Abstract
AISI4340 steel is the medium carbon low-alloy steel has got excellent prominence as a construction material. This steel is spheroidised on heating to the intercritical temperature range by different time intervals with the objective of increasing the number and fineness of the spheroids of cementite particles. A 9 hours, spheroidisation shows better spheroids of cementite particles. To study the effect of initial room temperature structure on spheroidisation primary heat treatments like normalising and hardening are carried out for as-bought steel. Tensile property (yield strength, ultimate tensile strength and percentage elongation), hardness (Rockwell C scale) and micro-structural features and micro-hardness of micro-phases (ferrite and cementite) are studied. A continuous reduction in the tensile strength, hardness and improvement in ductility, is observed with the increase in spheroidisation time is observed in all the spheroidisation paths. Also, increased spheroidisation time shows a lesser aspect ratio for spheroids. The micro-structure shows partial spheroidisation in all the conditions with more number of spheroids in normalised condition and finer size in hardened. Drastic reduction in strength and hardness values are observed in the hardened condition during spheroidisation.
Public interest statement
Steels are widely used as construction materials. It is essential to control the properties of the steel during production so that it has a superior combination of mechanical properties. It is important to improve the machinability of the steel so that it can easily be machined to the required shape and size. “Spheroidization” is a heat treatment process which improves the ductility of the steel and makes it a machinable alloy. Hardness is one of the mechanical properties which gets altered after the heat treatment given to the steel. Hence, it is essential to select the optimum parameters for spheroidizing so that steel acquires required properties. This article reports the relationship between the variation of hardness and micro-phases of the steel when it is subjected to spheroidizing heat treatment. Thus, it helps to obtain the steel with required properties by carrying out the heat treatment process “Spheroidization”.
1. Introduction
AISI4340 steel is the most common form of low-alloy steel which has moderate ductility due to medium carbon content and the presence of negligible alloying elements. An increase in carbon content results in higher hardness and strength with less ductility and toughness (Sidney, Citation2005). In day-to-day applications, it is mandatory to enhance the strength of the material to meet certain objectives (such as cuttability, formability and ductility), and a possible route to meet these challenges. One of the possible paths to alter the property is heat treatment (Arruabarrena et al., Citation2014). It is obligatory to use pre-treatment, normalising before main heat treatment (spheroidisation) to convert the initial room temperature structure into the standard form so that the result may be justifiable as per the demand (Gurumurthy et al., Citation2018). The persistence of spherodisation is to enhance cuttability, so that metal attains a considerable level of surface finish (Singh, Citation2012). The various conventional heat treatment processes employed for this category of steels are annealing, normalising, hardening, tempering, and surface hardening (Harisha et al., Citation2018). Among the various special treatments available, spheroidisation is nearer to annealing, aims to improve ductility and toughness with the elimination of continuous pattern of carbides along the grain boundary (Lü et al., Citation2016). The slow cooling rate used in annealing produces coarser phases of ferrite and pearlite. In hypereutectoid steel, the same treatment yields massive carbide and pearlite. The massive carbide is a harder phase present around the pearlite as a discrete or continuous form. This massive carbide phase has a sharp-cornered prismatic colony, offers severe resistance for machining (Calik et al., Citation2010; Lee et al., Citation2013). The spheroidisation process develops blunt cornered nearly round or spheroidal geometrical shape carbides in the ferritic matrix which makes the machining easier (Wei et al., Citation2006). It is also observed that in medium carbon steel (0.4 to 0.6 wt% C) spheroidisation develops partially globular cementite phases. Spheroidised structure is desirable for the development of the easy machinable condition, with periodically broken discrete chips to yield better surface finish (Rajan et al., Citation2012).
Spheroidisation focuses on carbide phase morphology change, depends on the dispersion of carbon in the lattice by enabling easy movement paths for the atoms by heating to a temperature around the critical temperature of that grade of steel (Lv et al., Citation2013). Spheroidisation phenomenon is accomplished by the controlled softening process which dominates the micro-structure to cause recovery and recrystallization with intentional carbide morphological changes (Singh, Citation2012). Hence, this secondary treatment helps the manufacturing process easier and improves product performance.
During austenitisation, the pro-eutectoid softer ferrite phase in the given pearlite colony swiftly transforms into austenite compared to the dissolution rate of cementite. The ferrite to austenite transformation on heating is a diffusion-controlled immense polymorphic conversion that occurs quickly (Herbs et al., Citation2016; Moleejane et al., Citation2014). This provides inhomogeneous austenite with the carbon potential little higher at locations where initially cementite was present. To obtain homogeneous austenite from this condition, the steel is to be heated to the stable austenite temperature range and held at that constant temperature for necessary phase alterations (Senthilkumar & Ajiboye, Citation2012). On cooling and maintaining isothermal condition at the soaking temperature for the critical duration, the dissection of lamellar cementite into dowels or band shapes happens to be the intermediate step of spheroidisation process (Biswas et al., Citation2017; O’Brien & Hosford, Citation2002). Protracted time at that temperature enhances further breakup of the pearlitic structure into cementite and cementite reforms slowly into the globular form (Oleg Sherby et al., Citation1985; Rajan et al., Citation2012).
The intention of the spheroidisation is to assure fine and uniform distribution of spheroidal carbides in the ferrite matrix, which will make the material softer and tougher. Increasing the size of the globules, matrix partially gives up its internal energy which increases the machinability. Globular structure of carbides embedded in the pearlitic of the ferritic matrix improves the cold workability and allows heavy deformation required for deep cold drawing. Generally, spheroidising treatment of carbon-steels containing carbon quantity below 0.4 wt% is not recommended for some material removal operations because the material is gummy and may stick to the rake surface of cutting tools. This is the ideal treatment for medium and high carbon, low or medium alloy steels.
The objective of the present investigation is to correlate mechanical characterization with phase morphology and novelty of the work is a study on the effect of initial room temperature structures on spheroidisation process and introduction of micro-hardness for micro-phase analysis in AISI4340 steel.
2. Methodology
2.1. Chemical analysis of steel specimen
Spectroscopic analysis of AISI4340 steel is carried out. This type of steel in heat-treated condition provides good wear resistance, ductility, and shock resisting properties. Considerable addition of Cr, Si and Mo makes the steel harder. depicts the alloying elements present in AISI4340 steel used here.
Table 1. Composition of AISI4340 steel
Specimen preparation
The hardness (ASTM E24 procedure) and tensile specimens (ASTME8/E8M) are prepared in Computer Numerical Control (CNC) machines.
Circular cross-section specimens are prepared for hardness and micro-structure tests. Specimens are polished using diamond paste embedded velvet cloth mounted on the disc polisher. The specimen is critically etched in NITAL solution, rinsed with distilled water to stop over-etching, acetone is used to clean the top surface and dried. Rockwell hardness tester is used for hardness measurement. Vicker’s hardness tester is used for micro-hardness of individual phases present at room temperature. The micro-structure is recorded using a Scanning Electron Microscope (SEM).
2.2. Heat treatment of AISI4340 Steel
Spheroidisation is performed with and without prior heat treatment, i.e. in as-bought (no prior treatment) or normalised/hardened (prior heat treatment) conditions. The effect of heat treatment is challenged in terms of tensile strength, hardness and micro-structure. Notation A, N, and H are used to designate the initial room temperature structures before spheroidisation treatment as as-bought, normalised and hardened respectively. Numbers 1, 3, 6 and 9 are used to represent the spheroidisation time as 0, 3, 6 and 9 hours respectively.
Muffle furnace is used for heating the specimen. The first set of as-bought specimens is kept at 850°C for 30 minutes, followed by a quick transfer to another furnace (less than 10 seconds) which is retained at 725°C for 10 minutes at the same temperature. The process is completed by rapid heating to 740°C and maintaining isothermally for different time durations (3, 6 and 9 hours) for sheroidisation (Bahrami Abbas et al., Citation2005) followed by air cooling. The inhomogeneity generated by complex heating and cooling cycle supports spheroidisation rate so quickly that the cycle time is reduced. Spheroidisation is restricted to 3-, 6- and 9-hour durations followed by slow air cooling to room temperature to analyse the time factor influence on the phase morphology.
The second set of specimens is heated for normalising to 900°C for 2 hours, allowed to cool to room temperature in still air condition. Spheroidisation cycle is then carried out on the normalised structure and spheroidised as explained for the first set of specimens. The third set of samples is heated at 900°C for 2 hours, quenched in water to room temperature to form martensite structure followed by further spheroidisation cycle as explained earlier. shows a block diagram of the methodology (Heat treatment) of the entire process used in this study.
3. Results and discussion
3.1. Tensile test analysis
To determine the effect of initial room temperature phase morphology on spheroidisation and mechanical properties, specimens are subjected to tensile test. The average of three consistent readings is considered for recording the tensile strength. The results have shown that, during spheroidisation, the tensile strength distribution pattern with respect to time shows a continuous decrease with an increase in treatment time ().
Figure 2. YS and UTS variation of AISI4340 at different initial room temperature structures and spheroidisation duration for (a) as-bought, (b) normalised and (c) hardened specimens
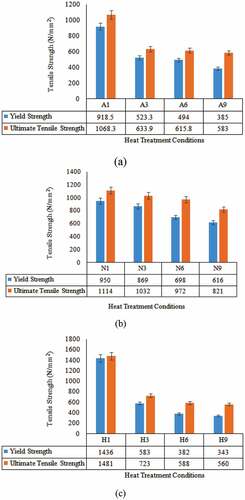
In the case of as-bought and normalised specimens, spheroidisation process makes the lamellar cementite change its geometry into discrete particles (break up) with continuous exposure for longer duration at the spheroidising temperature, the surface area of particles reduces for the given volume, i.e. spheroids are formed. Due to this process, stress relaxation takes place with the reduction in dislocations, grain boundary area, etc. to reduce tensile strength (Herbs et al., Citation2016).
The relationship between the yield strength and UTS remains the same during spheroidisation. During spheroidisation of the hardened specimen, a drastic reduction in strength is observed during the initial period of spheroidisation. This is due to the relaxation of thermal residual stresses present during spheroidisation, wherein spheroidisation acts like tempering, which relieves the residual stresses (Gurumurthy et al., Citation2018). Further, continuous processing for longer duration decreases the strength similar to as-bought or normalised specimens.
As-bought condition develops a coarse-grained structure with slightly inferior tensile properties compared to normalised one. As-bought structure has higher ductility and further soaking for a longer duration, the differences between YS and UTS increase, implies ductility increase (Chiteka, Citation2013). Even though there is a reduction in the tensile properties (YS and UTS) during spheroidisation, the difference between the YS and UTS value increases as the spheroidisation duration increases (). This implies that the ductility enhances during spheroidisation. This is because of the use of a coarser room temperature structure for spheroidisation. Normalised shows a gradual decrease in YS and UTS during spheroidisation compared to that of annealed ().
Unlikely, hardened shows excellent hardness. Even though the drastic reduction in strength is observed during the initial period of spheroidisation, compared to longer durations, the differences between YS and UTS in each successive step increase which indicates, the increase in softening effect ().
Among the different initial room temperature structures, the ductility of the as-bought specimen is maximum compared to the other two conditions. The lower ductility of the normalised specimen is due to the faster cooling rate during heat treatment. Hardened specimen shows the lowest ductility due to the formation of the martensitic structure as shown in . During spheroidisation, the increasing trend in ductility of all three initial room temperature structure conditions remains similar. Spheroidisation is the treatment that requires longer treatment time and during soaking, there is a decrease in the lattice defects especially dislocations (Sidney, Citation2005), which improves the ductility (). Moreover, in the normalised condition during spheroidisation, removal of residual stresses as well as a decrease in crystal imperfections, improves ductility (Patel & Chaudhari, Citation2015). Spheroidisation of a hardened specimen is similar to a long time tempering treatment, which relieves the residual stresses with a decrease in crystal defects, responsible for an increase in ductility (Singh, Citation2012).
3.2. Hardness test analysis
In all the three cases, a reduction in the hardness value of the spheroidised specimen during isothermal soaking () shows a similar pattern. An average of five consistent readings is considered for recording data. As stated in the tensile strength analysis, the reduction in hardness during isothermal holding at 740°C is related to the decrease in the crystal imperfections especially, dislocation density. Longer the spheroidisation time, more is the decrease in hardness due to the relaxation of material from crystal defects (Golanski, Citation2010).
Figure 4. Hardness variation at different initial room temperature structures and spheroidisation duration for (a) as-bought, (b) normalised and (c) hardened specimens
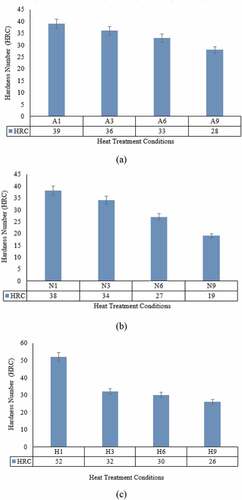
Hardness of normalised structure is in between as-bought and hardened and it follows the tensile property trend ( and ). As in the tensile test result, the hardness value is smaller in as-bought compared to the other two conditions (normalised and hardened). The gradual decrease in hardness is observed in both as-bought and normalised conditions during spheroidisation.
The hardened specimen shows a drastic reduction in the hardness value initially due to an ample reduction in the crystal defects and relaxation of residual stresses because spheroidisation acts as tempering (Moleejane et al., Citation2014). Further, continuous spheroidisation does not make much difference in hardness because prolonged isothermal holding than the critical duration will not cause further annihilation of the crystal imperfections (Sidney, Citation2005).
shows the VHN distribution among the micro-phases of specimens in different conditions. In as-bought and normalised, two sets of hardness values are clearly observed (lower, 173–186 VHN and higher 331–338 VHN) wherein normalised condition shows slightly higher hardness values (second row in ) as compared to as-bought (first row in ) which is due to the effect of faster cooling rate (Ndaliman, Citation2006). In first and second rows, lower hardness is of the ferrite micro-phase and higher hardness (Bold numbers) is that of cementite (Sidney, Citation2005). The corresponding higher value in normalised is due to the finer particle size of the constituent phases obtained by a faster cooling rate (Golanski, Citation2010).
Table 2. Micro-hardness (VHN) results for different phases
The hardened specimen shows almost the same values of hardness (Variation, 537–542 = 5 VHN), which implies that the hardened structure is a single phase (martensite). Generally, Martensite hardness in AISI4340 steel is 500 to 550 VHN (Singh, Citation2012). During spheroidisation (6 and 9 h), the lower hardness values (Variation, 339–335 = 4 VHN) are observed due to the sacrifice of higher hardness values (Variation, 528–523 = 5 VHN) in some locations, indicates the spontaneous precipitation of carbides from supersaturated solid solution, i.e. martensite. The number of carbide locations increases as the processing time increases from 6 to 9 hours (last row in ) shows spontaneous precipitation of carbides during the treatment. In as-bought and normalised also there is a continuous reduction in the hardness values of the corresponding phases during spheroidisation. It is the indication of continuous stress relaxation and annihilation of crystal defects due to continuous isothermal soaking (Ismail et al., Citation2016; Nikitin et al., Citation2019; RSengupta et al., Citation2019; Suryo et al., Citation2018)
3.3. Micro-structure analysis
3.3.1. Spheroidisation of as-bought specimen
As-bought specimen before the spheroidisation shows lamellar pearlite and pro-eutectoid ferrite as shown in . The pro-eutectoid ferrite and pearlitic colony are coarser in the as-bought specimen. During spheroidisation, the lamellar cementite breaks continuously so that the discrete cementite (carbides) particle slowly converts into a globular form. About 3-hour spheroidisation shows the initial stage of spheroidisation, wherein the surface area of cementite lamellae increases, i.e. pearlitic cementite long needle breaks slowly as the spheroidisation time increases (Lü et al., Citation2016). shows more number of spheroids compared to Figure representing the progress of spheroidisation. Still, some regions show incomplete (partial) spheroidisation.
3.3.2. Spheroidisation of normalised specimen
The normalised structure shows finer colonies of pearlite and pro-eutectoid phases () compared to as-bought. About 3-hour spheroidised specimen shows partial spheroidisation whereas 9-hour duration specimen gives better spheroidisation as shown in and c. The number of spheroids observed in the normalised condition is more compared to as-bought condition. At the same time, the spheroids are finer in normalised which increases tensile strength. This behaviour is very much observed in tensile results also. Specimen having more number of finer spheroids has better tensile property (Lv et al., Citation2013). It is reflected in the micro-structure also. Accordingly, 6 c has got more number of finer spheroids compared to 5 c condition.
3.3.3. Spheroidisation of hardened specimen
The hardened specimen shows a typical martensite (lath) structure of medium carbon steel (). About 3-hour spheroidisation shows spontaneous evolution of carbides from the supersaturated single phase martensite in the form of discrete (broken) particles (). About 9hour spheroidised shows further precipitation of carbides and decrease in l/d (length to a depth of phase) ratio (). A larger number of carbides are observed in the martensite structure during spheroidisation. The nucleation of these spheroids is possible from a large number of heterogeneous sites (crystal defects including dislocations) obtained by severe lattice distortion during martensite formation (Wei et al., Citation2006). Due to the nucleation of carbides, internal strain incurred in martensite during the diffusionless shear mechanism of phase transformation is relaxed (Lee et al., Citation2013). During continuous spheroidisation, l/d ratio of carbide particles decreases to reduce the free energy of the system.
4. Conclusions
AISI4340 steel is spheroidised as per the objectives and results confirmed the attainment of set objectives. Following conclusions are made from the analysis.
Increase in spheroidisation duration has resulted in decarese in YS and UTS, which is also similar in as-bought and normalised specimens. YS and UTS of normalized specimen show the higher value which is due to the refinement of grain size and formation of a large number of finer spheroids of carbide. The difference in YS and UTS of the hardened specimens shows smaller value, which is due to the increase in brittleness of the specimen.
Drastic reduction in the crystal imperfections during soaking has resulted in a severe reduction in the YS and UTS of the hardened specimen during early periods (3 h) of spheroidisation.
Hardness decrease pattern in as-bought and normalised conditions during spheroidisation remains the same even though higher hardness values are recorded in as-bought during spheroidisation stages. There is a drastic reduction in hardness value of the hardened specimen during initial periods of the spheroidisation, even though higher hardness values observed during hardening.
As-bought shows coarser-grained structure whereas normalised is finer. Lath martensitic structure is obtained in the hardened specimen. Spheroidised as-bought specimens shows a larger number of coarser spheroids whereas normalised shows more number of spheroids with finer size.
During spheroidisation (9 hours) of the hardened specimen, l/d (length to depth) ratio of carbide particles decreases. This is due to the reduction in surface area of the particle for the given volume.
In all the cases of spheroidisation, only partial spheroidisation is observed. Complete spheroidisation may take very long durations.
Nomenclature
AISI | = | American Iron and Steel Institute |
wt% | = | weight percentage |
CNC | = | Computer Numerical Control |
SEM | = | Scanning Electron Microscope |
YS | = | Yield Strength |
UTS | = | Ultimate Tensile Strength |
VHN | = | Vickers Hardness Number |
Additional information
Funding
Notes on contributors
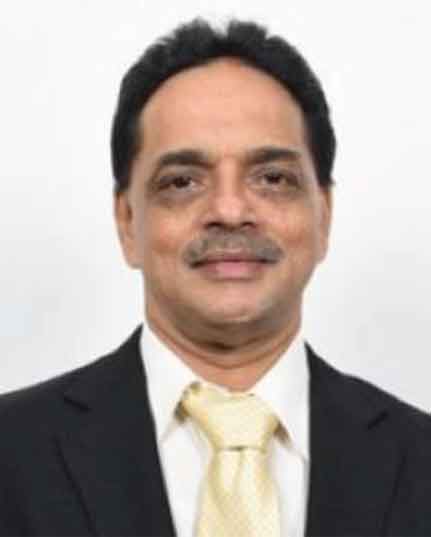
Harisha S R
Harisha S R is Assistant Professor in Mechanical & Manufacturing Engineering, MIT, MAHE, Manipal. He has about 9 years of experience in teaching.
Sathyashankara Sharma
Sathyashankara Sharma is working as Professor and Head in the Department of Mechanical & Manufacturing Engineering, MIT, MAHE, Manipal. He holds B.E. (Industrial and Production Engineering), M.Tech. (Materials Engineering) and Ph.D. (MaterialsEngineering) degrees. He has 33 years of teaching experience. His area of interest includes Engineering materials, Heat treatment of metals and composites, Machinability and Deformation behaviour of metals and composites. He has published more than 200 papers in journals and conferences.
Achutha Kini U
Achutha Kini U is Professor Mechanical & Manufacturing Engineering, MIT, MAHE, Manipal. He has about 30 years of experience in teaching.
Gurumurty B M
Gurumurthy B M is Assistant Professor in Mechanical & Manufacturing Engineering, MIT, MAHE, Manipal. He has about 9 years of experience in teaching.
Ananda Hegde
Ananda Hegde is Assistant Professor in Mechanical & Manufacturing Engineering, MIT, MAHE, Manipal. He has about 6 years of experience in teaching.
References
- Arruabarrena, A. J., . B., López, B., & Rodriguez-Ibabe, J. M. (2014). Influence of prior warm deformation on cementite spheroidization process in a low-alloy medium carbon steel. Metallurgical and Materials Transactions A, 45(3), 1470–14. https://doi.org/10.1007/s11661-013-2066-3
- Bahrami Abbas, A., Mousavi Anijdan, S. H. M., Golozar, M. A., Shamanian, M., & Varahram, N. (2005). Effects of conventional heat treatment on wear resistance of AISI H13 tool steel. Wear, 258(5–6), 846–851. https://doi.org/10.1016/j.wear.2004.09.008
- Biswas, P., Kundu, A., & Mondal, D. (2017). An experimental investigation on hardness and microstructure of heat treated EN 9 steel, IOP conf. Series: Materials Science and Engineering, 225, 1–6. https://doi.org/10.1088/1757-899X/225/1/012055
- Calik, A., Duzgun, A., Sahin, O., & Ucar, N. (2010). Effect of carbon content on the mechanical properties of medium carbon steels. Z. Naturforsch, 65(5), 468–472. https://doi.org/10.1515/zna-2010-0512
- Chiteka, K. (2013). Friction stir welding of high FSW machine carbon steel with excellent toughness and ductility. International Journal of Engineering Research and Technology, 2, 846–851. https://doi.org/10.1016/j.scriptamat.2010.03.060
- Golanski, G. (2010). Effect of heat treatment on the structure and properties of GX12CrMoVNbN9-1 cast steel. Archives of Materials Science and Engineering, 46(2), 88–97. http://www.amse.acmsse.h2.pl/vol46_2/4622.pdf
- Gurumurthy, B. M., Sharma, S. S., Kini, A. U., & Mansoor, S. I. (2018). Effect of preheat treatment structure on mechanical characterization of AISI 4340 ferrite bainite dual phase steel. International Journal of Mechanical Engineering and Technology, 9(8), 84–89. https://doi.org/10.18178/ijmerr.8.4.553-558
- Harisha, S. R., Sathyashankara Sharma, U., Kini, A., & Gowri Shankar, M. C. (2018). Study on spheroidization and related heat treatments of medium carbon alloy steels. MATEC Web of Conferences, 144(6), 02008. https://doi.org/10.1051/matecconf/201814402008
- Herbs, S., Schledorn, M., Maier, H. J., Milenin, A., & Nurnberger, F. (2016). Process integrated heat treatment of a microalloyed medium carbon steel: Microstructure and mechanical properties. Journal of Materials Engineering and Performance, 43, 37–42. https://doi.org/10.1007/s11665-016-2004-9
- Ismail, N. M., Khatif, N. A., Kecik, M. A., & Shahruddin, M. A. (2016). The effect of heat treatment on the hardness and impact properties of medium carbon steel, IOP conf. Series: Materials Science and Engineering, 114(1), 1–9. https://doi.org/10.1088/1757-899X/114/1/012108
- Lü, Z.-Q., Zhang, H.-F., Meng, Q., huawang, Z.-H., & Fu, W.-T. (2016). Effect of cyclic annealing on microstructure and mechanical properties of medium carbon steel. Journal of Iron and Steel Research International, 23(2), 145–150. https://doi.org/10.1016/S1006-706X(16)30026-7
- Lee, Y.-W., Son, Y.-I., & Lee, S.-J. (2013). Microstructure and mechanical properties of spheroidized D6AC steel. Materials Science and Engineering, 585, 94–99. https://doi.org/10.1016/j.msea.2013.07.040
- Lv, Z. Q., Wang, B., Wang, Z. H., Sun, S. H., & Fu, W. T. (2013). Effect of cyclic heat treatments on spheroidizing behavior of cementite in high carbon steel. Materials Science and Engineering, 574, 143–148. https://doi.org/10.1016/J.MSEA.2013.02.059
- Moleejane, C. M., Sanusi, K. O., Ayodele, O. L., & Oliver, G. J. (2014), “Microstructural features and mechanical behaviour of unalloyed medium carbon steel (EN8 steel) after subsequent heat treatment” WCECS, 22–24. San Francisco, USA.
- Ndaliman, M. B. (2006). An assessment of mechanical properties of medium carbon steel under different quenching media. AU Journal of Technology, 10(2), 100–104.
- Nikitin, E., Shumatbaev, G., Terenzhev, D., Sinyashin, K., & Rastergaev, E. (2019). New sintanyl phosphonates for protection of oil and gas pipelines from steel corrosion. Civil Engineering Journal, 5(4), 789–795. https://doi.org/10.28991/cej-2019-03091288
- O’Brien, J. M., & Hosford, W. F. (2002). Spheroidisation cycles for medium carbon steels. Metallurgical and Materials Transactions, 33A, 1255. https://doi.org/10.1007/s11665-997-0034-z
- Oleg Sherby, T., Oyama, D. W., Walser, K. B., & Wadsworth, J. N. M. I. (1985). Design of spheroidisation processing for ultra-high carbon steels containing Al. Journal of the Minerals, Metals and Materials Society, 37(6), 253–259. https://doi.org/10.1016/j.matdes.2005.08.008
- Patel, A. J., & Chaudhari, S. N. (2015). Effects of mechanical properties of medium carbon steels by tempering process at different temperature. International Journal of Advance Engineering and Research Development, 2(2), 185–191. https://doi.org/10.14445/22315381/IJETT-V9P350
- Rajan, T. V., Sharma, C. P., & Sharma, A. (2012). Heat treatment principles and techniques (2nd Edition ed.). PHI learning private limited.
- RSengupta, A., Gupta, R., & Biswas, A. (2019). Computational fluid dynamics analysis of stove systems for cooking and drying of muga silk. Emerging Science Journal, 3(5), 285–292. https://doi.org/10.28991/esj-2019-01191
- Senthilkumar, T., & Ajiboye, T. K. (2012). Effect of heat treatment processes on the mechanical properties of medium carbon steel. Journal of Minerals and Materials Characterization and Engineering, 11(2), 143–152. https://doi.org/10.4236/jmmce.2012.112011
- Sidney, A. H. (2005). Introduction to physical metallurgy (3rd Edition ed.). McGraw Hill.
- Singh, V. (2012). Heat treatment of metals (2nd Edition ed.). Standard publisher’s distributors.
- Suryo, S. H., Widyanto, S. A., Paryanto, P., & Mansuri, A. S. (2018). Hardness optimization of heat treatment process of bucket teeth excavator. Civil Engineering Journal, 4(2), 294–304. https://doi.org/10.28991/cej-030992
- Wei, S., Zhu, J., & Xu, L. (2006). Effects of vanadium and carbon on microstructures and abrasive wear resistance of high speed steel. Tribology International, 39(7), 641–648. https://doi.org/10.1016/j.triboint.2005.04.035