Abstract
A pozzolanic material ordinarily contains high amounts of siliceous or aluminous components, but has no cementitious property until when it reacts with calcium hydroxide, that is available in cement, in the presence of moisture. The present study evaluates the pozzolanicity of ceramic tile powder and its effect on both hydration mechanism and strength property of recycled aggregate concrete. It was seen that ceramic floor and wall tiles sourced from construction and demolition wastes, contain high silica and alumina oxides, which evidently showcased its pozzolanicity. This was further revealed by the microstructural images of ceramic blended cement. Strength properties of recycled aggregate concrete were enhanced with addition of ceramic powder and ceramic coarse fraction, more than the strength developed in the control concrete. The increased strength was an indication that the interfacial transition zone between the aggregate and blended cement paste enhanced the properties of recycled aggregate concrete (RAC). However, the tensile behavior of RAC was irregular, it initially decreased with 20% ceramic powder addition but it increased when 30% ceramic powder was added. Therefore, ceramic power derived from wall and floor tiles can be used as partial replacement for cement in recycled aggregate concrete.
Public Interest Statement
Over the years, the economic impact and problems associated with continuous exploitation of natural concrete aggregate sources has drawn attention from scientists and engineers worldwide. As a sustainability measure, various alternative materials are being investigated for possible use as partial or total replacement for natural aggregates. Among other materials, solid wastes which are generated from industrial or construction activities (usually landfilled materials) are given strong consideration, for possible inclusion in concreting. A persistent attention is paid on materials which possess good physical and engineering properties that are similar to that of conventional materials. It is interesting that a good number of investigations are currently focused on issues relating to sustainability of construction materials. Thus, a sure way for curtaining depletion of the natural sources is to systematically incorporate the industrial rejects into concrete production.
1. Introduction
About 900 million tons of construction and demolition (C&D) wastes are generated every year in Europe, USA and Japan, according to the report of World Business council for sustainable development (WBCFS Development, Citation2014). Similarly, a report by (Margarido, Citation2014), revealed that construction activities takes 50% of raw materials from nature, consumes 40% of total energy, and creates 50% of total waste. But it is noteworthy that some developed nations of the world are already adopting (C&D) wastes for production of nonstructural concrete (Achtemichuk, Hubbard, Sluce, & Shehata, Citation2009; Rodrígueza et al., Citation2016; Wai, Mahyuddin, Kenn, & Mohd, Citation2012). For instance, Spain, China and India are among countries where the processed ceramic and glass wastes (Padmini, Ramamurthy, & Mathews, Citation2009; Poon & Chan, Citation2007; Spain Ministry of the Presidency, Citation2008) are used as substitute materials in making recycled concrete. Recently, studies conducted on the performance of ceramics as aggregates and supplementary cementitious material in concrete (Bignozzi & Bonduà, Citation2011; Llamas, Juan, Moran, & Guerra, Citation2007; Sánchez de Rojas, Marín, Rivera, & Frías, Citation2006), have shown that similar mechanical characteristics exist between concrete made with ceramic and the conventional concrete.
Generally, a concrete produced with inclusion of C&D wastes is known as recycled aggregate concrete (RAC). Out of many means of sustainable development pursued for decades, C&D wastes maintain constant consideration by researchers as potential alternative to the natural aggregates. Over time, these waste materials are not gainfully utilised, in other words, the materials end up in landfill or, occasionally, utilized in backfilling of foundation trenches and abutments (Ishikura & Fujii, Citation2008; Rao, Jha, & Misra, Citation2007). Meanwhile, industries expend notable amount on transportation and their disposal, which are ever increasing as result of continuous industrial development (Topçu & Günçan, Citation1995).
Thus, this large amount of generated wastes, are still under investigation for their potential use as supplementary materials for construction industry. C&D assessment is borne out of the effort to undermine environmental degradation caused by the excessive exploration of natural aggregate sources, and the carbon dioxide (CO2) and other harmful substances released during production of cement. Subsequent reuse of C&D wastes on a large scale is an ideal means of reducing their effects on the environment, thus the excessive exploration of natural resources will be prevented.
In previous studies on the use of C&D wastes (Halicka, Ogrodnik, & Zegardlo, Citation2013; Lucas, de Brito, Veiga, & Farinha, Citation2016; Medina, Sánchez de Rojas, Thomas, Polanco, & Frías, Citation2016), extensive information are available on the mechanical and physical properties of RAC made with sanitary wares and electrical insulators as aggregates. However, there is need to also evaluate the aforementioned properties in RAC when ceramic powder is used as substitute for cement and concurrently with ceramic aggregates and recycled concrete aggregate (RCA) as replacement for gravel. Thus, as a contribution to existing findings, this study is focused on ascertaining the influence of ceramic content, fine and coarse fraction, on the strength properties of concrete made with crushed concrete.
1.1. Recent development in RAC
The concrete wastes are difficult materials to be stored, owing to challenges of inadequate dumping facilities, availability of landfills and high transportation costs. Thus, a beneficial reuse of RCA is mostly desired by the society and stakeholders in the built environment. In opposition to conventional disposal of C&D wastes, practiced in many decades ago, this material has been subjected to evaluation for its reuse in construction field (Casuccio, Torrijos, Giaccio, & Zerbino, Citation2008; Thomas, Setién, & Polanco, Citation2016). Generally, RAC can be produced with secondary materials generated from demolished concrete works (Ceia, Raposo, Guerra, Júlio, & de Brito, Citation2016; Rodrígueza et al., Citation2016), ceramic tiles (Awoyera, Akinmusuru, & Ndambuki, Citationin press; García-González, Rodríguez-Robles, Juan-Valdés, Morán-del Pozo, & Guerra-Romero, Citation2014; Medina, Frías, & Sánchez de Rojas, Citation2012), and steel slag (Awoyera, Adekeye, & Babalola, Citation2015; Motz & Geiseler, Citation2001).
Investigations conducted within the last decade have explored the physical and mechanical characteristics of RAC, coupled with its influence on properties of both fresh and hardened concrete (Achtemichuk et al., Citation2009; Chakradhara Rao, Bhattacharyya, & Barai, Citation2011; Evangelista & de Brito, Citation2007; Rahal, Citation2007). The use of crushed aggregates has a significant impact on the strengths of most RAC, which were reported to be lower than those of natural aggregates, thus the quality of the strengthen RAC is lower than that of normal weight concrete. Therefore, in line with the objective of this study, it is pertinent to further examine RAC mixes, made with ceramic tiles.
1.2. Ceramic tile wastes
Ceramic industry generates excess wastes during production. Survey index has shown that about 30% ceramic material ends up as waste during production (de Brito, Pereira, & Correia, Citation2005; Pacheco-Torgal & Jalali, Citation2010), and it is not recycled at present. On the other hand, ceramic wastes are also generated during demolition and construction activities. As a way of managing such wastes, recent research findings suggested that ceramic is a potential pozzolan which can partially be integrated into cement mix (Cheng, Huang, Liu, Hou, & Li, Citation2016). On a general note, pozzolanic materials are also known as supplementary cementitious materials (SCM). Other tested examples of pozzolan includes: fly ash (Achtemichuk et al., Citation2009; Babalola & Awoyera, Citation2016; Cheng et al., Citation2016),
A related study by Aruntaş, Gürü, Dayı, and Tekin (Citation2010) showcased the effects of waste marble on the properties of cement such as consistency, setting times, insoluble residue, and soundness, which are all within the acceptable ranges of different standards. The production of cheaper and more durable concrete using this waste can solve to some extent the social, ecological and environmental problems.
In the quest to develop more innovation in the RAC production, most of the recent studies have considered some ceramic products such as sanitary wares and electrical insulators as natural aggregate replacement. However, there is limited information about the use of ceramic floor and wall tiles powder as cement replacement in RAC. Consequently, this study focused on the use of combination of: gravel, waste ceramic tile and rubbles as coarse aggregate for concreting, while ceramic tile powder is to replace Portland cement in varying proportions.
2. Materials and methodology
2.1. Constituent materials used
The constituent materials used in this study include: Ordinary Portland cement, 42.5, (conforming to specifications) (British Standard Institute, Citation1989a; Nigeria Industrial Standards Center, Citation1989, Citation2003), gravel of 12.7 mm nominal sizes, and river sand of sizes 0–4 mm. The substitution materials, ceramic tile and RCA, were sourced from construction and demolition sites within Ota and Lagos, Nigeria. Both Ceramic tile and RCA were cleansed in order to remove debris from it and thereafter, they were crushed using a metal hammer, into gravel size. Meanwhile, portion of ceramic tile was ground into powder size, where the portion sieved through BS 53 micron standard sieve was used as a partial replacement for cement. Grading of ceramic powder was ensured. It reflects cement properties because material fineness mostly influences its pozzolanic reaction with parent binding agent (Pereira de Oliveira, Castro Gomes, & Santos, Citation2007; Uzal, Citation2014). A particle size distribution curve of cement and ceramic powder is shown in Figure . As can be seen, ceramic powder used was mostly finer than the cement. This is evidently appropriate as it is a promising property (Kulovaná & Pavlík, Citation2016), for artificial materials to be used in blended binder.
The physical properties of the aggregates used are as shown in Table . The values obtained were in agreement with standard specifications for aggregates (British Standard Institute, Citation1989b, Citation1990a, Citation1990b, Citation1990c). Particle size gradation of the aggregates is shown in Figure .
Table 1. Aggregates physical properties
It can be seen from Table that RCA exhibit high water absorption property, which can lead to a weak performance of concrete matrix, both in mechanical and durability-related terms (Wainwright, Trevorrow, Yu, & Wang, Citation1993). However, this shortcoming was controlled in this study by pre-wetting the aggregate for a period of 10–15 min (González-Fonteboa, Martínez-Abella, Carro López, & Seara-Paz, Citation2011; Sagoe-Crentsil, Brown, & Taylor, Citation2001).
2.2. Proportion of concrete mixes
Thirteen concrete mixes were developed using various proportions of ceramic powder (10, 20 and 30% as substitute for cement) and also with variation of RAC and ceramic coarse (25, 50 and 75% as substitute for gravel). Table shows the details of the mix proportion for all the concretes. Concerning the terms, NA refers to natural aggregate concrete that was made with conventional materials, moreover this serves as the etalon mix. Whereas, RAC means recycled aggregate concrete that was made with varying portions of ceramic powder, RCA and ceramic coarse. The mixes were designed for a grade 25 (M25) concrete targeted strength at 28 days, with water/binder ratio, (w/b), maintained at 0.6 and the slump was within 55–70 mm.
Table 2. Concrete mix proportion of constituent materials
2.3. Concrete preparation and testing
For each of the mixes, twelve (12) concrete cubes of 150 mm dimensions and eight (8) concrete cylinders of 100 mm diameter and 200 mm length were cast for subsequent determination of compressive and split-tensile strengths, respectively. Potable water was used during concrete mixing. The concrete mixing was in accordance with ASTM C685 (Citation2014) conditions. The concrete specimens were cured for 24 h in molds and after demolding were placed in a potable water and cured under the following conditions: 91 days at room temperature, T = 22 ± 1°C, and relative humidity, R.H = 26%. Both compressive strength and split tensile strengths of concrete cubes and cylinders, respectively, were determined at 3, 7, 28 and 91 days.
3. Results and discussions
3.1. Pozzolanic characteristics of ceramic powder and blended cement
Prior to concrete production, chemical composition of both ceramic tile powder and cement used were determined as shown in Table . Consequently, pozzolanicity of the ceramic powder was established using ASTM C618 (Citation2005) approach, that is, SiO2 + Al2O3 + Fe2O3 ≥ 70 wt.%. In this case, from Table , SiO2 + Al2O3 + Fe2O3 for ceramic powder equals 85.6wt% which was significantly greater than 70wt% recommended by ASTM C618 (Citation2005). Further, the chemical binding capability of the ceramic tile powder was evident by XRD result (Figure ), performed with a graphite monochromator that uses Copper (Cu) radiation. The sample was scanned from 2θ and varied from 10 to 70°.
Table 3. Metallic oxides composition of ceramic tile powder and cement (wt%)
The preliminary chemical composition analysis indicated that ceramic tile powder used possess high amorphous nature. In accordance with previous results, the XRD pattern presented in Figure indicates the presence of amorphous phase from the tile powder excepting the crystalline quartz phase, evidenced on the XRD spectra at 2θ = 23–35°. Micrographs of ceramic powder blended with cement, hydrated 1 and 7 days, are presented in Figures and .
Figure 4. Scanning electron microscope image of blended cement-ceramic powder hydrated for 1 day showing (a) CSH and Ca(OH)2 and (b) Ettringite.
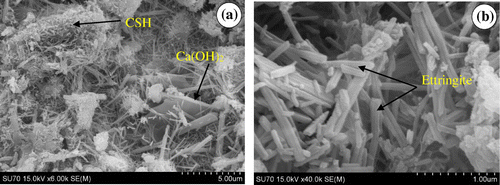
Figure 5. Scanning electron microscope image of blended cement-ceramic powder hydrated for 7 days showing (a) CSH network and (b) Ca(OH)2 and Ettringite.
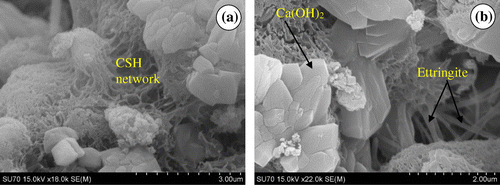
One day of hydration involves the appearance in cement matrix of portlandite (Ca(OH)2) crystals in hexagonal plate-like structure (Figure (a)), joining together with ettringite (Ca6Al2(SO4)3(OH)12·26H2O) in the form of short needles (Figure (b)) (Jumate & Manea, Citationxxxx). The SEM images also show the presence of alite (3CaO·SiO2) and belite (2CaO·SiO2) grains which are not hydrated yet, and the calcium silicates hydrates (CSH) crystalized at the surface of anhydrous blended cement grains. At the later stages of hydration (Figure (a)) the binder matrix is characterized by the presence of Ca(OH)2 crystals surrounded by a densified calcium hydrosilicate network, which include also the ettringite needles (Figure (b)).
3.2. Compressive and split tensile strength developed by RAC
The results of compressive and split tensile strengths measured at 3, 7, 28 and 91 days of the concrete mixtures are shown in Figures and , respectively. The presented values were the averages of three replicate runs of tests performed on concrete cubes and cylinders. For all the considered mixes, both the compressive strength and split tensile strength increase with increasing of curing age. This is one attribute that is common to any concrete matrix. The 28-day strengths of the concrete were evaluated (Figures and ) in an attempt to study the influence of ceramic powder on the RAC mixture. The 28-day compressive strength of all concrete mixtures was significantly influenced by the pozzolanic reaction which occur in cement matrix and on the other hand by the filler effect of fine particles in concrete matrix. For this compositions w/c ratio of 6 is quite high but its effect in the concrete matrix (increasing porosity) is diminished by the calcium silicate hydrates formation (CSH formed by cement hydration and pozzolanic reaction) in the free pores of the concrete matrix (space initial occupied of water) (Awoyera, Akinmusuru, & Ndambuki, Citation2016; Omary, Ghorbel, & Wardeh, Citation2016). Concrete mix containing 25% RCA, 75% ceramic coarse, and 30% ceramic powder blended cement gave 6.2% strength than the etalon mix. This increased strength was an indication that the interfacial transition zone between the aggregate and the blended cement paste enhanced the properties of RAC. However, the tensile behavior of RAC was irregular, it initially decreased with 20% ceramic powder addition but it increased when 30% ceramic powder was added.
After it was established that ceramic powder and coarse addition to RAC adequately improves it strength properties, an optimum mix was developed so as to ascertain the best strength characteristic. Figures and show the optimum surface of the best mix design for compressive and split tensile strength, respectively. Based on the optimization tests which was done at 95% confidence prediction, it was revealed that a mix combination of 25.89% ceramic powder, 1.85% RAC, 77.84% ceramic coarse, and 20.31% gravel would yield a compressive strength of 27.53 MPa and split tensile strength of 3.85 MPa after 28 days of curing.
4. Conclusion
This study has evaluated the pozzolanic influence of ceramic powder on the strength characteristics of recycled aggregate concrete and the following conclusions were drawn:
(i) | Ceramic powder obtained from wall and floor tiles falls within pozzolanic materials, as it was evident in its high silica and alumina oxides. Both SEM micrograph of ceramic blended cement and XRD of ceramics further revealed pozzolanicity of ceramics. The microstructural tests showed that mixture of ceramic powder and cement mixture form a good composite as a binder agent. | ||||
(ii) | With addition of ceramic powder and coarse aggregate to RAC, there was significant increase in strength characteristics of RAC as the curing age increased. Evidently, the ceramics enhanced the hydration of RAC. There existed good bonding between ceramics and other constituents. | ||||
(iii) | Optimal performance of RAC with ceramic powder and coarse found yielded compressive strength higher than the control concrete. An increment that represent about 5.5 and 10.12% strength gain than the control and designed mix concrete, respectively. |
Funding
This research was supported by the Covenant University, Nigeria.
Additional information
Notes on contributors
Paul O. Awoyera
Paul O. Awoyera is currently a visiting PhD research scholar in the Department of Civil Engineering, University of Nottingham, UK. He is an author or co-author of over 20 peer-reviewed scientific papers and also a reviewer for some reputable international journals. He is currently motivated in researches involving green building construction and forensic investigation of distressed structural elements.
Joseph O. Akinmusuru
Joseph O. Akinmusuru is an emeritus professor of civil engineering, currently at the Department of Civil Engineering, Covenant University, Nigeria. He has a world-class standing (he previously taught at the University of Michigan, US). He is an expert in geotechnical engineering practice involving design of underground structures.
Andreea Moncea
Andreea Moncea is a senior researcher at the National Institute for Research and Development in Environmental Protection, Bucharest, Romania. Her research is focused on microscale analysis of supplementary cementitious materials.
References
- Achtemichuk, S., Hubbard, J., Sluce, R., & Shehata, M. H. (2009). The utilization of recycled concrete aggregate to produce controlled low-strength materials without using Portland cement. Cement and Concrete Composites, 31, 564–569.10.1016/j.cemconcomp.2008.12.011
- Aruntaş, H. Y., Gürü, M., Dayı, M., & Tekin, İ. (2010). Utilization of waste marble dust as an additive in cement production. Materials and Design, 31, 4039–4042.10.1016/j.matdes.2010.03.036
- ASTM C618. (2005). Standard Specification for coal fly ash and raw or calcined natural pozzolan for use in concrete.
- ASTM C685/C685M–14. (2014). Standard specification for concrete made by volumetric batching and continuous mixing.. West Conshohocken, PA: Author.
- Awoyera, P. O., Adekeye, A. W., & Babalola, O. E. (2015). Influence of electric arc furnace (EAF) slag aggregate sizes on the workability and durability of concrete. International Journal of Engineering and Technology, 7, 1049–1056.
- Awoyera, P. O., Akinmusuru, J. O., & Ndambuki, J. M. (2016). Green concrete production with ceramic wastes and laterite. Construction and Building Materials, 117, 29–36.10.1016/j.conbuildmat.2016.04.108
- Awoyera, P. O., Akinmusuru, J. O., Ndambuki, J. M. (in press). The performance of ceramic tile wastes as substitute for natural aggregates in laterised concrete. Key Engineering Materials.
- Babalola, O. E., & Awoyera, P. O. (2016). Suitability of Cordia millenii ash blended cement in concrete production. International Journal of Engineering Research in Africa, 22, 59–67.10.4028/www.scientific.net/JERA.22
- Bignozzi, M. C., & Bonduà, S. (2011). Alternative blended cement with ceramic residues: Corrosion resistance investigation on reinforced mortar. Cement and Concrete Research, 41, 947–954.10.1016/j.cemconres.2011.05.001
- British Standard Institute. (1989a). BS 12, specification for ordinary and rapid-hardening Portland cement. London: Author.
- British Standard Institute. (1989b). BS 812: Part 103-2, Testing aggregates. Method for determination of particle size distribution. Sedimentation test. London: Author.
- British Standard Institute. (1990a). BS 1377: Part 1, Methods of test for soils for civil engineering purposes. General requirements and sample preparation. Author.
- British Standard Institute. (1990b). BS 812: Part 110, Methods for determination of aggregate crushing value. Author.
- British Standard Institute. (1990c). BS 812: Part 112, Methods for determination of aggregate impact value. London: Author.
- Casuccio, M., Torrijos, M. C., Giaccio, G., & Zerbino, R. (2008). Failure mechanism of recycled aggregate concrete. Construction and Building Materials, 22, 1500–1506.10.1016/j.conbuildmat.2007.03.032
- Ceia, F., Raposo, J., Guerra, M., Júlio, E., & de Brito, J. (2016). Shear strength of recycled aggregate concrete to natural aggregate concrete interfaces. Construction and Building Materials, 109, 139–145.10.1016/j.conbuildmat.2016.02.002
- Chakradhara Rao, M., Bhattacharyya, S. K., & Barai, S. V. (2011). Behaviour of recycled aggregate concrete under drop weight impact load. Construction and Building Materials, 25, 69–80.10.1016/j.conbuildmat.2010.06.055
- Cheng, Y., Huang, F., Liu, R., Hou, J., & Li, G. (2016). Test research on effects of waste ceramic polishing powder on the permeability resistance of concrete. Materials and Structures, 49, 729–738.10.1617/s11527-015-0533-6
- de Brito, J., Pereira, A. S., & Correia, J. R. (2005). Mechanical behaviour of non-structural concrete made with recycled ceramic aggregates. Cement and Concrete Composites, 27, 429–433.10.1016/j.cemconcomp.2004.07.005
- Evangelista, L., & de Brito, J. (2007). Mechanical behaviour of concrete made with fine recycled concrete aggregates. Cement and Concrete Composites, 29, 397–401.10.1016/j.cemconcomp.2006.12.004
- García-González, J., Rodríguez-Robles, D., Juan-Valdés, A., Morán-del Pozo, J. M., & Guerra-Romero, M. I. (2014). Ceramic ware waste as coarse aggregate for structural concrete production. Environmental Technology, 36, 1–10.
- González-Fonteboa, B., Martínez-Abella, F., Carro López, D., & Seara-Paz, S. (2011). Stress-strain relationship in axial compression for concrete using recycled saturated coarse aggregate. Construction and Building Materials, 25, 2335–2342.
- Halicka, A., Ogrodnik, P., & Zegardlo, B. (2013). Using ceramic sanitary ware waste as concrete aggregate. Construction and Building Materials, 48, 295–305.10.1016/j.conbuildmat.2013.06.063
- Ishikura, T., & Fujii, S. (2008). Concrete waste recycling process for high quality aggregate. La Grange Park, IL: American Nuclear Society.
- Jumate, E., & Manea, D. L. (2012). Application of X-ray diffraction (XRD) and scanning electron microscopy (SEM) methods to the Portland cement hydration processes, Journal of Applied Engineering Science, 2 35–42.
- Kulovaná, T., & Pavlík, Z. (2016). Characterization of composite materials based on cement-ceramic powder blended binder. AIP Conference Proceedings, 1738, 280004.10.1063/1.4952064
- Llamas, L. B., Juan, A., Moran, J. M., & Guerra, I. (2007). Eco-efficient concretes: Impact of use of white ceramic powder on the mechanical properties of concrete. Biosystems Engineering, 96, 559–564.
- Lucas, J., de Brito, J., Veiga, R. C., & Farinha, C. (2016). The effect of using sanitary ware as aggregates on rendering mortars’ performance. Materials & Design, 91, 155–164.10.1016/j.matdes.2015.11.086
- Margarido, F. (2014). Environmental impact and life cycle evaluation of materials. In M. Clara Gonçalves & F. Margarido (Eds.), Material for construction and civil engineering (pp. 799–835). Switzerland: Springer International Publishing.
- Medina, C., Frías, M., & Sánchez de Rojas, M. I. (2012). Microstructure and properties of recycled concretes using ceramic sanitary ware industry waste as coarse aggregate. Construction and Building Materials, 31, 112–118.10.1016/j.conbuildmat.2011.12.075
- Medina, C., Sánchez de Rojas, M. I., Thomas, C., Polanco, J. A., & Frías, M. (2016). Durability of recycled concrete made with recycled ceramic sanitary ware aggregate. Inter-indicator relationships. Construction and Building Materials, 105, 480–486.10.1016/j.conbuildmat.2015.12.176
- Motz, H., & Geiseler, J. (2001). Products of steel slags an opportunity to save natural resources. Waste Management, 21, 285–293.10.1016/S0956-053X(00)00102-1
- Nigeria Industrial Standards Center. (1989) NIS 444: Part II, conformity evaluation. Abuja: Author.
- Nigeria Industrial Standards Center. (2003) NIS 444: Part 1, composition, specifications and conformity criteria for common cements. Abuja: Author.
- Omary, S., Ghorbel, E., & Wardeh, G. (2016). Relationships between recycled concrete aggregates characteristics and recycled aggregates concretes properties. Construction and Building Materials, 108, 163–174.10.1016/j.conbuildmat.2016.01.042
- Pacheco-Torgal, F., & Jalali, S. (2010). Reusing ceramic wastes in concrete. Construction and Building Materials, 24, 832–838.10.1016/j.conbuildmat.2009.10.023
- Padmini, A. K., Ramamurthy, K., & Mathews, M. S. (2009). Influence of parent concrete on the properties of recycled aggregate concrete. Construction and Building Materials, 23, 829–836.10.1016/j.conbuildmat.2008.03.006
- Pereira de Oliveira, L. A., Castro Gomes, J. P., Santos, P. (2007, January). Optimization on pozolanic reaction of ground waste glass incorporated in cement mortars. SB07 Sustainable Construction, Materials and Practices, Volume: Part 2, Covilhã.
- Poon, C. S., & Chan, D. (2007). The use of recycled aggregate in concrete in Hong Kong. Resources, Conservation and Recycling, 50, 293–305.10.1016/j.resconrec.2006.06.005
- Rahal, K. (2007). Mechanical properties of concrete with recycled coarse aggregate. Building and Environment, 42, 407–415.10.1016/j.buildenv.2005.07.033
- Rao, A., Jha, K. N., & Misra, S. (2007). Use of aggregates from recycled construction and demolition waste in concrete. Resources, Conservation and Recycling, 50, 71–81.10.1016/j.resconrec.2006.05.010
- Rodrígueza, C., Parrac, C., Casadob, G., Minanoa, I., Albaladejoa, F., Benitoa, F., & Sanchez, I. (2016). The incorporation of construction and demolition wastes as recycled mixed aggregates in non-structural concrete precast pieces. Journal of Cleaner Production, 127, 152–161. doi:10.1016/j.jclepro.2016.03.137
- Sagoe-Crentsil, K. K., Brown, T., & Taylor, A. H. (2001). Performance of concrete made with commercially produced coarse recycled concrete aggregate. Cement and Concrete Research, 31, 707–712.10.1016/S0008-8846(00)00476-2
- Sánchez de Rojas M. I., Marín, F., Rivera, J., Frías, M. (2006). Morphology and properties in blended cements with ceramic wastes as a pozzolanic material. Journal of the American Ceramic Society, 89, 3701–3705.10.1111/jace.2006.89.issue-12
- Spain Ministry of the Presidency. (2008). Real Decreto 105/2008, de 1 de Febrero, por el quese Regula la Producción y Gestión de los Residuos de Construcción y Demolición [Royal Decree 105/2008, February 1, which regulates the production and management of construction and demolition waste], Madrid.
- Thomas, C., Setién, J., & Polanco, J. A. (2016). Structural recycled aggregate concrete made with precast wastes. Construction and Building Materials, 114, 536–546.10.1016/j.conbuildmat.2016.03.203
- Topçu, İ. B. & Günçan, N. F. (1995). Using waste concrete as aggregate. Cement and Concrete Research, 25, 1385–1390.10.1016/0008-8846(95)00131-U
- Uzal, B. (2014). 7 – Properties of concrete with high-volume pozzolans. In F. Pacheco-Torgal, S. Jalali, J. Labrincha, & V. M. John (Eds.), Eco-Efficient Concrete (pp. 138–152). Cambridge: Woodhead Publishing.
- Wai, H. K., Mahyuddin, R., Kenn, J. K., & Mohd, Z. S. (2012). Influence of the amount of recycled coarse aggregate in concrete design and durability properties. Construction and Building Materials, 26, 565–573.
- Wainwright, P. J., Trevorrow, A., Yu, Y., & Wang, Y. (1993, October). Modifying the performance of concrete made with coarse and fine recycled aggregates. In Third International RILEM Symposium on Demolition and Reuse of Concrete and Masonry on Demolition and Reuse of Concrete and Masonry, (E&FN Spon 1994) (pp. 319–330), Odense.
- WBCFS Development. (2014). The cement sustainability initiative, USA. Retrieved April 11, 2016, from http://www.wbcsdcement.org