Abstract
This study aims to fabricate bio-composites of hydroxyapatite/shellac/sorghum as bone scaffold material in biomedical applications. Hydroxyapatite is made from bovine bone powder, while shellac is the end product from processing lice with adhesive properties, which are biodegradable and non-toxic. Furthermore, sorghum was used as a pore-forming material. The production of the materials was carried out using dry method which was sintered at a temperature of 1000°C. Subsequently, characterization of the bio-composites was carried out through X-Ray Diffraction, Scanning Electron Microscopy and Fourier Transform Infrared. The results of hardness and compression test were compared using pure hydroxyapatite and human bone as gold standard material. Furthermore, the biodegradation rate of these materials was also reported.
PUBLIC INTEREST STATEMENT
A biocomposite of hydroxyapatite/shellac/sorghum powder can be used as bone filler material in orthopedics field. A stirring process was carried out to mix the ingredients before being pressed and heated at a temperature of 1000°C. The specimens were tested and compared with pure hydroxyapatite and human bone as a gold standard material.
It was reported that the results of the SEM observation, EDX, XRD and FTIR tests showed that the material structure of this biocomposite is hydroxyapatite, which is the main element as a bone filler material. The biocomposites also have mechanical properties that are close to human bone as a gold standard material. The rate of biodegradation of materials is also reported to show that these materials are bioresorbable materials. A further development of the material will be focused on developing the compressive strength and pore interconnectivity.
1. Introduction
Hydroxyapatite (HA) is a crystalline molecule composed of phosphorus and calcium core, with molecular formula of Ca10(PO4)6(OH)2. By estimation, 65% of the mineral fraction in human bones consists of this molecule (Andika et al., Citation2016). It is also one of the bio-ceramic materials utilized in biomedical application, due to its empirical components being the same as materials present in the human bones and teeth (Sedyono & Tontowi, Citation2008). Furthermore, hydroxyapatite can be synthesized from several natural sources such as mammalian bones, clam shells, coral or eggshell (Suryadi, Citation2011).
The characteristics of hydroxyapatite are capable of adapting to the human body (biocompatible) as they can be integrated with human bones (bioactive) as well as stimulating its growth and formation (osteoconductive) (Fahimah et al., Citation2014). The porous variety in form of scaffold has better resorbable and osteoconductive properties compared to the solid ones; therefore, it is widely developed in biomedicine. Hydroxyapatite scaffold has wide surface area, which is useful for biological tissue cell adhesion and new bone phase growth (Ismawati et al., Citation2016).
Meanwhile, sorghum is a cereal plant cultivated and developed, especially in marginal and dry areas in Indonesia. It has the potential to be used as a constituent in manufacturing HA scaffold. Furthermore, it was selected because it is a grain with higher productivity (average 5–7 tons/harvest/ha) compared to rice, wheat and corn. In fact, this reaches 11 tons/ha; however, it is quite unfortunate that sorghum has only been used as a mixture in feeding livestock (Rufaizah, Citation2011).
Furthermore, this study introduced a new material as bioadhesive in biomaterials, namely shellac. It is natural polymer having the bioadhesive potential as a raw material to produce environment-friendly resins and is also shellac is a hardened lice secretion (Sharma et al., Citation2006). It is natural, renewable, robust, tough, non-toxic, and produces waterproof layer and commonly found in South Asia (Liu et al., Citation2008). Shellac has been widely used in the furniture, property, food, and cosmetics industries. However, its application in the biomaterial field is very minimal, even though it is a potential biomedical material (Srivastava & Thombare, Citation2017).
Therefore, in this study, hydroxyapatite powder was modified using sorghum and shellac. Sorghum was used as a pore-forming material and shellac was used to bind hydroxyapatite powder. The characterization of the bio-composites was further carried out through X-Ray Diffraction (XRD), Scanning Electron Microscopy (SEM) and Fourier Transform Infrared (FTIR). The results of hardness and compressive strength were compared using pure hydroxyapatite and human bone as gold standard. The rate of biodegradation of materials was also reported to show that these materials are bioresorbable materials.
2. Materials and method
Bovine femur bone, sorghum, shellac solution and phosphate buffered saline (sigma-aldrich; P-5368, pH 7.4, 37°C) were used in this study. The constituent of the materials is shown in . The selected bovine bones aged 2–3 years old, were synthesized using local products from Surakarta, Indonesia. Furthermore, they were dried under the sun for 3 days and heated in boiling water. After chilling, the bones were cut into small pieces using a bone-sawing machine and crushed to form bone powder. The bone powder was further processed using a ball-milling machine to obtain finer powder (±125 µm). The powder was calcined at 700°C for 2 hours to obtain a bovine hydroxyapatite (BHA) powder. The sorghum flour used was 250 μm and shellac solution was obtained from excretion of lacca kerr insect and mixed with 97% ethanol at 1:10 %wt.
Table 1. Constituent materials of the bio-composites
Furthermore, the BHA powder was soaked in the shellac solution and allowed to dry-up before being homogenized with sorghum, based on different variations of 70/30, 75/25, 80/20, 85/15, and 90/10 % wt. The mixtures were stirred using a magnetic stirrer at 250 rpm, 70°C and 1 h. A tablet-shaped material mold (13.6x4 mm) was prepared to form the test specimens. Afterwards, the bio-composites were pressed at 60 bar, held for 5 minutes and sintered at 1000°C to bind the powder and evaporate the sorghum flour to obtain porosity in the specimen.
The XRD test was carried out to confirm if the bovine bone powder has turned into the hydroxyapatite structure. The FTIR test was used to determine the chemical bonds of the materials and identify the functional groups contained in the calcium phosphate compounds. Furthermore, hardness and compressive strength test were carried out to discover the effect of the HA/sorghum/shellac ratio on its mechanical properties (n = 7). A biodegradation rate of materials was observed by soaking in Phosphate Buffered Saline (PBS) solution to determine weight loss in 8 weeks (n = 7)
3. Results and discussion
3.1. XRD test
The XRD (Rigaku RINT-TTR III) characterization aims to determine the material crystalline phase. shows the diffractogram XRD for both pure HA and bio-composites of HA/shellac/sorghum. The composites pattern of HA/shellac/sorghum after sintering was similar to that of pure HA. The main peak of the two images appeared at wavelengths 31,36–33,14°. The similar pattern was due to the evaporation of sorghum when sintered at 1000°C and only HA material was left. The presence of evaporating material formed a porous material.
shows the comparison values between pure HA, composites HA/shellac/sorghum and the standard HA of JCPDS (Joint Committee on Powder Diffraction Standards) 9–432. It is observed in that the main peak of a pure HA was 2θ:31.753°, 32.887°, 32.170° and the standard of HA JCPDS 9–432 was 2θ:31.773°, 32.902°, 32.196°. The diffraction pattern of the sample produced the main intensity at a value of 2θ:32.293°, 33.429°, 32.708°, while the HA JCPDS 9–432 standard had the main intensity at 2θ:31.773°, 32.902°, 32.196°. From , it can be observed that pure HA and HA/shellac/sorghum powder had the same characteristics as HA JCPDS 9–432. The test on the HA powder also showed the main intensity at 2θ values to be 31.792°, 32.993°, 32.197° (Kurniasari & Cahyaningrum, Citation2016).
Table 2. The main peak of XRD diffractogram of HA/shellac/Sorghum
3.2. FTIR analysis
The FTIR analysis aims to identify the functional groups contained in the materials. shows a comparison of FTIR spectrum of pure HA, bio-composites before sintering and bio-composites after sintering.
The groups identified peak at 3500 cm−1 indicated hydroxyl (OH-), peak at 1400 cm−1 indicated as carbonate (CO32-) groups and peak 1000–600 cm−1 indicated phosphate functional group (PO43-).
Before sintering, HA/shellac/sorghum flour showed absorption at wave number of 3,426.69 and indicated the presence of an OH-, while 2,932.89 and 1,717.68 indicated CH and CO group respectively, which have been implicated as groups present in sorghum (Manuhara et al., Citation2016). Furthermore, pure HA and HA/shellac/sorghum possessed only three main peaks, indicating the functional groups of phosphate (PO43-), carbonate (CO32-) and hydroxyl (OH−) (Triyono, Citation2014), illustrating that sorghum flour was completely lost when sintering occurs at temperature of 1000°C.
3.3. Hardness test
Hardness testing was carried out by Vickers Hardness Tester with 50 g loadcell and indentation time for 10 s. Hardness testing of micro Vickers was carried out to determine the hardness of bio-composites of HA/shellac/sorghum and compared to pure HA. The results of the hardness materials can be seen in .
shows the hardness of HA/shellac/sorghum composites. It can be observed that the composition of HA variations and hardness were in direct proportion. This means that the higher variation of the sorghum mixture caused lower hardness.
Furthermore, the lowest hardness was achieved in a ratio of HA/sorghum of 50/50 (12.7 HVN). The material hardness and HA volume were in direct proportion. The ratio value of 60/40, 70/30 and 80/20 increased at 21.8 HVN, 28.4 HVN and 38.3 HVN, respectively. The highest hardness was achieved at a ratio of 90/10 (59.10 HVN). This hardness was lower compared to the control material (pure of HA/without sorghum) (100.8 HVN). The hardness of pure HA was higher compared to that of the commercial product of HA (25.57 ± 1.15 VHN) and human bone (29.85 HVN) [13]
The resulted hardness ratio of HA/sorghum materials is lower compared to the pure hydroxyapatite. This was caused by the presence of sorghum. Furthermore, the sorghum evaporated and formed a small hole when the mixture materials were sintered. The number of small holes caused decrease in material hardness. Porous materials have lower mechanical strength compared to solid materials (Triyono, Citation2014). The hardness of this material which approaches the cancellous bone (35.2 HVN) (Triyono, Citation2014) is a variation of 80/20 (38.3 HVN).
3.4. Compressive strength
Compressive strength testing was carried out by diametral tensile strength (DTS), using a Universal Testing Machine (JTM Technology Machine, 0.5 T Capacity) with a 100 kg loadcell and a rate of 5 mm/minute. The results of these tests are shown in .
shows the compressive composites of HA/shellac/sorghum. It shows that the greater composition of HA variations caused higher compression. This means that the higher variation of the sorghum flour mixture caused lower compression.
Furthermore, lowest compression was achieved in a ratio HA/sorghum of 50/50 (0.03 MPa). The compression and HA volume were in direct proportion. The compression ratio of 60/40, 70/30 and 80/20 increased at 0.1 MPa, 0.3 MPa and 0.94 MPa, respectively. The highest compression was achieved at a ratio of 90/10 (1.67 MPa). This compressive was lower compared to pure HA (3.12 MPa) and close to the compressive strength of commercial product of HA (5.80 ± 1.2 MPa) and human bone (Innocentini et al., Citation2010; Triyono et al., Citation2020). The material values for compression were lower compared to bone graft scaffold of HA-glycerin (5.71 ± 0.42 MPa) (Triyono et al., Citation2019).
The resulted compression ratio of HA/sorghum materials was lower compared to pure HA. This was caused by the presence of sorghum. The sorghum evaporated and formed a small hole when the mixture materials were sintered. Furthermore, the number of small holes caused decreased material compression. Due to the absence of small holes, the bonds between the particles become more evenly distributed, therefore increasing the compressive strength. The compression of these materials was lower compared to the cancellous bone (2–12 MPa) (Puspa & Asmi, Citation2014).
3.5. Biodegradation rate
The biodegradable materials used in this study were hydroxyapatite, shellac, and sorghum flour. In this test, the materials were immersed in a solution of Phosphate Buffered Saline (PBS) for 8 weeks. shows the results of testing the rate of biodegradation rate. It can be seen in that all materials lost weight during biodegradation, which they showed a decreasing mass during the immersion process. Furthermore, shows that the greater amount of the HA inhibits the rate of biodegradation. The largest to smallest mass reduction was 50/50, 60/40, 70/30, 80/20 and 90/10, respectively. The slowest rate was achieved by pure HA. This is caused by the amount of phosphate in HA. Excess phosphate buffers the degradation process, or phosphate can actually phosphorylate a hydroxy group or labyrinth from a polymer (Martinez et al., Citation2011).
Furthermore, the test specimens were compared using pure hydroxyapatite. The results show that the specimen mass reduction was lower compared to pure hydroxyapatite. The highest reduction of specimen mass 50/50 (19%) was lower compared to the pure hydroxyapatite (25%).
3.6. SEM observation
shows the SEM observation of bio-composition which was used to determine existing elements in the specimens. It was carried out on pure BHA and BHA/sorghum/shellac. These observations showed the formation of bonds between BHA powder and the presence of porosity in all specimens. Furthermore, (A-F) shows the porosity of the six variations of BHA/sorghum/shellac. The amount of sorghum affected the porosity and caused a reduction in bonds between HA particles. The produced porosity in (A-C) was greater compared to (D-E) because it has more sorghum content. Meanwhile, there was only a little porosity in pure HA. The porosity was produced by the evaporation of sorghum, which is fully oxidized at 374°C (Okano et al., Citation2014) and during the process of sintering at 1000°C sorghum had evaporated and formed pores. Porosity caused by evaporated sorghum during sintering process and causes weak bonds between HA particles. The hardness and compressive strength of the material tends to increase by decreasing sorghum ().
shows the porosity of the material. It can be seen that the highest porosity is achieved in the variation of 50/50 (35.39%), the value decreases in the variation of 60/40, 70/30, 80/20 and 90/10, respectively, 32.48%, 21.82%, 20.60%, and 19.31%. The lowest porosity is in pure HA (5.44%). The resulted porosity percentage show that the more composition of BHA will decrease the porosity. This is supported by the result of density test that the more composition of BHA causes greater density (see ).
(ratio of HA/sorghum):
A. 50/50C. 70/30E. 90/10
B. 60/40D. 80/20F. pure of HA
3.7. Density test
shows the material density. The lowest density was achieved at a ratio of 50/50 (1.12 gr/cm3). These values increase in the ratios of 60/40, 70/30, 80/20 and 90/10 at 1.33 gr/cm3, 1.5 gr/cm3, 1.57 gr/cm3 and 1.59 gr/cm3 respectively.
The bio-composites density of HA/sorghum/shellac was lower compared to pure HA (1.74 gr/cm3) and higher compared to human bone (0.9). The material values of density were lower compared to Sigma-Aldrich (2.2 gr/cm3) (Pramanik et al., Citation2014).
There was relationship between the results of compressive strength, hardness and bio-composite densities. Compressive strength and hardness were directly proportional to the density of the material. Compressive strength hardness and density of material were in direct proportion. Meanwhile, porosity was inversely proportional to density. A decreased porosity will always be followed by an increased density. The decreasing porosity is inversely proportional to the density of the material.
4. Conclusion
Novel bio-composites of BHA/sorghum/shellac possess characterization and mechanical properties as a biomaterial especially for bone scaffold material. The results of EDX, XRD and FTIR test revealed that the material structure was hydroxyapatite, which is the main element of a bone scaffold material. Furthermore, the bio-composites showed mechanical properties which are in accordance with the human bone as gold standard material. The amount of sorghum affected the porosity and caused a reduction in bonds between HA particles. The porosity was produced by the evaporation of sorghum, which was fully oxidized during the process of sintering, leading to the formation of pores. Furthermore, there was a weight loss on all bio-composites based on biodegradation test for 8 weeks. Therefore, further development of this study focusing on forming interconnected distributions of pores is needed.
Additional information
Funding
Notes on contributors
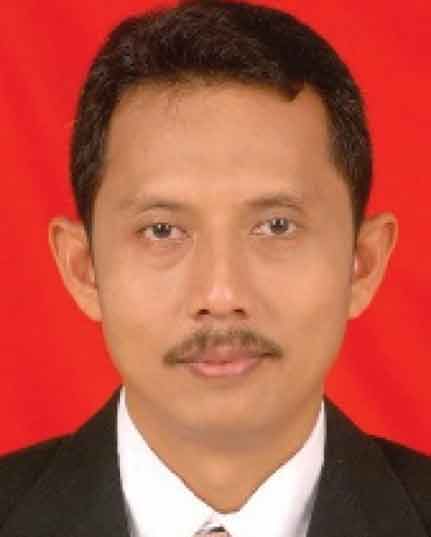
Joko Triyono
Joko Triyono received his BE degree from Sepuluh Nopember Institut of Technology (ITS) Surabaya in year 1993 and Master of Technology at the same University in year 2003. He passed Ph.D degree from Gadjah Mada University (UGM) Yogyakarta in year 2015 in Biomedical Engineering Study Program. Since 1997, he has been working at Mechanical Department Sebelas Maret University (UNS) Surakarta, Indonesia. He has published several papers in International Conference and International Journal. Until now, his research in the field of biomedical engineering included the development of material in the orthopedic field such as the development of bone graft material from bovine bone material and eggshell, the use of shellac as a filler for biocomposites material, development of CT-Scan data based on implant material and fabrication of bone graft material by 3D-printing technology.
References
- Andika, G., Andy P, I. N., Simpen, N. G., & Ayu Made, D. A. S. (2016). Extraction and characterization of hydroxyapatite of cattle bone waste using the hydrothermal alkali combination method with thermal decomposition. J. Kim, 10, 228–11.
- Fahimah, D. W. A., Wardhani, S., & Misbah, K. M. (2014). Effect of comparison of Ca:P mass ratio on hydroxyapatite synthesis of bovine bones by dry method, 1(2014), 196–202.
- Innocentini, M. D. M., Faleiros, R. K., Pisani, R., Thijs, I., Luyten, J., & Mullens, S. (2010). Permeability of porous gelcast scaffolds for bone tissue engineering. J Porous Mater, 17, 615627. https://doi.org/10.1007/s10934-009-9331-2
- Ismawati, H., Fadli, A., & Akbar, F. D. (2016). Chemical Department. Engineering Faculty, University of Riau, Effect of addition of dispersant and stirring time on making hydroxyapatite scaffold using gambas coir as template, 3, 1–6.
- Kurniasari, M., & Cahyaningrum, E. S. (2016). Synthesis and characterization of hydroxyapatite/collagen/chitosan composite by ex-situ method, UNESA J. Chem., 5, 114–118.
- Liu, X. L., Han, Y., Gao, G., Li, Z. Y., & F.Q, D. L. (2008). Effect of silane coupling agent on the mechanical, thermal properties and morphology of thermolite/PA 1010 composites. Chinese Journal of Polymer Science, 26(3), 255–262. https://doi.org/10.1142/S025676790800290X
- Manuhara, G. J., Amanto, B. S., & Astuti, T. A. (2016). Effect of drying temperatures on physical characteristics of sorghum flour modified with lactic acid. IOP Conf. Ser. Mater. Sci. Eng., 193, pp. 1–6.
- Martinez, V. A. B., Carbajal-de la Torre, G., Moller, A. D., Esparza-Ponce, H. E., & Espinosa-Medina, M. A. (2011). Study of bioactivity, biodegradability and mechanical properties of polyurethane/nano-hydroxyapatite hybrid composites. International Journal of the Physical Sciences, Vol.6(29), 668–669.
- Okano, K., Abe, T., & Ohara, I. (2014). On the isolation of apigenin from manchurian kaoliang (andropogon sorghum, brot), Bull. Agric. Chem. Soc.Japan 1934. 10857086, 10, 109–110. https://doi.org/10.1080/03758397
- Pramanik, S., Pingguan-Murphy, B., Cho, J., & Osman, A. N. (2014). Design and development of potential tissue engineering scaffold from structurally different longitudinal parts of a bovine-femur. Biomedical Engineering, 4, pp.5843.
- Puspa, K. A., & Asmi, D. S. (2014). Synthesis and characterization of hydroxyapatite bioceramics of bovine bone material at 800-1100oC. Theory and Applications, Fis, 2, pp.125–130.
- Rufaizah, U. (2011). Utilization of sorghum flour in making high-fiber food snack bars and sources of iron for young girls.
- Sedyono, J., & Tontowi, A. E. (2008). Synthesis and characterization process of hydroxyapatite from natural gypsum kulonprogo. Media Mesin, 9, pp.6–12.
- Sharma, K. K., Jaiswal, A. K., & Kumar, K. K. (2006). Role of lac culture in biodiversity conservation issues at stake and conservation strategy. Current Science, 91 (7). India.
- Srivastava, S., & Thombare, N. (2017). Safety assessment of shellac as food additive through long term toxicity study, trends in biosciences 10(2). Print: , 0974-8431, 733–740.
- Suryadi. (2011). Synthesis and characterization of hydroxyapatite biomaterials by wet chemical precipitation process.
- Triyono, J. (2014). Development of bovine hydroxyapatite-based biophotocomposite materials for artificial temporo mandibular joint materials. Dissertation of Postgraduate School UGM Yogyakarta.
- Triyono, J., Alfiansyah, R., Sukanto, H., Ariawan, D., & Nugroho, Y. (2020). Fabrication and characterization of porous bone scaffold of bovine hydroxyapatite-glycerin by 3D printing technology.. Journal of Bioprinting, 18. https://doi.org/10.1016/j.bprint.2020.e00078
- Triyono, J., Nurzengky, A., Sukanto, H., & Nugroho, Y. (2019). The effect of extruder pressure of 3D bioprinter on hardness and compressive of scaffold bovine hydroxyapatite, cogent engineering. 6, 1586812.