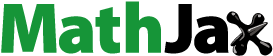
Abstract
This study aimed to investigate the usability of Recycled Concrete Aggregate (RCA) in warm mix asphalt (WMA) as the implementation of sustainable construction technology. Five replacement rates (0%, 25%, 50%, 75%, and 100%) were tested for the coarse fraction of virgin aggregate (VA) with 3 types of RCA: untreated RCA, HL-treated RCA, and HCL-treated RCA. Scanning electron microscopy (SEM) analyses were performed to investigate the surface morphology for both treated and untreated RCA. The optimum asphalt cement content for every substitution rate was determined using Marshall mix design method. Thereafter, asphalt concrete specimens were prepared using the optimum asphalt cement content, followed by the evaluation of their performance properties, including the moisture damage, resilient modulus, and permanent deformation characteristics. These properties were assessed using indirect tensile strength and uniaxial repeated loading tests, respectively. It was found that, for mixes with RCA content of 100%, the untreated RCA mixes possess higher OAC than that of treated RCA mixes by 0.26%. The moisture susceptibility was improved in case of HL and HCL treated RCA by 9.09% and 10.34% as compared to untreated RCA. However, the resilient modulus and resistance to permanent deformation for the mixes with 100% RCA were lower than those prepared with VA; the decrement in Mr values are 39.17%, 28.56% and 23.09% for the untreated RCA, HL-treated RCA and HCL-treated RCA, respectively. Finally, the cost, material, and energy-saving implications of RCA were discussed.
PUBLIC INTEREST STATEMENT
Recently, the increase of construction prices coupled with the increase of the environmental regulations and awareness has driven a strong movement toward the adoption of sustainable technology in the road construction projects. Warm mix asphalt is one of the sustainable approaches used to reduce the environmental impact and asphalt concrete production cost as compared to hot mix asphalt since its production and compaction temperatures are less than that of hot mix. This paper implements the use of Recycled Concrete Aggregate (RCA) in warm mix of asphalt. The RCA was used in different replacement rates and due to its high porosity, different treatment methods were applied. It can be noticed that the use of RCA has improved the strength of warm mix asphalt mixtures and their moisture susceptibility.
1. Introduction and background
Sustainable pavements are those that meet the requirements of the present generation without influencing the capability of the future generation to meet their needs. Sustainable pavement examples comprise warm asphalt mixtures (WMA), mixtures including recycled products, and those blended with waste products. The WMA mixtures are considered as one of the best alternative sustainable material in asphalt concrete paving, which could be produced and compacted by approximately (15–40°C) lower temperature than that for hot mix asphalt (HMA) mixtures, based on the kind of additives used to create the WMA (Buss, Citation2014). The temperature reduction in the mixing, handling, and compaction of the mix saves energy, minimizes emissions, and significantly reduces the production costs (Sarsam, Citation2016). Recently, the amount of building and demolition waste produced annually, worldwide, has been determined at 1183 million tones (Purushothaman, Amirthavalli, & Karan, Citation2014). The concrete is the most important element among these waste materials. Managing such enormous quantities of waste is a serious challenge because of the scarcity of landfills and transport costs (da Conceição Leite, Dos Santos Motta, Vasconcelos, & Bernucci, Citation2011). The use of RCA in asphalt concrete mixes for pavement construction is one of the valuable solutions to eliminate this problem while simultaneously serving the sustainability purpose. RCA is a composite fabric, in which cement mortar (30–35%) is covered in natural aggregates (65–70%) and can be manufactured by crushing concrete hunks into smaller parts (Kong et al., Citation2010; Rodríguez, Alegre, & Martínez, Citation2007). In general, RCA is rough, porous, flat and irregular compared to natural aggregates. RCA demonstrates the next features: High water absorption, reduced volume and specific gravity, low loss of abrasion, fast grinding into small fractions, among others (Lee, Du, & Shen, Citation2012; Malešev, Radonjanin, & Marinković, Citation2010). However, the RCA crushing process can deteriorate the bonding strength between the original natural aggregates and the mortar and increase the RCA microcracks (Lee et al., Citation2012). In order to improve the low quality of RCA’s physical and mechanical properties, substantial research has been conducted on the use of different treatment methods and procedures to improve these properties (Al-Bayati, Tighe, & Achebe, Citation2018), including (i) the method involving the removal of loose mortar particles from the aggregate surface and (ii) the method involving, extensively, modification and improvement of the quality of the adhered mortar. Through ultrasonic cleaning, the loose mortar particle adhered to the surface can be eliminated (Katz, Citation2004), ball milling, or heating followed by rubbing (Tamura, Noguchi, & Tomosawa, Citation2002; Tsujino, Kitagaki, Noguchi, Nagai, & Kunieda, Citation2008). Presoaking RCA in an acidic environment (Tam, Tam, & Le, Citation2007) using binding components such as reactive pozzolanic materials (Li, Xiao, & Zhou, Citation2009) and polymers (Kou & Poon, Citation2010) is a common procedure for surface treatment (such as coating/impregnation).
Although several researches have examined and evaluated the use of RCA in HMA, their use in WMA does not yet exist in the literature. Therefore, we reviewed the performance of HMA-containing RCA. Contradictory exists among the researches regarding the performance of HMA containing RCA. Paranavithana and Mohajerani (Citation2006) reported the use of coarse RCA on the performance properties of HMA at the RCA replacement rate of 0% and 100%. They found that the bulk density, void in mineral aggregates, voids filled with asphalt, and the resilient modulus for 100% RCA mixes were lower than those for 0% RCA. Moreover, the air voids and the stripping potential were higher for the 100% RCA mixture. Motter, Miranda, and Bernucci (Citation2015) investigated using of 5 replacement rates of RCA as a coarse aggregate (0%, 25%, 50%, 75%, and 100%), they concluded that the permanent deformation increased and the resistance to moisture-induced damage was improved with the increasing content of RCA. In addition, they stated that the mixes prepared with a high percent of RCA showed higher consumption of asphalt cement. Ismail and Ramli (Citation2013) reported different concentrations (0.1, 0.5, and 0.8 M) of hydrochloric acid (HCl) with various immersion periods (one, three, and seven days) have been tested to improve the performance of the RCA. The findings revealed a linear correlation between the mortar loss amounts and increased acid concentration, while no significant effect was observed during the immersion.
Al-Bayati et al. (Citation2018) evaluated the impact of coarse RCA on the volumetric properties of HMA using 0%, 15%, 30%, and 60% replacement rates, both untreated and RCA treated with 2 different techniques, Pre-treatment with low acid and 300° C heat treatment each was combined with a brief mechanical procedure. The tests results revealed that the addition of coarse RCA with various rates was extremely effective for both untreated and treated RCA. They also indicated that the RCA treated with various treatment types were more successful than the untreated RCA. Tam et al. (Citation2007) studied RCA soaking in 3 various strong acid solutions: sulfuric acid (H2SO4), hydrochloric acid, and phosphoric acid (H3PO4) at 0.1 M for 24 h at 20°C. The final outcome showed a significant reduction in water absorption, enhanced mechanical properties, and no adverse effect from chloride and sulfate ions on the RCA.
The objective of the submitted study is to evaluate the performance properties of warm mix asphalt containing different replacement rates of the recycled concrete aggregate, untreated RCA and treated RCA with HL slurry and HCL solution were used in the preparation of the mixes. The matter which could serves the sustainability objective.
2. The materials
Materials used in this research’s experimental part are asphalt cement, aggregate, mineral filler, and additives; The features of this material are presented in the following articles:
2.1. Asphalt cement
The asphalt cement obtained from the refinery of Doura was checked according to the criteria of Superpave performance grade (Table ). It is obvious from the results that the asphalt cement showed a performance grade of PG 64–16. The test is depicted in Figure .
Table 1. The physical properties of asphalt cement based on performance grade
2.2. Aggregate
Virgin aggregate and recycled concrete aggregate were utilized in asphalt concrete mixtures. The VA was crushed quartz bought from Al-Nibaie’s quarry, while the RCA obtained from a concrete recycling factory in Alrathwanya region; this form of aggregate was supplied from the Texas T-wall crushing. Figure shows the barriers with a design compressive strength of 30 MPa. The properties of the VC and RCA aggregates are listed in Table and Figure presents the gradations of aggregate.
Table 2. Physical properties of aggregates
2.3. Filler
The filler utilized in this research is limestone dust. The chemical and physical properties of the used filler are illustrated in Table .
Table 3. Properties of mineral filler
2.4. Hydrated lime slurry (HL)
A total of 1.5% hydrated lime slurry was used for the treatment of RCA. The chemical and physical properties of the HL are listed in Table .
Table 4. Properties of hydrated lime
2.5. Aspha-min
Aspha-min (Na2O.Al2O3.2SiO2) powder was used as the additive to produce WMA. It is a Sodium Aluminosilicate hydrothermally crystallized into a fine powder containing approximately 21% water by weight. The physical and chemical characteristics for the Αspha-mіn are listed in Table .
Table 5. Physical and chemical properties of WMA additive, aspha-min
2.6. Hydrochloric acid HCL
HCl (37%) is an acidic solution obtained from muaasker alrasheed at a low concentration of 0.1 M.
3. Method of treatment RCA
The RCA was washed and dried in an oven at 105 ± 5°C for 24 h before conducting Pre-soaking treatment. First type: The RCA was soaked in 1.5% hydrated lime slurry for 24 h, followed by dried in an oven for 4 h at 105 ± 5°C. Second type: the RCA was soaked in an acidic solution composed of Hydrochloric acid; (HCl) (37%) at a low concentration of 0.1Molarity for 24 h at room temperature around 25°C then, submerged in distilled water and drained; to remove the acidic solution, after that the samples were dried at 105 ± 5°C for 24 h. Next, the regular process of mixing and compaction followed the treatments. The research structure and experimental test combinations to meet the outlined objective in this study are shown in Figure .
4. Scanning electron microscope (SEM) analysis
A deeper insight into the possible effects of the treatments of both VA and RCA aggregate were provided using the SEM images with a magnification of 5.00 kx (Figure ).
Fine-crystalline medium (FCM) enveloping a relatively large crystal is the common characteristic for SEM imaging; although the morphology of the FCM varies from one image to another owing to the difference in the chemical composition. The VA image Figure ) shows the presence of a large grain in the center, which belonged to quartz crystal; the FCM consisted of irregular particles that split off from the quartz crystal during aggregate crushing. These particles have a sharp edge and a relatively flat surface. The FCM have a porous texture with several voids on its surface, as is evident from the image of treated VA in Figure ). The FCM has a dense mass, and the voids present in the VA image disappeared due to the coating effect of the HL slurry. Regarding the RCA image (Figure ), the FCM has deep and hierarchically organized pores of size 50–100 µm, and it was probably formed during a chemical reaction due to cement hydration, which is accompanied by a change in the volume. The untreated RCA morphology is rough, with a high pore structure it is irregular.
The adhered mortar was found to spread widely at various thicknesses, resulting in heterogeneity of the ground. The high magnification picture thus clearly showed the presence without a specific size or type of various voids and particles. This result explains higher water absorption and less RCA density. These results confirm the laboratory tests, which showed a high absorption of the water and low density of untreated RCA. For the treated RCA, the FCM porosity was reduced to a large extent when the RCA was treated with HL slurry (Figure )), which resulted in increased density as compared to that of the untreated RCA. For the RCA treated with HCL (Figure )), a significant change was noted in the degree of roughness of the RCA surface. The roughness vanished largely from the RCA surface after the acid treatment, as acidic solutions attack the surface and dissolve the adhered mortar.
5. Specimen preparation
All types of aggregates were sieved, washed, treated, and then dried to a constant weight at 110°C in order to meet the Iraqi specifications (section R9) table R9/3 grading of pavement layers; five-replacement rates for the VCA with RCA were investigated during the course of laboratory works (0%, 25%, 50%, 75%, and 100%). Three groups of specimens were prepared, (i) URW, in which the replacement percent consisted of untreated aggregate; (ii) TRW (HL), in which the replacement percent consisted of hydrated lime-treated aggregates; and (iii) TRW (HCL) in which the replacement percent consisted of HCl-treated aggregates. The experimental work employed the Marshall mix design method ASTM (D 6927-04) to determine the OAC for each replacement percent for both URW and TRW.
Then, the OAC used in specimen preparation for indirect tensile strength and uniaxial repeated loading tests for evaluation the performance properties of WMA. The mixing temperature was controlled at 125°C (30°C minus the HMA concrete temperature of 155°C, as per the Aspha-Min technical specification). Compaction temperature of 115°C (10°C minus the mixing temperature) was used; the bowl content was heated in the oven for 10 min at 115°C.
6. Results and discussions
6.1. Preliminary test: Marshall mix design
To determine the OAC for the URW and TRW mixes with varying percent of RCA, a complete mix design was adopted according to the Marshall method as summarized in the ASTM (D 6927-04). For each percent of RCA, 5 Marshall specimens were prepared, beginning with 4.4% asphalt cement with a constant increment rate of 0.3%. For 75% URW, 100% URW, and 100% TRW mixes, it was noted after plotting the Marshall properties that the stability and bulk density continuously increased with increasing asphalt cement content; consequently, Additional specimens of asphalt cement content are prepared, 5.9% for 75% URW and 100% TRW and 5.9% and 6.2% for 100% URW. The demonstrated specimens demonstrated a bend in stability and bulk density curves; hence, the OAC was well defined for these mixes. The results of the OAC for the URW and TRW mixes with all the RCA replacement rates are presented in Table . Reviews of the information provided indicate that 25% URW and 50% TRW specimens acquired, approximately, the same OAC as that by 0% URW and 0% TRW for both HL and HCL, respectively. Further increase in the RCA replacement resulted in higher OAC for both the mixes (i.e., URW and TRW) (Figure ), which can be mainly attributed to the high absorption property of the RCA. The specimens with 100% RCA content,the untreated RCA mixes possess higher OAC, than that of treated RCA mixes by 0.3%, which indicates that the hydrated lime and HCL could serve, to some extent, to reduce the porosity of RCA due to the fine-grain nature of hydrated lime as well as due to the corrosive influence of HCL on the attached mortar.
Table 6. Optimum asphalt content % for all the RCA replacement rates
The variation in the Marshall properties with asphalt cement contents for each RCA replacement rates are given in Figures and .
According to the stability curves shown in Figures and , the results indicate that the stability of mixtures containing RCA was higher than that for the control mixtures, and that all the URW, TRW (HL), and TRW (HCL) satisfied the minimum stability requirement presented in the SCRB specification of 8 KN. However, an improvement of 12.3% was noticed in the case where the VA was totally replaced by RCA for URW. These results are in agreement with those of Pérez et al., Citation2012; Wong, Sun, & Lai, Citation2007 and Zulkati, Wong, & Sun, Citation2012. Therefore, an increase in the stability values as the RCA content increases in the mixture may be due to the interlocking between the RCA particles; which causes an increase in the internal friction among the particles.
Based on the Marshall flow results illustrated in Figures and , the flow value at the asphalt cement content, which shows that the peak stability value for 75% URW was quite similar to that for 0% URW (3.07 mm and 3.05 mm, respectively). The flow values are in agreement with those reported by Pérez et al. and Rafi et al. For 100% TRW (HL) and 100% TRW (HCL), the corresponding flow values were 3.10 mm and 3.05 mm, respectively, which were slightly lower than those of 0% URW (3.3 mm). The average flow value at the peak stability (all the replacement percent) for TRW (HL) was 3.2 mm and that for TRW (HCL) was 3.14 mm, where also were slightly greater (4.25% and 2.42%, respectively). For the 3 mixtures, all flow values of peak stability satisfied the SCRB specification flow requirement of 2–4 mm. Concerning the bulk specific gravity outcome illustrated in Figures and , the same trend for URW and TRW were noted; that is, the RCA replacement rate increased with decreasing Gm bulk of the specimen. The peak value of Gm bulk corresponding to 100% TRW (HL) at 5.6% asphalt cement content and 100% URW at 5.9% asphalt cement content were lower than those of 0% TRW (HL), 0% TRW (HCL), and 0% URW at 5% asphalt cement content by 5.06%, 5.05%, and 5.29%, respectively. This difference can be attributed to the lower density of RCA grains as compared to that of the VA (Table ); this finding agrees with those for URW by Bhusal, Li, & Wen, Citation2011; Motter et al. Citation2015 and Rafi et al., Citation2011.
The volumetric property of air voids (AV) is illustrated in Figures and , which reveals that the mixes with higher RCA contents possess higher AV. At the asphalt contents that yielded the peak Gm bulk values, the AV for 100% URW, 100% TRW (HL), and 100% TRW (HCL) were higher than those of 0% URW by 3.85%, 17.74%, and 15.89%, respectively. In addition, the findings related to URW were comparable with those obtained by Motter, Miranda, and Bernucci (Citation2015) and Rafi et al., (Citation2011). Nevertheless, all the AV values for URW, TRW(HL), and TRW(HCL) mixes at the peak Gm bulk were within the range of SCRB specification requirement of 3–5%.
The voids in mineral aggregate (VMA) results illustrated in Figures and show that the URW, TRW(HL), and TRW(HCL) mixes with RCA have higher VMA values than those containing VA. However, the increment of VMA in TRW(HL) and TRW(HCL) were lower than that in URW. At the peak Gm bulk values, the average VMA (all replacement percent) for 100% URW, 100% TRW (HL), and 100% TRW(HCL) were 15.521%, 15.124%, and 14.907%, respectively. In general, the VMA increased with increasing RCA percent in the mix.
6.2. Moisture susceptibility
The moisture susceptibility of the asphalt concrete mixture was evaluated using the ASTM-D4867 standards for each mix type. The specimens were prepared using the Marshal compaction method with a number of blows per face that varied according to the RCA replacement percent of 50–65 to result in AV of the specimens being 6–8%. The test parameters were computed according to the following:
Where, Pu is the splitting load, t is the specimen height immediately before tensile testing, D is the specimen diameter, TSR is the tensile strength ratio, %, C.ITS is the average tensile strength of the conditioned subset, UC.ITS is the average tensile strength of the unconditioned subset. Based on the results exhibited in Figure .
It is clear that there was a featured trend for increasing dry ITS (unconditioned) with an increasing RCA replacement rate. Notably, the increment rate of dry ITS was higher for URW than for TRW; the constant of linear proportionality between the dry ITS and RCA replacement rate was 3.757 Psi/10% for URW, whereas it was 2.901 psi/10% and 4.134 Psi/10% for TRW(HL) and TRW(HCL), respectively. In addition, for the 100% RCA replacement rate, the dry ITS was higher than that of VA by 37.16%, 24.69%, and 34.76% for URW, TRW(HL), and TRW(HCL), respectively. The increase in the tensile strength was mainly due to the surface texture of the RCA, which affected the bond between asphalt and aggregate particle and increased the strength of the adhesion between them. However, it is believed that the internal friction of RCA was higher than that of natural aggregate because of the rougher surface texture of RCA. The inspection of the failed specimen in Figure shows that the failure surface for the mixes with a high content of RCA included broken RCA, whereas, for those mixes without RCA, the failure plane passed through the perimeter of aggregate.
It was obvious from the TSR results shown in Figure that the URW mix is more susceptible to moisture damage than TRW, with the average TSR for URW mixes (73.6%) being lower than that of TRW(HL) and TRW(HCL) by approximately 10.05% and 11.68%, respectively. This fining reveals the role of HL and HCL in the improvement of the wet ITS (conditioned) and TSR. Moreover, for the three types of mixes, the highest TSR value was obtained when the VA was entirely replaced by RCA. Reminding that the minimum acceptable limit for the TSR is 80%, which is used to distinguish between the moisture susceptible mixture and moisture resistance mixtures (Albayati,, Citation2018), it is clear that the 50% TRW, 75% TRW, and 100% TRW treatment type satisfied the specification requirement for this type of damage, whereas, for the untreated mixes, only 100% URW satisfied the limit. The results obtained, which were related to the improvement of TSR for URW when using RCA instead of VA was comparable with those reported by Motter et al. Citation2015; Paranavithana & Mohajerani, Citation2006 and Albayati et al., Citation2018
6.3. Uniaxial resilient modulus
The uniaxial repeated loading tested were conducted for cylindrical specimens (dimensions: [4 in] diameter × [8 in] height) using the pneumatic repeated load system. The specimens were prepared according to the steps explained in (Albayati, Citation2006). The uniaxial repetitive compressive stress of 137.9 kPa (20 psi) was used during the test with a 0.1-s loading time, followed by 0.9-s rest time (loading frequency of 1 Hz), the test was performed at 20°C (68°F). The resilient modulus was calculated according to the following formula:
where,
σ is the repeated axial stress.
Δr is the average of axial resilient deflection recorded
h is specimen height.
The resilient modulus test results are presented in Table and Figure ; it is obvious that the Mr value decreases for 3 type of mixes (i.e., URW, TRW(HL), and TRW(HCL)) as the RCA replacement rate increases, but the decrement in the case of TRW was less than that in the case of URW. When the VA aggregate was entirely replaced with RCA, the decrement in Mr values were by 39.17%, 28.56%, and 23.09% for URW, TRW(HL), and TRW (HCL), respectively.
Table 7. Resilient modulus tests results
The constant of the linear proportionality between the Mr and RCA replacement rate was −6146.6 Psi/10% for URW, −5315.8 Psi/10% for TRW(HL), and −5093.5 Psi/10% for TRW (HCL). A more thorough review of the Mr data signified both the treatment types for the aggregate incorporated in a noticeable improvement in Mr values, in HL treatment, the improvement was 17.43%, while it was 100% RCA replacement, and in HCL treatment the improvement is 26.42% in case of 100% RCA replacement. The obtained results of URW were comparable with that presented by Paranavithana and Mohajerani (Citation2006) and Mills-Beale and You (Citation2010), who investigated the Mr values for HMA with a different percent of RCA replacement.
6.4. Permanent deformation
The uniaxial repeat load experiment was carried on under the same load condition and specimens described above in the uniaxial resilient modulus tests until the specimens were deformed at 40° C (104° F) followed by permanent intercept deformation parameters (I) and slope (b), measured on permanent-deformed plots versus load-repetition after reprehensive load repetition, as illustrated originally by Albayati, Citation2006. The test outcomes of permanent deformation are illustrated in Figures –1, based on the information provided in Table .
Table 8. Permanent deformation parameters
The analyzes of the data show the permanent deformation generally increases when the RCA replacement increases in all types of mixes; however, the increment was less in case of TRW(HCL) and TRW(HL) than in URW. For mixes containing 100% RCA, the slope value that reflects the accumulation rate of permanent deformation was relatively 35.43%, 30.95%, and 27.8% higher than that of 0% RCA for URW, TRW(HL), and TRW(HCL) mixes, respectively. The average slope value for the URW mixes was 0.467, whereas it was 0.452 and 0.442, respectively, for TRW (HL) and TRW(HCL). In terms of the intercept value, although there was some discrepancy in the URW results, it can be concluded using the TRW data that the intercept follows approximately the same trend of slope, that is, higher the replacement rate of RCA, higher is the intercept value. The intercept values when the VA was entirely replaced by the RCA increased by 8.38%, 6.73%, and 5.64% for URW, TRW(HL), and TRW(HCL) mixes, respectively.
Based on the total permanent deformation at failure, the average permanent deformation (all replacement percent) for the URW was lower than that for TRW(HL) and TRW(HCL) by 16.89% and 23.42%, respectively (Figure ). Thus, the treatment of RCA with HL slurry, HCL yields an improved resistance against rutting type of failure in comparison with untreated RCA. The obtained results of permanent deformation for the URW mixes when using RCA instead of VA agrees with those reported elsewhere Bhusal & Wen, Citation2013; Mills-Beale &You, Citation2010; Pourtahmasb & Karim, Citation2014, although they investigated the performance of HMA.
7. Study of cost, materials and energy saving
As shown in Table , the total cost of the materials of the asphalt concrete mixes were determined referring to the native raw material cost. Figure displays the cost comparison of one cubic meter of various RCA rates. It can be seen that using hydrated lime-treated and HCL acid-treated aggregates at 100% RCA rate resulted in the highest cost savings as compared to 0% untreated aggregates by 6.09% and 6.46%, respectively. However, the cost-saving ratio of 0% RCA (Figure ), it shows that 50–100% RCA with HL-slurry and HCl-acid treated aggregates were the most cost-effective when compared to untreated RCA at the saving rate of 3.5–6%.
Table 9. Reference prices of raw materials (STCCM, Citation2018)
To demonstrate the potential savings of virgin aggregates, by considering pavement (1 km length, 8 m width, and 50 mm thickness); the material saving on VA were 374 tones for 100% RCA use or 93.5 tons for 25% RCA use. These savings are also reflected in decreasing CO2 footprint. The mixing temperature of WMA production for asphalt concrete was usually 30–60°C lower than that of HMA production. This is estimated to give 35% less energy consumption, resulting in correspondingly lower CO2 emissions (Bhusal et al., Citation2011). It can, therefore, be concluded that the use of 50% HL-treated and 75% HCL-treated RCA for WMA concrete will achieve the optimum advantage for both material and economic efficiency as well as environmental sustainability.
8. Conclusion
The purpose of this study was to estimate the performance properties of WMA containing different replacement rates of RCA, untreated and treated RCA with HL slurry, and with HCl solution used in the preparation of the mixes. Based on the results of the laboratory tests presented in this research, the following salient conclusions can be drawn:
SEM analysis revealed that the porosity of RCA was reduced to a large extent when the RCA was treated with HL slurry, resulting in a denser morphology; roughness disappeared broadly, and the adhered mortar was dissolved from the RCA surface when the RCA was treated with HCl solutions than when untreated.
The use of various RCA replacement rates had a significant impact on the Marshall mix design properties, some of which are summarized below:
Mixes with a higher percentage of RCA possess higher OAC as compared to those containing VA. Treated RCA with HL and HCL could reduce the OAC, for the mixes with RCA content of 100%, untreated RCA mixes possess higher OAC than that of treated RCA mixes by 0.26%.
An improvement in the Marshall stability and resistance to plastic flow was noted when the VA was entirely replaced by RCA for WMA mixes.
Mixes with higher RCA contents have higher AV.
This research demonstrates the potential improvement in the durability of asphalt concrete when using RCA for both URW and TRW mixes; the TSR increased when the RCA replacement rate was increased. The average TSR for the URW mixes (73.6%) was lower than that of TRW(HL) and TRW(HCL) by approximately 10.05% and 11.68%, respectively.
The Mr value decreased for both the type of mixes (i.e., URW and TRW) as the RCA replacement rate increased. When the VA aggregate was entirely replaced with RCA, the decrement in Mr values were 39.17%, 28.56%, and 23.09% for URW, TRW(HL), and TRW (HCL), respectively.
The permanent deformation generally increases as the RCA replacement rate increased in both the types of mixes, but the increment was less in case of TRW than in URW. For mixes containing 100% RCA, the accumulation rate of permanent deformation (slope) was approximately 35.43%, 30.95%, and 27.8% higher than that of 0% RCA for URW, TRW(HL), and TRW(HCL) and mixes, respectively.
Overall, this research showed that hydrated lime and HCl acid can efficiently reform and enhance RCA’s performance and can be applied for WMA mixing.The comprehensive view for the obtained results revealed that the use of either untreated or treated RCA instead of VA resulted in the improvement for the tension-stress failure mode and also showed lower performance for the compression-stress mode of failure. The Marshall properties with the inhomogeneous type of stress also improved in terms of stability, whereas there were discrepancies among other properties.
Additional information
Funding
Notes on contributors
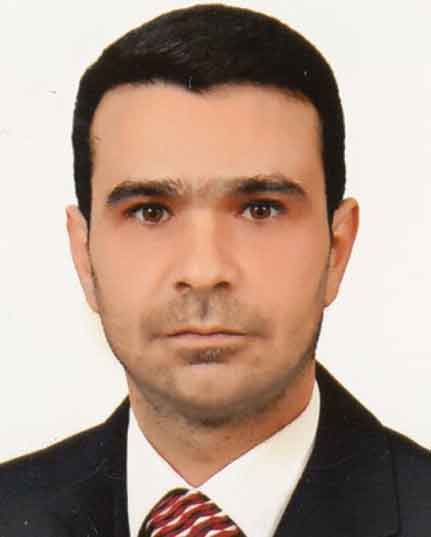
Amjad H. Albayati
Amjad H. Albayati is a professor in the department of civil engineering, University of Baghdad (Iraq). He obtained MSc and Ph.D in the highway and transportation engineering from the University of Baghdad in 2001 and 2006, respectively. He has publications in the fields of Pavement engineering, material characterization, sustainability and Traffic engineering. Currently, he is a manger of consulting engineering bureau for the University of Baghdad.
References
- Albayati, A., Wang, Y., Wang, Y., & Haynes, J. (2018). A sustainable pavement concrete using warm mix asphalt and hydrated lime treated recycled concrete aggregates. Sustainable Materials and Technologies, 18, e00081. doi:10.1016/j.susmat.2018.e00081
- Albayati, A. H. (2006). Permanent deformation prediction of asphalt concrete under repeated loading (pp.129). University of Baghdad, Iraq.
- Albayati, A. H. (2018). Performance evaluation of plant produced warm mix asphalt. Journal Of Engineering, 24(5), 145–20.
- Al-Bayati, H. K. A., Tighe, S. L., & Achebe, J. (2018). Influence of recycled concrete aggregate on volumetric properties of hot mix asphalt. Resources, Conservation and Recycling, 130, 200–214. doi:10.1016/j.resconrec.2017.11.027
- Bhusal, S., Li, X., & Wen, H. (2011). Evaluation of effects of recycled concrete aggregate on volumetrics of hot-mix asphalt. Transportation Research Record: Journal of the Transportation Research Board, 2205, 36–39. doi:10.3141/2205-05
- Bhusal, S., & Wen, H. (2013). Evaluating recycled concrete aggregate as hot mix asphalt aggregate. Advances in Civil Engineering Materials, 2(1), 20120053. doi:10.1520/acem20120053
- Buss, A. F. (2014). Investigation of sustainable pavement technologies evaluating warm mix asphalt using recycled asphalt materials. doi:10.31274/etd-180810-854
- da Conceição Leite, F., Dos Santos Motta, R., Vasconcelos, K. L., & Bernucci, L. (2011). Laboratory evaluation of recycled construction and demolition waste for pavements. Construction and Building Materials, 25(6), 2972–2979. doi:10.1016/j.conbuildmat.2010.11.105.
- Ismail, S., & Ramli, M. (2013). Engineering properties of treated recycled concrete aggregate (RCA) for structural applications. Construction and Building Materials, 44, 464–476. doi:10.1016/j.conbuildmat.2013.03.014
- Katz, A. (2004). Treatments for the improvement of recycled aggregate. Journal of Materials in Civil Engineering, 16(6), 597–603. doi:10.1061/(ASCE)0899-1561(2004)16:6(597)
- Kong, D., Lei, T., Zheng, J., Ma, C., Jiang, J., & Jiang, J. (2010). Effect and mechanism of surface-coating pozzalanics materials around aggregate on properties and ITZ microstructure of recycled aggregate concrete. Construction and Building Materials, 24(5), 701–708. doi:10.1016/j.conbuildmat.2009.10.038
- Kou, S. C., & Poon, C. S. (2010). Properties of concrete prepared with PVA-impregnated recycled concrete aggregates. Cement and Concrete Composites, 32(8), 649–654. doi:10.1016/j.cemconcomp.2010.05.003
- Lee, C.-H., Du, J.-C., & Shen, D.-H. (2012). Evaluation of pre-coated recycled concrete aggregate for hot mix asphalt. Construction and Building Materials, 28(1), 66–71. doi:10.1016/j.conbuildmat.2011.08.025
- Li, J., Xiao, H., & Zhou, Y. (2009). Influence of coating recycled aggregate surface with pozzolanic powder on properties of recycled aggregate concrete. Construction and Building Materials, 23(3), 1287–1291. doi:10.1016/j.conbuildmat.2008.07.019
- Malešev, M., Radonjanin, V., & Marinković, S. (2010). Recycled concrete as aggregate for structural concrete production. Sustainability, 2(5), 1204–1225. doi:10.3390/su2051204
- Mills-Beale, J., & You, Z. (2010). The mechanical properties of asphalt mixtures with recycled concrete aggregates. Construction and Building Materials, 24(3), 230–235. doi:10.1016/j.conbuildmat.2009.08.046
- Motter, J. S., Miranda, L. F. R., & Bernucci, L. L. B. (2015). Performance of hot mix asphalt concrete produced with coarse recycled concrete aggregate. Journal of Materials in Civil Engineering, 27(11), 04015030. doi:10.1061/(asce)mt.1943-5533.0001284
- Paranavithana, S., & Mohajerani, A. (2006). Effects of recycled concrete aggregates on properties of asphalt concrete. Resources, Conservation and Recycling, 48(1), 1–12. doi:10.1016/j.resconrec.2005.12.009
- Pérez, I., Pasandín, A. R., & Medina, L. (2012). Hot mix asphalt using C&D waste as coarse aggregates. Materials & Design (1980–2015), 36, 840–846. doi:10.1016/j.matdes.2010.12.058
- Pérez, I., Toledano, M., Gallego, J., & Taibo, J. (2007). Mechanical properties of hot mix asphalt made with recycled aggregates from reclaimed construction and demolition debris. Materiales de Construcción, 57(285), 17–29. doi:10.3989/mc.2007.v57.i285.36
- Pourtahmasb, M. S., & Karim, M. R. (2014). Performance evaluation of stone mastic asphalt and hot mix asphalt mixtures containing recycled concrete aggregate. Advances in Materials Science and Engineering, 2014, 1–9. doi:10.1155/2014/902307
- Purushothaman, R., Amirthavalli, R. R., & Karan, L. (2014). Influence of treatment methods on the strength and performance characteristics of recycled aggregate concrete. Journal of Materials in Civil Engineering, 27(5), 04014168. doi:10.1061/(asce)mt.1943-5533.0001128
- Rafi, M. M., Qadir, A., & Siddiqui, S. H. (2011). Experimental testing of hot mix asphalt mixture made of recycled aggregates. Waste Management and Research, 29(12), 1316–1326. doi:10.1177/0734242X10370379
- Rodríguez, G., Alegre, F. J., & Martínez, G. (2007). The contribution of environmental management systems to the management of construction and demolition waste: The case of the autonomous community of Madrid (Spain). Resources, Conservation and Recycling, 50(3), 334–349. doi:10.1016/j.resconrec.2006.06.008
- Sarsam, S. I. (2016). Comparative assessment of tensile and shear behavior of warm and hot mix asphalt concrete. Scientific research gate. International Journal of Engineering Papers, 1(2), 1–8. Retrieved from http://www.aiscience.org/journal/ijamr
- STCCM. (2018). State trading company for construction materials. Iraqi Ministry of Trading. Retrieved from http://www.tcm.mot.gov.iq/PageViewer.aspx?id=77
- Tam, V. W. Y., Tam, C. M., & Le, K. N. (2007). Removal of cement mortar remains from recycled aggregate using pre-soaking approaches. Resources, Conservation and Recycling, 50(1), 82–101. doi:10.1016/j.resconrec.2006.05.012
- Tamura, M., Noguchi, T., & Tomosawa, F. (2002, October). Life cycle design based on complete recycling of concrete. Proceeding of the first fib congress, Osaka, Japan.
- Tsujino, M., Kitagaki, R., Noguchi, T., Nagai, H., & Kunieda, Y. (2008). Completely recyclable concrete of aggregate-recovery type by using microwave heating technology. The 3rd ACF International Conference-ACF/VCA (pp. 239–522), Vietnam.
- Wong, Y. D., Sun, D. D., & Lai, D. (2007). Value-added utilisation of recycled concrete in hot-mix asphalt. Waste Management, 27(2), 294–301. doi:10.1016/j.wasman.2006.02.001
- Zulkati, A., Wong, Y. D., & Sun, D. D. (2012). Mechanistic performance of asphalt-concrete mixture incorporating coarse recycled concrete aggregate. Journal of Materials in Civil Engineering, 25(9), 1299–1305. doi:10.1061/(ASCE)MT.1943-5533.0000668