Abstract
In this research work the machining waste white cast iron powder (WCI) is introduced in the age hardenable Al7075 alloy matrix with the objective of enhancing the tensile properties by well-known age hardening treatment. This material holds good in light duty dies where in the strength-related characteristics improvement is the order of the day. In view of this the effect of aging kinetics on the hardness pattern and tensile strength of stir cast Al7075-white cast iron (WCI) particulate reinforced composites in as cast and peak aging conditions is investigated. The composite is cast by two step liquid stir casting route. During precipitation hardening heat treatment, reinforcement weight percentage (internal variable) and aging temperature (external variable) are considered to be the major strengthening variables. To understand the nature of failure in tensile study, fracture surface analysis is carried out using SEM. The experimental values revealed that there is a substantial enhancement in the desired properties during the precipitation hardening treatment, if the strengthening variables are properly controlled. Hardness and tensile strength of the composite have increased with increase in weight percentage of reinforcement and reduction in aging temperature. Maximum hardness and tensile strength are observed when Al7075 alloy is reinforced with 6 weight% of WCI, aged at 100ᴼC. SEM images of tensile fracture surface exhibits abundant cup-like depressions or dimples as well as river patterns indicating mixed mode of failure. The equally aligned facets (dendrites) present in the peak-aged fracture surfaces is the evidence for the attainment of optimum (peak) aging condition. The aim of the present research work is to improve the hardness-related properties by the combined effect of precipitation of secondary phases (intermetallics) through aging treatment and dispersion strengthening by the introduction of hard reinforcement WCI.
PUBLIC INTEREST STATEMENT
The exclusive goal of this research was to investigate the relationships of water quality parameters and indices versus soil erodibility parameters and develop a new Iraqi Water Quality Index (IWQI) based on 10 water quality parameters along Tigris Riverbanks in Baghdad City for samples that collected during winter of 2019 and summer of 2020. The mini-JET instrument was used to derive soil erodibility parameters for the five selected sites along Tigris Riverbanks. The results showed that the new IWQI classified the water as good quality. The results showed that there was a relationship between water quality indices and soil erodibility parameters of Tigris riverbanks. This research concluded that high soil erodibility was obtained at poor water quality. The significance of this study is to obtain the extent correlation between the water quality indices and its impact on the soil erodibility parameters and their correlations to riverbank stability.
1. Introduction
Past few decades has witnessed tremendous increase in the use of light weight and high strength materials to fabricate components chiefly for automotive and aerospace domains. This is the motivation for research in the development of new age materials. Aluminium (Al) is second most widely employed metal in the world due to its favorable properties. Al and its alloys are characterized by high specific strength and enhanced corrosion resistance. Among the commercially available Al alloys, Al7xxx series offers high specific strength and hardness, hence widely employed in aerospace and automotive structural applications (Deaquino et al., Citation2014). The strength and hardness of Al7xxx alloy can be enhanced with reinforcement of harder and refractory particulates followed by heat treatment, known as precipitation hardening. This heat treatment can be effectively employed for the enhancement of tensile properties in Al7xxx alloy and composites. Al7xxx alloys display an enhancement in partial solid solubility as the temperature is increased due to the presence of solvus line in its phase diagram. This is the prime reason for Al7xxx alloys to positively respond for precipitation hardening (Mandal, Citation2016).
Particulate reinforced metal matrix composites (PMCs) has attracted the attention of many researchers due to its ease of availability at competitive price. A number of successful manufacturing processes has been designed for the production of these composites. PMCs exhibit properties of isotropic nature. Desirable properties of the matrix material are improved by the particulate reinforcements because of enormous nucleation sites (reinforcements, dislocations, voids etc.). Generally carbides of silicon (SiC), boron (B4C) and titanium (TiC) and aluminium (Al4C3), oxides of aluminium (Al2O3) are employed as particulate reinforcements. Higher specific strength and stiffness are the common attributes of all the reinforcement materials (Ali & Yilmaz, Citation2008).
In this study, the composites are produced by a two-step stir casting method due to ease of production and economic viability. Homogeneous mixing of particulates in the matrix and optimum wetting of reinforcement surface can be obtained in two-step stir casting by suitably selecting the process parameters (Achutha Kini et al., Citation2019).
Reinforcement material is selected based on expected property improvement and cost. According to the literature survey conducted, there exists very limited research on the use of alternate materials as particulate reinforcements in MMCs. This study is focused on the combination of reinforcement and heat treatment effects in the improvement of hardness and tensile strength of precipitation hardened Al7075 alloy by varying the wt.% of WCI powder. As per literature survey WCI particulates have not been employed as reinforcement in MMCs. WCI is employed as particulate reinforcement since iron carbide (cementite) is present in it, as it is a very hard and refractory phase dominating the microstructure. WCI can enhance the property of the matrix material as it mainly consists of harder and refractory carbide phase. At the same time Al7075—WCI powder reinforce composite is cheaper in comparison with Al7075—ceramic reinforcements such as SiC, B4C, Al2O3, Si3N4, and TiB2 etc. These ceramic reinforcements also require special treatments and controlled conditioning. These reinforcements are not easily available as WCI. When these reinforcements are compared with WCI for hardness and strength-related properties, the latter is on par with such well-known reinforcements. The proposed system can be utilized in light duty dies where high hardness of the material can compensate for the wear and tear involved in the application. The main purpose of this research work is to obtain a cheaper class of metal matrix composite with excellent property obtained by the combined effect of solid solution strengthening by the heat treatment and harder reinforcement.
2. Methods
2.1. Preparation of composites: Two step stir-casting technique
Stir casting method was employed for the fabrication of composites. Initially, rods of Al7075 are cut into pieces and placed in a crucible made up of graphite. It is melted in 5 kW rating electric resistance furnace. Melting is continued until uniform temperature of 750ᴼC is attained. Slag or flux formed at the surface of the melt is removed by introducing small quantity of scum powder. Dry hexa chloroethane (C2Cl6, 0.3 wt.%) is added to the melt for degasification (John, Citation1999). Wettability of the reinforcement is enhanced by adding pieces of Mg (1 wt.%) to the melt. (Barbara et al., Citation2008). WCI particles are preheated to 500ᴼC for 2 h. This process removes all the volatile elements and maintains the particle temperature closer to melt.
The melt is then allowed to cool in air up to 600ᴼC to a semi solid state. The melt is stirred to form the vortex by using a stirrer in the speed range of 150–300 rpm for 20 min. During stirring the vortex is formed and WCI powder (2, 4 and 6 wt.%) is transferred into the melt. Optimum distribution of the WCI particles in the alloy can be obtained by maintaining a stirrer in the range of 200–250 rpm for the processing duration of 15 min.
The furnace temperature is monitored by a temperature probe. Once the mixing of reinforcement in semisolid state is complete, the furnace is reheated to 750ᴼC which is beyond the liquidus temperature of Al7075. Stirring is commenced again for about 10 min at around 400 rpm. Two step stir casting technique results in composites with less porosity, uniform reinforcement distribution and minimum casting defects.
Viscosity of the melt is enhanced at semi solid state which in turn reduces the possibility of floating of the WCI particles. Due to the stirring action at this stage, the gas layers are broken around the particle liquid interface which leads to better spread out of molten metal onto the particle surface. Hence, wettability is improved. The combined effect of reheating of composite slurry above its liquidus temperature and agitations created during stirring action enhances particle distribution by reducing the effect of sedimentation (Kenneth.; and Ayotunde, Citation2012).
2.2. Precipitation hardening treatment
Specimens (2, 4 and 6 wt.% WCI composites) are solution treated at 550ᴼC for 2 h followed by aging at temperatures of 100, 150 and 200ᴼC as shown in . After solutionising and aging, the specimens are water quenched to room temperature (Jamaluddin et al., Citation2019).
2.3. Hardness measurement
ASTM E18 standard is maintained for the preparation of hardness specimen. Rockwell hardness testing machine using a 1/16” diameter steel ball is utilized for the test. Minor and major loads of 10 and 100 kgf were applied during the measurement. B scale of measurement (HRB) is taken, as it is the most appropriate for aluminium alloys.
2.4. Measurement of tensile strength
Material behavior when subjected to tensile load is captured during tensile test. Electronic tensometer is employed for the test in accordance with ASTM-E8M. The specimen is firmly held onto a gripper. Tensile load is applied until the specimen is broken. A cross head speed of 10 mm/min having an increment in length of 0.01 mm and load cell value of 20.5 kN is employed. To minimize error three readings are averaged out for each condition and tabulated.
2.5. SEM analysis of fracture surface
Fracture surface of the composites are analyzed using ‘Scanning Electron Microscope (SEM); Model: EVO18, ZEISS’.
3. Results and discussion
3.1. Aging curve and hardness
The hardness of composite improves with increase in wt.% of reinforcement as shown in . The enhancement in the hardness can be attributed to the dislocations generated during solidification due to the incorporation of WCI particles. Dislocation density increases due to thermal gradient between the alloy and reinforcement, when the wt.% of WCI is increased. Microstructure and mechanical properties of the material is greatly influenced by the internal stresses developed due to the above said phenomena during solidification. The plastic deformation of the composite is hindered due to increase in dislocation density. This results in further enhancement of the hardness of composite (Mahathaninwonga et al., Citation2012).
During precipitation hardening treatment the hardness of the material reduces after solutionising due to the formation of high temperature single phase supersaturated solid solution. Upon aging, the matrix lattice is strained due to the formation of intermediate phases as solute rich intermetallics like MgZn2. At the same time, the precipitation of coherent intermetallics in the matrix takes place in a systematic process with number of stages like formation of Guinier Preston (GP) zones, partially coherent intermediate zones and fully coherent zones etc. with respect to aging time. While refinement of intermetallics happens in stages, the matrix is systematically strained to increase the internal energy of the system. This internal energy increase is reflected in the form of property change especially, peak hardness. Strained matrix not only increases the hardness, but also the tensile strength and fatigue resistance (Bayazida et al., Citation2014).
As the aging temperature increases, critical size of the precipitates nucleated is larger which leads to coarser precipitates. This phenomenon results in lower peak hardness and strength. As the alloy is aged further, the precipitate will form its own crystal structure which nullifies the coherency with the matrix lattice. The coherency strain between the matrix and formed precipitate is lost in this condition, at the same time dislocation annihilation takes place continuously as aging continues further. The number of precipitates in the matrix reduces due to the dissolution of some finer precipitates so that the remaining precipitates coarsen. This reduces the interparticle distance. This phenomenon also decreases the strain in the matrix lattice. Hence the alloy is said to be overaged (Bodunrin. et al., Citation2015).
From the aging curves as shown in a-d it is clear that the rate of aging in the composite is higher compared to the base alloy. The aging kinetics is enhanced as the wt.% of reinforcement in the base alloy increases which in turn results in reduction in time to attain peak hardness. Increase in the wt.% of reinforcement also leads to finer precipitates evolving from enormous number of nucleation sites in the peak-aged specimen. Hence the mobility of dislocation is hindered.
Figure 3. Aging curves of a) Al7075 alloy, b) Al7075-2 wt.% WCI, c) Al7075-4 wt.% WCI, d) Al7075-6 wt.% WCI
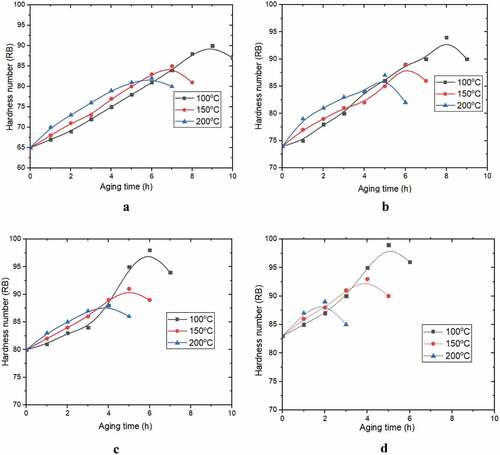
Aging is also accelerated due to higher dislocation density near the matrix reinforcement interface. More the dislocation density, higher will be the number of precipitates (intermetallics) as it produces heterogeneous nucleation sites (Kulkarni et al., Citation2004) for the intermetallics. As the wt.% of reinforcement increases, peak hardness increases at all aging temperatures. Lower aging temperature increases the peak hardness value due to increase in number of intermediate metastable phases during the spontaneous precipitation process of aging phenomena compared to faster diffusion kinetics at higher temperature aging (Rao et al., Citation2010).
3.2. Tensile strength
It is evident from the values obtained for UTS that there is a direct correlation between the content of WCI particles in the composite and the tensile strength in both as cast and heat-treated conditions as shown in . The UTS of peak aged composite has significantly increased in comparison with alloy. The enhancement in UTS can be attributed to the stronger interface between the matrix and reinforcement. UTS is directly proportional to the extent to which load is distributed from the matrix to the reinforcement.
Solutionizing treatment will enhance the ductility of the specimen by sacrificing on its tensile strength. This is due to the structure obtained at the solutionizing stage consisting of supersaturated solid solution without the strengthening intermetallic phases. Lower tensile strength is exhibited by solutionized specimen compared to as cast condition. Lowering the aging temperature increases the aging time but results in an enhancement of tensile strength of the material. The most optimum combination to obtain the highest UTS is lowest aging temperature (100°C) with maximum 6 wt.% of reinforcement.
Increase in UTS of Al7075-WCI composites when subjected to aging, can also be attributed to the formation of intermetallic precipitates (MgZn2) leading to straining of the matrix during the precipitation of intermetallics with a larger number of intermediate metastable phases (He et al., Citation2018).
3.3. Fracture surface analysis
3.3.1. Al7075 alloy
The mixed fracture mode (brittle and ductile) is predominant as observed due to the presence of river like pattern, micro cracks, voids and dimples along the fracture surface shown in . Hence as cast alloy exhibits lower UTS. Coarser cluster dimples, identical facets and river patterns are observed along the fracture surface of the peak-aged alloy shown in . Identical facets with lesser density of river patterns and voids present resulting in higher UTS. However, the facet clusters are separated by a large number of micro cracks even in the peak-aged samples shows failure is a mixed one.
3.3.2. Al7075-6 wt.% WCI composites
SEM fractographs of as cast and artificially aged composite with 6 wt.% WCI are shown in . Both brittle and ductile failure characters are visible in the composites. The presence of WCI particle on the fractured surface is an indication for the possibility of failure which is driven by strained matrix material. The presence of WCI particles in the vicinity of dimples is an indication of strong interfacial bonding between the matrix and reinforcement. The stress concentration during tensile loading around WCI particles will be less due to the micron size of the particles. Hence, the reinforcement particles will be subjected to relatively smaller load. Thus the probability of particle cracking is very less (Mahadevan et al., Citation2007). Coarser dimples formed by merging of number of finer equi-axial identical dimples, wrinkles at the dimple tops and less density of river patterns represent higher tensile strength of this composite over the alloy. The number of locations for dimples and voids will enhance for 6 wt.% of reinforcement (Pardeep et al., Citation2015). Since the number and density of river pattern is more than the dimples, the failure is a mixed mode one, where brittle failure mechanism is dominating. In peak-aged conditions, fracture is mainly due to improper interfacial bonding and void nucleation growth. These voids are then combined during tensile loading resulting in the coalescence of voids and subsequent formation of cracks (facets separation region) that lead to failure at the fracture surface termed as void nucleation growth failure (Nikhilesh & Shen, Citation2001). Tensile fractography of peak aged composite sample also show enormous number of identical finer dimples. Repetitively dispersed finer dimples is responsible for higher strength. Close-packed facets are the evidence for attainment of optimum aging condition.
4. Conclusions
The study of precipitation hardening effect on the aging characteristics and tensile fractography on Al7075-WCI composites is systematically investigated, and analysed. The composite is successfully stir cast and subjected to heat treatment. Al7075-WCI composites exhibit an increase in hardness in the range of 30–40%, in as cast condition compared to base alloy. Age hardening resulted in significant improvement of the mechanical properties of Al7075 alloy and Al7075-WCI composites. The enhancement in UTS of peak-aged composites can be ascribed to a greater extent to the generation of intermetallic precipitates, which behaves as the domains of hindrances for restraining down the dislocations and hence decreases the degree of plastic deformation. As the weight percentage of reinforcement increases, the presence of large number of harder particles and intermetallics resulting in higher density of dislocation leads to higher UTS at lower aging temperature. Lower aging temperature (100°C) with longer duration is more effective to obtain high strength and hardness compared to high temperature aging (150 and 200°C). Considerable increase in peak hardness is observed for all aging temperatures. Most significant is at 100ᴼC which resulted in 110–130% enhancement. The UTS of peak aged Al7075 increases with the addition of WCI. The UTS of the peak-aged composites has increased by 20–30% compared to base alloy. Overall, age hardening resulted in 45–65% increase in UTS for the composites. In Al 7075 alloy, dimple rupture is the predominant fracture mode as large number of small equiaxed dimples are observed in the fractograph of fracture surface. In Al 7075-WCI composites, the failure is mainly through the matrix material as fractography indicates the presence of reinforcements on the fracture surface.
Additional information
Funding
Notes on contributors
Jamaluddin Hindi
Our group’s research area is mechanical characterization and microstructure-related study of Al 7075 alloy-based composites is as cast and precipitation-hardened conditions. Al 7075-based composites are manufactured by two step stir casting method. Precipitation hardening treatment is imparted to alloy and composites to enhance the mechanical properties. Mechanical and microstructural characteristics are explored in both as-cast and age hardened conditions. Analysis of microstructure is carried out to correlate it with hardness-related properties. Precipitation hardening treatment has a positive impact on the mechanical behavior of alloy/composites since there is a considerable improvement in hardness and strength. Aging kinetics will be is accelerated by the increase in wt.% of reinforcement. This can be attributed to the enhancement in the dislocation density and higher precipitation rate of intermetallic phases. Enhancement in strength can be attributed to the combined effect of intermetallic precipitates and reinforcement particulates on the hindrance to dislocation movement.
References
- Achutha Kini, U., Jamaluddin, H., & Sharma, S. S. (2019). Wear related study on the precipitation hardened Al7075-Grey cast iron particulate reinforced composites. International Journal of Mechanical and Production Engineering Research and Development, 7(9), 703–11.
- Ali, K., & Yilmaz, S. (2008). Synthesis and characterization of aluminum alloy 7075 reinforced with silicon carbide particulates. Materials & Design, 2(9), 775–780. https://doi.org/10.1016/j.matdes.2007.01.007
- Barbara, P., Dante, P., & Taccardo, C. (2008). Application of traditional investment casting process to aluminium matrix composites. Composites: Part A, 39(6), 1606–1617. https://doi.org/10.1016/j.compositesa.2008.07.001
- Bayazida, S. M., Farhangia, A., & Radanc. (2014). Effect of cyclic solution treatment on microstructure and mechanical properties of friction stir welded 7075 Al alloy. Materials Science and Engineering, 49(6), 293–300. https://doi.org/10.1016/j.msea.2015.10.010
- Bodunrin., M. O., Kenneth, K., Alaneme, L., & Chown, H. (2015). Aluminium matrix hybrid composites: A review of reinforcement philosophies; mechanical, corrosion and tribological characteristics. Journal of Materials Research and Technology, 16(9), 169–181. https://doi.org/10.1016/j.jmrt.2015.05.003
- Deaquino, L., Gutierrez, C., Estrada, G., Hinojosa, R., & Sanchez, G. (2014). Structural characterization of aluminium alloy 7075–graphite composites fabricated by mechanical alloying and hot extrusion. Materials & Design, 53(6), 1104–1111. https://doi.org/10.1016/j.matdes.2013.08.005
- He, L., Xiaoming, W., & Chai, L. (2018). Microstructure and mechanical properties of an insitu TiB2/Al-Zn-Mg-Cu-Zr composite fabricated by Melt-SHS process. Materials Science & Engineering A, 20(7), 60–68. https://doi.org/10.1016/j.msea.2018.02.025
- Jamaluddin, H., Achutha Kini, U., & Sharma, S. S. (2019). Precipitation hardening effect on the aging characteristics of two step stir cast Al7075-GCIp composites. International Journal of Mechanical and Production Engineering Research and Development, 7(9), 670–676.
- John, E. G. (1999). The treatment of liquid aluminium and silicon alloys. McGraw-Hill.
- Kenneth.; and Ayotunde. (2012). Production and age-hardening behaviour of borax premixed SiC reinforced Al-Mg-Si alloy composites developed by double stir-casting technique. The West Indian Journal of Engineering, 34(4), 80–85.
- Kulkarni,, Krishnamurthy,, Deshmukh, S. P., & Mishra, R. S. (2004). Effect of particle size distribution on strength of precipitation-hardened alloys. Journal of Materials Research, 19(7), 2765–2773. https://doi.org/10.1557/JMR.2004.0364
- Mahadevan, K., Raghukandan, & Pillai. (2007). Experimental investigation on the influence of reinforcement and precipitation hardening parameters of AA 6061-SiCp composites. Indian Journal of Engineering & Materials Sciences, 14(5), 277–281. http://hdl.handle.net/123456789/197
- Mahathaninwonga, N. T., Plookphola, J., Wannasina, & Angoonb, W. (2012). T6 heat treatment of rheocasting 7075 Al alloy. Materials Science and Engineering, 32(5), 91–99. https://doi.org/10.1016/j.msea.2011.10.068
- Mandal, P. K. (2016). Characterisation and modeling of precipitation kinetics in 7075 Al-Zn-Mg Alloy. International Journal of Modern Engineering Research, 19(6), 33–48. http://www.ijmer.com/papers/Vol6_Issue2/Verson-2/F6223348.pdf
- Nikhilesh, C., & Shen, Y. L. (2001). (2001). Mechanical behavior of particle reinforced metal matrix composites. Advanced Engineering Materials, 3(6), 357–370. https://doi.org/10.1002/1527-2648(200106)3:6<357::AID-ADEM357>3.0.CO;2-I
- Pardeep, S., Satpal, S., & Khanduja, D. (2015). Study on microstructure of aluminium matrix composites. Journal of Asian Ceramic Societies, 3(5), 240–244. https://doi.org/10.1016/j.jascer.2015.04.001
- Rao, R. N., Das, S., Mondal, D. P., & Dixit, G. (2010). Effect of heat treatment on the sliding wear behaviour of aluminium alloy (Al–Zn–Mg) hard particle composite. Tribology International, 43(3), 330–339. https://doi.org/10.1016/j.triboint.2009.06.013