Abstract
Austempered ductile iron (ADI) has numerous applications because it is lightweight and has excellent mechanical properties. However, although the ADI obtained by the traditional austempering process possesses high strength and hardness, it has low toughness. To obtain superior mechanical properties for ADI, a modified austempering process is adopted. In this study, ADI is produced using a novel modified method with multi-stage austempering heat treatments. Various mechanical properties are determined to assess the relationship between heat treatment parameters and properties. Microstructural analysis is performed using scanning electron microscopy. The ADI produced using the aforementioned austempering process involving heat treatment at 420 °C is found to have the optimum combination of ultimate tensile strength and impact energy. Moreover, a higher nucleation rate is observed for samples supercooled at 260 °C over a short period.
PUBLIC INTEREST STATEMENT
Austempered Ductile Irons (ADI) are widely used in automobile industry and agriculture equipment due to its excellent strength to weight ratio. However, the mechanical properties of the ADI are dependent on the type of austempering heat treatment and its parameters. It is important to obtain the optimum combination of strength and impact energy in ADI. “Austempering” is a heat treatment process which improves the strength and hardness of the ductile iron without compromising in toughness. Manganese addition helps increasing the hardenability of the ADI. Hence, it is essential to select the appropriate type of austempering heat treatment with optimum addition of manganese, so that ADI acquires required properties. This article reports the effect of novel two step austempering treatment on the mechanical properties of ADI alloyed with manganese addition. This study helps to upgrade the knowledge regarding the assessment of manganese alloyed ADI produced by a novel method.
1. Introduction
Austempered ductile iron (ADI) is a revolutionary material extensively used in various applications because of its optimum combination of mechanical properties (Parez et al., Citation2006). Its unique microstructure, ausferrite, enables it as a substitute material for widely used materials, such as steel and aluminum, because it is lightweight and has high strength (Lerner & Kingsbury, Citation1997; Olawale & Oluwasegun, Citation2016). The addition of appropriate amounts of manganese to ADI improves material hardenability (Pereiraa et al., Citation2020). In addition to high hardness and tensile strength, the ADI must also be highly ductile and tough. Although the conventional austempering treatment is applied to achieve these properties, a modified austempering process may be more effective for simultaneously improving strength and toughness (J Yang & Putatunda, Citation2004). This improvement is mainly attributed to the microstructure refinement afforded by modified austempering and the high amount of carbon retained in austenite. The low-temperature supercooling of ductile iron initiates faster nucleation, resulting in finer ferrite. In the second step, the elevated austempering temperature boosts the diffusion rate of carbon, increasing the carbon content in the retained austenite. The combination of these properties results in high strength and toughness (Gazda et al., Citation2018). Thus, the modified austempering treatment can produce ADI with the optimum combination of strength and toughness. The foregoing is important considering that ADI has numerous uses, such as in farm machinery and equipment, heavy trucks, conveyors and tooling, railways, gears/shafts/powertrains, and light vehicles (Barbosa et al., Citation2015; Cemal Cakir & Isik, Citation2008; Klocke et al., Citation2010; Narasimha Murthy et al., Citation2009; Seker & Hasirci, Citation2006).
The studies on the properties of ADI and their correlation with the heat treatment parameters involved in the modified austempering process have been conducted by few researchers. Susil and Putatunda (Susil & Putatunda, Citation2001) reported the increase in the fracture toughness in low-manganese ADI produced by the two-stage austempering treatment. Yue Yi et al. (Yi et al., Citation2019) studied the characterization of ADI alloyed with copper produced using the non-conventional austempering process. The austempering heat treatment was performed at varying temperatures instead of constant temperature. The results indicate that the amount of retained austenite decreases as the temperature in the second-step of austempering increases. Gazda et al. (Gazda et al., Citation2018) analyzed the foremost properties of ADI in the two-step austempering process and reported that better mechanical properties are obtained using the modified process. Yang et al. (Jianghuai Yang & Putatunda, Citation2004) reported the strain hardening behavior of ADI afforded by the modified austempering treatment. The two-step austempering process was observed to result in fine grain sizes with increased hardness and yield strength.
Hardenability is an important property that must be considered in the selection of materials. To achieve increased hardenability, manganese may be added to ductile iron. However, the proportion of added manganese should be carefully ascertained to avoid carbide precipitation.
In the present work, the effect of different Mn proportions introduced to ADI and the resulting properties of ADI alloyed with these proportions are assessed.
2. Materials and methods
2.1. Material
Ductile iron casting is performed according to the standard guidelines (ASTM A897/A897M −15, Citation2015). The manganese content is varied from 0.3 to 1 wt% in three levels, and the compositions of cast alloys are checked by spectroscopic analysis. The proportions of all elements, except manganese, are maintained in three different castings; the chemical composition of ductile iron castings is summarized in . The ultimate tensile strength is obtained according to the intrusions given in ASTM standard E8/E8M (ASTM E8/E8M, Citation2016). For the microstructural analysis and hardness test, the specimens are machined out from round bars. For chemical composition, see the supplementary Table 1.
Table 1. Chemical composition of ductile iron
2.2. Design of experiments
The parameters selected for the heat treatment process are listed in .
Table 2. Factors with levels
2.3. Heat treatment and characterization
The heat treatment process is illustrated in below.
The ductile iron samples were initially placed into a muffle furnace for austenitization. These were heated by the oven at the austenitization temperature of 950 °C maintained for 2 h. Then, they were rapidly quenched in a salt bath to a supercooling temperature of 260 °C for 5 min. Thereafter, the samples are swiftly transferred to another salt bath of the same composition to perform austempering at different temperatures previously selected. For all trials, the austempering duration was 2 h at a constant temperature of 950 °C, and supercooling was conducted at 260 °C for 5 min.
The impact energy is calculated using the Charpy impact test as per ASTM A327/A327M (ASTM A327/A327M, Citation2011). The impact test was conducted on the “V” notched bar using the “Charpy” impact test machine (FIE, Model IT-30).
3. Results and discussions
summarizes the test results for hardness, ultimate tensile strength, ductility, and impact energy of the ADI samples produced by the modified heat treatment.
Table 3. Properties of ADI
The analysis indicates that increasing the austempering temperature decreased hardness and tensile strength. However, the amount of reduction yielded by this modified austempering process is considerably less than that resulting from the conventional heat treatment method (Hegde et al., Citation2019). The austempering temperature of 420 °C has resulted in the combination of superior mechanical properties. The effects of austempering temperature on various mechanical properties are graphically illustrated.
4. Microstructural analysis
Scanning electron microscopy (SEM) was used to determine the microstructures of heat-treated samples. show the microstructures of samples resulting from the conventional (without supercooling) and modified austempering processes, respectively. The structures are austenite and ferrite phases with graphite nodules. The retained austenite is carbon-enriched, whereas ferrite is acicular in nature. The modified austempering treatment yields finer grains, which are attributed to the higher nucleation rate achieved when the supercooling temperature is 260 °C. In contrast, the structure yielded by conventional austempering at 420 °C is coarser because of the slow nucleation rate. This result conforms with those reported by Yang and Putatunda (J Yang & Putatunda, Citation2004).
Figure 2. SEM images of ADI with 0.64-wt% Mn produced by conventional austempering at austenization temperatures of 950 and 420 °C.
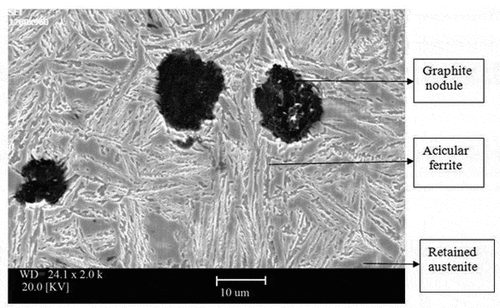
Figure 3. SEM images of ADI with 0.64-wt% Mn produced by modified austempering at austenization temperatures of 950 and 420 °C.
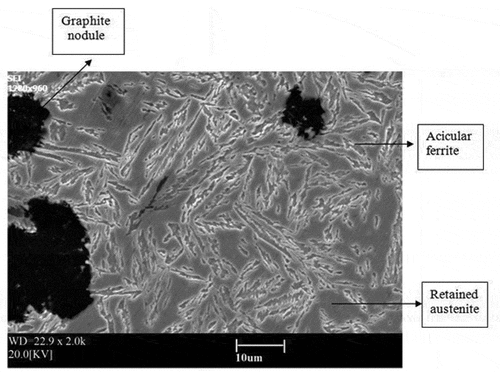
The effect of austempering temperature on hardness for both conventional and modified austempering processes is shown in . The hardness yielded by the modified austempering process compared with that resulting from conventional heat treatment is higher at all austempering temperatures (Hegde et al., Citation2019). This is attributed to the first-step quenching at 260 °C for 5 min. The extent of supercooling affects ferrite nucleation, and the critical nucleus size decreases with increasing supercooling. Because of the high degree of supercooling, the nucleation rate increases, resulting in numerous nuclei; consequently, finer grains are formed. Thus, the higher the degree of supercooling, the greater the number of nuclei and the finer the grain size. Because of the increased nucleation in the modified austempering process, finer ferrite is derived, thereby increasing the ADI hardness. However, when the austempering temperature was increased, the produced structure was coarser and feathery in nature, resulting in low hardness compared with that obtained at low temperatures. The variation in tensile strength with the austempering temperature is shown in . The ultimate tensile strength of the ADI yielded by the modified process was higher than that resulting from the conventional method. This is attributed to the finer ferrite formed by the modified process because of the supercooling and higher ferrite nucleation rate. Furthermore, the carbon content of the retained austenite may have also increased in the two-step austempering process because of the increase in the diffusion rate of carbon atoms. show the variations in ductility and impact energy with the austempering temperature, respectively. In the conventional and modified austempering processes, the ductility is found to increase with the austempering temperature. The greater ductility obtained at high austempering temperature results from the coarser and feathery ausferrite structure. However, the ductility obtained in both cases was observed to be virtually the same. The impact energy of ADI also increased with the austempering temperature, exhibiting the same trend as that of ductility. Manganese has no considerable effect on ADI hardness for the range of values considered in this study. However, because of the slight increase in the amount of retained austenite at high austempering temperature in both conventional and two-step austempering processes, a slight reduction in tensile strength was observed. The optimum properties obtained when higher manganese contents were used could possibly be due to the higher nodule count (Zhang et al., Citation2021).
The modified austempering process increased hardness and strength with better ductility in the samples alloyed with different amounts of manganese. This was not achieved by the conventional austempering process, which produced ADI with low hardness and high ductility at high austempering temperatures. Nevertheless, this inadequacy was overcome by the two-step austempering process, which resulted in higher ductility and optimum hardness. The manganese addition of up to 1 wt% did not produce any adverse effects on the mechanical properties of ADI.
5. Regression analysis
The derived results have been used to fit the regression equations that are useful for predicting the ADI properties. Based on the results obtained for impact energy and ultimate tensile strength, regression equations are generated using Minitiab software. The regression equations for impact energy and ultimate tensile strength are given by Eqs. (1) and (2), respectively:
Impact Energy (J) = −106.21 + 0.5 (a) + 2.25 (b),(1)
R2 = 99.5 %,
R2 (Adjusted) = 99.3 %;
Ultimate Tensile Strength (MPa) = 2931 − 4.807 (a)−28.3 (b),(2)
R2 = 98.2 %,
R2 (Adjusted) = 97.6 %,
where a and b are the austempering temperature (°C) and manganese content (wt%), respectively.
The optimum combination of hardness and ductility was obtained using the response surface methodology.
The optimized parameters are as follows:
austempering temperature = 370.5 °C;
manganese content = 0.59 wt%.
6. Conclusions
The following conclusions are drawn based on the results of the tests and analyses implemented in this study.
The increased temperature in the modified austempering process reduces the hardness and tensile strength of manganese-alloyed ADI.
The optimum combination of hardness and impact energy for the ADI is derived using the modified austempering process with supercooling at 260 °C and austempering at 420 °C.
The short-duration first-step quenching at 260 °C improves the nucleation rate, resulting in finer ferrite. This step is useful for obtaining the superior combination of tensile strength and impact energy as well as overcoming the inadequacy of conventional austempering.
The modified austempering process (at 420 °C with 0.6-wt% Mn) compared with the conventional process improves hardness and ultimate strength (by 30 % and 40 %, respectively) without compromising toughness.
Disclosure statement
No potential conflict of interest was reported by the author(s).
Additional information
Funding
Notes on contributors
Sathyashankara Sharma
Sathyashankara Sharma is working as Professor and Head in the Department of Mechanical & Manufacturing Engineering, MIT, MAHE, Manipal. He holds B.E. (Industrial and Production Engineering), M.Tech. (Materials Engineering) and Ph.D. (Materials Engineering) degrees. He has 33 years of teaching experience. His area of interest includes Engineering materials, Heat treatment of metals and composites, Machinability and Deformation behaviour of metals and composites. He has published more than 200 papers in journals and conferences.
References
- ASTM A327/A327M. (2011). “standard test methods for impact testing of cast irons”. ASTM International, West Conshohocken.
- ASTM A897/A897M −15, 2015, Standard Specification for Austempered Ductile Iron Castings Annual Book of ASTM Standards, Vol. 01. 02, ASTM International:
- ASTM E8/E8M. (2016). “standard test methods for tension testing of metallic materials”. ASTM International, West Conshohocken.
- Barbosa, P. A., Costa, É. S., Guesser, W. L., & Machado, Á. R. (2015). Comparative study of the machinability of austempered and pearlitic ductile irons in drilling process. J Braz. Soc. Mech. Sci. Eng, 37, 115–11. https://doi.org/10.1007/s40430-014-0161-z
- Cemal Cakir, M., & Isik, Y. (2008). Investigating the machinability of austempered ductile irons having different austempering temperatures and times. Mater. Des, 29(5), 937–939 doi:10.1016/j.matdes.2007.04.002.
- Gazda, A., Warmuzek, M., & Bitka, A. (2018). Optimization of mechanical properties of complex, two-stage heat treatment of Cu–Ni (Mn, Mo) austempered ductile iron. Journal of Thermal Analysis and Calorimetry, 132(2), 813–822. https://doi.org/10.1007/s10973-018-7004-6
- Hegde, A., Sharma, S., & Sadanand, R. (2019). Mechanical characterization and optimization of heat treatment parameters of manganese alloyed austempered ductile iron. Journal of Mechanical Engineering and Sciences, 13(1), 4356–4367. https://doi.org/10.15282/jmes.13.1.2019.01.0371
- Klocke, F., Arft, M., & Lung, D. (2010). Material-related aspects of the machinability of austempered ductile iron. Prod. Eng. Res. Devel, 4(5), 433–441. https://doi.org/10.1007/s11740-010-0227-4
- Lerner, Y. S., & Kingsbury, G. R. (1997). Wear resistance properties of austempered ductile iron. J. Mater. Eng. Perform, 7(1), 48–52. https://doi.org/10.1007/s11665-006-5003-4
- Narasimha Murthy, K., Sampathkumaran, P., & Seetharamu, S. (2009). Abrasion and erosion behaviour of manganese alloyed permanent moulded austempered ductile iron. Wear, 267(9–10), 1393–1398. https://doi.org/10.1016/j.wear.2008.12.033
- Olawale, J. O., & Oluwasegun, K. M. (2016). Austempered Ductile Iron (ADI): A Review. Materials Performance and Characterization, 5(1), 289–311. https://doi.org/10.1520/MPC20160053
- Parez, M. J., Cisneros, M. M., & Lopez, H. F. (2006). Wear resistance of Cu–Ni–Mo austempered ductile iron.wear. 260 (7–8) , 879–885 doi:10.1016/j.wear.2005.04.001.
- Pereiraa, L., Amaral, R. F., Wolfart Júnior, M., & Barcellos, V. K. (2020). Microstructural and mechanical properties of Cu-Ni-Mn-Mo austempered ductile iron obtained from two-step hot air austempering. J. Mater. Res. Technol, 9(3), 3055–3063. https://doi.org/10.1016/j.jmrt.2020.01.036
- Seker, U., & Hasirci, H. (2006). Evaluation of machinability of austempered ductile irons in terms of cutting forces and surface quality. J. Mater. Process. Technol, 173(3), 260–268. https://doi.org/10.1016/j.jmatprotec.2005.05.058
- Susil, K., & Putatunda. (2001). Development of austempered ductile cast iron (ADI) with simultaneous high yield strength and fracture toughness by a novel two-step austempering process. Materials Science and Engineering A, 315(1–2), 70–80. https://doi.org/10.1016/S0921-5093(01)01210-2
- Yang, J., & Putatunda, S. K. (2004). Improvement in strength and toughness of austempered ductile cast iron by a novel two-step austempering process. Materials & Design, 25(3), 219–230. https://doi.org/10.1016/j.matdes.2003.09.021
- Yang, J., & Putatunda, S. K. (2004). Influence of a novel two-step austempering process on the strain-hardening behavior of austempered ductile cast iron (ADI). Materials Science and Engineering A, 382(1–2), 265–279. https://doi.org/10.1016/j.msea.2004.04.076
- Yi, P., Guo, E.-J., Wang, L.-P., Feng, Y.-C., & Wang, C.-L. (2019). Microstructure and mechanical properties of twostep Cu-alloyed ADI treated by different second step austempering temperatures and times. Research & Development, 6, 342–351 doi:10.1007/s41230-019-9064-z.
- Zhang, Y., Guo, E., Wang, L., Zhao, S., Liu, X., Pengyue, Y., Yan, L., Feng, Y., & Song, M. (2021). Insights into effect of first-step austempering temperature on the microstructure and properties of austempered ductile iron. Materials Research Express, 8(8), 086512. https://doi.org/10.1088/2053-1591/ac1ca8