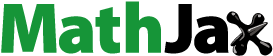
Abstract
In the present investigation, 5 wt% chemical grade MnO2 was added in a mixture of 50:50 Nigerian sources of kaolin and superfine calcined alumina powder and effect of this transition metal ion on their physico-mechanical properties, phase and microstructural evolution were studied during heating in the temperature range of 1,400–1,650°C. The heated samples were found to be highly porous (>30%) in this entire temperature range. The doping of 5 wt% MnO2 in this mixture did not improved the densification, but resulted into higher flexural strength (26 MPa) at 1,400°C compared to 7 MPa in the undoped sample. At 1,650°C, the reverse trend was observed, the flexural strength of undoped sample was found to be higher (38 MPa) than doped sample (27 MPa). The XRD study revealed the formation of mullite as major and corundum as minor phases in both the samples. The microstructural study shown the presence of needle shaped mullite crystals and corundum grains. The presence of inter-granular and intra-granular pores in MnO2 doped samples might have reduced the strength at 1,650°C. The aspect ratio of mullite needle at 1,650°C was found to be higher in doped sample. The theoretical and experimental value of >4 for MnO2 ion has been validated.
Public Interest Statement
This paper studies the performance in terms of densification, strength development, phase and microstructural evolution of mullite formation when kaolin-alumina mixture is doped with Mn4+. The paper compares the differences of the undoped with the doped mixture at different temperatures. The results obtained revealed a non-improvement in terms of densification but inferred increased flexural strength at lower temperatures. The formation of well-developed needle shaped mullite and corundum crystals justifies the obtained flexural strength at lower temperatures in the presence of Mn4+.
1. Introduction
Mullite is one of the most important phases in both traditional and advanced ceramics although it exists rarely in natural rocks. The importance of mullite is documented by the large number of publications. Its high thermal stability and the favorable properties like low thermal expansion and conductivity, high creep resistance and corrosion stability together with suitable strength and fracture toughness are some of the scientific and technical advantages for mullite based ceramic products. Depending on the synthesis procedure, different types of mullite crystals have been described by various authors (Anilkumar, Mukundan, & Warrier, Citation1998; Risbud & Pask, Citation1978). Sintered-mullites are produced by heat treatment of starting materials via solid-state reactions. These mullites are normally stoichiometric having chemical formula 3Al2O3·2SiO2. The starting materials for the synthesis of sinter-mullite are primarily alumina plus silica, alumino-silicates of the composition Al2SiO5, clays, Al2O3-rich sheet silicates which are abundantly available in nature. Out of these, kaolinite and other clay-based materials offer additional advantages such as easy shaping of components in green state due to their high plasticity. In one of our earlier study, a Nigerian source of kaolinitic clay containing high SiO2 together with impurities Fe2O3 and TiO2 gives rise to needle shaped mullite on heat treatment at 1,400°C; itself and the mullite content increases with increase in heating temperature (Ajanaku, Aladesuyi, Pal, & Das, Citation2016). The presence of transition metal ions (Fe3+ and Ti4+) in this clay up to certain limit as impurities might have promoted mullite formation at lower temperature. A report (Gralik, Chinelattot, & Chinelatto, Citation2014) on the impurities present in clay, particularly Fe2O3 and TiO2, indicated that impurities has phenomenal role during heating of clay and clay + alumina mixtures towards formation of mullite. Aladesuyi, Pal, Das, and Ajanaku (Citation2017) also reported that when 25 wt% of very fine calcined alumina was added to this Nigerian clay powder, Al2O3 reacted with the excess SiO2 and enhanced mullite formation. The authors observed that very little densification occurs at 1,400°C and alumina was mostly inert, however flaky primary mullite evolved from the kaolinite series of reactions. At 1,500°C, although densification did not improved much but needle shaped mullite formation nucleated at this temperature are grown and well crystallized at 1,600°C. After formation of mullite by the reactions of alumina and amorphous silica, the excess alumina recrystallized as corundum crystals. A study on the mullitization behavior of calcined clay–alumina mixture with different sources of alumina viz: reactive alumina, gibbsite and boehmite has been carried out and was found that mixture of calcined clay and reactive alumina exhibited better mullitization behavior compared to other combinations (Viswabaskaran, Gnanam, & Balasubramanian, Citation2003).
Mullite has ability to form mixed crystals in a wide Al2O3/SiO2 range and can incorporate a large variety of foreign cations into the structure depending on the synthesis temperature and atmosphere namely when added in differing amounts (Schneider, Citation2005) . The upper solubility limit is controlled by radii and oxidation states of the transition metal ions. Schneider (Citation1990) reported that highest degree of incorporation are observed for V3+, Cr3+ and Fe3+ followed by Ti4+. Only very low amounts of Mn2+, Fe2+ and Co2+ ions can enter the mullite structure. They also observed that transition metal ions preferably enter the octahedral position in mullite replacing Al. A low amount of tetrahedral-bound Fe3+ has also been identified (Mack, Becker, & Schneider, Citation2005). Fe3+ and Mn2+ ions in the middle of the 3d transition metal series make an exception. These cations have stable d5 electron configurations with nearly spherical symmetric charge distributions, similar to those of noble gases. Consequently Fe3+ and Mn2+ should exhibit no site preference and their incorporation behavior should mainly be controlled by the sizes of the cations. Actually a small amount of Fe3+ does enter the oxygen tetrahedral in mullite at high temperature. On the other hand, Mn2+ is obviously too large to be tetrahedrally incorporated in mullite (Schneider, Citation1990; Schneider & Vasudevan, Citation1989). The influence of transition metal ion on the formation of mullite with cases where Mn4+ ion added in the form of MnO2 in wear resistant high alumina ceramic compositions containing around 10 wt% kaolin has been studied (Das, Citation1998; Das, Ray, Mitra, & Gupta, Citation1993, Citation1999; Viswabaskaran et al., Citation2003). The authors observed that MnO2 as sintering aids promoted sintering kinetics by increasing the Al-diffusivity which is considered to be the rate controlling step in the sintering of Al2O3. The effects of MnO2 on the physical, mechanical and microstructural properties of alumina was also studied where it was observed that the positive effect of MnO2 addition on the hardness of alumina ceramics could be further enhanced with the increasing amount of MnO2 addition and sintering temperature (Cheng, Citation2011). The author also found that small quantities of MnO2 addition could lead to the enhancement of densification process. The grain growth would also be promoted by the addition of MnO2, cause the formation of intra-granular and inter-granular pores while only inter-granular pores is observed on the undoped alumina ceramics. Moreover, the author did not found any secondary phase formation and this shows that MnO2 is in solid solution of alumina. A colloidal technique during powder mixing process owing to the advantage of uniform distribution of the minor amounts of finer additive MnO2 to alumina ceramics was recommended (Toy, Demirci, Onurlu, Sadik Tasar, & Baykara, Citation1995).
In the present investigation, an attempt has been made to study the influence of Mn4+ in a mixture of 50:50 Nigerian kaolin and calcined alumina powder on mullite formation during heating at different temperatures. The densification behavior, strength development, phase and microstructural evolution were determined and discussed in this paper.
2. Materials and methods
Kaolinitic clay was collected at a location of latitude 7.08°N and longitude 3.27°E south-west Nigeria and it was processed to remove the grits as reported in earlier work (Ajanaku et al., Citation2016). High purity calcined alumina was obtained from ALCOA and chemical grade manganese di-oxide was procured from SD Fines and Chemicals. The chemical constituents present in the raw materials were determined by different techniques namely: volumetric method for SiO2 and Al2O3; complexometric method for CaO and MgO; spectrophotometry [LAMBDA-45, PerkinElmer, USA] for Fe2O3, TiO2; flame photometry [PFP-7, Jenway, UK] for Na2O and K2O and loss on ignition (LOI) by heating the samples up to 800°C gravimetrically.
Two batches were prepared using the above raw materials. The batch compositions are provided in Table . The batches, 250 gm of each were prepared by using the common ceramic processing technique such as wet mixing of raw materials in a pot mill, drying of slurry and powdering, granulation using 5–6% moisture. The bar samples (65 × 7 × 7 mm size) were fabricated in a hydraulic press [Carver Laboratory Press, 2698, India] at 400 kg/cm2. The compact bar samples were dried in air first and then in an electrically heated furnace at 100 ± 10°C till the moisture content reduced to less than 0.5 wt%. Then the dried samples were heated in an electrically operated furnace at temperature in the range of 1,400–1,600°C for a soaking period of 30 min. Standard method was applied to evaluate percent apparent porosity (%AP) and bulk density (BD) of the heated samples. Flexural strength of the samples were measured by universal testing machine (INSTRON 5500R, UK). The phase and microstructural analysis were performed using X-ray Diffraction [PAN analytical, ALMELO, X’Pert Pro MPD, Netherland], FESEM [Zeiss, Germany] and EDAX [Oxford, UK] technique. X-ray diffraction pattern of the powdered samples were recorded in the range of 10–80o in step-scan mode with step size 0.05° (2θ) and step time 75 s. For microstructural analysis of the vitrified samples, the samples were ground with SiC powder and then were polished with 6, 3 & 1 micron finish. The polished surface was chemically etched with 5% HF solution, washed with water and acetone followed by gold coating.
Table 1. Batch compositions
3. Results and discussions
The chemical analysis of the processed kaolin used in this study is given in Table .
Table 2. Chemical analysis of the processed kaolin (Ajanaku et al., Citation2016)
It was observed in our earlier study that the compact samples of this processed clay powder on heating in the temperature range of 1,400–1,600°C resulted almost densified and impervious product at 1,600°C. Silica together with impurity oxides (Fe2O3, TiO2) in the clay forms glassy phase in the above temperature range and that accompanying the formation of mullite (3Al2O3·2SiO2) crystals. Alumina content in the calcined alumina is >99.8 wt% and it is very fine with average particle size (d50) in the range of 6–8 μm. The assay content of MnO2 powder was found to be 80%. The oxide compositions of the prepared batches are provided in Table .
Table 3. Oxide composition of the batches
It may be seen that oxide constituents of both the batches are more or less same except SiO2 and Al2O3, which are slightly higher in LSK-1. MnO2 is specially added as dopant to LSK-2 batch in order to study the influence of Mn4+ ion on physico-mechanical properties and mullite formation in the mixture of kaolin and calcined alumina. It was observed that both the compositions shown negligible shrinkage in the entire heating range of 1,400–1,650°C and ultimately leads to poor densification and higher porosity. Table provided the variation in bulk density (BD), percent apparent porosity (%AP) and modulus of rupture (MOR) strength in relation to the heating temperatures.
Table 4. Physico-mechanical properties of the heated samples
It may be observed from the above table that the bulk density of LSK-2 samples is significantly dropped by the addition of 5 wt% MnO2 in the mixture of kaolin and calcined alumina. This might be due to the increasing amount of porosity in the kaolin and alumina mixture as the concentration of MnO2 addition is more than certain limit that could diminish its effect in enhancing the densification of the present experimental body. Cheng (Citation2011) in his study also found that addition of MnO2 from 0–1.5 wt% increased the relative density of the alumina ceramics. However, further addition of MnO2 up to 5 wt% caused the relative density of the alumina ceramics to drop to a certain level. Wet pot milling technique which was used during preparation of batches in the present study might have limitations when doping submicron particles. Toy et al. (Citation1995) suggested employing colloidal technique which allows a uniform distribution of minor amounts of MnO2 within the alumina ceramic. It is interesting to note that MnO2 doped sample (LSK-2) developed better strength (26 MPa) at 1,400°C compared to 7 MPa in undoped sample (LSK-1). This may be attributed to better bonding between the grains at lower temperature in presence of MnO2. On the other hand, it may be observed that at 1,650°C, LSK-1 (undoped) sample developed higher strength (38 MPa) compared to 27 MPa in MnO2 doped sample (LSK-2). These differences in strength development at 1,650°C will be better explained later while discussing microstructure evolution. Figure illustrates the XRD pattern of both 1,650°C heated samples. Both patterns look almost similar. The phases identified were mullite and corundum.
Figure 1. XRD pattern of LSK-1 and LSK-2 samples heated at 1,650°C temperature.
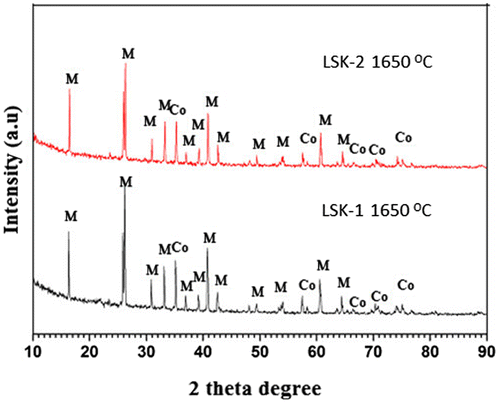
The microstructures of 1,650°C heated undoped sample (LSK-1) in different regions are shown in Figure along with the EDX analysis and it looks to be homogeneous with uniform grain growth. The structure is full of needle shaped mullite crystals embedded in glassy matrix and corundum grains all over.
The addition of MnO2 in LSK-2 body resulted in homogenous grain growth as observed in the different regions of the sample (Figure ). Few inter-granular and intra-granular pores could also be observed in the microstructures of the samples doped with MnO2. The lower strength in 1,650°C heated LSK-2 sample (27 MPa) compared to LSK-1 (38 MPa) is due to the presence of these pores. Larger size mullite needles with higher aspect ratio are seen in LSK-2 sample due to grain growth in presence of MnO2. Corundum crystals are also distributed in the matrix of LSK-2 sample.
A comparative study of the chemical analysis and oxide composition of the constituents were illustrated in Figure . This is done to adequately propose a model for understanding the transition metal ion participation in mullite formation. The active constituents as seen in Figure were SO2, Al2O3, K2O and Fe2O3. The thermal deactivation model that was derived by Benjamin, Reznik, Benjamin, and Williams (Citation2007) was adopted to understand the number of transition metal ion (N). The modified formula for this study becomes:(1)
(1)
where A1, B1, C1 and D1 are coefficients that describes the concentration of metal ion, kexp is the experimentally measured rate coefficient given by Su and Chesnavich (Citation1982) when they calculated the ion-polar molecule collision rate constant by parameterization. The value of the coefficient is determined by the polynomial curve-fit of the active constituents illustrated above. The processes for acquiring the coefficients are shown in Figure . The ranges of A1, B1, C1 and D1 are 23.8 to 25.1, −186 to −196.7, 423.6 to 446.7 and −232.3 to −245.5 respectively. Hence, the thermal model for the understanding of the influence of the transitional metal ion between 1,400–1,650°C is shown in Figure . The expected progression of the transition metal ion i.e. (LSK-1 and LSK-2) at varying temperatures is shown in Figure . Also, a case where the first coefficient of the first term of Equation (1) was considered to be dynamic was considered as shown in Figure . This assumption is to ascertain if the experimentally measured coefficient rate would shift. It was observed that it had no significant changes. Hence the theoretical and experimental value of >4 for MnO2 has been validated.
4. Conclusions
From the present study, it may be concluded that a compact of 50:50 Nigerian clay and calcined alumina powder resulted in porous samples when heated in the temperature range of 1,400–1,650°C. The doping of 5 wt% Mn4+ ion as MnO2 in this mixture did not improved densification, but increased the flexural strength at 1,400°C, while at 1,650°C, the strength dropped due to inhomogenous grain growth and generation of inter-granular and intra-granular pores. The XRD pattern and SEM photographs revealed the presence of well-developed needle shaped mullite and corundum crystals.
Funding
The authors received no direct funding for this research.
Acknowledgement
The authors appreciate the contributing institutions for the analysis and partial sponsorship of the research work.
Additional information
Notes on contributors
Olanrewaju Aladesuyi
Our research group focuses on finding solutions to solid waste environmental issues and development of appropriate technologies that will guide industrial implementation.
Aladesuyi Olanrewaju is a PhD candidate in Industrial Chemistry (Materials), Covenant University where he also lectures and researches.
Mousumi Pal
Mousumi Pal completed her PhD in Jadavpur University in 2016. Her research interest includes spectrophotometric studies on chemical compounds, solid waste utilization in ceramic composition and development of value added products for different applications.
Eterigho Moses Emetere
Eterigho Moses Emetere had his doctorate degree in Industrial Physics and very resourceful in modeling application.
Swapan Kumar Das
Swapan Kumar Das, is presently Guest Faculty, Ceramic Engineering, Department of Chemical Technology, Calcutta University, India. He obtained his PhD degree in Ceramic Engineering after completing his MTech Degree from Calcutta University.
Kolawole Oluseyi Ajanaku
Ajanaku Kolawole Oluseyi had his PhD degree in Industrial Chemistry. He is a Professor of Industrial Chemistry with specialization in the field of Materials.
References
- Ajanaku, K. O., Aladesuyi, O., Pal, M., & Das, S. K. (2016). Evaluation of Nigerian source of kaolin as a raw material for mullite synthesis. Oriental Journal of Chemistry, 32(3), 1571–1582. doi:10.13005/ojc/320333
- Aladesuyi, O., Pal, M., Das, S. K., & Ajanaku, K. O. (2017). Phase and microstructural evolution during sintering of mixture of 75:25 Nigerian kaolin and calcined alumina powder compacts. Journal of Materials and Environmental Sciences, 8(8), 2832–2839. Retrieved from https://www.jmaterenvironsci.com/Document/vol8/vol8_N8/282-JMES-2780-Aladesuyi.pdf
- Anilkumar, G. M., Mukundan, P., & Warrier, K. G. K. (1998). Low-temperature mullitization in boehmite-tetraethoxysilane gel precursor containing γ-alumina and mullite nucleating seeds. Chemistry of Materials, 10(8), 2217–2220. doi:10.1021/cm980149y
- Benjamin, E., Reznik, A., Benjamin, E., & Williams, A. L. (2007). Mathematical models for conventional and microwave thermal deactivation of Enterococcus faecalis, Staphylococcus aureus and Escherichia coli. Cellular and Molecular Biology, 53(3), 42–48. Retrieved from https://www.ncbi.nlm.nih.gov/pubmed/17531148
- Cheng, C. R. (2011). Effect of MnO2 on the physical, mechanical and microstructural properties of alumina (Unpublished Bachelor of Engineering Thesis, pp. 1–105). University of Tunku Abdul Rahman, Perak.
- Das, S. K. (1998). Ind. Pat. No. 180408. An improved process for manufacturing superior quality wear resistant ceramics.
- Das, S. K., Ray, K. C., Mitra, B. K., & Gupta, K. N. (1993). Alumina based ceramic compositions for wear resistant applications. Industrial Ceramics, 13(N ¾), 155–157.
- Das, S. K., Ray, K. C., Mitra, B. K., & Gupta, K. N. (1999). Ind. Pat. No. 182524. An improved process for the production of alumina based wear resistant ceramics.
- Gralik, G., Chinelattot, A. L., & Chinelatto, A. S. A. (2014). Effect of different sources of alumina on the microstructure and mechanical properties of the triaxial porcelain. Cerâmica, 60(356), 471–481. doi:10.1590/S0366-69132014000400004
- Mack, D. E., Becker, K. D., & Schneider, H. (2005). High-temperature M¨ossbauer study of Fe-substituted mullite. American Mineralogist, 90(7), 1078–1083.10.2138/am.2005.1689
- Risbud, S. H., & Pask, J. A. (1978). Mullite crystallization from SiO2-Al2O3 melts. Journal of the American Ceramic Society, 61(1-2), 63–67. doi:10.1111/j.1151-2916.1978.tb09232.x
- Schneider, H. (1990). Transition metal distribution in mullite. Ceramic Transactions, 6, 135–158.
- Schneider, H. (2005). Foreign cation incorporation in mullite. In H. Schneider & S. Komarneni (Eds.), Mullite (pp. 70–93). Weinheim: Wiley-VCH.10.1002/3527607358
- Schneider, H., & R. Vasudevan, (1989). Structural deformation of manganese substituted mullites: X-ray line broadening and lattice parameter studies. Neues Jahrbuch für Mineralogie Monatshefte, (4), 165–178.
- Su, T., & Chesnavich, W. J. (1982). Parametrization of the ion-polar molecule collision rate constant by trajectory calculations. Chemical Physics, 76, 5183. doi:10.1063/1.442828
- Toy, C., Demirci, M., Onurlu, S., Sadik Tasar, M., & Baykara, T. (1995). A colloidal method for manganese oxide addition to alumina powder and investigation of properties. Journal of Materials Science, 30(16), 4183–4187.10.1007/BF00360728
- Viswabaskaran, V., Gnanam, F. D., & Balasubramanian, M. (2003). Mullization behaviour of calcined clay – Alumina mixtures. Ceramics International, 29, 561–571. Retrieved from https://www.google.com.ng/url?sa=t&rct=j&q=&esrc=s&source=web&cd=1&cad=rja&uact=8&ved=0ahUKEwiwrY-43M7UAhWlKcAKHXNCDBsQFggkMAA&url=http%3A%2F%2Fvbceramics.com%2Fincludes%2Fpdf%2Fnews2.pdf&usg=AFQjCNFw3A-2SpIuT7Wi2QK72kp60tWCFg10.1016/S0272-8842(02)00203-1