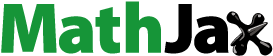
Abstract
This work investigates the physical, thermal and mechanical properties of thermal insulating bricks produced from Ghanaian red anthill clay (RAC) reinforced with sawdust, rice husk and their combinations. Mineralogical and chemical compositions using X-ray diffractometer (XRD) and X-ray fluorescence (XRF) techniques, respectively, were performed on the samples. 5, 10, 15 and 20 wt. % of reinforcements were used and the fabricated bricks were fired at 1200°C. Apparent porosity, bulk density, linear shrinkage, thermal conductivity, resistance to thermal shock and compressive strength of the samples were investigated. Results showed that the RAC composed of 52.35% silica and 31.16% alumina with a mineralogical composition of mainly quartz, kaolinite and iron oxide. Apparent porosity, linear shrinkage and resistance to thermal shock increased with an increase in weight percent of the additives while bulk density, thermal conductivity and compressive strength decreased with an increase in weight percent of additives. Results obtained indicated that the materials studied satisfy the physical, thermal and mechanical properties requirement for use as refractory material with the potential of improving the efficiency of refractory materials. Hence, these waste materials can be used in a sustainable manner for more productive applications.
PUBLIC INTEREST STATEMENT
Industrial furnaces are devices used to provide heat for processes. These furnaces are used for processes which operate at temperatures above 650°C. Due to their high temperatures of operation, they are designed such that heat generated is retained within the furnace. The efficiency of retaining the heat depends on the insulated enclosures EMPLOYED in the furnace design. Several materials have been used as refractory materials for heat retention in these furnaces. This study utilised various waste materials such as red anthill clay deposits, sawdust and rice husk in the construction of the refractory material. Results obtained indicated that the materials studied to satisfy the physical, thermal and mechanical properties requirement for use as refractory material. The waste materials also have the potential of improving the efficiency of refractory materials. Hence, these waste materials can be used in a sustainable manner for more productive applications.
1. Introduction
Industrial furnaces have been the backbone of metallurgical companies for ages. Metallurgical industries use these furnaces in their day-to-day processing of various metals. The furnaces use supplied heat energy from external sources to transform metallic ores into various useful products at elevated temperatures. However, efficiencies of these furnaces are not at their maximum. This deficiency is mostly attributed to energy leakages from the furnaces. Several researchers are looking at ways of improving the efficiencies of the various parts that make up these furnaces (Bonilla-Campos et al., Citation2019; Royo et al., Citation2018; Sadik et al., Citation2014; Wang et al., Citation2019). One of such parts is the refractory. A refractory must be able to withstand sudden changes in temperatures, conserve heat and must have low coefficient of thermal expansion. It should also be able to withstand the action of abrasive or corrosive solids, liquids or gases at high temperatures (Akinwekomi et al., Citation2012). Refractories are therefore used to provide linings for high-temperature furnaces, ovens, reactors and ladles to prevent escape of heat to the surrounding environment (Ajala & Badarulzaman, Citation2016; Gupta, Citation2016). Numerous materials have been used in the fabrication of the refractory materials (Sadik et al., Citation2014). However, all of these materials are still not able to completely trap the supplied heat within the furnace system (Ajala & Badarulzaman, Citation2016; Hadała et al., Citation2017; Sardeshpande et al., Citation2010).
Refractories are fabricated from several natural and synthetic materials (Wachtman & Lam, Citation1959). Ceramic materials are the major class of materials mainly used in their fabrications. These ceramic materials are inorganic, porous, non-metallic, heterogeneous; and thermally stable mineral aggregates, binder phase and additives (Akinwekomi et al., Citation2012; Olajide et al., Citation2015; Osarenmwinda & Abel, Citation2014). They are mainly used in the form of bricks and hence require higher binder content. As such clayey ceramic materials have been utilized in this regard for some time (Olajide et al., Citation2015). Different varieties and sources of clays have been used to produce refractory bricks. Their properties mostly depend on their source and the type of the clay. The different properties of the clays result in different heat losses to the surrounding environment when used as refractory materials. The raw materials used for the manufacturing of several refractory bricks include kaolinite (Al2Si2O5(OH)4), magnesite (MgCO3), chromite (FeCr2O4) and other types of clays (Omowumi, Citation2001). Apart from been used in the fabrication of refractories, they are also used for producing silica bricks, fire bricks, aluminous fire bricks, siliceous bricks, and high alumina bricks (Olajide et al., Citation2015).
In Africa, large aluminosilicate (fireclay) and magnesite deposits exist. Hence, most refractories produced on the African continent are mainly from the fireclay and magnesite deposits (Omowumi, Citation2001). However, improvement in the energy leakages to the environmental needs to be improved. In the quest of searching for alternative materials, researchers are exploring incorporating additives into these local materials to prevent or minimize the heat losses during their use in high-temperature furnaces, ovens, reactors and ladles (Ajala & Badarulzaman, Citation2016; Khina et al., Citation2011; Pilipchatin, Citation2000). Other researchers are also studying ways on improving the properties of refractory bricks by utilizing different natural sources of clay deposits (Andrews et al., Citation2013; Asante-Kyei, Citation2019; Ndaliman, Citation2006; Sobrosa et al., Citation2017). One of such natural clay deposits is the anthill clay, which researchers have reported to possess good combination of thermal and mechanical properties for potential production of refractories (Asante-Kyei, Citation2019; Ndaliman, Citation2006).
An anthill is a composite of clay and other materials used by ants to build mounded nest out of dirt or sand for their shelter. Ants and their burrowing activities are always a nuisance to agriculture activities, buildings and rural dwellers leading to environmental disturbance (Eggleton et al., Citation1999). The utilization of anthills in the fabrication of other materials such as refractories has been studied (Ajala & Badarulzaman, Citation2016; Akinwekomi et al., Citation2012; Khina et al., Citation2011; Osarenmwinda & Abel, Citation2014). Their use requires the destruction of the shelters of the ants which subsequently lead to a decline in the ants’ population. Lower population means reduced environmental hazard from ants. Anthill clays are cemented by the saliva secreted by the ant workers (Popoola & Opayele, Citation2012). Their secretion is very sticky binding the clay particles together, thereby increasing the strength, hardness and refractoriness of the mounds. Anthills are available worldwide though they are abundant in Africa and Australia (Nwakonobi et al., Citation2014). The properties of anthill clays have been reported to strongly depend on the type of soil within their surrounding environment (Akinwekomi et al., Citation2012; Hulugalle, Citation1995) Hence, Ghanaian anthill clays are likely to differ in properties from other anthill clay deposits. Also, not much studies have been carried out on utilising the properties of anthill clays and some additives to improve the efficiency of refractories (Nwakonobi et al., Citation2014).
Research works on the use of additives in anthill clay to enhance the clay’s refractory characteristics are ongoing (Akinwekomi et al., Citation2012; Hassan et al., Citation2014; Ndaliman, Citation2006; Nwakonobi et al., Citation2014; Ogunsemi et al., Citation2018). Some of the additives currently been used to enhance anthill clay’s refractoriness include graphite and asbestos (Ndaliman, Citation2006), bentonite and pulverised glass waste (Ogunsemi et al., Citation2018), high aluminium cement (Akinwekomi et al., Citation2012), saw dust (Hassan et al., Citation2014) and rice husk ash (Nwakonobi et al., Citation2014). Sawdust and rice husk are pore-inducing additives, which implies that when integrated into products, they generate pores and this helps to make the materials porous to satisfy the necessary insulating property. Refractory characteristics, for example, linear shrinkage, apparent porosity, and thermal shock resistance have all been enhanced by adding such additives (Hassan et al., Citation2014; Nwakonobi et al., Citation2014).
This work investigated the optimum volume fractions of sawdust, rice husk and their combinations in reinforcing Ghanaian red anthill clay. The reinforced refractories have a potential for being used as liners in high-temperature furnaces. The reinforcements act as pore inducers in creating the right environment needed in the refractories for the retention of the thermal energy generated during the heating and cooling of high-temperature furnaces. The use of these additives will help to handle waste through reuse and therefore promote cleanliness of the surroundings. It is anticipated that the new formulated material produced from anthill clays and pore inducers will provide improved thermal insulation and mechanical properties ideal for high-temperature liners. A series of property analyses were performed on the fabricated thermal insulating bricks.
2. Materials and methods
2.1. Materials
Red anthill clay (RAC) obtained at Kotei, a suburb of the Oforikrom Metropolitan Assembly in Kumasi, Ghana (Latitude N0639ʹ52.5ʹ’ Longitude W001
33ʹ47.4ʹ’) was used in this study. The soil obtained from this suburb falls within the Birimian basin and is made up of metamorphosed sediments added with metamorphosed tuff and lava. The area is also believed to have large masses of indistinguishable granites and gneisses. The site where the RAC was obtained is occupied by soils developed on granite and phyllites (Andrews et al., Citation2013).
Due to the hard nature of the anthill structure (Figure )), samples were obtained using an axe-shaped hoe. This resulted in the production of lumps of RAC which was further processed. Rice husk and sawdust additives were used. The ground rice husk and sawdust samples are shown in Figure . The rice husk was obtained from a rice farm in Ejisu, Ghana and the sawdust obtained from a small-scale sawmill industry in Anloga, also a suburb of the Oforikrom Metropolitan Assembly in Kumasi, Ghana.
2.2. Processing of raw materials
The flowchart for the various stages employed in the study is shown in Figure . RAC obtained was crushed and ground with the help of mortar and pestle. Sorting and picking of unwanted materials were also carried out. Afterwards, the ground RAC was sieved with a 2 mm mesh sieve (ASTM number 10). The oversized clay particles were re-crushed and re-sieved. The rice husk and saw dust were also milled to obtain the ground rice husk and ground saw dust, respectively. The ground rice husk and the saw dust were then sieved separately using a sieve opening of 1 mm (ASTM number 18) to obtain the required particle sizes. Powdered RAC with and without additives were carefully mixed to obtain the right plastic shape using less than 35 wt.% of water. Particle sizes of RAC and additives obtained were consistent with the work reported by El Halim and El Baroudy (Citation2014).
2.3. Characterisation of anthill clay
The RAC samples were characterized with respect to chemical composition, mineralogical, liquid limit, plastic limit and plastic index.
2.3.1. Chemical analysis of RAC
The chemical composition of the raw RAC and the fired samples in terms of major oxides (SiO2, Al2O3, Fe2O3, MnO, MgO, CaO, Na2O, K2O, TiO2 and P2O5 in wt. %) and trace elements (Zr, V, Ba, Pb, Rb, Cr, Ni, Zn, Sr and Y in ppm) were determined using an X-ray fluorescence (XRF) analysis. Samples passing through 75m mesh were used for all XRF analyses. 10 g of the sample and 0.9 g of wax were weighed and thoroughly mixed. The mixture was poured into the sample cup of the homogeniser and shaken for 5 minutes. The homogenised sample was compressed using a compressor sample holder and a weight of 50 tons. The pellet formed was removed and labelled. The labelled pellet was then placed in the sample holder of the XRF machine and analysed.
2.3.2. Mineralogical analysis of RAC
The mineralogy of the raw RAC and the fired bricks were determined by an X-ray diffraction (XRD) fitted with a PANalytical X’Pert PRO diffractometer using disoriented powder samples. The representative of the various clay samples were pulverized separately and 5 g of each was collected for the XRD analysis. A control unit operating at 40 kV, and iron filtered Cukα radiation at 30 mA, 2Ө range from 5 to 70 degrees, size 0.01 degrees and a scan speed of 1,000 degrees/min was employed.
2.3.3. Liquid limit tests
The liquid limit (LL) tests were performed in conformance with ASTM D4318-00. The RAC samples were air-dried and sieved. 200 g of the sample passing 425 µm mesh was collected and mixed thoroughly with distilled water to form a homogeneous paste that required 35 blows of the Casagrande apparatus to close the standard groove. The paste was left to stand for 24 hours to ensure uniform distribution of moisture. It was then remixed thoroughly before the test.
Portion of the paste was placed in the cup of the Casagrande apparatus, squeezed down and spread into position. It was trimmed till the maximum thickness depth reached 10 mm. A sharp groove was made along the diameter through the centerline of the cam follower. The cup was then dropped from a height of 10 mm by turning the crank at the rate of two-revolutions/sec, until the two halves of the soil cake came in contact with the bottom of the groove. The number of blows as the two halves of the soil cake came in contact with the bottom of the groove was recorded. More water was added to samples with blows exceeding 25. When the consistency of the mixture was such that after 25 blows, the groove was closed at a distance of 1.25 cm, the moisture contents corresponding to these mixtures were determined. The moisture content determined using EquationEquation (1)(1)
(1) was taken as the liquid limit (Astm, Citation2010).
For each, three levels of blows (one which ranges from 25 to 35 drops, one for closure between 20 and 30 drops, and one trial for a closure requiring 15 to 25 drops) were recorded with their corresponding moisture contents.
2.3.4. Plastic limit tests
ASTM D4318-00 testing method was also used for the plastic limit (PL) tests. A portion of the RAC mix used for the liquid limit test was retained for the determination of plastic limit. A ball of the RAC paste was moulded and rolled on smooth flat surface until it was sufficiently dried. The samples were then divided into approximately four equal parts. Each of the parts was rolled into threads between the first finger and the thumb. The threads were then rolled between the tips of the fingers until the threads each reduced to about 3 mm. The crumbled RAC was then placed in the moisture container and the moisture content determined by finding the difference between the mass before and after oven-dried.
The crumbled RAC samples were placed in an oven and heated to a temperature of 110°C for 24 hours in accordance with Astm (Citation2010). After which, the dried weights of the samples were measured and recorded. The weights of the empty containers were also measured and recorded. The average water content of the samples contained in the containers were computed in accordance with ASTM D2216. The average of the two computations is the plastic limit.
2.3.5. Plasticity index
The plasticity index (PI) of the RAC mix is the difference between the LLs and their corresponding PLs which is calculated as (Astm, Citation2010):
2.4. Refractory brick preparation
2.4.1. Mixing formulation
The RAC and the admixtures (sawdust and/or rice husk) were mixed in the ratio of 0, 5, 10, 15 and 20 wt.% of the admixture and formed into a cubic shape each of length 2 mm. The mixture formulations are shown in Table . Pre-determined masses of the RAC, as well as the additives, were weighed using the Sartorius Practum 213–1s electronic weighing balance. Varying percentages of water not exceeding 35% were added to each batch to make it plastic and mouldable. Each of them was labelled. Samples were then left to age for 30 minutes as reported by Olajide et al. Citation2015. Particle size distributions of the RAC samples were determined and were used to classify the RAC samples.
Table 1. Mixing Formulations for Thermal Insulating Brick Preparation
2.4.2. Moulding
RAC bricks were moulded using wooden moulds having dimensions of 165 mm in length, 63.5 mm in height and 38 mm in width. Each batch was introduced into the mould using a vibrator to form the thermal insulating bricks. The vibrator ensured uniform distribution of additives in the RAC. The green bricks were arranged for subsequent processes as shown in Figure .
2.4.3. Drying and firing
Sample bricks were left to dry in the sun for one week in order to remove moisture and also to prevent sudden cracks during firing. The sun-dried samples were further dried in an electric oven (Heraeus D—6450 Hanau) at a temperature of 110°C for 24 h. The samples were left to cool. They were further fired to a temperature of 1200°C for 1 h in a Vecstar Model HF 2 electric furnace.
2.5. Physical properties characterization of thermal insulating bricks
2.5.1. Apparent porosity test
The apparent porosity of the dry samples was determined in accordance with the method used by Kipsanai et al. Citation2017. The samples lengths, widths, and heights were measured using a Vernier calliper and the sample volumes (V) calculated. The weights (W1) of the samples were recorded. The test samples were immersed in water for 24 hours, removed and cleaned before weighing. The final weights were recorded as W2. Apparent porosities in percentages were then obtained from each sample from the relation in EquationEquation (3)(3)
(3) (Folaranmi, Citation2009; Kipsanai et al., Citation2017):
2.5.2. Bulk density test
The weights (W1) of the dry samples were recorded. The bulk volumes of the samples were estimated using their respective dimensions. The bulk densities were obtained by dividing each sample’s weight by its calculated volume as indicated in EquationEquation (4)(4)
(4) (Folaranmi, Citation2009).
2.6. Mechanical characterization of RAC bricks
A compressive strength test was conducted according to Olajide et al. Citation2015. The Blackhawk, 23 TONF, Model RC 250 0 41 92 B compressive strength tester was used. Samples were mounted and loads applied axially at uniform rates. The maximum loads which were applied prior to the fracture of the thermal insulating bricks were recorded. The compressive strengths in kg/ were the maximum pressure shown by the gauge dial which were read off the tester.
2.7. Thermal properties characterization of bricks
2.7.1. Linear shrinkage test
This test was performed to determine the dimensional stability of the samples after a specified period of time and temperature change, and the test method was in accordance with the ASTM C-326 standard for testing the linear shrinkage of refractory material (Chima et al., Citation2017). On the surface of the test samples, points 50 mm apart were marked. The test samples were dried in the oven at a temperature of 110°C for 24 hours. The distances between the marked points were measured as new length (L1). The dried test samples were then fired and the new measurement recorded as the fired length (L2).
The linear shrinkage was calculated using EquationEquation (5)(5)
(5) (Folaranmi, Citation2009; Kipsanai et al., Citation2017):
2.7.2. Thermal shock (spalling) resistance test
The resistance to thermal shock was measured according to Chima et al. (Citation2017) and in line with ASTM C-484. The test samples were thoroughly dried, placed in a furnace and heated at a uniform rate until the furnace temperature reached 1200°C. The heated samples were removed and cooled in air for 10 minutes after which they were observed for cracks. Samples without cracks were reheated in the furnace for a further 10 minutes after which they were cooled for an additional 10 minutes. Reheating, cooling, and observation of cracks cycle proceeded until there were the presence of cracks. The number of complete cycles that created visible cracks in each sample was recorded and was used to establish the thermal shock resistance.
2.7.3. Thermal conductivity test
The thermal conductivity values of the samples were determined using the Hot Disk 2500 S thermal conductivity testing machine. Two flat samples of thickness 25 mm each with smooth surfaces were prepared with a sample placed on the plate below the sensor (film of Kapton with radius 6.394 mm) and the other sample above the sensor such that the sensor is totally covered, forming a sample-sensor-sample sandwich. The piece was clamped firmly together and placed on the hot disk unit and then turned on. The sample was subjected to a 25.00 mm probing depth and 0.5 W heating power for a 40 s period. The software was then used to calculate the thermal properties of the samples.
3. Results and discussion
3.1. X-ray fluorescence
The chemical composition of the raw RAC sample obtained from XRF is presented in Table . It can be seen that major elements such as Si, Al and Fe were present in both the raw and fired samples in varying ratios. These elements play a significant role in the refractory properties of thermal insulating bricks. Minor elements such as Mg, P, S, K, Ti and Mn were also identified, which have significant effects on the hardness of the refractory bricks when subjected to heat. The presence of certain oxides such as Fe2O3, K2O and MgO in clay minerals act as fluxes to reduce the temperature needed for formation of glassy material in the brick body (Liew et al., Citation2004). This glassy material could influence the densification behaviour of the refractory brick during firing.
Table 2. Chemical Composition of Anthill Clay Samples
The chemical composition of the raw RAC showed the constituents being made up of 52.35% silica (SiO2), 31.1 6% alumina (Al2O3), 4.49% iron oxide (Fe2O3) and other traces. The high silica and alumina contents of the raw RAC makes it suitable for use as a refractory (Sadik et al., Citation2014). Clays with higher silica content surpassing 46.51%, have the capacity to withstand fairly high temperatures which indicates that this RAC sample can be used at elevated temperatures with superior refractory properties (Liew et al., Citation2004). Alumina content of 31.16% in the RAC sample also meets the requirement for it to be used in the manufacture of a refractory. The higher the alumina content in a material, the higher its refractoriness (Lee et al., Citation2001). The content of silica and alumina was within the standard range of 46–62 and 25–39 for SiO2 and Al2O3, respectively, in accordance with the work published by Yami and Umaru (Citation2007). The chemical composition of the RAC can be said to be due to modification of soil particles by the ants/termites through their extremely alkaline gut system with a pH value of 12 (Snyder, Citation1949). As expected, the firing of the bricks did not change the concentration of major and trace elements.
3.2. X-ray diffraction
Figure shows XRD results of the RAC and fired anthill clays. It can be seen that, the raw RAC contains kaolinite, hematite with an important amount of quartz. The peak intensity and the number of quartz (SiO2) are higher than that of kaolinite and hematite. The existence of the free quartz is due to excess silica as indicated in Table . This suggests that the raw RAC deposit is mainly made of kaolinite and free quartz.
The XRD result for the fired anthill clay sample was also found to contain quartz, hematite and mullite (3Al2O3.2SiO2) as a result of transformation of the kaolinite into the new phases. Kaolinite is the main mineral associated with quartz and the SiO2/Al2O3 ratio obtained from the raw anthill clay was greater than 1 as indicated in Table . Also, the Al2O3 content (~ 30%) is associated with kaolinite in clay samples. During firing, the kaolinite (Al2O3.2SiO2.2H2O) is first transformed to metakaolinite (Al2O3.2SiO2) and then to spinel (2Al2O3.3SiO2) before the formation of mullite. Mullite is the only stable intermediate phase in the alumina–silica system at atmospheric pressure. However, during firing, mullite transforms first at 1150 ºC with high amounts associated with clays containing kaolinite (Escalera et al., Citation2012).
Firing kaolinite at 1200 ºC will transform it to mullite according to the reactions:
The intensity of hematite remained approximately the same after firing at 1200°C as shown in the XRD pattern of hematite in Figure . It can be observed that the addition of additives (sawdust and rice husk) does not change the mineralogical composition of the raw RAC. This suggests the presence of identical phases. It can also be seen that the intensity of the phases does not change in the presence of additives. However, during firing with organic-based additives, Demir et al. (Citation2005) reported the release of extra heat within the brick, resulting in the decrease in the total energy needs of the furnace.
The textural class of the RAC studied is presented in Table . The analysis indicates that the RAC or the soil in the immediate environment is characterized by a lean clay texture.
Table 3. Particle Size Distribution of the Anthill Clay
3.3. Liquid limit, plastic limit and plastic index
Results of the Atterberg plasticity tests conducted on the RAC sample showed that the raw RAC samples have liquid limit (LL) of 30.5%, plastic limit (PL) of 24.67% and plasticity index (PI) of 5.83% (Table ). The low plastic index of the raw RAC sample can be attributed to the relatively high content (>50%) of sand and silt in the clay. This low PI implies that the RAC can easily be used in extrusion or manual processing of the clay. The PI and LL values obtained prove that the RAC samples are clayey materials with low plasticity. This, therefore, suggests that the RAC samples have good plasticity requirement needed for making refractory. This will provide the needed plasticity characteristics when mixed with water, which will help the anthill clay be formed into any required shapes.
Table 4. Atterberg Limits
3.4. Product description (after firing)
The zero percent sawdust/rice husk bricks were light brownish in colour (control). The brown colour of the control samples was due to their low iron oxide content (Figure )). When mixed with sawdust or rice husk, the colour changed to dark-brown as shown in Figure ). On firing the green bricks containing the additives, colour initially changed to black (Figure )) and eventually to a red-hot brick at 1200 ºC (Figure )). The initial black colour was due to burning of the sawdust and rice husk admixtures. Drying and firing of the anthill clay brick samples removed water and collapsed the hydrated crystal structures within it. The biomass also burnt off to create pores within the structure. Sawdust burns at relatively low firing temperatures (between 200°C and 650°C) as reported by Guo et al. (Citation2015). This process of firing induces a thermally activated, irreversible phase changes in the constituents of the anthill clay (Edomwonyi-Otu et al., Citation2010). The final-fired brick was reddish in colour.
3.5. Apparent porosity
Figure shows the apparent porosity results of the tested samples. The control sample had an apparent porosity of 24.77% which represents the lowest while the highest was 52.95% for anthill clay with 20 wt.% sawdust. The apparent porosity observed for the control sample can be attributed to the mineralogy, internal brick structure and geometry of the anthill clay. During firing of the control sample, there is the possibility of certain gases been released as a result of decomposition of some of the constituents present in the clay. The released gases are likely to create pores within the samples as they exit. Also, elimination of voids or pores through liquid phase formation that begins at temperatures above 900°C do contribute to the lowest porosity obtained for the raw RAC. The liquid phase formation has a tendency to reduce void or pores through filling the inter-granular spaces in the clay samples. The highest apparent porosity value was observed for the anthill clay sample with 20 wt. % sawdust. This may be due to the geometry and size of the sawdust particles used (Bergström et al., Citation2008).
Figure also shows the dependence of apparent porosity of the tested bricks with additive addition. The trends show that voids in the fired samples increase with the amount of additives. Sawdust addition shows the highest apparent porosity followed by sawdust + rice husk and finally rice husk additives. This is because the additive contents burn off during the firing process and create the pores or voids. The number of pores or voids formed increases as the weight of the additives increases. Also, the higher efficiency of combustion of sawdust compared to rice husk as reported by Permchart and Kouprianov (Citation2004) supports the trend obtained in the study.
The percentage apparent porosity of the control sample and that of 5 wt.% rice husk falls within the recommended values (10–30%) for internationally accepted standard for refractory bricks according to Chesters and Chesters (Citation1973) while that of the composite clay with additives excluding the 5 wt.% rice husk exceeds the range. It is interesting to note that formulations with sawdust only and combination of sawdust and rice husk did not fall within the acceptable range of apparent porosity. This can be attributed to the high combustion efficiency of sawdust and hence making available complete pores in the fabricated samples (Permchart & Kouprianov, Citation2004).
3.6. Bulk density
The bulk density values of the tested samples are shown in Figure . Bulk density for the control samples without additives was obviously the highest (1.86 g/cm3) which falls within the internationally accepted values (1.71–2.1 g/cm3) (Chesters & Chesters, Citation1973). The lower bulk densities of the samples with the additives are as a result of the lower densities of the sawdust and rice husk (Chopra, Citation1981). However, it can be observed that the bulk densities for samples with additives are slightly lower than the internationally accepted values for dense firebricks which must be expected.
It can also be observed that the anthill clay with various weight percent additives falls below the recommended bulk density range for refractory bricks according to (Chima et al., Citation2017). Anthill clay with 20 wt.% sawdust had the lowest bulk density due to its high porosity (Figure ) than all the tested samples. An increase in weight percent additives resulted in porous samples that are less dense (lightweight) and hence a decreasing trend for bulk density.
The use of 20 wt.% sawdust, rice husk and their combinations decreased the densities of the fired bricks. The calculated bulk density of the RAC sample was found to be 1.86 g/cm3 and the theoretical densities of sawdust reported by Aigbomian and Fan (Citation2013) is 0.21 g/cm3 and that of rice husk reported by Chopra (Citation1981) is 0.13 g/cm3 The measured bulk densities of RAC reinforced with 20 wt.% sawdust, 20 wt.% rice husk, and 20 wt.% sawdust + rice husk were 1.07, 1.23 and 1.15 g/cm3, respectively. It can also be observed in Figure that anthill clay with rice husk showed the highest bulk density followed by the combination of rice husk and sawdust. Anthill clay reinforced with sawdust had the lowest apparent density. The expected bulk densities from the rule of mixtures must be 1.506, 1.490, and 1.498 for 20 wt.% sawdust, 20 wt.% rice husk, and 20 wt.% sawdust + rice husk, respectively. This pattern is however in disagreement with the obtained data. This variation is due to the trend in porosity as observed in Figure . Increasing the weight percent of sawdust results in the introduction of more pores compared to the same weight percent increase in rice husk. Hence, the higher the porosity, the lower the apparent density as shown in the trend in Figure which resulted in the lower apparent density for the 20 wt.% sawdust addition.
Additionally, sawdust and/or rice husk does not alter the mineralogy of the clay composite as presented in Table . Increasing their content may result in low or no vitreous phase formation during firing. However, as sawdust or rice husk and its combination were increased, the amount of pores or voids increased, and hence reducing the bulk density of the clay composite. Sawdust addition to anthill clay was, therefore, more effective in terms of bulk density and porosity then rice husk.
3.7. Linear shrinkage
Figure shows the observed shrinkage during the firing cycles of anthill clay bricks containing varying amount of sawdust and rice husk additives. The bricks were initially dried to reduce the shrinkages that occur during firing cycles. This linear shrinkage strongly depends on the amount of water content present in the anthill clay and additives. Therefore, the fired linear shrinkages observed in Figure can be ascribed to loss of organic matter of the rich additives. The obtained fired linear shrinkage was highest (3.58%) for the rice husk reinforced anthill clay sample at 20 wt. %; and lowest (1.1%) for the control sample. The linear shrinkage for the tested samples is within the recommended range of less than 10% for fireclay as reported by Omowumi (Citation2001). The low linear shrinkage values are desirable in refractories since it prevents heat losses from the furnace. It also minimises cracking and warping of the brick from cyclic firing as reported by Umaru, 2015.
It is also evident from Figure that firing shrinkage increased with increase in the amount of sawdust, rice husk as well as combination of sawdust and rice husk. This trend is in agreement with what Olajide et al. Citation2015 reported earlier. It confirms that, the higher the shrinkage, the denser and less porous the material. The observed relatively higher values of firing shrinkage with decreasing amount of additives may be attributed to conversion of additives into ashes. The smaller the amount of additives the smaller the ashes which evidently decrease the volume of the anthill fired brick. However, the higher values of linear shrinkage may also be attributed to the migration of gases as a result of decomposition of certain compounds (Darweesh & El-Meligy, Citation2014). These decompositions of compounds as well as the rearrangement of grains/particles form a more compact solid texture in comparison to the green RAC brick which caused shrinkage.
The anthill clay samples with rice husk additives showed higher linear shrinkage probably due to less dimensional stability of rice husk than the sawdust. Since rice husk reinforced anthill clay shrinks more than sawdust reinforced anthill clay, the rice husk reinforced composite tend to have lower porosity (Nnuka & Okunoye, Citation1991). Also, the lower linear shrinkage of the control sample indicates that the moisture content of the raw anthill clay is low. It can clearly be seen from Figure that sawdust was a relatively more effective additive than the rice husk and combination of sawdust and rice husk in reducing the fired shrinkage behaviour of the anthill clay brick. This led to an increase in linear shrinkage by 18%—144% with an increase in sawdust content from 5 to 20 wt. %.
3.8. Thermal shock (spalling) resistance
The resistance to thermal shock values is presented in Figure . It can be observed that the thermal shock resistance improved significantly with increasing weight percent of additives. This is because an increase in weight percent additives translates to an increase in a number of pores which makes the samples more porous. Porous samples are impervious to thermal shock and hence an increasing trend for thermal shock resistance. Anthill clay with 15 wt.% and 20 wt.% additives falls within the acceptable range of 20–30 cycles for refractory fireclay bricks according to Mathew and Owoeye (Citation2016) while that of the control sample, 5 wt.%, and 10 wt.% additives fell below the acceptable range.
From the study, the anthill clay reinforced with sawdust samples showed the highest thermal shock resistance, followed by anthill reinforced by sawdust-rice husk samples and lastly anthill reinforced rice husk samples. The addition of sawdust to anthill clay creates more pores after firing as evident in the apparent porosity results. This enabled the sawdust added anthill clay samples to exhibit the highest thermal shock resistance and thermal insulation. The high thermal shock-resistance enables bricks to withstand rapid changes in temperature, due to their improved expansion tolerance.
3.9. Thermal conductivity
Thermal conductivity tests are useful for insulating applications where thermal gradients dictate the use of a material for refractory applications. The thermal conductivity results obtained as indicated in Figure shows that the control sample had the highest thermal conductivity of 0.55 W/m.K. This decreased by 9% and 47%, with the addition of 5 and 20 wt. % sawdust, respectively. This confirms that thermal conductivity depends not only on the properties of anthill clay but also on the geometry and amount of the additives. For all the tested samples, thermal conductivity decreased rapidly with increasing weight percentage of additives. This can be ascribed to the increase in pores arising from the burning off of the additives that created a vacuum. This reduces the heat flow rate in the porous medium causing a decrease in thermal conductivity of the samples. As such, the weight percentage increase in additives improves the sample’s thermal insulating properties as larger pores are created. This indicates that anthill clay with additives is more insulating than the unreinforced clay since the additives are primarily responsible for the creation of thermally insulating pores.
However, increasing porosity in an effort to reduce the thermal conductivity has detrimental effect on the mechanical properties of the fired brick. The results showed that rice husk was a more effective additive in improving the insulating behaviour of the anthill clay brick. This resulted in a decrease in thermal conductivity by 27%—58% while the rice husk content increased from 5 wt.% to 20 wt.%. The thermal conductivity of the test samples falls within the standard value of 0.01–1.1 W/mK for refractory fireclay bricks as reported by Amkpa et al. (Citation2017).
3.10. Compressive strength
Figure shows the observed variation in compressive strength of anthill clay bricks reinforced with sawdust, rice husk and sawdust-rice husk. It can be observed that the compressive strength of test samples fired at 1200°C decreased with an increase in the amount of additives. As expected, the compressive strengths were observed to decrease from 1.82 to 0.74 MPa, 2.32 to 1.05 MPa and 2.01 to 0.90 MPa, when sawdust, rice husk and sawdust-rice husk additives were increased from 5 to 20 wt.%, respectively. The decrease in compressive strength with an increase in additive content is obviously due to increased porosity during the process. It is a well-known fact that for ceramic-based materials, strength decreases with an increase in porosity. The presence of pores functions as a stress raiser or concentrate for failure and adversely affects strength by decreasing the load-exposed cross-sectional region (Akinwekomi et al., Citation2012). With an increase in weight percent of additives, the amount of pores increases accordingly. This means more stress concentrates for failure and therefore a decrease in strength. The compressive strength of the control sample and anthill clay samples reinforced with 5, 10 and 15 wt.% of sawdust, rice husk and sawdust-rice husk additives were within the recommended range of 0.981–6.867 MPa while that of anthill clays reinforced with 20 wt.% of sawdust and sawdust-rice husk additives were below this requirement suggested by Kipsanai et al. (Citation2017).
3.11. Implication of results
The increasing cost of thermal insulating and improved thermal efficiency of high-temperature furnace manufacturing has resulted in the search for cost-effective materials with good combination of properties. This work has shown the contributions of pore-inducers produced from wastes on physical, mechanical and thermal properties of Ghanaian red anthill clay deposits. A wide variety of pores creators for porous thermal insulating bricks have been widely investigated for production of various insulation bricks (Hassan et al., Citation2014; Hossain & Roy, Citation2020; Hassan et al., Citation2019; Sutcu, Citation2015). In this study the inclusion of rice husk, sawdust and their combinations in varying proportions showed that majority of the property values fell within the acceptable range for use as thermal insulating materials. This implies that utilizing the optimum proportion, pores can be created in an anthill clay matrix to provide the right property requirements needed for the production of thermally insulating fire clay.
The promising characteristics such as reduction in thermal conductivity and bulk density of the anthill clay matrix suggest that these waste materials can provide alternative materials for the preparation of insulation refractories. The thermal shock resistance and mechanical properties results have shown that the RAC has adequate strength and can maintain its structural integrity when subjected to fluctuating high temperatures. More so, the unique mechanical properties of the RAC are evident in the ability of anthill clay to maintain its structural integrity no matter the type of weather they are exposed to. The good strength property of RAC is proven to be as a result of the ant’s saliva that enhances the binding power of the clay and sand (Kipsanai et al., Citation2017).
Rice production is among the top producing crops grown worldwide. After harvesting and processing of the rice, about 20% rice husk is produced from rice paddy which ends up polluting the environment (Pode, Citation2016). Although these rice husk are organic in nature, they are classified as pollutants due to the duration they take to decompose (Hossain & Roy, Citation2019). Also, huge amount of sawdust is produced worldwide as a by-product of woodworking operations. This by-product is not fully utilized resulting in its stockpile and hence harmful to the environment. The unused sawdust is mostly burnt and this also leads to further environmental issues. Therefore, the utilization of the sawdust and rice husk and their combinations as pore-formers in RAC has environmental benefits. Also, utilizing these waste materials in the production of the fire clay liners will lead to the manufacturing of environmental-friendly materials.
The use of anthill clay deposits as potential refractory materials will also solve the environmental problems and damage of cultivated lands caused by anthill clays. The thermal, physical and mechanical results obtained in this study imply that 15% wt of sawdust reinforcement provides a good combination of properties to fire clay liners. Moreover, the use of these additives will help in waste management through reuse and hence improves the cleanliness of the environment.
Furthermore, the relatively low cost of sawdust, rice husk and RAC compared to the conventional materials used in producing refractories will help to reduce the overall cost of manufacturing high-temperature furnaces. These materials give an economic advantage in the production of fire clays than other conventional materials. Finally, clay materials have been reported to be abundantly available in Ghana and will therefore make the production of the thermally insulating fire clays from the RAC sustainable (Asamoah et al., Citation2018; Williams & Haydel, Citation2010). Therefore, the results obtained imply that the RAC and its additives studied will not only improve the performance of the fire clay but also used for the designing and manufacturing of environment-friendly, sustainable and economical fire clay liners.
4. Conclusion
The physical, mechanical and thermal properties of Ghanaian red anthill clay were investigated in this study. The following conclusions were drawn:
The apparent porosity of the formulated bricks increased from 24.77 to 52.95 %, 24.77 to 43.15%, and 24.77% to 40.73%, respectively, with the same increasing amount of sawdust, rice husk and sawdust-rice husk additives.
The bulk density values for all the formulations fell below the standard value of 1.98 g/cm3 for fire clay bricks. It can be concluded that the addition of sawdust causes pronounced changes in the bulk density than rice husk and sawdust—rice husk reinforcements.
The use of additives increased the linear shrinkage of the RAC up to about 223%. The linear shrinkage values also fall within the recommended range of less than 10% for fireclay as reported by Omowumi (Citation2001).
Thermal conductivity decreased from 0.55 to 0.32, 0.23 and 0.25 W/mK with increasing amount of sawdust, rice husk and sawdust-rice husk additives, respectively. The thermal conductivity values lie in the range acceptable for materials suitable for use in fire clay bricks.
The compressive strength of the anthill clay was reduced by 73%, 62% and 68% on addition of sawdust, rice husk and sawdust-rice husk, respectively. The compressive strength results for all tested samples were within the standard limit of 0.981 to 6.867 MPa for fire clay.
All the samples studied exhibited thermal shock resistance above the 20 cycles minimum requirement for use as fireclay.
The red anthill clay with 15 wt.% sawdust provided good combination of physical, thermal and mechanical properties within the standard values for refractory fireclay bricks for furnace lining.
Declaration of Interests
The authors declare that they have no conflict of interest.
Acknowledgements
The authors are grateful to Kwame Nkrumah University of Science and Technology, Kumasi, Ghana, for making available facilities for carrying out the research work.
Additional information
Funding
Notes on contributors
E. K. Arthur
Dr. E. K. Arthur is a Lecturer at the Materials Engineering Department, Kwame Nkrumah University of Science and Technology (KNUST), Ghana. He holds both MSc and PhD Degrees in Materials Science and Engineering from the African University of Science and Technology, Nigeria. His areas of publication include surface engineering, mechanical metallurgy, advanced composite materials, ceramic processing, materials selection in mechanical design and heavy metal removal from soil and water.
E. Gikunoo
Dr. E. Gikunoo is a Senior Lecturer at the Materials Engineering Department, KNUST, Ghana. He holds a BSc in Metallurgical Engineering from KNUST, MS in Mechanical Engineering from University of Saskatchewan, Canada, and PhD in Mechanical Engineering from the Louisiana State University, USA. He has published on composite materials, waste utilisation, point-of-care devices, mechanical metallurgy, and environmental pollution among others.
References
- Aigbomian, E. P., & Fan, M. (2013). Development of wood-crete building materials from sawdust and waste paper. Construction and Building Materials, 40, 361–20. https://doi.org/10.1016/j.conbuildmat.2012.11.018
- Ajala, A. J., & Badarulzaman, N. A. (2016). Thermal conductivity of aloji fireclay as refractory material. International Journal of Integrated Engineering, 8(3), 16–20. https://publisher.uthm.edu.my/ojs/index.php/ijie/article/view/1343
- Akinwekomi, A. D., Omotoyinbo, J. A., & Folorunso, D. (2012). Effect of high alumina cement on selected foundry properties of anthill clay. Leonardo Electronic Journal of Practices and Technology, (21), 37–46. http://lejpt.academicdirect.org/A21/get_htm.php?htm=037_046
- Amkpa, J. A., Badarulzaman, N. A., & Aramjat, A. B. (2017). Influence of sintering temperatures on physico-mechanical properties and microstructure of refractory fireclay bricks. International Journal of Engineering and Technology, 8(6), 2588–2593. https://doi.org/10.21817/ijet/2016/v8i6/160806214
- Andrews, A., Adam, J., & Gawu, S. K. (2013). Development of fireclay aluminosilicate refractory from lithomargic clay deposits. Ceramics International, 39(1), 779–783. https://doi.org/10.1016/j.ceramint.2012.06.091
- Asamoah, R., Nyankson, E., Annan, E., Agyei-Tuffour, B., Efavi, J., Kan-Dapaah, K., Apalangya, V., Damoah, L., Dodoo-Arhin, D., & Tiburu, E. (2018). Industrial applications of clay materials from ghana-A review, 34(4), 1719–1734. http://dx.doi.org/10.13005/ojc/340403
- Asante-Kyei, K. (2019). Design and fabrication of gas kiln using local materials to compose its refractory bricks and mortar. Journal of Arts and Humanities, 8(3), 73–84. http://dx.doi.org/10.18533/journal.v8i3.1584
- Astm, D. (2010). Standard test methods for liquid limit, plastic limit, and plasticity index of soils.
- Bergström, D., Israelsson, S., Öhman, M., Dahlqvist, S.-A., Gref, R., Boman, C., & Wästerlund, I. (2008). Effects of raw material particle size distribution on the characteristics of Scots pine sawdust fuel pellets. Fuel Processing Technology, 89(12), 1324–1329. https://doi.org/10.1016/j.fuproc.2008.06.001
- Bonilla-Campos, I., NIETO, N., Del Portillo-Valdes, L., Egilegor, B., Manzanedo, J., & Gaztañaga, H. (2019). Energy efficiency assessment: Process modelling and waste heat recovery analysis. Energy Conversion and Management, 196, 1180–1192. https://doi.org/10.1016/j.enconman.2019.06.074
- Chesters, J. H., & Chesters, J. (1973). Refractories: Production and properties. Iron and Steel Institute London.
- Chima, O., Nwoye, C., & Nnuka, E. (2017). Enhancement of refractory properties of blended clay with groundnut shell and rice husk additives. American Journal of Engineering Research (AJER), 6(6), 218–226. https://d1wqtxts1xzle7.cloudfront.net/53764291/ZC0606218226.pdf?149923928 2=&response-content-disposition=inline%3B+filename%3DEnhancement_of_Refractory_Properties_of.pdf&Expires =1601205034&Signature=Dg016IefASnWD3OQVNb4maPj6RerDuZ71Da~p3GRqi~ljlMkkSdGU1mXlflg7CKJXmHpreRlJ89IPYNvd3~h4HiLULg0qy1njWwhXRxbBLDpQ~RL~ikzP73bZ4xyv3Oz1m4Bct5x90B78CNV5311FSDM3ju26-uqh8m3gt5D6bqAlspziiGoSUbObo8hEfOfV1h46VAlH7I49Dl9Td8fD9Oz~KAlWU0k9VgJ2BHTHgGH1K7gXiAkvLUHIdHT-nmsmusHK5wq~JdA9h8ty~Q070VGfS~dAXtX6Ex2CShTBEsRxGfzvAKWYzVOHvTLHI8-9zw-BgEF7Ehwo8-7kZYoQw__&Key-Pair-Id=APKAJLOHF5GGSLRBV4ZA
- Chopra, S. (1981). Cementitious binder from rice husk: An overview. Cement Research Institute.
- Darweesh, H., & El-Meligy, M. (2014). Non-conventional lightweight clay bricks from homra and kraft pulp wastes. Journal of Chemistry and Materials Research, 2(2), 123–129.
- Demir, I., Baspinar, M. S., & Orhan, M. (2005). Utilization of kraft pulp production residues in clay brick production. Building and Environment, 40(11), 1533–1537. https://doi.org/10.1016/j.buildenv.2004.11.021
- Edomwonyi-Otu, L., Aderemi, B., & Ofoku, A. (2010). Studying the effect of kaolin calcination temperature and dealumination time on alum yield from kankara kaolin. African Journal of Natural Sciences, 13, 69–74.
- Eggleton, P., Homathevi, R., Jones, D., Macdonald, J., Jeeva, D., Bignell, D., Davies, R., & Maryati, M. (1999). Termite assemblages, forest disturbance and greenhouse gas fluxes in Sabah, East Malaysia. Philosophical Transactions of the Royal Society of London. Series B, Biological Sciences, 354(1391), 1791–1802. https://doi.org/10.1098/rstb.1999.0521
- El Halim, A., & El Baroudy, A. (2014). Influence addition of fine sawdust on the physical properties of expansive soil in the Middle Nile Delta, Egypt. Journal of Soil Science and Plant Nutrition, 14(2), 483–490.
- Escalera, E., Antti, M.-L., & Odén, M. (2012). Thermal treatment and phase formation in kaolinite and illite based clays from tropical regions of Bolivia. IOP Conference Series: Materials Science and Engineering Volume 31, 6th EEIGM International Conference on Advanced Materials Research 7–8 November 2011. Nancy, France: European School of Materials Engineering (EEIGM).
- Folaranmi, J. (2009). Effect of sawdust additive on the properties of clay. Australasian Journal of Technology, 13(1), 53–56.
- Guo, M., Song, W., & Buhain, J. (2015). Bioenergy and biofuels: History, status, and perspective. Renewable and Sustainable Energy Reviews, 42(February), 712–725. https://doi.org/10.1016/j.rser.2014.10.013
- Gupta, R. (2016). Fuels, furnaces and refractories. PHI Learning Pvt. Ltd.
- Hadała, B., Malinowski, Z., & Rywotycki, M. (2017). Energy losses from the furnace chamber walls during heating and heat treatment of heavy forgings. Energy, 139(November), 298–314. https://doi.org/10.1016/j.energy.2017.07.121
- Hassan, A. M., Moselhy, H., & Abadir, M. F. (2019). The use of bagasse in the preparation of fireclay insulating bricks. International Journal of Applied Ceramic Technology, 16(1), 418–425. https://doi.org/10.1111/ijac.13094
- Hassan, M., Yami, A., Raji, A., & Ngala, M. (2014). Effects of sawdust and rice husk additives on properties of local refractory clay. The International Journal of Engineering and Science, 3(8), 40–44.
- Hossain, S. S., & Roy, P. (2019). Fabrication of sustainable insulation refractory: Utilization of different wastes. Boletín de la Sociedad Española de Cerámica y Vidrio, 58(3), 115–125. https://doi.org/10.1016/j.bsecv.2018.09.002
- Hossain, S. S., & Roy, P. (2020). Sustainable ceramics derived from solid wastes: A review. Journal of Asian Ceramic Societies, 1–26. https://doi.org/10.1080/21870764.2020.1815348
- Hulugalle, N. (1995). Effects of ant hills on soil physical properties of a Vertisol. Pedobiologia, 39, 34–41.
- Khina, B., Volochko, A., & Zhukova, A. (2011). Obtaining heatproof coatings on fireclay refractories by SHS. Glass and Ceramics, 68(1–2), 65. https://doi.org/10.1007/s10717-011-9323-y
- Kipsanai, J. J., Namango, S. S., & Muumbo, A. M. (2017). A study of selected Kenyan anthill clays for production of refractory materials. International Journal of Scientific and Research Publications, 7(9), 169–179.
- Lee, W., Vieira, W., Zhang, S., Ahari, K. G., Sarpoolaky, H., & Parr, C. (2001). Castable refractory concretes. International Materials Reviews, 46(3), 145–167. https://doi.org/10.1179/095066001101528439
- Liew, A. G., Idris, A., Wong, C. H., Samad, A. A., Noor, M. J. M., & Baki, A. M. (2004). Incorporation of sewage sludge in clay brick and its characterization. Waste Management & Research, 22(4), 226–233. https://doi.org/10.1177/0734242X04044989
- Mathew, G. O., & Owoeye, S. S. (2016). Characterization of Abaji clay deposits for refractory applications. Leonardo Electronic Journal of Practices and Technologies, 15(29), 115–126.
- Ndaliman, M. B. (2006). Refractory properties of termite hills under varied proportions of additives. Leonardo Electronic Journal of Practices and Technologies, 9(9), 161–166.
- Nnuka, E., & Okunoye, P. (1991). Industrial potentials of ukpor clay. The Nigerian Metallurgical Society Annual Conference Proceedings, Aladja. 34–39.
- Nwakonobi, T., Anyanwu, C., & Tyav, L. (2014). Effects of rice husk ash and termite hill types on the physical and mechanical properties of burnt termite clay bricks for rural housing. Global Journal of Pure and Applied Sciences, 20(1), 57–64. https://doi.org/10.4314/gjpas.v20i1.9
- Ogunsemi, B., Ikubanni, P., Agboola, O., Adediran, A., Olawale, O., Ibikunle, R., Ake, M., & Oki, M. (2018). Investigative study of the effects of certain additives on some selected refractory properties of ant-hill clay for furnace lining. International Journal of Civil Engineering and Technology (IJCIET), 9(12), 761–772. https://eprints.lmu.edu.ng/id/eprint/2380
- Olajide, O. I., Michael, O. B., & Terna, T. D. (2015). Production and characterization of aluminosilicate refractory brick using Unwana Beach silica sand, Ekebedi and Unwana clays. British Journal of Applied Science & Technology, 5(5), 461. https://doi.org/10.9734/BJAST/2015/12532
- Omowumi, O. (2001). Characterization of some Nigerian clays as refractory materials for furnace lining. Nigerian Journal of Engineering Management, 2(3), 1–4.
- Osarenmwinda, J., & Abel, C. P. (2014). Performance evaluation of refractory bricks produced from locally sourced clay materials. Journal of Applied Sciences and Environmental Management, 18(2), 151–157. https://doi.org/10.4314/jasem.v18i2.1
- Permchart, W., & Kouprianov, V. I. (2004). Emission performance and combustion efficiency of a conical fluidized-bed combustor firing various biomass fuels. Bioresource Technology, 92(1), 83–91. https://doi.org/10.1016/j.biortech.2003.07.005
- Pilipchatin, L. (2000). Sintering of fireclay-kaolin mixtures with refractory clay. Glass and Ceramics, 57(5–6), 212–214. https://doi.org/10.1007/BF02681282
- Pode, R. (2016). Potential applications of rice husk ash waste from rice husk biomass power plant. Renewable and Sustainable Energy Reviews, 53(January), 1468–1485. https://doi.org/10.1016/j.rser.2015.09.051
- Popoola, K., & Opayele, A. (2012). Morphometrics of Macrotermes bellicosus (African mound termite)(Blattodea: Termitidae) and the impact of its saliva amylase on the strength of termitarium soil. New York Science Journal, 5(12), 207–216. http://ir.library.ui.edu.ng/handle/123456789/891
- Royo, P., Ferreira, V. J., López-Sabirón, A. M., García-Armingol, T., & Ferreira, G. (2018). Retrofitting strategies for improving the energy and environmental efficiency in industrial furnaces: A case study in the aluminium sector. Renewable and Sustainable Energy Reviews, 82(Part 2, February), 1813–1822. https://doi.org/10.1016/j.rser.2017.06.113
- Sadik, C., El Amrani, I.-E., & Albizane, A. (2014). Recent advances in silica-alumina refractory: A review. Journal of Asian Ceramic Societies, 2(2), 83–96. https://doi.org/10.1016/j.jascer.2014.03.001
- Sardeshpande, V. R., Shendage, D., & Pillai, I. R. (2010). Thermal performance evaluation of a four pan jaggery processing furnace for improvement in energy utilization. Energy, 35(12), 4740–4747. https://doi.org/10.1016/j.energy.2010.09.018
- Snyder, T. E. (1949). Catalog of the termites (isoptera) of the world. In Catalog of the termites (isoptera) of the World.
- Sobrosa, F., Stochero, N., Marangon, E., & Tier, M. (2017). Development of refractory ceramics from residual silica derived from rice husk ash. Ceramics International, 43(9), 7142–7146. https://doi.org/10.1016/j.ceramint.2017.02.147
- Sutcu, M. (2015). Influence of expanded vermiculite on physical properties and thermal conductivity of clay bricks. Ceramics International, 41(2), 2819–2827. https://doi.org/10.1016/j.ceramint.2014.10.102
- Wachtman, J., Jr, & Lam, D., Jr. (1959). Young’s modulus of various refractory materials as a function of temperature. Journal of the American Ceramic Society, 42(5), 254–260. https://doi.org/10.1111/j.1151–2916.1959.tb15462.x
- Wang, Y., Huang, J., Su, C., & Li, H. (2019). Furnace thermal efficiency modeling using an improved convolution neural network based on parameter-adaptive mnemonic enhancement optimization. Applied Thermal Engineering, 149(February), 332–343. https://doi.org/10.1016/j.applthermaleng.2018.12.048
- Williams, L. B., & Haydel, S. E. (2010). Evaluation of the medicinal use of clay minerals as antibacterial agents. International Geology Review, 52(7–8), 745–770. https://doi.org/10.1080/00206811003679737
- Yami, A. M., & Umaru, S. (2007). Characterization of some Nigerian clays as refractory materials for furnace lining. Continental Journal of Engineering Sciences, 2, 30–35. https://d1wqtxts1xzle7.cloudfront.net/3916038/30-35.pdf?response-content-disposition=inline%3B+filename%3DCHARACTERIZATION_OF_SOME_NIGERIAN_CLAYS.pdf&Expires=1601205107&Signature=KEgOBW-flOa9MVjk5CkPh8Xz8PD3MjuSfSlyK4Re3sDwkPZCbU8nG0sioD~22YXA~ml4BtZKhHfGKvbPN704GqBM9J6dsiSGFOAIXmWLqo8YAeSq4TH1p0Luh-BxOI~OqCxHwlmwcoIwzj2UEHKe0x8CIR7VDWy0KvKgZywE~vXjT4Yo9lNQm5NknGnMu~aU1hd1~wFhXGsEbuJ8YCAEl2rAABZ1Uk6u4~KPeLYmAVjH0cDt11ciW8erAQgITeJOyfmqp5dsGyVpAPD75uvVV5dzxOhdQaynlyIgZ~zt-JDE6DukAFwy~sNT060TfuaBMSzAWiya7sA8ypCP8Of9Fg__&Key-Pair-Id=APKAJLOHF5GGSLRBV4ZA