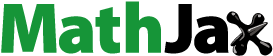
Abstract
In this study, we developed an optimization model for determining the optimal parameters for multi-pass CNC turning processes. The six elements of sustainable manufacturing were considered in this study to derive new insights into multi-pass turning modeling. This paper details the relationship between time and power and considers total noise in terms of the personal health element and cost of quality in terms of the manufacturing cost element. The objective functions for our model include the total energy, surface roughness, total noise, total cost, and total carbon emission. The decision variables for our model include the cutting depth, feed rate, cutting speed, and number of roughing passes. The proposed model was solved using the Gamultiobj algorithm (MATLAB). This algorithm was used to identify a set of non-dominated points on the Pareto front. Additionally, a single optimal solution is identified using the TOPSIS method. There are twelve combinations of multi-objective optimization processes carried out. One of twelve combinations, for the five objective functions, the optimal values were determined as follows: total energy value of 495,965.751 joules, surface roughness of 0.285 μm, average noise of 78.788 dBA, total cost of $288.587, and carbon emission of 337,748.265 kgCO2.
PUBLIC INTEREST STATEMENT
Sustainable manufacturing processes are urgently required in the current economy. One of the goals of implementing sustainable manufacturing processes is to reduce carbon emissions. Over the next 30 years, carbon emissions are expected to be reduced by 50%. Manufacturing industries can adopt modeling and optimization processes to reduce carbon emissions. Some concepts that can be used for model development include the six elements of sustainable manufacturing. These six elements were adopted in our mathematical models to identify optimal manufacturing process parameters. The developed model was optimized using multi-objective optimization. Based on all objective of our functions, which were optimized simultaneously by considering carbon emission, it is expected that the proposed optimal solution will satisfy all stakeholders.
1. Introduction
Sustainable manufacturing processes must be able to reduce negative environmental impacts, improve resource efficiency, reduce product defects, improve operational personnel health, and improve process quality in terms of overall lifecycle cost benefits (Eslami et al., Citation2019). Achieving a sustainable manufacturing process begins with the proper assessment of performance in terms of the sustainability of manufacturing. The triple bottom line (environmental, economic, and social aspects) and six elements for sustainable manufacturing (manufacturing cost, energy consumption, waste management, environmental impact, personnel health, and operator safety) should be considered by manufacturing companies engaging in various manufacturing processes (Jayal et al., Citation2010).
The 2015 Paris Agreement is a legal action designed to combat climate change with the goal that by 2050, carbon emissions, which represent an important issue in terms of environmental impact, will be minimized and approach zero (Banister, Citation2019). In the industrial sector, the goal is to reduce carbon emissions by 50% by 2050. As part of the industrial sector, the production of goods made from metal is dominated by carbon emissions during manufacturing processes (Allwood et al., Citation2010). Therefore, it is important for the manufacturing industry to adopt new strategies to reduce carbon emissions as part of implementing sustainable manufacturing. One strategy that can be applied to achieve low carbon emissions is the modeling and optimization of production processes. The optimization of production processes can be performed at the levels of production lines, work stations, and machines (Hu et al., Citation2019; Jiang et al., Citation2019; Lu et al., Citation2016; Tian et al., Citation2019). Optimization at the machine level is fundamental, meaning detailed problems can be modeled, optimized, and analyzed.
In modern manufacturing industries, production processes are implemented using various types of CNC machines. Specifically, CNC turning machines are widely used in many manufacturing processes (Ameur, Citation2021; Arif et al., Citation2014; Du et al., Citation2020; Lu et al., Citation2016). There are two types of CNC turning operations: single-pass and multi-pass turning processes. Multi-pass turning is more relevant to real-world operations than single-pass turning (Aungkulanon & Luangpaiboon, Citation2016; Rao & Kalyankar, Citation2013). CNC multi-pass turning processes have several advantages over conventional multi-pass turning in terms of speed, production rates, and accuracy. Regardless, the CNC multi-pass turning process has some disadvantages, such as requiring higher electrical energy, meaning it has a negative impact on the environment (Zhong et al., Citation2017).
The modeling and optimization of multi-objective CNC multi-pass turning in the context of sustainable manufacturing have been studied extensively (Bagaber & Yusoff, Citation2019; Du et al., Citation2020; Hu et al., Citation2019; Jiang et al., Citation2019; Khalilpourazari et al., Citation2020; Lu et al., Citation2016; Pangestu et al., Citation2021; Perdomo et al., Citation2020). Model development with objective functions that minimize the energy and precision values of machined products while considering decision variables such as cutting depth, feed rate, cutting speed, and number of roughing passes has also been studied (Khalilpourazari et al., Citation2020; Lu et al., Citation2016). Bagaber and Yusoff (Citation2019) developed a model with objective functions that minimize energy and machining costs by considering decision variables such as cutting depth, feed rate, and cutting speed. Hu et al. (Citation2019) developed a model with objective functions that minimize energy consumption and transportation energy consumption by considering decision variables such as cutting depth, feed rate, and cutting speed. Jiang et al. (Citation2019) developed a model with objective functions that minimize carbon emissions, surface roughness, and processing time by considering decision variables such as cutting depth, feed rate, and spindle rotation speed.
Du et al. (Citation2020) developed a model with objective functions that minimize energy consumption and surface roughness by considering decision variables such as cutting depth, feed rate, and cutting speed. Perdomo et al. (Citation2020) developed a model with objective functions that minimize manufacturing costs, carbon emissions, and operational safety by considering decision variables such as cutting depth, feed rate, cutting speed, and number of roughing passes. Pangestu et al. (Citation2021) developed a model with objective functions that minimize energy consumption, manufacturing cost, carbon emission, and processing time by considering decision variables such as cutting depth, feed rate, spindle rotation speed, and number of roughing passes. Related literature review and the position of this research are presented in .
Table 1. CNC multi-pass turning modeling research
This study focused on the six elements of sustainable manufacturing and their application to the CNC multi-pass turning machining process. These six elements are incorporated into various mathematical models to determine the optimal CNC multi-pass turning machining process parameters. Comparing to Pangestu et al. (Citation2021) this paper gives a more comprehensive sustainability consideration by adding in social aspects in terms of noise which can affect the personal health of the operator. Furthermore, this paper use cutting speed in decision variables and tool movement model that are different from Pangestu et al. (Citation2021). This paper presents some novel concepts to elucidate the relationship between time and power and considers total noise in terms of the personal health element and cost of quality in terms of the manufacturing cost element. The noise will be minimized in this research to reduce the effects on the operator health. We aimed to develop a multi-objective optimization model to determine the optimal parameters for the CNC turning multi-pass machining process, namely cutting depth, feed rate, cutting speed, and number of roughing passes. The objective functions for our model include the total energy, surface roughness, total noise, total cost, and total carbon emission.
2. Model development for machining parameters
The system diagram adopted in this study is presented in . This figure presents the triple bottom line and five of the elements of sustainable manufacturing used for model development. Regarding the environmental aspect, two elements are considered, namely carbon emission and energy consumption. Regarding the economic aspect, two different elements are considered, namely manufacturing cost and quality. Finally, personal health is added which considered as one element related to the social aspect. In the objective function, the personal health is measured by the society loss. We express the loss using Taguchi loss function which has been widely known as the measure of loss to society. The Taguchi loss function is also used to measure the loss due to surface roughness. Both personal health and surface roughness are included in smaller the better characteristics.
These five objective functions were solved simultaneously using the Gamultiobj algorithm (MATLAB). This algorithm finds Pareto front of multiple fitness functions using a Non-dominated Sorting Genetic Algorithm II (NSGA II). This algorithm is a fast and elitist multi-objective genetic algorithm. The algorithm uses Euclidean distance to select non-dominated solutions. Model’s structure, usefulness, optimization approach and metrics to select nondominated solutions are described in Deb et al. (Citation2002). The best solution is determined using Technique for Order of Preference by Similarity to Ideal Solution (TOPSIS) which widely used to determine the best solution from a set of Pareto optimal solutions such as in Pawanr et al. (Citation2019). TOPSIS is one of multi criteria decision making techniques which used to find a solution based on the smallest distance from the ideal positive solution and the farthest distance from the ideal negative solution (Hwang et al., Citation1993).
Our model development process is based on the relationship between the time required by the machining process and the power required to produce a unit product. This relationship is an essential consideration that will be used as a model development reference to ensure that the developed model is sufficiently close to a real system. Several previous models have considered the relationship between processing time and power per unit product (Shin et al., Citation2019; Tian et al., Citation2019; Yi et al., Citation2015; Zhang et al., Citation2017; Zhang et al., Citation2016). presents the relationship between the processing time and power per unit product derived in this study. This details the processing time and power, particularly the time and power required to change the tool between the roughing pass and finishing pass. Based on a mathematical model related to the objective functions per unit product and decision variables considered in this study was formulated. The notations used in this paper are listed in Appendix 1.
2.1. Total machining time

According to , the total machining time is defined as one cycle time from startup to the finishing pass per unit product. The total machining time consists of a constant time and variable time. The constant time consists of the startup time and standby time. The variable time consists of the spindle rotation change time, idle time, machining time, time for tool changing from roughing to finishing, and total tool changing time.
2.1.1. Spindle rotation change time

According to , the spindle rotation change time consists of the acceleration and deceleration times for both the roughing and finishing passes. The spindle rotation change time per unit product is defined in EquationEquation (1(1)
(1) ; Hu et al., Citation2019). EquationEquations (2)
(2)
(2) to (5) define the acceleration and deceleration times for the roughing and finishing processes.
2.1.2. Idle time

The idle time of the machining process can be divided into three stages based on the tool movement during the machining process, as shown in . The first stage of the idle time consists of tool movement along the 1 r path. The second stage of idle time consists of tool movement after completing the first roughing pass (paths 3 r-4 r-5 r). The first stage of idle time occurs once for each machining process per unit product, whereas the second stage of idle time occurs for roughing passes two to . Based on , this paper proposes additional time for the finishing tool return (path 3 f) as the third stage of idle time. This idle time is defined in EquationEquation (6)
(6)
(6) and the idle times of stages one, two, and three are defined in EquationEquations (7)
(7)
(7) , (Equation8
(8)
(8) ), and (Equation9
(9)
(9) ), respectively.
2.1.3. Machining time

The machining time is the specific time used by the tool to cut a workpiece. According to , the machining time of the first roughing pass is defined by path 2 r. The machining time for the finishing pass is presented in , as indicated by path 2 f. The machining time formulations used in this study are presented in ; (Arif et al., Citation2014; Bouzid, Citation2005; Chen & Tsai, Citation1996). The machining time equation for the multi-pass turning process consists of n roughing and finishing passes. Specifically, the machining time model for the roughing passes is defined in Equation (10) and the machining time for the finishing passes is defined in Equation (11). The machining time per unit product for n roughing and finishing passes is defined in Equation (12).
2.1.4. Time for tool changing from the roughing to the finishing pass

According to , there are three stages of tool changing from the roughing to the finishing pass. The first stage is the time required for tool movement after the nth roughing pass (B) to the tool home (Ot). The second stage is the fixed time required to change the roughing tool to the finishing tool with a value of . According to , the third stage is the time required for tool movement from Ot to C. The time required for tool changing from the roughing to the finishing pass per unit product is defined in EquationEquation (13)
(13)
(13) . EquationEquations (14)
(14)
(14) and (Equation15
(15)
(15) ) present the formulas for the first and third tool change times, respectively.
2.1.5. Time for tool replacement

During the machining process for p products, the tool must be sharpened or replaced. The tool replacement time per unit product is related to the tool life. The time of tool replacement per unit product is determined by multiplying the time for tool replacement per edge by the total number of edges per unit product. The time for tool replacement for the multi-pass turning process is defined in EquationEquation (16)(16)
(16) . Tool life (EquationEquation 17
(17)
(17) ) has two components, namely the tool life for roughing and that for finishing, as defined in EquationEquations (18)
(18)
(18) and (Equation19
(19)
(19) ), respectively.
Based on these time elements, the total time required for the machining process per unit product is defined in EquationEquation (20)(20)
(20) .
2.2. Total energy consumptions

Our model formulation for total energy consumption is based on . Based on the considered decision variables, energy consumption is divided into two categories. Energy consumption is not influenced by the decision variables for startup and standby energy consumption, but it is influenced by the other decision variables. The second category includes spindle rotation change, idle machine, machining, tool changing from the roughing to the finishing pass, tool replacement, and tool wear energy consumption. The startup energy consumption is the energy required during the startup time. According to , by assuming that the power increase is linear, the energy consumption is determined to be the product of half of the startup time and startup power. The start-up energy consumption is defined in EquationEquation (21)
(21)
(21) . The standby energy consumption
is the energy required during standby time, as shown in EquationEquation (22)
(22)
(22) .
The spindle rotation changes energy consumption is the energy required for acceleration and deceleration. It consists of four elements: the acceleration energy consumption of the roughing pass, deceleration energy consumption of the roughing pass, acceleration energy consumption of the finishing pass, and deceleration energy consumption of the finishing pass. The energy consumption for spindle rotation change is defined in EquationEquation (23)
(23)
(23) . The elements of this energy consumption are defined in EquationEquations (24)
(24)
(24) to (27). The idle machine energy consumption
can be determined by multiplying the idle power by the idle time, as shown in EquationEquation (28)
(28)
(28) .
The machining energy consumption is the energy required during workpiece cutting. The machining energy consumption
is determined by multiplying the machining power (Pm) by the machining time (tm). As shown in , Ptool is the power required to remove material. If the material removal rate (MRR) is assumed to be constant, then Ptool is also constant (Du et al., Citation2020; Pawanr et al., Citation2021). Ptool has a functional relationship with MRR in terms of the specific energy used for cutting operations (k; Du et al., Citation2020; Nur et al., Citation2015). As shown in , Ptool is one component of Pm. The machining energy consumption consists of the energy consumption of the roughing and finishing passes. EquationEquation (29)
(29)
(29) defines the machining energy consumption, and EquationEquations (30)
(30)
(30) and (Equation31
(31)
(31) ) represent the machining energy consumption of the roughing and finishing passes, respectively.
The energy consumption for tool changing from the roughing to the finishing pass is determined by multiplying the power and time required for changing the roughing tool to the finishing tool, as shown in EquationEquation (32)
(32)
(32) . Tool replacement energy consumption occurs when the tool module is active and the power is in the standby condition (Arif et al., Citation2014). The tool replacement energy consumption
is then calculated as the product of the standby power, total number of cutting edges per unit product, and tool replacement time per edge, as shown in EquationEquation (33
(33)
(33) ; Lu et al., Citation2016). The tool wear energy consumption
is defined as the tool energy footprint per edge per piece, which represents the energy contained in the tool, energy consumed for tool manufacturing, and energy consumed for tool coating (Arif et al., Citation2014). EquationEquation (34)
(34)
(34) defines the tool-wear energy consumption (Lu et al., Citation2016).
Based on these energy consumption elements, the total energy consumption for the machining process per unit product is defined in EquationEquation (35)(35)
(35) .
2.3. Surface roughness

The product quality following the turning process must meet standard specifications. One of the product qualities considered in the turning process is surface roughness, which is an important quality characteristic (Phadke, Citation1989). There are two methods for considering surface roughness in the turning process model: the objective function and the constraint function (Jiang et al., Citation2019; Lu et al., Citation2016; Schultheiss et al., Citation2017). In a previous study, the surface roughness function was expressed as a regression function that was obtained experimentally (Jiang et al., Citation2019). However, we adopt the function in EquationEquation (36)(36)
(36) to represent surface roughness, which was taken from Stahl et al. (Ståhl et al., Citation2011).
2.4. Total noise

The total noise generated by the turning process affects worker health. In a previous study, the total noise was not included in the turning process model. The total noise objective function used in this study adopts a quadratic function formula taken from Cirtu et al. (Citation1976) and Olaru et al. (Citation2017). In these two studies, a total noise objective function for the multi-pass turning process was not formulated. In this study, total noise has two components, namely noise originating from the roughing and finishing passes. The formulas for the total noise objective function and the components are presented in EquationEquations (37)(37)
(37) to (39).
2.5. Total cost

The total cost consists of machining, tool replacement, tool wear, and idle machine costs (Liu et al., Citation2016). Other studies have considered total energy costs (Bagaber & Yusoff, Citation2019; Pangestu et al., Citation2021; Tian et al., Citation2019). However, previous studies did not include the cost of quality loss. We adopted Taguchi’s quality loss function to calculate the cost of quality loss caused by surface roughness and total noise. The machining cost is formulated based on direct and overhead labor costs, which are multiplied by the total machining time. The machining cost formula is defined in EquationEquation (40)
(40)
(40) . The idle machine cost
is the product of the direct and overhead labor costs multiplied by the idle machine time. The idle machine cost formula is defined in EquationEquation (41)
(41)
(41) . The tool replacement cost
is the product of the direct and overhead labor costs and the tool replacement time. The tool replacement cost is defined in EquationEquation (42)
(42)
(42) . The tool wear cost
is the product of the tool cost and the number of cutting edges per unit product, as defined in EquationEquation (43)
(43)
(43) . The total energy cost
is dependent on the cost of the electricity used during the multi-pass turning process per unit product. The total energy cost is the product of the electricity cost coefficient and total energy, as shown in EquationEquation (44)
(44)
(44) .
In this research, the quality cost is represented by loss to society in term of personal health and economic loss in term of surface roughness. Those losses are converted into monetary values using Taguchi loss function in which both the total noise and surface roughness are smaller are better characteristics. The quality cost of surface roughness is the product of the quality cost constant related to surface roughness and the square of the surface roughness, as shown in EquationEquation (45)
(45)
(45) . The quality cost of the total noise is the product of the quality cost constant related to the total noise and the square of the total noise, as shown in EquationEquation (46)
(46)
(46) . The quality cost is the sum of the quality cost of the surface roughness and the quality cost of the total noise, as shown in EquationEquation (47)
(47)
(47) .
Based on these cost elements, the total cost for the multi-pass turning process per unit product is formulated in EquationEquation (48)(48)
(48) .
2.6. Total carbon emissions

The total carbon emission model is based on a previous study that did not consider the multi-pass turning process (Li et al., Citation2013; Liu et al., Citation2016). The total carbon emission consists of the carbon emissions related to electrical energy consumption, cutting tools, raw material consumption, and chip disposal. The carbon emission of electrical energy consumption is expressed in EquationEquation (49)
(49)
(49) as the product of a constant related to the carbon emissions caused by electrical energy consumption and the total energy. The carbon emission of the cutting tool
stems from the production of the cutting tool, as indicated in EquationEquation (50)
(50)
(50) . The carbon emission of the raw materials
is expressed as a function of the mass of the material removed during the roughing and finishing passes, as shown in EquationEquations (51)
(51)
(51) to (54). EquationEquation (55)
(55)
(55) represents the carbon emission from chip disposal. Based on these carbon emissions elements, the total carbon emissions formula for the multi-pass turning process per unit product is defined in EquationEquation (56)
(56)
(56) .
2.7. Objective and constraint functions
Based on the model development for machining parameters discussed in Subsections 2.2 to 2.6, the objective functions for the proposed model are the total energy (f1; EquationEquation (35)(35)
(35) ), surface roughness (f2; EquationEquation (36)
(36)
(36) ), total noise (f3; EquationEquation (37)
(37)
(37) ), total costs (f4; EquationEquation (48)
(48)
(48) ), and total carbon emission (f5; Equation (56)). The optimal machining parameters must be appropriate for the constraint functions. The constraint functions used in this study are the depth of the cut, cutting speed, feed rate, tool life, cutting force, power, stable cutting region, and chip-tool interface temperature. The constraints related to the solution space are the cutting speed, feed rate, and depth of cut in the form of lower and upper bounds. The tool life constraint is required to achieve optimal manufacturing cost and product quality. The cutting force constraint is required to avoid the uncontrollable deflection of tools and workpieces. The cutting power constraint is required to achieve optimal energy consumption. The stable cutting region constraint is required to prevent vibration and adhesion. The chip-tool interface temperature must be limited to improve tool life. The higher the temperature, the shorter the tool life. The depth of cut and feed rate in the roughing pass are typically greater than those in the finishing pass. Each of these constraints is applied in both the roughing and finishing passes of the turning process. These parameter relationship constraints are suitable for our model. The constraint functions adopted in this study refer to those in previous studies (Arif et al., Citation2014; Lu et al., Citation2016), as shown in EquationEquations (57)
(57)
(57) to (77).
2.8. The roughing pass constraints
The cutting speed
The feed rate
The depth of cut
The tool life
The cutting force
The cutting power
The stable cutting region
The chip-tool interface temperature
2.9. The finishing pass constraints
The cutting speed
The feed rate
The depth of cut
The tool life
The cutting force
The cutting power
The stable cutting region
The chip-tool interface temperature
2.10. The parameter relationships
The cutting speed
The feed rate
The depth of cut
The total deep of cut
The number roughing passes
3. Numerical examples and analysis
The parameter values used for the numerical example in this study were taken from previous studies (Cirtu et al., Citation1976; Hu et al., Citation2019; Lu et al., Citation2016; Olaru et al., Citation2017; Tian et al., Citation2019). The workpiece used in the numerical example is made of carbon steel C45. The diameter of the workpiece is 80 mm and the length
is 200 mm. The total cutting depth
of the workpiece is 10 mm. The cutting tool specifications are listed in and the constants related to the tool are listed in . list the parameters related to the machining time, total energy, surface roughness, total noise, total cost, total carbon emission, and constraint functions. All of these parameters were substituted into the equations representing the objective functions and constraints of the model. We assumed in this numerical example that the operator wears the protective personal equipment to reduce the effects of noise and prevent the occurrence of accidents. Additional environmental conditions like temperature, humidity, and vibration will be considered in a future study.
Table 2. Tool specifications (modified from Lu et al., Citation2016)
Table 3. Constants related to the tool (modified from Lu et al., Citation2016)
Table 4. Parameter values related to the machining process (modified from Lu et al., Citation2016)
Table 5. Parameter values related to energy consumption
Table 6. Parameter values related to noise (modified from Cirtu et al., Citation1976; Olaru et al., Citation2017)
Table 7. Parameter values related to total cost (Tian et al., Citation2019)
Table 8. Parameter values related to carbon emission (Tian et al., Citation2019)
There were two stages to find the single optimal solution to minimize subject to EquationEquations (57)
(57)
(57) to (77). The first stage was to find the Pareto frontiers set for all five objective functions. In the second stage is to find the Pareto point to get the single optimal solution. Finding the Pareto point to get the single optimal solution is difficult (Costa & Lourenço, Citation2017). Some of the methods applied are hypervolume under the Pareto front (Lu and Anderson-Cook, Citation2013). In this study, the single optimal solution will be found using TOPSIS method. The TOPSIS method for selecting a single optimal solution from a set of Pareto points was also carried out by Chen et al. (Citation2022) and Faghiri et al. (Citation2022).
The first stage that to find the Pareto frontiers set, the proposed model was solved using the Gamultiobj function in MATLAB 2020a (MATLAB, Citation2020). The gamultiobj algorithm is also used for multi objective optimization including Sellami et al. (Citation2020) and Kallio and Siroux (Citation2021). Four setting parameter values were used to run the Gamultiobj algorithm to find the Pareto frontiers. The four parameter settings are run for number of roughing passes (n) equal to 3,4 and 5. The first setting parameter value for the number of roughing passes (n) = 3 because of the total cutting depth of the workpiece is 10 mm. Meanwhile, the upper bound of the depth of cut in roughing passes and finishing pass is 3 mm. The finishing pass is determined once, so it takes a minimum of 3 roughing passes before the finishing pass. shows parameter values related to constraint functions and shows setting parameter values in Gamultiobj algorithm.
Table 9. Parameter values related to constraint functions (Lu et al., Citation2016)
Table 10. Setting parameter values in gamultiobj algorithm
In this paper, the calculation and the results of the Pareto frontier are only for the first setting parameter value and for the number of roughing passes (n) = 3. There were 200 points of Pareto front corresponding to non-dominated solutions for the first setting and n = 3. Ideally, with five objective functions, the Pareto front graph should be shown in five dimensions (5D). Since it is impossible to draw the Pareto graph in 5D, we show the Pareto graph in two dimensions (2D) and three dimensions (3D) for all possible combinations. The number of combinations for both 2D and 3D Pareto fronts graph are 10. Four Pareto front graph () are shown consecutively in the next section, while the rest of combination are provided in Appendix 2. presents 2D of the Pareto front graph and the tradeoff between the total energy (f1) and total noise (f3). presents 2D of the Pareto front graph and the tradeoff between the surface roughness (f2) and total cost (f4). presents 3D of the Pareto front and the tradeoff between the total energy (f1), surface roughness (f2), and total noise (f3). presents 3D of the Pareto front graph and the tradeoff between surface roughness (f2), total noise (f3), and total cost (f4).
After identifying the non-dominated solutions (Pareto front) using the Gamultiobj algorithm, the next stage is to determine a single best solution using the TOPSIS method. There were 200 points corresponding to non-dominated solutions (Pareto front), among which the best solution was identified using TOPSIS. There are seven steps in the TOPSIS method to determine a single optimal solution. show the process of finding a single optimal solution using TOPSIS for the first setting parameter value and the number of roughing passes (n) equals 3.
Create an evaluation matrix,
, consisting of A alternatives and F criteria. In this case, A are 200 points corresponding to non-dominated solutions and F are objective functions.
Normalize evaluation matrix using this formula
(3) Calculate the weighted normalized decision matrix,
.
Table 11. Matrix A alternatives and F criteria
Table 12. Normalize matrix A alternatives and F criteria
Table 13. Weighted normalize matrix
Table 14. Maximum and minimum alternative
Table 15. Euclidean distance between the target
Table 16. TOPSIS scores
Table 17. Minimum objective function values for setting #1 and n = 3
Table 18. Decision variables values for setting #1 and n = 3
Where ,
, where weight for f1 = 0.20, f2 = 0.10, f3 = 0.10, f4 = 0.20 and f5 = 0.40
(4) Determine the maximum
and the minimum
alternative for each criterion:
(5) Calculate the Euclidean distance between the target alternative and the maximum
and minimum
alternative:
,
(6) For each alternative calculate the similarity to the minimum alternative using
. The results are TOPSIS scores.
(7) Find the maximum TOPSIS score. The maximum TOPSIS score is 0.7270 in A31.The maximum score TOPSIS score is correspondence with the optimal single solution.
Another combination of setting parameter values and the number of roughing passes (n) run in the similar method and stage. The first stage is to find the Pareto front and the second stage is to find a single optimal solution with TOPSIS. shows the minimum objective function values of twelve runs for all combinations of four setting parameter values and number of roughing passes (n) equal to 3,4, and 5. Decision variables and minimum objective function values for all combinations are shown in Appendix 3.
Table 19. Minimum objective function values
It is more difficult to determine the effect of setting parameters and number of roughing passes (n) on the optimal solution. Based on and , if analyzed based on parameter settings, the first parameter setting gives optimal results for the objective functions f1,f4, and f5. Suppose analyzed based on the number of roughing passes, the number of roughing passes (n) equals 4 providing optimal results for the objective functions f1,f3,f4, and f5. Generally, the minimum values of the five objective functions are associated with the first parameter setting, and the number of roughing passes (n) equals 4. The interesting results are emerged in the objective function, mainly the f3 (noise). From the total noise with roughing pass (n) = 4, the average noise for the roughing and finishing passes is 78.788 dBA. This noise value is below the maximum noise limit of 85 dBA based on the Indonesia National Standard (SNI 16-7063-2004), for an operator works without using ear protection.
Finally, the single optimal solution for the five objective functions (total energy value, surface roughness, total noise, total cost, and carbon emission) was associated with the first parameter setting, and the number of roughing passes (n) equals 4. It is defined as follows: the total energy value is 495,965.751 Joule, surface roughness is 0.285 μm, total noise is 393.938 dBA, total cost is $ 288.587, and carbon emission is 337,748.265 . The values of the decision variables were suitable with
,
,
,
,
,
,
,
,
,
,
,
,
,
This result is the single optimal solution. It is good to be recommended according to the numerical example in this model.
If this solution is to be implemented in a real manufacturing process, it will need to be additional coded on the CNC machine. This will make the CNC machine smarter, because it can change machining parameters from one roughing pass to another. The values of the decision variables for the feed rate and depth of cut
for the roughing pass tend to be close to the upper bond. The value of the feed rate is close to nine and the value of the depth of cut is close to three. This condition minimizes the processing time. In contrast, the values of the decision variables for the feed rate
and depth of cut
for the finishing pass tend to be close to the lower bound. The values of the feed rate and depth of cut are both close to one to keep the value of the surface roughness smaller than
.
4. Conclusions and future research
In this study, a multi-objective optimization model was developed by considering five objective functions that represent environmental, economic, and social factors. This paper proposed novel ideas for examining machining process time and machining power in detail. Additionally, the objective functions adopted in this study consider the total noise and cost of quality. Based on optimization performed using the Gamultiobj algorithm and TOPSIS method, a single optimal solution was identified for the first parameter setting value and four roughing passes (n) equals 4. The limitations of this paper are the firstly, the formulas for the total noise objective function are derived from regression equations with different CNC turning machines, and secondly, the parameters used in the numerical example are taken from some papers. So, for future research it should be considered such as a case study on one machine system, because the results will be different for other CNC turning machines. However, this proposed model can be a reference to be applied to different CNC turning machines.
Acknowledgements
This work was supported by the MR-UNS PNBP under Grant 452/UN27.21/PN/2020.
Disclosure statement
No potential conflict of interest was reported by the author(s).
Additional information
Funding
Notes on contributors
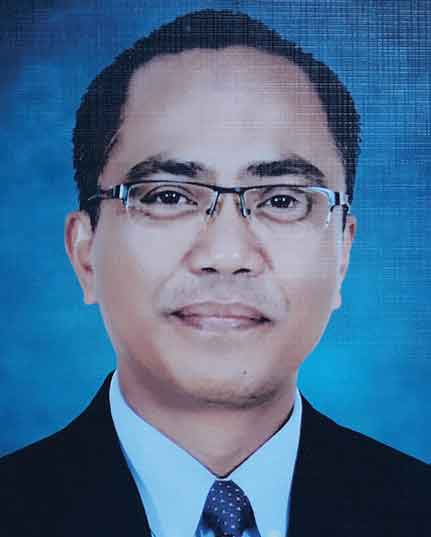
Eko Pujiyanto
Eko Pujiyanto received the B.S. degree in Mathematics in 1993 and the M.Eng. degree in Industrial Engineering in 1998, both from Bandung Institute of Technology, Bandung and Ph.D. degree in Mechanical Engineering in 2012 from Gadjah Mada University, Yogyakarta, Indonesia. He is currently a member of The Center for Research in Manufacturing System at Sebelas Maret University. His main research is the modeling and experimentation of manufacturing processes. His research interests include modeling and optimization of sustainable manufacturing process using statistical and computational, and data analysis and optimization using heuristics. In addition to research in the field of sustainable manufacturing modeling, he is also experimental-based research related to biomaterials using the Taguchi Method. The results of the multi-response experiment using the Taguchi method were optimized simultaneously with the multi-objective optimization tool. He has authored/coauthored several papers on these subjects.
References
- Allwood, J. M., Cullen, J. M., & Milford, R. L. (2010). Options for achieving a 50% cut in industrial carbon emissions by 2050. Environmental Science & Technology, 44(6), 1888–27. https://doi.org/10.1021/es902909k
- Ameur, T. (2021). Multi-objective particle swarm algorithm for the posterior selection of machining parameters in multi-pass turning. Journal of King Saud University - Engineering Sciences, 33(4), 259–265. https://doi.org/10.1016/j.jksues.2020.05.001
- Arif, M., Stroud, I. A., & Akten, O. (2014). A model to determine the optimal parameters for sustainable-energy machining in a multi-pass turning operation. Proceedings of the Institution of Mechanical Engineers, Part B: Journal of Engineering Manufacture, 228(6), 866–877. https://doi.org/10.1177/0954405413508945
- Aungkulanon, P., & Luangpaiboon, P. (2016). Vertical transportation systems embedded on shuffled frog leaping algorithm for manufacturing optimisation problems in industries. SpringerPlus, 5(1), 1–25. https://doi.org/10.1186/s40064-016-2449-1
- Bagaber, S. A., & Yusoff, A. R. (2019). Energy and cost integration for multi-objective optimisation in a sustainable turning process. Measurement: Journal of the International Measurement Confederation, 136, 795–810. https://doi.org/10.1016/j.measurement.2018.12.096
- Banister, D. (2019). The climate crisis and transport. Transport Reviews, 39(5), 565–568. https://doi.org/10.1080/01441647.2019.1637113
- Bouzid, W. (2005). Cutting parameter optimization to minimize production time in high speed turning. Journal of Materials Processing Technology, 161(3), 388–395. https://doi.org/10.1016/j.jmatprotec.2004.07.062
- Chen, L. G., Li, P. L., Xia, S. J., Kong, R., & Ge, Y. L. (2022). Multi-objective optimization for membrane reactor for steam methane reforming heated by molten salt. Science China Technological Sciences, 65(6), 1396–1414. https://doi.org/10.1007/s11431-021-2003-0
- Chen, M. C., & Tsai, D. M. (1996). A simulated annealing approach for optimization of multi-pass turning operations. International Journal of Production Research, 34(10), 2803–2825. https://doi.org/10.1080/00207549608905060
- Cirtu, N. D., Dimitriu, R., Hartley, D., & Golder, A. A (1976). Survey of the noise levels of metal-cutting machine tools. Proceedings of the sixteenth international machine tool design and research Conference, 363–369. https://doi.org/10.1007/978-1-349-81544-9_50
- Costa, N., & Lourenço, J. (2017). Reproducibility of nondominated solutions. Chemometrics and Intelligent Laboratory Systems, 168, 1–9. https://doi.org/10.1016/j.chemolab.2017.07.002
- Deb, K., Pratap, A., Agarwal, S., & Meyarivan, T. (2002). A fast and elitist multi-objective genetic algorithm: NSGA-II. IEEE Transactions on Evolutionary Computation, 6(2), 182–197. https://doi.org/10.1109/4235.996017
- Du, F., He, L., Huang, H., Zhou, T., & Wu, J. (2020). Analysis and multi-objective optimization for reducing energy consumption and improving surface quality during dry machining of 304 stainless steel. Materials, 13(21), 1–26. https://doi.org/10.3390/ma13214693
- Eslami, Y., Dassisti, M., Lezoche, M., & Panetto, H. (2019). A survey on sustainability in manufacturing organisations: Dimensions and future insights. International Journal of Production Research, 57(15–16), 5194–5214. https://doi.org/10.1080/00207543.2018.1544723
- Faghiri, S., Aria, H. P., & Shafii, M. (2022). Multi-objective optimization of acetone droplet impingement on phase change material in direct-contact discharge method. Journal of Energy Storage, 46, 103862. https://doi.org/10.1016/j.est.2021.103862
- Hu, L., Liu, W., Xu, K., Peng, T., Yang, H., & Tang, R. (2019). Turning part design for joint optimisation of machining and transportation energy consumption. Journal of Cleaner Production, 232, 67–78. https://doi.org/10.1016/j.jclepro.2019.05.297
- Hwang, C.-L., Lai, Y.-J., & Liu, T.-Y. (1993). A new approach for multiple objective decision making. Computers & Operations Research, 20(8), 889–899. https://doi.org/10.1016/0305-05489390109-V
- Jayal, A. D., Badurdeen, F., Dillon, O. W.,sJr., & Jawahir, I. S. (2010). Sustainable manufacturing: modeling and optimization challenges at the product, process and system levels. CIRP Journal of Manufacturing Science and Technology, 2(3), 144–152. https://doi.org/10.1016/j.cirpj.2010.03.006
- Jiang, Z., Gao, D., Lu, Y., & Liu, X. (2019). Optimization of cutting parameters for trade-off among carbon emissions, surface roughness, and processing time. Chinese Journal of Mechanical Engineering, 32(1), 1–18. (English Edition). https://doi.org/10.1186/s10033-019-0408-9
- Kallio, S., & Siroux, M. (2021). Exergy optimization of a multi-stage solar micro-cogeneration system. IET Renewable Power Generation, 1–12. https://doi.org/10.1049/rpg2.12372
- Khalilpourazari, S., Khalilpourazary, S., Çiftçioğlu, A. Ö., & Weber, G. (2020). Designing energy-efficient high-precision multi-pass turning processes via robust optimization and artificial intelligence. Journal of Intelligent Manufacturing, 321, 1621–1647. https://doi.org/10.1007/s10845-020-01648-0
- Li, C., Tang, Y., Cui, L., & Yi, Q. (2013). Quantitative analysis of carbon emissions of CNC-based machining systems. 10th IEEE international conference on networking, sensing and control, 869–874. https://doi.org/10.1109/ICNSC.2013.6548852
- Liu, Z. J., Sun, D. P., Lin, C. X., Zhao, X. H., & Yang, Y. (2016). Multi-objective optimization of the operating conditions in a cutting process based on low carbon emission costs. Journal of Cleaner Production, 124, 266–275. https://doi.org/10.1016/j.jclepro.2016.02.087
- Lu, L., & Anderson-Cook, C. M. (2013). Adapting the Hypervolume Quality Indicator to Quantify Trade-offs and Search Efficiency for Multiple Criteria Decision Making Using Pareto Fronts. Qual. Reliab. Engng. Int, 29, 1117–1133. https://doi.org/10.1002/qre.1464
- Lu, C., Gao, L., Li, X., & Chen, P. (2016). Energy-efficient multi-pass turning operation using multi-objective backtracking search algorithm. Journal of Cleaner Production, 137, 1516–1531. https://doi.org/10.1016/j.jclepro.2016.07.029
- MATLAB. (2020). Version 9.8 (R2020a). Natick, Massachusetts: The MathWorks Inc.
- Nur, R., Kurniawan, D., Noordin, M. Y., & Izman, S. (2015). Optimizing power consumption for sustainable dry turning of treated aluminum alloy. Procedia Manufacturing, 2, 558–562. https://doi.org/10.1016/j.promfg.2015.07.096
- Olaru, S. C., Slǎtineanu, L., Silitrǎ, M., Mihalache, A. N., & Coteatǎ, M (2017). Investigation of the sound intensity level in the case of a universal lathe. MATEC Web of Conferences, 112, 1–6, https://doi.org/10.1051/matecconf/201711201025
- Pangestu, P., Pujiyanto, E., & Rosyidi, C. N. (2021). Multi-objective cutting parameter optimization model of multi-pass turning in CNC machines for sustainable manufacturing. Heliyon, 7(2), e06043. https://doi.org/10.1016/j.heliyon.2021.e06043
- Pawanr, S., Garg, G. K., & Routroy, S. (2019). multi-objective optimization of machining parameters to minimize surface roughness and power consumption using TOPSIS. 7th CIRP Global Web Conference, Procedia CIRP 86, 116–120. https://doi.org/10.1016/j.procir.2020.01.03
- Pawanr, S., Garg, G. K., & Routroy, S. (2021). Modelling of variable energy consumption for CNC machine tools. Paper Presented at the Procedia CIRP, 98, 247–251. https://doi.org/10.1016/j.procir.2021.01.038
- Perdomo, I. L. F., Quiza, R., Haeseldonckx, D., & Rivas, M. (2020). Sustainability-focused multi-objective optimization of a turning process. International Journal of Precision Engineering and Manufacturing - Green Technology, 7(5), 1009–1018. https://doi.org/10.1007/s40684-019-00122-4
- Phadke, M. S. (1989). Quality engineering using robust design (pp. 40–50). Prentice Hall.
- Rao, R. V., & Kalyankar, V. D. (2013). Multi-pass turning process parameter optimization using teaching-learning-based optimization algorithm. Scientia Iranica, 20(3), 967–974. https://doi.org/10.1016/j.scient.2013.01.002
- Schultheiss, F., Johansson, D., Bushlya, V., Zhou, J., Nilsson, K., & Ståhl, J. (2017). Comparative study on the machinability of lead-free brass. Journal of Cleaner Production, 149, 366–377. https://doi.org/10.1016/j.jclepro.2017.02.098
- Sellami, A., Ali, M. B., & Kairouani, L. (2020). Pareto-optimization of msf-ot/tvc desalination plant using surface response methodology and genetic algorithm. Desalination and Water Treatment, 204, 10–21. https://doi.org/10.5004/dwt.2020.26229
- Shin, S. M., Kim, Y. M., & Meilanitasari, P. (2019). A holonic-based self-learning mechanism for energy-predictive planning in machining processes. Processes, 7(10), 739. https://doi.org/10.3390/pr7100739
- Ståhl, J. E., Schultheiss, F., & Hägglund, S. (2011). Analytical and experimental determination of the ra surface roughness during turning. Procedia Engineering, 19, 349–356. https://doi.org/10.1016/j.proeng.2011.11.124
- Tian, C., Zhou, G., Zhang, J, & Zhang, C. (2019). Optimization of cutting parameters considering tool wear conditions in low-carbon manufacturing environment. Journal of Cleaner Production, 226, 706–719. https://doi.org/10.1016/j.jclepro.2019.04.113
- Yi, Q., Li, C., Tang, Y, & Chen, X. (2015). Multi-objective parameter optimization of CNC machining for low carbon manufacturing. Journal of Cleaner Production, 95, 256–264. https://doi.org/10.1016/j.jclepro.2015.02.076
- Zhang, H., Deng, Z., Fu, Y, Lv, L., & Yan, C. (2017). A process parameters optimization method of multi-pass dry milling for high efficiency, low energy and low carbon emissions. Journal of Cleaner Production, 148, 174–184. https://doi.org/10.1016/j.jclepro.2017.01.077
- Zhang, Z., Tang, R., Peng, T., Tao, L., & Jia, S. (2016). A method for minimizing the energy consumption of machining system: integration of process planning and scheduling. Journal of Cleaner Production, 137, 1647–1662. https://doi.org/10.1016/j.jclepro.2016.03.101
- Zhong, Q., Tang, R., & Peng, T. (2017). Decision rules for energy consumption minimization during material removal process in turning. Journal of Cleaner Production, 140, 1819–1827. https://doi.org/10.1016/j.jclepro.2016.07.084