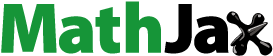
ABSTRACT
The purpose of this study was to investigate the hot properties of low calcium dialuminate cement castable as binder with varying amount of Li2CO3 and castament FS20 superplasticizer as admixtures. Thermal damage test was carried out through quenching in air for five cycles ΔT = 1175°C. The samples were preheated at 1500°C for 2 h. The results gave a retained Young’s modulus of low-cement castable with 0.3 wt.% Li2CO3 and 0.5 wt.% castament down to 10.36% while 0.1 wt.% Li2CO3 and 0.5 wt.% castament showed a retained modulus down to 13.47%. For the samples without admixture, the loss of Young modulus was 92.4% and 93.7% with 0.3 wt.% of Li2CO3 admixture. The superplasticizer has a great effect on thermal shock resistance of low calcium dialuminate cement castable. The results confirmed that 0.1 wt%Li2CO3 and 0.5 wt% castament have better thermal shock resistance and longer service life for applications in refractories. The increase of mass of the refractory materials during five thermal shock cycles in air is the main factor affecting the degradation of this refractory material due to the oxidation of SiC to SiO2.
1. Introduction
The formation and propagation of crack is a common occurrence in refractory castable that have been submitted to continuous thermal varation, and usually results to a decrease in mechanical strength and overall degradation of aforementioned materials [Citation1]. When a refractory castable is subjected to severe stress, especially from a thermo mechanical point of view, it is degraded by a combination of several mechanisms, principally thermal shock, abrasion, corrosion, and mechanical impact [Citation2]. Defloculation of agglomerated dialuminate cement particles using High Range Water Reducer (HRNR) or superplasticizers is a key to correcting the workability of concrete and reduce the amount of mixing water [Citation3].
Superplasticizer improves the properties of numerous materials particularly with respect to interparticle forces in cement suspensions. The current understanding of these forces founded major advance in Lifitz’s theory. These forces are essentially attractive in suspension. The difference between these attractive forces and the repulsive forces due to surface charge or absorbed species governs the behavior of particulates in suspension. These forces can be combined to obtain the sum of three main interaction; van der waals forces or dispersion forces, electrostatic and steric forces [Citation3]. Superplasticizers in concrete play a role in dispersion of flocculated cement grain and to release entrapped water by creating a repulsive force among them [Citation4,Citation5]. The heterogeneous surface charge distribution originating from different mineral phases and the absorbed superplasticizer molecules could bring certain effects, generally retardation on the hydration of cement [Citation5–7].
Refractory concrete as structural material for high-temperature application has received significant attention during the last decade [Citation4]. Ultra-high Performance Concrete (UHPC) requires an optimized granulometry for packing density, a very low water/cement ratio (below 0.25) and compressive strength higher than 150 MPa. During a rapid temperature change of a material, there occurs transient temperature distribution which induce thermal stress, resulting to thermal shock. The stress intensity is related to the difference in temperature between an ascending thermal shock and a descending one. The descending temperature is more destructive to brittle materials and tensile stress is generated on the surface. This circumstance may be sufficient to activate preexisting micro-cracks and to lead to body damage or fracture [Citation8,Citation9].
Densification of Calcium Aluminate Cement (CAC) usually starts at a temperature above 1200°C. Therefore, it is imperative to obtain a high performance at temperature where CAC does not show its optimized properties, where additives/admixtures leading to liquid formation and consequently faster densification present an interesting technological alternative. Another point of view from previous works states that a little amount of Li2CO3 (0.1 wt.%) improves the reactivity of CA2 cement by reducing the reaction peak time from 17 h to 23 min [Citation10].
The aim of this work is to study the behavior of low calcium dialuminate cement castable with and without Li2CO3 admixture and Castament FS20 subjected to thermal shock from 1200°C to 25 ± 2°C and to estimate the service life of this refractory castable for petrochemical and high-temperature applications.
2. Materials and methods
2.1. Sample preparation
The explanation of the samples and their codes is presented in , the chemical composition of the raw materials is presented in and the formulation of concrete is presented in .
Table 1. Explanation of concrete samples
Table 2. Chemical composition of raw materials for concrete
Table 3. Formulation of refractory concrete
The alumina refractory concrete was prepared using calcium dialuminate cement (CA2) from Cameroon as binder, tabular alumina (1–2 mm and 0–1 mm) as aggregates from Almatis Germany. Silica fume (ø < 0.1 µm) and reactive alumina CTC 50 were used as fine particles and admixtures (lithium carbonate and superplasticizer castament FS20) respectively.
The formulation was designed according to Funk and Dinger packing model with q = 0.26, where DI and DS are, respectively, the dimension of the largest and the smallest particles [Citation1,Citation8–11].
The mixture content was W/C ratio = 1.6 of about 12 wt.% water in the concrete with and without admixtures, 0.5 wt.% superplasticizer, castament FS20 from BASF construction solution GMBH Germany and a varying amount of lithium carbonate from 0 wt.%, 0.1 wt.% and 0.3 wt%. These were molded and cured at an ambient temperature of 25 ± 2°C for 48 h, stabilized at 105°C for 24 h and then sintered at 1500°C with a soaking time of 2 h.
2.2. Thermal shock damage test
The refractory concretes were subjected to thermal shock by quenching in compressed air flow at a Biot number β = 0.3. The thermal shock damage test was conducted by quenching a specimen in air 6 Bars that is from 1200°C to 25 ± 2°C, with Δ T = 1175 ± 2°C, for five consecutive heating and cooling cycles (ASTMC1171-91). Basically, the samples were placed in an electric furnace previously heated at 1200°C for 24 h and kept at this temperature for 30 min; after that the samples were taken out of the furnace very fast in order to preserve the frozen state of the reaction during sintering. They were quenched in air at a pressure of 6 bars for 15 min until the sample attained room temperature (25 ± 2°C). The cycle was repeated five times. The damage caused by the thermal changes was evaluated by elastic modulus measurements at room temperature. The relative variation of dimensions (delta L/L0) and mass (delta m/m0) of the samples submitted to thermal shock was measured using an electronic caliper and precise electronic scale, respectively.
The Young’s modulus (E), shear modulus (G) and Poisson’s ratio (v) were determined using the European Norm EN 843–2:2006. The Young’s modulus was calculated using the formula:
where b is the width, h the thickness, m the mass, l the length and ff the longitudinal resonant frequency of the sample [Citation12].
3. Water absorption and apparent density of refractory concrete
Measurements of water absorption and apparent density of the refractory concrete were carried out according to the norm BS EN 14,617–1: 2013 [Citation13]. The samples were dried at 105°C for 48 hours in an electric dryer to determine its constant weight and then immersed in a water bath at an ambient temperature of 23°C containing distilled water for 24 hours. The humid weight (mh) was compared to the dry weight (md) according to the following equation
The apparent density (ρa) of a sample is defined as the quotient of the dry mass (m) of product by the volume occupied by the solid material including the empty spaces found in the grains according to the norm BS EN 14,617–1:2013 [Citation13]. The apparent density is calculated according to the equation:
ρa = apparent density g/cm3
md = dry mass of sample
V = volume of sample
4. Results and discussions
4.1. Young’s and Shear Modulus of low CA2 cement refractory
presents the Young’s modulus and shear modulus of low calcium dialuminate cement castable (8 wt.%) stabilized at 105°C for 24 hrs with and without Li2CO3 and castament FS20 as superplasticizer. For sample 0ALCO without admixtures, the Young’s modulus is about 3.1 GPa and shear modulus 1.3 GPa. When 0.3 wt.% Li2CO3 is added to the low cement castable, the Young’s modulus reduces to 2.5 GPa. It can be retained that Li2CO3 when reduces the setting time and favors a reduction of the Young’s modulus of the concrete. The addition of 0.1 wt.% Li2CO3 and 0.5 wt.% superplasticizer castament FS20 (0105ALCO) increases the Young’s modulus from 3.1 GPa to 13.5 GPa and the shear modulus from 1.3 GPa to 5.5 GPa. Increasing the amount of Li2CO3 from 0.1 wt% to 0.3 wt.% presented a high Young’s modulus of 17.1 GPa and shear modulus of 6.9 GPa for 0305ALCO.
When the concrete is heated at 1500°C for 2 h (), the Young’s modulus of the low calcium dialuminate cement concrete increased from 3.1 GPa to 19.5 GPa for 0ALCOT and from 2.5 GPa to 19.1 GPa with the addition of 0.3 wt.% of Li2CO3 for sample 03ALCOT. The addition of admixtures 0.1 wt% Li2CO3 and 0.5 wt.% of castament shows the Young’s modulus increased from 13.5 GPa to 31.5 GPa (0105ALCOT). The highest value of Young’s modulus after treatment at 1500°C is 37.1 GPa and shear modulus of 16 GPa corresponding to 0.3 wt.% Li2CO3 and 0.5 wt.% Castament FS20 (0305ALCOT).
It’s known with ordinary Portland cement, that the strength and elastic modulus decrease when exposed to high temperatures, but with calcium dialuminate cement, recent work [Citation14] showed that the refractory concrete using low calcium dialuminate cement presented a decrease of Young’s modulus from 20°C to 1120°C with the relative variation of ΔE ≈ −92% and an increase of Young’s modulus from 1120°C to 1620°C with the relative variation of ΔE ≈ +95% following an increase from 1620°C to 20°C with relative variation of ΔE ≈ +298% during cooling.
Castament FS 20 is a carboxylic acrylic ether named polycarboxylate ether or polycarboxylate polyether superplasticizer of class sieve segregation (%) SR 1 ≤ 20. In concrete at 105°C and 1500°C, this water reduction admixture creates dispersion forces in flocculated cement grain and release entrapped water by creating a repulsive force among them. The superplasticizer also lowers the surface tension of water at the onset of the settlement of the solid particles in the mix, influences the liberation of entrapped air and facilitates the workability properties of the refractory material in order to get better physical and hardened properties of concrete [Citation5–7]. This justifies the high Young’s modulus of the concrete when 0.5 wt.% of superplasticizer is added.
After five cycles of thermal shock at a pressure of 6 bars from 1200°C to 25 ± 2°C, the Young’s modulus of concrete decreases from 19.5 GPa to 1.5 GPa and shear modulus from 8.2 GPa to 0.6 GPa for concretes sintered without admixtures 0ALCOTS (). When 0.3 wt.% of Li2CO3 is added, the Young’s modulus decreases from 19.1 GPa to 1.2 GPa and the shear modulus from 7.7 GPa to 0.5 GPa for 03ALCOTS. The reduction of Young’s modulus in this case is about 93.5%.
The highest value of Young’s modulus after fives thermal shock is 4.3 GPa. With 0.1 wt.% Li2CO3 admixture and 0.5 wt.% of castament, the Young’s modulus decreases from 31.5 GPa to 4.3 GPa corresponding to a reduction of 86.54% for 0105ALCOTS. Contrary to this, the highest value of Young’s modulus obtained at 1500°C was 37.1 GPa with 0.3 wt.% Li2CO3 and 0.5 wt.% castament (0305ALCOTS). This value decreased to 3.8 GPa after five thermal shock cycles with a corresponding Youngs modulus reduction of 90%. The refractory material is heterogeneous, constituting a matrix and aggregates; the significant reduction of Young’s modulus during thermal shock results from the thermal tension on aggregate and matrix simultaneously. From the results, low calcium dialuminate cement refractories with high Young’s modulus (≈ 37 GPa), such as those attained for alumina-based castable showed a reduced amount of stored elastic strain energy under severe thermal stresses. This was very notable for the 0.3 wt.% Li2CO3 and 0.5 wt.% castament specimen than the 0.1 wt.% Li2CO3 and 0.5 wt.% castament. From , the density of the low calcium dialuminate cement concrete without admixtures increase from 1.75 to 2.18 g/cm3 when sintered at 1500°C. It can be said that the bulk density of the concrete increase after heat treatment at 1500°C implying that during heat treatment, densification occurs through compaction of materials and decreasing pores. After five thermal shock cycles at a pressure of 6 bars from 1200°C to 25 ± 2°C, the density reduces to 1.79 g/cm3. This reduction in density was observed in all the samples, indicating that thermal shock favors the creation of fractures and pores. Also, from , the thermal shock is characterized by a reduction of the density of low-cement castables. This is more intense for low strength than high strength castable. Explaining that the more durable low-cement castable is neither the one with lower strength nor higher strength values.
4.2. Effect of density and thermal shock resistance
The thermal shock resistance of materials is not only dependent on intrinsic factors such as structure, grain size, shape and distribution of internal defects, but on macroscopic physical indices such as strength, modulus of elasticity, thermal conductivity, thermal expansive coefficient and Poisson’s ratio [Citation15–17].
The relative reduction of density after five thermal shock cycles for sample 0305AlCOT is about 17% (similar to 03AlCOT), while the relative reduction of density for sample 0105AlCOT was 13% (similar to sample 0AlCOT). This means that Li2CO3 has an impact on the density, that is an increase in the quantity of Li2CO3 the reduction percentage of the relative density. The lower the relative thermal shock resistance of castable with Li2CO3 and castament, the better the resistance of the castable for a long service lifetime.
The relative reduction of Young’s modulus after five thermal shock cycles for sample 0305AlCOT was 90% while 0105AlCOT present a reduction of 86.5%, without a superplasticizer (castament), its relative reduction of Young’s modulus is about 93%. Although the superplasticizer plays a beneficial role by increasing the density, the Young’s modulus and service lifetime of the concrete, the addition of Li2CO3 at about 0.1 wt.% improves the quality of concrete and increases its service lifetime. In general, catastrophic thermal shock failure results from a material’s inability to store high elastic energy, sample 0105ALCO with E value (≈31 GPa) showed a very high ability to store elastic modulus.
Thermal quenching leads to crack nucleation and/or propagation, resulting to a decrease in strength. The formation of cracks has an impact on the Young’s modulus and density of the material. This could be connected to the number of cycles, as well as to the damage during quenching. It is observed that refractory materials presenting low Young’s modulus (19.1 GPa) for 03ALCOT and very high Young’s modulus (37.1 GPa) for 0305ALCOT do not store high elastic energy in their structure. The authors l’Hopital et al. [Citation18] stated that stronger refractories with high E modulus ≈ 37 GPa can be good for applications in environments presenting sudden temperature changes. There is a great effect of Li2CO3 and castament (superplasticizer) on thermal shock resistance of low calcium dialuminate cement castable. 0.1 wt.% of Li2CO3 and 0.5 wt.% of castament FS20 (superplasticizer) in castable refractory concrete present the best thermal shock resistance.
4.3. Effect of silica fume on the weight and dimensions of castable after five thermal shock cycles
The variation of relative weight and relative dimension is presented in respectively. The weight of the concrete sample increase after five thermal shock cycles from 1200°C to 25°C. This increase in weight is very high, between +6.3 and +6.4 wt.% for samples without castament (0ALCOTS, 03ALCOTS) and +5 wt.% when 0.5 wt.% castament FS20 is added (01051LCOTS, 0305ALCOTS). The silica fume added to the concrete contains a little amount of carbon (3 wt.%). When the concrete with silica fume mixture is sintered at 1500°C for 2 h, the reactions that occur are as follows:
Knowing that
The reaction producing SiC(g) and CO(g) has been highlighted by authors to be endothermic and the Gibb’s energy given as [Citation19–22]:
where carbon monoxide evaporates and silicon carbon remains in solid state in the concrete samples.
During thermal shock from 1200°C to 25°C at a pressure of 6 bars, passive oxidation of SiC occurs with an increase in mass following the equation:
The SiO2 formed during passive oxidation get deposited over the surface of SiC, leading to an increase in the mass and the dimensions of the concrete. These observations were also made by Wei et al., Roy et al. and Chia-Tsing Wei [Citation23–27].
The low increase in weight with castament addition is due to the compaction of concrete whereby air cannot easily get to the center of the concrete for SiC oxidation.
Salomao et al. [Citation28] explained that the oxidation of SiC(s) in reducing gas CO(g) contributes to the formation of anorthite in the presence of CaO(s) and Al2O3(s) by the following reactions:
SiC oxidation and the formation of anorthite have a favorable Gibbs energy value negative. They concluded that only SiC oxidation and anorthite formation are predicted in the 400 − 1200°C temperature range. While Kazemi [Citation29] explained that in the presence of CaO, the superfine silica and alumina particles react with this CaO at high T° (1000–1500°C) leading to the formation of low melting phases, such as anorthite (CaO.Al2O3.2SiO2) and gehlenite (2CaO.Al2O3.SiO2) and causes reduction of the strength of the refractory at high temperatures. If a great amount of reactive alumina is available, CA2 reacts with alumina to form CA6, causing a theoretical volume change of CA2 = +13.6% and CA6 = +3.01%. This variation may reduce crack during different thermal treatments of high alumina. The authors believe that a volume increase occurs during the formation of mullite at high temperature and can promote cracking through the development of residual stress. The variation of dimensions and weight for this work are theoretically predicted by the oxidation of SiC, formation of mullite, anorthite, gehlenite and CA6.
5. Conclusions
The goal of this work was to know if the low CA2 cement in concrete can be used for alumina refractory concrete and to study the behavior of this concrete with admixtures.
The percentage of the relative reduction of Young’s modulus after five thermal shocks showed that a little amount of Li2CO3 (about 0.1 wt.%) and superplasticizer (castament FS20 at 0.5 wt.%) in the cement improves the quality of concrete and can increase the service lifetime.
Decreasing the refractory Young’s modulus will result in a cascading negative effect on the elastic modulus and consequently affecting the thermal shock behavior.
The relative increase in mass and dimensions of the refractories after five thermal shock cycles in air might be linked to the oxidation of residual silicon carbide in the concrete.
From the results, it can be assumed that stronger refractories with high E modulus ≈31 GPa can be good options for applications in environments presenting sudden temperature changes. The variation of dimensions and weight for this work are theoretically predicted by the oxidation of SiC, formation of mullite, anorthite, gehlenite and CA6.
Financial and Ethical disclosures
No funding was received for this research paper and the authors declare that they have no conflict of interest.
Acknowlegments
This work was supported by T.U. University of Freiberg Germany through the cooperation between MIPROMALO Yaounde-Cameroon and T.U. Freiberg Germany.
Disclosure statement
No potential conflict of interest was reported by the authors.
Additional information
Funding
References
- Luz AP, Santos T Jr., Medeiros J, et al. Thermal shock damage evaluation of refractory castables via hot elastic modulus measurements. Ceram Inter. 2013;39(6):6189–6197.
- Kakroudi MG, Yeugo-Fogaing EY, Gault C, et al. Effect of thermal treatment on damage mechanical behaviour of refractory castables: comparison between bauxite and andalusite aggregates. J Euro Ceram Soc. 2008;28(13):2471–2478.
- Houst YF, Bowen P, Perche F, et al. Design and function of novel superplasticizers for more durable high performance concrete (superplast project). Cem Concr Res. 2008;38(10):1197–1209.
- Schröfl C, Gruber M, Plank J. Preferential adsorption of polycarboxylate superplasticizers on cement and silica fume in ultra-high performance concrete (UHPC). Cem Concr Res. 2012;42(11):1401–1408.
- Zhang Y-R, Kong X-M, Lu Z-B, et al. Effects of the charge characteristics of polycarboxylate superplasticizers on the adsorption and the retardation in cement pastes. Cem Concr Res. 2015;67:184–196.
- Ilg M, Plank J. A novel kind of concrete superplasticizer based on lignite graft copolymers. Cem Concr Res. 2016;79:123–130.
- Morin V, Tenoudji FC, Feylessoufi A, et al. Superplasticizer effects on setting and structuration mechanisms of ultrahigh-performance concrete. Cem Concr Res. 2001;31(1):63–71.
- Hamidouche M, Bouaouadja N, Olagnon C, et al. Thermal shock behaviour of mullite ceramic. Ceram Inter. 2003;29(6):599–609.
- Chen S-K, Cheng M-Y, Lin S-J, et al. Thermal characteristics of Al2O3–MgO and Al2O3–spinel castables for steel ladles. Ceram Inter. 2002;28(7):811–817.
- Tchamba AB, Mbessa M, Langollo YT, et al. Reactivity of calcium dialuminate (CaAl4O7) refractory cement with lithium carbonate (Li2CO3) admixture. J Asian Ceram Soc. 2020;8(2):223–233.
- Niziurska M, Malolepszy J, Malata G. The influence of lithium carbonate on phase composition of calcium aluminate cement paste. Proc Eng. 2015;108:363–370.
- Advanced technical ceramics mechanical properties of monolithic ceramics at room temperature; determination of Young’s modulus, shear modulus and Poisson’s ratio. Standard EN 843-2. 2006.
- Agglomerated stone. Standard test methods. Determination of apparent density and water absorption, Standard BS EN 14617-1. 2013.
- Tchamba AB, Elimbi A, Mbessa M, et al. Thermoelastic properties evolution and damping phenomena of Cameroonian calcined bauxite stabilized with calcium dialuminate refractory cement. Ceram Inter. 2015;41(1):53–59.
- Prompt N, Ouedraogo E. High temperature mechanical characterisation of an alumina refractory concrete for blast furnace main trough; PartI. General context. J Euro Ceram Soc. 2008;28:2859–2865.
- Wei Z, Wenyong D, Chiyoda N. Research on thermal shock resistance of mullite-bauxite-silicon carbide castable refractory. Chin J Geochem. 2012; 31(2):204–208.
- Martinovic S, Vlahovic M, Boljanac T, et al. Cavitation resistance of refractory concrete: influence of sintering temperature. J Euro Ceram Soc. 2013;33:7–14.
- L’Hôpital E, Lothenbach B, Le Saout G, et al. Incorporation of aluminium in calcium-silicate – hydrate. Cem Concr Res. 2015;75:91–103.
- Plank J, Yu B. Preparation of hydrocalumite-based nanocomposites using polycarboxylate comb polymers possessing high grafting density as interlayer spacers. Appl Clay Sci. 2010;47:378–383.
- Serivener KL, Cabiron JL, Letourneux R. High-performance concretes from calcium aluminate cements. Cem Concr Res. 1999;29:1215–1223.
- – Bier TA, Mathieu A, Espinosa B, et al. ‘Admixtures and their interactions with high range calcium aluminate cement. Proceedings 4th biennial worldwide congress, hosted by the Technical Association Of Refractories Japan. Technical Paper, TP-GB-RE-LAF-003 Unitecr Congress. Japan; 1995.
- Miller PD, Lee JG, Cutler IB. The reduction of silica with carbon and silicon carbide. J Am Ceram Soc. 1978;62:3–4.
- Wei Z, Wenyong D, Chiyoda N. Research on thermal shock resistance of mullite-bauxite-silicon carbide castable refractory. Chin J Geochem. 2012;31:204–208.
- Roy J, Chandra S, Das S, et al. Oxidation behaviour of silicon carbide, a review. Rev Adv Mater Sci. 2014;38:29–39.
- – Wei GC-T. Beta SiC powders produced by carbothermic reduction of silica in a high-temperature rotary furnace, metals and ceramics division, oak ridge national laboratory, oak ridge, Tennessee 37830. Communications of the Am Ceram Soc. 1983.
- Maldhure AV, Tripathi HS, Ghosh A. Mechanical properties of mullite–corundum composites prepared from bauxite. Int J Appl Ceram Technol. 2015;12(4):860–866.
- Luz AP, Huger M, Pandolfelli VC. Hot elastic modulus of Al2O3–SiC–SiO2–C castables. Ceram Inter. 2011;37:2335–2345.
- Salomao R, Pandolfelli VC. The role of hydraulic binders on magnesia containing refractory castables: calcium aluminate cement and hydratable alumina. Ceram Inter. 2009;35:3117–3124.
- Kazemi N. Reasons for crack propagation and strength loss in refractory castables based on change in their chemical compositions and micromorphologies with heating special focus on the large blocks. J Asian Ceram Soc. 2019;7(2):109–126.