Abstract
The goal of the current paper is to study the effect of natural pozzolana (NP) when ground to a micro and nano size on some concrete properties. Syria is rich in natural pozzolana with an estimated quantity of nearly 1 billion tonnes. Four properties, namely compressive strength, chloride permeability, chloride-induced reinforcement corrosion and acid attack on mortar, have been investigated. Six levels of micro-NP (from 0% to 50%), and nano-NP (from 0% to 5%) were added as cement replacement to produce the studied concrete/mortar mixtures. The results revealed that grinding NP to extremely fine particles has positive effects. The shortcoming related to the lower early compressive strength can be eliminated. Further, much lower chloride permeability and longer corrosion initiation times were clearly observed in the concrete containing nano-NP. The best results were obtained when NP was added at 30% or more at micro-scale and at 3–4% at nano scale. Furthermore, acid resistance particularly at the early ages of exposure was noticeably improved with such additives. SEM technique fitted with EDX analysis was employed in the current research to study the microstructure of the cement paste after being exposed to acid solutions. XRD and TGA techniques were used as well.
PUBLIC INTEREST STATEMENT
Concrete is the most widely used building material due to its versatility, durability and cost effectiveness. Its main ingredients are aggregates (fine & coarse) and binder (cement and water). The binder is the most expensive component in the concrete mix and can be considered the most controlling factor in terms of the concrete properties. Use of natural additives in the concrete mix, particularly at a nano size, is a good approach. Apart from the better performance, it gives ecological and economic benefits. The current paper investigates the effect of adding natural pozzolana either at micro- or nano-size on some concrete properties.
1. Introduction
Syria has no supplementary cementing materials of an industrial origin. However, it is rich in natural sources. Many quarries of natural pozzolana (NP) exist in the country with an estimated quantity of about one billion tonnes (GEMGR, Citation2011). The annual production of cement in Syria is about 6 million tonnes. This number is highly expected to increase sharply in the future due to the inevitable rebuilding stage.
As Syria is classified among the low-income countries, there are many attempts to find more economic approaches. One of these approaches is the use of natural additives to reduce the production cost of cement. The Syrian plants currently add a significant percentage of NP (~ 25%) to CEM I in order to produce a blended cement of CEM II type. The advantages related to the use of such additives are reported in the literature. These benefits cover the economic, ecological and performance-related aspects (Mehta & Monteiro, Citation2006). The natural additives were widely used at micro-scale in the concrete binder (Ghrici et al., Citation2006; Kaid et al., Citation2015; Pourkhorshidi et al., Citation2010; Senhadji et al., Citation2012; Tchamdjou et al., Citation2017). However, there is a limited work on its use at nano-scale. It was frequently reported in the literature, that the micro natural pozzolana has affected the early mechanical strength of concrete, because of the slowness of the pozzolanic reactions (Al-swaidani, Citation2016). Therefore, the elimination of such shortcoming can be reached through the grinding of this natural pozzolana to nano particles. These nano particles have filling effect and can effectively accelerate the hydration reactions, and thus, concrete of low early strength prepared with nano NP is not expected to be obtained.
Nano-silica additive is the most widely reported in the literature in terms of its use as cement replacement at a nano scale. Its very small particles can fill the pores, leading to a denser microstructure, with more (C-S-H) phases. Consequently, durability and strength properties can be enhanced (Nasution et al., Citation2015; Shebl et al., Citation2009; Singh et al., Citation2013). For instance, Saloma et al. (Nasution et al., Citation2015) reported that the sulfate resistance was significantly improved when nano-silica was added to the concrete mixture. El-Feky et al. (El-Feky et al., Citation2016) in their recent study concluded that adding 1.5% or 3% nano silica has reduced the corrosion rate to 40% when compared with that of the control mix after 7 days of testing. They also reported a reduction in concrete permeability of about 50% as compared to control, when a percentage of 4.5% nano-silica was added. He & Shi (He & Shi, Citation2008) concluded that addition of 1% of nanomaterials such as nano-SiO2 and nanomontimorillonite has improved the resistance of mortar against chloride ion penetration. This improvement was indicated by the reduced coefficient of chloride diffusion. These nanomaterials have also reduced the ionic permeability of the mortar. This reduction was further indicated by the reduced electric charge passing through the mortar. The investigation of Said et al. (Said et al., Citation2012) has showed that adding 3% nano silica has led to a significant improvement in the resistance to chloride penetration. They attributed this improvement to the refinement in the cement matrix pores caused by the addition of such nanoparticles (Said et al., Citation2012). Du et al. (Du et al., Citation2014) used much lower doses of nano-silica. Even at these doses (i.e. 0.3%), significant reductions in water penetration depth and chloride migration coefficient were observed. These reductions were about 45% and 30%, respectively when compared with that of the control. They ascribed this behavior to the easier dispersion of nano-silica when used at a low dosage. Gopalakrishnan & Jeyalakshmi (Gopalakrishnan & Jeyalakshmi, Citation2020) investigated the effects of micro and nano additives on the durability of mortars exposed to combined chloride and sulfate attack. They concluded that all mixtures containing nanoparticles showed low chloride penetrability, thus high corrosion resistance of reinforcement can be obtained. In addition, the mixtures prepared with MK and nanoparticles as cement replacement have had the best performance when exposed to 5%NaCl-5%Na2SO4 for 90 days. More detailed information on the effects of nano-silica on the durability of concrete can be found in the state of the art review recently published by Balapour et al. (Balapour et al., Citation2018).
The current paper covers the second part of a research recently conducted by the authors (Al-swaidani, Citation2019). In addition to studying the mortar/concrete compressive strength, it highlights some important aspects of concrete durability; namely chloride and acid attacks. The investigated concrete mixtures were prepared with binders containing either micro or nano natural pozzolana. The durability-related investigations consist of the following:
Study of the concrete chloride permeability.
Study of the chloride-induced reinforcement corrosion
Study of the acid resistance.
Although many studies on the use of nano particles as cement replacement were reported in the literature, the authors think that the importance of this research can be summarized in the following:
(i) The use of natural pozzolana when added to the binder at nano-scale can be considered a new contribution to the field of using nano natural additives.
(ii) The properties of nano-natural pozzolana-based mortar/concrete such as compressive strength, chloride penetrability and reinforcement corrosion resistance have not been widely studied.
(iii) Very few papers investigating the effects of acid attack on the concrete/mortar containing nanoparticles can be found in literature.
(iv) Six replacement levels ranging from 0% to 50% at micro-scale and from 0% to 5% at nano-scale have been investigated.
(v) The current research can be useful for other regions of similar geology.
(vi) The rebuilding stage which is coming sooner or later in the country will inevitably need such economic approaches.
(vii) The encouraging results obtained by this study might be the motivation of further & comprehensive studies.
Despite all difficulties, the authors have tried to exploit all possibilities & facilities, such as SEM, AFM, XRD and TG/DTA techniques … etc. available in the local laboratories in order to conduct the present experimental work and support the obtained results.
2. Materials and methods
In the current study, Natural pozzolana was quarried from the site of “Tel Shihan” situated about 70 km southeast of Damascus and 15 km northwest of al-Swaida’a province which is widely covered by Harrat al-Shaam, a volcanic field of about 45,000 km2 covering parts from Jordan and KSA (Al-swaidani, Citation2019). Thus, the studied natural pozzoalana is of volcanic origin. It was ground at two levels; i.e. micro and nano scale. The main oxides constituting NP are as follows: SiO2: 44.9%, Al2O3: 16.5%, Fe2O3: 8.9%, CaO: 9.6%, MgO: 8.4% and alkali oxides: 4.4%. The mineralogical analysis of the investigated natural pozzolana carried out by XRD technique (SATOE STADI X-ray diffractometer (XRD) using CuKα radiation; the range of the scan is from 5° to 70°) with its micrographs obtained by SEM (scanning electron microscopy, VEGA II TESCAN) & AFM (Nanoscope EasyScan II Atomic Force Microscope) techniques is presented in . The vesicular structure is clearly seen in .a & 1.b. The minerals detected in NP are Fujasite (Fu), Anorthite (An), Forstrite (Fo), Diopside (Dp) and Calcite (Ca). A glassy phase was also detected in NP as shown in .c. The dominant elements in NP are Si & Al and to a lesser degree Fe, Ca and Mg as clearly seen in .d. The morphological analysis of NP after being ground to a nano scale is shown in .e and .f. It can be seen that SEM and AFM techniques have yielded a similar structure.
Figure 1. Photographs and Microanalysis of the investigated natural pozzolana. (a) Photograph of the natural pozzolana grains, as received. (b) Scanning Electron Micrograph (SEM) of a NP grain showing its vesicular structure. (c) XRD analysis of NP showing the following minerals: An: Anorthite; Ca: Calcite; Dp: Diopside; Fo: Forsterite and Fu: Faujasite. (d) Energy Disperse X-ray (EDX) analysis of NP. (e) SEM micrograph of Nano-NP. (f) Micrograph of Nano-NP taken using Atomic Force Microscopy (AFM)
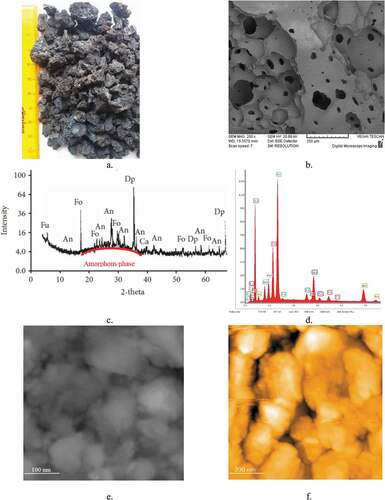
NP either at micro or nano-scale was added as cement replacement at 6 percentages; 0% (reference), 10%, 20%, 30%, 40% and 50% were added at micro level, and 0%, 1%, 2%, 3%, 4% and 5% were added at nano level. The added percentages were made by mass. The micro natural pozzolana (Micro-NP) has been obtained after 2.5 hours of grinding in a dry condition, while the nano natural pozzolana (Nano-NP) was obtained after 6 hours of grinding using a ball mill (Retsch, S100, Germany); 3 hours in a wet condition followed by 3 hours of grinding in a dry condition. The laboratory grinding ball mills for each Micro-NP and Nano-NP are of capacities of 25 kg and 100 g, respectively (Al-swaidani, Citation2019). The particle size distributions of both Micro-NP and Nano-NP analysed by a laser analyser; Malvern Master sizer 2000 model are displayed in . The median particle sizes of Micro-NP and Nano-NP are about 14 µm and 92 nm, respectively. The cement used in this study is of Cem. I type with the following properties: a) Median particle size: 15 µm; b) Its main components, calculated using Bogue’s Formulas: C3S: 60.82, C2S = 10.31, C3A = 7.02, C4AF = 10.73. The investigated mortar/concrete mixtures have been prepared using the aforementioned binders, potable water, a standard sand for mortars and fine & coarse aggregates for concrete mixtures. The water-binder (w/b) ratio used in making concrete/mortar mixtures was 0.5. The coarse and fine aggregates were crushed dolomitic stone and natural sand. The aggregate grading is plotted in . The method of mixing proposed by Jo et al. (Jo et al., Citation2007) with some modification was adopted in the present study.
The current paper investigates the following important strength and durability-related properties:
(i) Compressive strength of mortar
(ii) Chloride penetration into the concrete mixtures.
(iii) Chloride-induced corrosion of reinforcement embedded in the formulated concretes.
(iv) Acid attacks on mortars prepared using either Micro-NP or Nano-NP.
2.1. Compressive strength of mortars/concrete
The compressive strength development of mortars was determined on 50 mm cubic specimens prepared with the studied binders and a standard sand. The water-binder ratio was 0.5. The test was carried out after 2, 7, 28, 90 and 180 day curing, using the “Zwick Roell” testing machine shown in , at a loading rate of 2400 ± 200 N/s. In addition, 150 mm3-cubic concrete specimens prepared with the studied binders were also tested under compression after 2, 7, 28, 90 and 180 day curing, using ELE testing machine of 2000 kN capacity.
2.2. Chloride ion penetration
This property was investigated using the procedure described in ASTM ca. 1202. The Schematic representation of the chloride ion penetration test with a photograph of the experimental set-up are shown in . Three concrete cylinders of 100 × 200 mm were cast. Two curing ages were studied; namely 28 and 90 days. Slices of Ø100 mm and 50 mm in height were extracted from the middle part of each concrete cylinder. After 6 hours of exposure to the 3% NaCl solution, there was calculated the charge passed through the tested slices. This calculation is described in the aforementioned standard, i.e. ASTM ca. 1202. When the charge value is less than 2000 Coloumbs, the investigated concrete can be classified as low permeable to chloride ions.
Figure 5. Schematic representation of the chloride ion penetration test (a) with a photograph of the experimental set-up (b)
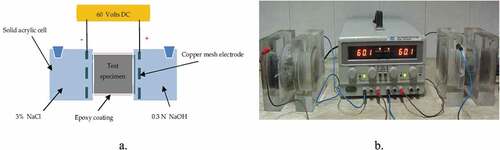
2.3. Chloride-induced corrosion of reinforcement
This property was evaluated using a rapid test performed on what is termed as “Lollipop RC specimen”. This specimen was immersed in a sodium chloride (NaCl) solution with a concentration of 15%. In the galvanic cell, the steel embedded in the specimen “the working electrode” was connected to the positive terminal while a steel plate “the counter electrode” was connected to the negative one. A potential of 12 V was impressed to initiate the corrosion process. The RC specimen was monitored at 3 hours-intervals to observe the corrosion initiation and to record the current readings. Three Lollipop RC specimens of each concrete mixtures were tested after 28 & 90 days curing. More details about this test can be found in a reference recently published by al-Swaidani & Aliyan (Al-swaidani & Aliyan, Citation2015).
2.4. Acidic attacks
The experimental part also covers an important aspect of the exposure to industrial aggressive environments. This part was evaluated in accordance with ASTM C267 (2001). The two aggressive acids simulating such environments are 5% HCl and 5% HNO3 with pH values of 0.4 & 0.45, respectively. The 28-day cured-cubic mortars prepared using either micro or nano additives were immersed in the aforementioned aggressive solutions for 84 days. The acid solution was renewed weekly. The specimen weight was recorded at 0, 2, 7, 14, 28, 56 and 84 days of exposure. The loss in weight (ΔW) was calculated using the equation nr. (1).
ΔW (%) = (Wo-Wi)/Wo (1)
Where Wo is the original weight (in grams), Wi is the weight (in gram) of the specimen after i day of exposure to the acidic solution.
3. Results and discussion
3.1. Compressive strength of mortars
The results of the compressive strength test carried out on cubic mortars/concrete were displayed in . As seen in .a, all mortars/concrete prepared using Micro-NP exhibited compressive strength values of less than that of the reference mortar/concrete; i.e. with zero additive, particularly at early ages. This expected result, which was similarly reported by other researchers when similar natural pozzolana were investigated (Al-Zboon & Al-Zou’by, Citation2016; Ghrici et al., Citation2006; Kaid et al., Citation2015; Ramezanianpour et al., Citation2010; Senhadji et al., Citation2012), can be attributed to the pozzolanic reactions. These reactions slowly occur between the amorphous phase in natural pozzolana (SiO2active & Al2O3active) and the portlandite formed through the hydration reactions of cement compounds. However, with the increase in curing ages, the compressive strength of mortar/concrete specimens containing micro-NP has attained values close to that of the reference mortar/concrete. Some useful correlations between the relative compressive strength and the curing time at all percentages of Micro-NP have been extracted, as shown in .b. The correlation coefficients of R2 ≥ 0.9 indicate an excellent correlation between these parameters. (Montgomery & Peck, Citation1982).
On the other hand, all mortars/concrtete prepared using Nano-NP, particularly at early ages, achieved higher values when compared with that of the control; .d & e. This might be explained by the effect that the nano particles have. Because of their high surface area and superior pozzolanic reactivity (-Askkarinejad et al., Citation2012), nano additives accelerate the hydration process effectively and thus lead to formation of a matrix of reduced porosity and enhanced strength (Sumesh et al., Citation2017). In addition, nano particles might have a filler effect as they fill the pores. It is to be noted that the correlation between the relative compressive strength and the curing time when Nano-NP was used has less strength when compared with Micro-NP. This clearly indicates that the Micro-NP-based mortars/concrete have more sensitivity to curing time when compared with the mortars/concrete prepared with nano particles. For instance, mortars prepared with 30% Micro-NP have recorded 21.5 MPa after 7 day curing; i.e. about 0.64 of the control. On the other hand, the mortars prepared with 3% Nano-NP have recorded much bigger value (i.e. about 39 MPa) which exceeded the compressive strength of the reference mortar by about 23%. However, when the curing process continued up to 180 days, the compressive strength of 30% Micro-NP-based mortars attained 50.57 MPa, which is less than that of the control (i.e. 56.03) by only 9% vis-à-vis an increase of only 11% when 3% Nano-NP was added. Further, it should be noted that the cubic concrete specimens under compression have a trend similar to that of mortars as shown in .c & f.
3.2. Chloride ion penetration
The results obtained by the chloride permeability test are depicted in . All Micro-NP- and Nano-NP- based concrete specimens exhibited more resistance to chloride ion penetration when compared with the concrete of zero additive. The 28 day-cured concretes prepared with 4% Nano-NP have recorded values of less than 2000 Coulombs and it is much lower than that of the control. In addition, this value is less than that recorded by the 28 day-cured concrete of 30% or 40% Micro-NP. However, after 90 days curing, the values obtained were close to each other and approached 1000 Coulombs. This can be explained by the continuation of the pozzolanic reaction, which leads to formation of more hydration products such as additional C-S-H or C-A-S-H. The formation of such secondary hydration products results in refining the pores in the matrix and thus leads to a much lower permeable structure (Al-swaidani & Aliyan, Citation2015; Ghrici et al., Citation2006; Pourkhorshidi et al., Citation2010).
Further, it can be generally seen that the concrete specimens containing nano-NP have better performance than that of micro-NP-based concrete particularly at ages no longer than 28 days. This can be due to the higher reactivity of the natural pozzolana when ground to nano-scale particles (-Askkarinejad et al., Citation2012; Askkarinejad et al., Citation2016). These highly reactive nanoparticles will accelerate the hydration process and thus more cementitious compounds can be formed. This leads to a less permeable concrete (Sumesh et al., Citation2017). Furthermore, it should be noted that moving from 4% to 5% nano-NP has changed the trend and slightly increased the concrete chloride ion penetrability. This result needs more investigation. However, according to the author, it can be ascribed, at the current time, to some agglomeration, which may occur particularly when high doses of nanoparticles such as 5% or more are used (Al-swaidani, Citation2019; Said et al., Citation2012; Shebl et al., Citation2009).
3.3. Chloride-induced corrosion of reinforcement
The reinforcement corrosion was evaluated by an accelerated test. A constant voltage was applied throughout the test. During the test, the current values were recorded with time. shows a schematic representation of the current values versus time “in hour” recorded for 3% Nano-NP and 30% Micro-NP specimens. This representation consists of three regions; the first one is characterized by a descending curve. This descending part might be attributed to the salts in the solution, which temporarily blocks the pores (Reddy et al., Citation2011). The second region is characterized by a constant current or a curve of slightly increased current. The third part is characterized by a sudden rise in the current values, which is associated with the appearance of cracks on the surface of the RC specimen.
Figure 8. Typical curves of current versus the exposure time (a), with macrographs of RC specimens that suffered a chloride attack, (b, left) and photograph of corroded rebars after being removed from the RC specimens and cleaned of the corrosion products (b, right)

displays the values representing the average corrosion initiation times recorded for all investigated concrete mixtures after curing ages of 28 and 90 days. All concrete specimens prepared either with Micro- or Nano-NP, exhibited more resistance to chloride attack when compared with the plain concrete. Adding 3% Nano-NP or 30% Micro-NP delayed the initiation of reinforcement corrosion to about 400 h; i.e. roughly more than three times the corrosion initiation time recorded by the reference specimen. This can be attributed to the filling effect of nano additive, which leads to formation of a denser microstructure. These results are similar to those reported by other researchers (Al-swaidani & Aliyan, Citation2015; Guneyisi et al., Citation2005; Horsakulthai et al., Citation2011). In addition, the presence of NP either at micro or nano scale might increase the chloride binding capacity of the binder paste, and thus the available chloride concentration will be lower (Birnin-Yauri & Glasser, Citation1998; Thomas et al., Citation2012; Yang et al., Citation2019). Nano-NP can react with CH and gypsum, and thus the content of AFm phase is increased, and more chloride ions are probably restricted.
Figure 9. Values of corrosion initiation time recorded for the tested RC specimens. a) micro-NP, b) nano-NP
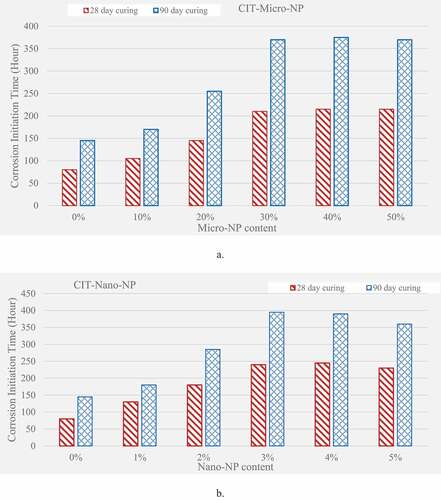
Further, it should be noted that moving from 4% to 5% nano-NP has changed the trend and slightly decreased the reinforcement corrosion resistance. This result needs more investigation. However, according to the author, it can be ascribed at the current time, to some agglomeration, which may occur particularly when high doses of nanoparticles such as 5% or more are used (Al-swaidani, Citation2019; Said et al., Citation2012; Shebl et al., Citation2009). This result is consistent with the results obtained in the chloride ion penetration test.
Because the corrosion test is time-consuming, an attempt was made to correlate the results obtained with those of the chloride penetration test, which can be done in a shorter time. This correlation is illustrated in . There was observed an inverse relationship between CIP and CIT; i.e. when the charge passed “in Coloumbs” increased the corrosion initiation time decreased, the regression coefficient (R2) of this correlation is about 0.95. This number denotes an excellent relationship between the CIP and CIT (Montgomery & Peck, Citation1982). Therefore, the obtained relationship is reliable and might be helpful for the concrete designers.
3.4. Acid attack
The weight loss was considered as an indicator of the measurement of the acid resistance performance offered by the additives used either at micro or nano-scale. The results are illustrated in for the attacks made by 5% HCl or 5% HNO3 solutions, respectively. As observed, the investigated mortars suffered such attacks, despite the fact that the Nano NP-based mortars have had the highest resistance to such aggressive environments. For instance, after 7 days of exposure to 5% HCl or 5% HNO3, the reference mortar lost about 12% and 10% by weight, respectively. However, 3% Nano NP-based mortar has lost only 8% and 6%, respectively. Similar results with a slight increase in weight loss values were obtained with the use of a percentage of 30% Micro-NP or more. The better performance of Micro- or Nano-NP-based mortars can be attributed to the pozzolanic reaction. This reaction between the glassy phase in NP and CH formed during the hydration of cement compounds, i.e. C3S & C2S, led to a refinement of the pore structure resulting in a highly impermeable matrix. In addition, the pozzolanic reaction also fixes Ca(OH)2, which is usually the most affected product of cement hydration in so far as the acidic attack is concerned (Neville, Citation2011). The best performance in the nano additives-based mortars can be due to the lower porosity and the lower permeability, which were achieved by the early pozzolanic reactions and the filling effect that the nano particles have.
Figure 11. Weight loss values versus exposure time of cubic mortars immersed in 5% HCl solution with a macrograph of some corroded samples. a) Micro-NP-based mortars, b) Nano-NP-based mortars
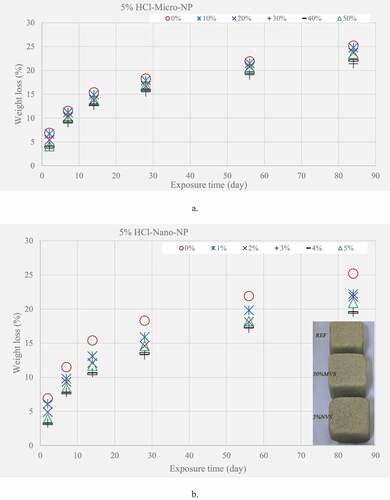
Figure 12. Weight loss values versus exposure time of cubic mortars immersed in 5% HNO3 solution with a macrograph of some corroded samples. a) Micro-NP-based mortars, b) Nano-NP-based mortars
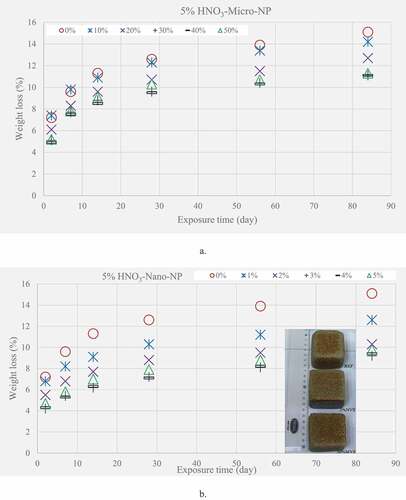
Figure 13. SEM micrographs accompanied by EDX analysis of pastes after being immersed in 5% HCl solution for 28 days. a) the reference paste, b) the paste containing 30% Micro-NP, c) the paste containing 3% Nano-NP
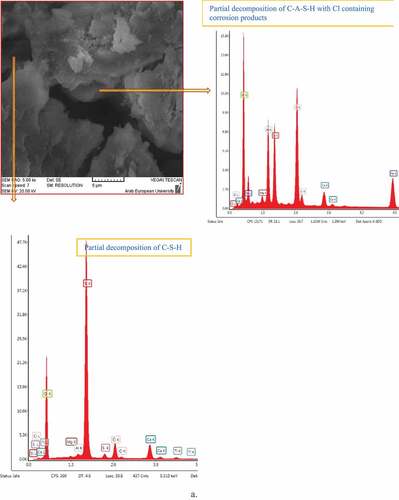
Further, the microstructural analysis shown in –16, demonstrates suffering of the reference paste after the exposure to the acidic solutions. A porous matrix can be obviously noted in the reference paste, .a & .a. The highly soluble products such as CaCl2 and Ca(NO3)2 formed through the acidic attack leached away leaving large pores behind. Moreover, partial decomposition of C-S-H can be traced easily. On the other hand, a less porous and more homogeneous microstructure can be noted in the 3% Nano-NP- or in the 30% Micro-NP-based pastes, .b, 13.c, 16.b and 16.c., even under exposure to acidic solutions for 28 days. This can be ascribed to the pozzolanic reactions, which consume CH, the most affected compound by such kind of attack (Guneyisi et al., Citation2005). In addition, it can be obviously seen in .c, that Friedel salt’ hexagonal plates were formed when the nano-NP-based paste was exposed to 5% HCl. Such Friedel salt formation was also reported by other researchers (Israel et al., Citation1997) This salt may further block the pores and thus increase the resistance to 5% HCl solution. Moreover, the Friedel’s salt made the cement paste have a denser microstructure and a lower permeability (Shao et al., Citation2013).The Friedel’s salt (3CaO.Al2O3.CaCl2.10H2O) which is a member of AFm family, is more stable than the hydroxyl aluminate AFm (Birnin-Yauri & Glasser, Citation1998), although the formation of Cl-Afm phase can be also traced, .c. Such formation of Friedel’ salt was confirmed through XRD & TGA analysis, as shown in , respectively. Further, after 28 days of exposure to 5% HCl clearer amorphous phases can be seen. This is probably due to the partial degradation of C-S-H & C-A-S-H by the acidic attack and its transformation to amorphous silicates, although significant crystalline phases can be still seen. This result is in well agreement with the results obtained by Gutberlet et al. (Gutberlet et al., Citation2015) and Pavlik (Pavlík, Citation1994).
Figure 14. XRD of 3% Nano-NP-based pastes, after immersion in lime-saturated water and in 5% HCl solution for 28 days, respectively. (C-S-H: calcium silicate hydrates; C-A-S-H: calcium silicate & aluminate hydrates; AFt: Ettringite; AFm: Monosulfoaluminate; CH: calcium hydroxide; FS: Friedel’s salt; CC: calcium chloride)
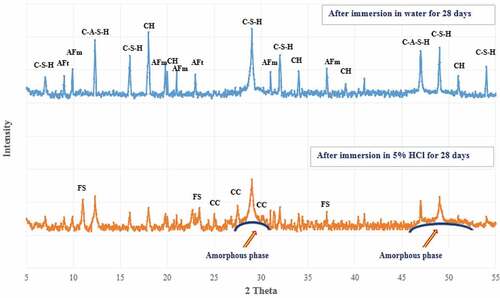
Figure 15. TGA (a) & DTA (b) analysis of 3% Nano-NP-based pastes, after immersion in lime-saturated water and in 5% HCl solution for 28 days, respectively. (FS: Friedel’s salt; CC: calcium chloride)
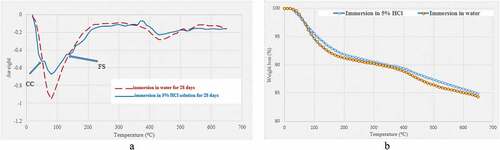
4. Conclusion
As many quarries of NP are available in Syria, the attempt to add NP at nano level can be considered a promising approach to overcome the shortcomings associated with the use of NP at micro level.
The following conclusions can be highlighted:
A small amount (~3%) of Nano-NP can be beneficial to obtain far higher early strength as compared with that obtained, particularly when a significant amount of Micro-NP (~30%) was added.
The results of chloride ion penetration test revealed that 3% & 4% Nano-NP-based concretes had far higher resistance to chloride diffusion than the concrete of zero NP. Similar results were also observed with the use of Micro-NP at a percentage of 30% or more.
The longest corrosion initiation times were noted in the RC concrete specimens containing 30% Micro-NP or 3–4% Nano-NP. Therefore, a NP-based concrete structure that is more sustainable & durable even in chloride-bearing environments can be achieved.
The acid resistance of the tested mortars was noticeably improved when Micro-NP or Nano-NP was added. The microstructural analysis showed that NP-based pastes, even after 28 days of exposure to acid solutions, were less porous and more homogeneous when compared with the paste with zero content of NP.
It is worth mentioning that the current paper highlighted some short-term tests. For further investigation, long-term tests are highly recommended particularly when reinforced concrete containing either micro- or nano-NP are exposed to aggressive environments such as sea or saline water.
Disclosure statement
No potential conflict of interest was reported by the author(s).
Additional information
Funding
Notes on contributors
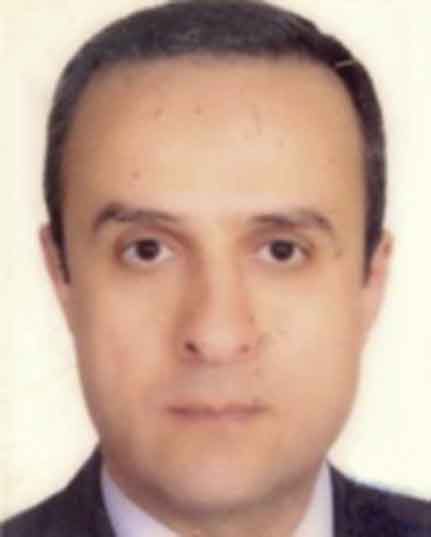
Aref M. Al-swaidani
Aref M. al-Swaidani received his PhD in Materials and Structural Engineering from INSA de Lyon, France and Damascus University, Syria (under joint supervision). He is currently associate professor at Faculty of Architectural Engineering, Arab International (Formerly European) University, Syria (Full time), and at Higher Institute of Earthquake Research and Studies, Damascus University (Part time). His research interests cover durability and sustainability of concrete structures, use of nanomaterials in engineering applications, recycling of demolished concrete structures, Application of machine learning in civil engineering, improvement of clayey soil properties using micro- and nano-additives.
References
- Al-swaidani, A. M. (2016). Prediction of compressive strength and some permeability related properties of concretes containing volcanic scoria as cement replacement. Romanian Journal of Materials, 46(4), 505–23. https://solacolu.chim.upb.ro/p505-514.pdf
- Al-swaidani, A. M. (2019). Use of micro and nano volcanic scoria in the concrete binder: study of compressive strength, porosity and sulfate resistance. Case Studies in Construction Materials, 11(December 2019), e00294. https://doi.org/10.1016/j.cscm.2019.e00294
- Al-swaidani, A. M., & Aliyan, S. D. (2015). Effect of adding scoria as cement replacement on durability-related properties. International Journal of Concrete Structures and Materials, 9, 241–254. https://doi.org/10.1007/s40069-015-0101-z
- Al-Zboon, K., & Al-Zou’by, J. (2016). Effect of volcanic tuff on the characteristics of cement mortar. European Journal of Environmental and Civil Engineering. https://doi.org/10.1080/19648189.2015.1053151
- -Askkarinejad, A., Pourkhorshidi, A., & Parhizkar, T. (2012). Evaluation the pozzolanic reactivity sonochemically fabricated nano natural pozzolan. Ultrasonics Sonochemistry, 19(1), 119–124. https://doi.org/10.1016/j.ultsonch.2011.05.005
- Askkarinejad, A., Zisti, F., Pourkhorshidi, A., & Parhizkar, T. (2016). Hydrothermal preparation of natural pozzolan nanostructures as a new route to activate cement replacement materials. Synthesis and Reactivity in Inorganic, Metal-Organic, and Nano-Metal Chemistry 46(8), 1157-1162. https://doi.org/10.1080/15533174.2013.776595
- Balapour, M., Joshaghani, A., & Althoey, F. (2018). Nano-SiO2 contribution to mechanical, durability, fresh and microstructural characteristics of concrete: A review. Construction and Building Materials, 181(August 2018), 27–41. https://doi.org/10.1016/j.conbuildmat.2018.05.266
- Birnin-Yauri, U. A., & Glasser, F. P. (1998). Friedel’s salt, Ca2Al(OH)6(Cl,OH)z2H2O: its solid solutions and their role in chloride binding. Cement and Concrete Research, 28(12), 1713–1723. https://doi.org/10.1016/S0008-8846(98)00162-8
- Du, H., Du, S., & Liu, X. (2014). Durability performances of concrete with nano-silica. Construction and Building Materials, 73,(30 December 2014), 705–712. https://doi.org/10.1016/j.conbuildmat.2014.10.014
- El-Feky, M. S., Serag, M. I., Yasien, A. M., & Elkady, H. (2016). Bond strength oF nano silica concrete subjected to corrosive environments. ARPN Journal of Engineering and Applied Sciences, 11(23), 13909–13924. http://www.arpnjournals.org/jeas/research_papers/rp_2016/jeas_1216_5472.pdf
- GEMGR. (2011). ““The General Establishment of Geology and Mineral Resources” in Syria (inArabic),” AGuide forMineral Resources in Syria.
- Ghrici, M., Kenai, S., & Meziane, E. (2006). Mechanical and durability properties of cement mortar with Algerian natural pozzolana. Journal of Material Science, 41(21), 6965–6972. https://doi.org/10.1007/s10853-006-0227-0
- Gopalakrishnan, R., & Jeyalakshmi, R. (2020). The effects on durability and mechanical properties of multiple nano and micro additive OPC mortar exposed to combined chloride and sulfate attack. Materials Science in Semiconductor Processing, 106(February 2020), 104772. https://doi.org/10.1016/j.mssp.2019.104772
- Guneyisi, E., Ozturan, T., & Gesoglu, M., & Guneyisi. (2005). A study on reinforcement corrosion and related properties of plain and blended cement concretes under different curing conditions. Cement & Concrete Composites, 27(2005), 449–461. https://doi.org/10.1016/j.cemconcomp.2004.05.006
- Gutberlet, T., Hilbig, H., & Beddoe, R. E. (2015). Effect of mineral acids on the degradation process. Cement and Concrete Research, 74(August 2015), 35–43. https://doi.org/10.1016/j.cemconres.2015.03.011
- He, X., & Shi, X. (2008). Chloride permeability and microstructure of Portland cement mortars incorporating nanomaterials, transportation research record. Journal of the Transportation Research Board 2070(1), 13–21. https://doi.org/10.3141/2070-03
- Horsakulthai, V., Phiuvanna, S., & Kaenbud, W. (2011). Investigation on the corrosion resistance of bagasse-rice husk-wood ash blended cement concrete by impressed voltage. Construction and Building Materials, 25(1), 54–60. https://doi.org/10.1016/j.conbuildmat.2010.06.057
- Israel, D., Macphee, D., & Lachowski, E. (1997). Acid attack on pore-reduced cements. J. Mater. Sci, 32(15), 4109–4116. https://doi.org/10.1023/A:1018610109429
- Jo, B. W., Kim, C. H., Tae, G., & Park, J. B. (2007). Characteristics of cement mortar with nano-SiO2 particles. Construction and Building Materials, 21(6), 1351–1355. https://doi.org/10.1016/j.conbuildmat.2005.12.020
- Kaid, N., Cyr, M., & Khelafi, H. (2015). Characterization of an Algeria natural pozzolan for its use in eco-efficient cement. Int. J. Civ. Eng, 13(4A), 444–454. http://ijce.iust.ac.ir/article-1-974-en.html
- Mehta, P. K., & Monteiro, P. J. M. (2006). Concrete: Microstructure, properties and materials (3ed). McGraw-Hill.
- Montgomery, D. C., & Peck, E. A. (1982). Introduction to linear regression analysis. Wiley.
- Nasution, A., Imran, I., & Abdullah, M., & Saloma. (2015). Improvement of concrete durability by nanomaterials. Procedia Engineering, 125(2015), 608–612. https://doi.org/10.1016/j.proeng.2015.11.078
- Neville, A. M. (2011). Properties of Concrete (fifth edition). Pearson Education, 2011.
- Pavlík, V. (1994). Corrosion of hardened cement paste by acetic and nitric acids part I: Calculation of corrosion depth. Cem. Concr. Res, 24(3), 551–562. https://doi.org/10.1016/0008-8846(94)90144-9
- Pourkhorshidi, A. R., Najimi, M., Parhizkar, T., Jafarpour, F., & Hillemeier, B. (2010). Applicability of the standard specification of ASTM C 618 for evaluation of natural pozzolans. Cement & Concrete Composites, 32(10), 794–800. https://doi.org/10.1016/j.cemconcomp.2010.08.007
- Ramezanianpour, A., Mirvalad, S., Aramun, E., & Peidayesh, M. (2010). Effect of four Iranian natural pozzolans on concrete durability against chloride penetration and sulphate attack. In P. Claisse (Ed.), Proceedings of the 2nd international conference on sustainable construction materials and technology, 28-30 June, Ancona, Italy. http://www.claisse.info/2010%20papers/t37.pdf
- Reddy, D. V., Edouard, J. B., Sobhan, K., & Rajpathak, S. S. (2011). Durability of reinforced fly ash-based geopolymer concrete in the marine environment. In Proceedings of the 36th conference on our world in concrete & structures, August 14–16, Singapore: CIPREMIER PTE LTD.
- Said, A. M., Zeidan, M. S., Bassuoni, M. T., & Tian, Y. (2012). Properties of concrete incorporating nano-silica. Construction and Building Materials, 36(2012), 838–844. http://doi.org/10.1016/j.conbuildmat.2012.06.044
- Senhadji, Y., Escadeillas, G., Khelafi, H., Mouli, M., & Benosman, A. S. (2012). Evaluation of natural pozzolan for use as supplementary cementitious material. European Journal of Environmental and Civil Engineering, 16(1), 77–96. https://doi.org/10.1080/19648189.2012.667692
- Shao, Y., Zhou, M., Wang, W., & Hou, H. (2013). Identification of chromate binding mechanisms in friedel’s salt. Construction and Building Materials, 48(November 2013), 942–947. http://doi.org/10.1016/j.conbuildmat.2013.07.098
- Shebl, S., Allie, L., Morsy, M., & Aglan, H. (2009). Mechanical behaviour of activated nano silicate filled cement binders. Journal of Materials Science, 44(6), 1600–1666. https://doi.org/10.1007/s10853-008-3214-9
- Singh, L. P., Karade, S. R., Bhattacharyya, S. K., Yousuf, M. M., & Ahlawat, S. (2013). Beneficial role of nano-silica in cement based materials- a review. Construction and Building Materials, 44(October 2013), 1069–1077. https://doi.org/10.1016/j.conbuildmat.2013.05.052
- Sumesh, M., Alengaram, U. J., Jumaat, M. Z., Mo, K. H., & Alnahhal, M. F. (2017). Incorporation of nano-materials in cement composite and geopolymer based paste and mortar-A review. Construction and Building Materials, 148(September 2017), 62–84. https://doi.org/10.1016/j.conbuildmat.2017.04.206
- Tchamdjou, W. H. J., Grigoletto, S., Michel, F., Courard, L., Cherradi, T., & Abidi, M. L. (2017). Effects of various amounts of natural pozzolans from volcanic scoria on performance of Portland ement mortars. Int. J. Eng. Res. Afr, 32(2017), 36–52. https://doi.org/10.4028/www.scientific.net/JERA.32.36
- Thomas, M. D. A., Hooton, R. D., Scott, A., & Zibara, H. (2012). The effect of supplementary cementitious materials on chloride binding in hardened cement paste. Cement and Concrete Research, 42(1), 1–7. https://doi.org/10.1016/j.cemconres.2011.01.001
- Yang, Z., Gao, Y., Mu, S., Chang, H., Sun, W., & Jiang, J. (2019). Improving the chloride binding capacity of cement paste by adding nano-Al2O3. Construction and Building Materials, 195(20 January 2019), 415–422. https://doi.org/10.1016/j.conbuildmat.2018.11.012