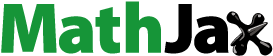
ABSTRACT
A comparative study on the microwave hybrid sintering and conventional sintering of Al2O3 slip casts is reported to observe temperature distribution, grain-growth kinetics and densification in different regions of samples. It was found that the microwave hybrid sintering resulted in a significantly lower temperature difference between the surface and the center as compared to that in conventional sintering. Remarkably, in the microwave-hybrid-sintered samples, the estimated activation energy for grain growth at the center was approximately 27% lower than that at the surface in the conventionally sintered samples. The grain-growth rate in microwave hybrid sintering was more than three times higher at the sample center ((62.07 ± 0.06) × 10–21 m3/s) than at the sample surface in the conventional sintering ((18.75 ± 0.11) × 10–21 m3/s). The volume diffusion for grain growth was found to be the most effective mechanism in all samples, irrespective of the sintering technique and point of observation. It is suggested that the heat-flux, as well as the microwave effect and influence of surface charge due to the electric field of the field-assisted process were the reasons for these outcomes.
1. Introduction
Alumina (Al2O3) is one of the most economical and most commonly used materials in structural ceramics owing to advantageous properties such as a high melting point, corrosion resistance, wear resistance, hardness, thermal conductivity, and biocompatibility. It has numerous applications and is used as a material for electronic-device substrates, combustion-engine components, gears, refractories, and body joints and dental implants [Citation1–3].
Sintering is a process of consolidating powder particles to fabricate bulk material by mass transport [Citation4,Citation5]. Generally, Al2O3 powder and green bodies of desired shapes are sintered into dense bodies using the conventional sintering process, especially on the industrial scale. However, conventional sintering consumes large amounts of energy as Al2O3 has a very high melting point (2072°C), which necessitates very long processing times and high temperatures. Using conventional sintering as the powder-consolidating process, Lahiri et al. [Citation6] sintered ~92% dense α–Al2O3 at 1700°C with a heating cycle of 9 h, Fabris et al. [Citation7] used a temperature of 1670°C and heating cycle of more than 16 h to achieve ~98% dense Al2O3, and Tuan et al. [Citation8] used a temperature of 1600°C and heating cycle of 6 h.
The increasing acceptance of microwave sintering for ceramics manufacturing reflects its executability as a field-assisted process [Citation9,Citation10]. One of the largest points of interest is that irrespective of the material chemistry, microwaves almost always decrease the sintering temperature. However, most ceramic materials cannot absorb microwaves properly at low temperatures owing to low dielectric losses, and the dielectric loss increases with the sample temperature. Therefore, collateral heating is applied either by conventional means or by using a susceptor such as silicon carbide, which is effective for low-temperature heating with microwaves [Citation11,Citation12].
Owing to the aforementioned advantages, microwave hybrid sintering has previously been proposed as a solution for sintering Al2O3 with relatively low temperatures and time durations. With microwave hybrid sintering, the shrinkage curves shift toward lower temperatures relative to those for conventional sintering [Citation5,Citation13,Citation14]. Experimental demonstrations and mathematical modeling have been performed in attempts to explain how electromagnetic fields and diffusional transport interact with one another in this field-assisted sintering process, as well as to explain the reasons for the outcomes [Citation15–17]. However, the topic is still in debate, as the mechanisms and laws governing microwave sintering remain unclear. Limited comparative research has been published on the conventional and microwave sintering of Al2O3 [Citation18–20]. Nevertheless, further comparative study is required to clarify the phenomenon of microwave sintering. In particular, the temperature distribution, heat-flux behavior, densification, grain-growth kinetics, and their associated mechanisms on the surface as well as at center of the samples treated by microwave and conventional sintering need to be investigated thoroughly.
The accurate temperature measurement during microwave sintering of a sample is of importance in exploring the mechanisms of microwave sintering. The presence of a thermocouple in a microwave cavity may lead to electromagnetic field perturbations [Citation18]. The need for accurate temperature measurement further enhances especially when a kinetic comparison with conventional sintering is performed because such a comparison cannot be carried out properly if the exact temperature is unknown.
To verify the temperatures at the surface and at the center of the sintered bodies, process temperature control rings (PTCR) were used. A PTCR is a ring-shaped ceramic body that is used to accurately measure the temperature of the heating process taking place at the location of the ring. It measures the total heat transferred to the ring via conduction, convection, and radiation. A PTCR shrinks when exposed to heat, and the degree of shrinkage depends on the actual temperature at its location as well as the duration for which it is exposed to heat. The measured shrinkage is converted into the ring temperature, which represents the total amount of heat absorbed by the ring [Citation21,Citation22], with the help of a chart. The temperature of a sample can be measured more accurately using a combination of a PTCR and the thermocouple of the furnace as mentioned in Section 2.
The objective of the present study was to determine how microwave hybrid sintering is different from conventional sintering for the consolidation of Al2O3, with a focus on densification behavior and grain growth kinetics on the surface as well as at the center of the sample. To this end, α–Al2O3 green bodies were fabricated by slip casting, which is a commercially used method to mold large bodies of any shape. The green bodies were sintered using conventional sintering and microwave hybrid sintering. A combination of PTCRs and furnace thermocouples was used to measure the temperatures. The grain-growth exponents, rates, and activation energies were estimated, and the heat flux and possible mechanisms for the grain growth were explored.
2. Experimental procedure
Fine α–Al2O3 powder (99.99%, AKP–50, Sumitomo Chemical, Japan) was used as the precursor. Particle size distribution of the α–Al2O3 powder was measured by a particle size analyzer (LS13 320 MW, Beckman Coulter Inc., USA). The powder was ball-milled for 72 h in an ethanol medium, prior to measuring the primary particle size, to remove the agglomerates. α–Al2O3 slip casts were fabricated, using the as-received powder, for each sintering technique (conventional and microwave hybrid sintering). An Al2O3 solid loading of 80 wt% (50 vol%) in deionized water was used for the slip casting. Ammonium polymethacrylic acid solution (DARVAN® C–N, 25 wt% active matter, R.T. Vanderbilt Company, Inc., USA) was used as the dispersant, and it was added in the quantities with 0.10–0.70 wt% active matter with respect to Al2O3. A planetary centrifugal mixer (ARE-500, Thinky Corporation, Japan) was used to mix the slurries for 10 min at 1000 rpm. The dispersant amount was optimized by viscosity measurement (DV2TLV viscometer, Brookfield Ametek, USA) using an SC4–25 coaxial cylindrical spindle at a shear rate of 2 s−1. Prior to the viscosity measurements, all slurries were subjected to pre-shearing for 30s at a shear rate of 30s−1, followed by a rest condition for 1 min, in order to ensure the same rheological experience for the slurries.
After the optimization of rheological properties, polyvinyl alcohol (31,000–50,000 Mw, 87–89% hydrolyzed, Sigma-Aldrich) with 20 wt% solution in deionized water was added as a binder with quantity of 1 wt% active matter w.r.t Al2O3. The slurries were mixed again for 10 min. Debubbling was performed in the same mixer using the “defoaming” mode at 1000 rpm for 20 min. Subsequently, the slurries were poured into a two-part gypsum mold with a diameter of 30 mm and height of 50 mm. After drying and shaping in the mold, the green casts were taken out of the mold and dried at 120°C for 12 h, following which they were debinded at 700°C for 2 h in an electric box furnace (XY–1700 Mini, Hantech Co., Korea). The heating rate used in drying and debinding was 2°C/min. Next, the green casts were ground to a height of 15 mm, and the green density was measured by dimensional analysis. It was made sure that all the samples had the same relative green density of 58.5%.
For accurate temperature measurements, Al2O3 cylindrical green bodies (diameter: 40 mm; height: 21 mm) were fabricated via light uniaxial pressing. Three different types of PTCRs (outer diameter = 20 mm, inner diameter = 10 mm, thickness = 7 mm; FERRO France Sarl, France) with different temperature ranges were used such that one ring was at center of the compact, and the other was on the surface, as shown in . Conventional sintering was performed in an electric box furnace (XY–1700 Mini, Hantech Co., Korea), while microwave hybrid sintering was carried out in a single-mode-cavity microwave furnace (SINTERMAT–1600, Unicera, Inc., Korea) at 2.45 GHz, with SiC granules surrounding the sample for radiant heating. A heating rate of 10°C/min was used up to 1550°C, with no holding time. The furnace thermocouples were touching the surface of the samples in both the furnaces. After sintering, a vernier caliper was used to measure the diameters of the shrunk PTCRs. The measured diameter was then converted into temperature according to the chart provided by the PTCR manufacturer.
Figure 1. Schematic of temperature measurement for an Al2O3 uniaxially pressed sample, using PTCR in a (a) conventional furnace and (b) microwave furnace.
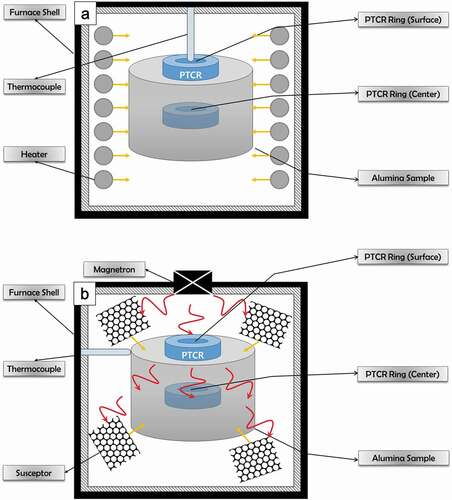
To reduce the errors in the measured temperature due to a slightly higher absorption of heat after a certain heating cycle ends, the surface temperature during the conventional sintering was assumed to be the set temperature since the surface was in contact with the thermocouple, and the small difference in the measured temperature with PTCR was subtracted. Then, the same difference was subtracted from the measured temperature at the center, as well as from the surface and central temperatures of the sample microwave hybrid sintered at the same set temperature. Although the temperatures measured with PTCR may not exactly be the actual temperatures, the difference between the temperatures at the center and surface for a certain sintering process, as well as that between the two different sintering processes could be found and compared with the help of the differences in the PTCR diameters. The specifications of the rings, set temperatures, and measured temperatures are given in .
Table 1. Temperature measurement results
Thus, after the temperature measurements, the green slip casts, without any PTCR, were placed in a high-purity alumina crucible that was packed with the same powder as the compact to avoid contamination from the environment, and both conventional and microwave hybrid sintering were carried out. The furnace thermocouples were in contact with the surface of the samples in both the furnaces. The furnace temperature was set to 1550°C, and the heating rate was 10°C/min. For each sintering technique, five different holding times ranging from 0–120 min were used.
To analyze the surface (s) and center (c) points, as schematically shown in , the sintered samples were first cut to full depth, perpendicular to the surface, to obtain a piece 3 mm in width along a segment containing point s. Subsequently, the piece was cut parallel to the surface to obtain pieces with points s and c, each having a depth of 3 mm. Next, the density was analyzed using Archimedes’ method. Ten readings were taken for every sample, and the average was calculated. Phase analysis of all the samples was carried out by X-ray diffraction (D8 Advance X-ray diffractometer, Bruker, Germany). The samples were then polished (MetPrep 3, Allied High Tech, Canada) and thermally etched in the electric box furnace at 1450°C for 30 min. The heating rate was 10°C/min. Microstructural analysis was performed by field emission–scanning electron microscope (FE–SEM, JSM-7100 F, JEOL, Japan). An image processing software package (Fiji-ImageJ) [Citation23] was used to measure the grain size distribution from around three hundred grains for each sample using the FE–SEM images. The grain size distribution for each sample was split into 0.5 µm bins (ranges), and the results were analyzed thoroughly.
Figure 2. Schematic of an Al2O3 slip cast sample and the points of interest (s: surface; c: center).
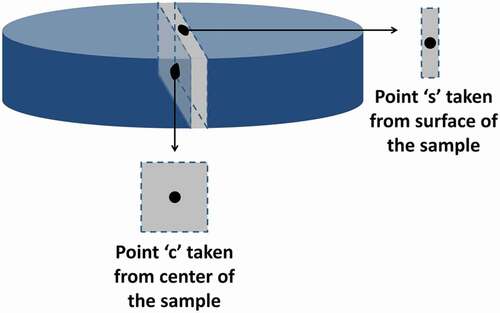
For estimating the activation energies for grain growth, new green slip casts were fabricated following the previous method, and the samples were sintered using both conventional and microwave hybrid sintering methods at set temperatures of 1400, 1450, and 1500°C. No holding time was given, and a heating rate of 10°C/min was used. After cutting and polishing, the samples were thermally etched at temperatures that were less than the set sintering temperatures by 100°C. Next, FE-SEM analysis was carried out to evaluate the grain size.
3. Results and discussion
shows the morphology and particle-size distribution of the ball-milled fine α–Al2O3 AKP–50 powder particles. As shown in , the powder particles are submicron and have random shapes. Agglomeration occurred owing to their fineness, which caused van der Waals attractive forces to be dominant. However, the primary particle size seems to be approximately 0.2 to 0.3 μm. As shown in , the powder exhibits an average particle size of 0.31 µm, which is in agreement with the FE-SEM results, indicating that the ball-milling resulted in good deagglomeration of the powder. Hence, all the particle sizes were in the colloidal range (0.1–10 µm), which is preferred for slip casting [Citation24].
It is well known that the solid loading in a slurry for slip casting should be as high as possible to achieve a high green density [Citation25]. Therefore, a solid loading of 80 wt% (50 vol%) was used for the slurries prepared in this work. However, ceramic particles are prone to agglomeration because of van der Waals forces, especially at high solid loading. Therefore, a dispersant was needed to be used to disperse the particles. Studies have shown that the surface properties of powders change with the addition of a dispersant; consequently, repulsive forces, either due to the electrostatic repulsion originating from the overlapping of electrical double layers or due to steric hindrance resulting from the absorption of large molecules, become higher than the attractive forces, causing the particles to remain suspended in the slurry [Citation24,Citation25].
shows the optimization of the slurry rheology. No viscosity value could be obtained when dispersant was used with active matter of 0.1–0.25 wt% w.r.t Al2O3 as the slurry was too thick to measure viscosity using the SC4–25 coaxial cylindrical spindle. The lowest measured viscosity of 7.60 Pa.s was obtained when the dispersant was used with an active matter of 0.5 wt% with respect to Al2O3. Therefore, this quantity of the dispersant was chosen for all the samples. Since a decrease in flocculation increases the amount of liquid available for shearing, the slip produces the minimum flocculation when it exhibits the minimum viscosity. The viscosity increased with further increase in the dispersant quantity. This increase in viscosity is regarded to disturbance in particle stabilization due to the surface tension effect of the increased quantity of dispersant [Citation26].
shows the results of temperature measurements with PTCRs. For the set temperature of 950°C, the measured temperature at the surface of the conventionally sintered sample is considered to be correct as the thermocouple was in contact with the surface. However, a large difference of 100°C is observed between the temperatures at the center and the surface, with the center showing a temperature of 850°C. Similarly, the temperature measured during conventional sintering was significantly higher at the surface than at the center for the set temperatures of 1250 and 1550°C (see ).
Figure 5. Measured temperature versus set temperature of the (a) conventionally sintered samples and (b) microwave-hybrid-sintered samples.
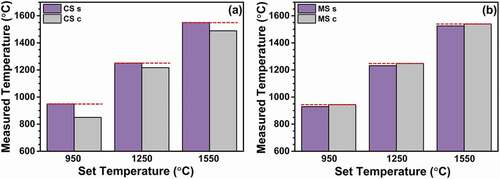
During microwave hybrid sintering, the temperatures obtained from the PTCRs are higher at the center than at the surface, and those at the center are approximately near to the set temperatures. In addition, the temperature difference between the surface and the center is remarkably lower than that observed during conventional sintering. The details are presented later along with the discussions for the densification and grain-size results.
Phase analysis of all 20 samples, whose surfaces and centers were sintered by either technique, was performed to check whether there was any detectable impurity or phase change during either type of sintering. shows the XRD patterns of four samples. Every sample contained an α–Al2O3 phase similar to the as-received powder, and no secondary phase was present in any of the samples.
The variations in sintering results can be clarified by a descriptive analysis of the microstructural evolutions as a function of holding time, mode of sintering, and sample region. shows FE–SEM microstructures obtained from the surface and center of samples sintered by conventional sintering with holding times of 0, 30, 60, 90, and 120 min. All the samples contained a few equiaxed and many non-equiaxed grains, with non-uniform grain-size distributions. Such a random mixture of relatively smaller and larger grains is obtained during the sintering of Al2O3 in air [Citation27].
The intrinsic motion of a grain boundary in a single-material system (such as the current system) is regulated by the diffusion of matter from the shortening grain to the enlarging grain. This implies that the grain-boundary movement is proportional to the diffusion coefficient. This diffusion coefficient is exhausted if the oxygen partial pressure is very low, which can occur in vacuum [Citation28]. Hence, sintering of Al2O3 in vacuum slows down the sintering rate, impeding the amplified grain growth. In contrast, in air, no low oxygen partial pressure is present that could cause exhaustion of the oxygen diffusing through the grain boundaries and limit its motion [Citation27]. In addition, it has been reported in other studies that during sintering in air, water vapor affects the mass transport such that the grain growth is enhanced [Citation29,Citation30].
The pores were very small when no holding time was applied, and they were larger in the samples that underwent holding, demonstrating a pore coarsening phenomenon. In a sintering process, small pores are dragged by the moving grain boundary, decreasing the number of pores. Where some pores shrink because of the diffusion of matter, others grow by Ostwald ripening. Such pore growth usually occurs at high temperatures and long holding times [Citation31]. This can be regarded as a reason for the larger pores in the samples that underwent holding at the sintering temperature.
The pores were intra-granular as well as inter-granular, consistent with the results of other reported studies [Citation27,Citation32,Citation33]. The appearance of intra-granular pores may indicate a high sintering temperature. At a high sintering temperature, if the rate of grain boundary migration is larger than the grain boundary diffusion rate, then the pores inside the grains cannot be discharged in time and remain inside the grains, forming intra-granular pores [Citation32].
For all sintering time conditions, the grains are clearly larger on the surface point than in the center. Furthermore, as the holding time increases, the grains become larger. The larger grain size on the surface indicates a higher temperature and higher grain-boundary mobility.
Similarly, shows FE–SEM microstructures obtained from the surface and center of samples sintered by microwave hybrid sintering with holding times of 0, 30, 60, 90, and 120 min. Similar to the conventionally sintered samples, the microwave-hybrid-sintered samples also contained few equiaxed grains and many non-equiaxed grains, with non-uniform grain-size distributions. The pores are intra-granular as well as inter-granular, as expected when Al2O3 is sintered in the presence of an electric field [Citation34].
In contrast to the samples sintered by conventional sintering, the microwave-hybrid-sintered samples had larger grains in center than on surface. It is also clear that the grains increase in size as the holding time increases. The larger grain size at the center indicates a higher temperature and higher grain-boundary mobility.
shows the relative densities from the surface and center of the sintered samples. The relative densities of all the samples were above 95%. Irrespective of the sintering technique, all the samples showed a direct relation between the relative density and holding time. The relative densities were higher at the center than on the surface for the microwave-hybrid-sintered samples. The relative densities were higher on the surface than at the center for the conventionally sintered samples. The relative density of a full sample (denoted by the symbol f) was measured between the relative densities of the surface and center regions. The measured temperatures were higher at the surface of the conventionally sintered samples than at the surface as well as at the center of the microwave-hybrid-sintered samples (). However, for a certain holding time, the relative density was higher at the center as well as the surface of the microwave-hybrid-sintered sample. MS 120 c resulted in the highest relative density overall (98.7%). MS 120 s had a relative density of 98.2%. Meanwhile, CS 120 s exhibited a relative density of 97.9%, and CS 120 c had a relative density of 97.3%. The detailed reasoning will be provided together with the grain size results.
Evidently, the grain growth is extremely sensitive to the heating mechanism and point of observation along the sample. shows quantitative proof of the change in grain size with respect to the sintering method and holding time. shows the grain size distributions from surface and center of the conventionally sintered samples. CS 0 c has grain size distribution up to only 2.5 µm. The highest volume percentage of grains (41.8%) lies in the 0.5–1 µm range for this sample. The grain size distribution drastically widens as the holding time increases. CS 90 c has the highest volume percentage of grains (15.0%) in the 2–2.5 µm range. Finally, CS 120 c has the highest volume percentage of grains (16.5%) in the 3.5–4 µm range. The grain size distributions for both samples reach 7 µm.
Figure 10. Grain-size distributions of (a) conventionally sintered samples and (b) microwave-hybrid-sintered samples, (c) average grain sizes at the surface and center points after different holding times, and (d) schematic showing the directions of the temperature gradient and grain growth during conventional and microwave sintering.
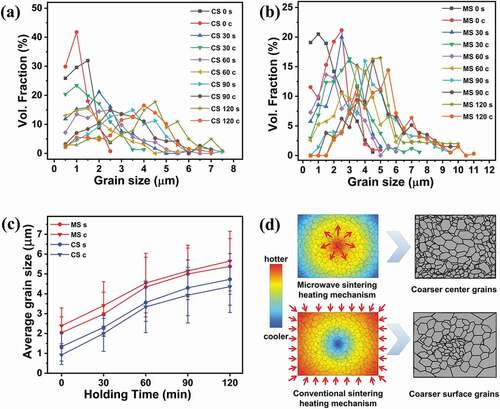
CS 0 s had a broader grain size distribution than CS 0 c, with 32.0 vol% grains in the 1–1.5 µm range. The grain size distribution drastically increases with holding time. The grain size distribution for CS 30s reaches 6 µm, whereas those for CS 60s, CS 90s, and CS 120 s reach 7.5 µm. The highest volume percentage of grains also shifts to larger grain sizes with increasing holding time. CS 120 s has its highest grain volume fraction (17.8%) in the 4–4.5 µm range. Thus, it can also be concluded that the highest volume percentage of grains is shifted toward larger grain sizes on the surface than at the center. In addition, the grain size distribution is broader on the surface for conventionally sintered samples than at the center.
shows the grain size distributions from the surface and center of the microwave-hybrid-sintered samples. MS 0 s has a grain size distribution up to 4.5 µm, with the highest volume percentage of grains (20.5%) lying in the 0.5–1 µm range. Meanwhile, MS 0 c is distributed up to 5 µm, with the highest volume percentage of grains (21.1%) in the 2–2.5 µm range. The grain size distribution significantly increases with holding time, especially at the centers of the samples. MS 120 s and MS 120 c do not contain grains up to 1.5 µm. The grain size reaches 10 µm for MS 120 s and 11 µm for MS 120 c. Thus, it can also be concluded that the grain size distribution is broader at the center for microwave-hybrid-sintered samples than on the surface. In addition, the highest volume percentage of grains is shifted toward larger grain sizes at the center than on the surface for a certain holding time. Comparing microwave hybrid sintering and conventional sintering, it can also be seen that the overall grain size distribution (on the surface as well as at the center) is wider in the case of microwave hybrid sintering. In addition, the increase in the distribution with holding time is more significant in the case of microwave hybrid sintering than in the case of conventional sintering.
The average grain size () exhibits a behavior similar to that of the relative density () for both sintering techniques. For a certain holding time, the average grain size was larger at the center as well as the surface of the microwave-hybrid-sintered samples, even though the measured temperature was higher at the surface of the conventionally sintered samples. As can be seen, the average grain size is larger on the surface than at the center in the case of conventional sintering. The average grain size is larger at the center than on the surface in the case of microwave hybrid sintering. In addition, all the samples exhibit direct relations between the average grain size and holding time, i.e. as the holding time increases, the average grain size increases, irrespective of the sintering technique. MS 120 c exhibits the largest average grain size overall (5.7 µm). The average grain size for MS 120 s is 5.3 µm. Meanwhile, CS 120 s has an average grain size of 4.8 µm, and the average grain size is 4.3 µm for CS 120 c.
The densification and grain growth results are explained below. Microwave sintering utilizes microwave electromagnetic radiation. Therefore, it is speculated that the microwave electromagnetic field enhances the basic driving force of reducing the total interfacial energy or provides an extra driving force due to the ponderomotive force, which is the oscillatory motion of charged particles in the presence of a coherent electromagnetic field for the diffusion of ions [Citation18,Citation35]. This leads to an accelerated mass transport via electromagnetic activation, rather than thermal activation. This phenomenon is called the “microwave effect,” which also leads to a decrease in the activation energy for sintering [Citation35,Citation36].
Previously, it was shown that compared to conventional sintering, microwave sintering enhances the sinterability by increasing the densification rate in Al2O3, owing to the microwave effect [Citation37–39]. Zuo et al. [Citation5] reported that conventionally sintered pure Al2O3 exhibited an activation energy for densification of 528 ± 22 kJ/mol, which decreased to 440 ± 8 kJ/mol for microwave sintering. In another study [Citation14], the activation energies for sintering were 652 and 451 kJ/mol for conventionally sintered and microwave-sintered alumina, respectively, and the decrease in activation energy was attributed to the microwave effect. Khalid et al. [Citation13] reported a significantly low activation energy for densification of 246 ± 11 kJ/mol for α–Al2O3, and this low activation energy was considered to be due to the microwave effect. The activation energy for sintering in fact is the activation energy for the dominant diffusion mechanism. It is directly related to the diffusion coefficient of the rate-limiting species, which are the slowest diffusing species [Citation40]. It is suggested that the enhanced densification in the microwave-hybrid-sintered samples relative to the surface of the conventionally sintered samples was caused by the microwave effect.
The analysis of grain-growth kinetics is an important approach to understand the mechanisms involved in the different grain-growth behaviors shown by the same material (Al2O3). Janney et al. [Citation41] reported that microwave-sintered samples showed a larger average grain size than conventionally sintered sample. They estimated the activation energies for the grain growth of Al2O3 during conventional and microwave sintering, and the estimated activation energy for grain growth during microwave sintering was 20% less than that during conventional sintering because of the microwave effect. Wang et al. [Citation42] showed an increase in grain growth during microwave sintering due to the microwave effect. Golestani-fard et al. [Citation19] also observed an increased grain growth for microwave sintering than for conventional sintering. It is suggested that similar to the densification results, the enhanced grain growth for the microwave-hybrid-sintered samples, compared to that for the surface of the conventionally sintered samples, was due to the microwave effect.
The broadening of the grain size distributions with holding times are attributed to the closure of open porosities with an increase in the relative density. Grain growth elongates the open pores, thereby increasing the length and decreasing the diameter because of densification. This leads to pinching off of the pores, resulting in closed pores. The conversion of open pores that act as grain-growth inhibitors into closed pores enhances the grain growth [Citation4].
Another means of explaining these results was suggested by Becker et al. [Citation43]. They proposed that during electric-field-assisted sintering of ceramics, there exists a high surface area of material if there is no plastic deformation. The high surface area causes buildup and discharge of the surface charge. As a result, particle sliding occurs due to surface softening, which speeds up densification. If there is no plastic deformation, the electric field also affects the grain-growth mechanisms. The charged defects that move to the particle surface also affect the grain-boundary mobility, influencing the grain growth.
As shown in , the relative densities at the center are higher than those on the surface for the samples sintered by microwave hybrid sintering, whereas the opposite is true for the samples sintered by conventional sintering. Similarly, as is clear from , the average grain size is larger at the center than on the surface in the case of microwave-hybrid-sintered samples. The opposite is true in the case of conventionally sintered samples. These results can be explained by the temperature gradient shown in .
Microwaves are absorbed volumetrically by the sample, i.e. the sample starts volumetric bulk self-heating via molecular interactions with the electromagnetic field, and the electromagnetic energy is converted into heat energy to heat the sample. As the heat is generated from within the volume and radiates outwards because the surface keeps losing heat to the surroundings, a heat flux that is directed outwards is generated. Interfaces exhibit a significant boundary resistance to thermal transport, depending on how efficiently the phonons can cross the interface. Therefore, heat transport across an interface results in a step change in temperature from one side of the interface to the other [Citation13,Citation44]. Consequently, the heat moves from the core of the sample to the surface with a continuous relative temperature drop. Hence, the densification and grain growth are higher at the center, with the shift of grain-size distribution to larger grains.
In the presence of a susceptor material (SiC was used as the susceptor in this study), the sample absorbs radiant heat from the surroundings as well. The hybrid heating of the sample causes a more even temperature distribution throughout the sample in the low-loss Al2O3, resulting in a relatively more uniform heating throughout the sample. This reduces the magnitude of temperature gradient between the sample surface and the center. The curve of the parabolic temperature distribution in the sample is relatively flattened [Citation45], which is in agreement with the results of the temperature measurements as shown in . The difference between the temperature values at the center and the surface of the microwave-hybrid-sintered samples is quite small when compared with conventional sintering. An important point to note is that despite using a susceptor, the temperature was higher at the sample center than the surface, which proposes that the heating was volumetric. It is suggested that the susceptor did not shield the interior of the sample from the microwave electric field, and an appreciable microwave electric field was present inside the sample that led to an influence on the mass transport due to the microwave effect.
In the case of conventional sintering, heat moves from the heating elements to the sample surface and is absorbed by the sample surface. The surface heats up, and the heat energy further moves toward the core of the sample via conduction. Further, a relative temperature drop occurs continuously from the surface toward the core [Citation44,Citation46]. Hence, the grains at the sample surface are larger than those at the center with conventional sintering.
To explore the effects of activation energy for grain growth in the current study, the newly fabricated green slip casts were sintered at set temperatures of 1400, 1450, and 1500°C without any holding time. To estimate the temperatures that the samples were exposed to, linear intercepts of the measured values shown in were obtained, as shown in . The estimated temperature values are presented in .
Table 2. Estimated temperatures from the measured temperatures using PTCRs
The microstructures of the center and surface of the conventionally sintered samples are shown in . Evidently, the samples experienced pore-coarsening with increase in temperature. The grains are larger at the surface than at the center, and the grain size increases as the temperature increases. depicts the microstructures of the center and surface of the microwave-hybrid-sintered samples. The samples experienced pore-coarsening with increase in temperature. Notably, the grains are larger at the center than at the surface, and the grain size increases as the temperature increases. Comparing the results shown in , it can be seen that larger grains are produced in the microwave-hybrid-sintered samples than in the conventionally sintered ones. represents the quantified data for the average grain sizes. It can be seen that the microwave effect results in a larger average grain size at the center and the surface, even if the measured temperature is lower than that at the surface of the conventionally sintered samples.
Figure 12. FE–SEM images showing the microstructures of the conventionally sintered samples at different set temperatures with no holding time (s: surface; c: center).
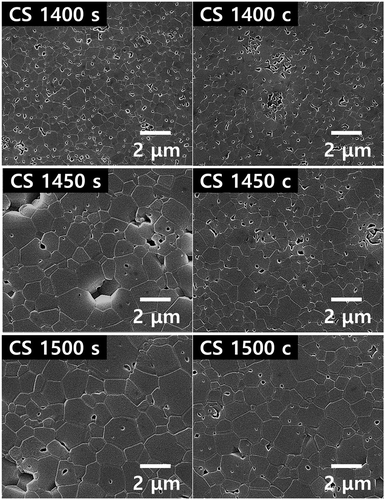
Figure 13. FE–SEM images showing the microstructures of microwave-hybrid-sintered samples at different set temperatures with no holding time (s: surface; c: center).
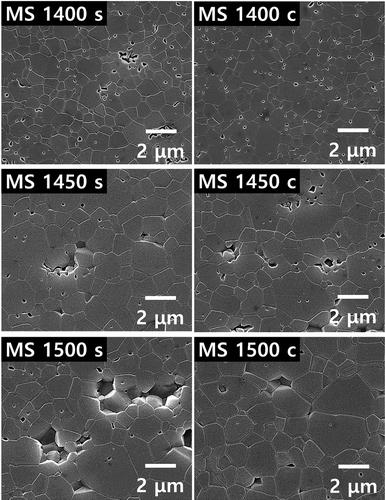
Figure 14. Average grain sizes at the surface and center points after sintering at different estimated temperatures.
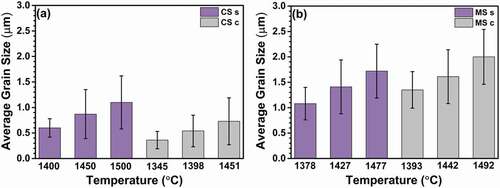
Because grain growth is a thermally activated process, it is assumed that the grain growth is dependent on the sintering temperature according to the following equation [Citation47]:
where Dt is the final grain size, D0 is the initial grain size, R is the gas constant, and T is the sintering temperature. Considering D0 to be a constant for all the samples, the activation energy can be obtained from the slope of the Arrhenius plot between the left-hand side and right-hand side of Equation 1.
The Arrhenius plots are shown in along with the estimated activation energy values. For the conventionally sintered samples, the estimated activation energy at the center is 152.78 ± 0.6 kJ/mol, whereas that at the surface is 134.60 ± 1.4 kJ/mol. The activation energy at the surface of the microwave-hybrid-sintered samples is estimated to be 106.15 ± 0.7 kJ/mol, whereas that at the center is 98.70 ± 0.4 kJ/mol.
Figure 15. Estimated activation energy for grain-growth at the (a) surface and (b) center of the conventionally sintered samples, and that at the (c) surface and (d) center of the microwave-hybrid-sintered samples.
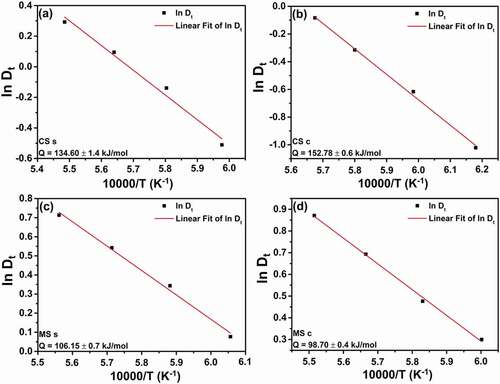
Comparing the conventionally sintered and microwave-hybrid-sintered samples, it can be noted that the activation energy for grain growth is significantly lowered when the same material (Al2O3) is sintered in the microwave-hybrid environment. The activation energy for grain growth at the center of the microwave-hybrid-sintered samples is approximately 27% less than that at the surface of the conventionally sintered samples. If only surfaces of the samples sintered by the two different processes are compared, then the activation energy is found to be 21% less in the case of microwave hybrid sintering. These results are attributed to the microwave effect.
It is suggested that in the current study, slip casting as a wet shaping method played an important role in lowering the activation energies for the densification as well as for the grain growth because of a higher particle compaction and better homogeneity of particle coordination [Citation19]. In addition, it is suggested that the sintering aids present in the as-received Al2O3 powder helped to decrease the activation energies for the grain growth further.
The grain growth rate is another important parameter of grain-growth kinetics that can be calculated from a kinetic law of the following form [Citation48]:
where K is the grain growth rate, D is the grain size after the holding time, D0 is the grain size in the absence of holding, t is the holding time, and n is a grain-growth constant depending on the grain-growth mechanism. For a single-phase system, the grain-growth constant typically varies between 2 and 4. An n value of 2 corresponds to grain-growth by grain boundary diffusion, 3 corresponds to volume diffusion, and 4 means grain-growth by surface diffusion. For grain growth by surface diffusion, a high volume percentage of free surface (porosity) is required [Citation48]. As all the samples sintered at the set temperature of 1550°C have relative densities greater than 95%, the possibility of grain growth by surface diffusion can be ruled out.
represents the plots of Dn – D0n versus holding time t, where the n value taken was 2. The linear fits for CS s, CS c, and MS c exhibit linear regression coefficients of 0.97, and that shown by MS s is 0.96. presents the plots of Dn – D0n versus holding time, where the n value taken was 3. The linear fits for CS s, CS c, and MS c exhibit linear regression coefficients of 0.99, and that shown by MS s is 0.98. Although the two n values do not bring a big difference, an n value of 3 gives R2 values closer to 1. Thus, it is suggested that for all the samples; both those that were conventionally sintered and those that were microwave-hybrid-sintered, and both on the surface and at the center, grain growth by volume diffusion was more dominant than grain boundary diffusion. A grain-growth constant of 3 has also previously been shown for the grain-growth analysis of Al2O3 for conventional as well as microwave sintering [Citation31,Citation41].
Figure 16. Grain-growth mechanism estimation with grain-growth constants n of (a) 2 and (b) 3, and (c) grain-growth rate (K) for conventionally sintered and microwave-hybrid-sintered Al2O3.
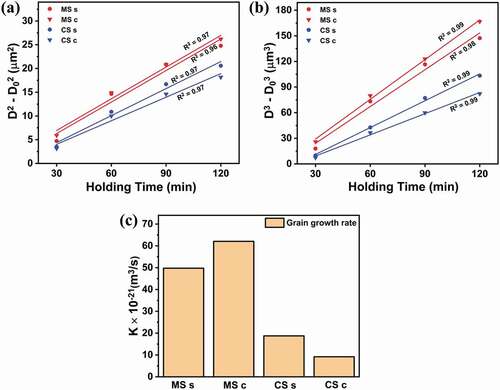
The grain-growth rate (K) for conventionally sintered and microwave-hybrid-sintered Al2O3 was calculated from the slopes of graphs plotted between D3 – D30 and the holding time. There was indeed a difference in the grain-growth rate between the sintering techniques and for different points of observation. The grain-growth rate at the center of the microwave-hybrid-sintered samples was (62.07 ± 0.06) × 10–21 m3/s, whereas that on the surface was lower at (49.77 ± 0.13) × 10–21 m3/s. In contrast, for conventionally sintered samples, the grain-growth rate on the surface was high, at (18.75 ± 0.11) × 10–21 m3/s, whereas that at the center was low, at (9.18 ± 0.10) × 10–21 m3/s. Hence, microwave hybrid sintering resulted in a remarkably enhanced grain-growth rate compared to conventional sintering. This rate was more than three times higher at the centers of the microwave-hybrid-sintered samples than on the surfaces of the conventionally sintered samples. In addition, it was more than five times higher on the surface with microwave sintering than at the center with conventional sintering.
The microwave-hybrid-sintered samples showed a higher grain-growth rate than conventionally sintered samples, further confirming that Al2O3 grains grow faster with microwave hybrid sintering than with conventional sintering. These data confirm that the microwave effect not only decreases the activation energy for grain growth, but also accelerates grain boundary migration during microwave hybrid sintering.
Diffusion mechanisms for densification may be different between conventional and microwave sintering [Citation41], but diffusion mechanisms should not be confused with grain-growth mechanisms as all the samples showed same dominant grain-growth mechanism (volume diffusion). The structural changes in grains during grain growth under conventional and microwave hybrid sintering were similar, and the difference was in the grain size. Hence, the postulation that the same dominant grain-growth kinetics mechanism exists in both conventional and microwave sintering is supported by the similarity of microstructural evolutions, as shown in . The postulation is also supported by the observation of dominant cubic grain-growth kinetics in both the sintering methods, as shown in : the same value of n, providing an excellent fit for both different sintering techniques. Thus, it is suggested that the difference in grain growth observed during the two sintering processes was due to the difference in the rate of material transfer, i.e. the diffusivities of the controlling species, rather than the mechanism involved.
4. Conclusion
In this study, slip casting of α–Al2O3 was performed, and the samples were subjected to conventional and microwave hybrid sintering. The sintering temperatures were accurately measured using PTCRs. The microstructural evolutions, densification behaviors, grain-size distributions, and grain-growth kinetics at the surface and the center of the samples were studied and compared.
The temperature measurements revealed that when fired at a certain set temperature, the temperature was significantly lower at the sample center than at the surface in the case of conventional sintering; a set temperature of 1550°C resulted in a temperature of 1489°C at the center. In the case of microwave hybrid sintering, a set temperature of 1550°C resulted in a temperature of 1525°C at the surface and 1540°C at the center. These results indicate that despite using a susceptor, the resulting heat flux was directed outwards.
The highest relative density achieved was 98.70% at the center of the sample subjected to microwave sintering with a holding time of 120 min. The former sintering technique resulted in higher relative densities at the center, while the latter technique resulted in higher relative densities on the surface, with 97.88% being the highest relative density for conventional sintering with a holding time of 120 min. For a certain set temperature, the microwave hybrid sintering resulted in relative densities higher than those obtained from the conventional sintering, despite a lower actual temperature at the surface and center than that at the surface of the conventionally sintered samples. The highest volume fraction of the grains shifted to a larger grain-size range at the surface than at the center for the conventionally sintered samples, with CS 120 s showing 17.76 vol% grains in the 4–4.5 μm grain-size range. The outcomes were opposite in the case of the microwave-hybrid-sintered samples, with MS 120 c showing 14.40 vol% grains in the 5–5.5 μm grain-size range.
The estimated activation energy for grain growth was the lowest at the center of the microwave-hybrid-sintered samples, whereas it was the highest at the center of the conventionally sintered samples. The grain-growth rate was more than three times higher at the centers of the microwave-hybrid-sintered samples ((62.07 ± 0.06) × 10–21 m3/s) than at the surfaces of the conventionally sintered samples. These all results were mainly attributed to the heat-flux, as well as the microwave effect and the influence of surface charge in the presence of microwave electromagnetic fields.
Acknowledgments
The authors gratefully acknowledge the National Research Foundation of Korea (NRF), Ministry of Education, Ministry of Science and ICT (MSIT), Korea, for the financial support under project number NRF-2018R1D1A1B07043025. The authors also thank the Ministry of Trade, Industry & Energy (MOTIE), Korea, for the financial support through the program “Industrial strategic technology development program” under project number 20011520.
Disclosure statement
No potential conflict of interest was reported by the author(s).
Additional information
Funding
References
- Parikh PB. Alumina ceramics: engineering applications and domestic market potential. Trans Indian Ceram Soc. 1995;54:179–184.
- Shirai T, Watanabe H, Fuji M, et al. Structural properties and surface characteristics on aluminum oxide powders. Annu Rep Adv Ceram Res Cent Nagoya Inst Technol. 2009;9:23–31.
- Pulgarín HLC, Albano MP. Sintering and microstrusture of Al2O3 and Al2O3-ZrO2 Ceramics. Procedia Mater Sci. 2015;8:180–189.
- Rahaman MN. Sintering of ceramics. 1st ed. Boca Raton: CRC Press; 2007.
- Zuo F, Badev A, Saunier S, et al. Microwave versus conventional sintering: estimate of the apparent activation energy for densification of α-alumina and zinc oxide. J Eur Ceram Soc. 2014;34:3103–3110.
- Lahiri S, Sinhamahapatra S, Tripathi HS, et al. Rationalizing the role of magnesia and titania on sintering of α-alumina. Ceram Int. 2016;42:15405–15413.
- Fabris DCN, Polla MB, Acordi J, et al. Effect of MgO.Al2O3.SiO2 glass-ceramic as sintering aid on properties of alumina armors. Mater Sci Eng A. 2020;781:139237.
- Tuan WH, Chen RZ, Wang TC, et al. Mechanical properties of Al2O3/ZrO2 composites. J Eur Ceram Soc. 2002;22:2827–2833.
- Clark DE, Sutton WH. Microwave processing of materials. Annu Rev Mater Sci. 1996;26:299–331.
- Katz JD. Microwave sintering of ceramics. Annu Rev Mater Sci. 1992;22:153–170.
- Heuguet R, Marinel S, Thuault A, et al. Effects of the susceptor dielectric properties on the microwave sintering of alumina. J Am Ceram Soc. 2013;96:3728–3736.
- Khalid MW, Kim Y Il, Haq MA, et al. Densification behavior of microwave hybrid sintered Al2O3 bimodal powder mixtures and comparison with 3D modeling and simulation. Int J Refract Met Hard Mater. 2021;99:105586.
- Khalid MW, Kim Y Il, Haq MA, et al. Microwave hybrid sintering of Al2O3 and Al2O3–ZrO2 composites, and effects of ZrO2 crystal structure on mechanical properties, thermal properties, and sintering kinetics. Ceram Int. 2020;46:9002–9010.
- Mizuno M, Obata S, Takayama S, et al. Sintering of alumina by 2.45 GHz microwave heating. J Eur Ceram Soc. 2004;24:387–391.
- Rybakov KI, Olevsky EA, Krikun EV. Microwave sintering: fundamentals and modeling. J Am Ceram Soc. 2013;96:1003–1020.
- Bhattacharya M, Basak T. Susceptor-assisted enhanced microwave processing of ceramics - a review. Crit Rev Solid State Mater Sci. 2017;42:433–469.
- Singh S, Gupta D, Jain V, et al. Microwave processing of materials and applications in manufacturing industries: a review. Mater Manuf Process. 2015;30(1):1–29.
- Zuoa F, Saunier S, Marinel S, et al. Investigation of the mechanism(s) controlling microwave sintering of α-alumina: influence of the powder parameters on the grain growth, thermodynamics and densification kinetics. J Eur Ceram Soc. 2015;35:959–970.
- Golestani-fard F, Mazaheri M, Aminzare M, et al. Microstructural evolution of a commercial ultrafine alumina powder densified by different methods. J Eur Ceram Soc. 2011;31:2593–2599.
- Yun HS, Kim JC, Jeong DY, et al. Effect of nanoscale powders and microwave sintering on densification of alumina ceramics. Met Mater Int. 2016;22:1108–1115.
- Chen Y, Fan B, Shao G, et al. Preparation of large size ZTA ceramics with eccentric circle shape by microwave sintering. J Adv Ceram. 2016;5:291–297.
- Santos T, Hennetier L, Costa VAF, et al. Microwave versus conventional porcelain firing: temperature measurement. J Manuf Process. 2019;41:92–100.
- Schindelin J, Arganda-Carreras I, Frise E, et al. Fiji: an open-source platform for biological-image analysis. Nat Methods. 2012;9:676–682.
- Tarì G, Ferreira JMF, Fonseca AT. Influence of particle size and particle size distribution on drying-shrinkage behaviour of alumina slip cast bodies. Ceram Int. 1999;25:577–580.
- Tsetsekou A, Agrafiotis C, Leon I, et al. Optimization of the rheological properties of alumina slurries for ceramic processing applications part II: spray-drying. J Eur Ceram Soc. 2001;21:493–506.
- Promdej C, Areeraksakul S, Pavarajarm V, et al. Preparation of translucent alumina ceramic specimen using slip casting method. J Ceram Soc Japan. 2008;116:409–413.
- Mata-Osoro G, Moya JS, Pecharroman C. Transparent alumina by vacuum sintering. J Eur Ceram Soc. 2012;32:2925–2933.
- Bennison SJ, Harmer MP. Swelling of hot-pressed Al2O3. J Am Ceram Soc. 1985;68:591–597.
- Chinelatto ASA, Tomasi R. Influence of processing atmosphere on the microstructural evolution of submicron alumina powder during sintering. Ceram Int. 2009;35:2915–2920.
- Wei GC, Rhodes WH. Sintering of translucent alumina in a nitrogen-hydrogen gas atmosphere. J Am Ceram Soc. 2000;83:1641–1648.
- Ratzker B, Wagner A, Kalabukhov S, et al. Non-uniform microstructure evolution in transparent alumina during dwell stage of high-pressure spark plasma sintering. Acta Mater. 2020;199:469–479.
- Yang Y, Li X, Liu Z, et al. Pressureless sintering of YIG ceramics from coprecipitated nanopowders. Magnetochemistry. 2021;7:56.
- Gajdowski C, Bohmler J, Lorgouilloux Y. Influence of post-hip temperature on microstructural and optical properties of pure MgAl2O4 spinel: from opaque to transparent ceramics. J Eur Ceram Soc. 2017;37:5347–5351.
- Kim BN, Hiraga K, Morita K, et al. Microstructure and optical properties of transparent alumina. Acta Mater. 2009;57:1319–1326.
- Thridandapani RR, Folz DC, Clark DE. Estimation of activation energies for sintering 8 mol% yttria-zirconia using conventional and microwave heating. Int J Appl Ceram Technol. 2014;11:938–945.
- Freeman SA, Booske JH, Cooper RF. Microwave field enhancement of charge transport in sodium chloride. Phys Rev Lett. 1995;74:2042–2045.
- Fang Y, Cheng J, Roy R, et al. Enhancing densification of zirconia-containing ceramic-matrix composites by microwave processing. J Mater Sci. 1997;32:4925–4930.
- Zuo F, Carry C, Saunier S, et al. Comparison of the microwave and conventional sintering of alumina: effect of MgO doping and particle size. J Am Ceram Soc. 2013;96:1732–1737.
- Samuels J, Brandon JR. Effect of composition on the enhanced microwave sintering of alumina-based ceramic composites. J Mater Sci. 1992;27:3259–3265.
- Tyrpekl V, Naji M, Holzhäuser M, et al. On the role of the electrical field in spark plasma sintering of UO2+x. Sci Rep. 2017;7:1–9.
- Janney MA, Kimrey HD, Schmidt MA, et al. Grain growth in microwave-annealed alumina. J Am Ceram Soc. 1991;74:1675–1681.
- Wang J, Binner J, Pang Y, et al. Microwave-enhanced densification of sol-gel alumina films. Thin Solid Films. 2008;516:5996–6001.
- Becker MZ, Shomrat N, Tsur Y. Recent advances in mechanism research and methods for electric-field-assisted sintering of ceramics. Adv Mater. 2018;30:1–8.
- Every AG, Tzou Y, Hasselman DPH, et al. The effect of particle size on the thermal conductivity of ZnS/Diamond composites. Acta Metall Mater. 1992;40:123–129.
- Curkovic L, Veseli R, Gabelica I, et al. A review of microwave-assisted sintering technique. Trans Famena. 2021;45:1–16.
- Ramesh S, Zulkifli N, Tan CY, et al. Comparison between microwave and conventional sintering on the properties and microstructural evolution of tetragonal zirconia. Ceram Int. 2018;44:8922–8927.
- Shukla S, Seal S, Vij R, et al. Reduced activation energy for grain growth in nanocrystalline yttria-stabilized zirconia. Nano Lett. 2003;3:397–401.
- Santanach JG, Weibel A, Estourns C, et al. Spark plasma sintering of alumina: study of parameters, formal sintering analysis and hypotheses on the mechanism(s) involved in densification and grain growth. Acta Mater. 2011;59:1400–1408.