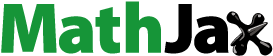
Abstract
High-speed turbomachinery applications demand a highly stable spindle support system with a need for hydrodynamic bearings with better performance and stability characteristics. The multipad adjustable bearing geometry proposed in this study offers a unique attribute of altering the film thickness in the bearing clearances. The adjustability principle is applied to the four circumferentially spaced bearing pads or elements to translate in radial and tilt directions. The proposed bearing design provides an efficient alternative in the field of active journal bearings. This paper presents a geometrical approach employed in formulating a theoretical equation for film thickness variation under different pad adjustments. The mathematical relation for film thickness is derived using certain trigonometric relations by considering both the radial and tilt adjustment parameters. The present approach provides an accurate approximation of circumferential film thickness variation for an adjustable bearing in comparison with other film thickness models.
PUBLIC INTEREST STATEMENT
In turbomachinery and machine tool applications, there is always a necessity for developing fluid film bearings with high-performance capabilities. The bearing design with adjustable elements proposed in this study overcomes the limitations exhibited in different variants of bearing designs developed over the years. In the field of tribology of bearings, a variation of lubricant thickness in plain journal bearings is widely studied. A limited amount of research has been carried out in determining the lubricant film profile in pad bearings subjected to certain adjustment conditions. The proposed bearing is self-controllable during the operation with certain modifications. A geometrical approach is presented in this paper to develop a modified film thickness equation incorporating the different adjustments applied to the bearing pads. The approach used in this study is better than those of other studies and therefore the lubricant film profile predicted, provides an accurate estimate of the actual film profile.
1. Introduction
Fluid film bearing geometries are often modified to provide optimum performance for different turbomachinery applications. The performance of such bearings is enhanced over the years, by constantly redesigning to maintain a stable spindle support system. Currently, an extensive range of journal bearing designs is available with the fixed sleeve as well as tilting pad configurations. All the existing bearings have exhibited a correlation of being responsive to bearing operating conditions. This led to the development of alternative bearing designs with adjustable geometries.
An adjustable pad bearing arrangement was initially designed and developed to facilitate a controlled hydrodynamic operation (U.S. Patent No. 5,772,334, 1998). Two forms of bearing designs were proposed, a conventional form of hydrodynamic bearing and a bearing rotor system with inverse orientations. One embodiment of the invention was made of a fixed central shaft with adjustable cantilevered bearing segments. The fixed inner stator consisted of hydrostatic pockets, which separate the adjustable hydrodynamic segments individually controlled by tapered pins. Martin (Citation1999) mathematically modeled one form of an adjustable bearing with inverse orientations. Finite element (FE) models of bearing segments were developed with displacements applied on the nodes adjacent to the tapered pin positions. Finite-difference approximations of pressure, film thickness, viscosity, and temperature models developed interacted with the FE models. Convergent solutions were obtained for the above parameters by applying an iterative computational process. An expanded form of governing Reynolds equation was derived by taking consideration of non-uniform variations in lubricant film profile (Martin, Citation2002). Martin and Parkins (Citation2002) later studied the theoretical performance of bearing with inverse orientation under symmetrical and asymmetrical pad adjustment configurations. The influence of variable load magnitudes and directions on rotor attitude angle, eccentricities, static loci, displacement and velocity coefficients were analyzed in detail. Experimental tests were also conducted on two forms of adjustable bearings in a marine gearbox test rig (Martin & Parkins, Citation2001). The experimental results obtained for different operating conditions hold good agreement with the theoretical results.
A novel experimental test setup was later built for testing the adjustable bearings with inverse orientations. A measurement technique was devised for deriving the oil film displacement coefficients with loading applied using electromagnets and for subsequent changes in rotor position (Martin, Citation2004a, Citation2004b). Martin (Citation2008) has outlined the various strands of research carried out in the field of adjustable bearings and discussed their potential attributes (Martin, Citation2011).
Shenoy (Citation2008) evaluated the theoretical performance characteristics of a single-pad adjustable bearing. The bearing element had a unique ability to incorporate radial and tilt adjustments which entitles a control over radial clearance and film thickness developed. Steady-state performance characteristics of the bearing were studied operating under laminar and turbulent flow regimes. Linearized turbulent lubrication model of Ng and Pan was incorporated into Reynolds equation and solved by finite-difference approximation (Shenoy & Pai, Citation2008, Citation2009a). Further studies were also carried out by operating under unidirectional and offset load conditions (Shenoy & Pai, Citation2009b). Based on the investigations of the effect of pad displacements on bearing performance characteristics under journal misaligned conditions, superior results were observed for bearing operated under negative pad orientations (Shenoy & Pai, Citation2009c, Citation2009d).
Dynamic characteristics of a single-pad rotor bearing system were later analyzed by employing a linearized perturbation technique to determine the dynamic coefficients of the bearing. An improvement in bearing stiffness and damping coefficients were observed under negative pad adjustments. These adjustments also help in improving the bearing stability under turbulent flow conditions (Shenoy & Pai, Citation2010, Citation2011a). Influence of couple stress fluids and nanoparticle additives on the bearing performance characteristics were also analyzed in detail in further studies (Shenoy, Binu, Pai, Rao, & Pai, Citation2012; Shenoy & Pai, Citation2011b).
Extensive research has also been performed in the field of active journal bearings. Krodkiewski, Cen, and Sun (Citation1997) presented a mathematical modeling technique for a rotor bearing system incorporated with active journal bearings. The proposed bearing consists of a deformable flexible sleeve activated by controlling the chamber pressures using servo valves in the hydraulic system. This resulted in eliminating the self-excited vibrations generated and thereby improving the stability of rotor bearing system. Later, the studies were extended onto a multi-bearing rotor system with simulations carried out by employing both linearized and nonlinear models (Krodkiewski & Sun, Citation1998). The critical speeds, instability thresholds, and vibration responses were predicted using linearized approach, and the results were verified using nonlinear models. Sun and Krodkiewski (Citation2000) experimentally verified the mathematical modeling technique and showed reasonable agreement both qualitatively and quantitatively. Significant improvement of system stability was attained by maintaining appropriate chamber pressures.
Chasalevris and Dohnal (Citation2012) described a variable geometry journal bearing capable of quenching its effective stiffness and damping properties by incorporating an additional fluid film thickness. The proposed bearing consists of an adaptable bearing part designed to undergo displacement during passage through resonance. They focused on suppressing the vibration amplitudes under critical speed conditions in both horizontal and vertical directions. Simulations were later performed on a medium speed rotor bearing system and attained a 50% reduction in the maximum stresses developed under resonance conditions (Chasalevris & Dohnal, Citation2014).
Later, Chasalevris & Dohnal (Citation2015) developed an experimental prototype variable geometry bearing and determined their dynamic responses of the system. A detailed outline of the design and application of the proposed bearing on a real rotor bearing system was also presented. The operating principles were further extended onto partial arc bearings with adjustable geometry, where bearing segments are actuated by employing piezoelectric actuators. The proposed bearing design was implemented on industrial turbines, where enhanced stability margins were observed at high rotational speeds (Chasalevris & Dohnal, Citation2016).
The objective of this study is to mathematically formulate the film thickness in a multipad externally adjustable fluid film bearing. Four adjustable bearing segments circumferentially arranged with a pad angle of 48° as shown in Figure is considered for the analysis. These bearing segments are configured to have both radial and tilt adjustments as in Figure . In this paper the modified film thickness equation is derived theoretically incorporating symmetrical pad adjustments. The film thickness equation developed can be applicable to the multiple numbers of pads present in the bearing and provides an accurate approximation of the film thickness gradient in the bearing clearances.
Figure 1. Schematic representation of four-pad adjustable bearing (Source: United States Patent and Trademark Office, www.uspto.gov, U.S. Patent No. 5,772,334, Citation1998): (1) bearing casing, (2) adjustable pad, (3) tilting spacer, and (4) radial displacement spacer.
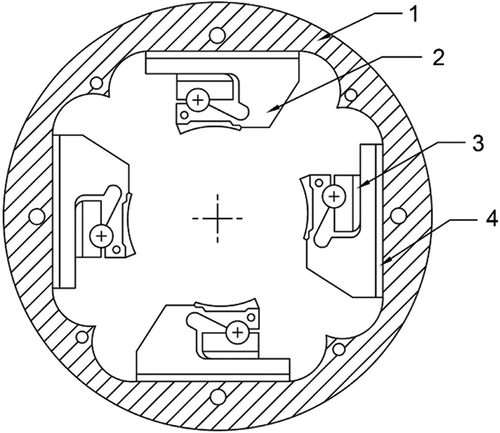
The present study can be further extended in determining the theoretical performance characteristics of a four-pad externally adjustable bearing by employing the modified film thickness equation defined in this paper. The static characteristics such as load capacity, attitude angle, friction variable, side leakage and Sommerfeld number can be evaluated for different pad adjustments. The theoretical steady-state analysis can be validated with the experimental results of Pai and Parkins (Citation2018) for a four-pad adjustable bearing with a pad angle of 48°.
2. Background and existing film thickness models
The film thickness gradients developed in different forms of adjustable bearings have been investigated by many researchers over the years. An adjustable bearing concept with inverse orientations mathematically modeled by Martin (Citation1999) developed a film thickness equation for determining the lubricant film profile under rotor displacement and different segment adjustment conditions (Martin & Parkins, Citation2002). The equation was generalized for all the four segments in consideration with rotor offset position. Trigonometric relations were applied in deducing the equation with respect to the rotor geometry and adjustable segments on the stator.
For an alternate form of adjustable bearing with a single adjustable pad, Shenoy (Citation2008) determined the variation of fluid film thickness by superimposing the radial and tilt displacements of the bearing element on a conventional film thickness equation. This principle was adopted based on the superimposition of ramp depth of a tri taper bearing as described in Hargreaves (Citation2016). Dimensionless film thickness equation developed by Shenoy (Citation2008) by considering a straight-line approximation of the pad angle under different adjustments is given as follows:
3. Model description and solution technique
3.1. Adjustability principle of multipad bearing
In the present study, a four-pad externally adjustable bearing configuration with L/D ratio of 0.53 is considered, as shown in Figure . The bearing geometry consists of four bearing pads with an angle of 48° circumferentially spaced and capable of translating in radial and tilt directions. These pad adjustments act as an effective means to control the bearing radial clearance and circumferential film thickness gradient. Figure illustrates the bearing pad adjustment configuration, where symmetrical adjustments will be provided to the remaining pads under different operating conditions.
Under negative radial adjustment, the bearing pads are displaced to move inward and thereby reducing the radial clearance spaces. However, an increment in radial clearance is observed under positive pad adjustments. Tilt angles are provided to the leading edges of the pad by maintaining zero tilt at the trailing end. An inward tilt movement can be observed under negative tilt adjustments and vice versa with positive tilt configurations. A non-uniform variation in fluid film profile can be noticed under different positive and negative tilt displacements.
3.2. Formulation of modified film thickness equation
Figure demonstrates the mathematical approach utilized for deriving a modified film thickness equation incorporating different radial and tilt adjustments. Nonlinear variation in lubricant film profile under varied pad adjustments need to be determined. Pad clearance (Cp = ± 0.3C) can undergo variation in both positive and negative directions. The pad radius (Rp ) along with clearance parameter (Cp ) facilitates the radial adjustment of pads:
Figure 3. Representation of the mathematical approach applied to develop modified film thickness: (1) profile of multipad bearing, (2) negative radial adjustment, (3) positive radial adjustment, and (4) positive tilt adjustment.
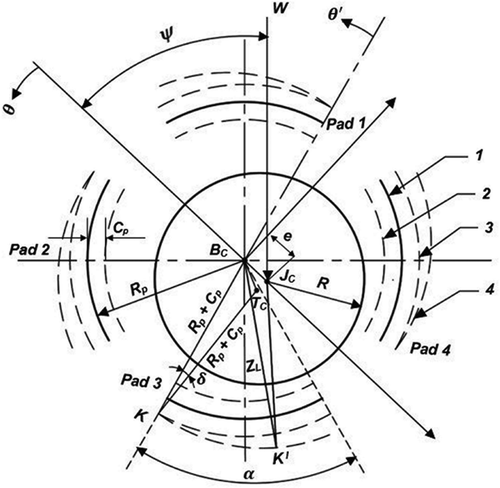
The leading edges of four pads are subjected to tilt displacement resulting in a non-uniform bearing configuration. Trigonometric relations are applied to model the tilt orientations of bearing elements as shown in Figure . The tilt angle provided is considered with respect to the bearing center and tilted pad center position
. The radial distance of the tilted pad about the bearing center varies along the pad curvature and is measured using Equation (4). The non-dimensional modified film thickness equation developed by incorporating the radial adjustments and tilt angles in either positive or negative directions is given as follows:
where α is the pad angle
4. Theory
The generalized Reynolds equation governs the pressure variation in the bearing clearance spaces. By applying some basic assumptions of lubrication theory, governing Reynolds equation in two dimensions for an incompressible lubricant can be derived (Majumdar, Pai, & Hargreaves, Citation2004). Controlled hydrodynamic operation can be modeled by incorporating the adjustable bearing parameters present in the modified film thickness equation into the Reynolds equation:
For steady-state conditions, the time dependent term in Equation (6) is neglected. The governing Reynolds equation is later non-dimensionalized and can be written as
5. Pressure boundary conditions
In this analysis, pressure variation across the fluid film is neglected. Pressures along the bearing edges is set to zero as an initial condition and is represented as
Negative pressures generated in the bearing clearances is defined to be equal to zero throughout the iterative solution method, which allows the cavitation to occur at ambient pressures in the bearing clearances:
6. Computational technique
The non-dimensional governing Reynolds equation is discretized using second-order finite-difference approximation technique. A computer program is developed using MATLAB R2016b to determine the pressure distribution and variation of circumferential fluid film thickness under different pad orientations. An arbitrary value of attitude angle (ѱ) is assumed beforehand with respect to the bearing vertical position. Equation (7) is solved for pressure variation by applying Reynolds boundary conditions. To attain attitude angle convergence, pressure convergence criteria must be satisfied initially. Gauss Seidel iterative method with successive over relaxation scheme is applied to attain converged pressure values. The iterative method will be repeated until the following pressure convergence criterion is satisfied:
The load capacity of bearing along its line of centers and perpendicular directions are determined from the following force components as defined in Majumdar et al. (Citation2004):
Resultant force acting on the journal
The calculated attitude angle is given as
Calculated attitude angle (ϕ) will be determined from the radial and transverse force components obtained by utilizing the converged bearing pressure values. After each iteration, the assumed attitude angle (ѱ) is compared with calculated value ϕ and further modified with a small increment of Δѱ. The iteration process is continued until attitude angle converges with a tolerance value of 0.001. This convergence technique helps to provide a better approximation of film thickness variation in pad clearances and determine the steady-state characteristics of the adjustable bearing.
7. Validation
The fluid film variation in a 120° single-pad adjustable bearing was initially predicted by Shenoy (Citation2008) applying the superimposed film thickness equation mentioned in Equation (1). The modified film thickness equation developed in the present study can also simulate the fluid film profile for the single-pad bearing under different pad adjustments, and their comparison plots with the results of Shenoy (Citation2008) are detailed in Figure . The bearing pad is radially displaced up to ± 25% of the bearing clearance and applied with a tilt angle of ± 0.0061° at the leading edge of the bearing pad. Larger film thickness values are attained under positive pad adjustment conditions due to the additional bearing clearance spaces developed. Based on the comparison plots, film thickness profile observed over single-pad adjustable bearing by applying the present approach shows good agreement with the variation demonstrated by Shenoy (Citation2008). This assessment validates the modified film thickness equation developed in the present study.
Figure 5. Comparison of dimensionless film thickness variation on a 120° single-pad adjustable bearing for ε = 0.4. (a) Variation presented by Shenoy (Citation2008) and (b) present analysis results.
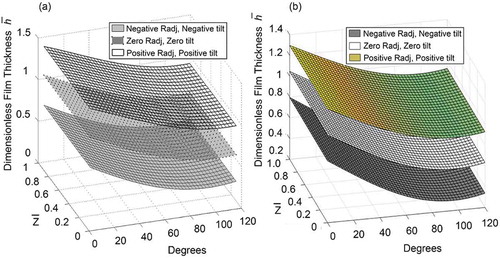
8. Results and discussions
Based on the comparison plots presented in Figure , lubricant film thickness values recorded over the pad area for a single-pad bearing under different pad adjustments are detailed in Table . The variation in fluid film zone determined by Shenoy (Citation2008) for a single-pad bearing is based on applying a film thickness equation derived by considering straight line approximation of the pad angle. In the present study, trigonometric relations are applied to develop a modified film thickness equation as defined in Equation (5), to accurately predict the fluid film profile under different pad orientations. The bearing pad is radially displaced in either direction and tilted along the leading edge of the pad.
Table 1. Comparison of dimensionless film thickness variation observed in Shenoy (Citation2008) and present analysis for a 120° single-pad bearing under ε = 0.4
Lower film thickness values are observed under negative pad adjustments due to the reduction in bearing clearances. Under pad tilt condition, maximum tilt is attained at the leading edge of the pad with trailing end of the pad prevailing in no-tilt condition. Based on the comparative analysis presented in Table , film thickness generated near the trailing end of the pad is found to be approximately constant for different tilt adjustments by applying the modified film thickness equation developed in the present study. Whereas, the film thickness predicted by Shenoy (Citation2008) near the trailing end shows inappropriate variation under different tilt angles. The results obtained using present approach hold true to the practical conditions and provide an accurate prediction for bearing with adjustable elements in comparison with the theoretical approach presented by Shenoy (Citation2008).
The present study is further extended to multipad adjustable bearing with four bearing pads subjected to symmetrical pad adjustments. The variation in fluid film zone is recorded for radial displacement of ± 0.3C and a tilt angle of ± 0.0055°. Figure illustrates the lubricant film profile generated for a four-pad adjustable bearing under different radial and tilt adjustments.
Figure 6. Variation of dimensionless fluid film thickness in a four-pad adjustable bearing with different radial and tilt adjustments under ε = 0.4.
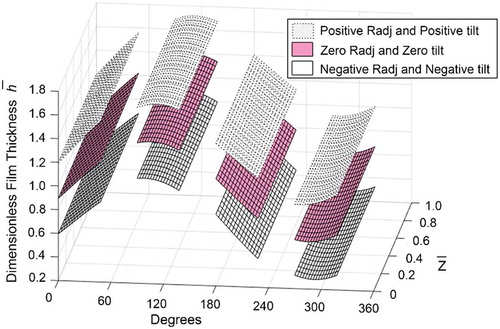
Circumferentially spaced four bearing pads under negative R adj cause a reduction in bearing clearance and developed lower fluid film thickness in comparison with positive and zero adjustments. Larger bearing eccentricities will be attained under positive pad adjustments due to increase in radial clearances. From Figure , it is observed that lower film thickness is attained over bearing pads 3 and 4 under the influence of applied bearing load acting on the pad. However, the maximum film thickness is observed in the unloaded region of bearing pads 1 and 2. The film thickness recorded at different positions of four bearing pads under different radial and tilt adjustments are detailed in Table .
Table 2. Dimensionless film thickness variation observed over a four-pad adjustable bearing for different radial and tilt adjustments at ε = 0.4
Fluid film profile of multipad adjustable bearing under negative radial displacement and negative tilt angle operated under different eccentricity ratios is described in Figure . At smaller eccentricity ratios, pad clearances will be relatively higher leading to the development of larger film thickness at the convergent region of bearing pad surfaces 3 and 4. However, under higher eccentricity ratios, film thickness generated over bearing pads 3 and 4 is comparatively lower than observed in bearing pads 1 and 2. This is due to the influence of applied bearing load acting on the pad, positioning of journal center in the fourth quadrant and reduction in clearance spaces with increase in eccentricity ratios. The finite variation observed near the trailing and leading edges of the bearing pads operated at different eccentricity ratios are detailed in Table . Larger film thickness is observed in the divergent region of bearing pads under different eccentricity ratios. Higher hydrodynamic pressures will be generated in bearing pad surfaces with minimum film thickness.
Table 3. Dimensionless film thickness variation in four-pad adjustable bearing with negative R adj and negative tilt angle operated for different eccentricity ratios
9. Conclusion
Circumferential film thickness gradient and radial clearances in a multipad adjustable bearing are greatly influenced by its unique ability of pad orientations. In the present study, a modified film thickness equation is derived by embodying the radial displacements and tilt angles applied to bearing pads. The developed film thickness equation is initially applied on a single-pad adjustable bearing, and an accurate approximation of lubricant film profile was obtained in comparison with the results presented by Shenoy (Citation2008). The variation in lubricant film thickness for a four-pad adjustable bearing is also recorded for different radial and tilt adjustments. A reduction in film thickness is observed under negative adjustment of bearing pads due to the decrease of bearing radial clearances. Higher hydrodynamic pressures can be generated by symmetrically varying the pad displacement positions. The modified film thickness equation developed can determine the fluid film thickness in an adjustable bearing incorporated with any number of additional bearing elements. The modified film thickness equation can be used in the Reynolds equation to evaluate the performance envelope of multipad adjustable bearings.
Nomenclature
C | = | radial clearance (m) |
| = | pad clearance (m), |
D | = | journal diameter (m) |
| = | journal eccentricity (m), |
| = | film thickness (m), |
L | = | journal length (m) |
| = | steady-state film pressure (N/m2), |
| = | constant supply pressure (N/m2) |
R | = | journal radius (m) |
R adj | = | radial pad adjustment, R adj = (adjR/C) |
R p | = | pad radius (m) |
T adj | = | tilt pad adjustment, R adj = (adjT/C) |
t | = | time (s) |
U | = | peripheral velocity of journal (m/s), |
W | = | load carrying capacity (N), |
| = | radial load component (N), |
| = | Transverse load component (N), |
x | = | circumferential coordinate axis (m), |
z | = | axial coordinate (m), |
| = | pad angle (rad) |
| = | tilt angle (rad) |
| = | lubricant viscosity (Ns/m2) |
| = | angular coordinates of the bearing (rad), |
| = | bearing number, |
| = | attitude angle (rad) |
| = | assumed attitude angle (rad) |
Additional information
Funding
Notes on contributors
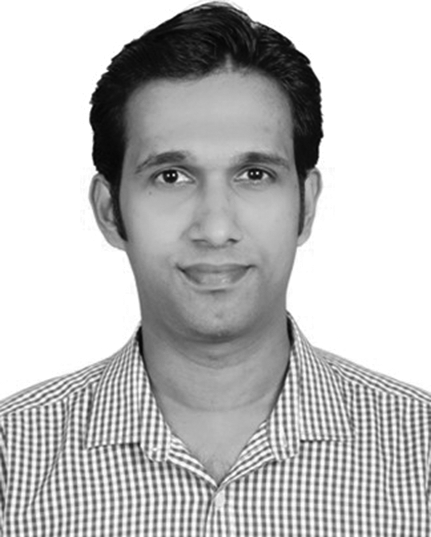
Girish Hariharan
Mr. Girish Hariharan is a PhD student at Manipal Institute of Technology, MAHE, India. He is pursuing his Doctoral degree in Tribology under the supervision of Prof. Raghuvir Pai. In 2018, He received a Japan Student Services Organisation (JASSO) Scholarship for a short-term study in Kyushu Institute of Technology, Japan. His present research is in the field of externally adjustable fluid film bearings. Other research interests include Tribology of water lubricated bearings and CFD analysis of blood flow.
Raghuvir Pai
Dr. Raghuvir Pai is a Professor in Manipal Institute of Technology, MAHE, India. He worked as a DST-BOYSCAST Postdoctoral research fellow at Cranfield University, England. He has 166 research publications in journals and international and national conferences. His expertise in research is in the field of water lubricated bearings, externally-adjustable bearings, tri-taper bearings, tribology of machining metal matrix composites, Nano lubricants in bearings and FSI study of cartoid artery.
References
- Chasalevris, A. , & Dohnal, F. (2012). A journal bearing with variable geometry for the reduction of the maximum amplitude during passage through resonance. Journal of Vibration and Acoustics , 134(6), 061005. doi:10.1115/1.4007242
- Chasalevris, A. , & Dohnal, F. (2014). Vibration quenching in a large scale rotor-bearing system using journal bearings with variable geometry. Journal of Sound and Vibration , 333(7), 2087–2099. doi:10.1016/j.jsv.2013.11.034
- Chasalevris, A. , & Dohnal, F. (2015). A journal bearing with variable geometry for the suppression of vibrations in rotating shafts: Simulation, design, construction and experiment. Mechanical Systems and Signal Processing , 52, 506–528. doi:10.1016/j.ymssp.2014.07.002
- Chasalevris, A. , & Dohnal, F. (2016). Improving stability and operation of turbine rotors using adjustable journal bearings. Tribology International , 104, 369–382. doi:10.1016/j.triboint.2016.06.022
- Hargreaves, D. J. (2016). Predicted performance of a tri-taper journal bearing including turbulence and misalignment effects. Proceedings of the Institution of Mechanical Engineers, Part J: Journal of Engineering Tribology , 209(2), 85–97. doi:10.1243/PIME_PROC_1995_209_411_02
- Krodkiewski, J. M. , Cen, Y. , & Sun, L. (1997). Improvement of stability of rotor system by introducing a hydraulic damper into an active journal bearing. International Journal of Rotating Machinery , 3(1), 45–52. doi:10.1155/S1023621X97000055
- Krodkiewski, J. M. , & Sun, L. (1998). Modelling of multi-bearing rotor systems incorporating an active journal bearing. Journal of Sound and Vibration , 210(2), 215–229. doi:10.1006/jsvi.1997.1323
- Majumdar, B. C. , Pai, R. , & Hargreaves, D. J. (2004). Analysis of water-lubricated journal bearings with multiple axial grooves. Proceedings of the Institution of Mechanical Engineers, Part J: Journal of Engineering Tribology , 218(2), 135–146. doi:10.1177/135065010421800208
- Martin, J. K. (1999). A mathematical model and numerical solution technique for a novel adjustable hydrodynamic bearing. International Journal for Numerical Methods in Fluids , 30(7), 845–864. doi:10.1002/(ISSN)1097-0363
- Martin, J. K. (2002). Extended expansion of the Reynolds equation. Proceedings of the Institution of Mechanical Engineers, Part J: Journal of Engineering Tribology , 216(1), 49–51. doi:10.1243/1350650021543889
- Martin, J. K. (2004a). Measured stiffness and displacement coefficients of a stationary rotor hydrostatic bearing. Tribology International , 37(10), 809–816. doi:10.1016/j.triboint.2004.04.010
- Martin, J. K. (2004b). Measuring the performance of a novel fluid film bearing supporting a rotor on a stationary shaft by non-contacting means. Proceedings of the Institution of Mechanical Engineers, Part K: Journal of Multi-Body Dynamics , 218(3), 143–151.
- Martin, J. K. (2008). Innovative bearings to improve performance and efficiency in industry. International Journal of Performability Engineering , 4(4), 345–356.
- Martin, J. K. (2011). Improved performance of hydrodynamic bearings by proactive adjustment. Mechanics & Industry , 12(1), 17–24. doi:10.1051/meca/2011005
- Martin, J. K. , & Parkins, D. W. (1998). U.S. Patent No. 5,772,334. U.S. Patent and Trademark Office.
- Martin, J. K. , & Parkins, D. W. (2001). Testing of a large adjustable hydrodynamic journal bearing. Tribology Transactions , 44(4), 559–566. doi:10.1080/10402000108982495
- Martin, J. K. , & Parkins, D. W. (2002). Theoretical studies of a continuously adjustable hydrodynamic fluid film bearing. Journal of Tribology , 124(1), 203–211. doi:10.1115/1.1396343
- Pai, R. , & Parkins, D. W. (2018). Performance characteristics of an innovative journal bearing with adjustable bearing elements. Journal of Tribology , 140(4), 041705. doi:10.1115/1.4039134
- Shenoy, B. S. (2008). Performance evaluation of single pad externally adjustable fluid film bearing (Doctoral Dissertation). Retrieved from http://eprints.manipal.edu/141415/
- Shenoy, B. S. , Binu, K. G. , Pai, R. , Rao, D. S. , & Pai, R. S. (2012). Effect of nanoparticles additives on the performance of an externally adjustable fluid film bearing. Tribology International , 45(1), 38–42. doi:10.1016/j.triboint.2011.10.004
- Shenoy, B. S. , & Pai, R. (2008). Steady state performance characteristics of a single pad externally adjustable fluid film bearing. Journal of Advanced Mechanical Design, Systems, and Manufacturing , 2(5), 937–948. doi:10.1299/jamdsm.2.937
- Shenoy, B. S. , & Pai, R. (2009a). Steady state performance characteristics of single pad externally adjustable fluid film bearing in the laminar and turbulent regimes. Journal of Tribology , 131(2), 021701. doi:10.1115/1.3070580
- Shenoy, B. S. , & Pai, R. (2009b). Performance evaluation of a single-pad, externally-adjustable fluid film bearing. Australian Journal of Mechanical Engineering , 7(2), 125–135. doi:10.1080/14484846.2009.11464586
- Shenoy, B. S. , & Pai, R. (2009c). Theoretical investigations on the performance of an externally adjustable fluid-film bearing including misalignment and turbulence effects. Tribology International , 42(7), 1088–1100. doi:10.1016/j.triboint.2009.03.008
- Shenoy, B. S. , & Pai, R. (2009d). Performance characteristics of a misaligned single pad externally adjustable fluid-film bearing. Tribology in Industry , 31(3–4), 29–36.
- Shenoy, B. S. , & Pai, R. (2010). Stability characteristics of an externally adjustable fluid film bearing in the laminar and turbulent regimes. Tribology International , 43(9), 1751–1759. doi:10.1016/j.triboint.2010.04.015
- Shenoy, B. S. , & Pai, R. (2011a). Dynamic characteristics of a single pad externally adjustable fluid film bearing. Industrial Lubrication and Tribology , 63(3), 146–151. doi:10.1108/00368791111126563
- Shenoy, B. S. , & Pai, R. (2011b). Effect of turbulence on the static performance of a misaligned externally adjustable fluid film bearing lubricated with couple stress fluids. Tribology International , 44(12), 1774–1781. doi:10.1016/j.triboint.2011.06.025
- Sun, L. , & Krodkiewski, J. M. (2000). Experimental investigation of dynamic properties of an active journal bearing. Journal of Sound and Vibration , 230(5), 1103–1117. doi:10.1006/jsvi.1999.2671