, Abhilash P, Arun S, et al. LTCC tapes based on Al2O3-BBSZ glass with improved thermal conductivity. Ceram Int. 2015;41:13572–13581.