Abstract
In the last 15 years Bangalore city has systematically modernized its concrete production process with the help of ready-mix concrete (RMC) facility. However, one of the present requirements of these facilities is to lower its carbon footprint by reducing consumption of Portland cement in the concrete production process. Further, the demand for high-strength concrete (HSC) has increased due to construction of high-rise buildings and other major infrastructure projects in the urban areas of the city. Therefore, this study presents the experimental test results of HSC mixes proportioned with reduced consumption of Portland cement. Four types of concrete mixes with 50% of Portland cement replaced by ground granulated blast furnace slag (GGBS) were considered. Additionally, two control mixes without GGBS replacement were also tested. Fresh, hardened, and durability properties of all the mixes were experimental determined and presented. The results showed that concrete mixes proportioned with 50% GGBS obtained a maximum 28-day compressive strength of 77 MPa. Further, all the mixes with GGBS exhibited superior durability properties when compared to control mixes. Thus, concrete mixes with 50% GGBS replaced for Portland cement are favourable for producing HSC at RMC facilities at Bangalore city.
PUBLIC INTEREST STATEMENT
There has been tremendous growth in the infrastructure of Bangalore city in last two decades. This has increased the demand on high-strength concrete in the city. Further, with growing emission concerns the practice of reducing the consumption of Portland cement has become the need of the hour. Therefore, the primary objective of this study is to develop high-strength concrete inclusive of 50% ground granulated blast furnace slag replaced for Portland cement, and further investigate its strength and durability properties experimentally, and also evaluate its economic benefits. The outcome of this research will help field engineers and practitioners to effectively use GGBS in production of high-strength concrete at ready-mix concrete plants.
1. Introduction
In the past two decades, Bangalore city has seen tremendous growth in the infrastructure. The primary cause for such growth has been the boom in the education, information technology and industrial sectors of urban regions. The increase in infrastructure projects also puts pressure on production and consumption of construction materials like Portland cement concrete. While Bangalore metropolitan area has effectively managed to modernize its concrete production facility by introduction of ready-mix concrete (RMC) plants, there are still challenges faced. One such challenge is to make these facilities sustainable by reducing the consumption of Portland cement in the concrete manufacturing process. There are various supplementary materials used to substitute Portland cement, such as fly ash (Wang et al., Citation2017), silica fume (Mohamed & Najm, Citation2017), ultra-fine slag (Ting et al., Citation2020), ground granulated blast furnace slag (GGBS) (Lim et al., Citation2016), etc. Therefore, in practice it is crucial to choose and optimize the supplementary materials, which shall provide desirable effect on the properties of concrete such as workability, slump retention, strength and durability, but at the same time should be easy to handle and cost effective.
In India, the use of GGBS in RMC plants is very common, and its positive effect in reducing CO2 emissions by lowering specific fuel consumption and reducing limestone calcination is known (Higgins, Citation2007). Further, according to Ernst and Young estimate (Existing and Potential Technologies for Carbon Emissions Reductions in the Indian Cement Industry, Citation2013), the generation of GGBS in India will be approximately 44 Mt per annum in 2020 and 95 Mt per annum in 2030. In Bangalore, according to the field survey conducted there are 122 captive and 154 commercial RMC plants, and the concrete consumption per month is approximately 0.5–0.7 Mcm, with approximate GGBS consumption of 0.15 Mt. Further, in RMC plants, only 25–30% of GGBS is used for manufacturing up to M30 grade concrete, and this reduces to only 15–20% for manufacturing up to M40 grade concrete, respectively. Also, in practice the replacement rate of GGBS reduces for high-strength concrete (HSC) (i.e., typically greater than 60 MPa). Therefore, there is a need to effectively use GGBS in production of HSC in RMC plants.
For Bangalore city, one of the current requirements of RMC plants is production of HSC, and this is due to increased construction activity with high-rise buildings and other major infrastructure projects. Further, the benefits of partially replacing of Portland cement by GGBS have been reported (Elchalakani et al., Citation2014). However, due to variability in the properties of GGBS and other raw materials, it is necessary to conduct studies with locally available materials to have a better understanding for such concrete mixtures. Therefore, the primary objective of this study is to develop HSC inclusive of 50% GGBS replaced for Portland cement and further investigate its strength and durability properties experimentally. The outcome of this research will help field engineers and practitioners to effectively use GGBS in the production of HSC at RMC plants and overcome some of the industry challenges in the aforementioned paragraphs.
2. Materials and methods
2.1. Materials
The chemical analysis of OPC and GGBS was performed using XRF technique. presents the physical and chemical properties of OPC and GGBS. As seen, OPC confirms to IS 269–2015 standard (IS 269: Citation2015, Citation2015) and GGBS confirms to ASTM C 989 standard (ASTM C989/C989M-18a, Citation2018). Locally available crushed aggregates were used in this study. presents the various properties of the crushed aggregates. As seen, both crushed stone sand and coarse aggregates are of desirable quality. The particle size distribution of the aggregates is presented in . The coarse aggregate meets the requirement of IS 383-2016 standard (IS 383: Citation2016, Citation2016) with maximum aggregate size of 20 mm. Similarly, the fine aggregates meet the requirements of IS 383-2016 standard and is categorized in grading zone II. In order to achieve good workability and consistent slump values, polycarboxylate-based high-range water-reducing admixture (HRWRA) was used. All the mixes were proportioned using normal tap water.
Table 1. Physical and chemical properties of OPC and GGBS
Table 2. Properties of natural aggregates
Table 3. Particle size distribution of aggregates
2.2. Mixture proportioning
Concrete mixture proportioning was based as per IS 10262: 2019 standard (IS: 10262, Citation2019). The studied mixes were proportioned at a laboratory at RMC facility as shown in . Further, extensive laboratory trials were performed prior to the selections of the specific mixes (Raghavendra & Ramalinga Reddy, Citation2019). Finally, a total of six mixes were selected for this study. Two different water to binder ratio with varying amount of cementitious material was considered. The GGBS replacement rate was fixed at 50% by weight of OPC, and this replacement rate was based on the findings of past studies (Raghavendra & Ramalinga Reddy, Citation2019; Rashad, Citation2018). presents the details of the mix proportions evaluated. The HRWRA was identified based on the minimum initial slump requirement of 150 mm. As seen in , the requirement of the HRWRA increased with the reduction in water to binder ratio and also with reduction in total binder content in the mix. In order to achieve cost effective mix, it is critical to obtain optimum dosage of HRWRA. The results presented in showed that incorporation of GGBS has reduced the requirement of HRWRA for Mix B and Mix E, when compared to reference Mix A and Mix D, respectively.
Table 4. Details of mix proportions evaluated
2.3. Specimen preparation
A total of 144 concrete specimens were casted, and the details of specimen type is presented in Tle 6. Concrete mix was prepared in a pan mixer as shown in Figure (a). Fine and coarse aggregates were first blended, and later cement and GGBS was added and dry mixing continued for 4 min to achieve uniform mix. Part of mix water (i.e., 90%) was added and mixing continued for 2 min. Then, determined dosage of HRWRA was blended with remaining mix water (i.e., 10%) and introduced in to the concrete mix, and mixing continued for additional 4 min. After completion of the mixing, fresh concrete as shown in ) was immediately used to determine the various properties. Later, concrete specimens were prepared in steel moulds as shown in ). Demoulding of specimens was done after 24 h, and specimens were submerged in water tank for curing periods of 7, 28, 56 and 90 days.
2.4. Test methods
Tests were conducted on the fresh and hardened concrete following various standard procedures. present the tests performed on fresh and hardened concrete, respectively. For each of the different tests and curing periods, a replica of three specimens was used. Compressive strength test was performed according to IS 516: 2018 (Citation2018) using a compression testing machine of 3,000 kN capacity as shown in ). Load was applied at a rate of 5.15 kN/s without shock until failure. Compressive strength was determined by considering the load at failure. Water absorption was performed according to ASTM C 642 (Citation2013). First, the cube specimens were dried in the oven at 105 ± 5 °C for 24 h and its weight was noted. Afterwards, the cube specimens were completely submerged in water for 24 h, and then removed and cleaned of the excess surface moisture and weighed. Water absorption was determined by noting the difference in the weights of complete dry and complete moist cube, and divided by its complete dry weight. Water permeability test was performed using the German standard DIN 1048-1 (Citation1991) on 150 mm cube specimens. The specimens were assembled in the test cells and a water pressure of 5 bars was applied for 72 h. Water pressure was applied by means of an arrangement consisting of water tank connected to an air compressor through a valve to adjust the pressure. Finally, the specimens were split perpendicular to the water-injected face and with the help of Vernier caliper the depth of water penetration was determined. Chemical resistance was performed according to ASTM C 267 (Citation2012). The specimens were demoulded and soaked in water for 28 days. Later, the same specimens were immersed in 3% sulphuric acid sol. and 3% hydrochloric acid sol. in such a way that they were completely submerged for a period of 14 days. The chemical resistance of the specimens was determined by noting its weight loss. Rapid chloride penetrability test (RCPT) was carried on 51 mm thick and 102 mm dia. cylinder specimens as shown in ). All specimens were perfectly dried before testing. Later the specimens were assembled between two compartment cell assembly, which was air and water tight. The cathode compartment is filled with 3% NaCl and anode compartment is filled with 0.3 normality NaOH sol. This test primarily consists of monitoring the amount of electrical current passing through 51-mm-thick cylinder specimens for a duration of 6 h period, while maintaining a potential difference of 60 V dc across the ends of the specimens, immersed in sodium chloride sol. on one end and sodium hydroxide sol. on the other end. The total charge passed in coulombs has been found to be related to the resistance of the specimens to chloride ion penetration. presents the chloride ion penetrability based on charge passed. As seen, for specimens with low resistance to chloride ion penetrability the charge passed in coulombs should be greater than 4,000. While for specimens with very high resistance to chloride ion penetrability the charge passed in coulombs should be less than 100.
Table 5. Tests on fresh concrete
Table 6. Tests on hardened concrete
Table 7. Chloride ion penetrability based on charge passed
3. Results and discussion
3.1. Fresh properties of concrete
presents the fresh properties of concrete. At the initial stage of fresh concrete, the atmospheric and concrete temperatures were recorded. The addition of 50% GGBS caused reduction in concrete temperature on average of 3°C, when compared to the control mix. This reduction in temperature plays an important role in producing temperature-controlled concrete, and also beneficial in case of mass concreting. Slump test was conducted immediately after mixing of concrete. All the mixtures containing 50% GGBS exhibited very good slump, with mixtures becoming more mobile and cohesive. This improvement can be attributed to relatively smooth surface characteristics of GGBS which absorb lower water at the time of mixing (Neville, Citation1997). shows the rate of slump loss for concrete mixtures containing 50% GGBS in comparison to mixtures without GGBS. It is very important for RMC plants to control the rate of loss of slump, especially when the concrete mix is in transit. When in transit the RMC shall be transported in truck mixer. Further, in urban areas of Bangalore, due to drastic traffic growth, congestion and traffic jams are quite common, which affects the overall transit time of concrete mix. Therefore, lower rate of slump loss is preferred. After 60 min of mixing, slump loss of 20% was observed for Mix A, Mix C, Mix E, and Mix F. While Mix B and Mix D exhibited 33% slump loss. However, the major difference was observed after 180 min, where concrete mixtures with 0% GGBS and water to binder ratio of 0.25 exhibited the highest slump loss of 80%, and concrete mixtures with 50% GGBS and water to binder ratio of 0.30 exhibited the lowest slump loss of 48%. Further, at a constant water to binder ratio, the slump retention capacities of GGBS mixes were better than the OPC mixes. Air content test was determined using pressure meter. From the obtained results it can be seen that concrete mixtures with 50% GGBS had slightly lower percent of air content, when compared to mixtures with no GGBS. Initial and final setting time was determined using concrete penetrometer. It is seen that increasing the GGBS from 0% (Mix A) to 50% (Mix B, Mix C) the initial and final setting time increased on average by 25% and 46%, respectively. Similarly, when GGBS increased from 0% (Mix D) to 50% (Mix E, Mix F) the initial and final setting time increased on average by 11% and 26%, respectively. The initial and final setting time increased for all the mix types by increasing the water to binder ratio, with least values obtained for Mix A and highest for Mix F.
Table 8. Fresh properties of various mix types
3.2. Hardened properties of concrete
3.2.1. Compressive strength
The compressive strength of concrete is very important in most cases to ensure the quality of concrete on site. Therefore, achieving the desired strength becomes very crucial for RMC plants, especially when delivering concrete for major infrastructure projects. shows the compressive strength of various mixes evaluated at different curing periods. As seen, after 7 days of curing, all mixes with GGBS, irrespective of water to binder ratio, exhibited lower strength then the control mix without GGBS. However, at later stages the compressive strength for GGBS mixes increases. shows the gain in compressive strength of various mixes with curing time. It is observed, on average, irrespective of water to binder ratio, the strength gain for GGBS mixes after 28 days, 56 days and 90 days was 48%, 65% and 73%, respectively, when compared to 7 days. Similarly, the average strength gain for control mix, irrespective of water to binder ratio was 24%, 30% and 34% after 28 days, 56 days and 90 days, respectively, when compared to 7 days. From the obtained results the superior strength properties of GGBS mixes were evidenced after 90 days of curing. It is well known that high slag (typically greater than 45%) in concrete mixtures cause reduction in the compressive strength of concrete at initial stages, and many studies in past have reported this trend (Ghoddousi et al., Citation2014; Güneyisi & Gesoğlu, Citation2011; Khodair & Bommareddy, Citation2017; Monkman & Shao, Citation2010; Zhang et al., Citation2012). However, in this particular study, it is interesting to see that after 28 days there is enhancement in the compressive strength for all the mixtures containing GGBS. For instance, shows the diminishing or enhancing effect of GGBS on compressive strength of concrete at various curing periods, when compared to control mix. As seen, after 7 days there is diminishing effect with a maximum of 15% for Mix B and Mix E. While after 28 days there is only enhancement, with a maximum of 15% for Mix F after 90 days of curing. This can be attributed to lower water to binder ratio and high cementitious content in the mix. Further, moisture curing also contributes towards enhancement of compressive strength for GGBS mixes, and similar trend has also been reported in the past (Topçu & Boğa, Citation2010). Also, GGBS chemical composition, particularly ratio of (CaO + Al2O3 + MgO) to SiO2 which indicates its chemical hydraulic moduli is believed to contribute towards mechanical strength (Rashad, Citation2018). For GGBS used in present study the moduli was found to be high (i.e., 1.93) and can be one of the reasons for enhancement in the compressive strength.
3.2.2. Water absorption and permeability
The water absorption of concrete gives an understanding on the pore structure of the hardened concrete and also provides valuable information with respect to possible resistance to intrusion of unwanted substance in concrete matrix, and thereby influencing the durability of concrete. Higher water absorption values shall have negative influence on the durability properties of concrete. As seen in , after 28 days of curing the concrete mixtures with GGBS had very low water absorption ranging between 0.7% to 1.2%. While the conventional mixtures had water absorption of 1.45% and 1.57%. Further, slightly lower water absorption was observed for mixtures with lower water to binder ratio. shows the permeability test results on the various mixes. As seen, inclusion of GGBS has reduced the water permeability. For instance, irrespective of water to binder ratio, the average permeability for conventional mixes was observed to be 14.5 mm while inclusion of 50% GGBS has reduced this to 12 mm. This translates to 17% reduction in water permeability for concrete mixes with GGBS. This reduction in water absorption and permeability can be attributed to the pore refinement caused due to the presence of GGBS. Large pores get transformed into smaller pores, since more voids get filled with C-S-H, thereby densifying the microstructure of hydrated cement paste (Gao et al., Citation2005), and reducing the water absorption and permeability of concrete mixes. In practice, improvement in water absorption and permeability of concrete mixes with GGBS shall have positive effect on the service life of the concrete structures.
3.2.3. Penetration of chloride ion
shows the RCPT test results for various mixes. All the mixes showed very low chloride ion penetrability according to ASTM standards, which can be compared as presented in . However, the concrete mixes with GGBS showed lower 28 days total charge passed (coulombs). For instance, Mix B and Mix C showed average of 488 and 468 coulombs, respectively, which is 29% and 32% lower than the control Mix A. Similarly, Mix E and Mix F showed average of 555 and 483 coulombs, respectively, which is 29% and 39% lower than the control Mix D. This can be attributed to filling up of the pores of concrete matrix with slag and its products of pozzolanic reaction, causing reduction in the transport of chloride ions. Further, it is found that for high-volume slag mixes at very low water to binder ratio, it is very effective in reducing the chloride ion penetration over long period when exposed to harsh environment conditions (Thomas et al., Citation2008). This means it is a direct advantage for Mix B, Mix C, Mix E, and Mix F, which shall produce very durable concrete matrix over long periods of time.
3.2.4. Chemical resistance
shows the chemical resistance of various mixes. The inclusion of GGBS in concrete showed improvement in chemical resistance. For instance, the weight loss percent for Mix B and Mix C was 31% and 44% lower than the control Mix A. Similarly, the weight loss percent for Mix E and Mix F was 27% and 40% lower than the control Mix D. From obtained results it is clear that at fixed GGBS replacement, increasing the cementitious content and reducing the water to binder ratio has improved the chemical resistance of concrete mixes. Therefore, the least percent weight loss of 1.175% was obtained for Mix C. Further, such improvement is attributed to positive effects of GGBS in the concrete mixes, which play a vital role in lowering presence of Ca (OH)2 (Oner & Akyuz, Citation2007). Since Ca (OH)2 is prone to acid attack, it is highly unstable and gets easily leached out in presence of acid. With respect to chemical resistance, there are also long-term benefits of high GGBS replacement mixes. For instance, a study conducted by Hooton and Emery (Hooton & Emery, Citation1990) reported very low damage for concrete mixes when more than 45% of Portland cement was replaced by GGBS and exposed to sulphate solution for a duration of 10.5 years. Therefore, for Mix B, Mix C, Mix E, and Mix F there will be long-term benefits in terms of concrete durability.
4. Cost benefits
For success of the concrete mix at the RMC industry its cost is very important. Therefore, cost comparison of the proposed mixes was done with an actual industry mix (i.e., adopted at the RMC plant). The industry mix consists of cement partially replaced with GGBS and Alccofine, producing concrete mixtures with 28-day compressive strength of more than 60 MPa, which makes industry mix comparable with the mixes proposed in this study. presents the details of the cost comparison. Since mixes with lower water to binder ratio provided better performance, only Mix A, Mix B, and Mix C were considered in this comparative study. As seen from , by replacing Portland cement by 50% GGBS, a maximum reduction in cost of the concrete was 23% and 13%, when compared to industry and conventional mix (i.e., without GGBS), respectively. This clearly shows the economic benefits of the proposed mixes for the RMC industry.
Table 9. Details of cost for various proposed mixes
5. Conclusion
This study focuses on utilization of GGBS as partial replacement (i.e., 50% by weight) to Portland cement in producing HSC at a ready-mix facility at Bangalore city. After extensive laboratory trials, six mixes were selected with two different water to binder ratio and varying cementitious content. Strength and durability properties of the mixes were experimentally determined. Based on the obtained results following are the important findings and conclusion.
The addition of GGBS as partial replacement to Portland cement reduced the water demand and improved the workability of concrete mixtures. This can be attributed to surface characteristics of GGBS, which is smooth and reduces the requirement for water. Further, it also improved the slump retention capacity. Mix C, Mix E, and Mix F showed lower slump loss after 180 minutes.
The compressive strength for all the mixes containing GGBS was lower after 7 days of moisture curing. However, after 28 days moisture curing all the mixes containing GGBS showed improved compressive strength when compared to control mix. Among all the mixes, Mix C showed the best performance in terms of compressive strength. Improved strength for GGBS mixes can be attributed to lower water to binder ratio, increased cementitious content, moisture curing of specimens, and better chemical hydraulic moduli of GGBS.
With respect to durability properties, all the mixes containing GGBS showed improved performance. This was noticed by reduced water absorption and permeability for all the mixes containing GGBS, when compared to control mix. Further, reduction in chloride ion penetration and improved resistance to acid attack was also observed for all the mixes containing GGBS. This behaviour can be attributed to filling up of the pores of concrete matrix with slag and its products of pozzolanic reaction, thus making it dense.
The replacement of Portland cement by 50% GGBS reduced the cost of concrete mix by as much as 23% when compared to industry mix.
According to the results of this study the best performance in terms of workability, strength, durability, and economy was observed for Mix C.
Disclosure of potential conflicts of interest
The authors do not have any conflict of interest.
Acknowledgements
The authors would like to thank ISO laboratory, Bangalore. Appreciation is also extended to Aparna ready mix concrete company and quality team for performing trial mixes.
Additional information
Funding
Notes on contributors
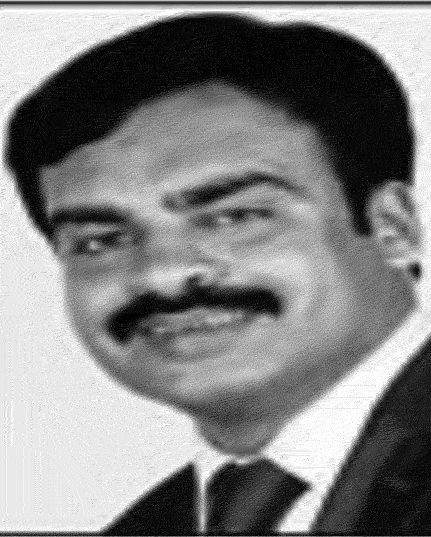
Raghavendra Y B
Raghavendra Y. B. holds a B.E (Civil) and M.Sc. Engineering (Research) degree. Currently, he is pursuing PhD in Civil Engineering at REVA University. He is awarded as young engineer of Karnataka-2016, sponsored by Indian Concrete Institute (Bangalore Centre). He is working for ready mix industry for past 16 years. He is certified lead auditor on QMS as per ISO 9001:2015 standard, Bureau VERITAS. He has published articles in various national and international journals. He is the project external guide for B.E. and MTech students of B.I.T, EPCET, BMS & MVJ College of Engineering. His research interests include special concrete, use of admixtures in concrete, concrete mix design and curing of concrete. He is lifetime member of ICI and ACCE
References
- ASTM C267-01. (2012). Standard test methods for chemical resistance of mortars, grouts, and monolithic surfacings and polymer concretes, ASTM International, West Conshohocken, PA. https://doi.org/10.1520/C0267-20
- ASTM C642-13. (2013). Standard test method for density, absorption, and voids in hardened concrete. ASTM International, West Conshohocken, PA. https://doi.org/10.1520/C0642-13
- ASTM C989/C989M-18a. (2018). Standard specification for slag cement for use in concrete and mortars. ASTM International, West Conshohocken, PA. https://doi.org/10.1520/C0989_C0989M-18A.
- DIN 1048-1. (1991). Testing concrete; testing of fresh concrete (foreign standard)
- Elchalakani, M., Aly, T., & Abu-Aisheh, E. (2014). Sustainable concrete with high volume GGBFS to build Masdar City in the UAE. Case Studies in Construction Materials, 1, 10–15. https://doi.org/10.1016/j.cscm.2013.11.001
- Existing and Potential Technologies for Carbon Emissions Reductions in the Indian Cement Industry. (2013). A set of technical papers produced for the project ‘low carbon technology road map for the Indian cement industry.
- Gao, J. M., Qian, C. X., Liu, H. F., Wang, B., & Li, L. (2005). ITZ microstructure of concrete containing GGBS. Cement and Concrete Research, 35(7), 1299–1304. https://doi.org/10.1016/j.cemconres.2004.06.042
- Ghoddousi, P., Javid, A. A. S., & Sobhani, J. (2014). Effects of particle packing density on the stability and rheology of self-consolidating concrete containing mineral admixtures. Construction and Building Materials, 53, 102–109. https://doi.org/10.1016/j.conbuildmat.2013.11.076
- Güneyisi, E., & Gesoğlu, M. (2011). Properties of self-compacting Portland pozzolana and limestone blended cement concretes containing different replacement levels of slag. Materials and Structures, 44(8), 1399–1410. https://doi.org/10.1617/s11527-011-9706-0
- Higgins, D. (2007). Briefing: GGBS and sustainability. Proceedings of the ICE-Construction Materials, 160(3), 99–101. https://doi.org/10.1680/coma.2007.160.3.99
- Hooton, R. D., & Emery, J. J. (1990). Sulfate resistance of a Canadian slag cement. ACI Materials Journal, 87, 547–555.
- IS 269: 2015. (2015). Ordinary Portland cement – Specification. Bureau of Indian Standards, New Delhi, India.
- IS 383: 2016. (2016). Coarse and fine aggregate for concrete – Specification. Bureau of Indian Standards, New Delhi, India.
- IS 516: 2018. (2018). Hardened concrete- Methods of test. Bureau of Indian Standards, New Delhi, India.
- IS: 10262. (2019). Concrete mix proportioning – Guidelines. Bureau of Indian Standards, New Delhi, India.
- Khodair, Y., & Bommareddy, B. (2017). Self-consolidating concrete using recycled concrete aggregate and high volume of fly ash, and slag. Construction and Building Materials, 153, 307–316. https://doi.org/10.1016/j.conbuildmat.2017.07.063
- Lim, T. Y. D., Teng, S., Bahador, S. D., & Gjørv, O. E. (2016). Durability of very-high-strength concrete with supplementary cementitious materials for marine environments. ACI Materials Journal, 113(1). https://doi.org/10.14359/51687981
- Mohamed, O. A., & Najm, O. F. (2017). Compressive strength and stability of sustainable self-consolidating concrete containing fly ash, silica fume, and GGBS. Frontiers of Structural and Civil Engineering, 11(4), 406–411. https://doi.org/10.1007/s11709-016-0350-1
- Monkman, S., & Shao, Y. (2010). Carbonation curing of slag-cement concrete for binding CO2 and improving performance. Journal of Materials in Civil Engineering, 22(4), 296–304. https://doi.org/10.1061/(ASCE)MT.1943-5533.0000018
- Neville, A. M. (1997). Properties of concrete. Prentice hall.
- Oner, A., & Akyuz, S. (2007). An experimental study on optimum usage of GGBS for the compressive strength of concrete. Cement and Concrete Composites, 29(6), 505–514. https://doi.org/10.1016/j.cemconcomp.2007.01.001
- Raghavendra, Y. B., & Ramalinga Reddy, Y. (2019). Optimum usage of GGBS in ready mix concrete industry. International Journal of Engineering and Advanced Technology, 8,, 4542–4553. https://doi.org/10.35940/ijeat.F8861.088619
- Rashad, A. M. (2018). An overview on rheology, mechanical properties and durability of high-volume slag used as a cement replacement in paste, mortar and concrete. Construction and Building Materials, 187, 89–117. https://doi.org/10.1016/j.conbuildmat.2018.07.150
- Thomas, M. D. A., Scott, A., Bremner, T., Bilodeau, A., & Day, D. (2008). Performance of slag concrete in marine environment. ACI Materials Journal, 105, 628–634.
- Ting, L., Qiang, W., & Yuqi, Z. (2020). Influence of ultra-fine slag and silica fume on properties of high-strength concrete. Magazine of Concrete Research, 72(12), 610–621. https://doi.org/10.1680/jmacr.18.00492
- Topçu, İ. B., & Boğa, A. R. (2010). Effect of ground granulate blast-furnace slag on corrosion performance of steel embedded in concrete. Materials & Design, 31(7), 3358–3365. https://doi.org/10.1016/j.matdes.2010.01.057
- Wang, Q., Wang, D., & Chen, H. (2017). The role of fly ash microsphere in the microstructure and macroscopic properties of high-strength concrete. Cement and Concrete Composite, 83, 125–137. https://doi.org/10.1016/j.cemconcomp.2017.07.021
- Zhang, M. H., Islam, J., & Peethamparan, S. (2012). Use of nano-silica to increase early strength and reduce setting time of concretes with high volumes of slag. Cement and Concrete Composites, 34(5), 650–662. https://doi.org/10.1016/j.cemconcomp.2012.02.005