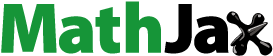
Abstract
Dimethyl carbonate (DMC) is an environmentally friendly molecule which can be produced from CO2 and methanol which was also productized by hydrogenation of CO2. The catalytic conversion of DMC into fuels and chemicals expands the repertoire of the renewable chemical industry as well as the utilization of CO2. In this paper we present a novel route for the conversion of DMC into aromatic hydrocarbons via catalytic pyrolysis. Molecular sieve HZSM-5 was found to give high catalytic activity and aromatics selectivity. Under optimized condition (400°C, N2 flow rate of 10 ml/min and Weight Hourly Space Velocity of 0.5 h−1), a yield of aromatic hydrocarbons of 21.76 wt% was observed. The catalyst also exhibited excellent reusability under optimized reaction conditions as it remained its initial activity after fifth cycle.
Public Interest Statement
This work propose an alternative way to produce aromatic hydrocarbons from dimethyl carbonate. Dimethyl carbonate is an environmentally friendly molecule which can be produced from CO2 and methanol which was also productized by hydrogenation of CO2. The catalytic conversion of dimethyl carbonate into fuels and chemicals expands the repertoire of the renewable chemical industry as well as the utilization of CO2. In this paper we present a novel route for the conversion of dimethyl carbonate into aromatic hydrocarbons via catalytic pyrolysis. Thus catalytic pyrolysis of dimethyl carbonate is doubtless a promising method for fuel additives and chemicals production and has a good potential to be developed into a commercial process.
1. Introduction
The growing consumption of fossil resources such as petroleum and natural gas has brought huge impact on the global climate and environment. In particular, the combustion of transportation fuels generated large amount of carbon dioxide (CO2), which is considered to be the largest contributor to the greenhouse effect. In order to eliminate the problems brought by CO2 emissions as well as to make good use of this large carbon source, a series of technologies for the conversion of CO2 into valuable chemicals were developed by researchers worldwide (Sakakura, Choi, & Yasuda, Citation2007; Wang & Cao, Citation2012). Among these technologies, the hydrogenation of CO2 to produce methanol is believed to be a promising route for the utilization of CO2 (Liu, Lu, & Yan, Citation2003).
Methanol, which is largely produced in petroleum industry, is an important bulk feedstock for organic chemical industry, and it is also considered as a green fuel alternative. As fossil resources are rapidly diminishing, the development for the production of methanol from sustainable carbon sources such as CO2 has attracted wide attention (Papavasiliou, Avgouropoulos, & Ioannides, Citation2012; Park, Jung, Um, Song, & Kim, Citation2012; Xu et al., Citation2005). Since the first report of the hydrogenation of CO2 into methanol using Cu–Al catalyst by Ipatieff and Monroe (Citation1945), many researchers started to focus their attention on the development of this reaction. Note that the toxicity of methanol limited the direct use of methanol as fuel alternative (Barceloux, Bond, Krenzelok, Cooper, & Allister Vale, Citation2000; McMartin, Ambre, & Tephly, Citation1998). In this respect, technologies for further conversion of methanol into high grade fuels are developed, among which the synthesis of dimethyl carbonate (DMC) from methanol and CO2 is a promising strategy (Fang & Fujimoto, Citation1996; Wang, Zhao, Wei, & Sun, Citation2005). DMC is an environmentally friendly compound which can be used as green solvent and gasoline additive (Pacheco & Marshall, Citation1997). DMC has excellent features as fuel additive, and it can replace the conventional gasoline additive methyl tert-butyl ether (MTBE) (Imura, Sugita, Noriyuki, & Ome, Citation1986). The synthesis of DMC using CO2 as carbon source has potential for the large scale production of sustainable fuel additives (Niu, Luo, Zhang, Xiao, & Lu, Citation2008). Nevertheless, DMC as sustainable fuel alternative is still limited by its low carbon chain length and low combustion heat. To increase the chain length of DMC is a strategy to improve the combustion performance. Richter et al. reported the transesterification of DMC and ethanol into diethyl carbonate catalyzed by solid acid catalyst (Zielinska-Nadolska, Warmuzinski, & Richter, Citation2006). Andrew et al. studied the acid-catalyzed transesterification of DMC with various aliphatic alcohols (Parrott et al., Citation2010). However, external aliphatic alcohols have to be used as feedstock using transesterification strategy.
Herein, we report a novel strategy for the conversion of CO2-derived DMC into aromatic hydrocarbons via catalytic pyrolysis. The advantage can be realized by applying catalytic pyrolysis for aromatic hydrocarbons production (Fukuda, Citation2015). Aromatic hydrocarbons can be directly used as transportation fuels and also can provide the basic feedstocks for the petrochemical industry (Bi et al., Citation2013; Carlson, Tompsett, Conner, & Huber, Citation2009; Fan et al., Citation2013; Zhang, Xiao, Jin, Xiao, & Chen, Citation2013; Zhang et al., Citation2016). In this process, aromatic hydrocarbons are produced by one-step pyrolysis of DMC as the single feedstock. The impact of catalyst and reaction conditions were investigated in detail and molecular sieve HZSM-5 was found to exhibit the highest activity and aromatics selectivity. The catalyst also exhibited excellent stability and reusability.
2. Experimental section
2.1. Materials
The typical properties of the catalysts were listed in Table . The catalysts were granulated and sieved to 20–40 mesh, calcinated at 600°C for 6 h and stored in desiccator after cooled down. ZSM-5 was provided by the catalyst plant of Nankai University. HZSM-5 was purchased from Fuxu zeolite Company in China. DMC and other reagents were purchased from Sinopharm Chemical Reagent Company (Shanghai, China). All the reagents were AR grade and directly used without further purification.
Table 1. Typical properties of the catalysts
2.2. Experimental setups and procedures
Pyrolysis of DMC was carried out in a tubular reactor (10 mm i.d.) made of quartz glass. 1.0 g catalyst was loaded in the heating zone with quartz wool before the reaction. During the pyrolysis process, DMC was continuously fed into the heating zone at a fixed rate by an autosampler and purged with nitrogen at a fixed flow rate. The liquid products were condensed and collected in a liquid nitrogen trap. The gas products were collected with a gasbag. For catalyst regeneration, air (100 ml/min) was used to remove the coke at 600°C.
The absolute mole of DMC was detected by GC with an error within ±2.07%. The absolute moles of most of liquid components such as benzene, toluene, o/p/m-xylene, naphthalene and 1-methylnaphthalene were determined by the calibrated GC–MS peak area with the standard samples (error within ± 1.88%). For solid product analysis, the solid residues after each experiment were immediately removed from the heating zone and cooled to room temperature in N2 flow. The solid residue in each experiment was weighed (±2.15%). The DMC conversion (Equation Equation(2.1)(2.1)
(2.1) ), overall percentage of quality of the gas, solid aromatic and oxygenates products, percentage of mass (Yield (wt%)) of a specific product, and aromatic selectivity (S (wt%)) were calculated based on Equations Equation(2.2)
(2.2)
(2.2) Equation(2.3)
(2.3)
(2.3) Equation(2.4)
(2.4)
(2.4) –Equation(2.5)
(2.5)
(2.5) .
(2.1)
(2.1)
(2.2)
(2.2)
(2.3)
(2.3)
(2.4)
(2.4)
(2.5)
(2.5)
2.3. Analytical determination
Nitrogen adsorption/desorption isotherms was measured by a Micromeritics ASAP 2020 analyzer. The surface area was determined using Barrett-Emmet-Taller (BET) method.
The concentration of DMC was detected by GC using external standard method. Which was equipped a flame-ionization detector and a nitrogen as carrier gas.
Liquid samples were analyzed by a GC–MS (Thermo Trace GC Ultra with a PolarisQ ion trap mass spectrometer) equipped with a TR-35MS capillary column (30 m × 0.25 mm × 25 um). Helium gas was used as the carrier gas. The initial oven temperature was 40°C and was kept constant for 5 min, then to 290°C at the rate of 10°C /min and hold for 10 min. The product peaks in the chromatograms were identified from the data of NIST MS library search.
3. Results and discussion
3.1. Theoretical analysis of catalytic pyrolysis of dimethyl carbonate
During the reaction, DMC molecules entered the catalysts pores and were converted into aromatic hydrocarbons, carbon monoxide, carbon dioxide, water, and coke. The challenge for the selective production of aromatic hydrocarbons was to minimize the formation of gas and coke. The overall stoichiometry for the conversion of dimethyl carbonate into toluene, CO, and H2O was shown in Equation Equation(3.1)(3.1)
(3.1) (Carlson, Vispute, & Huber, Citation2008). The maximum theoretical quality yield of toluene from DMC was 25.45% Equation(3.2)
(3.2)
(3.2) , when CO and H2O were produced as by-products.
(3.1)
(3.1)
(3.2)
(3.2)
Chen and co-workers (Citation1986) have defined the effective hydrogen-to-carbon ratio (H/Ceff) as shown in Equation Equation(3.3)(3.3)
(3.3) . (H, C, and O correspond to the number of atoms of hydrogen, carbon, and oxygen, respectively).
(3.3)
(3.3)
The H/Ceff ratio of petroleum-derived feeds ranges from slightly over 2 (for liquid alkanes) to 1 (for benzene). The H/Ceff ratio of DMC (C3H6O3) was H/Ceff = 0 < 1. The H/Ceff ratio of toluene (C7H8) was H/Ceff = 8/7 > 1. In this respect, the catalytic pyrolysis of DMC into aromatic hydrocarbons dramatically upgrades its performance for the use of fuels.
3.2. Catalytic pyrolysis of DMC using different catalysts at different temperatures
HZSM-5 with a Si/Al ratio of 25 was firstly examined for the catalytic pyrolysis of DMC. The conversion and yield data of the reaction at various pyrolysis temperatures (Table ). The water content of the liquid product was determined using Karl-Fischer method. As shown in Table , the conversions of DMC at temperature range from 350 to 600°C were all nearly complete catalyzed by HZSM-5(25). At elevated temperatures, the yield of gas and coke raised, and the yield of aromatics raised firstly and then dropped down (Ates, Tophanecioglu, & Putun, Citation2015). At lower temperatures such as 350 or 400°C, no coke was produced, and a highest aromatics mass yield of 10.5 wt% was observed at 400°C.
Table 2. The results of catalytic pyrolysis DMC with different catalysts and temperature
Pyrolysis of DMC using ZSM-5 and HZSM-5 with Si/Al ratio of 50 and 63 as catalyst was also conducted. As listed in Table , similar results as HZSM-5(25) were observed, indicating that these catalysts were all able to catalyze the pyrolysis of DMC into aromatics. The yields of coke were almost lower than 3.53%, which was due to the high oxygen content in DMC (53 wt% oxygen content). Generally, the yield of aromatics decreased as temperature rose when used HZSM-5(25), HZSM-5(50) and ZSM-5 as catalyst (Table ). But, there is no clear trend in HZSM-5(65) as catalyst. A highest yield of 13.83 wt% of aromatics could be achieved using HZSM-5(50) as catalyst at 350°C. The yield of gas product ranged from 69.50% to 81.87%, and the main gas products were determined to be CO, CO2 and CH4. The high yield of gas product may also be attributed to the high oxygen content of DMC, as oxygen tends to bond with carbon to produce stable CO and CO2 molecule during the pyrolysis process.
3.3. Product distribution of the catalytic pyrolysis of DMC with different catalyst
The aromatic hydrocarbons are the target product in the pyrolysis process. The product distribution of the liquid product was determined by GC–MS, and the data were listed in Table . Due to the high oxygen content in DMC, large amount of water (53.21–81.51 wt% of liquid product) was generated in the pyrolysis process. For the organic product, five kind of main product was determined to be benzene, toluene, xylene, trimethylbenzene and naphtal. With a rise of pyrolysis temperature, the selectivity of toluene decreased while the selectivity of xylene and trimethylbenzene increased. Among these catalysts that they used, the most promising results in relation to organic distillate fraction, aromatic formation were obtained with HZSM-5 catalyst (Jamil, Ahmad, Yusup, & Abdullah, Citation2016). It is noted that the highest selectivity of toluene and xylene was observed with HZSM-5(25) as catalyst at 400°C.
Table 3. Product distribution of the catalytic pyrolysis of DMC with different catalyst
The data in Table suggested that shape-selective catalysis played an essential role in the catalytic pyrolysis of DMC. All the DMC vapors formed during the pyrolysis can be adsorbed on the catalyst surface, and have to diffuse into the pores for catalytic reforming. HZSM-5 and ZSM-5 have the same pore structures, but different numbers of acid sites. ZSM-5 contains Brønsted acid sites (Carlson et al., Citation2008). Compared with HZSM-5 catalysts, ZSM-5 showed much lower selectivity for benzene, toluene and xylene. This could be explained that HZSM-5 has similar average pore size but much stronger acidity than ZSM-5. As reported in literature Carlson et al. (Citation2009), higher Si/Al ratio leads to stronger Lewis acidity and is beneficial for the ring formation during the pyrolysis process, therefore leading to higher carbon yield of the aromatic products. It is also proved by the results listed in Table as the selectivity of aromatics dropped down dramatically as the Si/Al ratio of the catalysts increased. So, a toluene selectivity of 13.08% (entry 2, Table ) was observed, which was significantly higher than other catalysts. Table shows the selectivity of liquid products from catalytic pyrolysis of DMC with various catalysts. In the presence of HZSM-5(25), the major products were benzene, toluene and xylene.
3.4. Influence of process conditions on catalyst pyrolysis of DMC
The influence of gas flow rate and space velocity was also investigated catalyzed by HZSM-5(25) under 400°C. The flow rate of carrier gas nitrogen varied from 5 ml/min to 40 ml/min, and the weight hourly space velocity (WHSV) ranged from 0.25 to 1.0 h−1. The results were listed in Table . For all the experiments, the conversion of DMC was all nearly complete. As WHSV increased, the carbon yield of aromatic hydrocarbons increased at first to reach a maximum value of 18.23% and then decreased. While the yield of coke decreased with increasing WHSV, indicating shorter residence time would help to reduce the formation of coke. The minimum selectivity of gas product was also observed at WHSV of 0.5 h−1. Therefore, a WHSV of 0.5 h−1 is chosen to be the optimal WHSV value. The influence of WHSV could be explained that higher WHSV leads to higher DMC concentration in the reaction system, therefore the catalytic activity is higher. However, when the active site of the catalyst is saturated, further increase of WHSV would led to the incomplete reaction of intermediates, therefore the selectivity of aromatics decreases while the gas product increases.
Table 4. Product distribution with different reaction condition
The flow rate of N2 is also an important factor for the yield of aromatics. Generally, lower flow rate gave higher aromatic yield, but the coke formation also increased. The lower N2 flow rate would extend the residence time of DMC in the catalyst zone therefore increased the probability of the formation of aromatic ring and at the same time the carbonation of DMC to form coke. It should be noted that under the lowest N2 flow rate of 5 ml/min, the aromatic yield dramatically dropped compared with that under 10 ml/min of N2 flow. This phenomenon was due to the formation of coke and gas product with extended residence time. Using the optimized WHSV of 0.5 h−1 and N2 flow rate of 10 ml/min, the highest aromatic selectivity of 21.76% was achieved. The gas product was also collected and analyzed by GC, and the results showed the main component was CO and CO2, mixed with small amount of H2 and CH4.
3.5. Catalyst recycle and regeneration test
HZSM-5(25) recycle and regeneration test was carried out at 400°C with N2 flow at 10 ml/min and at a WHSV of 0.5 h−1. After the pyrolysis experiment, a certain amount of coke was formed on the surface of the catalyst. However, purging air into the reactor could burn the coke and therefore reactivate the catalyst.
As shown in Table , the yield of aromatic hydrocarbons decreased from 21.76 to 21.26% after one cycle run, but the catalytic activity almost remained the same in the following runs. The change in the yield of coke was not obvious, while the yield of gas increased from 41.52 to 43.56% after the first run. The selectivity for benzene, toluene and xylene varied slightly in the five runs, whereas the selectivity of naphtal increased from 5.69 to 11.42%. In the process of catalyst regeneration, the catalyst pores may become larger, resulting in a higher yield of naphthalene. The overall result suggest that HZSM-5(25) was a stable catalyst for the pyrolysis reaction of DMC into aromatic hydrocarbons.
Table 5. Products distributions at 400°C in recycle catalytic runs
4. Conclusion
In summary, a novel strategy for the conversion of CO2-derived DMC into aromatic hydrocarbons via catalytic pyrolysis was developed. The molecular sieve HZSM-5(25) catalyst exhibited the highest activity for the formation of aromatics, and a highest aromatics selectivity of 21.76% was observed under optimal conditions. The influence of temperature, flow rate of carrier gas and WHSV was investigated. Under optimal conditions, the catalyst HZSM-5(25) could be easily reactivated and reused without loss of activity in five runs. This catalytic pyrolysis method presents a new strategy for the utilization of CO2 as well as the production of renewable gasoline alternatives.
Funding
The authors are grateful for the financial Supported by China Postdoctoral Science Foundation [grant number 2017M621989], Anhui Province Postdoctoral Science Foundation [grant number 2017B216], the Research Fund Anhui University of Science and Technology [grant number ZY534], Science and Technology Project of Anhui Province [grant number 1604a0802122].
Additional information
Notes on contributors
Yan Zhao
Yan Zhao obtained his PhD degree from the Department of Chemistry at the University of Science and Technology of China (USTC) in 2014. He then began her academic career at the School of Materials Science and Engineering, Anhui University of Science and Technology. His research interests cover conversion of biomass or the compounds from biomass into value-added chemicals and liquid fuels via catalytic pyrolysis, and the synthesis of heterogeneous catalysts for green chemistry processes.
References
- Ates, F., Tophanecioglu, S., & Putun, A. E. (2015). The evaluation of mesoporous materials as catalyst in fast pyrolysis of wheat straw. International Journal of Green Energy, 12, 57–64.10.1080/15435075.2014.889005
- Barceloux, D. G., Bond, G. R., Krenzelok, E. P., Cooper, H., & Allister Vale, J. (2000). American academy of clinical tox icology practice guidelines on the treatment of methanol poisoning. Journal of Toxicology: Clinical Toxicology, 40, 415–446.
- Bi, P. Y., Yuan, Y. N., Fan, M. H., Jiang, P. W., Zhai, Q., & Li, Q. X. (2013). Production of aromatics through current-enhanced catalytic conversion of bio-oil tar. Bioresource Technology, 136, 222–229.10.1016/j.biortech.2013.02.100
- Carlson, T. R., Tompsett, G. A., Conner, W. C., & Huber, G. W. (2009). Aromatic production from catalytic fast pyrolysis of biomass-derived feedstocks. Topics in Catalysis, 52, 241–252.10.1007/s11244-008-9160-6
- Carlson, T. R., Vispute, T. P., & Huber, G. W. (2008). Green gasoline by catalytic fast pyrolysis of solid biomass derived compounds. Chemsuschem, 1, 397–400.10.1002/(ISSN)1864-564X
- Chen, N. Y., Degnan, T. F., Jr, & Koenig, L. R. (1986). Liquid fuel from carbohydrates. ChemTech, 16, 506–511.
- Fan, M., Jiang, P., Bi, P., Deng, S. M., Yan, L. F., Zhai, Q., … Li, Q. X. (2013). Directional synthesis of ethylbenzene through catalytic transformation of lignin. Bioresource Technology, 143, 59–67.10.1016/j.biortech.2013.05.097
- Fang, S., & Fujimoto, K. (1996). Direct synthesis of dimethyl carbonate from carbon dioxide and methanol catalyzed by base. Applied Catalysis A: General, 142, L1–L3.10.1016/0926-860X(96)00081-6
- Fukuda, S. (2015). Pyrolysis investigation for bio-oil production from various biomass feedstocks in Thailand. International Journal of Green Energy, 12, 215–224.10.1080/15435075.2014.891519
- Imura,R., Sugita, Y., Noriyuki, T., Ome, K. (1986). Control method of magnetic anisotropy and device utilizing the control method. Patent US 4600488.
- Ipatieff, V. N., & Monroe, G. S. (1945). Synthesis of methanol from carbon dioxide and hydrogen over copper-alumina catalysts. Mechanism of reaction. Journal of the American Chemical Society, 67(12), 2168–2171.10.1021/ja01228a032
- Jamil, F., Ahmad, M. M., Yusup, S., & Abdullah, B. (2016). Upgrading of bio-oil from palm kernel shell by catalytic cracking in the presence of HZSM-5. International Journal of Green Energy, 13, 424–429.10.1080/15435075.2014.966370
- Liu, X. M., Lu, G. Q., & Yan, Z. F. (2003). Recent advances in catalysts for methanol synthesis via hydrogenation of CO and CO2. Industrial & Engineering Chemistry Research, 42, 6518–6530.10.1021/ie020979s
- McMartin, K. E., Ambre, J. J., & Tephly, T. R. (1998). Methanol poisoning in human subjects. Role for formic acid accumulation in the metabolic acidosis. The American Journal of Medicine, 68, 414–418.
- Niu, D. F., Luo, Y. W., Zhang, L., Xiao, L. P., & Lu, J. X. (2008). Electrosynthesis of dimethyl carbonate from CO2 in mild condition. Chinese Journal of Organic Chemistry, 28, 832–836.
- Pacheco, M. A., & Marshall, C. L. (1997). Review of dimethyl carbonate (DMC) manufacture and its characteristics as a fuel additive. Energy & Fuels, 11, 2–29.10.1021/ef9600974
- Papavasiliou, J., Avgouropoulos, G., & Ioannides, T. (2012). CuMnOx catalysts for internal reforming methanol fuel cells: Application aspects. International Journal of Hydrogen Energy., 37(21), 16739–16747.10.1016/j.ijhydene.2012.02.124
- Park, S. H., Jung, H. M., Um, S., Song, Y. W., & Kim, H. S. (2012). Rapid synthesis of Pt-based alloy/carbon nanotube catalysts for a direct methanol fuel cell using flash light irradiation. International Journal of Hydrogen Energy, 37, 12597–12604.10.1016/j.ijhydene.2012.06.004
- Parrott, A. J., Bourne, R. A., Gooden, P. N., Han, S. B., Martyn, P., & Derek, J. I. (2010). The continuous acid-catalysed etherification of aliphatic alcohols using stoichiometric quantities of dialkyl carbonates. Organic Process Research & Development, 14, 1420–1426.10.1021/op1002243
- Sakakura, T., Choi, J. C., & Yasuda, H. (2007). Transformation of carbon dioxide. Chemical Reviews, 107, 2365–2387.10.1021/cr068357u
- Wang, M., Zhao, N., Wei, W., & Sun, Y. H. (2005). Synthesis of dimethyl carbonate from urea and methanol over ZnO. Industrial & Engineering Chemistry Research, 44(19), 7596–7599.10.1021/ie0504553
- Wang, W. J., & Cao, Y. Y. (2012). Combined carbon dioxide reforming with steam reforming of ethanol for hydrogen production: Thermodynamic analysis. International Journal of Green Energy, 9, 503–516.10.1080/15435075.2011.622024
- Xu, A., Indala, S., Hertwig, T. A., Pike, R. W., Knopf, F. C., Yaws, C. L., & Hopper, J. R. (2005). Development and integration of new processes consuming carbon dioxide in multi-plant chemical production complexes. Clean Technologies and Environmental Policy, 7, 97–115.10.1007/s10098-004-0270-y
- Zhang, H., Xiao, R., Jin, B., Xiao, G. M., & Chen, R. (2013). Biomass catalytic pyrolysis to produce olefins and aromatics with a physically mixed catalyst. Bioresource Technology, 140, 256–262.
- Zhang, Q., Wang, T., Tan, J., Zhang, Q., Li, Y., & Ma, L. (2016). Catalytic conversion of biomass-derived sorbitol to aromatic compounds. International Journal of Green Energy, 13, 767–773.10.1080/15435075.2016.1161627
- Zielinska-Nadolska, I., Warmuzinski, K., & Richter, J. (2006). Zeolite and other heterogeneous catalysts for the transesterification reaction of dimethyl carbonate with ethanol. Catalysis Today, 114, 226–230.10.1016/j.cattod.2006.01.001