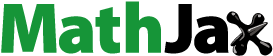
Abstract
Previous studies of Candelilla bagasse fiber (CBF) have demonstrated the improvement of fiber-polymer adhesion; in the present investigation, the CBF was used to reinforce fiber of Polypropylene composites varying the amount of fiber (0, 20 and 30 wt%), using Maleic anhydride as compatibilizer. The total wax of cuticle/intercuticular varies between 9.5 and 10.5 wt%; according to the TAPPI standard Polypropylene/candellia fiber, composites were realized with intercuticular wax. The amount of fiber of 20% and 30% varied in the composite, with and without compatibilizer. In this paper, we will demonstrate that this cuticular fiber wax acts in synergy with the composite in mechanical properties, mechanical dynamics analysis to observe adherence and in “cole-cole” diagrams.
PUBLIC INTEREST STATEMENT
A synergy of Candelilla wax and polypropylene grafted with Maleic anhydride demonstrates the adhesion, and mechanical and dynamic properties. The mechanical properties increases using 20 wt% of Candelilla fiber; the adhesion represent a better interaction of wax–compatibilizer. This research has opened the opportunity to use the compost of Candelilla wax and made a sustainable polymer for the North Mexican communities.
1. Introduction
The improvement of the mechanical properties of composites using cellulosic fibers is a challenge for researchers due to the hydrophilic and hydrophobic characters of this mixture; some products in the composite market are already handled. Several authors published different treatments on fiber surface modification methods, for example, on fiber; alkali treatment increases amorphous cellulose and decreases the crystalline cellulose (Saxena, Pappu, Haque, & Sharama, Citation2011), acetylated test and stabilize the cell wall against moisture absorption (Kalia, Kaith, & Kaur, Citation2009), stearic acid treatment (Kalaprasad et al., Citation2004): the stearic acid/ethanol increases the compatibility between fiber-polymer, silane treated incorporated into the cellulose improving the tensile strength (Kalaprasad & Thomas, Citation2003), etc.
The amount of wax in the fiber has been characterized by several authors in the botanic and phytologist researches. The amount and quality of the wax in the fiber depends on the abiotic stress, type of the cuticular or epicuticular anatomy; all of these factors help the formation of wax consisting of hydrocarbon (long-chain), alcohols (primary or secondary), aldehydes ketones, esters, etc. (Barthlott et al., Citation2006; Domınguez, Heredia‐Guerrero, & Heredia, Citation2011).
The Candelilla fiber content wax of long-chain hydrocarbon (C31, C32), aldehyde ketones, esters (Morales‐Rueda, Dibildox‐Alvarado, Charo‐Alonso, & Toro‐Vazquez, Citation2009), Toro y col. takes advantage of the wax to synthetized organogels (Kalaprasad et al., Citation2004).
The Candelilla bagasse fiber (CBF) was used in a previous paper. The present investigation is a continuation of the previous research (Morales‐Cepeda, Lozano, Ponce-Medina, LaFleur, & Salas-Papayanopolos, Citation2015). The amount of wax in fiber was investigated, in order to find the synergy between the cellulose fiber/wax. Composites of CBF/Polypropylene were obtained using an internal mixing, the dynamic and mechanical characterization, to verify the synergistic of CFB-wax and Polypropylene.
2. Experimental
2.1. Materials
Polypropylene (Profax-6523; homopolymer polypropylene) was obtained from LyondellBasell. Candelilla fiber (bagasse fiber Euphorbia antisyphilitica) was purchased from Multiceras S.A. de C.V., García, Nuevo León. Polypropylene was grafted with a Maleic anhydride (PP-g-MA), Sigma- Aldrich.
Figure illustrates the research step; the first step was to collect and cut the fiber. The size of the fiber was reduced as per the procedure described by Morales et al. (Citation2015). The third step was the composite preparation using two amounts of fiber (20 and 30 wt%). The final step was the characterization of the composites using a different ASTM and Tappi Normas.
2.1.1. Fiber preparation
Candelilla fiber was cut into a length of 4 mm, and then it was used as a mixer to produce a fiber dust. In other words, this process reduces the fiber to approximately 1 mm snippets. Fiber snippets were passed through a 75-µm sieve particle size. The fibers were collected in summer. The Candelilla power was made using a planetary ball mill described by Morales et al. (Morales‐Cepeda et al., Citation2015).
2.1.2. Composite preparation
PP composites were prepared according to Morales et al. (Morales‐Cepeda et al., Citation2015), using an internal mixer (Hakke Record 90). The rotor speed was 50 rpm and the mixing temperature was 180°C. The total mixing time was 13 min. The fiber content used was 20% and 30% (wt%), and the amount of the compatibilizer was fixed at 2 wt%.
2.1.3. Water absorption
The composite samples were cut in approximate dimensions of 77 × 55 × 3.5 mm, according to ASTM D570. The initial humidity content of Candelilla fiber was in the range of 8.9% (TAPPI T-204). Water absorption data were obtained by placing the samples in 50 ml screw-cap flasks containing distilled water. Experiments were conducted at room temperature for immersion periods. The water absorption content of the samples was calculated based on the increase in the sample weight at the corresponding time. The samples were rapidly removed from the flask and superficially dried on filter paper to eliminate the water surface. The samples were then weighed to determine water absorption (Deng et al., Citation2010; Stamboulis, Baillie, Garkhail, Hgh, & Peijs, Citation2000).
2.1.4. Determination of wax in the epicuticular, cuticular and intracuticular
The determination of wax (extract) in the fiber structure was determined using the TAPPI T204 Norma. The humidity of the fiber was calculated using TAPPI T257. The extracts obtained are soluble in neutral organic solvents and insoluble in water. This material is mainly resin, fatty acids and their esters, waxes and non- saponifiable substances. The extract (wax or resin) was determined using two solvents: ethanol and ethanol/acetone mixture (50 Vol%). The samples of Candelilla were 15 g and refluxed in soxhlet for 2–3 min. The percentage of the extract was calculated as follows:
2.2. Measurement of mechanical properties; test of composites
The tensile test was performed using a universal machine (INSTRON Testing Machine model 3365) according to ASTM D638 at a testing crosshead speed of 3 mm/min and load test of 5 KN.
2.2.1. Dynamic mechanical studies
Dynamic Mechanical Analysis (DMA) was performed on a dual cantilever clamp with a frequency of 1 Hz with an amplitude of 30 µm and ramp of 5°C/min from –70°C to 120°C for the samples. The equipment used was marked as “TA instruments”; from this technique, the behavior of the storage modulus, loss modulus and mechanical loss factor module (as δ) was studied. The specimens were made according to ASTM D7028 whose dimensions were 59.95 mm long, 12.05 mm wide and 1.95 mm thick. The specimens for analysis were prepared in a Carver press at a temperature of 180°C for Candelilla fiber composites with polypropylene at a pressure of 5 US Ton, with a maximum time of 13 min. Then they were transferred to a cold press applying a pressure of 5 US Ton during 5 min to prevent the formation of air bubbles. Equation 1 shows the relation of composite and resin; the “C” value is the compatibility between of the resin and the composite:
2.2.2. SEM picture
The measurements were recorded in a JEOL JSM 7600TFE; the sample were covered with gold.
3. Results and discussion
The naturals fibers contents hydrophilic groups, like hydroxyl groups; they absorb moisture content; all this is due to the cuticle of the plant. This cuticle contains two types of lipophilic polymers: continuous and cuticular saws. This cuticular has some main functions: to reduce the loss of water, the diffusion of gases, to allow the interaction of the insects–plant, prevents accumulation of water and dust, controls temperature changes and provides mechanical support for the plant. The production of these lipophilic polymers depends on the cycle of the plant, during its growth, development and post-harvest. The hypothesis of the synthesis of cuticular and epicuticular wax has two steps of biosynthesis: (1) pathway of acyl-CoA reduction, primary alcohol with chain from 26 to 28 carbons up to 30 to 32 carbons, even numbers of carbons (Kunst, Jetter, & Samuels, Citation2006; Shepherd & Griffiths, Citation2006) and (2) where the predominant compounds are formed a number of odd coals (Kunst et al., Citation2006).
According to the classification of the natural and synthetic fibers, Candelilla fibers come from a small shrub considered within the lignocellulosic/cellulosic materials (Jawaid & Abdul Khalil, Citation2011). From the Candelilla plant, the wax that is in the epicuticular layer is harvested and subsequently removed leaving the wax in the cutina and intracuticular layer; in this investigation the bags were used. If the amount of moisture is removed during the extraction of the autocratic wax, there is a barge free of moisture (on the surface) and with intracuticular waxes. These waxes contain alkanes and some alcohols similar to those used in saponification.
In Table , in summary of the wax in the epicuticular and cutina/intracuticulars, the solvent difference is observed. If we add the amount of total wax present in the fiber using the solvents, the wax extract is 22.4% more using Ethanol/acetone mixture for Epicuticular. On the contrary, in the case of cuticular/intracuticulars wax was 63% more for Ethanol solvent. Table , shows the total amount of wax in the fiber cuticular, which is between 9.2 ± 0.4 and 9.9 ± 0.6, depending on the solvent used.
Table 1. Results of the wax, extracted to the Candelilla fiber compost (CFB)
Table 2. Total of wax Candelilla
The dependence on solvent during the extraction of wax is due to the polarity and affinity of the solvents with extracts (Barthlott et al., Citation1998; Morales‐Rueda et al., Citation2009). It is concluded that this value is between 9.2% and 10.0%. The melting temperature of epicuticular or cutina/intracuticulars wax is within the range of 61–66°C unrefined wax; SEM picture shows the fibers (Figure ). Point A shows a groove of a cutine that has a size of 6 µm, white tubular crystallite forms of wax around 3.5–0.5 µm thickens, these forms indicate β-diketones in the epiticular (Barthlott et al., Citation1998; Morales‐Rueda et al., Citation2009); the plasmatic membrane has 1 µm of thickness. Point B in the picture, Candelilla wax coat the epidermis, in crystal forms like Platelets and attached rods (star-like structures) is the crystallization of primary alcohols, particularly the C32 homolog (Barthlott et al., Citation1998). The cuticular wax (CW) depends on the season; in this case, it was collected during the summer.
3.1. Water absorption test of the composites
The composite 20 describes polypropylene with 20 wt% of CFB.Sample 20MA is Polypropylene with 20 wt% of CFB using PPMA (polypropylene with anhydride Maleic compatibilizer); composite 30 describes the propylene with 30 wt% of CFB, and composite 30MA is polypropylene with 30 wt% of CFB using PPMA (compatiblizer).
Water absorption of the polymer was calculated; PP pure was 0.025 wt% (Deng et al., Citation2010). In Figure , the water absorbed is plotted, for the compounds, as it is reported by some authors. The absorption of water inside the composite matrices depends on the free volumeof the fiber, temperature, type of fiber, orientation of the fiber within the matrix (Andreopoulos & Tarantili, Citation1998; Choi, Citation1996; Deng et al., Citation2010; Ellyin & Maser, Citation2004; Schrader, Citation1991; Smith & Weitsman, Citation1996; Stamboulis et al., Citation2000; Stamboulis, Baillie, & Peijs, Citation2001).
According to Figure , absorption increases as the amount of fiber in the polymer increases; epoxy resins have a similar effect to that observed by Rong, Zhang, Liu, Yang, & Zeng, (Citation2001) and Zhong, Lv, & Wei, (Citation2007). These authors assign it to the amount of lumen present for sisal in epoxy resins. In the case of polyolefin as a matrix in compound polymers, the effect is observed, with plants that do not have wax in the external wall.
Free volumeof composites/fiber was calculated according to literature (White & Lipson, Citation2015, 2016). Free value can be observed in Figure ; the maximum value is 2.6 wt%, the free value is not depending on the percent of fiber in the matrix. SEM picture shows the fiber is involved in the matrix (Figure ).
4. Mechanical properties
Table of mechanical properties shows what has been observed by some previous investigations with cellulose fibers; the composites with cellulosic fibers increase by an average 25% compared to the pure polypropylene resin.
Table 3. Mechanical properties of Candelilla fiber composites (CFB)
The Young’s modulus represents the elastic modulus of the materials; as an example, a rubber has enormous Young’s modulus. The composites of the PP and CFB present Young modulus increase slightly in a range of 29% with respect to the resin of PP (Djidjelli et al., Citation2007). Some authors report the same increase of the amount of fiber up to a maximum of 20 wt% (Kalaprasad, Mathew, Pavithran, & Thomas, Citation2003); the sample with 20MA is 2.3 times higher than 30MA. The maximum amount of the CFB in polypropylene is 20wt% of CFB; an increase of the fiber decreases the Young’s module.
When a sample is pull present, tensile strength can be measured. The values of tensile strength are not significant in the composites and resin. This is similar to what was observed by several authors, such as due to the synergy between the fibers–resin. The materials and the composites present an ability to resist breaking under tensile stress. In the present research, the tensile resistance at break point for the composites was studied under the fundamental that a material flexible follows Hooke’s law; in the case of materials composed of cellulose fibers, the tensile strength is low at the breaking point. Tensile strength improved up to 50% with the incorporation of the compatibilizer. This is normal for composite materials with fibers. This behavior is due to the entanglement of the fibers and to the values of crystallinity that increased due to the treatment with ball milling (Djidjelli et al., Citation2007); the crystallinity of the CBF after the treatment was of 60% and is of the order of jute, Sisal (Chattopadhyay, Khandal, Uppaluri, & Ghoshal, Citation2010; Djidjelli et al., Citation2007; Joseph, Joseph, & Thomas, Citation1999; Kalaprasad et al., Citation2003). The good packaging of the fiber helps to improve some mechanical properties (Figure ) and this is reflected in the mechanical properties and the SEM picture as discussed below.
The tensile deformation decreases by half in the cases of composites with and without compatibilizer; therefore, it supposes that there is no significant influence in increasing the CFB in the composites.
Maximum tensile strength increased 10% with respect to compatibilizer. Cutaneous/intracuticular wax is of the N-Acrylamides type, present in the current composite as a lubricant, and improves the mechanical properties of the composites of this type of lubricant. The effect of stearic acid as a compatibilizer has been studied by Kalaprasad et al. (Citation2003) and lubricant by Salas et al. (Salas‐Papayanopolos et al., Citation2014), where it has a positive effect in increasing or maintaining the mechanical properties. This effect is similar in the waxes present in the CBF.
The hydrophilic character of the fibers is an important challenge for blends with cellulose fiber on plastic reinforcement. It is known that the hydroxyl group of the cellulose has the hydrophilic character of the fiber, and therefore the low interaction between the fiber and the hydrophobic polymer matrix, coupled with the moisture content of the fibers, is dependent on the content of the fibers. The CFB has the advantage of being a deserted plant (Morales‐Rueda et al., Citation2009), and contains 8–10% moisture, as well as 9% intracuticular wax, which benefits the interfacial union between fiber, compatibilizer and the polymeric matrix. This benefits in lowers amount of compatibilizer added or to avoid the chemical modification of the fibers (Figure ).
The improvement of mechanical properties of composites using cellulosic fibers is a challenge for researchers due to the hydrophilic and hydrophobic character of this mixture. Some products in the composite market are already handled.
Figure is a hypothetical representation of the system CFB fiber/C31-alkanes and polypropylene Maleic anhydride/polypropylene, the C31-alkanes. In the interaction of PP-Maleic anhydride (PPMA) and the fiber, the ring of the Maleic anhydride is open to connect to the OH bound of the cellulosic chair structure. The wax or the resins in the fiber is connected to the polypropylene chain. The authors Guan Gong et al. (Gong, Jingshen, Lin, Chan, & Yang, Citation2009) demonstrate that the stearic acid form chemical interaction between the CaCO3; the stearic acid was coating in the surface of the CaCO3. This suggests similar effect of the wax or resins in the fiber/polypropylene.
5. Dynamic mechanical properties
Dynamic mechanical properties are used to corroborate the compatibility of cellulose fiber and polypropylene. Figure shows two curves for two transitions types; these transitions have been studied by a different researcher. The first peak is the elastic response (gummy state or elastic response) and the second peak represents the vitrea transition (no elastic response). As reference, the glassy state for the polypropylene is 10–30°C and the viscous state is between 20°C and 40°C.Similar responses have the composites from polypropylene, which has an elastic response between 0°C to 40°C; for the composites 20, 30, 30MA where the effect of the compatibilizer is not notable. The sample 20MA presents low temperature in elastic response between −30°C and 20°C (Corradini, Medeiros, Carvalho, Curvelo, & Mattoso, Citation2006; Da Roz, Carvalho, Gandini, & Curvelo, Citation2006); similar behavior using different glycerol was observed; the elastic response was moved to low temperature to increase the glycerol amount between 5 and 40 wt%. The composite 20MA presents a balance between the wax present in the fiber and the compatibilizer MA (Corradini et al., Citation2006; Da Roz et al., Citation2006).
Table presents a summary of the value from the center of the peak and FHWM data for the poly (propylene) resin and composites, in general, to increase the amount of fiber, the peak width the maximum for the sample of 20 weight% fiber with a Maleic anhydride (Gong et al., Citation2009; Pothan, Oommen, & Thomas, Citation2003; Pothan, Thomas, & Groeninck, Citation2006). At low temperatures, Tg does not increase, due to the lower mobility of the polymeric segment increase with the temperature.
Table 4. Center of peak and FHWM data for the poly(propylene) resin and composites
The adhesion factors are shown in the Figure , which depends on the temperature at the viscous region for the polypropylene resin and the copolymers at different amounts of fiber with and without compatibilizer. The curves show similar behavior with and without compatibilizer; the difference is that when using compatibilizer, the adhesion is slightly lower. It is because the wax present in the fiber improve the adhesion we know that the Candelilla wax (CW) contained 78.9 ± 0.1% of hentriacontane (C31H64), nonacosane, tritriacontane, and triterpene alcohols (Domınguez et al., Citation2011).
The wax present in the Candelilla fiber promotes a better adhesion between the fiber and resin (Table ); the PPMA improved the adhesion of resin/composite.
Table 5. Value of adhesion factor “A”
The importance of the Vitrea transition temperature appreciated in the adhesion force increases with the temperature; at the smallest change of the temperature, bigger adhesion force varies (Figure ). Hence, the mobility of the polymer chain to arrange the Tg; this causes snagging end chain, and the adhesion is higher. The values reported for the adhesion of factor “A” in Table are negative for the samples 20 and 20MA. For different temperatures, different authors demonstrated a greater adhesion. Otherwise, with sample 30 and 30MA where this value is positive, allows us to say that there is a fiber agglomeration and the adhesion between the matrix and the fiber (Gong et al., Citation2009).
Table shows the value of “C”; it is the correlation of polypropylene (resin) and composite with and without Maleic anhydride. The fiber content, a wax 5.0 ± 0.5wt%, is enough to have a lower value of factor, if the composite content Maleic anhydride the value of “C” increases. The value proposes that the free volumeof the composite decreases due to the mobility of the polymer chain.
Table 6. Factor “C”
If we review the literature on fibers, we can find that the core fiber and blast fiber are hemps, kenaf, jute; the fiber of Candelilla is within this classification. The fibers contain wax substances ranging from 0 to 0.8 weight%, which are the cause of moisture absorption; but in the case the wax contained in the Candelilla fiber, which is a semi-desert plant, is of the intracuticular type, waxes contained on the fiber.
The cole-cole plot (Figure ) shows the correlation between the module of storage and loss module. The form of PP and composite shows the imperfect semi-circle for composites; this behavior was observed for composites of polyesters and cellulosic fiber (Pothan et al., Citation2003, Citation2006). Pothan et al. (2003, 2005) demonstrated the homogeneous polymeric system, which shows a semicircle diagram. Figure for the Candelilla/PP polymeric system has a semi-circle diagram; the composites used were Maleic anhydride to the right, which also increases width and height.
5.1. Morphology analysis
The ordering of the fibers is demonstrated in the SEM image (Figure ), where the fibers are oriented in the form of sandwiches, embedded in the polypropylene (PP) polymer matrix. The fiber has an approximate size of 5 microns, corresponding to the fiber size previously estimated by Morales‐Cepeda et al. (Citation2015).
6. Conclusions
The wax of Candelilla is present in the fiber after the previous extraction; it was demonstrated that the Candelilla fiber (CFB) contains 10% of wax, which is found in the cuticle and intercuticle of the fiber. Candelilla wax helps the adhesion between polypropylene and Candelilla fiber, which is like stearic acid studied in other investigations. The maximum adhesion value between PP and CFB was achieved in the composite with 20 wt% fiber; water absorption is lower with 20 wt% of fiber in the composites. The “cole-cole” diagrams are typical for composites with natural fibers incorporated. DMA showed that the same concentration of 20 wt% of fiber has low mobility of segments observed in the glass transition temperature. All these results suggest that the wax and resins presents in the Candelilla fiber helps as compatibilizer between the fiber and the polypropylene.
Mechanical properties demonstrate that the synergist between wax or resin and the compatibilizer, due to the best results are using 20 wt% of CFB in the composites.
Acknowledgements
The authors would like to thank Multiceras for the donation of Candelilla bagasse (CBF). The authors are grateful to Indelpro for their kind donation of polypropylene (Profax-6523), and Chemtura for the Polybond 3200.
Additional information
Funding
Notes on contributors
Ana Beatriz Morales-Cepeda
Dr. Ana Beatriz Morales-Cepeda is a researcher at the Tecnológico Nacional de México/Instituto Tecnológico de Ciudad Madero, at the Centro en Investigación en Petroquímica, in the area of sustainable polymers based on cellulose, also in composites with a base of fibers and/or metallic nanoparticles. Collaborates with universities such as Ecóle Polytechinique Canada, Concordia Canada; University of Jena, Germany.
References
- Andreopoulos, A. G. , & Tarantili, P. A. (1998). Water sorption characteristics of epoxy resin–UHMPE fibers composites. Journal Applications Polym Sciences , 70, 747–755. doi:10.1002/(ISSN)1097-4628
- Barthlott, W. , Neinhuis, C. , Cutler, D. , Ditsch, F. , Meusel, I. , Theisen, I. , & Wilhelmi, H. (1998). Classification and terminology of plant epicuticular waxes. Botanical Journal of the Linnean Society , 126, 237‐260. doi:10.1111/j.1095‐8339.1998.tb02529.x
- Barthlott, W. , Neinhuis, C. , Cutler, D. , Ditsch, F. , Meusel, I. , Theisen, I. , … Wynne Griffiths, D. , Botanical Journal of the Linnean Society (1998), 126: 237–260). (2006). The effects of stress on plant cuticular waxes. Journal Compilation New Phytologist , 171, 469–499. doi:10.1111/j.1469‐8137.2006.01826.x
- Chattopadhyay, S. K. , Khandal, R. K. , Uppaluri, R. , & Ghoshal, A. K. (2010). Mechanical, thermal, and morphological properties of maleic anhydride‐g‐polypropylene compatibilized and chemically modified banana‐fiber‐reinforced polypropylene composites. Journal Applications Polym Sciences , 117, 1731–1740. doi:10.1002/app.32065
- Choi, H.-M. (1996). Needlepunched cotton nonwovens and other natural fibers as oil cleanup sorbents. Journal Environment Sciences Health, Particle A: Toxic/Hazard Substances Environment Engineering , 31(6), 1441–1457. doi:10.1080/10934529609376434
- Corradini, E. A. , Medeiros, E. S. D. , Carvalho, A. J. F. , Curvelo, A. A. S. , & Mattoso, L. H. C. (2006). Mechanical and morphological characterization of starch/zein blends plasticized with glycerol. Journal of Applied Polymer Science , 101, 4133–4139. doi:10.1002/app.23570
- Da Roz, A. L. , Carvalho, A. J. F. , Gandini, A. , & Curvelo, A. A. S. (2006). The effect of plasticizers on thermoplastic starch compositions obtained by melt processing. Carbohydrate Polymers , 63, 417–424. doi:10.1016/j.carbpol.2005.09.017).
- Deng, H. , Reynolds, C. T. , Cabrera, N. O. , Barkoula, N. ‐. M. , Alcock, B. , & Peijs, T. (2010). Water absorption behavior of all‐polypropylene composites and their effect on mechanical properties. Composites Part B , 41, 268–275. doi:10.1016/j.compositesb.2010.02.007
- Djidjelli, H. , Boukerrou, A. , Founas, R. , Rabouhi, A. , Kaci, M. , Farenc, J. , … Benachour, D. (2007). Preparation and characterization of poly(vinyl chloride)/virgin and treated sisal fiber composites. Journal Applications Polym Sciences , 103, 3630–3636. doi:10.1002/app.25502
- Domınguez, E. , Heredia‐Guerrero, J. A. , & Heredia, A. (2011). The biophysical design of plant cuticles: An overview. New Phytologist , 189, 938–949. doi:10.1111/j.1469‐8137.2010.03553.x
- Ellyin, F. , & Maser, R. (2004). Environmental effects on the mechanical properties of glass–fiber epoxy composite tubular specimens. Composites Science and Technology , 64(12), 1863–1874. doi:10.1016/j.compscitech.2004.01.017
- Gong, G. , Jingshen, W. , Lin, Y. , Chan, C. , & Yang, M. ; Journal of Macromolecular Science, Part B: Physics, 48:329–343 . (2009). Dynamic rheological behavior of isotactic polypropylene filled with nano‐ calcium carbonate modified by stearic acid coating. Journal of Macromolecular Science, Part B , 53(3), 412‐427.
- Jawaid, M. , & Abdul Khalil, H. P. S. (2011). Cellulosic/synthetic fiber reinforced polymer hybrid composites: A review. Carbohydrate Polymers , 86, 1–18. doi:10.1016/j.carbpol.2011.04.043
- Joseph, P. V. , Joseph, K. , & Thomas, S. (1999). Effect of processing variables on the mechanical properties of sisal‐ fiber‐ reinforced polypropylene composites. Composites Science and Technology , 59, 1625–1640. doi:10.1016/S0266-3538(99)00024-X
- Kalaprasad, G. , Francis, B. , Thomas, S. , Kumar, C. R. , Pavithran, C. , Groeninckx, G. , & Thomas, S. (2004). Effect of fibre length and chemical modificatirons on the tensile properties of intimately mixed short sisal/glass hybrid fibre reinforced low density polyethylene. Polymer International, 53: 1624-1638. doi:10.1002/pi.1453
- Kalaprasad, G. , Mathew, G. , Pavithran, C. , & Thomas, S. (2003). Melt rheological behavior of intimately mixed short sisal–glass hybrid fiber‐reinforced low‐density polyethylene composites. I. Untreated fibers. Journal Applications Polym Sciences , 89, 432–442. doi:10.1002/app.11975
- Kalaprasad, G. , & Thomas, S. (2003, July). Melt rheological behavior of intimately mixed short sisal‐glass hybrid fiber‐ reinforced low‐density polyethylene composites. II. Chemical Modification Article in Journalof Applied Polymer Science , 89(2), 443‐450. doi:10.1002/app.1197610.1002/pp.11976
- Kalia, S. , Kaith, B. S. , & Kaur, I. (2009). Pretreatments of natural fibers and their application as reinforcing material in polymer composites—A review. Polym Engineering Sciences , 49, 1253–1272. doi:10.1002/pen.21328
- Kunst, L. , Jetter, R. , & Samuels, L. (2006). Biosynthesis and transport of plants cuticular waxes. In Biology of the Plant Cuticle. M. Riederer & C. Müller (Eds.). Annual plant reviews, biology of the plant cuticle (pp. 182–207). Germany: Wiley –blackwell. ISBN: 978-1-405-13268-8
- Morales‐Cepeda, A. B. , Lozano, T. , Ponce-Medina, M. E. , LaFleur, P. G. , & Salas-Papayanopolos, H. (2015). Preparation and characterization of candelilla fiber (Euphorbia antisyphilitica) and its reinforcing effect in polypropylene composites. Cellulose . doi:10.1007/s10570‐015‐0776‐y
- Morales‐Rueda, J. A. , Dibildox‐Alvarado, E. , Charo‐Alonso, M. A. , & Toro‐Vazquez, J. F. (2009). Rheological properties of candelilla wax and dotriacontaneorganogels measured with a true‐ gap system. Journal of the American Oil Chemists’ Society . doi:10.1007/s11746‐009‐1414‐3
- Pothan, L. A. , Oommen, Z. , & Thomas, S. (2003). Dynamic mechanical analysis of banana fiber reinforced polyester composites. Composites Science and Technology , 63, 283–293. doi:10.1016/S0266‐3538(02)00254‐3
- Pothan, L. A. , Thomas, S. , & Groeninck, G. (2006). The role of fibre/matrix interactions on the dynamic mechanical properties of chemically modified banana fibre/polyester composites. Composites: Part A , 37, 1260–1269. doi:10.1016/j.compositesa.2005.09.001
- Rong, M. Z. , Zhang, M. Q. , Liu, Y. , Yang, G. C. , & Zeng, H. M. (2001). The effect of fiber treatment on the mechanical properties of unidirectional sisal‐reinforced epoxy composites. Composites Science and Technology , 61, 1437–1447. doi:10.1016/S0266‐3538(01)00046‐X
- Salas‐Papayanopolos, H. , Morales, A. B. , Lozano, T. , Laria, J. , Sanchez, S. , Rodriguez, F. , … Cerino, F. (2014). Improvement of toughness properties of polypropylene/wollastonite composites using an interface modifier. Polymer Composites . doi:10.1002/pc.22766
- Saxena, M. , Pappu, A. , Haque, R. , & Sharama, A. (2011). In S. Kalia, B. S. Kaith & I. Kaur (Eds.), Book: Cellulose fibers: Bio‐ and nano‐ polymer composites, green chemistry and technology. Springer. ISBN: 978‐3‐642‐17369‐1. doi:10.1007/978‐3‐642‐17370‐7
- Schrader, E. (1991). Remediation of floating, open water oil‐spills‐comparative efficacy of commercially available polypropylene sorbent booms. Environmental Geology and Water Sciences , 17(2), 157–166. doi:10.1007/BF01701571
- Shepherd, T. , & Griffiths, D. W. (2006). The effects of stress on plant cuticular waxes. New Phytologyst , 171, 469–499. doi:10.1111/j.1469‐8137.2006.01826.x
- Smith, L. V. , & Weitsman, Y. J. (1996). Sea water effects on the fatigue response of polymeric composites. In A.H. Cardon, H. Fukuda & K. Reifsnider (Eds.), Progress in Durability Analysis of Composite Systems , 217–223. ISBN 9789054108092
- Stamboulis, A. , Baillie, C. A. , Garkhail, S. K. , Hgh, V. M. , & Peijs, T. (2000). Environmental durability of flax fibres and their composites based on polypropylene matrix. Applications Compos Materials , 7(5–6), 273–294. doi:10.1023/A:1026581922221
- Stamboulis, A. , Baillie, C. A. , & Peijs, T. (2001). Effects of environmental conditions on mechanical and physical properties of flax fibers. Composites Particle A: Applications Sciences Manufacturing , 32(8), 1105–1115. 20 Springer GS, editor. Environmental effects on composite materials; 1981. doi:10.1016/j.compositesb.2010.02.007
- White, R. P. , & Lipson, J. E. G. (2016). Lipson polymer free volumeand its connection to the glass transition. ACS Macro Letters . doi:10.1021/acs.macromol.6b00215
- White, R. P. , & Lipson, J. E. G. (2015). Free volumein the melt and how it correlates with experimental glass transition temperatures: Results for a large set of polymers. ACS Macro Letters , 4, 588−592. doi:10.1021/acsmacrolett.5b00217
- Zhong, J. B. , Lv, J. , & Wei, C. (2007). Mechanical properties of sisal fiber reinforced ureaformaldehyde resin composites. EXPRESS Polymer Letters , 1(10), 681–687. doi:10.3144/expresspolymlett.2007.93