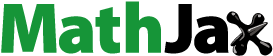
Abstract
This paper presents the performance of teaching–learning-based optimization (TLBO) algorithm to obtain the optimum set of design and operating parameters for a smooth flat plate solar air heater (SFPSAH). The TLBO algorithm is a recently proposed population-based algorithm, which simulates the teaching–learning process of the classroom. Maximization of thermal efficiency is considered as an objective function for the thermal performance of SFPSAH. The number of glass plates, irradiance, and the Reynolds number are considered as the design parameters and wind velocity, tilt angle, ambient temperature, and emissivity of the plate are considered as the operating parameters to obtain the thermal performance of the SFPSAH using the TLBO algorithm. The computational results have shown that the TLBO algorithm is better or competitive to other optimization algorithms recently reported in the literature for the considered problem.
Public Interest Statement
Solar air heater is extensively used nowadays in various applications like space heating, seasoning of timber, curing of industrial products, etc. It consists of an absorbed plate with parallel plate below forming a small passage through which air is to be heated and flow. But the main drawback of solar air heater is low thermal efficiency, since the heat transfer coefficient is less between the absorber plate and air. Sometimes surfaces are roughed or longitudinal fines are used or geometrical parameters are changed to increase the thermal efficiency. In the present work, optimal set of operating parameters are investigated using the teaching–learning-based optimization algorithm, at which the thermal performance of a smooth flat plate solar air heater could be maximum. The computational results have shown that the TLBO algorithm is better or competitive to other optimization algorithms recently reported in the literature for the considered problem.
1. Introduction
Solar air heating is a solar thermal technology, in which the energy from sun is captured by an absorbing medium and used to heat air. Solar air heating is extensively used nowadays in commercial and industrial applications. Solar air heaters are simple in design and construction, but efficiency of flat plate solar air heater is low because of low convective heat transfer coefficient between the absorber plate and the flowing air that increases absorber plate temperature, leading to higher heat losses to environment. Low value of heat transfer coefficient is due to presence of laminar sublayer that can be broken by providing artificial roughness on heat transferring surface.
The use of flat-plate solar collectors to heat air to relatively low temperature has become a common practice in numerous applications from space heating to food dehydration industry (Hegazy, Citation1996). Hegazy (Citation1996) optimized the flow channel depth for a conventional flat-plate solar air heater. The author had derived an expression for estimating the channel depth-to-length ratio that yields an outlet air temperature equal to the absorber plate mean temperature in terms of flow pumping power. This expression is of great importance for designers of this type of solar air heater. A parametric study was also carried out to investigate the effect of the channel depth on collector useful heat gain of collector over a wide range of D/L (depth of flow channel/length of absorber plate) ratios, and for different pumping power requirements.
Gupta, Solanki, and Saini (Citation1997) explained that the systems operating in a specified range of Reynolds number show better thermohydraulic performance depending upon the insulation. Ammari (Citation2003) presented a mathematical model for computing the thermal performance of a single-pass flat-plate solar air collector. The author had investigated the influence of the addition of the metal slats on the efficiency of solar collector with the help of the model developed. The effect of volume air flow rate, collector length, and spacing between the absorber and bottom plates on the thermal performance of the solar air heater was investigated.
Mittal and Varshney (Citation2006) investigated thermohydraulic performance of a wire mesh-packed solar air heater having its duct packed with blackened wire screen matrices of different geometrical parameters (wire diameter and pitch). The authors had concluded that the Reynolds number was a strong parameter affecting the effective efficiency. Also, it was found that for higher values of the temperature rise, the effective efficiency values closely followed the thermal efficiency values, whereas there was an appreciable difference in the lower range of temperature rise values. The authors had also commented that merely the porosity of the bed does not govern the performance. Kalogirou (Citation2006) used artificial neural networks (ANN) for the prediction of the performance parameters of flat-plate solar collectors. Six ANN models were developed for the prediction of the standard performance of collectors.
Layek, Saini, and Solanki (Citation2007) optimized solar air heater having chamfered rib-groove roughness on absorber plate. The entropy generation in the duct of solar air heater having repeated transverse chamfered rib-groove roughness on one broad wall was studied numerically. The authors had concluded that the roughness parameters like relative roughness pitch, relative roughness height, relative groove position, chamfer angle, and flow Reynolds number had a combined effect on the heat transfer as well as fluid friction.
Improving the thermal performance by enhancing the heat transfer rate and reducing friction losses depends on the geometrical parameters of the solar air heater and hence, there is a need for optimization of design and operating parameters of the solar air heater. Varun and Siddhartha (Citation2010) used genetic algorithm to investigate the thermal performance optimization of a flat-plate solar air heater. The authors considered different systems and operating parameters to obtain maximum thermal performance. Thermal performance was obtained for different Reynolds numbers, emissivity of the plate, tilt angle, and number of glass plate by using genetic algorithm.
Varun, Sharma, Bhat, and Grover (Citation2011) implemented a stochastic iterative perturbation technique to obtain the optimum set of different system and operating parameters, such as the number of glass cover plate, emissivity of the plate, mean plate temperature, rise in temperature, tilt angle, and solar radiation intensity for different Reynolds numbers. El-Sebaii, Aboul-Enein, Ramadan, Shalaby, and Moharram (Citation2011) presented an analytical model for the air heater with flat and V-corrugated plates. The authors had investigated the thermal performance of double-pass flat- and V-corrugated-plate solar air heaters theoretically and experimentally. The effect of mass flow rate of air on pressure drop, thermal and thermohydraulic efficiencies of the flat- and V-corrugated-plate solar air heater were also investigated.
Lanjewar, Bhagoria, and Sarviya (Citation2011) presented experimental investigation of heat transfer and friction factor characteristics of a rectangular duct roughened with W-shaped ribs on its underside on one broad wall arranged at an inclination with respect to flow direction. The authors had compared the results of heat transfer and friction factor with those for a smooth duct under similar flow and thermal boundary conditions to determine the thermohydraulic performance. Correlations were also developed for heat transfer coefficient and friction factor for the roughened duct.
Tanda (Citation2011) discussed the performance of solar air heater ducts with different types of ribs on the absorber plate. All the rib-roughened channels performed better than the reference smooth channel in the medium–low range of the investigated Reynolds number values. Gill, Singh, and Singh (Citation2012) designed, fabricated, and tested two low-cost solar air heaters, i.e. single glazed and double glazed. The collector efficiency factor, heat-removal factor based on air outlet temperature, and air inlet temperature for solar air heaters were also determined.
There is an increasing interest among researchers in the design, development, and optimization of a smooth flat-plate solar air heater (SFPSAH) over past few decades. Siddhartha, Sharma, and Varun (Citation2012) used particle swarm optimization algorithm for optimization of thermal performance of SFPSAH. The authors had carried out simulation for three different cases using the climatic condition data of Hamirpur city of India to investigate the thermal performance of SFPSAH. Maximization of thermal efficiency was set as an objective function. Siddhartha, Chauhan, Varun, and Sharma (Citation2012) used simulated annealing algorithm to optimize the thermal performance of SFPSAH and predicted the optimum set of design and operating parameters.
Chamoli, Chauhan, Thakur, and Saini (Citation2012) presented an extensive study of the research carried out on double-pass solar air heater. Karwa and Chitoshiya (Citation2013) presented an experimental study of thermohydraulic performance of a solar air heater with 60° V-down discrete rib roughened on the airflow side of the absorber plate along with a smooth duct air heater. The authors claimed that the thermal efficiency was increased by 12.5–20% due to the roughness on the absorber plate depending on the airflow rate; higher enhancement was at the lower flow rate.
It has been observed that only few researches had attempted the optimization of flat-plate solar air heater by considering the different system and operating parameters to obtain maximum thermal performance (Varun & Siddhartha, Citation2010; Siddhartha, Chauhan, et al., Citation2012). Varun and Siddhartha (Citation2010) used GA, Siddhartha, Chauhan, et al. (Citation2012) used PSO and Siddhartha, Sharma, et al. (Citation2012) used simulated annealing (SA) for optimization of thermal performance of a SFPSAH. However, the parameter setting of the GA, PSO, and SA algorithms is a serious problem which influences their efficiency and affects the performance of the algorithms, for example, GA requires the crossover probability, mutation rate, and selection method; PSO requires learning factors, the variation of weight, and the maximum value of velocity; SA requires temperature decrement. Similarly, the other advanced optimization algorithms like artificial bee colony (ABC) requires number of employed bees, onlooker bees, and value of limit; harmony search (HS) requires the harmony memory consideration rate, pitch adjusting rate, and number of improvisations. Unlike other optimization techniques, a recently developed optimization technique, namely teaching–learning-based optimization (TLBO) algorithm does not require any algorithm parameters to be tuned, thus making the implementation of TLBO algorithm simpler. This algorithm requires only the common control parameters and does not require any algorithm-specific control parameters. In the literature, it is observed that the TLBO algorithm is not yet used in the field of optimization of a SFPSAH. Hence, in this paper, TLBO algorithm is used to estimate the optimal performance of a SFPSAH, with various effective parameters. The next section presents the details of the TLBO algorithm.
2. TLBO algorithm
TLBO is a teaching–learning process-inspired algorithm proposed by Rao, Savsani, and Vakharia (Citation2011a, Citation2011b) and Rao, Savsani, and Balic (Citation2011) based on the effect of influence of a teacher on the output of learners in a class. The algorithm describes two basic modes of the learning: (1) through teacher (known as teacher phase) and (2) interacting with the other learners (known as learner phase). In this optimization algorithm, a group of learners is considered as population and different subjects offered to the learners are considered as different design variables of the optimization problem, and a learner’s result is analogous to the “fitness” value of the optimization problem. The best solution in the entire population is considered as the teacher. The design variables are actually the parameters involved in the objective function of the given optimization problem and the best solution is the best value of the objective function. The working of TLBO is divided into two parts, “Teacher phase” and “Learner phase”. The flow chart of TLBO algorithm is shown in Figure . Working of both these phases is explained below.
Figure 1. The flow chart of TLBO algorithm (Rao et al., Citation2011a).
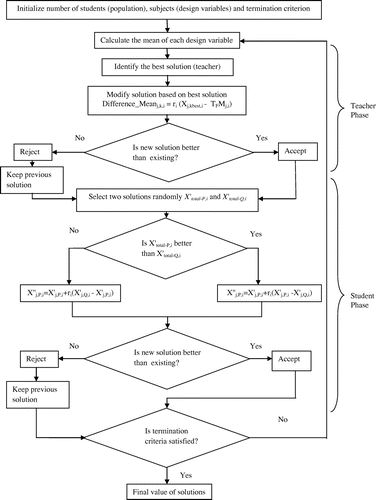
2.1. Teacher phase
It is the first part of the algorithm where learners learn through the teacher. During this phase, a teacher tries to increase the mean result of the class in the subject taught by him or her depending on his or her capability. At any iteration i, assume that there are “m” number of subjects (i.e. design variables), “n” number of learners (i.e. population size, k = 1, 2, … , n), and Mj, i be the mean result of the learners in a particular subject “j” (j = 1, 2, … ,m) The best overall result Xtotal-kbest, i considering all the subjects together obtained in the entire population of learners can be considered as the result of best learner kbest. However, as the teacher is usually considered as a highly learned person who trains learners, so that they can have better results, the best learner identified is considered by the algorithm as the teacher. The difference between the existing mean result of each subject and the corresponding result of the teacher for each subject is given by,(1)
(1)
where, Xj, kbest, i is the result of the best learner (i.e. teacher) in subject j. TF is the teaching factor. It is important to note here that after conducting a number of computational experiments on various benchmark functions (Rao & Waghmare, Citation2014), it was observed that the best value of objective function can be achieved when TF value is taken as 1. So, in the TLBO algorithm, the value of TF is considered as 1 and the term “TF” is removed in the TLBO algorithm. Hence, Equation 1 is rewritten as:(2)
(2)
Based on the Difference_Meanj, k, i, the existing solution is updated in the teacher phase according to the following expression.(3)
(3)
where is the updated value of Xj, k, i.
is accepted if it gives better function value. All the accepted function values at the end of the teacher phase are maintained and these values become the input to the learner phase. The learner phase depends upon the teacher phase.
2.2. Learner phase
It is the second part of the algorithm where learners increase their knowledge by interaction among themselves. A learner interacts randomly with other learners for enhancing his or her knowledge. A learner learns new things if the other learner has more knowledge than him or her. Considering a population size of “n”, the learning phenomenon of this phase is expressed below:
Randomly select two learners P and Q, such that (where
and
are the updated values of Xtotal-P, i and Xtotal-Q, i, respectively, at the end of teacher phase)
(4a)
(4a)
(4b)
(4b)
is accepted if it gives a better function value.
The TLBO algorithm has been already tested on several constrained and unconstrained benchmark functions and proved better than the other advanced optimization techniques (Rao & Patel, Citation2012, Citation2013; Rao & Waghmare, Citation2014) had evaluated the performance of the TLBO algorithm over a set of multi-objective unconstrained and constrained test functions and the results were compared against the other optimization algorithms. The TLBO algorithm was observed to outperform the other optimization algorithms for the multi-objective unconstrained and constrained benchmark problems.
Waghmare (Citation2013) presented the correct understanding about the TLBO algorithm in an objective manner and comments were made on the note of Črepinšek, Liu, and Mernik (Citation2012). Yu, Wang, and Wang (Citation2014) used improved TLBO for numerical and engineering optimization problems. The authors mentioned that the claim made by Črepinšek, Liu, and Mernik (Citation2014) that Waghmare (Citation2013) used different success rates was unsuitable. The comparisons of evolutionary algorithms conducted by Veček, Mernik, and Črepinšek (Citation2014) attempted to cast the TLBO algorithm in a poor light, although this attempt may also be seen as not meaningful. The findings were simply comparisons of the basic TLBO algorithm with different modified versions of DE and did not consider other important algorithms, such as the GA, SA, PSO, and ACO (Yu et al., Citation2014). It may be mentioned that various researchers like Niknam, Azizipanah-Abarghooee, and Rasoul Narimani (Citation2012), Rao, Kalyankar, and Waghmare (Citation2014), Baykasoğlu, Hamzadayi, and Köse (Citation2014), Satapathy and Naik (Citation2014), Medina, Das, and Coello (Citation2014), Basu (Citation2014), Zou, Wang, Hei, Chen, and Yang (Citation2014), Camp and Farshchin (Citation2014), Moghadam and Seifi (Citation2014) and Sultana and Roy (Citation2014) proved the better performance of the TLBO algorithm as compared to the other evolutionary algorithms. Hence, the TLBO algorithm is attempted in the present work for the optimization of thermal performance of SFPSAH.
3. Thermal performance of solar air heater
The thermal performance of SFPSAH is investigated using the TLBO algorithm based on heat transfer phenomena (ASHRAE Standards) and calculation of flat-plate collector loss coefficients (Klein, Citation1975).
Figure presents the zenith angle, angle of incidence, tilts angle, and azimuth angle for a tilted surface (Twidell & Weir, Citation2005). The angle between the sun direction and the normal direction of a tilted surface can be represented as:
Figure 2. Zenith angle, angle of incidence, tilts angle, and azimuth angle for a tilted surface (Twidell & Weir, Citation2005).
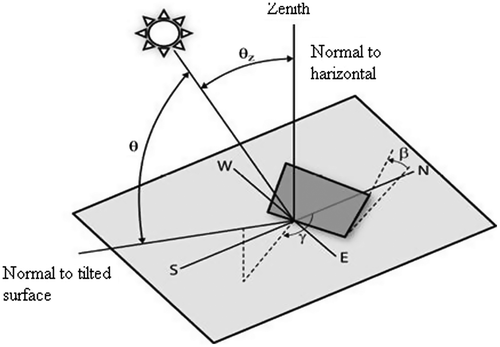
(5)
(5)
where θ is the angle of incidence, θz is the solar zenith, β is the tilt angle, γs is the azimuth angles, and γ is the azimuth angle for a tilted surface.
The design parameters are: number of glass cover plates, irradiance, and Reynolds number and the operating parameters are: wind velocity, plate tilt angle, emissivity of the plate, and ambient temperature. The thermal performance of a SFPASH can be predicted on the basis of detailed considerations of heat transfer processes and correlations for heat transfer coefficient, heat removal factor, etc. The objective function for thermal performance of SFPSAH can be proposed as given by ASHRAE Standards (Citation1997) and expressed by the following equation:(6)
(6)
The top loss coefficient is determined using relation (7) (Klein, Citation1975).
The different relations used for calculating overall loss coefficient (U0), heat removal factor at outlet (F0), and temperature rise (T0 − Ti) are computed using relation (7), (11) and (13), respectively.(7)
(7)
where(8)
(8)
(9)
(9)
(10)
(10)
Heat removal factor at outlet (F0) can be expressed as:(11)
(11)
where(12)
(12)
The temperature rise (T0 − Ti) is computed by the following equation.(13)
(13)
The constraints of the problem are:
1 ≤ N ≤ 3; N is varied in steps of 1.
600 ≤ S ≤ 1,000; S is varied in steps of 200.
2,000 ≤ Re ≤ 20,000; Re is varied in steps of 2,000.
The computations were carried out using TLBO algorithm for three different cases using the climatic condition data of the city of Hamirpur, India, situated between 31°25′–31°52′ N (latitude) and 76°18′–76°44′ E (longitude).
The other climatic conditions of the city of Hamirpur, India, are as follows:
where is the wind velocity (m/s) and Ta is ambient temperature.
The following three different cases are considered (Siddhartha, Chauhan, et al., Citation2012).
Case 1: Obtain the value of V and Ta through TLBO algorithm and generate єp (0.85–0.95) and β (0°–70°) randomly.
Case 2: Obtain the value of β and Ta through TLBO algorithm and generate єp (0.85–0.95) and v (1–3) randomly.
Case 3: Obtain the value of V and β through TLBO algorithm and generate єp (0.85–0.95) and Ta (280–310 K) randomly for a fixed value of N (1, 2 and 3) and fixed S (600, 800, and 1,000 W/m2) and varying Re ranging from 2,000 to 20,000 in an incremental step of 2,000. The next section explains the detailed results and discussion.
4. Results and discussion
To check the effectiveness of the TLBO algorithm, extensive computational trials are conducted on a flat-plate solar air heater and results are compared with those obtained by the other optimization algorithms. For the fair comparison of the TLBO algorithm, the same number of function evaluations are used (Siddhartha, Chauhan, et al., Citation2012). Population size 30 and maximum number of generations 50 are considered. Like other optimization algorithms (e.g. PSO, ABC, ACO, etc.), TLBO algorithm also does not have any special mechanism to handle the constraints. So, for the constrained optimization problems, it is necessary to incorporate any constraint handling techniques with the TLBO algorithm. In the present experiments, Deb’s heuristic constrained handling method (Deb, Citation2000) is used to handle the constraints with the TLBO algorithm. Deb’s method uses a tournament selection operator, in which two solutions are selected and compared with each other. The TLBO code is written in MATLAB and implemented on a laptop having Intel core i3 2.53 GHz processor with 1.85 GB RAM.
Table presents the typical parameter values of solar air heater system (Siddhartha, Sharma, et al., Citation2012). Table shows the optimum results of thermal performance obtained using the TLBO algorithm and comparison is made with those obtained by the PSO algorithm at N = 3 and S = 600 W/m2. The optimum results of thermal performance is also found at different values of N and S, but for the comparison purpose, it is reported at N = 3 and S = 600 since the results for another settings are not available in Siddhartha, Chauhan, et al. (Citation2012). From Table , it can be seen that the thermal efficiency is improved by 5.54% for case 1, 5.39% for case 2, and 5.44% for case 3 using the TLBO algorithm. The optimal thermal performance corresponding to the optimized set of values of velocity (v), tilt angle (β), emissivity of plate (єp), and ambient temperature (Ta) is determined using the TLBO algorithm as provided in Table .
Table 1. Typical values of solar air heater system parameters (Siddhartha, Chauhan, et al., Citation2012)
Table 2. Set of optimal results at N = 3 and S = 600 W/m2
Table presents the range of thermal performance variation for different number of glass cover plates. In total, three sets of glass plates have been considered. Three cases are considered to evaluate the thermal performance of solar air heater using the TLBO algorithm and the results are compared with the PSO algorithm. From Table , it can be seen that the thermal efficiency increases as the number of glass cover plate increases. For case 1, the maximum thermal efficiency is obtained at S = 600 and Re = 20,000 and is improved by 8.70, 7.36, and 5.54% for N = 1, 2, and 3, respectively, using the TLBO algorithm. For case 2, the maximum thermal efficiency is obtained at S = 600 and Re = 20,000 and is improved by 8.89, 7.35, and 5.22% for N = 1, 2, and 3, respectively, using the TLBO algorithm. For case 3, the maximum thermal efficiency is obtained at S = 600 and Re = 20,000 and is improved by 8.88, 7.21, and 5.21% for N = 1, 2, and 3, respectively, using TLBO algorithm.
Table 3. Range of thermal performance variation for different number of glass cover plates
Table presents a set of optimum results of thermal performance of solar air heater at different Reynolds numbers for N = 1 and S = 600 W/m2 using the TLBO algorithm and the results are compared with those obtained by GA, PSO, and SA algorithms. The thermal performance in terms of thermal efficiency and different operating parameters for different Reynolds number varying from 2,000 to 20,000 with incremental step of 2,000 are estimated and included in Table . In Table , the symbol “–” indicates that the results are not available in the cited reference. From Table , it can be seen that the thermal efficiency of solar air heater obtained using the TLBO algorithm is better than that obtained using other optimization algorithms by the previous researchers.
Table 4. Set of optimum results at different Reynolds numbers (N = 1 and S = 600 W/m2)
Table presents the set of optimum results at different Reynolds numbers, N = 2 and S = 600 W/m2. It can be seen that the maximum thermal efficiency of 74.5783% is obtained using the TLBO algorithm at Reynolds number of 20,000, with v = 1.8635 m/s, Ta = 304.6286 K, β = 6.3283°, and єp = 0.8738. The set of optimum results at different Reynolds numbers, N = 3 and S = 600 W/m2 are shown in Table . The maximum thermal efficiency obtained using TLBO algorithm is 76.6739%. It can be observed that for the same settings, the thermal performance of a SFPSAH obtained by the TLBO algorithm is better as compared to the other algorithms.
Table 5. Set of optimum results at different Reynolds numbers (N = 2 and S = 600 W/m2)
Table 6. Set of optimum results at different Reynolds numbers (N = 3 and S = 600 W/m2)
Table presents the set of optimum results at different Reynolds numbers, N = 1 and S = 800 W/m2. It can be seen that the maximum thermal efficiency of 69.8921% is obtained using the TLBO algorithm at Reynolds number of 20,000, with v = 2.3732 m/s, Ta = 305.8392 K, β = 43.4174°, and єp = 0.9146. The set of optimum results at different Reynolds numbers, N = 2 and S = 800 W/m2 is shown in Table . The maximum thermal efficiency obtained using TLBO algorithm is 74.4992%. It can be observed that for the same settings, the thermal performance of a SFPSAH obtained by the TLBO algorithm is better as compared to the other algorithms.
Table 7. Set of optimum results at different Reynolds numbers (N = 1 and S = 800 W/m2)
Table 8. Set of optimum results at different Reynolds numbers (N = 2 and S = 800 W/m2)
A set of optimum results at different Reynolds numbers, N = 3 and S = 800 W/m2 is shown in Table . The maximum thermal efficiency obtained using the TLBO algorithm is 76.5913%. It can be observed that for the same settings, the thermal performance of a SFPSAH is better for the TLBO algorithm as compared to that obtained by the other algorithms. Table presents the set of optimum results at different Reynolds numbers, N = 1 and S = 1,000 W/m2. It can be seen that the maximum thermal efficiency of 69.1102% is obtained using the TLBO algorithm at Reynolds number of 20,000 with v = 2.1194 m/s, Ta = 296.9633 K, β = 36.6728°, and єp = 0.9043.
Table 9. Set of optimum results at different Reynolds numbers (N = 3 and S = 800 W/m2)
Table 10. Set of optimum results at different Reynolds numbers (N = 1 and S = 1,000 W/m2)
Table presents the set of optimum results at different Reynolds numbers, N = 2 and S = 1,000 W/m2. It can be seen that the maximum thermal efficiency of 74.2392% is obtained using the TLBO algorithm at Reynolds number of 20,000, with v = 2.3991 m/s, Ta = 298.7654 K, β = 18.3877°, and єp = 0.9257. The set of optimum results at different Reynolds numbers, N = 3 and S = 1,000 W/m2 is shown in Table . The maximum thermal efficiency obtained using TLBO algorithm is 76.4188%. It can be observed that for the same settings, the thermal performance of a SFPSAH obtained by the TLBO algorithm is better as compared to the other algorithms.
Table 11. Set of optimum results at different Reynolds numbers (N = 2 and S = 1,000 W/m2)
Table 12. Set of optimum results at different Reynolds numbers (N = 3 and S = 1,000 W/m2)
Set of optimum results at different Reynolds numbers, N = 1 and S = 1200 W/m2 is shown in Table . The maximum thermal efficiency obtained using TLBO algorithm is 69.06378%. It can be observed that for the same settings, the thermal performance of a SFPSAH is better for the TLBO algorithm as compared to other algorithms. Table presents the set of optimum results at different Reynolds numbers, N = 2 and S = 1200 W/m2. It can be seen that the maximum thermal efficiency of 74.1743% is obtained using the TLBO algorithm at Reynolds number 20,000, with v = 1.8973 m/s, Ta = 290.3753 K, β = 16.4672°, and єp = 0.8623. A set of optimum results at different Reynolds numbers, N = 3 and S = 1200 W/m2 is shown in Table . The maximum thermal efficiency obtained using TLBO algorithm is 76.0374%. It can be observed that for the same settings, the thermal performance of a SFPSAH obtained by the TLBO algorithm is better as compared to the other algorithms.
Table 13. Set of optimum results at different Reynolds numbers (N = 1 and S = 1,200 W/m2)
Table 14. Set of optimum results at different Reynolds numbers (N = 2 and S = 1,200 W/m2)
Table 15. Set of optimum results at different Reynolds numbers (N = 3 and S = 1,200 W/m2)
In Tables –, the symbol “–” indicates that the results are not available in the cited reference. From Tables –, it can be seen that TLBO algorithm performed better than the other optimization algorithms considered by the previous researchers.
4.1. Effect of Reynolds number on thermal performance
In this section, the effect of Reynolds number on thermal performance of SFPSAH is analyzed with respect to the design and operating parameters. Figure presents variation of thermal performance for different Reynolds number (Re) using TLBO algorithm. Figure shows the comparison of different algorithms with Reynolds number. Figure shows variation of thermal performance for different number of glass plates at S = 600 W/m2 (using TLBO algorithm). The thermal performance of a flat-plate solar air heater increases with the increase in Reynolds number as seen in Figures –. The thermal efficiency ranges from 31.7385 to 69.9757 with an increasing Reynolds number varying from 2,000 to 20,000 with single glass cover and irradiance of 600 W/m2 as shown in Table . Similarly, the performance range is 38.1378–74.5783 and 43.3532–76.6739 for the same range of Reynolds number and irradiance having two and three glass covers, respectively. The maximum value of thermal efficiency is 76.67% and it is obtained with three glass cover plates and irradiance of 600 W/m2 at Reynolds number of 20,000. The maximum value of efficiency is obtained at V = 1.2729 m/s, tilt angle = 59.5832°, emissivity of plate = 0.8835, ambient temperature = 293.9362 K, and temperature rise = 2.1395 K. Hence, it can be concluded from Tables – that the thermal performance of a flat-plate solar air heater increases with increase in Reynolds number.
4.2. Effect of number of glass plates on thermal performance
From Figure and Tables –, it can be seen that as the number of glass plates of solar air heater increases, the thermal efficiency of the solar air heater increases. The thermal performance of the solar air heater is investigated for different sets of glass plates varying from 1 to 3. The range of thermal performance for single glass cover varies from 28.3282% for I = 1200 W/m2 and Re = 2,000 to 69.9757% for I = 600 W/m2 and Re = 20,000. Similarly, for two glass covers, the thermal performance varies from 35.4562% for I = 1200 W/m2 and Re = 2,000 to 74.7183% for I = 600 W/m2 and Re = 20,000, and for three glass covers, the thermal performance varies from 40.2748% for I = 1200 W/m2 and Re = 2,000 to 76.6739% for I = 600 W/m2 and Re = 20,000.
4.3. Effect of solar radiation intensity on thermal performance
Figure shows the effect of solar radiation intensity on thermal performance for N = 1. The maximum thermal performance is 76.6739, 76.5913, 76.4188, and 76.0374% for irradiance of 600 W/m2, 800 W/m2, 1,000 W/m2, and 1200 W/m2, respectively. Hence, it can be concluded that as the irradiance increases, the thermal performance slightly decreases as can be seen from Figure and Tables –.
5. Conclusions
In the present work, a recently developed optimization algorithm known as TLBO algorithm is used for investigating the thermal performance of a SFPSAH. Maximization of thermal efficiency of SFPSAH is considered as the objective function. The thermal performance is obtained for different Reynolds numbers, irradiance, and number of glass plates. The maximum value of thermal efficiency of 76.67% is obtained with wind velocity of 1.2729 m/s, tilt angle of 59.5832°, plate emissivity of 0.8835, ambient temperature of 3.9362 K, temperature rise of 2.1395 K, irradiance of 600, and Reynolds number of 20,000. The final results obtained by the TLBO algorithm are compared with other optimization algorithms like GA, PSO, and SA and found to be satisfactory. The results also show that the thermal performance increases with the Reynolds number and the number of glass cover plates, but slightly decreases with the increase in irradiance. The TLBO algorithm is an effective algorithm and has potential for finding the optimal set of design and operating parameters at which the thermal performance of a SFPSAH is maximum. The TLBO algorithm may be tried on more complex problems in the near future.
Nomenclature | ||
Ac | = | area of absorber plate (m2) |
cp | = | specific heat of air (J/kg K) |
d | = | hydraulic diameter of duct (m) |
F0 | = | heat removal factor referred to outlet temperature (dimensionless) |
G | = | mass velocity (kg/sm2) |
h | = | convective heat transfer coefficient (W/m2K) |
hw | = | wind convection coefficient (W/m2K) |
S | = | irradiance (W/m2) |
k | = | index of iteration |
k′ | = | construction factor |
kmax | = | maximum number of observations |
= | mass flow rate of air (kg/s) | |
N | = | number of glass covers (dimensionless) |
pk | = | position of kth iteration |
pr | = | Prandtl number (dimensionless) |
Re | = | Reynolds number (dimensionless) |
t | = | thickness of insulating material (m) |
Ta | = | ambient temperature of air (K) |
Ti | = | inlet temperature of air (K) |
T0 | = | outlet temperature of air (K) |
Tp | = | temperature of absorber plate (K) |
U0 | = | overall loss coefficient (W/m2K) |
Ut | = | top loss coefficient (W/m2K) |
v | = | wind velocity (m/s) |
xi | = | experimental value at ith iteration |
yi | = | simulated value at ith iteration |
Greek symbols | ||
(τα) | = | transmittance–absorptance product (dimensionless) |
λ | = | thermal conductivity of air (W/mK) |
λi | = | thermal conductivity of insulating material (W/mK) |
ηth | = | thermal efficiency (dimensionless) |
єp | = | emissivity of plate (dimensionless) |
єg | = | emissivity of glass cover (dimensionless) |
β | = | tilt angle (°) |
Cover image
Source: Author.
Additional information
Funding
Notes on contributors
R. Venkata Rao
R. Venkata Rao is a professor in the Department of Mechanical Engineering of S.V. National Institute of Technology, Surat, Gujarat (India). He received his BTech degree from Nagarjuna University, his M.Tech degree from BHU, Varanasi, and his PhD degree from BITS, Pilani, India. He has about 23 years of teaching and research experience. He has authored about 260 research papers published in various reputed international journals and conference proceedings. He is also on the editorial boards of various international journals. His research interests include: advanced engineering optimization techniques and the applications, fuzzy multiple attribute decision-making, advanced manufacturing technology, automation and robotics.
References
- Ammari, H. D. (2003). A mathematical model of thermal performance of a solar air heater with slats. Renewable Energy, 28, 1597–1615.10.1016/S0960-1481(02)00253-7
- ASHRAE Standards. (1997). Methods of testing to determine the thermal performance of solar collectors. New York, NY: Author, 93–77.
- Basu, M. (2014). Teaching–learning-based optimization algorithm for multi-area economic dispatch. Energy. Retrieved from http://dx.doi.org/10.1016/j.energy.2014
- Baykasoğlu, A., Hamzadayi, A., & Köse, S. Y. (2014). Testing the performance of teaching–learning based optimization (TLBO) algorithm on combinatorial problems: Flow shop and job shop scheduling cases. Information Sciences. Retrieved from http://dx.doi.org/10.1016/j.ins.2014.02.056
- Camp, C. V., & Farshchin, M. (2014). Design of space trusses using modified teaching–learning-based optimization. Engineering Structures, 62–63, 87–97.10.1016/j.engstruct.2014.01.020
- Chamoli, S., Chauhan, R., Thakur, N. S., & Saini, J. S. (2012). A review of the performance of double pass solar air heater. Renewable and Sustainable Energy Reviews, 16, 481–492.10.1016/j.rser.2011.08.012
- Črepinšek, M., Liu, S.-H., & Mernik, L. (2012). A note on teaching–learning-based optimization algorithm. Information Sciences, 212, 79–93.
- Črepinšek, M., Liu, S.-H., & Mernik, M. (2014). Replication and comparison of computational experiments in applied evolutionary computing: Common pitfalls and guidelines to avoid them. Applied Soft Computing, 19, 161–170.
- Deb, K. (2000). An efficient constraint handling method for genetic algorithms. Computer Methods in Applied Mechanics and Engineering, 186, 311–338.10.1016/S0045-7825(99)00389-8
- El-Sebaii, A. A., Aboul-Enein, S., Ramadan, M. R. I., Shalaby, S. M., & Moharram, B. M. (2011). Investigation of thermal performance of-double pass-flat and v-corrugated plate solar air heaters. Energy, 36, 1076–1086.10.1016/j.energy.2010.11.042
- Gill, R. S., Singh, S., & Singh, P. (2012). Low cost solar air heater. Energy Conversion and Management, 57, 131–142.10.1016/j.enconman.2011.12.019
- Gupta, D., Solanki, S. C., & Saini, J. S. (1997). Thermohydraulic performance of solar air heaters with roughened absorber plates. Solar Energy, 61, 33–42.10.1016/S0038-092X(97)00005-4
- Hegazy, A. A. (1996). Optimization of flow-channel depth for conventional flat plate solar air heaters. Renewable Energy, 7, 15–21.10.1016/0960-1481(95)00117-4
- Kalogirou, S. A. (2006). Prediction of flat-plate collector performance parameters using artificial neural networks. Solar Energy, 80, 248–259.10.1016/j.solener.2005.03.003
- Karwa, R., & Chitoshiya, G. (2013). Performance study of solar air heater having v-down discrete ribs on absorber plate. Energy, 55, 939–955.10.1016/j.energy.2013.03.068
- Klein, S. A. (1975). Calculation of flat plate collector loss coefficients. Solar Energy, 17, 79–80.10.1016/0038-092X(75)90020-1
- Lanjewar, A., Bhagoria, J. L., & Sarviya, R. M. (2011). Heat transfer and friction in solar air heater duct with W-shaped rib roughness on absorber plate. Energy, 36, 4531–4541.10.1016/j.energy.2011.03.054
- Layek, A., Saini, J. S., & Solanki, S. C. (2007). Second law optimization of a solar air heater having chamfered rib-groove roughness on absorber plate. Renewable Energy, 32, 1967–1980.10.1016/j.renene.2006.11.005
- Medina, M. A., Das, S., Coello Coello, C. A., & Ramírez, J. M. (2014). Decomposition-based modern metaheuristic algorithms for multi-objective optimal power flow—A comparative study. Engineering Applications of Artificial Intelligence, 32, 10–20.10.1016/j.engappai.2014.01.016
- Mittal, M. K., & Varshney, L. (2006). Optimal thermohydraulic performance of a wire mesh packed solar air heater. Solar Energy, 80, 1112–1120.10.1016/j.solener.2005.10.004
- Moghadam, A., & Seifi, A. R. (2014). Fuzzy-TLBO optimal reactive power control variables planning for energy loss minimization. Energy Conversion and Management, 77, 208–215.10.1016/j.enconman.2013.09.036
- Niknam, T., Azizipanah-Abarghooee, R., & Rasoul Narimani, M. (2012). A new multi objective optimization approach based on TLBO for location of automatic voltage regulators in distribution systems. Engineering Applications of Artificial Intelligence, 25, 1577–1588.10.1016/j.engappai.2012.07.004
- Rao, R. V., Kalyankar, V. D., & Waghmare, G. (2014). Parameters optimization of selected casting processes using teaching–learning based optimization algorithm. Applied Mathematical Modelling, 38, 5592–5608.10.1016/j.apm.2014.04.036
- Rao, R. V., & Patel, V. (2012). An elitist teaching–learning-based optimization algorithm for solving complex constrained optimization problems. International Journal of Industrial Engineering Computations, 3, 535–560.10.5267/j.ijiec
- Rao, R. V., & Patel, V. (2013). Comparative performance of an elitist teaching–learning-based optimization algorithm for solving unconstrained optimization problems. International Journal of Industrial Engineering Computations, 4, 29–50.10.5267/j.ijiec
- Rao, R. V., Savsani, V. J., & Balic, J. (2011). ‘Teaching–learning-based optimization algorithm for unconstrained and constrained real parameter optimization problems. Engineering Optimization, 44, 1447–1462.
- Rao, R. V., Savsani, V. J., & Vakharia, D. P. (2011a). Teaching–learning-based optimization: A novel method for constrained mechanical design optimization problems. Computer Aided Design, 43, 303–315.10.1016/j.cad.2010.12.015
- Rao, R. V., Savsani, V. J., & Vakharia, D. P. (2011b). ‘Teaching–learning-based optimization: A novel optimization method for continuous non-linear large scale problems. Information Sciences, 183(1), 1–15.
- Rao, R. V., & Waghmare, G. G. (2014). A comparative study of a teaching–learning-based optimization algorithm on multiobjective unconstrained and constrained functions. Journal of King Saud University – Computer and Information Sciences, 26, 332–346.
- Satapathy, S. C., & Naik, A. (2014). Modified teaching–learning-based optimization algorithm for global numerical optimization—A comparative study. Swarm and Evolutionary Computation, 16, 28–37.10.1016/j.swevo.2013.12.005
- Siddhartha, S., Chauhan, S. R., Varun, V., & Sharma, N. (2012). Thermal performance optimization of smooth flat plate solar air heater (SFPSAH) using simulated annealing: Evaluation and comparisons. IEEE, Copyright Notice: 978-1-4673-6008-1/11
- Siddhartha, Sharma, N., & Varun (2012). A particle swarm optimization algorithm for optimization of thermal performance of a smooth flat plate solar air heater. Energy, 38, 406–413.10.1016/j.energy.2011.11.026
- Sultana, S., & Roy, P. K. (2014). Optimal capacitor placement in radial distribution systems using teaching learning based optimization. International Journal of Electrical Power & Energy Systems, 54, 387–398.
- Tanda, G. (2011). Performance of solar air heater ducts with different types of ribs on the absorber plate. Energy, 36, 6651–6660.10.1016/j.energy.2011.08.043
- Twidell, J., & Weir, T. (2005). Renewable energy resources (2nd ed.). Taylor & Francis.
- Varun, Sharma, N., Bhat, I. K., & Grover, D. (2011). Optimization of a smooth flat plate solar air heater using stochastic iterative perturbation technique. Solar Energy, 85, 2331–2337.10.1016/j.solener.2011.06.022
- Varun, & Siddhartha (2010). Thermal performance optimization of a flat plate solar air heater using genetic algorithm. Applied Energy, 87, 1793–1799.10.1016/j.apenergy.2009.10.015
- Veček, N., Mernik, M., & Črepinšek, M. (2014). A chess rating system for evolutionary algorithms: A new method for the comparison and ranking of evolutionary algorithms. Information Sciences. Retrieved from http://dx.doi.org/10.1016/j.ins.2014.02.154
- Waghmare, G. (2013). Comments on ‘a note on teaching–learning-based optimization algorithm’. Information Sciences, 229, 159–169.10.1016/j.ins.2012.11.009
- Yu, K., Wang, X., & Wang, Z. (2014). An improved teaching–learning-based optimization algorithm for numerical and engineering optimization problems. Journal of Intelligent Manufacturing. doi:10.1007/s5-014-0918-3
- Zou, F., Wang, L., Hei, X., Chen, D., & Yang, D. (2014). Teaching–learning-based optimization with dynamic group strategy for global optimization. Information Sciences, 273, 112–131.10.1016/j.ins.2014.03.038