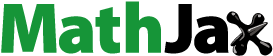
ABSTRACT
Here, we focused on the firing atmosphere to promote low-temperature sintering and enhance the dielectric properties of low-temperature co-fired alumina (LTCA) containing 5 wt.% of CuO–TiO2–Nb2O5–Ag2O as the sintering aid. Controlling the oxygen partial pressure (pO2) to form Ag–Cu–Ti–Nb–O-based complex oxides and lowering the melting temperature of the sintering aid are necessary to improve the sinterability. Moreover, controlling the pO2 such that AgNbO3 disappears is important to improve the dielectric properties of LTCA. A dense sintered body with approximately 95% relative density was obtained by firing an LTCA sample for 2 h at a firing temperature of 900°C and pO2 of 0.02 atm, and its dielectric properties were measurable. The thermal conductivity of 17 W/mK was better than that of conventional low-temperature co-fired ceramics (2–7 W/mK). These results provide important guidelines for low-temperature sintering and producing LTCA with enhanced dielectric properties.
1. Introduction
Alumina (Al2O3) has a high thermal conductivity, high physical strength, and excellent dielectric properties [Citation1–5], and it is therefore widely used to fabricate electronic components, such as wiring substrates and integrated circuits (IC) packages. However, in general, the sintering temperature of pure alumina, even in fine powder form, is approximately 1400°C or higher, which is not preferable for energy saving and realizing a carbon-neutral society. Furthermore, co-fired conductor materials must have a high melting point, such as that of W or Mo, resulting in high electrical resistance. The ceramics that can be fired together with low-resistance conductor materials, such as Ag (melting point of 961°C) or Cu (melting point of 1084°C), are called low-temperature co-fired ceramic (LTCC) materials [Citation6–10]. Because LTCC materials allow the fabrication of several electrical components, including built-in capacitors, inductors, and low-loss transmission lines, they are widely used for producing high-frequency modules. However, LTCC materials must contain large amounts of glass in alumina (approximately 50–60% of the total weight) to achieve low-temperature sintering; hence, the majority of these materials exhibit several limitations, such as low thermal conductivities.
As a first step toward the production of LTCC modules with high thermal conductivities and physical strengths (such as those of alumina), several researchers have developed sintering aids that allow low-temperature sintering when mixed in small quantities. Although researchers [Citation11–16] have previously examined sintering aids based on MnO–TiO2 [Citation11,Citation13], CuO–TiO2 [Citation11,Citation12,Citation14,Citation15], and CuO–TiO2–MgO [Citation16], none of the compositions delivered adequate sintering performance at 1000°C. In contrast, we obtained dense alumina at sintering temperatures of 935–1000°C by adding 4–10 wt.% of CuO–Nb2O5 (binary type) and CuO–TiO2–Nb2O5 (ternary type) sintering aids to alumina [Citation17–20]. Furthermore, the sintering temperature could be decreased to 900°C (or below) using 5 wt.% of quaternary sintering aids. In this case, Ag2O was added to a CuO–TiO2–Nb2O5 ternary sintering aid [Citation21–23]. We confirmed that the melting temperature of CuO–TiO2–Nb2O5 was lowered by the addition of Ag2O [Citation21,Citation23]. The production of Co-firing alumina, containing 5 wt.% of the aforementioned quaternary sintering aids, with Ag electrodes at 900°C or below was also possible by increasing the Ag2O content in the sintering aid [Citation22]. One of the obtained sintered materials exhibited a thermal conductivity of 18 W/mK [Citation21,Citation22], which was significantly higher than that of conventional LTCC materials (approximately 2–7 W/mK [Citation8,Citation9]). The microwave relative dielectric constant (εr) (measured at approximately 12 GHz) after firing at 860°C for 24 h was 11.2, and the product of the quality factor and resonant frequency (Q × f) was 4600 GHz [Citation22]. These values are sufficient for the LTCC materials used in the microwave region spanning from 300 MHz to 30 GHz. This suggests that the obtained novel materials, named as “low-temperature co-fired alumina” (LTCA) materials, can be used as LTCC modules owing to their high thermal conductivities [Citation23].
However, the retention time of LTCA at the firing temperature is 24 h, and further enhancement in sinterability (that is, shortening of the retention time) is essential for its practical use. In addition, the dielectric properties of LTCA are significantly inferior to those of the alumina single component [Citation21–23]. At present, efforts are being made to use millimeter waves (region: 30 GHz or higher) for high-speed data transfer [Citation24]; hence, a significant improvement in the Q × f value of LTCA fired for a relatively shorter retention time is required. However, in reality, the sinterability of the LTCA sample with a retention time of 2 h at 900°C in an air atmosphere is worse than that of the sample with a retention time of 24 h at the same temperature [Citation23]; hence, we were unable to measure the dielectric properties. Therefore, in this study, we focused on the firing atmosphere. Although certain studies on the effect of firing atmosphere on the sinterability of alumina have been conducted [Citation18,Citation25], none of them were centered on LTCA. Here, we investigated the enhancement in both the sinterability and dielectric property of LTCA, specifically by controlling the oxygen partial pressure (pO2).
2. Materials and methods
2.1. Fabrication of LTCA
shows the process flow for obtaining alumina ceramics containing the CuO–TiO2–Nb2O5–Ag2O sintering aid used in this study. Alumina powder (95 wt.%; TM-5D; Taimei Chemical Co., Ltd.; average particle diameter of 0.2 μm) was mixed with 5 wt.% of a sintering aid composed of CuO, TiO2, Nb2O5, and Ag2O (commercially available chemicals). The molar ratio of CuO:TiO2:Nb2O5:Ag2O was fixed at 4:1:2:3.2, which was previously determined as the best co-firing ratio for quaternary oxides [Citation22]. The powder was mixed in a ball mill for 16 h using water as the dispersion medium. The mixture was then dried, granulated in polyvinyl alcohol binder, and finally molded into discs by applying a uniaxial pressure of 75 MPa. After burning the binder, the green bodies (unfired discs) were fired at temperatures ranging from 750 to 1000°C for 2 h (heating and cooling rates: 10°C/min); nitrogen (N2) gas, air, and oxygen (O2) gas, were used in the firing atmosphere. The pO2 was controlled by changing the flow ratio of the O2 and N2 gases, as required. For comparison, samples fired in the same atmosphere for 24 h were also prepared and evaluated.
2.2. Characterizations
The properties of the sintered samples, such as the bulk density (ρ), microwave dielectric property, and thermal conductivity (κ), were measured. The theoretical densities of the samples were calculated from those of alumina (3.99 g/cm3), CuO (6.31 g/cm3), TiO2 (4.25 g/cm3), Nb2O5 (4.47 g/cm3), and Ag2O (7.14 g/cm3), assuming the properties to be additive; the theoretical density of alumina containing 5 wt.% of the sintering aid used in this study was 4.05 g/cm3. The relative density was calculated as the ratio of measured bulk density to theoretical density. The following three major dielectric properties were analyzed using a network analyzer (Agilent Technologies, 8720ES) using the Hakki-Coleman method [Citation26]:
Relative dielectric constant (εr)
Product of the quality factor and resonant frequency (Q × f)
Temperature coefficient of the resonant frequency (τf)
The τf values were calculated using the following equation:
where f(T0) and f(T1) are the resonant frequencies at 20 and 80°C, respectively. The thermal conductivities were measured using the xenon flash method (Netzsch, LFA447).
Further measurements for analyzing the sintering performance and dielectric properties of the LTCA were conducted using scanning electron microscopy (SEM; JEOL, JSM-7600 F) and X-ray diffraction (XRD; Rigaku, Ultima IV) with a Cu Kα radiation source, along with a differential thermal analyzer (DTA; Seiko Instruments, TG/DTA32).
3. Results and discussion
3.1. Effect of three firing atmospheres (air, O2, and N2) on the sintering performance of the LTCA
shows the relationship between the ceramic density and firing temperature of the alumina containing 5 wt.% of the CuO–TiO2–Nb2O5–Ag2O sintering aid. It can be seen that the sintering performance changes according to the firing atmosphere. No significant dependence of the sintered density on the firing atmosphere was observed at a firing temperature of 750°C. The densities of the samples were approximately the same as those of the green compacts, indicating that densification of alumina was not initiated at this temperature. At a firing temperature of 800°C, densification was observed in all the samples, and the sintered density of the samples was higher in the N2 () atmosphere than that in air () or the O2 () atmosphere. The obtained sintered densities of the samples in the three firing atmospheres were in the following order: N2 = air > O2. At firing temperatures in the range of 800–900°C, the increase in the sintered density of the samples under air and O2 atmospheres was larger than that in the N2 atmosphere. Furthermore, the sintered density was in the following order: air > O2 > N2. At the firing temperature of 900°C, the sintered density of the sample fired in air reached approximately 3.79 g/cm3, which is approximately 94% of the theoretical density of the material (4.05 g/cm3). At the firing temperature of 1000°C, the sintered densities of the samples under all the three firing atmospheres were more than 94% of their theoretical densities.
Figure 2. Relationship between the sintered density and firing temperature of the alumina containing the CuO–TiO2–Nb2O5–Ag2O sintering aid obtained under (a) N2 atmosphere, (b) air, (c) O2 atmosphere, and (d) N2–O2 (pO2 = 0.02 atm) atmosphere. The retention time at each temperature was 2 h.
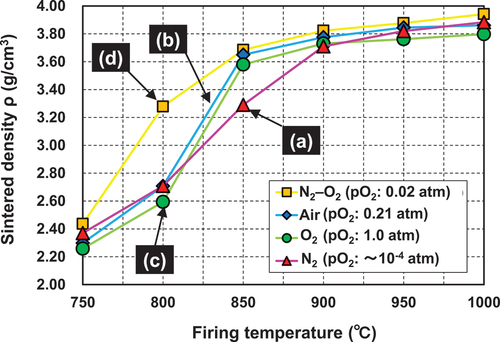
presents the SEM images of the fractured surfaces of the sintered samples under various firing conditions. At a firing temperature of 800°C in air, a slight necking was observed (). Necking and grains with angular shapes were observed clearly at a firing temperature of 900°C (). At a firing temperature of 950°C, grain growth and near disappearance of voids were observed (). For the samples fired at 900°C in N2 and O2 atmospheres ( d and e), the grain morphologies were similar to that of the sample fired at the same temperature in air (); however, the porosities were slightly higher.
Figure 3. SEM images of the fractured surfaces of the sintered samples fired at (a) 800°C in air, (b) 900°C in air, (c) 950°C in air, (d) 900°C in an N2 atmosphere, (e) 900°C in an O2 atmosphere, and (f) 900°C in an N2–O2 atmosphere (pO2 = 0.02 atm). The retention time at each temperature was 2 h.
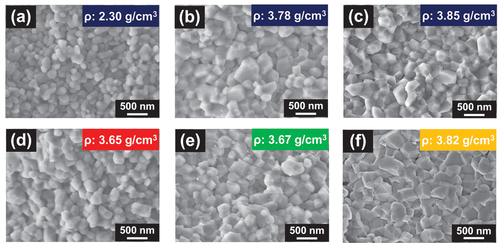
The above results clarify the dependence of the sintering behavior of alumina on the firing atmosphere, despite containing the same sintering aid. shows the DTA curves of the heat-treated sintering aids in different atmospheres (heating rate was 10°C/min). The melting temperature of the sintering aid determined from the endothermic peak in air was approximately 866°C (), which was lower than that in the O2 atmosphere (approximately 875°C) (). It can also be seen that the melting temperature of the sintering aid in the N2 atmosphere was approximately 831°C (), which was more than 30°C lower than the melting temperatures in the other atmospheres. However, at temperatures between 800 and 850°C (see ), the densification of the samples fired in air and the O2 atmosphere was faster compared to that in the N2 atmosphere, although the sintering aids did not melt in air and the O2 atmosphere. Therefore, we assumed that the densification of the alumina was due to the difference in the solid compounds produced during the firing; hence, we performed an XRD analysis of the sintering aids after the heat treatment at different temperatures.
Figure 4. DTA curves of the CuO–TiO2–Nb2O5–Ag2O sintering aids obtained in (a) air, (b) O2 atmosphere, (c) N2 atmosphere, and (d) N2–O2 (pO2 = 0.02 atm) atmosphere.
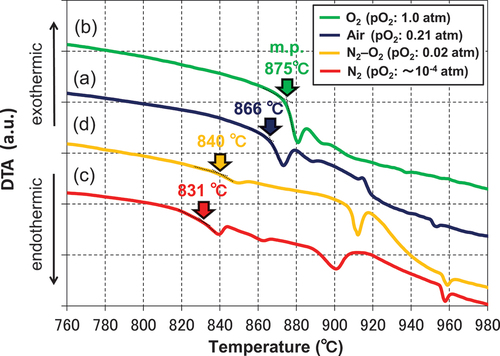
presents the XRD patterns of the sintering aids after heat treatment at 750, 800, and 850°C in air. According to the DTA results (), the sintering aids fired in air did not yield the liquid phase until the firing temperatures reached 866°C. Instead, a novel Ag–Cu–Ti–Nb–O-type complex oxide (represented by the symbol ●) was produced in the temperature range of 750–800°C. This compound was presumed to have the same crystal structure as that of the quadruple-perovskite-type Cu3.21Ti1.16Nb2.63O12 (ICDD-PDF #01-080-7641; space group: Im ; lattice parameter a: 0.747946 (4) nm) [Citation27], and Ag was incorporated into the structure. This complex oxide was considered to significantly promote solid-state sintering [Citation23] in the temperature range of 750–850°C, as shown in . Currently, we are also conducting a detailed study to determine the accurate composition and structure of the novel Ag–Cu–Ti–Nb–O-type complex oxide, which will be beneficial for future studies in this field.
shows the XRD patterns of the sintering aid after heat treatment at 850°C in different firing atmospheres. The sintering aid samples fired in the O2 atmosphere did not yield the liquid phase until the firing temperature reached 875°C; however, the Ag–Cu–Ti–Nb–O-type complex oxide was also detected at 850°C (), as in the case of heat treatment in air (). Therefore, we assumed that the difference in the sinterability of the samples fired in air and the O2 atmosphere was due to the difference in their solid-phase diffusivity, which depends on the melting temperature of each sintering aid. In contrast, the sinterability of the sample fired in the N2 atmosphere at 800°C was better than those of the samples fired in other atmospheres, because the melting temperature of the former sample was the lowest among those observed in the three atmospheres, as shown in . However, the Ag–Cu–Ti–Nb–O-type complex oxide was not produced, even at the elevated firing temperature of 850°C (). Therefore, we concluded that the degree of sintering was lower in the N2 atmosphere than in air and the O2 atmosphere at 850–900°C.
Figure 6. XRD patterns of the sintering aid after heat treatment at 850°C for 2 h in (a) O2 atmosphere, (b) air, (c) N2 atmosphere, and (d) N2–O2 (pO2 = 0.02 atm) atmosphere.
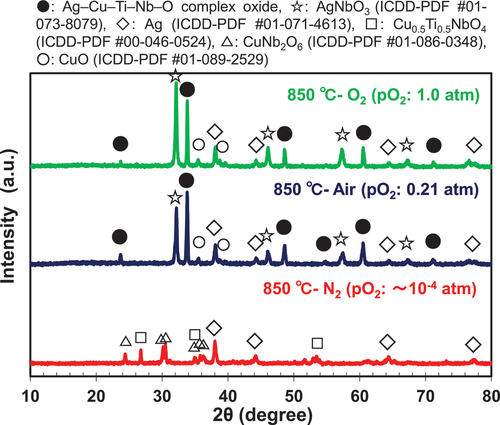
For reference, the trends of the melting temperature and the XRD patterns shown in were qualitatively consistent with the results of the experiments performed using the CuO–TiO2–Nb2O5 sintering aid [Citation18].
3.2. Improvement in the sinterability of LTCA by controlling pO2 during firing
From the above results, two factors that enhance the sinterability of LTCA were suggested, as reported in a previous study on alumina with ternary sintering aids [Citation18]:
(1) Formation of Ag–Cu–Ti–Nb–O complex oxide from the sintering aid.
(2) Low melting temperature of the sintering aid.
To verify these aforementioned factors, the pO2 in our study was controlled by changing the flow rate ratio of N2 and O2, and the effect of the pO2 on the density of the sintered body was investigated in detail.
a and b show the pO2 dependence of the sintered densities of alumina containing 5 wt.% of the CuO–TiO2–Nb2O5–Ag2O quaternary sintering aid obtained by firing at 920 and 850°C for 2 h, respectively. Furthermore, previous results for alumina containing 5 wt.% of the CuO–TiO2–Nb2O5 ternary sintering aid (the molar ratio CuO: TiO2: Nb2O5 was 4: 1: 2) are also shown [Citation18]. In these figures, the curve exhibits a convex shape, indicating the pO2 dependence of the density of the sintered body. Although the pO2 dependence of the density of the sintered sample with the quaternary sintering aid was smaller than that of the sintered alumina with the abovementioned ternary sintering aid, a similar pO2 dependence was observed. Moreover, the density of the sintered body reached the maximum value at a pO2 of 0.02 atm, which is lower than that in air. In addition, the densities of the sintered bodies fired at 0.002 atm ≤ pO2 < 0.21 atm exceeded those of the samples fired in air.
Figure 7. pO2 dependence of the sintered densities of the alumina containing 5 wt.% of the CuO–TiO2–Nb2O5 (ternary) or CuO–TiO2–Nb2O5–Ag2O (quaternary) sintering aids fired at (a) 920°C and (b) 850°C for 2 h.
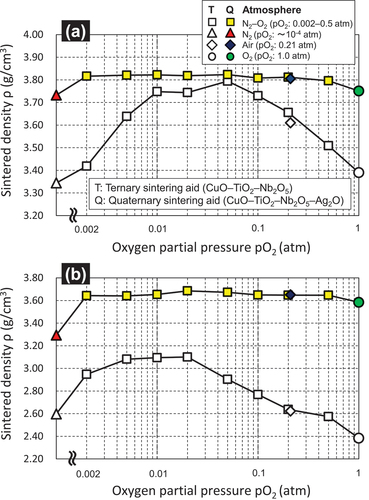
In this study, the pO2 during firing was found to play a crucial role in determining the density of the sintered body. shows the relationship between the firing temperature and the sintered densities of the samples fired in an atmosphere with a pO2 of 0.02 atm. At all the firing temperatures, the sintered density in the atmosphere with a pO2 of 0.02 atm was higher than those of the samples fired in the other three atmospheres. In addition, as shown in , the fractured surface of the sample fired at 900°C was angular, and grain boundary fracture as well as traces of intragranular fracture were observed.
To understand the reason for these results, the following qualitative analysis was performed. presents the pO2 dependence of the XRD patterns of the sintering aids after heat treatment at 850°C for 2 h using N2–O2 mixed gas. Interesting results were obtained that differed from those obtained using the ternary sintering aid. At a pO2 of 0.5 atm, AgNbO3 was obtained as the main phase, although the Ag–Cu–Ti–Nb–O complex oxide was also present. The intensity of the peak corresponding to AgNbO3 decreased with decreasing pO2, and nearly disappeared at pO2 ≤ 0.02 atm (). In contrast, the Ag–Cu–Ti–Nb–O complex oxide remained when the pO2 was equal to or more than 0.005 atm. When the pO2 was 0.002 atm, the intensity of the peak of the complex oxide significantly decreased. Furthermore, as described in , formation of the complex oxide was not confirmed in the case of firing in the N2 atmosphere.
The presence or absence of the Ag–Cu–Ti–Nb–O complex oxides () and the pO2 dependence of the sintered densities () are qualitatively consistent. In addition, as shown in a and d, among the firing conditions for forming the Ag–Cu–Ti–Nb–O complex oxide, the melting point of the sintering aid at the pO2 of 0.02 atm was 840°C, which was lower than that in air (866°C). Thus, the melting point of the sintering aid () was in qualitative agreement with the pO2 dependence of the sintered densities (). As shown in , the factor leading to the decrease in the melting temperature of the sintering aid due to the decrease in pO2 during heat treatment is unclear at this time. We presume that the ratio of Cu+ to Cu2+ in the sintering aid increases with decreasing pO2, which may be the cause of the decrease in the melting temperature; further research on this topic will be presented in our future studies. summarizes the relationship between the melting temperatures of the quaternary sintering aids used in this study and those of the ternary sintering aids reported in a previous study [Citation18], as well as the sintered densities of the alumina containing the above sintering aids after firing at 850°C for 2 h. In this figure, the plots are divided into the cases where the (Ag–)Cu–Ti–Nb–O complex oxides are formed and those where they are absent. From the above figure, it is clear that increasing the density of the sintered body of alumina is effective as the sintering aid forms the abovementioned complex oxide and has a low melting point. This clarifies the factors essential for enhancing the sinterability of alumina in this system.
Figure 8. XRD patterns of the sintering aid after heat treatment at 850°C and different pO2 adjusted by the N2–O2 mixture atmosphere. The retention time at each temperature was 2 h.
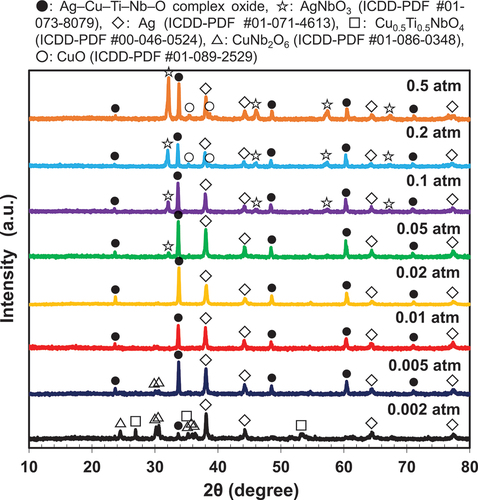
Figure 9. Relationship between the sintering densities of the alumina containing 5 wt.% of the CuO–TiO2–Nb2O5 (ternary) or CuO–TiO2–Nb2O5–Ag2O (quaternary) sintering aids, and the melting temperatures of these sintering aids under different firing atmospheres after firing at 850°C for 2 h. Compound ● denotes that the quadruple-perovskite-type Cu–Ti–Nb–O-based or Ag–Cu–Ti–Nb–O-based complex oxides were produced during the heat treatment; No-compound ● denotes that these compounds were not produced.
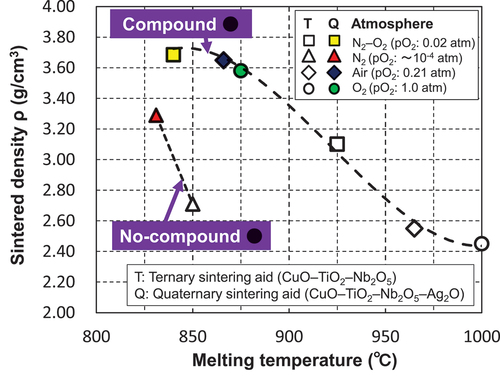
3.3. Effect of firing atmosphere on the dielectric properties of LTCA
Notably, the pO2 during firing also affects the dielectric properties of the LTCA. shows the sintered densities, dielectric properties, and thermal conductivities of the samples prepared under different firing atmospheres, firing temperatures, and retention times. The dielectric properties of the samples fired for 2 h at 900°C in the O2 atmosphere (pO2 = 1.0 atm, K01) and air (pO2 = 0.21 atm, K02) were extremely poor, and the dielectric measurements were impossible, although the relative density of the sample was approximately equal to or more than 90%. For reference, the dielectric properties of the sample that was fired for 24 h at 850°C in air (K06) were as follows: εr = 10.4, Q × f = 3510 GHz (measurement frequency of approximately 12 GHz), and τf = – 64 ppm/K. In addition, according to our previous study [Citation28], it has been reported that the dielectric property of the sample fired for 24 h at 900°C in an air atmosphere using the same kind of raw material powder and composition as in this study was low and could not be measured. In contrast, the dielectric properties of the sample fired for 2 h at 900°C and a pO2 controlled to 0.02 atm (K03) were measurable, yielding εr = 10.8, Q × f = 3830 GHz, and τf = – 52 ppm/K, which were also equal to or higher than those of K06 described above. The thermal conductivity of the sample was 17 W/mK, which is higher than those of conventional LTCC materials. The dielectric properties of the sample fired at 850°C for 24 h in the N2–O2 atmosphere (pO2 = 0.02 atm, K07) were εr = 10.7, Q × f = 4150 GHz, and τf = – 64 ppm/K. Furthermore, the dielectric properties of the sample (K04) fired for 2 h at 900°C in the N2 atmosphere were extremely poor and unmeasurable. Because the dielectric properties of the sample (K08) fired at 900°C for 24 h in the same N2 atmosphere can be measured, it was considered that the difference between these two samples lies in the sinterability. Therefore, lowering the pO2, within the range in which sinterability can be ensured, can yield higher Q X f and f values; in particular, the value of τf can be remarkably enhanced.
Table 1. Firing conditions, sintered densities, dielectric properties (εr, Q × f, and τf), and thermal conductivities of alumina containing 5 wt.% of the CuO–TiO2–Nb2O5–Ag2O sintering aid. The cross marks (“×”) denote that the dielectric measurements of the samples could not be performed owing to the significantly low values of the properties.
From the XRD patterns of the sintered bodies (), the dielectric properties are considered to be related to the disappearance of the AgNbO3 phase owing to the decrease in the pO2. This is because AgNbO3 has a Q value (measured at 1 MHz) less than 1000, and a temperature coefficient of dielectric constant (τε) of approximately 5000 ppm/K (or τf ~ −2500 ppm/K) [Citation29,Citation30]. A similar relationship between the disappearance of AgNbO3 and τf has been confirmed in the low-temperature sintered Al2O3–TiO2 [Citation28]. However, Ag is also precipitated when the pO2 decreases, as shown in , and the verification of insulation reliability will be necessary for future studies.
Figure 10. XRD patterns of the alumina containing 5 wt.% of the CuO–TiO2–Nb2O5–Ag2O sintering aids fired at 900°C for 2 h under different firing atmospheres.
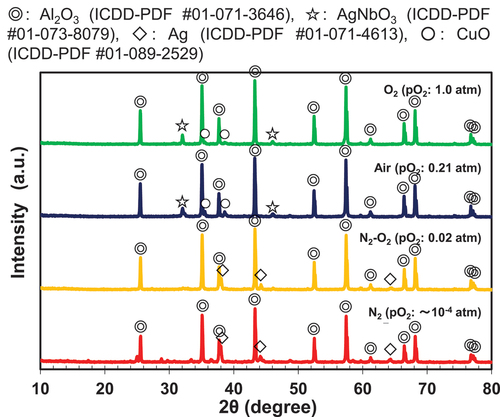
Thus, it was observed that by controlling the pO2, even with the same composition of LTCA, both the sinterability and precipitation phase can be modified to enhance the dielectric properties of LTCA; this results in the shortening of the firing time.
4. Conclusions
In this study, we focused on the firing atmosphere to promote low-temperature sintering and enhance the dielectric properties of LTCA containing 5 wt.% of the CuO–TiO2–Nb2O5–Ag2O sintering aid. From the results, we conclude the following:
(1) The sintered body density is maximized at pO2 < 0.21 atm, which is the pO2 of atmospheric air. Thus, the sinterability is enhanced by shortening the firing time.
(2) To improve sinterability, the formation of the Ag–Cu–Ti–Nb–O-based complex oxide and lowering of the melting temperature of the sintering aid are necessary.
(3) A dense sintered body was obtained with a relative density of approximately 95% for the sample fired for 2 h at a pO2 of 0.02 atm and a firing temperature of 900°C. The dielectric and thermal properties of the LTCA significantly improved and were observed to be better than those of conventional LTCC materials.
(4) By controlling the pO2 such that the Ag–Cu–Ti–Nb–O-based complex oxide remains and AgNbO3 disappears, the dielectric properties, particularly Q × f and τf, can be enhanced.
For practical use, τf must be reduced to zero while ensuring sinterability. Further improvements in the Q × f value is also desirable for applications in the millimeter-wave region.
Acknowledgments
We would like to thank Prof. Hirotaka Ogawa, Prof. Akinori Kan, and Dr. Susumu Takahashi of Meijo University for their help with the dielectric property experiments.
Disclosure statement
No potential conflict of interest was reported by the author(s).
Additional information
Funding
References
- Yeh TS, Sacks MD. Low-temperature sintering of aluminum oxide. J Am Ceram Soc. 1988;71(10):841–844.
- Alford NM, Penn SJ. Sintered alumina with low dielectric loss. J Appl Phys. 1996;80(10):5895–5898.
- Krell A, Blank P, and Ma H, et al. Processing of high-density submicrometer Al2O3 for new applications. J Am Ceram Soc. 2003;86(4):546–553.
- Huang CL, Wang JJ, and Huang CY. Microwave dielectric properties of sintered alumina using nano-scaled powders of ? Alumina and TiO2. J Am Ceram Soc. 2007;90(5):1487–1493.
- Li H, Xi X, Ma J, et al. Shui, Low-temperature sintering of coarse alumina powder compact with sufficient mechanical strength. Ceram Int. 2017;43(6):5108–5114.
- Nishigaki S, Fukuta J. Low-temperature, cofireable, multilayered ceramics bearing pure-Ag conductors and their sintering behavior. Adv Ceram. 1989;26:199–215.
- Kagata H, Saito R, Katsumura H. Al2O3-MgO-ReOx (Re: rare earth)-based LTCC and its application to multilayer non-shrinkage substrate for microwave devices. J Electroceram. 2004;13(1–3):277–280.
- Sebastian MT, Jantunen H. Low loss dielectric materials for LTCC applications: a review. Int Mater Rev. 2008;53(2):57–90.
- Induja IJ, Abhilash P, Arun S, et al. LTCC tapes based on Al2O3–BBSZ glass with improved thermal conductivity. Ceram Int. 2015;41(10):13572–13581.
- Bilaç O, and Duran C. Al2O3/glass/hBN composites with high thermal conductivity and low dielectric constant for low temperature cofired ceramic applications. J Asian Ceram Soc. 2021;9(1):283–290.
- Cutler IB, Bradshaw C, Christensen CJ, et al. Sintering of alumina at temperatures of 1400 °C and below. J Am Ceram Soc. 1957;40:134–139.
- Xue LA, Chen IW. Low-temperature sintering of alumina with liquid-forming additives. J Am Ceram Soc. 1991;74(8):2011–2013.
- Moreira MC, Segadães AM. Phase equilibrium relationships in the system Al2O3-TiO2-MnO, relevant to the low-temperature sintering of alumina. J Eur Ceram Soc. 1996;16(10):1089–1098.
- Zhang QL, Yang H, Zou JL, et al. Sintering and dielectric properties of Al2O3 ceramics doped by TiO2 and CuO. J Electroceram. 2007;18(3–4):225–229.
- Fu Y, Shen P, Hu Z, et al. The role of CuO–TiO2 additives in the preparation of high-strength porous alumina scaffolds using directional freeze casting. J Porous Mater. 2016;23(2):539–547.
- Dong G, Li W. Microwave dielectric properties of Al2O3 ceramics sintered at low temperature. Ceram Int. 2021;47(14):19955–19958.
- Shigeno K, Katsumura H, Kagata H, et al. Low temperature sintering of alumina by CuO–TiO2–Nb2O5 additives. Key Eng Mater. 2006;320:181–184.
- Shigeno K, Kojima E, and Fujimori H. Improvement in the low-temperature sintering performance and characteristics of alumina with CuO-TiO2-Nb2O5 additive by controlling the firing atmosphere. J Jpn Soc. Powder Metall 2016;63(7):701–705.
- Liu HH, and Jean JH. Processing and properties of a low-fire, high-thermal-conductivity alumina with CuTiNb2O8. Int J Ceram Eng Sci. 2020;2(1):38–45.
- Yang Y, Ma M, Zhang F, et al. Low-temperature sintering of Al2O3 ceramics doped with 4CuO–TiO2–2Nb2O5 composite oxide sintering aid. J Eur Ceram Soc. 2020;40(15):5504–5510.
- Shigeno K, Katsumura H, and Kagata H, et al. Preparation and characterization of low temperature sintered alumina by CuO-TiO2-Nb2O5-Ag2O additives. Ferroelectrics. 2007;356(1):189–196.
- Shigeno K, Asakawa T, Kuraoka Y, et al. Effects of chemical compositions on electrical properties of low temperature co-fired alumina ceramics with built-in silver electrodes. Trans Mater Res Soc Jpn. 2016;41(1):121–126.
- Shigeno K, Kuraoka Y, Asakawa T, et al. Sintering mechanism of low-temperature co-fired alumina featuring superior thermal conductivity. J Am Ceram Soc. 2021;104(5):2017–2029.
- Ohsato H, Varghese J, Vahera T, et al. Micro/millimeter-wave dielectric indialite/cordierite glass-ceramics applied as LTCC and direct casting substrates: current status and prospects. J Korean Ceram Soc. 2019;56(6):526–533.
- Coble RL. Sintering alumina: effect of atmospheres. J Am Ceram Soc. 1962;45(3):123–127.
- Hakki BW, Coleman PD. A dielectric resonator method of measuring inductive capacities in the millimeter range. IEEE Trans Microwave Theory Tech. 1960;8(4):402–410.
- Reeves-McLaren NR, Ferrarelli MC, Tung YW, et al. Synthesis, structure and electrical properties of Cu3.21Ti1.16Nb2.63O12 and the CuOx–TiO2–Nb2O5 pseudoternary phase diagram. J Solid State Chem. 2011;184(7):1813–1819.
- Shigeno K, Li M, Fujimori H. Development of novel temperature-stable Al2O3−TiO2-based dielectric ceramics featuring superior thermal conductivity for LTCC applications. J Eur Ceram Soc. 2021;41(1):376–386.
- Valant M, Axelsson A, Alford N. Review of Ag(Nb, Ta)O3 as a functional material. J Eur Ceram Soc. 2007;27(7):2549–2560.
- Khan HU, Alam K, Mateenullah M, et al. Synthesis and characterization of solid solution Ag(NbxTa1−x)O3 (x = 0, 0.25, 0.5, 0.75, 1.0). J Eur Ceram Soc. 2015;35(10):2775–2789.