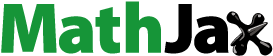
ABSTRACT
The economic design of the slabs is the most influential on the construction cost and choosing the appropriate system is the key to the slabs optimal design, and there are many systems that have been developed recently to reach the most economical design. In this research, we try to mix two systems, each of them has its optimal use, and each of them has its advantages and limits for uses, and they have been mixed to try to find a dual system with more advantages. This paper presents a slab system consisting of flat slab system that its field strip areas were replaced with two-way hollow block systems. Consequently, the total weight of the resulting slab was reduced, which positively affected the quantities of steel reinforcement used directly, in addition to its reflection on the design of columns and foundations due to the low self-weight of the slabs. The validity of the proposed concept has been verified through a finite element analysis using Program SAP2000 that was applied to several cases with different configurations under static and dynamic loadings.
Introduction
Nowadays, several types of R.C. floor systems are used covering various architectural and functional buildings’ requirements as demonstrated (Sergiu, Ciprian, & Floreaissues, Citation2010; Zekirija & Isak, Citation2017). Some of these systems are shown in .
Several technologies have developed that work through the optimization of the reinforced concrete section in an attempt to reduce its volume as in the mid-20th Century, systems of hollow core floors have been invented to reduce the heavy self-weight of classic R.C. flooring systems, but it was observed that shear and fire resistance for slabs of this system are considerably reduced. shows several types of this construction flooring system as demonstrated (Ihsan, Adel, & Radhwan, Citation2018; Liu, Citation2018).
Recently, a new technology called “Bubble Slab” has been developed through using two-way voided flat slabs. The slab middle layer of concrete was replaced by plastic balls to reduce floor concrete quantities; shows the bubble slab system as demonstrated (Bhagyashri & Barelikar, Citation2016; Churakov, Citation2014; Ihsan et al., Citation2018; Lai, Citation2010; Reshma & Binu, Citation2016; Surendar & Ranjitham, Citation2016; Tae-Young, Sang-Mo, & Sang-Dae, Citation2010).
The objective of the present study is to introduce a proposal for a combined flooring slab construction system that is a mix of two different systems. This proposed system consists of flat slab system replacing its field strips by two-way hollow block slabs, aimed to achieve a dual system with more advantages. The effect of applying the proposed system on the required quantities of concrete and steel reinforcement has been studied under the effect of static and dynamic loadings.
Proposed slab system
The proposed slab is a combination between flat slab and two-way hollow block slab. The new system is obtained through keeping the solid flat slab in the column strips, while replacing the interior field strips by two-way foamed blocks. The main object is reducing the self-weight of solid interior panels by using light weight foam blocks, which consequently reduces concrete quantities, reinforcement and reduces the total gravity loads that leads accordingly to reduce the cost for columns and foundations. Using two-way ribbed slab concept is easier, cheaper, and practically more familiar compared to other current developed systems such as bubble deck slab. shows the proposed mixed flat/ribbed slab. The validity of the proposed system was verified as detailed below.
Evaluation methodology
The evaluation of the proposed system was done by comparing the results of the designed floors using traditional Flat Slab system, and the results when re-designed using the proposed system. A comparison of the results of the two design concepts was made to clarify the advantages of the proposed system. The performance of the proposed system was evaluated under the effect of static and dynamic loads to test the extent to which it meets the design criteria in terms of stress and serviceability.
Three floor slabs with different spans were used as studied cases. The dimensions of the studied cases are shown in and summarized in for both conventional and proposed systems. The evaluation methodology steps for the studied floors models were as follows: -
Dimensions estimation for the (columns, column & field strips, slab & drop panel thickness) for the three studied flat slab cases has been performed to satisfy the requirements of the Egyptian Code of Practice (ECP 203, Citation2007).
The conventional flat slab system has been analyzed using Program SAP2000 (Computers and Structures, Inc. Citation2002); thus, the assumed dimensions were checked under the effect of the service loads, for the ultimate moment values and also checked for the ultimate punching shear.
In the proposed system, the three finite element models were modified by making the interior panels were replaced with two-way foam ribbed slabs for each model. The ribs were modeled as solid slab with virtual thickness “tv” that has same stiffness of corresponding ribbed slabs for simplicity.
Finally, comparing the overall performance in terms of resulting straining actions with corresponding deformations for both systems was done.
Table 1. Configuration & dimensions for studied cases
Materials properties: -
The service floor loads:
Numerical modeling
Two-dimensional linear static and dynamic analysis using finite element program SAP2000 was used to study the structural behavior of the proposed system and comparing to the conventional flat slab. The FEM for each case was consisted of three typical continuous bays along both directions, the concrete flooring slabs are modeled using 1764–4356 Shell elements according to the model. The flooring models were loaded with uniformly distributed dead and live loads and then analyzed for static and dynamic responses. For simplicity in the proposed system, the interior panels are modeled as solid slabs using virtual thickness “tv” with the same flexural stiffness of the corresponding flat slab. shows the equivalent thickness for all cases. For example, for case 2 the total ribbed slab thickness ts = 29 cm using block height = 24 cm with slab thickness = 5.0 cm.
For flexural resistance, the corresponding moment of inertia of the typical section:
Thus, the used equivalent virtual solid slab thickness “tv” = 20.85 cm.
This simplification was verified for accuracy by making one of the slab models with ribs and comparing the results with the approximate model, which showed the convergence of the results. shows the ultimate straining actions for case 2.
Shear stresses analysis
As shear stress is one of the most critical aspects in flat slab analysis and design, the problem becomes more critical for the proposed mixed system due to the corresponding reduction in shear resistance of the critical sections. Due to keeping column strips and drop panels with same configuration for both conventional and proposed systems, punching shear resistance at the critical sections according to ECP has been checked; . The field strip that has been modified must be able to transfer the loads above it to its circumference without the occurrence of shear failure and therefore this must be checked.
Dynamic analysis
A modal analysis was performed for both conventional and proposed systems. compares between the first three modes of the proposed and the conventional flat slab systems. Also, an impulsive gravity load of = 200 kg/m2 is applied for the studied cases of both conventional and proposed systems using the shown load function.
Table 2. Dynamic characteristics for the two systems
Results
The resulting straining actions for conventional flat slabs system and proposed mixed system were checked according to ECP; accordingly, the critical sections are perfectly safe and the required steel reinforcements were determined for both conventional and proposed systems. The critical sections for ultimate design moments; sec. 1, 2, 3 are shown in . For instance, for case 1, the critical design bending moment (M11) for the column strip at sec. 2 equals (−40.7 m.t) for the conventional system against (−35.9 m.t) for the proposed system, with a reduction ratio equals 11.8%. Similarly, at sec.2 of the column strip, the reduction ratios of bending moment for cases 2, 3 equal 6.9%, 7.7%, respectively.
Samples of the resulting straining actions are shown in . While in , a comparison between the maximum straining actions values and deflection for the conventional system and the proposed system was performed.
Table 3. Comparisons of ultimate design moments M11 and deflections
The results indicate that a significant increase of the maximum deflection values for the proposed system than the conventional system; this result is expected due to the valuable reduction of stiffness that exceeds 60 %. presents a comparison of the resulting deflection values with the allowable coded limits that indicates acceptable results for case 1 and case 2, while for case 3 (of longest studied spans 11.0 m), the actual deflection “∆act.” slightly increases the allowable limit “∆all..” Therefore, the deflection values has been rechecked more accurately using the exact configuration for the proposed system representing the interior panels by actual ribbed slabs, accordingly, “∆act.” decreased to “42 mm” that is within the allowable limit.
For all studied cases, the savings of self-weight of floors, concrete quantities, and the quantities of required steel reinforcements are summarized in , and the reduction percentage ratios applying the proposed concept are presented in .
Table 4. Comparisons of quantities between proposed system & conventional flat slab
Table 5. Reduction ratios between proposed system & conventional flat slab
Finally, the results indicate a valuable reduction for concrete and steel reinforcement quantities for all cases as shown.
presents the self-weight load reduction ratio using the proposed system; the reduction ratios are relatively low as the proposed system in this study is conservative due to keeping column strips and drop panels with the same configuration. Self-weight represents the greater ratio of flooring loads. Consequently, the design loads for columns and foundations were reduced between 7% and 10%.
Table 6. Comparisons of ultimate column loads
Concerning the dynamic analysis, shows the modal responses for the first three modes of the proposed system that indicate a small difference with the conventional flat slab system; this difference ranges 5–10%. Additionally, the results indicate an increase of the maximum deflection and velocity values for the proposed system than the conventional system, although the results are within the allowable vibration limits according to the international vibration codes (BS Citation1993; DIN Citation1999; SN 640 312, Citation1992). displays comparison between the deflection and vibration velocity values.
Table 7. Comparisons of dynamic characteristics
shows the punching shear check results for all cases at the critical sec. 3, also, provided the ratio of the equivalent thickness for the interior panel ribbed slab section “tv.sh.” to the solid flat slab thickness. The punching shear check for all cases provided adequate safety margin. It is recommended to keep safety margin for punching shear without more calculation to use thickness ratio not to be less than 0.4.
Table 8. Punching shear results
Conclusions
The proposed system is capable to resist efficiently same service load patterns as traditional solid flat plate slabs. In addition, the required steel reinforcement’s quantity of the flooring slabs was reduced with a valuable ratio reached to 16% and the floor concrete quantity was reduced up to 14% consequently; the design loads for columns and foundations were reduced up to 10%. The savings of required concrete and steel quantities would be more valuable for multi-story buildings. The results indicate an increase of deflection values for the proposed system than the conventional system, but it’s still within the acceptable limits.
The punching shear check for all cases at the critical sections is adequately safe, we can propose that the ratio of the equivalent thickness for the interior panel ribbed slab section “tv.sh.” to the solid flat slab thickness not to be less than 0.4 to provide more safety margin against punching shear.
Concerning the dynamic analysis, the results show that the proposed system has adequate efficient to conventional one. Additionally, the results of applying dynamic impulsive load satisfying the vibration velocity limits according to related standard.
Disclosure statement
No potential conflict of interest was reported by the author(s).
References
- Bhagyashri, G., & Barelikar, S. M. (2016). An experimental study on two-way bubble deck slab with spherical hollow balls. International Journal of Recent Scientific Research, 7(6), 11621–11626.
- BS 7385. (1993). Evaluation and measurement for vibration in buildings, Part 2: Guide to Damage Levels from Ground borne Vibration,. BSI 389 Chiwick High Road London W4 4AL: British Standards Institution 0580221881 .
- Churakov, A. (2014). Biaxial hollow slab with innovative types of voids. Construction of Unique Buildings and Structures, 6(21), 70- 88 2304 - 6295 .
- Computers and Structures, Inc. (2002). SAP2000 nonlinear Ver. 10. Berkeley, California.
- DIN 4150. (1999). Vibration in Buildings - Part 3: Effects on Structures. Germany: German Inistitute for Standardization.
- ECP 203. (2007). The Egyptian code for design and construction of concrete structures. Giza, Egypt: Housing and Building Research Center.
- Ihsan, A. A., Adel, A. A., & Radhwan, A. (2018). A state-of-the-art review on hollow core slabs. Journal of Engineering And Applied Sciences, 13(9). 1819-6608 ARPN.
- Lai, T. (2010). Structural behavior of bubble deck slabs and their application to lightweight bridge decks. M. Sc. in Civil and Environmental Engineering, Massachusetts Institute of Technology, MIT.
- Liu, F. (2018). Dynamic analysis of hollow core concrete floors. Stockholm, Sweden: Licentiate Thesis in Structural Engineering and Bridges.
- Reshma, M., & Binu, P. (2016). Punching shear strength development of bubble deck slab using GFRP stirrups. IOSR Journal of Mechanical and Civil Engineering (IOSR-JMCE), 01–06. e-: 2278-1684,p-: 2320-334X. Retrieved from www.iosrjournals.org
- Sergiu, C., Ciprian, A., & Floreaissues, N. (2010). Achieving an experimental model concerning bubble deck concrete slab with spherical gaps. Buletinul Institutului Politehnic Din Iaşi publicat de Universitatea Tehnică, Gheorghe Asachi, din Iaşi Tomul LVI (LX), Secţia Construcţii. Ărhitectură.
- SN 640 312. (1992). Effects of Vibration on Construction. Switzerland - Zurich: Swiss Consultants for Road Construction Association.
- Surendar, M., & Ranjitham, M. (2016). Numerical and experimental study on bubble deck slab. International Journal of Engineering Science and Computing, IJESC 6 5 5959- 5962 2321 3361 . Coimbatore, India.
- Tae-Young, J., Sang-Mo, K., & Sang-Dae, K. (2010). New eco-friendly two-way void slab. International Conference of Sustainable Buildings Asia, SB10, Seoul, Korea.
- Zekirija, I., & Isak, I. (2017). Comparative study between waffle and solid slab systems in terms of economy and seismic performance of a typical 14-story RC building. Journal of Civil Engineering and Architecture, 1068–1076. doi:10.17265/1934-7359