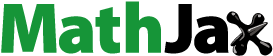
ABSTRACT
β-SiAlON/TiC0.3N0.7 composites containing 2.0-7.5 wt.% TiC0.3N0.7 are prepared by pressureless spark plasma sintering (SPS) with Al2O3-AlN-Y2O3 additives. The TiC0.3N0.7 phase particles are homogeneously dispersed in the β-SiAlON matrix. The reaction between the sample and the graphite mold can be avoided during the pressureless SPS. The β-SiAlON/TiC0.3N0.7 composite with 5 wt.% TiC0.3N0.7, fabricated at 1550°C, exhibits a high density of 3.28 g cm−3 (98% relative density), high Vickers hardness of 14.53 GPa, and high fracture toughness of 7.20 MPa m1/2. By further SPS under a pressure of 24 MPa at 1400 oC, these properties are enhanced to a higher density of 3.32 g cm−3 (full density), higher Vickers hardness of 15.87 GPa, and higher fracture toughness of 7.44 MPa m1/2. Obviously, the fracture toughness of the as-prepared β-SiAlON/TiC0.3N0.7 composites is apparently higher than those of the reported β-SiAlON-based ceramic composites prepared by pressurized SPS, which is mainly attributed to the highly dense microstructures of the interlocking lath β-SiAlON grains and the uniformly distributed TiC0.3N0.7 particles, and the disappearance of the oriented ununiform stress caused by uniaxial pressure in normal pressurized SPS. Accordingly, the pressureless SPS could be a potential technique for the fabrication of high-performance β-SiAlON matrix composites.
1. Introduction
Silicon nitride ceramic is an advanced ceramic material with low density, high strength, good friction and oxidation resistance and high chemical corrosion resistance, which is widely used in cutting tools, bearings, reciprocating engine parts, wear and metal forming components [Citation1–4]. β-SiAlON is a β-Si3N4 solid solution by substitution of a silicon-nitrogen bond with aluminum-oxygen bond [Citation5–7], named after the elements they contain silicon (Si), aluminum (Al), oxygen (O) and nitrogen (N). SiAlON shows similar physical and mechanical properties to those of Si3N4 ceramics, but better thermal shock resistance because of its lower thermal expansion. However, the SiAlON matrix composites still exhibit some inadequacies such as the inherent brittleness of ceramic [Citation8–10]. Many efforts have been made to improve the brittleness properties of the ceramics via well-definable composition and microstructure by carefully controlling the process parameters and methods [Citation11–13].
The dispersion of the second phases has been regarded as an effective way for ceramic toughening. It is reported that TiN particulates improve the fracture toughness of Si3N4 and SiAlON composites at room temperature [Citation8,Citation10,Citation14–18]. The Si3N4/TiN nanocomposites containing 10 wt.% TiN obtained by hot pressing show a fracture toughness of ~6.7 MPa m1/2 [Citation19]. The fracture toughness of 5.52 MPa m1/2 was obtained in α-β-SiAlON/TiN composites with 5 wt.% TiN prepared by microwave sintering at 850°C [Citation20]. Spark plasma sintering (SPS) shows high efficiency for the densification of ceramics, including Si3N4, at relatively low temperatures under a pressure [Citation21]. Compared to the traditional sintering processes, the SPS technology achieves the same sintering effect at lower temperatures within a shorter sintering time for Si3N4-based ceramics [Citation22]. The fully dense nanocomposite containing 10 wt% TiN, fabricated successfully by SPS at 1600°C for 3 min under a pressure of 30 MPa using Si3N4 and TiN nanopowders, exhibits the highest fracture toughness of ~4.9 MPa m1/2 [Citation17]. Fully dense β-SiAlON/TiN composites are produced by spark plasma sintering (SPS) at 1750°C under a pressure of 30 MPa for 30 min, using Si3N4, Al2O3, AlN and TiO2 powders. The fabricated composite with 15 wt.% micronized TiO2 possesses a high toughness of 6.3 MPa m1/2 [Citation10]. However, the Si3N4-based ceramics or SiAlONs may be easily reacted with the graphite mold during pressurized SPS at high temperatures. In this work, we successfully prepared β-SiAlON/TiC0.3N0.7 composites with high mechanical properties by means of pressureless SPS, which could avoid the above-mentioned reaction between the sample and the graphite mold. The densification of β-SiAlON/TiC0.3N0.7 composites could take place by intrinsic pulsed electric field effects on the mass transport in the pressureless SPS process, forming highly densified microstructures of interlock β-SiAlON lath grains + dispersed TiC0.3N0.7 particles without the oriented ununiform stress distribution caused by uniaxial pressure in normal pressurized SPS. Consequently, the high density, hardness and fracture toughness would be achieved.
2. Experimental procedures
The starting materials were Si3N4 (SN-E10 grade, 0.6 μm, 95% α-phase, UBE Industries, Japan), Al2O3 (Meryer, 100 nm, Germany), AlN (Meryer, 50 nm, Germany), Y2O3 (Meryer, 100 nm, Germany), and TiC0.3N0.7 (Xing Rong Yuan, 2 μm, China) powders. According to the weight radios of the samples with different TiC0.3N0.7 contents, as listed in , the powders were mixed by wet ball-milling with ethanol for 48 h (zirconia balls and high-density polyethylene jar). The weight ratio of the balls to the powders was kept at about 10:1. The zirconia balls with 3.5 and 5.0 mm in diameter with the weight ratio of 8:2 were used. The milled powders were then dried in a drying box at 80°C for 12 h, sieved with 140 meshes, and cold isostatic pressed (~270 MPa) into pellets with 28 mm in diameter.
Table 1. Compositions and sample names
The pellets were sintered by pressureless SPS (lab-made SPS system) under a nitrogen atmosphere using a special cylindrical graphite mold with the inner diameter of 30 mm (see ). The samples with different TiC0.3N0.7 contents, namely 1-SNT0, 1-SNT2, 1-SNT5 and 1-SNT7.5 (see ), were heated to the sintering temperature between 1500°C and 1650°C at a rate of 100°C/min, held at each temperature for 20 min, and then cool down to room temperature at a rate of 70°C/min. All the samples pressureless SPSed at 1550°C exhibited the best properties in density, hardness, fracture toughness. Therefore, they were selected for further improvement by further pressurized SPS under a pressure of 24 MPa at 1400, 1425 and 1450 oC, respectively, for 5 min. These samples were named 2-SNT0, 2-SNT2, 2-SNT5 and 2-SNT7.5 (also see ).
The as-prepared samples were polished with diamond paste up to 1.0 μm for phase and microstructure analyses, and also for the density, hardness, fracture toughness, and thermal conductivity measurements. The phases were analyzed by X-ray diffraction (XRD) using Bruker D8 Advance SS/18 kW with Cu Kα radiation and Jade 6.5 software. The Rietveld refinements of XRD patterns were performed with the aid of Topas 3.1 software to estimate the theoretical density of the samples. The microstructures were observed by scanning electron microscopy (SEM) equipped with energy-dispersive X-ray spectroscopy (EDS) (Su-70, Hitachi). The bulk density of the samples was measured by the Archimedes method. Vickers hardness and fracture toughness were determined using the indentation technique. The Vickers hardness was measured with a hardness tester (Micro-586 Vickers Hardness Tester, Shanghai Taiming Optical Instrument Co., Ltd.) with an indentation load of 10 kg (98 N) and a dwell time of 15 s. The Vickers hardness (HV in GPa) is given by [Citation23]
where F is the test force in Newton (N), α is the angle between two opposite faces of a regular quadrilateral pyramid diamond indenter (136°±0.5° in this work), and d is the mean value of the two diagonals of the indentation in mm.
The fracture toughness (KIC in MPa m1/2) is determined by [Citation24]
where E is Young’s modulus in GPa (300 GPa for Si3N4 in this work [Citation24]) and C is the mean crack length from the center of the indentation in μm.
The thermal diffusivity (λ) was measured by the laser flash technique (NETZSCH LFA 467) and the heat capacity Cp was determined using differential scanning calorimetry (NETZSCH DSC 404F3). The total thermal conductivity (κ) is calculated using the equation , where ρ is the mass density of the sample.
3. Results and discussion
3.1. Phases and microstructures
In this investigation, the β-SiAlON/TiC0.3N0.7 composites were prepared with 6 Al2O3-3 AlN-6 Y2O3 or 5 Al2O3-2.5 AlN-5 Y2O3 additives (wt.%) and different TiC0.3N0.7 contents. The β-SiAlON ceramics were formed by the following reaction [Citation10]:
Based on the Al2O3-AlN-Y2O3 phase diagram, the Y2O3 additive can decrease the forming temperature of the transient liquid phase and thus reduce the sintering temperature [Citation25]. The pulsed electrical current with 10 ms on/10 ms off period and about 2000 A was used in this work. As a result of particle rearrangement due to the Si3N4-dissolution to β-SiAlON precipitation, the densification of the β-SiAlON/TiC0.3N0.7 composites can also occur by intrinsic pulsed electric field effects on the mass transport without pressure during the pressureless SPS process, forming the highly densified microstructures, showing similar sintering behavior as comparing to the normal pressurized SPS.
represents the typical XRD patterns for the mixed powder and the pressureless SPSed sample 1-SNT5 at different temperatures. The mixed powder contains α-Si3N4 phase mainly, together with minor β-Si3N4 and TiC0.3N0.7 phases, and Al2O3, AlN and Y2O3 additive phases. As the mixed powder pressureless SPSed at 1500–1650°C for 20 min, the crystalline phases are β-SiAlON and minor TiC0.3N0.7 phases. Almost all the α-Si3N4 phase has reacted with the additives Al2O3 and AlN and transforms to β-SiAlON ceramic completely.
Figure 2. XRD patterns for (a) the mixed powder and the 1-SNT5 sample with 5.0 wt.% TiC0.3N0.7 after pressureless SPS at different temperatures 1500–1650 °C and (b) the 1-SNT0, 1-SNT2, 1-SNT5 and 1-SNT7.5 samples with 0, 2.0, 5.0 and 7.5 wt.% TiC0.3N0.7, respectively, after pressureless SPS at 1550 °C
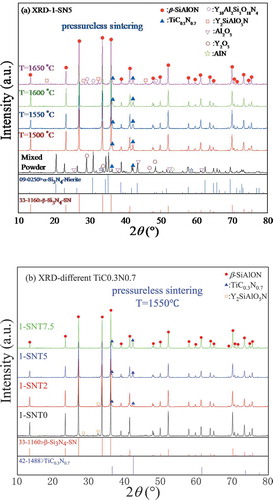
The Al2O3, AlN and Y2O3 react chemically with SiO2 on the surface of Si3N4, forming a transient liquid phase during the sintering and finally become glass phases along the grain boundaries of the β-SiAlON/TiC0.3N0.7 crystalline phases. Therefore, both the formation of the liquid phase and the phase transformation of α-Si3N4 to β-SiAlON in the liquid phase also occur during the pressureless SPS process. As the sintering temperature increases to 1650°C, the minor impurity crystalline phases, seeming Y2SiAlO5N and Y10Al2Si3O18N4, appear in the sample, which may arise from the crystallization from the glass phases. Similar phase formation is also found in the other samples with different TiC0.3N0.7 contents as shown in . The β-SiAlON/TiC0.3N0.7 composites with 0, 2.0, 5.0 and 7.5 wt.% TiC0.3N0.7, containing β-SiAlON and TiC0.3N0.7 crystalline phases, along with the grain boundary glass phases, can be fabricated by the pressureless SPS at ~1550°C. As the TiC0.3N0.7 content increases, the intensity of the TiC0.3N0.7 peak increases (see ).
shows the backscattering electron micrographs of the polished surfaces of the representative sample 1-SNT5 pressureless SPSed at different temperatures. Clearly, the micrographs consist of the dark gray, bright white, white and dark regions. The dark regions in are pores, which reveal that the pressureless SPS temperature of 1500°C is too low for sample 1-SNT5 to obtain dense ceramic due to the high viscosity of the liquid phase along the grain boundary. Based on the compositions obtained by EDS analysis and the XRD results, it is confirmed that the dark gray region belongs to the β-SiAlON phase and the bright white phase region to the TiC0.3N0.7 phase, while the white region is of the glass phase or minor impurity Y2SiAlO5N phase formed from the residual additives along the grain boundaries of the β-SiAlON phase. As the sintering temperature is increased to 1550°C, there are no pores present in the samples whose microstructures are mainly composed of interlock elongated β-SiAlON grains uniformly dispersed with TiC0.3N0.7 particles (see ). As the sintering temperature is further increased to 1600°C, no obvious change is found in the microstructure (see ). However, when sintering at 1650°C, the long columnar grains begin seemingly to grow larger (see ).
Figure 3. Typical back scattering electron micrographs on the polished surfaces of the representative 1-SNT5 sample with 5.0 wt.% TiC0.3N0.7 after pressureless SPS at different temperatures, consists of the dark gray phase region, the bright white phase region and the white phase region
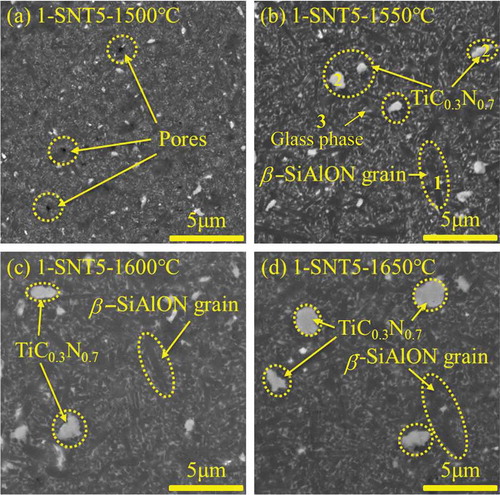
shows the typical EDS spectra for elongated β-SiAlON phase (dark gray region, marked 1 in ), TiC0.3N0.7 phase (bright white region, marked 2 in ) and glass phase (white region, marked 3 in ) in the micrograph on the polished surface of the sample 1-SNT5 pressureless SPSed at 1550°C for 20 min. The dark gray region is of the β-SiAlON phase formed by the reaction of Si3N4, Al and O, which mainly contains Si and N together with a small amount of Al and O but not Y (see ). The bright white region is the TiC0.3N0.7 phase, which mainly contains Ti, N and C, along with a small amount of Si, O and Al but not Y (see ) affected from the β-SiAlON matrix. The element Y distributes mainly in the glass phases or in the minor impurity Y2SiAlO5N (see ). The large amount of Si and N in the glass phase should be affected by the β-SiAlON matrix since the glass layer is very thin (about 80 nm).
Figure 4. EDS results for (a) the elongated dark gray region (β -SiAlON phase), (b) the bright region (TiC0.3N0.7 phase) and (c) the white region (glass phase) in the micrograph on the polished surface of the 1-SNT5 sample with 5.0 wt.% TiC0.3N0.7 after pressureless SPS at 1550°C (see )
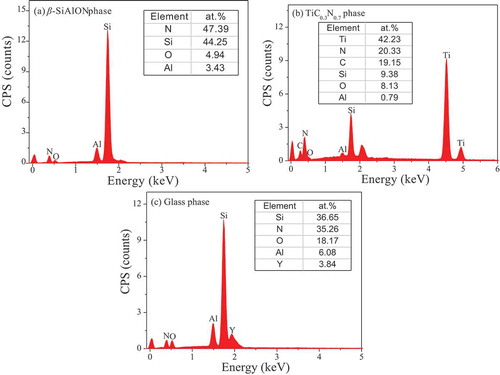
The elemental mapping on the polished surface of the 1-SNT5 sample pressureless SPSed at 1550°C is illustrated in . It is clearly seen that TiC0.3N0.7 particles are uniformly distributed in the β-SiAlON matrix. It can be envisaged that the oriented ununiform stress distribution, caused by uniaxial pressure in normal pressurized SPS, can be disappeared in the pressureless SPSed samples, which would be beneficial to the enhancement of fracture toughness.
3.2. Density, hardness, and fracture toughness
The high density, hardness and fracture toughness can be obtained by the pressureless SPS. shows the density, hardness and fracture toughness for the samples pressureless SPSed at the different temperatures. The values of density and hardness for the sample 1-SNT0 without TiC0.3N0.7 increase sharply with increasing the sintering temperature from 1500°C to 1600°C, and then decrease slightly with further increasing sintering temperature to 1650°C, which may be due to the larger grain size and the slight decomposition of Si3N4 created at this higher sintering temperature. The 1-SNT2, 1-SNT5 and 1-SNT7.5 samples containing different TiC0.3N0.7 contents exhibit a similar trend as the 1-SNT0 sample with increasing the sintering temperature. The densities for the 1-SNT2, 1-SNT5 and 1-SNT7.5 samples containing TiC0.3N0.7 are somehow higher than that of the 1-SNT0 sample due to the higher density of the TiC0.3N0.7 phase. The highest densities for the 1-SNT0, 1-SNT2, 1-SNT5 and 1-SNT7.5 reach 3.18, 3.25, 3.28 and 3.26 g cm−3 respectively. The theoretical density of the pressurized SPSed sample 2-SNT5 is ~3.27 g cm−3, estimated based on XRD Rietveld refinement and EDS analysis, considering the crystalline phases β-SiAlON and TiC0.3N0.7 only without taking account of the glass phase, which lower than the highest density 3.32 g cm−3 of its further pressurized SPSed sample (seen in section 3.4). Therefore, the highest densities, 3.24, 3.29, 3.32 and 3.32 g cm−3 for the further pressurized SPSed samples 2-SNT0, 2-SNT2, 2-SNT5 and 2-SNT7.5 with 0, 2.0, 5.0 and 7.5 wt.% TiC0.3N0.7 were taken as their theoretical density. The relative densities for the pressureless SPS samples are also plotted in . One can see that all the pressureless SPS samples show high relative densities around 98% and slightly higher with the introduction of the conductive TiC0.3N0.7 phase. The conductive TiC0.3N0.7 phase uniformly distributed in the β-SiAlON matrix increases the electrical conductivity of the composite materials and consequently affects their sintering behavior by the electric current passing through the sample in SPS [Citation26]. As the result, it promotes the sample sintering at relatively lower temperatures, and thus leads to obtain the higher density, hardness and fracture toughness as well as the complete phase transformation of α-Si3N4 to β-SiAlON.
Figure 6. (a) Density (ρ), (b) hardness (HV) and (c) fracture toughness (K1C) of the samples after both pressureless SPS and further pressurized SPS at different temperatures (T)
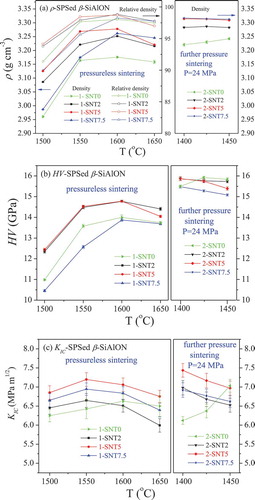
For the pressureless SPS at 1550°C and 1600°C, all the samples show better density, hardness and fracture toughness, shown in . For example, the density, hardness and fracture toughness for the 1-SNT5 are 3.27 g cm−3, 14.48 GPa and 7.20 MPa m1/2 as the sample sintered at 1550°C, while 3.28 g cm−3, 14.78 GPa and 7.06 MPa m1/2 as the sample sintered at 1600°C. The fracture toughness of 7.20 MPa m1/2 obtained for the β-SiAlON with 5.0 wt.% TiC0.3N0.7 sintered at 1550°C is higher than 6.7 MPa m1/2 for the 10 wt.% TiN-Si3N4 nanocomposite obtained by hot pressing [Citation19], 5.52 MPa m1/2 for the 5 wt.% TiN-α-β-SiAlON composite achieved by microwave sintering at 850°C [Citation20], and 6.2 MPa m1/2 for the 10 wt.% TiN-β-SiAlON composite prepared by SPS at 1600°C for 10 min under a pressure of 30 MPa [Citation18]. The β-SiAlON/TiC0.3N0.7 composites pressureless SPSed at 1550°C exhibit the best fracture toughness, which were selected for further pressurized SPS at temperatures between 1400°C and 1450°C for 5 min under a pressure of 24 MPa. The related results will be presented later.
The higher fracture toughness for the samples prepared by the pressureless SPS may be mainly ascribed to the highly dense microstructures with the interlocking of the lath β-SiAlON grains and the uniformly distributed TiC0.3N0.7 particles, and the disappearance of the oriented ununiform stress distribution caused by uniaxial pressure in normal pressurized SPS. The toughening mechanisms of the β-SiAlON/TiC0.3N0.7 composites fabricated in this work should be a crack deflection, branching and bridging, penetration and impedancing. shows a typical Vickers fingerprint and the crack propagation on the polished surfaces of the 1-SNT5 sample. A large number of interlocking lath β-SiAlON grains aligned in various directions are distributed inside the matrix. The TiC0.3N0.7 particles distribute uniformly in the β-SiAlON matrix. When a crack encounters the lath β-SiAlON grains or TiC0.3N0.7 particles of a certain specific orientation during the propagation process, the crack has to deflect around the β-SiAlON lath, leading to an increase in the resistance of crack propagation, shown in (b)-d) and (f). For some elongated lath β-SiAlON grains or TiC0.3N0.7 particles with specific orientation and distribution, the crack is difficult to deflect and can only cut through or penetrate the β-SiAlON grain, hereby consuming more energy, shown in (g)-(h). The crack bridging occurs as the hardness of TiC0.3N0.7 is higher than that of β-SiAlON and the TiC0.3N0.7 particles can bridge at the ends of two cracks, shown in . The oriented ununiform stress distribution caused uniaxial pressure in normal pressurized SPS also decreases fracture toughness. The pressureless SPS avoids this problem.
3.3. Thermal properties
The value of thermal conductivity, shown in , decreases from 14.3 Wm−1K−1 at 25°C to 12.3 Wm−1K−1 at 500°C for the sample 1-SNT0, from 14.8 Wm−1K−1 to 12.5 W m−1K−1 for the 1-SNT2 sample, from 15.1 W m−1K−1 to 13.1 W m−1K−1 for the 1-SNT5 sample, and from 15.5 W m−1K−1 to 13.7 W m−1K−1 for the 1-SNT7.5 sample. The increase of thermal conductivity with the increase of TiC0.3N0.7 is mainly due to the more conductive TiC0.3N0.7 phase with a higher thermal conductivity. The phonon scattering resulting from the glass phases formed along the grain boundaries may somewhat decrease the thermal conductivity. No doubt, a high thermal conductivity of the ceramic composites is beneficial for their practical applications.
3.4. Further modification of pressurized SPS
The samples pressureless-sintered at 1550°C for 20 min were sintered again by SPS at different temperatures under a pressure of 24 MPa for 5 min. shows the typical XRD patterns for the 2-SNT5 sample with 5.0 wt.% TiC0.3N0.7 (see ) after pressurized SPS at different temperatures. After further pressurized SPS at 1400°C, 1425°C and 1450°C, the phases in the samples have no apparent change, showing the main crystalline β-SiAlON phase and minor TiC0.3N0.7 phase as well as some glass phases. As the TiC0.3N0.7 content increases, the intensity of the TiC0.3N0.7 peak increases (see ).
Figure 9. XRD patterns for the β-SiAlON/TiC0.3N0.7 composite samples: (a) 2-SNT5 with 5.0 wt.% TiC0.3N0.7 after further pressurized SPS at different temperatures and (b) 2-SNT0, 2-SNT2, 2-SNT5 and 2-SNT7.5 with 0, 2.0, 5.0 and 7.5 wt.% TiC0.3N0.7, respectively, after further pressurized SPS at 1400°C

After further pressurized SPS, the samples exhibit much denser microstructure as compared with those of the pressureless-sintered samples, containing β-SiAlON phase (dark gray regions), TiC0.3N0.7 phase (bright white regions), and glass phase (white regions), as shown in . It is anticipated that these samples could have a higher performance. As demonstrated in , the density, hardness and fracture toughness of the samples are somewhat enhanced. The density increases from 3.18 to 3.22–3.24 g cm−3 for the 2-SNT0 sample, from 3.25 to 3.28–3.29 g cm−3 for the 2-SNT2 sample, from 3.28 to 3.31–3.32 g cm−3 for the 2-SNT5 sample, and from 3.26 to 3.31–3.32 g cm−3 for the 2-SNT7.5 sample. The density increases slightly with increasing TiC0.3N0.7 content because of the higher-density TiC0.3N0.7. The theoretical density of the 2-SNT5 sample is ~3.27 g cm−3, estimated based on XRD Rietveld refinement and EDS analysis. A small number of Al and O are considered to replace Si and N, respectively, in β-Si3N4, thereby leading to the formation of β-SiAlON. The samples after further pressurized SPS can be considered to be fully dense.
Figure 10. Typical back scattering electron micrographs on the polished surfaces of the representative samples: (a) 2-SNT0, (b) 2-SNT2, (c) 2-SNT5, (d) 2-SNT7.5 after further pressurized SPS at 1400°C for 5 min, which consist of the dark gray, bright white and white phase regions
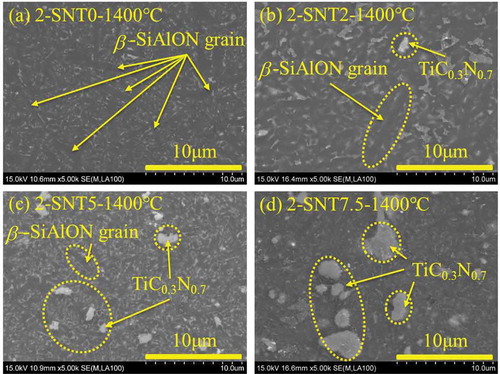
As reported in [Citation27], the density of 3.25 g cm−3 is obtained for the Si3N4 ceramics by pressurized SPS at 1650°C for 10 min using 9.0 wt.% Al2O3 and 6.0 wt.% Y2O3 as additives. The silicon nitride ceramics fabricated by pressurized SPS exhibit the density of 3.08 g cm−3 for sintering at 1500°C, 3.23 g cm−3 for sintering at 1600°C, and 3.23 g cm−3 for sintering at 1650°C using 2.0 wt.% Al2O3 and 5.0 wt.% Y2O3 as additives [Citation22]. A study by Hayashi et al. [Citation28] indicates that the Si3N4–based ceramic material prepared by sintering in a graphite resistance furnace at 1900°C for 2 to 48 h under a nitrogen pressure of 0.9 MPa with MgSiN2 as additive possesses a density ranging from 3.20 to 3.26 g cm−3. Thus, the density of the present samples fabricated by further pressurized SPS or even merely by pressureless SPS is comparable with or higher than those reported in literature.
After the further pressurized SPS, the Vickers hardness increases from 14.00 GPa to 15.50–15.92 GPa for the 2-SNT0 sample, from 14.77 GPa to 15.73–15.86 GPa for the 2-SNT2 sample, from 14.78 GPa to 15.39–15.87 GPa for the 2-SNT5 sample, and from 13.87 GPa to 15.08–15.48 GPa for the 2-SNT7.5 sample. The hardness for 2-SNT0, 1-SNT2 and 2-SNT5 is not apparently different at different TiC0.3N0.7 contents after the further pressurized SPS, while the hardness of 2-SNT7.5 is slightly lower, which may be due to the less sintering aids of Al2O3-AlN-Y2O3.
The second-stage pressurized SPS can also enhance the fracture toughness of β-SiAlON/TiC0.3N0.7 composites. It is increased from 6.40 to 7.00 MPa m1/2 for the 2-SNT0 sample, from 6.65 to 6.98 MPa m1/2 for the 2-SNT2 sample, from 7.20 to 7.44 MPa m1/2 for the 2-SNT5 sample, and from 6.94 to 6.92 MPa m1/2 for the 2-SNT7.5 sample. The relatively low fracture toughness of 6.12 MPa m1/2 for the 2-SNT0 sample after pressurized SPS may be because the sintering temperature is too low to obtain higher density for the sample due to its lower flowability. This implies that the secondary phase TiC0.3N0.7 in the β-SiAlON matrix may increase the flowability of the composite at high temperature. Consequently, pressureless SPS along with further pressurized SPS can fabricate β-SiAlON/TiC0.3N0.7 ceramic composites with excellent mechanical properties and meanwhile the reaction between the sample and the graphite mold can considerably be restrained.
4. Conclusions
The β-SiAlON/TiC0.3N0.7 ceramic composites with excellent mechanical properties have been fabricated by pressureless spark plasma sintering (SPS) at relatively low sintering temperatures. The mechanical properties of the composites can be further improved by a further SPS at 1400 oC for 5 min under a pressure of 24 MPa. This technique can avoid the oriented ununiform stress distribution, caused by uniaxial pressure in normal pressurized SPS and simultaneously minimize the reaction between the sample and the graphite mold.
The formation of the liquid phase and the phase transformation of α to β-SiAlON occur in the pressureless SPS process. The prepared β-SiAlON/TiC0.3N0.7 composites have an interlock microstructure formed by lath β-SiAlON grains with TiC0.3N0.7 particles dispersed uniformly in the matrix. The composite with 5 wt.% TiC0.3N0.7 exhibits a high density of 3.28 g cm−3, high hardness of 14.53 GPa, and high fracture toughness of 7.20 MPa m1/2. The high fracture toughness may mainly arise from the highly densified microstructures with the interlocking of the lath β-SiAlON grains and the uniformly distributed TiC0.3N0.7 particles, and the disappearance of the oriented ununiform stress distribution caused by uniaxial pressure in normal pressurized SPS.
With a further SPS at 1400°C under a pressure of 24 MPa for 5 min, the fully dense β-SiAlON/TiC0.3N0.7 composites are obtained and their mechanical properties are somewhat enhanced. For the composite with 5 wt.% TiC0.3N0.7, the Vickers hardness is enhanced to 15.87 GPa and the fracture toughness to 7.44 MPa m1/2. The present fracture toughness is well comparable with its publically available values. Therefore, the pressureless SPS may be a promising technique for the fabrication of the high-performance β-SiAlON matrix composites.
Disclosure statement
No potential conflict of interest was reported by the authors.
Additional information
Funding
References
- Riley FL. Silicon nitride and related materials. J Am Ceram Soc. 2000;83(2):245–265.
- Freitag DW. In situ processed Si3N4 whiskers in the system barium aluminosilicate-Si3N4. Mat Sci Eng A. 1995;195:197–205.
- Pierson HO Handbook of refractory carbides and nitrides: properties, characteristics, processing and apps. William Andrew; 1996.
- Ziegler A, Idrobo JC, Cinibulk MK. Interface structure and atomic bonding characteristics in silicon nitride ceramics. Science. 2004;306(5702):1768–1770.
- Peng H Spark plasma sintering of Si3N4-based ceramics, Department of Inorganic Chemistry, Vol. Doctoral Dissertation. Stockholm University, Stockholm, Sweden; 2004.
- Yi XM, Akiyama T, Kurokawa K. Combustion synthesis and spark plasma sintering of β-SiAlON, nitride ceramics. Combust Synth Prop Appl. 2015;1:97–124.
- Karunaratne BSB, Lumby RJ, Lewis MH. Rare-earth-doped α-Sialon ceramics with novel optical properties. J Mater Res. 1996;11(11):2790–2794.
- Huang ZH, Yang JZ, Liu YG, et al. Novel Sialon-based ceramics toughened by Ferro-Molybdenum alloy. J Am Ceram Soc. 2012;95:859–861.
- Chen WW, Cheng YB, Tuan WH. Preparation of Sialon-transition metal silicide composites. J Eur Ceram Soc. 2006;26(1–2):193–199.
- Nekouee KA, Khosroshahi RA. Sintering behavior and mechanical properties of spark plasma sintered β-Sialon/TiN nanocomposites. Int J Refract Met Hard Mater. 2016;61:6–12.
- Kurama S, Schulz I, Herrmann M. Wear properties of α-and α/β-SiAlON ceramics obtained by gas pressure sintering and spark plasma sintering. J Eur Ceram Soc. 2011;31(5):921–930.
- Jones MI, Hirao K, Hyuga H, et al. Wear properties of Y–α/βcomposite sialon ceramics. J Eur Ceram Soc. 2003;23(10):1743–1750.
- Nayebi B, Asl MS, Kakroudi MG, et al. Temperature dependence of microstructure evolution during hot pressing of ZrB2–30 vol.% SiC composites. Int J Refract Met Hard Mater. 2016;54:7–13.
- Duan RG, Roebben G, Vleugels J, et al. Effect of TiX (X = C, N, O) additives on microstructure and properties of silicon nitride based ceramics. Sc Mater. 2005;53(6):669–673.
- Duan RG, Roebben G, Vleugels J, et al. In situ formation of Si2N2O and TiN in Si3N4-based ceramic composites. Acta Mater. 2005;53(9):2547–2554.
- Calloch P, Brown IWM, MacKenzie KJD, et al. Synthesis and properties of new β-Sialon/TiN composites via a novel AlxTiy intermediate. Ceram Int. 2016;42(2):2330–2338.
- Lee CH, Lu HH, Wang CA, et al. Microstructure and mechanical properties of TiN/Si3N4 nanocomposites by spark plasma sintering (SPS). J Alloy Compd. 2010;508(2):540–545.
- Sun QC, Wang ZX, Yang J, et al. High-performance TiN reinforced Sialon matrix composites: A good combination of excellent toughness and tribological properties at a wide temperature range. Ceram Int. 2018;44(14):17258–17265.
- Tian C, Jiang H, Liu N. Thermal shock behavior of Si3N4–TiN nano-composites. Int J Refract Met Hard Mater. 2011;29(1):14–20.
- Canarslan ÖS, Rosa R, Köro˘glu L, et al. Microwave sintering of SiAlON ceramics with TiN addition. Materials. 2019;12(1345):1–13.
- Zhou M, Zhong J, Zhao J, et al. Microstructures and properties of Si3N4/TiN composites sintered by hot pressing and spark plasma sintering. Mater Res Bull. 2013;48(5):1927–1933.
- Belmonte M, González-Julián J. Spark plasma sintering: A powerful tool to develop new silicon nitride-based materials. J Eur Ceram Soc. 2010;30(14):2937–2946.
- Gong JH, Wu JJ, Guan ZD. Examination of the indentation size effect in low-load vickers hardness testing of ceramics. J Eur Ceram Soc. 1999;19(15):2625–2631.
- Anstis GR, Chantikul P, Lawn BR, et al. A critical evaluation of indentation techniques for measuring fracture toughness: i, direct crack measurements. J Am Ceram Soc. 1981;64(9):533–538.
- Fabrichnaya O, Pavlyuchkov D, Neher R, et al. Liquid phase formation in the system Al2O3–Y2O3–AlN: part II. thermodynamic assessment. J Eur Ceram Soc. 2013;33(13–14):2457–2463.
- Zhou MY, Rodrigo D, Cheng YB. Effects of the electric current on conductive Si3N4/TiN composites in spark plasma sintering. J Alloy Compd. 2013;547: 51–28.
- Lukianova OA, Novikov VY, Parkhomenko AA, et al. Microstructure of spark plasma-sintered silicon nitride ceramics. Nanoscale Res Lett. 2017;12(1):293–298.
- Hayashi H, Hirao K, Toriyama M, et al. MgSiN2 addition as a means of increasing the thermal conductivity of β-Silicon Nitride. J Am Ceram Soc. 2001;84(12):3060–3062.