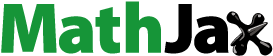
ABSTRACT
The effects of Cr2O3 on the crystallization, structure, and properties of Ti-bearing blast furnace slag-based glass ceramics were investigated. The results show that the transition temperature and crystallization temperature decreased with introduction of Cr2O3 as a while. Specifically, the crystallization temperature first decreased, then increased with the increase Cr2O3 concentration from 0.2 wt% to 0.8 wt%, and finally decreased with further increased in Cr2O3 concentration. The crystal phases were identified as anorthite, diopside, and akermanite. As the content of Cr2O3 increased to 0.8 wt%, the dendrites gradually decreased and the granular crystals gradually increased. When the Cr2O3 concentration further increased, the number of granular crystals gradually decreased and the dendrites gradually accumulated. With the increase of Cr2O3 from 0.2 wt% to 0.8 wt%, the structure of the investigated glass gradually depolymerized, while the opposite trend was presented with further increased in Cr2O3 content. With increasing Cr2O3 content from 0.2 wt% to 2 wt%, the flexural strength values and Vickers hardness values of the glass ceramics first increased and then decreased, and the maximum values of flexural strength and Vickers hardness were obtained as 94.371MPa and 974.43MPa, respectively. The prepared Ti-bearing blast furnace slag-based glass ceramics showed good acid and alkali resistance.
1. Introduction
Blast furnace slag is an important industrial solid waste produced in the blast furnace ironmaking process [Citation1], which is primarily used to produce building materials with low added values, such as cement, concrete, and bricks [Citation2]. The Ti-bearing blast furnace slag is a by-product of vanadium-titanium-bearing magnetite smelting in blast furnace ironmaking and mainly composed of SiO2, CaO, MgO, TiO2, and Al2O3 [Citation3]. Since the presence of TiO2 will reduce the stability of building materials [Citation4], it is typically used to extract titanium. However, the economic value of Ti-bearing blast furnace slag with low-grade TiO2 (<10 wt%) is rather low. As a result, it is pertinent to develop a method to efficiently and comprehensively utilize low Ti-bearing blast furnace slag.
Glass ceramic is a multiphase material with both a mini-crystal phase and glass phase [Citation5–7]. Glass ceramics possess many remarkable properties, such as excellent mechanical strength, chemical stability, thermal stability, corrosion resistance, and so on [Citation8–16]. The properties of glass ceramics largely depend on crystallization behaviors, such as crystal grain size, quantity, types of main crystal phases, and so on. Various nucleating agents can effectively promote the transformation of glass and refine the crystal grains to achieve bulk crystallization. Examples include Cr2O3, TiO,2 and CaF2, which can each be added to the glass system to improve the material properties [Citation17–19].
Based on the composition of Ti-bearing blast furnace slag, it is considered a typical silicate material, which can be utilized as a glass ceramic. In addition, according to previous studies [Citation3,Citation7,Citation20,Citation21], TiO2 can be regarded as a good nucleating agent to control the crystallization behavior of glass ceramics. As a result, the low Ti-bearing blast furnace slag can be a good candidate for the preparation of slag-based glass ceramics [Citation22], where a small amount of TiO2 in the Ti-bearing blast furnace slag can be the nucleating agent. In our previous work [Citation23], the effects of TiO2 on the crystallization behavior of Ti-bearing blast furnace slag-based glass ceramics were investigated. The results suggested that it was difficult to achieve three-dimensional crystal growth and two-dimensional crystallization was shown in the sample with 2 wt% TiO2. To further optimize the crystallization properties of Ti-bearing blast furnace slag-based glass ceramics, an appropriate nucleating agent must be considered. Zhang et al. [Citation24]. showed that adding Cr2O3 can accelerate the crystallization of the pyroxene phase, and the prepared glass ceramics showed high strength and good chemical resistance with the introduction of Cr2O3. Wang et al. [Citation25] reported that the addition of a small amount of Cr2O3 can induce the crystallization of the parent glass, and found that the glass ceramics showed uniform, compact grains, and high bending strength values in the range of 84.6 ~ 101.7 MPa. Back et al. [Citation9] revealed that the crystallization activation energy of SiO2-Al2O3-CaO-MgO based glass ceramics was reduced with the addition of Cr2O3. Deng et al. [Citation26] also reported that by increasing the Cr2O3 concentration from 1.5 wt% to 2.5 wt%, the two-dimensional crystallization can be changed to three-dimensional crystallization, and the dendrite could be gradually refined. From the above studies, adding a certain amount of Cr2O3 can effectively promote crystallization and improve the bending strength, chemical resistance, and so on.
In this work, by analyzing the crystallization behavior and properties of prepared glass ceramics with different additions of Cr2O3, the effects of Cr2O3 on the Ti-bearing blast furnace slag-based glass ceramics were investigated. This study provides theoretical and technical support for the efficient and comprehensive utilization of low Ti-bearing blast furnace slag.
2. Experimental
2.1. Sample preparation
Ti-bearing blast furnace slag was obtained from an iron and steel plant in China, which was the main raw material in preparation of glass ceramics. As shown in , the chemical compositions were characterized by X-ray fluorescence spectroscopy (XRF) (Polish PANalytical B.V., Axios Advanced).
Table 1. Chemical composition of the original Ti-bearing blast furnace slag (wt%)
The CaO/SiO2 mass ratio of the original Ti-bearing blast furnace slag was about 1.1, which was higher than that of ordinary silicate-based glass ceramics, so the chemical reagent SiO2 was added to adjust the CaO/SiO2 to 0.5. At the same time, 0.2 wt%, 0.5 wt%, 0.8 wt%, 1.1 wt%, and 2 wt% Cr2O3 were added, respectively. The chemical compositions of the glass ceramics were shown in . After accurate weighing, the specimens were placed in an agate mortar and ground for 30 minutes until uniformly mixed. Then, the powder specimens were placed into a corundum crucible, in a high-temperature tube furnace to melt. The temperature was then increased from room temperature to 1500°C in air and held for 4 hours. After that, the specimens were taken out and quenched with water to obtain the basic glasses, which were identified by X-ray diffraction (XRD) (PANalytical X’Pert Powder, Spectris Pte, the Netherlands), as shown in .
Table 2. Chemical composition of Ti-bearing blast furnace slag-based glass ceramics (wt%)
Afterward, 1 wt% polyvinyl alcohol and 5 wt% zinc stearate and pure water were used as binders. An FYD-30 electric powder compactor was used to press the basic glass into the cylinder with a diameter of 8 mm and cuboid with dimensions of 50x6x6 mm for mechanical property detection. The pressed samples were heated to 600°C for 1 h in a high-temperature tube furnace. The transition temperatures (Tg) of the investigated glasses were determined using differential scanning calorimetry (DSC) (449F3, NETZSCH, Germany). The nucleation temperature was estimated to be 800°C, which is normally 50 ~ 100°C greater than the Tg of glasses [Citation5,Citation27].
The first exothermic peak temperature of DSC was used as the crystallization temperature to prepare glass ceramics. The specimens were held at 800°C for 2 h and then heated to its crystallization temperature for 1.5 h at a heating rate of 5°C/min to obtain the glass ceramics. The specific preparation process of Ti-bearing blast furnace slag-based glass-ceramics was shown in .
2.2. Characterizations and measurements
The parent glass powders were examined by DSC in air from room temperature to 1300°C at a heating rate of 5°C/min to obtain the transition temperature and crystallization temperature. The crystallization phases of glass ceramics were identified by XRD. In addition, scanning electron microscopy with energy-dispersive spectrometry (SEM-EDS) (JSM-7800 F, JEOL, Japan) was used to observe the distribution of crystal phase and morphology of the prepared glass ceramics. The structures of the parent glasses were analyzed using a Raman spectrometer (HORIBA Jobin Yvon S.A.S, France) at room temperature in the range of 200–1500 cm−1. The microhardness-tester (MH-5 L, Shanghai, China) was used to measure the Vickers hardness with a measuring force of 300 N and a load time of 15 s, and the Vickers hardness values were obtained by calculating the average of five detection values. The flexural strength of glass ceramics was detected by the electronic universal material testing machine (CMT4303, MTS, American) with a span of 40 mm and descending speed of 0.5 mm/min. Afterward, the flexural strength values of the glass ceramics were calculated by the equation according to GB/T 6569–2006, as shown in Equationequation (1)(1)
(1) :
where is the flexural strength (MPa), F is the maximum load (N) and L is the lower span of fixture (mm). Also, b and d are the width and height of the sample (mm), respectively. The flexural strength values were obtained by calculating the average of five measurements.
The density was determined using Equationequation (2)(2)
(2) :
where ρ is the density of the glass ceramics, is the mass of the glass ceramics,
is the height of cylindrical sample, and
is the radius of the cylindrical sample.
Moreover, after immersing the glass ceramics in 5% H2SO4 and 5% NaOH solutions for 24 hours, the changes in surface and weight before and after were observed to determine the acid and alkali corrosion resistance of the glass ceramics. The chemical stability was calculated by weighing the samples before corrosion (m0) and after corrosion (m1):
3. Results and discussion
3.1. Thermal analysis of glass ceramics
shows the DSC curves of Ti-bearing blast furnace slag-based glass samples with different Cr2O3 contents at a heating rate of 5°C/min. The transition temperature (Tg) and crystallization temperature (Tp) have been determined as the endothermic and exothermic peak temperatures, respectively, as marked in . The transition temperature and crystallization temperature decreased with the introduction of Cr2O3 as a while. Specifically, the crystallization temperature first decreased with the introduction of Cr2O3, then increased with the increase Cr2O3 concentration from 0.2 wt% to 0.8 wt%, and finally decreased with further increases in Cr2O3 concentration.
Therefore, it can be concluded that crystallization was promoted as the introduction of Cr2O3 as a while. However, it was slightly inhibited as the Cr2O3 concentration increased from 0.2 wt% to 0.8 wt%, and then was slightly promoted again as a further increase in Cr2O3 concentration. Two observed exothermic peaks were observed in the DSC curves for all samples, indicating that there were at least two successive crystallization events. It can be observed that Tg was approximately 720 ~ 750°C. Therefore, in this work, the nucleation temperature was estimated to be 800°C in this work, which was normally 50 ~ 100°C greater than Tg of glasses. The actual Tp of each glass was applied as the crystallization temperature for the preparation of glass ceramics.
3.2. Crystal phase and morphological analysis
The crystal phases of the prepared glass ceramics were identified by XRD, as shown in . There were anorthites, ordered (CaAl2Si2O8), diopside (Ca0.959Ti0.041) (Mg0. 987Al0.013) (Si1.905Al0.095O6) and akermanite, syn(Ca2MgSi2O7) crystals co-precipitated. It can be seen that part of titanium has entered into the crystal of diopside and the chromium has entered into glass phase. The relative intensity of CaAl2Si2O8 was the strongest, indicating that it was the primary crystal of the prepared glass ceramics. With increasing Cr2O3 concentration, no obvious change was observed. Therefore, the introduction of Cr2O3 did not change the main crystals of Ti-bearing blast furnace slag-based glass ceramics.
shows the SEM results of the polished Ti-bearing blast furnace slag-based glass ceramics. Apparently, the distributions between the glassy phase and the crystal phase were relatively uniform. The results of EDS point detections showed that the crystal phase in the glass ceramics was CaAl2Si2O8. As shown in the example of 0.2 wt% Cr2O3, shown in , this is consistent with the XRD results. Other phases were not identified which may be due to their low content and/or small size. As can be observed from –c), the crystals were interlaced with each other in the form of dendrites and embedded in the glass ceramics. In addition, it can be observed that the size of dendrites in the glass ceramic with no introduction of Cr2O3 was much smaller than that of additional Cr2O3. As Cr2O3 content increased from 0.2 wt% to 0.8 wt%, the dendrites gradually decreased and granular crystals gradually increased. When the Cr2O3 concentration is increased to 0.8 wt%, the dendrites almost change to granular crystals, and the crystal size was obviously decreased to less than 1 μm. However, with increase in Cr2O3 concentration, the number of granular crystals gradually decreased, and the dendrites gradually accumulated again via aggregation.
Figure 5. SEM images of the polished Ti-bearing blast furnace slag-based glass ceramics. (a)S0, (b)S1, (c)S2, (d)S3, (e)S4 and (e)S5
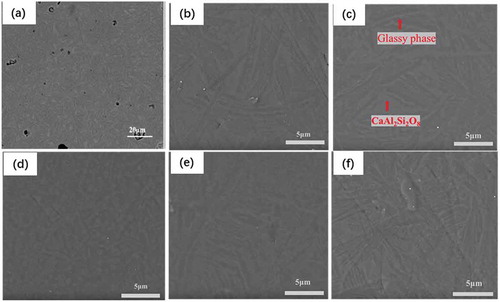
This can suggest that the addition of 0.2 wt% Cr2O3 can promote the dendrites in glass to grow up quickly, while the morphology of the main crystals was transformed into granular crystals and the size of the crystals was refined with further increase in Cr2O3 concentration from 0.2 wt% to 0.8 wt%. Also, with further increase in Cr2O3 concentration, crystallization was promoted again to cause the presence of greater size of dendrites.
3.3. Structural analysis of parent glasses
The structure of the glass is a deeply related to its properties. The Raman spectra for CaO-Al2O3-SiO2-TiO2-Cr2O3 glasses at room temperature were recorded to investigate the parent glass structure. According to previous studies [Citation28–30], the characteristic peaks within the 800–1100 cm−1 region included the main information on silicate-based glasses. Therefore, the present Raman spectra within 800–1100 cm−1 region were deconvoluted by assuming the Gaussian-Deconvolution method similar to the method by Mysen et al. [Citation31]. The [SiO4] tetrahedron structural units can be separated into five types – Qi (i = 0,1,2,3,4, where i represents the number of bridge oxygen per SiO4 tetrahedra) from the previous reports [Citation17,Citation28,Citation30,Citation32]. Therefore, the best-fit simulations with the minimum correlation coefficient r2 ≥ 0.995 were applied, as shown in –f) [Citation29,Citation32]. It was observed that there were an intense band at about 890 cm−1 which was attributed to the vibrations of Ti-O-Si or Ti-O-Ti [Citation29,Citation33]. The other strong band located at about 1035 cm−1 was corresponded to Q3 and a relatively weak band near 930 cm−1 and 1 000 cm−1 were referred to as Q1 and Q2 structure based on previous study [Citation34]. It can be seen that the intensity of Q3 gradually decreased with the content of Cr2O3 increasing from 0 wt% to 0.8 wt%, while it was increased with further increase in Cr2O3 concentration.
Figure 7. Deconvolved results of Raman spectra for the parent glasses with different Cr2O3 contents. (a)S0, (b)S1, (c)S2, (d)S3, (e)S4 and (f)S5
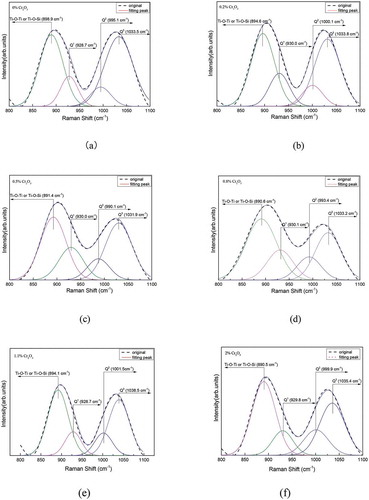
A summary of the deconvolution results was shown in . The results suggested that the main structure unit in Ti-bearing blast furnace slag-based glass was the sheet (Q3). The ratio of dimer (Q1) and chain (Q2) gradually increased, while the ratio of Q3 gradually decreased as the Cr2O3 content increased from 0 wt% to 0.8 wt%. However, the relative intensities of Q3 increased with constantly increasing Cr2O3 concentration.
Table 3. Deconvolved results of Raman spectra for the parent glasses
Based on some studies [Citation29,Citation35], the average number of bridging oxygen atoms of each sample can be estimated by the area ratio of each structural unit (Q0, Q1, Q2, and Q3) multiplied by the number of bridging oxygens, as shown in . It was clear that the amount of bridging oxygen reached a minimum as Cr2O3 content is 0.8 wt%. According to previous study [Citation17], the increase in bridging oxygen caused the silicate structure to polymerize. Therefore, with the increase of Cr2O3 from 0 wt% to 0.8 wt%, the structure of the investigated glass was gradually depolymerized, while the opposite trend was presented with further increase of Cr2O3. The decrease of the sheet (Q3) reduced the degree of polymerization of CaO-Al2O3-SiO2-TiO2-Cr2O3 glasses. As a consequence, when the content of Cr2O3 was 0.8 wt%, it contributed to the formation of a simple silicon-oxygen group, which can provide excellent kinetic conditions for crystallization, so that the crystallization temperature was the lowest at 8 wt% Cr2O3 [Citation17]. Moreover, the simple silicon-oxygen group of glass can promote nucleation and crystallization. As the concentration increased to 0.8 wt%, the number of nuclei formed gradually increased, and the growth spaces of the nuclei restricted to each other during crystallization so that the crystal grain size was gradually decreased. As a result, the dendrites were gradually changed to a smaller sized granular crystal and the surface of the glass ceramics became denser. With a further increase in Cr2O3, crystallization was inhibited, and the dendrites were precipitated again by another increase in Q3.
3.4. Properties of Ti-bearing blast furnace slag-based glass ceramics
showed the measurement results of the flexural strength of Ti-bearing blast furnace slag-based glass ceramics. With the introduction of Cr2O3, the flexural strength showed a slight decrease. Then, as the concentration of Cr2O3 further increased from 0.2 wt% to 2 wt%, the flexural strength values initially increased and then decreased, reaching a maximum of 94.371 MPa when the Cr2O3 content was 0.8 wt%. According to a previous study [Citation1], uniform crystal distribution and small size crystals can enhance the flexural strength. When the content of Cr2O3 increased from 0.2 wt% to 0.8 wt%, the size of the crystal was smaller, and the distribution was uniform, thus leading to enhanced flexural strength. When the content of Cr2O3 increased from 0.8 wt% to 2 wt%, the size of the crystal gradually increased and the microstructure became loose and the flexural strength values decreased accordingly. While the greater flexural strength for the sample with no addition of Cr2O3 may be due to its evenly distributed small dendrites in glass.
The Vickers hardness values for the glass ceramic samples with different Cr2O3 concentrations are presented in . The Vickers hardness values increased first and then decreased with the concentration of Cr2O3 increasing from 0.2 wt% to 2 wt%. Furthermore, when the content of Cr2O3 is 0.8 wt%, the Vickers hardness value reached a maximum hardness of 974.43 MPa. When the Cr2O3 content is 0.8 wt%, the largest number of small-sized granulate crystals were formed in the glass ceramics and uniformly distributed, and the glass ceramics have excellent Vickers hardness values.
Therefore, it can be concluded that Cr2O3 can promote nucleation and crystallization with a low content (≤0.8 wt%). The crystallization temperature can be decreased, and the crystal size can be refined as the concentration of Cr2O3 increased from 0.2 wt% to 0.8 wt% due to the role of depolymerization on the silicate glass network. With further increase in Cr2O3 content, the opposite trend was obtained due to the highly polymerized structure. Additionally, the small-sized granulate crystals can enhance the flexural strength and Vickers hardness of Ti-bearing blast furnace slag-based glass ceramics.
In summary, this research demonstrated that a certain amount of Cr2O3 can promote the precipitation of crystals and generate crystallite to improve the related mechanical performance of glass ceramics.
To analyze the corrosion resistance properties of the prepared glass ceramics, the glass ceramic samples were immersed in 5% H2SO4 and 5% NaOH solutions for 24 h, as shown in . It can be seen that the glass ceramics showed a certain amount of fading after soaking in 5% H2SO4 solution for 24 hours. However, no obvious changes were found on the surface of the samples after soaking in 5% NaOH solution for 24 hours.
Figure 11. The surface condition of the glass ceramics before and after the acid and alkali resistance test
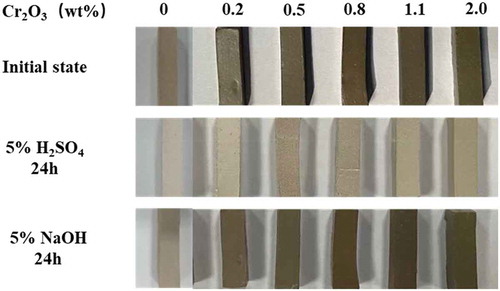
The weight changes of glass ceramics before and after the acid and alkali corrosion test are listed in . The mass loss of samples in acid was less than 2%, and in an alkaline environment was less than 1%. As a result, the prepared glass ceramics have good acid and alkali resistance properties, especially the alkali resistance properties. In addition, the densities of the prepared glass ceramic were measured and shown in . The densities are in the range of 2.65–2.80 g/cm3, which was similar range with other slag-based glass ceramics reported by previous studies [Citation24,Citation36,Citation37],
Table 4. Density, Acid, and Alkali Resistance of the glass ceramics with different contents of Cr2O3.
The prepared glass ceramics showed excellent properties, such as flexural strength, acid resistance, alkali resistance for the samples with no addition and 0.8 wt% addition of Cr2O3, as shown in . The maximal flexural strength of the investigated blast furnace slag glass-ceramic reached 109.58 MPa. The introduction of Cr2O3 induced a slightly decrease in flexural strength and an increase in hardness. On the whole, the flexural strength of the current blast furnace slag-based glass-ceramics is slightly higher than that of others but lower than that of AOD slag-based glass-ceramics. The slag-based glass ceramics showed excellent acid and alkali corrosion resistance [Citation5,Citation38,Citation39].
Table 5. Comparison of main properties of glass-ceramics prepared with better properties with those of others’ works
4. Conclusion
Herein, the effects of Cr2O3 on the crystallization behaviors, microstructure, mechanical properties, and physicochemical properties of Ti-bearing blast furnace slag-based glass ceramics were investigated. The following conclusions can be drawn:
1) The transition temperature and crystallization temperature decreased with the introduction of Cr2O3 as a while. Specifically, the crystallization temperature first decreased with the introduction of Cr2O3, then increased with the increase Cr2O3 concentration from 0.2 wt% to 0.8 wt%, and finally decreased with further increases in Cr2O3 concentration.
2) The crystal phases of Ti-bearing blast furnace slag-based glass ceramics are identified as anorthite, ordered (CaAl2Si2O8), diopside ((Ca0.959Ti0.041)(Mg0.987Al0.013) (Si1.905Al0.095O6)) and akermanite, syn(Ca2MgSi2O7). The main crystal phases of glass ceramics show negligible changes with increasing Cr2O3 content. As the content of Cr2O3 increased to 0.8 wt%, the dendrites gradually decreased and the granular crystals gradually increased. When the Cr2O3 concentration further increased, the number of granular crystals gradually decreased and the dendrites gradually accumulated.
3) The main structure unit in Ti-bearing blast furnace slag-based glass was the sheet Q3. With the increase of Cr2O3 from 0 wt% to 0.8 wt%, the structure of the investigated glass was gradually depolymerized, while the opposite trend was presented with further increase in Cr2O3 content. The relationship between the structure and crystallization of the prepared glass ceramics was discussed.
4) With increasing Cr2O3 content from 0.2 wt% to 2 wt%, the flexural strength values and Vickers hardness values of the glass ceramics first increased and then decreased. When the content of Cr2O3 was 0.8 wt%, the maximum values of flexural strength and Vickers hardness were obtained as 94.371MPa and 974.43MPa, respectively. The greater flexural strength of the sample with no addition of Cr2O3 may be due to it’s evenly distributed small dendrites in glass. The prepared Ti-bearing blast furnace slag-based glass ceramics showed good acid and alkali resistance, especially alkali resistance. The recommended content of Cr2O3 was 0.8 wt% for the addition of Ti-bearing blast furnace slag-based glass ceramics.
Acknowledgments
This work was supported by National Training Program of Innovation and Entrepreneurship for Undergraduates (202010611041).
Disclosure statement
No potential conflict of interest was reported by the author(s).
Additional information
Funding
References
- Zhao Y, Chen D, Bi Y, et al. Preparation of low cost glass–ceramics from molten blast furnace slag. Ceram Int. 2012;38(3):2495–2500.
- Ren S, Aldahri T, Liu W, et al. CO2 mineral sequestration by using blast furnace slag: from batch to continuous experiments. ENERGY. 2021;214:118975.
- Khater G. Influence of Cr2O3, LiF, CaF2 and TiO2 nucleants on the crystallization behavior and microstructure of glass-ceramics based on blast-furnace slag. Ceram Int. 2011;37(7):2193–2199.
- Zhen Y-L, Zhang G-H, Chou K-C. Carbothermic reduction of titanium-bearing blast furnace slag. High Temp Mater Process. 2016;35(3):309–319.
- Wang Y-C, Liu P-J, Luo G-P, et al. Optimization of heat treatment of glass-ceramics made from blast furnace slag. High Temp Mater Process. 2020;39(1):539–544.
- Mukherjee DP, Das SK. Influence of TiO2 content on the crystallization and microstructure of machinable glass-ceramics. J Asian Ceram Soc. 2016;4(1):55–60.
- Mukherjee. The influence of TiO2 content on the properties of glass ceramics: crystallization, microstructure and hardness. Ceram Int. 2014;40(3):4127–4134.
- Gao H, Liu XH, Chen JQ, et al. Preparation of glass-ceramics with low density and high strength using blast furnace slag, glass fiber and water glass. Ceram Int. 2018;44(6):6044–6053.
- Back G-S, Yoon M-J, Jung W-G. Effect of the Cr2O3 and TiO2 as nucleating agents in SiO2-Al2O3-CaO-MgO glass-ceramic system. Met Mater Int. 2017;23(4):798–804.
- Sakamoto A, Yamamoto S. Glass–ceramics: engineering principles and applications. Int J Appl Glass Sci. 2010;1(3):237–247.
- Xi C, Zheng F, Xu J. Preparation of glass-ceramic foams using extracted titanium tailing and glass waste as raw materials. Constr Build Mater. 2018;190:896–909.
- Hisham NAN, Zaid MHM, Saparuddin DI, et al. Crystal growth and mechanical properties of porous glass-ceramics derived from waste soda-lime-silica glass and clam shells. J Mater Res Technol. 2020;9(4):9295–9298.
- Saparuddin DI, Hisham NAN, Aziz SA, et al. Effect of sintering temperature on the crystal growth, microstructure and mechanical strength of foam glass-ceramic from waste materials. J Mater Res Technol. 2020;9(3):5640–5647.
- Al-Wafi R, Eldera SS, Hamzawy EMA. Characterization and in vitro bioactivity study of a new glass ceramic from mica/apatite glass mixtures. J Mater Res Technol. 2020;9(4):7558–7569.
- Nilanjana. Synthesis of transparent chloroborosilicate nanoglass-ceramics: crystallization and growth mechanism of BaCl2 nanocrystalsPeer review under responsibility of The Ceramic Society of Japan and the Korean Ceramic Society.View all notes. J Asian Ceram Soc. 2018;3(4):390–401.
- Saifang. Fabrication of a high-strength lithium disilicate glass-ceramic in a complex glass systemPeer review under responsibility of The Ceramic Society of Japan and the Korean Ceramic Society.View all notes. J Asian Ceram Soc. 2018;1(1):46–52.
- Zhang S, Zhang Y, Qu Z. Effects of soluble Cr2O3 doping on the glass structure, microstructure, crystallization behavior, and properties of MgO-Al2O3-SiO2 sapphirine glass ceramics. Mater Chem Phys. 2020;252:123115.
- Tian J, Wang S, Jiang T. Dielectric characterization of a novel Bi2O3-Nb2O5-SiO2-Al2O3 glass-ceramic with excellent charge-discharge properties. J Eur Ceram Soc. 2019;39(4):1164–1169.
- Khater GA. Influence of Cr2O3, LiF, CaF2 and TiO2 nucleants on the crystallization behavior and microstructure of glass-ceramics based on blast-furnace slag. Ceram Int. 2011;37(7):2193–2199.
- Rezvani M, Eftekhari-Yekta B, Solati-Hashjin M. Effect of Cr2O3, Fe2O3 and TiO2 nucleants on the crystallization behaviour of SiO2-Al2O3-CaO-MgO(R2O) glass-ceramics. Ceram Int. 2005;31(1):75–80.
- Gu-Seul, nbsp, and Back. Effect of the Cr2O3 and TiO2 as nucleating agents in SiO2-Al2O3-CaO-MgO glass-ceramic system. Met Mater Int. 2017;23(4):798–804.
- Dang W, He H-Y. Glass-ceramics fabricated by efficiently utilizing coal gangue. J Asian Ceram Soc. 2020;8(2):365–372.
- Lai F, Leng M, Li J, et al. The Crystallization Behaviors of SiO2-Al2O3-CaO-MgO-TiO2 Glass-Ceramic Systems. Crystals. 2020;10(9):794.
- Zhang S, Zhang Y, Wu T. Effect of Cr2O3 on the crystallization behavior of synthetic diopside and characterization of Cr-doped diopside glass ceramics. Ceram Int. 2018;44(9):10119–10129.
- Wang Y-C, Xin W-B, Huo X-G, et al. Preparation and Properties of Blast Furnace Slag Glass Ceramics Containing Cr2O3. High Temp Mater Process. 2019;38(2019):726–732.
- Deng L-B, Jia R-D, et al. Influence of Cr2O3 on the viscosity and crystallization behavior of glass ceramics based on blast furnace slag. Mater Chem Phys. 2020;240:122212.
- Endo. Production of glass ceramics from sewage sludge. Water Sci Technol. 1997;36(11):235–241.
- Mysen BO, Ryerson FJ, Virgo D. THE INFLUENCE OF TIO2 ON THE STRUCTURE AND DERIVATIVE PROPERTIES OF SILICATE MELTS. Am Mineral. 1980;65(11–1):1150–1165.
- Li J, Shu Q, Chou K. Structural study of glassy CaO-SiO2-CaF2-TiO2 Slags by Raman Spectroscopy and MAS-NMR. ISIJ Inter. 2014;54(4):721–727.
- Mysen BO, Virgo D, Scarfe CM. RELATIONS BETWEEN THE ANIONIC STRUCTURE AND VISCOSITY OF SILICATE MELTS - A RAMAN-SPECTROSCOPIC STUDY. Am Mineral. 1980;65(7–8):690–710.
- Mysen BO, Finger LW, Virgo D, et al. Curve-fitting of Raman spectra of silicate glasses. Am Mineral. 1982;67(7–8):686–695.
- Chen Y, Lai F, Li J. Effect of B2O3 on Structure of Glassy F-Free CaO-SiO2-B2O3 Systems by 29 Si MAS NMR and Raman Spectroscopy. JOM. 2020;72(3):1414–1421.
- Huang W-J, Zhao Y-H, Yu S, et al. Viscosity property and structure analysis of FeO–SiO2–V2O3–TiO2–Cr2O3 Slags. ISIJ Inter. 2016;56(4):594–601.
- Zhang S, Zhang Y, Gao J. Effects of Cr2O3 and CaF2 on the structure, crystal growth behavior, and properties of augite-based glass ceramics. J Eur Ceram Soc. 2019;39(14):4283–4291.
- Zheng K, Liao J, Wang X, et al. Raman spectroscopic study of the structural properties of CaO-MgO-SiO2-TiO2 slags. J Non-Crystalline Solids. 2013;376:209–215.
- Zhang S, Zhang Y, Gao J, et al. Effects of Cr2O3 and CaF2 on the structure, crystal growth behavior, and properties of augite-based glass ceramics. J Eur Ceram Soc. 2019;39(14):4283–4291.
- Karamanov A, Pisciella P, Pelino M. The effect of Cr2O3 as a nucleating agent in iron-rich glass-ceramics. J Eur Ceram Soc. 1999;19(15):2641–2645.
- Zhang W, He F, Xie J. Crystallization mechanism and properties of glass ceramics from modified molten blast furnace slag. J Non-Crystalline Solids. 2018;502:164–171.
- Zhang S, Zhang Y, Qu Z. Physicochemical property and chromium leaching behavior in different environments of glass ceramics prepared from AOD stainless steel slag. J Alloys Compd. 2019;805:1106–1116.