Abstract
Metal Matrix Composites (MMCs) and Hybrid Metal Matrix Composites (HMMCs) are advanced materials that possess distinctive mechanical properties, rendering them well-suited for a wide range of industrial applications. Nevertheless, the mechanical properties of MMCs and HMMCs can be further improved by optimizing their compositions and production routes. MMCs and HMMCs possess distinct mechanical characteristics, however their processing and production present various obstacles. However, the current processing and manufacturing methods for MMCs and HMMCs have limitations such as high production costs, limited design flexibility, and reduced mechanical properties. Therefore, the problem that needs to be addressed is the development of efficient and cost-effective processing and manufacturing methods that can improve the mechanical properties of MMCs and HMMCs while maintaining their unique properties. Therefore, this study conducted an experimental study on the mechanical and tribological features of HMMCs, where graphite powder and Boron Carbide were used as reinforcements, and AA7075 was used as the matrix. Induction stir casting was used to prepare the composite samples with different wt. % of reinforcements. Here, the Yield Strength (YS), Ultimate Tensile Strength (UTS), elongation, hardness, impact, and wear rate are used as output response characteristics. From the obtained results, YS, UTS, and elongation were enhanced by +85.31%, +88.24%, and -63.75%, respectively, while the hardness and impact strength was improved by approximately 18% and 110%, respectively, with the reinforcement of Gr/B4C as compared to unreinforced AA7075. Finally, the findings of this study could potentially aid in advancement of novel and enhanced hybrid composites for diverse applications.
1. Introduction
When two or more materials with different properties are mixed, a composite material is obtained. Therefore, the new material has the properties of both materials, which makes it act in its own way. At the microscopic level, different parts of a composite can be distinguished (Güler & Bağcı, Citation2020; Imran & Khan, Citation2019). Composites are typically made of materials with more than one phase. These materials are usually split into two classes, including the matrix (Samal et al., Citation2020) and dispersion phases (Hu & Cong, Citation2018), where the first phase completely encircles the other phase, known as the dispersed phase, which remains stable, while in the latter phase, there is a distinct form (i.e. second phase). Which is called as scattered phase. Usually, in some cases, the dispersion phase or second phase is also called the reinforcement phase because this phase is sturdier than the matrix phase. This phase is known as the ‘scattered phase.’ Some researchers say that the dispersed phase is the reinforcing phase because it is often stronger than the matrix. While certain materials, such as metal alloys, doped ceramics, and polymers with additives, may contain a limited number of dispersed phases, they do not qualify as composites because of their similar physical properties to those of the main ingredients (for instance, steel possesses physical properties similar to pure iron). The efficiency of stress transmission across phase interfaces plays a crucial role in determining the behavior and performance of composite materials. This aspect significantly impacts the overall functionality and effectiveness of these materials.
Notable progress has been observed in various industrial sectors and applications (Zhang & Chromik, Citation2022) within the composite market, and this growth can be attributed to the increasing demand for materials (i.e. possessing some specific features), that are environmentally friendly and more cost-effective. The global increase in carbon dioxide emissions from automobiles has necessitated revision of regulations pertaining to vehicle emissions. To conform to the requirements of the market and satisfy the stringent emission standards imposed on them, manufacturers have been steadily reducing their overall weight and improving their fuel economy. Consequently, there has been substantial interest in the use of metal matrix composites (MMCs) in automotive applications. MMCs are used in the aerospace and spacecraft industries in the construction of a select number of aircraft, helicopters, and spacecraft designs, where lightweight structural materials are required. Hard reinforcing particles are combined with a metal matrix phase to form MMC, which are then used in various applications. Most MMCs have a low-density metal alloy that serves as the base material. Based on forecasts made by industry professionals, the automotive composite business in the United States is anticipated to produce approximately one billion dollars in sales by the year 2025. According to information gathered worldwide in 2018, the market for automotive composites earned $15.7 billion. Owing to their capacity to provide superior toughness and strength while simultaneously lowering an aircraft’s total weight, composites are gaining an increasing amount of traction in the aerospace sector. Although demand for MMC is rising due to the participation of other sectors as well, the energy sector is now the biggest consumer of MMC and is forecast to soon overtake the aerospace sector.
The development of hybrid metal matrix composites (HMMCs) began in the early 1990s and research in this area has grown rapidly in recent years. HMMCs are currently being considered for a wide range of applications, including automotive, aerospace, energy, and medical applications. HMMCs are a type of composite material fabricated by combining two or more different types of reinforcements in a metal matrix. Reinforcement can be in the form of nanoparticles, short fibers, or whiskers. The combination of different types of reinforcements can provide a synergistic effect, resulting in improved properties compared to those of composites with a single type of reinforcement. HMMCs have a wide range of potential applications, including aerospace, automotive, energy and medical applications. In contrast, HMMCs offer several advantages over traditional MMCs, including improved strength and stiffness, increased toughness and wear resistance, reduced weight, improved thermal and electrical conductivity and increased corrosion resistance. The industrial requirements for HMMCs are still under development, but some of the key requirements include the ability to produce HMMCs with consistent and reproducible properties, to produce HMMCs at a cost that is competitive with traditional MMCs, and to use HMMCs in a variety of applications. Hence, the development of HMMCs is still in its early stages; however, the potential benefits of this technology are significant. HMMCs have the potential to revolutionize a wide range of industries and are expected to play an increasingly important role in the future. This study makes the following novel contributions.
This study investigated the mechanical and tribological behaviors of hybrid composites reinforced with graphite and boron carbide particles in an AA7075 alloy matrix.
Induction stir casting, which is a novel technique that has not been widely used for this purpose, was used to produce the composites.
The composites exhibited improved mechanical properties, including the yield strength (YS), ultimate tensile strength (UTS), elongation, impact strength, and hardness.
It also found that the composites had improved tribological properties, including wear rate.
The rest of the article is organized as follows: Section 2 presents literature survey of various MMCs and HMMCs with different reinforcements and their insights and findings. Section 3 explains the materials and methods used in this study. Section 4 describes the preparation of composites using the experimental setup. Section 5 discusses the mechanical and tribological features of the prepared samples along with the unreinforced MMCs. Finally, Section 6 presents the conclusion, followed by references.
2. Literature survey
In this study, Devaraj et al. (Citation2021) investigated the performance of microtextured cutting inserts in the turning process of aluminum (Al)-MMC. The researchers analyzed various design parameters of the cutting inserts and their impact on the machining process. In addition, this study aimed to enhance the understanding of the machining characteristics and optimize the cutting parameters for Al-MMC. Ekici et al., (Citation2022) examined the repeated low-velocity impact responses of Al-MMCs reinforced with SiC particles. This study investigated the mechanical behavior and impact resistance of composites under repetitive low-velocity impact loading conditions. These findings contribute to the understanding of the dynamic behavior of SiC-particle-reinforced Al MMCs. Zhang et al. (Citation2019) conducted an in-situ investigation to analyze the deformation behavior and fracture mechanism of laminated Al/Ti composites manufactured through a hot rolling process. This study provides insights into the mechanical properties and deformation mechanisms of these composites, offering valuable information for their design and application in engineering structures. The characterization and mechanical characteristics of α-Al2O3 particle reinforced Al-MMC were the primary focus of the study conducted by Al-Mosawi et al. (Citation2017). Techniques such as uniball magneto-milling and uniaxial hot-pressing are used throughout the manufacturing process of the composites. Insights on the microstructure, density, and mechanical behavior of these composites were garnered because of the research. Akbar et al. (Citation2020) investigated the influence of reinforcing materials on the characteristics of Al-MMCs produced using the stir casting method. In this study, the mechanical characteristics, microstructure, and performance of composites made using a variety of reinforcing materials were analyzed and compared. These results contribute to a better understanding of how the characteristics of Al-MMCs are affected by the type of reinforcing material used.
Wu et al. (Citation2019) investigated how the presence of a large weight percentage of particulate B4C affects both the microstructure and mechanical behavior of an Al-MMC. They examined the impact of B4C particles on the microstructure and mechanical characteristics of the composite material, which provided insights into the processes that, contribute to the strengthening of such composites and allow for performance improvement. Manohar et al. (Citation2021) examined how different processing factors affected the mechanical characteristics of an AA7175/B4C composite that fabricated using powder metallurgy methods. The purpose of this research was to contribute to the development of powder metallurgy methods for use with aluminum-based composites by optimizing the processing parameters to improve the mechanical characteristics of the composite. Shen et al. (Citation2020) conducted research on the effect of negative Poisson’s ratio on the post-buckling behavior of functionally graded graphene reinforced MMC laminated plates in thermal environments. This study explored the mechanical behavior and thermal stability of laminated plates, providing insights into the structural response of laminated plates under thermal loading conditions. According to first-order shear deformation theory, Zhang et al. (Citation2020) performed a mechanical investigation of functionally graded graphene oxide-reinforced composite beams. In this study the mechanical response and load-carrying capability of these composite beams were examined. The results of this investigation provide useful information for the design and analysis of functionally graded composite structures. Moita et al., (Citation2019) conducted an elastoplastic and nonlinear study of functionally graded axisymmetric shell structures in a thermal environment using a conical frustum finite element model. This analysis is nonlinear. Their research focused on the mechanical behavior and structural response of functionally graded shell structures when subjected to thermal loading. The results of their study provide insights into the performance and stability of these structures.
Azarniya et al. (Citation2019) presented a comprehensive review of in situ HMMCs, focusing on phase transformations and mechanical aspects. The review paper included topics such as the synthesis techniques, microstructural development, and mechanical characteristics of these composites. This has provided researchers and engineers working on the subject with significant insights. The production and characterization of nano graphene and zirconia (ZrO2) reinforced AA6061 MMCs were carried out by Boppana et al. (Citation2020). This study focused on the fabrication process, microstructural characterization, and mechanical properties of these composites, contributing to the understanding of nanographene and ZrO2 reinforcement in Al-MMCs. Dinaharan and Akinlabi (Citation2018) conducted research on low-cost MMCs reinforced with fly ash. These composites are based on aluminum, magnesium, and copper. A friction stir procedure was used to fabricate these composites. This study focuses on the fabrication process, microstructural characterization, and mechanical properties of these composites, providing insights into the potential use of fly ash as a reinforcement material in MMCs. Budumuru and Mosa (Citation2021) analyzed the shielding effectiveness and mechanical properties of HMMCs reinforced with Al2O3 and fly ash for the oblique incidence of electromagnetic waves. This study also investigated the electromagnetic wave attenuation and mechanical behavior of the composite, providing insights into the potential applications of Al2O3 and fly ash as reinforcements in MMCs.
Kumar and Sharma (Citation2018) examined the effects of SiC, Al2O3, and ZrO2 particles on the laser beam melting and deposition (LBMed) characteristics of Al-MMCs prepared via the stir casting process. This study investigated the microstructural evolution and thermal behavior of these composites during the LBMed process, providing insights into their processability and potential applications. Sonker et al. (Citation2023) examined the effects of Zn/Sic particle incorporation on their properties. This study aims to enhance the understanding of these composites for potential applications in various industries. The findings of this study contribute to existing knowledge and provide insights into the development of aluminium-based composites with improved performance. In Vijayalakshmi and Reddy (Citation2023), the authors conducted an experimental study to investigate the mechanical properties of the Al5083/ZrO2/B4C HMMCs. They examined the effects of incorporating ZrO2 and B4C particles on the mechanical properties of AA5083. Kotteda et al. (Citation2022) focused on characterizing the behavior of composites and evaluating their potential applications. The findings of this study contribute to the understanding of metal matrix nanocomposites and provide insights into the development of HMMCs materials with enhanced properties. Sekaran et al. (Citation2023) conducted mechanical and physical characterization studies on ceramic reinforced Al-Mg hybrid nanocomposites. The composite, which comprised 15% Sic and 5% Al2O3, exhibited better mechanical properties than the Al-Mg cast alloy, with increased hardness, impact strength, and UTS. This study recommends HMMC for applications in steel bridge construction. As time passes on, many of the researchers focussed on developing various Al-MMCs with low-cost fabrication techniques in the view of making the synthesizing process feasible for mass production (Kotteda et al., Citation2022; Kotteda, Kumar, & Kumar, Citation2024; Vijaybabu et al., Citation2019). However, aluminium metal matrix composites being offered promising solutions as a replacement for cast iron and steel in automobile and aerospace sector, that is due to the fact that they are having light weight with high strength. Specifically, the fuselage application in an aircraft to bear various loads during the space travel by providing high specific strength structure that can reduce the dead weight of the transport vehicle predominantly (Kotteda, Kumar, Kumar, Gupta, & Kalidindi, Citation2024a). In addition to this, understanding the machining behaviour of Al-HMMCs is needed to transform the cast composite sample into a finished product with feasible surface finish in future studies (Kotteda, Kumar, Kumar & Gupta, Citation2024; Kotteda, Kumar, Kumar, Gupta, & Raju, Citation2024). The AA7475/ZrO2/Gr HMMCs were fabricated using the induction furnace stir casting technique. The mechanical and physical properties of HMMCS were studied and microstructural behaviour of HMMCS are evaluated for uniform distribution of reinforcements in matrix material (Madhavarao et al., Citation2024).
2.1. Research gap
Prior research has not focused on the mechanical and tribological properties of the Gr/B4C-reinforced AA7075 alloy matrix synthesized via induction stir casting route. While there may be independent studies on comparable composites or methods of manufacture, the amalgamation of these particular materials and procedures in relation to mechanical and tribological behaviour is lacking or insufficient. This study intends to fill this knowledge gap by conducting an experimental investigation that will provide valuable insights into the mechanical properties, tribological characteristics, and behavior of the Gr/B4C reinforced AA7075 alloy matrix manufactured through induction stir casting. The findings of this study may help close the knowledge gap and advance our understanding of this specific composite material and manufacturing process combination.
2.2. Problem statement
The mechanical properties of MMCs and HMMCs can be further improved by improving their composition, processing, and manufacturing procedures. However, there are significant difficulties in the processing and manufacturing of MMCs and HMMCs. Nevertheless, the present technologies have drawbacks, such as high production costs, limited design flexibility, and poor mechanical characteristics. The issue that must be addressed is the development of efficient and cost-effective processing and manufacturing methods to improve the mechanical properties of MMCs and HMMCs while preserving their distinctive qualities. The goal is to improve qualities such as the YS, UTS, elongation, hardness, impact resistance, and wear rate by optimizing the composition and production procedures. This project seeks to contribute to the creation of novel and improved hybrid composites for diverse industrial applications by resolving this issue.
3. Materials and methods
The experimental examination of the mechanical and tribological behavior characteristics of the Gr/B4C reinforced AA7075 alloy matrix by induction stir casting can be separated into different phases as illustrated in and detailed below.
AA7075 selection and preparation with Gr/B4C reinforcement: The AA7075 alloy was used as the matrix material. The reinforcements consisted of Gr and B4C particles. To guarantee optimal dispersion and adherence inside the matrix, Gr/B4C particles were produced and pre-treated.
Induction stir casting for composite production: Gr/B4C reinforcements were incorporated into an AA7075 alloy matrix using the induction stir casting technique. The AA7075 alloy was melted and pre-treated Gr/B4C particles were introduced into the molten matrix. To ensure equal dispersion and distribution of the reinforcements within the matrix, stirring was performed using an induction stir-casting rig. Subsequently, the composite material was hardened and shaped into necessary forms or specimens for testing.
Tensile test: Tensile tests were performed to assess the mechanical properties of the composite including the YS, UTS, and elongation. The specimens were created in accordance with the ASTM (American Society for Testing and Materials) standard dimensions. This testing was performed with the assistance of a testing machine, which delivered a controlled force to the specimens until failure occurred. The mechanical properties were determined using the load and deformation data obtained during the test.
Hardness test: The hardness of the composite material was measured using hardness tests, which were performed using a Rockwell hardness tester. The hardness value was measured based on the depth of indentation after a small starting force was applied followed by a major load. These levels indicate the resistance of a material to deformation and wear.
Test for impact: Impact tests were performed to determine the impact strength or toughness of the composite material. For this purpose, the Charpy V-notch test is widely utilized, which is a pendulum-type impact testing machine was used to submit V-notch specimens to impact forces. The impact energy absorbed by the specimen during fracture was measured to demonstrate the capacity of the material to withstand abrupt impact loads.
Wear test: Wear tests were performed to assess the tribological properties of the composite material. To simulate wear conditions, the composite specimen was exposed to controlled sliding or rotational motion against a counter surface. The wear rate was determined by measuring the mass loss of the specimen or the changes in the surface profile.
Features: The test findings were used to determine the output response characteristics of the composite material, such as YS, UTS, elongation, hardness, impact strength, and wear rate. These metrics quantified the mechanical and tribological properties of the Gr/B4C reinforced AA7075 alloy matrix.
3.1. Matrix material AA7075
AA7075 is a high-strength alloy composed primarily of aluminium, as shown in , with additional elements such as zinc, copper, magnesium, and chromium added to enhance its properties. This alloy is often used in aerospace applications because of its high strength-to-weight ratio and excellent fatigue resistance. lists the elements and their weight % for the composition of AA7075, which typically consists of 88.6%–90.6% aluminium, 5.6%–6.1% zinc, 1.2%–1.6% copper, 2.1%–2.5% magnesium, and trace amounts of other elements such as Fe, Si, Mn, and Ti. The addition of Zn to the alloy improves its strength and hardness, whereas Cu enhances its resistance to corrosion and fatigue. Mg contributes to the strength of the alloy and improves its weldability. Meanwhile, Mn provides an increased resistance to corrosion and wear. It is known for its high strength, with an YS of approximately 503 MPa elongation of 11% and UTS of approximately 572 MPa, respectively. AA7075 raw material illustrated in has excellent fatigue resistance, making it ideal for use in aircraft structures and other applications that require materials to withstand cyclic loading.
Table 1. Composition of AA7075 by weight percentage.
3.2. Reinforcement (graphite and B4C)
3.2.1. Graphite powder
Graphite powder is a form of carbon that is commonly used as an electrode material in DEDM process. It has several unique properties that make it an excellent choice for this application. One of the main properties of graphite powder is its high electrical conductivity. listed the various properties of graphite powder (Anirudh et al., Citation2017). This allows it to be used as an electrode material in DEDM, where it generates a spark that erodes the work piece material. Graphite can effectively conduct electricity because of its unique structure, which consists of layers of carbon atoms arranged in a hexagonal lattice. Another important property of graphite powder is its low coefficient of friction. This allows it to be easily mixed with a dielectric fluid, which is used to cool and flush away debris during the DEDM process. The low friction also helps to reduce the wear on the electrode, increase its lifespan and reduce the need for frequent replacement. Graphite powder as shown in also has a high melting point and is chemically stable, making it suitable for use in high-temperature and corrosive environments. In addition, it has good thermal conductivity, which helps dissipate the heat generated during the DEDM process.
Figure 3. Stir casting machine (up left). Stirrer setup (up right). Mixing (down left). Final work piece (down right).
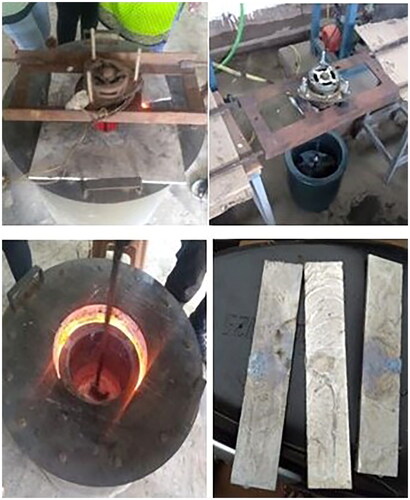
Table 2. Chemical and Physical properties of graphite powder.
3.2.2. Boron carbide
B4C is a ceramic material that is used as reinforcement in HMMCs. It is a very hard material with a high melting point and is very resistant to wear and corrosion. These properties make it an ideal reinforcement for HMMCs used in applications where high strength, toughness, and wear resistance are required. B4C is a valuable reinforcement material for HMMCs. It has several advantages, including high strength, toughness, wear resistance, and corrosion resistance. These properties make B4C-reinforced HMMCs suitable for a wide range of applications such as aerospace, automotive, defence, energy, and medical applications. It is a relatively expensive material, but its benefits often justify its cost. For example, boron carbide reinforced HMMCs can be used to make jet engine components that are lighter and stronger than those made from traditional materials. This can lead to fuel savings and improved performance. Thus, it is a valuable reinforcement material for HMMCs. This provides several advantages that make it suitable for a wide range of applications. lists the chemical and physical properties of B4C (Anirudh et al., Citation2017).
Table 3. Chemical and Physical properties of B4C.
3.3. Stir casting procedure
Stir casting is a commonly used technique for the fabrication of HMMCs that involves the incorporation of reinforcement materials into a molten metal matrix. In this process, the reinforcement materials were stirred into the molten metal using a mechanical stirrer, and the resulting mixture was then cast into the desired shape and allowed to solidify. As mentioned earlier, AA7075 is a high-strength aluminium alloy that is commonly used as a matrix material in HMMCs. Graphite powder and B4C are two reinforcement materials often used in conjunction with AA7075 in stir-casting processes. Graphite powder is a form of carbon with high electrical and thermal conductivity, a low coefficient of friction, and excellent wear resistance. The addition of AA7075 can improve the mechanical properties of the resulting HMMC, such as strength, stiffness, and wear resistance. In addition, the presence of graphite powder can improve the machinability of HMMC. In contrast, B4C is the hardest material with high strength, hardness, and thermal stability. When added to AA7075, B4C can improve the mechanical and thermal properties of HMMC, such as the UTS, hardness, and resistance to high-temperature environments. In addition, the presence of B4C can enhance the wear and corrosion resistance of HMMC. Overall, stir casting of AA7075 with graphite powder and B4C as reinforcement materials can lead to HMMCs with improved mechanical, thermal, and tribological properties, including strength, stiffness, wear resistance, and thermal stability. These properties make HMMCs suitable for use in high-performance applications, where materials must withstand extreme conditions and maintain their structural integrity over long periods of time.
3.4. Mechanical and tribological properties
YS, UTS, elongation, and hardness are important mechanical properties commonly used to describe the strength and durability of materials. These properties can be measured using various testing methods and can provide valuable information for the design, manufacturing, and selection of materials for various applications. The wear rate is an important tribological property used to describe the behavior of composites.
YS: It is the stress at which a material begins to deform permanently or plastically. It is the point on the stress-strain curve where the material shows a significant deviation from the linear elastic deformation and enters plastic deformation. It is an important parameter because it represents the ability of a material to withstand deformation without undergoing significant permanent deformation.
UTS: It is the maximum stress or load that a material can withstand before it breaks or fractures under tension. It is a measure of the resistance of the material to being pulled apart or stretched to the point of failure.
Elongation: Elongation refers to an increase in the length of a material when subjected to tensile (pulling) forces. It is typically expressed as a percentage of the original length of the material. Elongation is an important property, as it provides information about the material’s ductility or ability to deform plastically before failure.
Hardness refers to the resistance of a material to indentation, scratching, or deformation. This is a measure of how easily a material can be scratched, dented, or worn away. Hardness is typically measured using a hardness tester that applies a known amount of force to a small area of the material and measures the depth or size of the resulting indentation.
Impact: Impact refers to the ability of a material to resist fracture under high-velocity and high-energy loading conditions such as shock or impulse loading. It is a measure of the toughness of a material and its ability to absorb and dissipate energy before failure. Impact strength is typically evaluated using impact tests, such as the Charpy or Izod test, where a notched or unnotched sample is subjected to a single high-energy impact from a swinging pendulum or a falling weight. The impact strength was measured in terms of the energy absorbed by the sample during fracture and is reported in units of Joules (J) or foot-pounds (ft-lbf). It is particularly relevant for materials that undergo brittle fracture, although it can also be used to assess the impact behavior of ductile materials under specific temperature or loading conditions, such as the brittle-ductile transition temperature.
Wear rate: It refers to the rate at which material is removed over a specific period. This parameter is important for comprehending the performance and lifespan of mechanical components. Wear is an inevitable phenomenon that can significantly impact the functionality and longevity of both mechanical and biological systems, ultimately leading to system failure. The significance of material wear is rapidly increasing, and it can have a substantial functional and economic impact, similar to that of friction. In numerous industrial applications, components experience wear and necessitate replacement. Such replacements can incur high costs owing to the expense of components, labor, and equipment downtime required for part replacement.
4. Composite preparation
The development of a new composite material called HMMCS involves the combination of B4C and graphite with a reinforced AA7075 alloy. The manufacturing process utilized permanent mould die casting and melt-stirring techniques, incorporating several unique steps to achieve consistent dispersion of the B4C and graphite particles. The production process began by breaking down the ingot-shaped aluminium alloy into smaller pieces, which were then stored in a graphite crucible in a resistance furnace operating at 2 kW and 230 V. The alloy was heated to 800 °C for melting. To minimize casting defects, such as porosity, blowholes, and voids, commercially available hexachloroethane tablets (C2Cl6) were used to degas the molten metal. After degassing, the temperature of the molten metal was lowered and maintained at 730 °C before the introduction of B4C and graphite particles. Prior to their introduction, the B4C and graphite particles, which were 50 µm in size, underwent a preheating process at 200 °C for 2 h to remove loose scales, residues, and moisture. A motorized stirrer was employed to create a vortex in the molten metal at speeds ranging from 550 rpm to 600 rpm. Through a series of funnels, B4C and graphite particles were continuously discharged into the swirling molten metal at a controlled rate of 15–20 g/min. To ensure the proper dispersion of the reinforcing particles, the stirring speed was reduced to 300 rpm and maintained for approximately 15 min. Upon completion of the stirring operation, the molten mixture consisting of metal and reinforcing particles was poured into a preheated cast iron mold at a pouring temperature of 700 °C. The composite was then cooled to ambient temperature, allowing it to solidify to its final shape. To evaluate the effect of the matrix and reinforcement on the mechanical properties, three different composite configurations were produced: one with 5% volume of B4C and 5% volume of graphite, another with 6% volume of B4C and 4% volume of graphite, and a third with 4% volume of B4C and 6% volume of graphite. In addition, an unreinforced AA7075 alloy was cast for comparison.
4.1. Experimental process
The molten metal used in the stir casting process was prepared separately in a furnace, and a standard ladle with a capacity of 1 kg was used to transfer molten aluminium to the stir casting furnace. The metal was maintained at 700 °C in the stir-casting furnace. First, the stir casting furnace was filled with molten aluminium. The B4C particles were weighed separately and placed in individual containers in a furnace, where they were preheated. As the temperature in the furnace approached 700 °C, a cover material was added to the molten metal. This cover aids in removing oxides and impurities from the metal, thus ensuring a cleaner final product. Once the molten metal was ready, a stirrer was inserted into the crucible and activated to create a vortex within the molten metal. The stirring speed was adjusted using a potentiometer to achieve the desired vortex characteristics. Once the proper stirring speed was achieved, B4C particles were gradually introduced into the vortex. Care was taken to ensure the controlled and steady addition of reinforcements. After all the B4C particles were added, the stirrer was rotated for an additional ten minutes. This extended stirring time allowed for thorough and even dispersion of the B4C particles within the molten metal. This step was crucial for ensuring the homogeneity and integrity of the final composite material. Once the stirring process was complete, a ladle was used to transfer the molten metal from the crucible to the die cavity. The molten metal was left in the die for approximately two minutes to solidify and harden. Subsequently, the die was removed and the resulting solidified composite was obtained. shows the stir casting machine (top left), stirrer setup (top right), mixing (down left) and final work piece (down right).
presents the different compositions of the composite material consisting of an aluminium 7075 matrix and two types of reinforcements: B4C and Gr. The weight percentages of the reinforcements were varied for each composition.
Table 4. Details of the mixing weight ratio of reinforcement with matrix AA7075.
Matrix material: AA7075
B4C Reinforcement (wt %): Weight percentage of B4C reinforcement in the composite.
Gr Reinforcement (wt %): Weight percentage of Gr reinforcement in the composite.
It provides three different compositions, each with a combination of B4C and Gr reinforcements and their corresponding weight percentages:
Composition 1:
B4C Reinforcement (wt %): 5%
Gr Reinforcement (wt %): 5%
Composition 2:
B4C Reinforcement (wt %): 6%
Gr Reinforcement (wt %): 4%
Composition 3:
B4C Reinforcement (wt %): 4%
Gr Reinforcement (wt %): 6%
These compositions indicate the relative amounts of B4C and Gr reinforcements added to the AA7075 matrix to form a composite material. The weight percentages represent the proportion of each reinforcement component in the overall composite composition. These variations in the composition allow the study of the influence of different reinforcement ratios on the mechanical and tribological properties of the composite material.
5. Results and discussion
5.1. Tensile test
The samples made using unreinforced AA7075 and reinforced AA7075 alloys with different compositions, namely AA7075 + Gr 5% + 5% B4C, AA7075 + Gr 6% + 4% B4C, and AA7075 + Gr 4% + 6% B4C, were evaluated using a Universal Testing Machine (UTM) to determine their mechanical properties. The UTM follows a general procedure for calculating the mechanical characteristics:
Sample preparation: Prepare samples of each composition with AA7075 alloy, Gr, and B4C according to the desired shape and dimensions according to the testing standards.
Mounting the sample: Each prepared sample was securely mounted onto the UTM using appropriate grips or fixtures to ensure stability during testing.
Initial setup: Configure the UTM with the necessary parameters, such as a suitable load cell, crosshead speed and gauge length for elongation measurement. These settings may vary depending on the specific testing standards and requirements.
YS determination: An increasing load was gradually applied to each sample using the UTM until it reached a point where a permanent deformation of 0.2% (or a predetermined value) occurred. The load was recorded as the yield strength (YS) of the material.
UTS testing: Continue applying an increasing load using the UTM until each sample fractures. The load at the fracture point was recorded as the UTS.
Elongation measurement: Throughout the tensile testing process, the UTM measured the change in the gauge length of each sample. The elongation percentage was calculated by comparing the final gauge length after fracture to the original gauge length.
By following these steps for each sample, the UTM can provide data on the mechanical properties, including YS, UTS, and elongation as listed in , for the unreinforced and reinforced AA7075 + Gr 5% + 5% B4C, AA7075 + Gr 4% + 6% B4C, and AA7075 + Gr 6% + 4% B4C compositions. These results made it possible to compare the mechanical properties of the unreinforced and reinforced samples quantitatively, which shows how reinforcement affects the way a material behaves when stretched. As listed in , three compositions were used in the tensile test: AA7075 + Gr 5% + B4C 5%, AA7075 + Gr 4% + B4C 6%, and AA7075 + Gr 6% + B4C 4%. The YS and UTS values for each composition were recorded in N/mm2 and the elongation was obtained in percentages. The results indicate that the composition with 4% B4C and 6% Gr has the highest UTS value of 320 N/mm2, whereas the same composition has the highest YS value of 150.09 N/mm2.
Table 5. The tensile test results with different composition.
5.2. Hardness test
Rockwell hardness testing is a widely used technique for determining the hardness of materials by measuring the depth of penetration under specific loads. The Rockwell hardness testing machine initiated the process by applying a minor load to establish the zero position, following which a major load was applied to measure the depth of penetration. In the present scenario, the Rockwell hardness testing machine was utilized to assess the hardness of one unreinforced sample (AA70775) and three reinforced samples (AA7075 + Gr 5% + 5% B4C, AA7075 + Gr 4% + 6% B4C, and AA7075 + Gr 6% + 4% B4C). To ensure accurate testing, samples were subjected to metallographic finishing. This involves utilizing emery paper with varying grits, such as 100, 220, 400, 600, and 1000. By progressively employing these different grits, the surface underwent refinement, eliminating any roughness and achieving a smooth finish.
Once the samples were suitably prepared, they were placed in a Rockwell hardness tester. A load of 200 g was applied commencing with a minor load to establish the starting position. Subsequently, a major load was applied to measure hardness. This major load induced indentation on the surface of the sample. Each load was maintained for 20 sec to ensure precision. Subsequently, the penetration depth was measured, and the Rockwell hardness value was determined using a specific scale associated with the Rockwell hardness testing method. It is important to acknowledge that the hardness of the samples was influenced by their composition, particularly the inclusion of Gr and B4C. The Rockwell hardness testing machine provides a quantitative measurement of the hardness, facilitating the evaluation of the material’s resistance to deformation and its suitability for various applications. By subjecting the unreinforced and three reinforced samples with different compositions to the Rockwell hardness test and analysing the obtained hardness values, it becomes possible to compare their relative hardness and discern the impact of Gr and B4C additions on the hardness properties of the material. shows the results of the Rockwell hardness test for the simple alloys without reinforcement (Sample No. 1) and wt. % variation of different reinforcements like B4C, Gr, and AA7075 (Samples No. 2-4). As shown in , the hardness value for each composition was recorded, and the results showed that the composition with 4% B4C and 6% Gr had the highest hardness value of 74, whereas the AA7075 + Gr 5% + B4C 5% composition had the lowest hardness value of 66.
Table 6. The hardness test results with different composition.
5.3. Impact test
The Charpy V-notch test is a common method for measuring the impact strength or toughness of a material. They can be used for both metals and composites. It measures how well a material can absorb energy when hit by force. A Charpy V-notch test was used to measure the impact strength of an unreinforced AA7075 sample and a Gr/B4C-reinforced sample with different weight percentages (wt %). Typically, the samples are cut to certain sizes, and one side has a V-shaped notch. For the test, the sample was hit with a hammer with a swinging head that broke it. The impact strength of each sample was determined by measuring the amount of energy that the sample took at the point where it broke. This energy measure is expressed in joules (J). The test was performed according to the ASTM standards to ensure that the results were consistent and easy to compare. Using this test on both the unreinforced AA7075 sample and the Gr/B4C-reinforced AA7075 sample with different weight percentages, the impact strength of each composition was measured as shown in , which allows us to compare how well the samples can with stand impact loading. As listed in , the results show that the composition with 4% B4C and 6% Gr has the highest impact strength value of 4.2, whereas the AA7075 + Gr 5% + B4C 5% composition has the lowest impact strength value of 2.8.
Table 7. The impact test results with different composition.
Overall, demonstrate the influence of varying amounts of Gr and B4C reinforcement materials on the UTS, hardness, and impact strength of AA7075 aluminium alloy. These results can be used to determine the optimum composition for specific applications based on the required mechanical properties. and shows the output characteristics of the final work piece with different compositions.
5.4. Wear test
Here, a DUCOM TL-20 model pin-on-disk tribometer was used to determine the wear rate of three different composites of AA7075 namely, AA7075 + Gr 5% + 5% B4C, AA7075 + Gr 4% + 6% B4C, and AA7075 + Gr 6% + 4% B4C. The testing device comprised a rotating pin that was pressed against a stationary disk under different loads and sliding velocities. In this experiment, a sliding velocity of 3 m/s and loads of approximately 20, 40, 60, 80, and 100 N were considered to determine the wear rate of the three distinct samples as listed in . In addition, a graphical illustration of the wear test results is shown in , where the sample prepared with AA7075 + Gr 5% + 5% B4C composition obtained a lower wear rate than the other two samples.
Table 8. The wear test results with different composition.
6. Conclusion
This study examines the mechanical and tribological characteristics of Metal Matrix Composites composed of AA7075 aluminium alloy reinforced with Gr/B4C particles. The results showed substantial enhancements in the mechanical characteristics of the composites in comparison to the unreinforced AA7075.
The inclusion of Gr/B4C reinforcements resulted in an increase of around 85.31% in the YS and 88.24% in the UTS. However, it also led to a reduction of approximately 63.75% in elongation.
In addition, the hardness and impact resistance had an approximate increase of 18% and 110% respectively.
Furthermore, the rate of wear gets reduced to 5.56%, 50%, and 25% by applying different loads to the AA7075 + 5% Gr + 5% B4C reinforced sample.
The findings emphasize the capability of Gr/B4C reinforcements to create novel and upgraded hybrid composites with improved mechanical properties. This study aims to tackle the obstacles related to the processing and manufacturing of MMCs and HMMCs including the issues of expensive production, restricted design adaptability, and decreased mechanical behaviour. The outcomes of this research have implications for various industrial applications that require sophisticated materials with enhanced mechanical and tribological properties. Even though this study was able to show that Gr/B4C reinforcements make AA7075's mechanical properties better, there are still many things that could be improved including optimization of composition and processing parameters, to find the best balance between strength, flexibility, and other performance parameters. Microstructural analysis to understand how reinforcements are distributed within the matrix and how they bond to the surfaces can help improve the design of composites. By focusing on these future research directions, HMMCs will continue to be improved and used in more industries. They can also be made into more advanced materials with improved mechanical properties.
Authors contributions
Kantheti Prasada Raju performed the experiments, collected the data, and wrote the original draft; Kunjee Lal Meena defined the methodology and supervised the work; Rama Bhadri Raju Chekuri reviewed and edited the manuscript; all authors read and approved the final manuscript.
Data availability statement
The data that supports the findings of this study are available from the corresponding author (Kantheti Prasada Raju) up on reasonable request.
Disclosure statement
No potential conflict of interest was reported by the author(s).
Additional information
Funding
Notes on contributors

Prasada Raju Kantheti
Prasada Raju Kantheti is a Research Scholar in the Department of Mechanical engineering at Nirwan university, Jaipur, India. He received his M.Tech. Degree in Advanced Manufacturing Systems from B.V.C. Engineering College, Andhra Pradesh, India. His areas of interest are Characterization of materials, Composites, Unconventional machining and Alternative fuels. He had published 7 research papers in various International Journals and conferences to his credit.
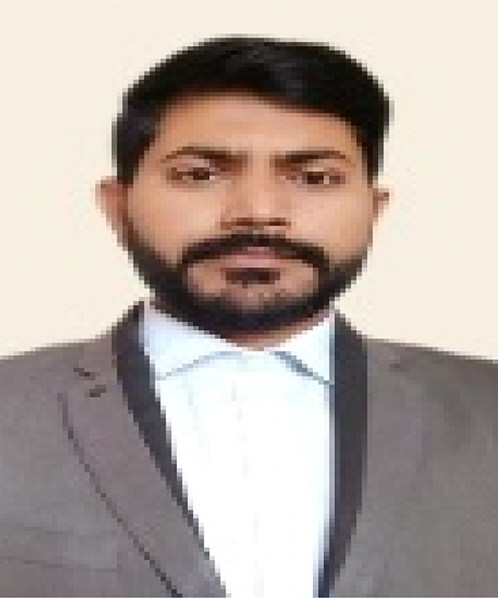
Kunjee Lal Meena
Dr Kunjee Lal Meena is an Associate Professor & HOD in the Department of Mechanical engineering at Nirwan university, Jaipur, India. He received his PhD degree in Production Engineering from IIT Roorkee, India. He has completed M.Tech In production Engineering from IIT Delhi and B.Tech in mechanical engineering from NIT Bhopal His areas of interest are Developed Ceramic Nanocomposites material using sintering Technique. He had published 10 research papers in various International Journals and conferences to his credit.

Rama Bhadri Raju Chekuri
Rama Bhadri Raju Chekuri received his Ph.D. in Mechanical Engineering from K L Deemed to be University and is presently working as Associate Professor in the department of Mechanical Engineering at S.R.K.R Engineering College, India. His research interests include machining processes and unconventional ones in particular, optimization techniques in machining processes. He had published more than 25 research papers in various International/ National journals and conferences.
References
- Akbar, H. I., Surojo, E., Ariawan, D., Putra, G. A., & Wibowo, R. T. (2020). Effect of reinforcement material on properties of manufactured aluminum matrix composite using stir casting route. Procedia Structural Integrity, 27, 62–68. https://doi.org/10.1016/j.prostr.2020.07.009
- Al-Mosawi, B. T., Wexler, D., & Calka, A. (2017). Characterization and mechanical properties of α-Al2O3 particle reinforced aluminium matrix composites, synthesized via uniball magneto-milling and uniaxial hot pressing. Advanced Powder Technology, 28(3), 1054–1064. https://doi.org/10.1016/j.apt.2017.01.011
- Anirudh, M. S., Asif, S. N., Nadella, S. V., & Nagireddy, K. (2017). Investigation of mechanical properties of al 7075/B4C/GR hybrid metal matrix composite. International Journal of Mechanical Engineering and Technology, 8(5), 400–408.
- Azarniya, A., Azarniya, A., Abdollah‐zadeh, A., Madaah Hosseini, H. R., & Ramakrishna, S. (2019). In situ hybrid aluminum matrix composites: a review of phase transformations and mechanical aspects. Advanced Engineering Materials, 21(7), 1801269. https://doi.org/10.1002/adem.201801269
- Boppana, S. B., Dayanand, S., Kumar, M. A., Kumar, V., & Aravinda, T. (2020). Synthesis and characterization of nano graphene and ZrO2 reinforced Al 6061 metal matrix composites. Journal of Materials Research and Technology, 9(4), 7354–7362. https://doi.org/10.1016/j.jmrt.2020.05.013
- Budumuru, S., & Mosa, S. A. (2021). Analysis of shielding effectiveness and mechanical properties of metal matrix composite AL6061 reinforced with Al2O3 and fly ash for oblique incidence of EM wave. International Journal of Intelligent Computing and Cybernetics, 14(3), 398–411. https://doi.org/10.1108/IJICC-01-2021-0014
- Devaraj, S., Malkapuram, R., & Singaravel, B. (2021). Performance analysis of micro textured cutting insert design parameters on machining of Al-MMC in turning process. International Journal of Lightweight Materials and Manufacture, 4(2), 210–217. https://doi.org/10.1016/j.ijlmm.2020.11.003
- Dinaharan, I., & Akinlabi, E. T. (2018). Low cost metal matrix composites based on aluminum, magnesium and copper reinforced with fly ash prepared using friction stir processing. Composites Communications, 9, 22–26. https://doi.org/10.1016/j.coco.2018.04.007
- Ekici, R., Kosedag, E., & Demir, M. (2022). Repeated low-velocity impact responses of SiC particle reinforced Al metal-matrix composites. Ceramics International, 48(4), 5338–5351. https://doi.org/10.1016/j.ceramint.2021.11.077
- Güler, Ö., & Bağcı, N. (2020). A short review on mechanical properties of graphene reinforced metal matrix composites. Journal of Materials Research and Technology, 9(3), 6808–6833. https://doi.org/10.1016/j.jmrt.2020.01.077
- Hu, Y., & Cong, W. (2018). A review on laser deposition-additive manufacturing of ceramics and ceramic reinforced metal matrix composites. Ceramics International, 44(17), 20599–20612. https://doi.org/10.1016/j.ceramint.2018.08.083
- Imran, M., & Khan, A. A. (2019). Characterization of Al-7075 metal matrix composites: A review. Journal of Materials Research and Technology, 8(3), 3347–3356. https://doi.org/10.1016/j.jmrt.2017.10.012
- Kotteda, T. K., Eshwar, D., Balakrishna, G., Kuchampudi, S. V., Prasad, B. D., & Sadasivam, S. (2022). Experimental investigation on metal matrix nanocomposite: Aluminium alloy 6061 and 7075 with SiC and fly ash. Journal of Nanomaterials, 2022, 1–14. https://doi.org/10.1155/2022/8368934
- Kotteda, T. K., Kumar, M., & Kumar, P. (2024). Experimental insights and micrographical investigation on graphene nanoplatelet–reinforced aluminum cast composites. The International Journal of Advanced Manufacturing Technology, 131(5-6), 2707–2718. https://doi.org/10.1007/s00170-023-12270-8
- Kotteda, T. K., Kumar, M., Kumar, P., & Chekuri, R. B. R. (2022). Metal matrix nanocomposites: future scope in the fabrication and machining techniques. The International Journal of Advanced Manufacturing Technology, 1–19. https://doi.org/10.1007/s00170-022-09847-0
- Kotteda, T. K., Kumar, M., Kumar, P., Gupta, A., & Kalidindi, S. R. R. (2024a). Mechanical and Metallurgical behaviour of Aluminum/graphene nanocomposites in Fuselage applications. Cogent Engineering, 11(1), 2324030. https://doi.org/10.1080/23311916.2024.2324030
- Kotteda, T. K., Kumar, M., Kumar, P., & Gupta, A. (2024). Development of forecast models on electrical discharge machined graphene nanoplatelets reinforced aluminum composite fabricated via stir casting route. Cogent Engineering, 11(1), 2328821. https://doi.org/10.1080/23311916.2024.2328821
- Kotteda, T. K., Kumar, M., Kumar, P., Gupta, A., & Raju, K. M. K. (2024). A review on machinability and optimization of machining parameters of metal matrix composites. Journal of Physics: Conference Series, 2765(1), 012005. https://doi.org/10.1088/1742-6596/2765/1/012005
- Kumar, V., & Sharma, V. (2018). Effects of SiC, Al2O3, and ZrO2 particles on the LBMed characteristics of Al/SiC, Al/Al2O3, and Al/ZrO2 MMCs prepared by stir casting process. Particulate Science and Technology.
- Madhavarao, S., Rao, V. K., & Chekuri, R. B. R. (2024). Preparation and investigation of mechanical behavior and characterization of AA7475/ZrO2/Gr hybrid MMC. Engineering Research Express, 6(1), 015071. https://doi.org/10.1088/2631-8695/ad20b6
- Manohar, G., Pandey, K. M., & Maity, S. R. (2021). Effect of processing parameters on mechanical properties of Al7175/Boron Carbide (B4C) composite fabricated by powder metallurgy techniques. Advances in Science and Technology, 105, 8–16.
- Moita, J. S., Araújo, A. L., Soares, C. M. M., & Soares, C. A. M. (2019). Elastoplastic and nonlinear analysis of functionally graded axisymmetric plate-shell structures. Composite Structures, 226, 111186.
- Samal, P., Vundavilli, P. R., Meher, A., & Mahapatra, M. M. (2020). Recent progress in aluminum metal matrix composites: A review on processing, mechanical and wear properties. Journal of Manufacturing Processes, 59, 131–152. https://doi.org/10.1016/j.jmapro.2020.09.010
- Sekaran, P. R., Ramakrishnan, H., Venkatesh, R., & Nithya, A. (2023). Mechanical and physical characterization studies of nano ceramic reinforced Al–Mg hybrid nanocomposites. Silicon, 15(10), 4555–4567. https://doi.org/10.1007/s12633-023-02473-9
- Shen, H. S., Xiang, Y., & Reddy, J. N. (2020). Effect of negative Poisson’s ratio on the post-buckling behavior of FG-GRMMC laminated plates in thermal environments. Composite Structures, 253, 112731. https://doi.org/10.1016/j.compstruct.2020.112731
- Sonker, P. K., Singh, T. J., & Yadav, N. P. (2023). Experimental research and effect on mechanical and wear properties of aluminium based composites reinforced with Zn/Sic particles. Discover Materials, 3(1), 9. https://doi.org/10.1007/s43939-023-00045-7
- Vijayalakshmi, K., & Reddy, G. B. (2023). Experimental study on mechanical properties of Al5083/ZrO2/B4C hybrid aluminum metal matrix composites. Materials Today: Proceedings, 80, 1392–1396. https://doi.org/10.1016/j.matpr.2023.01.152
- Vijaybabu, G., Prasadraju, K., Raju, V. V. M. K., & Sunilkumar, K. (2019). Studies on effect of ash in aluminium hybrid metal matrix composites. Materials Today, 18, 2132–2136. https://doi.org/10.1016/j.matpr.2019.06.640
- Wu, C., Shi, R., Luo, G., Zhang, J., Shen, Q., Gan, Z., Liu, J., & Zhang, L. (2019). Influence of particulate B4C with high weight fraction on microstructure and mechanical behavior of an Al-based metal matrix composite. Journal of Alloys and Compounds, 789, 825–833. https://doi.org/10.1016/j.jallcom.2019.03.065
- Zhang, Y., & Chromik, R. R. (2022). Tribology of self-lubricating metal matrix composites. In Self-lubricating composites (pp. 31–71). Springer Press.
- Zhang, X., Yu, Y., Liu, B., Zhao, Y., Ren, J., Yan, Y., Cao, R., & Chen, J. (2019). In-situ investigation of deformation behavior and fracture mechanism of laminated Al/Ti composites fabricated by hot rolling. Journal of Alloys and Compounds, 783, 55–65. https://doi.org/10.1016/j.jallcom.2018.12.272
- Zhang, Z., Li, Y., Wu, H., Zhang, H., Wu, H., Jiang, S., & Chai, G. (2020). Mechanical analysis of functionally graded graphene oxide-reinforced composite beams based on the first-order shear deformation theory. Mechanics of Advanced Materials and Structures, 27(1), 3–11. https://doi.org/10.1080/15376494.2018.1444216