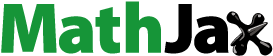
Abstract
Organic fertilizer forms the lifeblood & basic necessity of every poor farmer as a result of high cost of buying the chemical (Inorganic) fertilizer. The organic machinery plant consists of the shredder, the mixer, the pelletizer and a conveyor system that will link the shredder to the mixer, in such a way that, the shredding and mixing operation can be done simultaneously. The shredder consists of components such as a 3 kW electric motor, rotating shaft, 2 mm thick mild steel, a rotating blade which will act as the stirrer and a sieve. The mixer consists essentially of a 3 kW electric motor and a rotating shaft of 90 mm. Main features of the pelletizer are electric motor (single phase, 3 kW), 50 mm axial shaft, screw auger, extrusion barrel, bearing case, pulley, chain and sprockets. The dimension of the machine frame is (800 × 500 × 600 mm). The performance of the machine was based on pelleting efficiency, percentage recovery and throughput capacity of the machine, which were determined at three different mesh sizes of 2, 4 and 6 mm. Results obtained showed that the 6 mm mesh size has the highest pelletizing efficiency (76%). Characterization of the organic manure was carried out indicated a carbon to nitrogen ratio of approximately 30 and a pH value of 7. This is an indication that the organic manure is rich in nutrient composition and healthy for soil rejuvenation.
Public Interest Statement
This research aimed at developing organic fertilizer machinery which can be producing organic fertilizer for small to large scale farming to restore lost fertility to the soil and boosting crop production. Organic fertilizer is the end product obtained by converting various organic wastes such as crop residue, urban wastes, poultry droppings, animal dung, etc., into a usable fertilizer by a modified aerobic anaerobic process of composting. Organic fertilizer has advantages which include: high nutrient content; suitability to a range of crops; fast biodegradability and safety. Organic fertilizers are used as supplements to chemical fertilizers, thereby reducing the import of the chemicals. The agriculture sector is deemed unsustainable with the negative environmental consequences on the soil condition, since the current agriculture practices are basically chemical based farming, which make considerable contributions to the degradation of the natural resources, particularly soils. Heavy application of Chemical fertilizers has polluted surface and groundwater resources.
1. Introduction
Agriculture is an economic driven activity which aims to produce and increase production of crops and food supply to feed the human population. However, the continued exploitation of our natural resources such as land and other resources lead to poor productivity level and future shortage of food supply while the use of modern agricultural practices had damaged our environment (Crucefix, Citation1998). Also, the increasing prices of farm inputs in the market is a common problem farmer in the word today because not everyone could afford to buy farm inputs just to increase productivity and that affects food security. Organic fertilizer is the end product obtained by converting various organic wastes such as crop residue, urban wastes, poultry droppings, animal dung, etc. into a usable fertilizer by a modified aerobic anaerobic process of composting. Organic fertilizer has advantages which include: high nutrient content; suitability to a range of crops; fast biodegradability and safety (Akinnuli & Bodunde, Citation2017). Organic fertilizers are used as supplements to chemical fertilizers, thereby reducing the import of the chemicals (Mansell, Syers, & Gregg, Citation1981). Farmers are clearing new land resulting in deforestation, tilling of pasture and soil degradation. For the agricultural sector, the need to shift into sustainable farming practices is necessary for food security and to mitigate climate change. Organic land management may help to stop soil erosion and convert carbon losses into gains particularly due to the use of green and manure, soil fertility.
The principal objectives of organic agriculture include; to produce food of high nutritional quality in sufficient quantities; to interact in a constructive and life-enhancing way with natural systems and cycles; to encourage and enhance biological cycles within the farming system, involving microorganisms, soil flora and fauna and plants and animals; to maintain and increase long term fertility of soils, to help in the conservation of soil; to work, as far as possible, within a closed system with regard to organic matter and nutrient elements; to work, as far as possible, with materials and substances which can be reused or recycled, either on the farm or elsewhere; to give all livestock conditions of life which allow them to perform the basic aspects of their innate behavior; to minimize all forms of pollution that may result from agricultural practice; to maintain the genetic diversity of the agricultural system and its surroundings, including the protection of plant . Organic fertilizer is capable of restoring lost fertility to the soil and boosting crop production Traditional agricultural practices result in excessive leaching of the soil.
This research aimed at developing organic fertilizer machinery which can be producing organic fertilizer for small, medium and large scale farming to restore lost fertility to the soil and boosting crop production.
Organic fertilizers are used as supplements to chemical fertilizers, thereby reducing the import of the chemicals by 30%. The agriculture sector is deemed unsustainable with the negative environmental consequences on the soil condition, since the current agriculture practices are basically chemical based farming, which make considerable contributions to the degradation of the natural resources, particularly soils. Heavy application of fertilizers has polluted surface and groundwater resources. Intensive cropping to feed the ever expanding population coupled with high erosion rates in the uplands has resulted severe soil nutrient depletion. Based on these scenarios, there is an urgent need to find ways and means of alleviating such problems by creating new and innovative processes which would allow this resource to be better utilized and simultaneously reduce environmental impacts. Organic-based agricultural production is the rapidly emerging technology in the sector which partly solves waste disposal problems through conversion f biodegradable wastes into organic compost ensuring the availability of organic fertilizer (Moore, Daniel, Sharpley, & Wood, Citation1991).
Organic fertilizer is the end producer obtained by converting organic wastes such as crop residue, urban waste, poultry dropping and animal dung etc. into a useable fertilizer by a modified aerobic—cum-anaerobic process of composting. Organic fertilizer has advantages which include: high nutrient content; suitability to a range of crops; fast biodegradability and safety. Fresh composted manure generally has high nitrogen content than composted manure (Kibret, Ramayya, & Abunie, Citation2016). However, the use of composted manure will contribute more to the organic matter content of the soil. Fresh manure is high in soluble forms of nitrogen which can lead to sand build up and leaching. If over applied it can introduce pathogens and viable weed seed into the soil (Kibret et al., Citation2016). Organic based fertilizer production partly solves disposal problems through conversion of biodegrable waste into organic compost which can supplement chemical fertilizers (Mansell et al., Citation1981), it can also help check soil erosion by improving the soil structure and increasing the moisture holding capacity of the soil (Hochmuth & Jones, Citation2009) and can convert carbon losses into the gain particularly due to the use of green manure thereby increasing soil fertility (Kibret et al., Citation2016). Composting is a biological process in which organic wastes are broken down by microorganism and converted into a product to be used as a soil conditioner known as organic fertilizer. This process depends upon the activity of microorganism. These microorganisms require a carbon to nitrogen ration (C:N) between 25 and 30 moisture content of 40–60%, pH between 5 and 12 (Klausner, Kanneganti, & Bouldin, Citation1994) and particle size greater than 30% free air space (Willson,Citation1989) when manure is composted, its volume decreases and nutrient density increases (Holden, Citation1990).
Pawar et al. (Citation2017) designed and fabricated organic fertilizer manufacturing machine, and found out that chemical fertilizers are expensive for formers to combat with in rejuvenating the lost nutrients of the soil. They indentified four major problems which propel their design and they are:
(i) | There is no more scope for organic farming which is required. | ||||
(ii) | The machines available for preparing organic fertilizers are costly which farmers cannot afford to buy. | ||||
(iii) | Available machines are fuel consuming and operates at high power consumption which indirectly increases the cost. | ||||
(iv) | Available machines are very bulky. |
2. Materials and methods
2.1. Material selection
The materials used for fabrication were selected after careful study of its physical, mechanical, chemical and aesthetic characteristics as shown in Table . For the purpose of this work, due to economic consideration and material availability, high and medium carbon steel were mostly used for body parts while cast iron was chosen for pulley.
Table 1. Component description
The following machine components were employed in the construction of the shredding machine:
(i) | A variable speed electric motor; | ||||
(ii) | Belt; | ||||
(iii) | Pulley; | ||||
(iv) | Galvanized sheet metal; | ||||
(v) | Cylindrical drums; | ||||
(vi) | Bearing support; | ||||
(vii) | Machine Frame; | ||||
(viii) | The control system; | ||||
(ix) | Shaft; | ||||
(x) | Chopper; | ||||
(xi) | Granulator; | ||||
(xii) | Inner drum; and | ||||
(xiii) | The leg and stand orientation. |
3. Design and fabrication of an organic manure machine
The machine for processing organic manure comprises three main components namely:
(i) | Shredder | ||||
(ii) | Mixer | ||||
(iii) | Pelletizer |
3.1. Design of a shredder
According to Dieter and Schmidt (Citation2009), the mass of the drum, m of the shredder is given by Equation (1):(1)
(1)
where ρ is the density of the material (kg/m3); and V the volume of the material (m3).
but
(2)
(2)
Hence Equation (1) becomes:(3)
(3)
Weight of the shredder drum is given by Equation (4):(4)
(4)
(5)
(5)
Hence from Equation (3):
A medium carbon steel with approximately 0.250–0.6% carbon content is selected for the fabrication of the shredder drum because it balances ductility and strength and has good wear resistance (Khurmi & Gumpta, Citation2010; Nishimura & Dangl, Citation2010 )
Organic waste is fed uniformly through feeding drum and tray. Then the shaft rotated through electric motor by means of pulleys makes the chopping drum to cut the waste by the effect of impact shear obtained from the shearing blades, the model design for the cover for the Shredding Machine is as shown in Figures and shows the stand for the Shredding Machine. The cut is also made inside the chopping house due to the effect of tensile, friction, and impact effect in chopping process. Then the cut pieces pass through the concave holes of the sieve & come out of the machine. The sieves of different sized holes can be used. Figures and show the fabricated shredding machine and fabricated pelletizer.
3.2. Machine capacity
The machine is designed to accommodate 10 kg of organic waste in 1 min. The machine member is subjected to torsion (action of two equal and opposite couple acting in parallel plane which could be torque or twisting moment. The stress induced by the torsion results in torsional shear stress which is zero at the centroidal and maximum at the outer surface. The machine has a shaft fixed at one end and is subjected to torque T at the other end. As a result of this torque, every cross section of the shaft is subjected to torsional shear stress (Khurmi & Gumpta, Citation2010).
3.3. Power transmission
Power transmitted by shaft in watt is given by the Equation (6):(6)
(6)
where P is the power rating of the electric motor (watt), T is the torque transmitted in (Nm), and N is the number of revolutions per minute.
Torque T is given by Equation (7):(7)
(7)
where m is the mass of the inner drum (12.5 kg), a is the acceleration due to gravity (9.81 m/s2), r is the radial distance (0.25 m).
From Equation (9):
N is the number of revolution per minute which 400 rpm, Equation (6) therefore gives:
Having a factor of safety of 2, it gives 2.568 kW. Hence, 3 kW electric motor will produce sufficient motion for the belt and shaft.
3.3.1. Power required by the shredding drum
According to Shigley and Mischke (Citation2003), Equation (8) gives the force required for each load per second on the shredding drum:(8)
(8)
The torque T due to applied load is given by the Equation (10):(9)
(9)
Substituting Equation (8) into (9):(10)
(10)
The power P required to drive this torque is given by Equation (11):(11)
(11)
3.4. The shredding machine shaft design
Shaft designs consist primarily of the determination of the correct shaft diameter that will ensure satisfactory rigidity and strength when the shaft is transmitting power under different loading conditions (Shigley & Mischke, Citation2003).
The design of the machine is such that the shaft receives power from the electric motor via a V-belt.
For rotating shaft, the torsional moment acting on the shaft is given by Equation (12):(12)
(12)
The magnitude of the load is given by Equation (13):(13)
(13)
where m is the mass of the drum (12.5 kg), a is the acceleration due to gravity (9.81 m/s2).
Hence, from Equation (13) the magnitude of load is 122.5 N
The bending moment of the shaft of length 2 m with a central load is given in Equation (14) as depicted in Figure .(14)
(14)
The shaft is solid having little or no axial loading.
The shaft diameter is given in Equation (15):(15)
(15)
where Mt is the torsional moment (35.80 Nm), Mb is the bending moment (86.6 Nm), Kb is the combined shock and fatigue factor applied to bending moment for gradual loading (1.0), Kt is the combined shock and fatigue factor applied to torsional moment for gradual loading (1.5), ss is the allowable shear stress for shaft without keyway (55 × 106 N/m2) and d is the shaft diameter (m).
From Equation (15):
The shaft diameter for the shredder is calculated as 49, 50 mm to the nearest standard size.
3.5. Belt design
V-belt is selected for use because of the following:
(i) | Great amount of power is to be transmitted from one pulley to another. | ||||
(ii) | The two pulleys are near to each other. |
According to Khurmi and Gumpta (Citation2010), for a rubber belt material whose pulley material is cast iron, the coefficient of friction between the belt and pulley is 0.30. The ratio between the velocities of the driver and the driven pulley is given in Equation (16):(16)
(16)
where d1 is the diameter of the driver pulley (mm), d2 is the diameter of the driven pulley (mm), N1 is the speed of the driver (rpm), N2 is the speed of the driven (rpm).
The length that passes over the driver in one minute is given in Equation (17):(17)
(17)
Similarly, the length that passes over the driven in one minute is given in Equation (18):(18)
(18)
The velocities of the driver and driven is given in Equation (19):(19)
(19)
Similarly, for the driven pulley,
There is no slip since V1 = V2.
The angle of V-belt is usually from 30° to 40° (Khurmi & Gumpta, Citation2010).
According to IS-2494-1974 as cited by Khurmi and Gumpta (Citation2010), for a V-belt whose power in kW ranges from 0.7 to 35.
The minimum pitch diameter of pulley (D) is 80 mm, the top width (b) is 12 mm and the thickness t, is 8 mm.
The weight per meter length is 1.06 N(20)
(20)
where x is the centre distance between the two pulleys (1,000 mm).
And the angle of lap on the smaller pulley is given by Equation (21):(21)
(21)
Centrifugal tension is given by Equation (22):(22)
(22)
where m is the mass of belt per meter length (0.15 kg/m) and v is the speed of belt, m/s (2.50 m/s)
Maximum tension in the belt T is given by Equation (23):(23)
(23)
The pitch length of belt is given in Equation (24):(24)
(24)
The inside length of the belt is given as .
From the above estimation proposed by Khurmi and Gumpta (Citation2010) can be inferred that a V-belt of 2464 mm should be selected for the machine. According to 2494-1974, the inside length of the selected V-belt (2484 mm) is given as A2464-IS:2494.
3.6. Design of the pelletizer
The screw type pelletizing machine was designed and fabricated using locally available construction materials to make handling and packaging organic manure easy for onward utilization for remediating the soil. The machine was designed to be portable for easy transportation and to be operated by an individual and pelletizing was achieved through the process of extrusion and bonding of organic manure with the aid of binding agents such as starch. Main features of the machine are electric motor (single phase, 3 kW), 50 mm axial shaft, screw auger, extrusion barrel, bearing case, pulley, chain and sprockets. The dimension of the machine frame is (800 × 500 × 600 mm). The performance of the machine was based on pelleting efficiency, percentage recovery and throughput capacity of the machine, which were determined at three different particle sizes. The following are design considerations: system capacity, hopper capacity, power requirement, forces acting on the shaft and shaft diameter.
3.7. Design of the hopper
A hopper in form of rectangular based pyramid frustum, which is made of mild steel, is considered.
The selected dimensions are:
(i) | Upper face of the hopper: 260 × 240 mm | ||||
(ii) | Lower face of the hopper: 70 × 50 mm | ||||
(iii) | Height: 150 mm. |
The development of the hopper is such that the dimensions are marked out and cut out from a mild steel sheet, and then welded together. Pellets are produced through the process called extrusion. The pelletizing machine comprises some basic component like the hopper through which feed manure into the machine, to the pelleting chamber which consists of the worm, auger or screw (shaft) which propel the manure. The shaft transmits motion by means of a 3 kW electric motor. The output pellet is formed by compacting and forcing through a die opening (with suitable diameter die hole) by a mechanical process.
The inner diameter d1 = 16 mm and the outer diameter d2 = 20 mm. The thickness t, to inner diameter ratio is t/d1 = 0.125.
A cylinder with t/d1 < 0.05 is generally regarded as a thin walled cylinder (Khurmi & Gumpta, Citation2010). Thus, this pelleting cylinder is a thick walled cylinder theory, the radial stress σr, the hoop stress σh and the axial stress σz at a diameter d in the body of the cylinder are given in Equation (25):
(25)
(25)
(26)
(26)
(27)
(27)
For open ends of cylinder when an internal pressure P1 is applied only. The minimum stresses occur at the cylinder bore, that is, at d = d1. The internal pressure which is equal to the extrusion pressure is given by Equation (27). Figures and show the fabricated Mixer and the model design of the Mixer respectively.
4. Performance evaluation
4.1. Development of an integrated process for the production of organic fertilizer
The composting process is described by Equation (28):(28)
(28)
The process flow for production is described in Figure .
4.2. Process flow for production
Composting materials are poultry and hog manure in a ratio of 2:1 (Holden, Citation1990). Compost additives are additives divided into two basic categories:
(i) | Brown materials (high carbon source) such as straw, paper, sawdust, rice dust etc. | ||||
(ii) | Green materials (high nitrogen source) such as grass chippings, fresh manure, vegetable trimmings etc. |
According to Holmer, Gabutinn, and Schnitzler (Citation1997), the ideal mixture of material should be carbon to nitrogen in the ratio 30:1 by weight.
4.2.1. Stage 1: Weighing and drying of compost
The poultry and hog manure used for the production of organic fertilizer was collected from Afe Babalola University Farms, Ado Ekiti, Nigeria. The wet samples were weighed with the aid of weighing balance and sun dried (Figures and ) for 5 days and re-weighed (Figures and ).
The moisture content of the compost was determined using Equation (29) and the results are presented in Table .(29)
(29)
The base materials (poultry and hog manure) was turned, mixed and aerated in the ratio 2:1 respectively, (12.2 g: 6.1 g). Thus, the total weight of the compost was 18.3 g. Upon further drying, the total weight of the compost reduces to 18.2 g.
4.2.2. Stage 2: Shredding
This involves breaking the compost into finer size with the aid of a developed shredding machine as shown in Figure . The shredding consists of a rotating shaft, belt, pulley, machine frame, bearings, shredding drums, 0.5 microns mesh, and a 3 kW variable speed electric motor. A 1.5 mm thick mild steel was used in the fabrication of the shredding drums due to availability, strength and cost considerations. The shredding of composite is as shown in Figure and the reidue from the shredding is as shown in Figure .
4.2.3. Stage 3: Analysis of chemical compositions
The carbon, nitrogen, phosphorus and potassium content of the shredded compost was analysed to determine the need of additives or otherwise as shown in Figure . Carbon content is estimated by the loss of weight in a sample heated at a temperature high enough to burn organic matter but not too high to decompose the carbonated. Two samples A and B of the compost were dried at 105°C in an oven to remove moisture. The samples were weighed and heated at 360°C for 2 h and reweighed after the temperature drops below 105°C.
About 20 ml of hydrogen chloride was added to 5 g of each sample and placed in the fume cupboard. It was digested in the digester at 400°C until a clear solution is obtained.
The loss on ignition was calculated as follow
For sample A
For sample B
The average of this two samples is 51.670%. This is the carbon content of the compost.
Determination of the nitrogen content in the sample involves the complete digestion of sample in hot concentrated acid and in the presence of an appropriate metal ion catalyst. The process of digestion is followed by distillation. The final titre value for sample A and B are 4.95 and 4.05 respectively. The percentage of nitrogen for sample A is determined from Equation (30):(30)
(30)
where T is the control titre value (100 ml), C is the molarity of acid (0.054 M) , V1 is the volume of digest used in distillation (4.95 ml), V2 is the volume of blank (0.05), Vs = volume of sample distilled (10 ml), Wt = weight of sample distilled (2.002 g).
From Equation (30):
For sample B, T is the control titre value (100 ml), C is the molarity of acid (0.054 M) , V1 is the volume of digest used in distillation (4.05 ml), V2 is the volume of blank (0.05), Vs = volume of sample distilled (10 ml), Wt = weight of sample distilled (1.765 g).
From Equation (30):
The average of percentage of nitrogen for sample A and B gives 1.78% which is the percent composition of nitrogen.
4.2.4. Stage 4: Addition of additives
Depending on the nature of additives and the production capacity (targeted output per day) the compost is weighed. An ideal additive should supply carbon and nitrogen in the ratio 30:1 carbon in excess shredding of additives before it is blended with the milled compost. Wood chips are then added as additives to the compost in the right population as indicated in Table .
Table 2. Carbon nitrogen ratio of additives
4.2.5. Stage 5: Mixing of additives with compost
The biomasses (compost and additives) must be thoroughly mixed by means of a mixer (rotating drum internally equipped with a rotary screw). To optimize the composting process the materials are blended in such a way to obtain a theoretical C:N ratio of 30 after this the process is monitored for about 120 days. The Temperature range varies between 55 and 65°C (daily temperature tends must be recorded during the composting process) while the percentage of dry matter was between 60 and 75% (waste maybe added to keep the dry matter in this percentage).
4.2.6. Stage 6: Turning
Since few thermophilic organisms which aid decomposition can actively carry out decomposition above 70°C therefore the optimum temperature range is 55–65°C for 14 days. Turning continues until the mixture is mostly broken down and is dark crumbly and smell rich and earthly size of compost i.e. between 5 and 50 mm. This was achieved with the aid of a mixer.
4.2.7. Stage 7 : Pelletization
Mechanical pelletizer powered by an electric motor was used for the for pelletization process. Pellet sizes was in the range of (2–6 mm) according to the 3 different mesh sizes (2, 4 and 6 mm) in order to prevent nutrient loss from the soil.
4.2.8. Stage 8: Drying
The pelletized manure was sundried for 3 days.
4.5. Pelleting efficiency
The pelletizing efficiency is given by Equation (31):(31)
(31)
where w0 is the total mass of pellets produced and wi is the total mass of input manure.
5. Results and discussion
5.1. Results
The weight of compost and the moisture loss for poultry and hog manure during 5 days of sun drying is shown in Table .
Table 3. Weight of compost and moisture loss for poultry and hog manure
From Table , there is significant moisture loss in the manure as a result the moisture content of both the poultry and hog manure decreases with increasing days of drying, this result is presented in Figure .
From Figure , as a result of evaporation of moisture when subjected to sun drying for 5 days, the moisture content of both the poultry and hog manure decreases with increasing days of drying.
5.2. Characterization of the organic manure
The nutrient content of the organic manure was determined at the Chemical Analysis Laboratory of Afe Babalola University, Ado Ekiti (ABUAD), Nigeria and The Federal University of Technology, Akure (FUTA), Nigeria. The result obtained is presented in Table .
Table 4. Characterization of the organic manure
From Table , a C:N ratio of approximately 30 is obtained from both analysis and the pH of the organic manure is neutral. This is an indication that the organic manure is rich in nutrient composition and healthy for soil rejuvenation.
From Table , the pelletizing efficiency which is the percentage ratio of recovered pellets to the total weight of manure fed is increases as the mesh size increases. Some of the manure got stuck as a result of decreasing mesh size, hence the total mass of pellets increases as mesh size increases (Figure ). The only demerit is that the rate of decomposition of manure when applied on soil increases as mass of pellets decreases.
Table 5. Pelletizing efficiency
The pelletized manure using 6, 4 and 2 mm mesh sizes is presented in Figures – respectively.
6. Conclusion
This project was designed, fabricated and tested with locally sourced materials to meet high demand of farmers on organic fertilizers due to adverse effects of chemical (inorganic) fertilizers on the crops. From the analysis, results obtained and their discussions, the following conclusions were drawn from the research carried out:
• | The performance of the machine was based on pelleting efficiency, percentage recovery and throughput capacity of the machine, which were determined at three different mesh sizes of 2, 4 and 6 mm. | ||||
• | Results obtained showed that the 6 mm mesh size has the highest pelletizing efficiency (76%). Characterization of the organic manure was carried out indicated a carbon to nitrogen ratio of approximately 30 and a pH value of 7. This is an indication that the organic manure is rich in nutrient composition and healthy for soil rejuvenation. Increase in mesh size increases the mass of pellets. Increase in mesh size increases the efficiency of the pellets. | ||||
• | Total weight of manure fed increases as the mesh size increases. |
Additional information
Funding
Notes on contributors
I.A. Daniyan
Dr I.A. Daniyan is a lecturer in the Department of Mechanical and Mechatronics Engineering, Afe Babalola University Ado Ekiti.
A.M. Omokhuale
Mr A.M. Omokhuale is a B.Eng graduate of the Department of Mechanical and Mechatronics Engineering, Afe Babalola University Ado Ekiti. He played an active role in this research.
A.A. Aderoba
Prof. A.A. Aderoba obtained his PhD over 40 years ago. He has served for 35 years at the Federal University of Technology Akure in the Department of Mechanical Engineering and at presently he is the Director of Directorate of Technological Development (DTD) and the HOD of Mechanical and Mechatronics Engineering, Afe Babalola University Ado Ekiti.
O.M. Ikumapayi
Engr. O.M. Ikumapayi is a research student and a lecturer at the Department of Mechanical and Mechatronics, Afe Babalola University Ado Ekiti.
B.A. Adaramola
Dr B.A. Adaramola is a senior lecturer at the Department of Mechanical and Mechatronics Engineering, Afe Babalola University Ado Ekiti, Nigeria.
References
- Akinnuli, B. O., & Bodunde, O. P. (2017). Development of a charcol-fuelled dryer for the production of organic fertilizer from frog waste. African Journal of Science, Technology, Innovation and Development, 8(1), 1–7.
- Crucefix, D. (1998). Organic agriculture and sustainable rural livelihood in developing countries. Natural and Ethical Trade Programme.
- Dickson, N., Richard, T., & Kozlowski, R. (1991). Composting to reduce the waste stream – A guide to small scale food and yard waste composting. Ithaca, NY: Natural Resource, Agricultural, and Engineering Service (NRAES-43).
- Dieter, G.E, & Schmidt, L.C. (2009): Engineering design (4 ed.). New York, NY: McGraw-Hill.
- Hochmuth, G., & Jones, J. (2009). Collecting a poultry litter sample for analysis. SS495. Gainesville: University of Florida Institute of Food and Agricultural Sciences. Retrieved from http://edis.ifas.ufl.edu/SS495
- Holden, C. (1990). Process technology and market development for composted poultry manure: An overview of challenges and opportunities. In Proceedings of the 1990 National Poultry Waste Management Symposium (pp. 236–242).
- Holmer, R. J., Gabutinn, L. B., & Schnitzler, W. H. (1997). Organic fertilizer from city waste: A model approach in a south east Asian urban environment. Kasetsart Journal (Natural Science), 32, 50–53.
- Khurmi, R. S., & Gumpta, J. K. (2010). A textbook of machine design. New Delhi: Eurasia Publishing House.
- Kibret, H. A., Ramayya, A. V., & Abunie, B. B. (2016). Design, fabrication and senstitivity testing of an efficient bone pyrolysis kiln and biochar based indigenous ferlizer pelletizing machine for linking renewable energy with climate smart agriculture. ARPN Journal of Engineering and Applied Sciences, 11(12), 1–7.
- Klausner, S. D., Kanneganti, V. R., & Bouldin, D. R. (1994). An approach for estimating a decay series for organic nitrogen in animal manure. Agronomy Journal, 86, 897–903.10.2134/agronj1994.00021962008600050026x
- Mansell, G. P., Syers, J. K., & Gregg, P. E. H. (1981). Plant availability of phosphorus in dead herbage ingested by surface casting earthworms. Soil Biology and Biochemistry, 13, 163–167.10.1016/0038-0717(81)90013-4
- Moore, P. A., T. C. Daniel, A. N. Sharpley and A. N. Wood. (1991). Poultry manure management (pp. 1–10). Arkansas Agricultural Experiment Station.
- Nishimura, M. T., & Dangl, J. L. (2010). Arabidopsis and the plant immune system. The Plant Journal, 61, 1053–1066. doi:10.1111/j.1365-313X.2010.04131.x
- Pawar, P., Mahajan, A., Pawar, S., Pawar, V., Pachpore, S. S., & Bachhav, M. S. (2017, Feb). Design & fabrication of organic fertilizer manufacturing machine. International Research Journal of Engineering and Technology (IRJET), 4, 1348–1350.
- Shigley, J. E., & Mischke, C. R. (2003). Mechanical engineering design (Sixth Metric Edition, Library of Congress Cataloging in Publication Data). New York, NY: Mc Graw Hill.
- Willson, G. B. (1989, August). Combining raw materials for composting. Biocycle, 82–85.